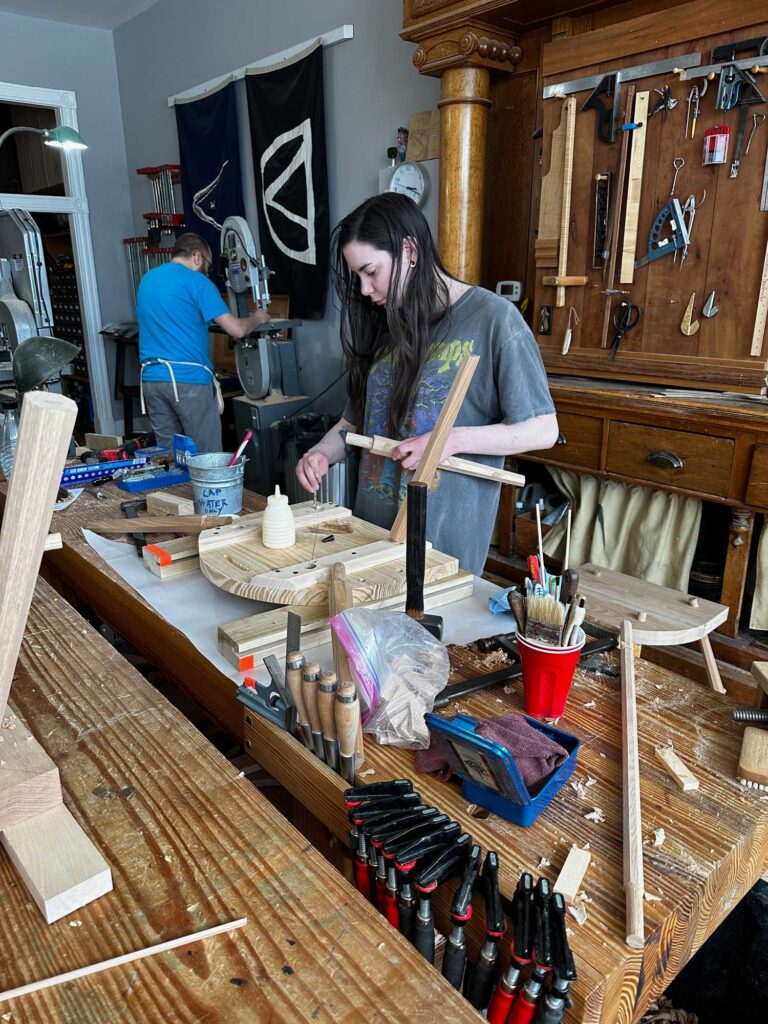
This may or may not work. For the last month, our blog has been sinking into madness. Subscribers weren’t receiving emails, our RSS feed was jacked up and this week we started receiving fatal errors whenever we tried to post.
We have lots of technical help, and I hope in the coming week things will be cleared up for good (we are migrating our blog to a self-hosted server with lots of in-person, on-the-phone support). Then I’ll be able to tell you about the final make-room-at-Anthe sale we are now running. And lots of other news.
But until then, our apologies for the weirdness. I hope we will be able to answer your questions today. Let’s give it a go. Write your question in the comment field below, and we will answer it.
Comments are now closed.
— Christopher Schwarz
Whatever happens in the digital world, looks like that chair is on the way to success.
How do you sharpen your Barr bench chisels? Freehand or LN honing guide? If the latter, which jaws?
The bench chisels fit just fine in the stock jaws of my Lie-Nielsen honing guide. The big 2″ chisel is a little too think to fit into the stock jaws. I could change the jaws out, but I don’t. Instead I just let the big chisel sit on the bars between the jaws and clamp the chisel in place. The top part of the jaws grab the back of the chisel just fine.
Boy this is hard to describe in words.
Anyway, I know that my method is not at exactly 35° as a result. But it’s a consistent angle. And that’s what matters to me.
Great. Thanks! Hadn’t thought of dropping it on the bars.
Sorry, another question. I’ve noticed a fascination with Japanese tools. My only experience with them are pull saws from places like Woodcraft. Are the chisels and planes really the cat’s pajamas?
I went through that phase in the late 1990s. Some of the handmade stuff is extraordinary. But like any tool tradition, you need to educate yourself to get the best results. Just because a chisel comes from Japan doesn’t mean it is superior.
The people who commit to learning about the tools and their makers are rewarded with beautiful tools that work incredibly well. But I can say the same about the Western tool tradition. Choose a tradition, immerse yourself in it and you’ll gather a kit that will last you the rest of your life and serve you well.
Hi Chris, in your guidance for your stick chair class (I’m coming to the one in London) you say that the Windsor Workshop delrin travisher can negate the need for an inshave. Why? What’s different about it?
You can set the Windsor Workshops travisher to take a heavy inshave-like cut. And then adjust the blade to take a fine cut. It’s not a perfect solution, but it’s a great way to do the operation with one tool.
If I may, do you just have too many copies of these books on sale, or are you not going to carry the physical title any longer.
Anyone who doesn’t buy them at these prices are fools. Fools!
These titles will remain in print. I’ll explain it all in a post this coming week. These are the titles that are taking up lots of floor space, or they are titles where we have a 30-year supply (or more) of the books.
Or living overseas, you have no idea how frustrating it is to sit in Australia see these bargains “going to waste”.
I agree, I’d love to order from LAP.
Will you be making any more stickers or are you out of ideas?
My daughter Madeline was the Sticker Queen. She fulfilled the stickers as a way to make ends meet in college. She has now graduated and is working a very busy job in Pittsburgh. She doesn’t have the time to so the sticker business.
I haven’t run out of ideas. I just run out of a way to mail them out.
Have you any info on Glen-Drake tools. Was looking to get a second one, but over a month site says he trying to get caught up on things.
I haven’t heard from Kevin in awhile. I will check in. In the meantime, it looks like Lie-Nielsen still has the Tite-Mark:
https://www.lie-nielsen.com/products/tite-mark-marking-gauges-tite-mark-?path=tite-mark-marking-gauges&node=4179
TFWW has them in stock, too. https://toolsforworkingwood.com/store/item/MS-TITEMARK.XX/Tite-Mark+Marking+Gauges
I asked Laura Mays about this two years ago when I was taking a class from her as they both are in Ft. Bragg, CA and I wanted to purchase some of this tools. From what Laura said is that Kevin is still making tools but rather than focus on selling directly to customers, he is focusing on selling to retailers. I know Tools for Working Wood sells a lot of his Tite Mark gauges. He’s a very nice man if you ever get the chance to meet him in person.
Any experience or thoughts on the Brian Boggs bandsaw fence: https://boggsbench.com/product/boggs-micro-fence-plans/
I’m afraid you are asking the wrong guy. Brian is a certified genius, and I’m sure the fence works beautifully (I watched the video that explains it). But that’s just not how my brain works when it comes to making joinery. If you think about dialing in .002″ on a band saw fence, and you get excited, Brian is the way forward. (Or if you are in a production shop where parts need to be interchangable.)
I cut a tenon as close as possible. If it’s too thick I get my shoulder plane out.
I’m building a white oak table top for an exterior location. I’d prefer to use a ‘natural’ oil finish. What’s your favorite clear exterior oil finish?
Any of the drying oils will work. I use tung oil and refined/purified linseed oil for exterior applications.
I am making a cabinet from 1” quartersawn poplar. There are 2 doors, each 29” long and 15” wide. I am using 2 battens for each door that are 12” long and 3” wide. The battens and the door are 1” thick. I am planning to use #20 clinching nails to secure the battens to the door. Should I glue the 3 boards for each door or is it better to just tongue and groove them and let the nails hold them on? Should the pilot hole go completely through both boards? Should it be larger than usual? I usually use a tapered bit; would a straight bit be better?
On the edge joints: that is a choice governed by the style of the piece and the time you have on hand. My preference would be to T&G the edges and glue them together.
Then make a mockup of the batten-door joint to experiment with the right size and shape of pilot hole. When I clench, the pilot typically foes through both pieces to reduce blow-out on the exit side.
Two related questions.
1) After I sawed out the red oak laminated back of one of my Gibson chairs a couple checks opened up (1/2″ long by 1/32″ wide when viewed from the end grain). Because of where they are located in the laminations, I don’t think they will cause structural problems but I’d like to help reduce the likelihood that they will enlarge. Would injecting hide glue work? I plan to finish the chair with wax/oil.
2) Any plans to make a video documenting how you experiment when you are building your chairs? Things like leaving tenons long, changing the angles of sticks, etc. I ask because in a couple recent blogs you wrote about experiment or perish and teaching people how to build specific chairs vs. just teaching skills to build chairs. My 2 cents are that you do the latter through specific examples so this is just another tempest in a tea pot. I have no problem with doing the experimentation on my own but out here in CA even red oak is expensive and the quality is really bad. I figure 50% waste for this set of chairs and I hit all three hardwood suppliers within 90 miles and picked through their entire selection of red oak three times to get enough to build the chairs. Sadly, the city of Sacramento is loaded with 100 year-old street trees that include elm but the wood/epoxy table slabbers got the contract with the city to cut the trees that need removing and they cut them into as long and wide of 4/4 live edge slabs as they can, dry them improperly so they crack, and then sell the cracked wood for exorbitant prices.
Hey Gerlach,
Have you tried Macbeath hardwoods in Berkeley.
I usually find very good wood there and red oak in 8/4 is usually under $8 bf
Yep, that is where I got most. The first time I went I got a couple boards but there wasn’t enough straight stuff for sticks, the second time, a couple months later, they hadn’t restocked. A couple months later and the restock boards were pretty much all really bad. When I have a chance I’m going to look at the Stockton store as they said it has a much larger inventory and they get their stock from there.
It’s not super consumer friendly, but go to Moore Newton as well, they typically have a ton more selection and better prices than MacBeath, but they don’t really cater to the hobbiest. It’s very much a trade place.
I wouldn’t go there, open a new account, and buy one board. But if you were planning on spending a decent amount, or picking up a healthy amount of material.
When I have non-structural cracks that I want to hide, I usually fill them with epoxy. It will add strength and fill the gap. Just know that the wood will do whatever it damn well pleases. So you might not with the Battle of the Crack.
On designing and experimentation, I use construction softwood scraps to mock up news designs (such as my recent peasant chair and revised Hobbit chair). After 20-something years of building chairs, we also have a ton of chair parts. I know people who also use reclaimed/dumpster wood they have harvested from the curb.
I don’t think I am aware enough of my design/experimentation process to describe it in a video that makes sense. Some of my design process is iterative – designs change slowly over time. Other times I have a brainwave. And I also have a long list of ideas that I want to try on a chair someday that are waiting for the right chair or amount of free time.
I have a chance to get a good old jointer at a decent price. It’s has an old 3 blade straight knife cutter head? If cost isn’t a concern and labor isn’t an issue would you recommend switching to a helical insert style cutter? As someone who has used lots of machines and iterations, is this a good upgrade? I like things that save me time and grief and get me working with sharp tools. Are helical heads officially the way to go for overall better performance?
Thanks
Keep doing what you guys do.
We have helical heads on our jointer and planer. They do a better job with figured woods and the blades last for years, even in a professional environment.
Yes, they are worth the investment.
I’m making two of the staked stools for our kitchen. These would need to be taller than the ones you made. 1) the spread of the legs would be quite wide if I stick with the same angles as suggested for the normal height stool. Is there a way to adjust this or would this make the stool unstable? 2) the stretchers I assume would still be about 17 inches from the seat to make a place to put your feet or does this compromise strength? And they need to be closer to the floor?
My best recommendation is to go to a furniture store with a camera and a tape measure. Sit in kitchen stools that are the same height as what you desire. Study the rake and splay and where the stretchers are and how thick the components are.
When I make so many changes to an existing design, I usually look to what has worked in the past. Do that. Then modify from there.
Have you written about and/or can you recommend any resources on what a beginner should know when visiting a lumber yard to select and purchase wood for the first time?
The lumberyard experience is so varied that I cannot imagine a guide that would make sense for most readers. The way we buy wood in Kentucky is entirely different than how it’s done in the Eu, for example. And how a commercial outfit buys lumber has little to do with how a home woodworker does it.
My advice would be to read a book on understanding wood, its properties and how it is processed for sale. Our books “With the Grain” and “Cut & Dried” do that part.
Then go visit a lumberyard. Call ahead and ask if it’s OK for customers to pick their own boards (many yards won’t allow this; I don’t buy form them).
A good yard will be happy to explain how they sell wood. If they are jerks, go somewhere else.
The other option is to buy from a trusted online seller that will ship stuff to you. Irion Lumber and Hearne Hardwoods are two suppliers who do an amazing job of pulling good boards and shipping them to you. There are many others like Irion and Hearne. Ask around.
Sorry I don’t have a great answer.
You might want to check out the podcast “Shannon’s Lumber Industry Update”. Episode 16-18 are a three-part guide to buying lumber
Good morning, I am in the “make pretty” stage of a bookcase project and considering the finish. Could I just use general finishes milk paint or does it need something else applied over the paint to protect it after a couple of coats? Thanks for your advice!
I just use two coats (usually two coats…sometimes three, almost never just one) of the paint and call it done. Seems to work fine.
Simple and easy, thanks Megan!
Will there be some kind of meet-up while CS is in Bavaria? I know Chris would probably hate every minute of it, but I might be in the area in July, and, although I couldn’t swing one of the classes,I’d love to pay my respects.
Appreciate all you guys do!
Well you are welcome to stop by the Dictum store while I’m in Munich. Always happy to shake someone’s hand and say hi.
If we do plan an evening soiree, I will post the details here.
Sounds like a good class; 2 estrogen-enhanced entities for shop assistants, one of whom is your daughter! As an icebreaker 50 years ago, does my heart good to see.
Any guess when the Anthe grand opening might happen? Given the earlier postponement I will not be surprised if you decline to comment yet but my summer is starting to get scheduled.
I’m afraid I don’t have a date yet. Daily disasters (blog DNS/printing delays) keep me from being able to plan ahead. Right now I am shooting for Aug. 24, which is the traditional Way-Goose day, which seems appropriate.
“Well, I’ve eliminated DNS.
I cant possibly be DNS.
I found something else wrong and fixed it.
It’s still broken.
It was DNS.”
Moral: It always DNS.
I am building a pair of end tables with cylindrical tenons through the top. There is some tearing on one around the top (exit side) of the mortises. It’s not splelching level, just sort of a ragged edge that will show once leveled out. Any ideas for hiding this? -Deke
Oh, and to avoid in the future? My backing board was probably to thin and flexible, but do you have experience drilling from both sides like Chris Williams? Since these are table tops the chewed up edge won’t be carved away. Thanks!
I don’t know about hiding it. I would plane away the top until the ragged edge disappeared. A firm wedging also helps in these situations.
You can drill from both sides – a very traditional approach. You just have to make sure you are at the right angle and your auger is very sharp to do a clean job of it.
In a woodshop, couldn’t the Garland split-head rawhide mallet work more or less interchangeably with/as a lump hammer? (Your recent post about the Garland was my introduction to it. I love the idea of it.
Ya know…I was going to ask him that, but I didn’t. I figured he bought it so people would stop clutching their pearls when he used a lump hammer on his froe.
The feedback and sound is totally different. I rely on the sound that the lump hammer and component make to determine if a joint has been seated firmly. Rawhide just gives you a generic thump. Just my preference.
Hello! While reading that you do not de-tension band saws earlier this week, I was wondering what you advise about hand saws, for storage of roughly a week between uses;
-wooden frame turning saws
-metal frame coping saws
-metal tubular frame buck saws
I don’t have a buck saw, so on that one, I can’t say. But I do, I think mostly out of habit, detension my Knew Concepts coping and fret saws before putting them back in my chest…simply because it’s so easy to do (flip the lever). I don’t detension my Blue Spruce. I have a wooden frame turning saw at home that gets used rarely, so I keep that one detensioned to keep th twin from stretching. Chris’ answer will likely vary.
My answer isn’t much different. I detension wooden turning saws and metal-frame coping saws for storage. It’s easy, so why not? (It’s not easy or necessary for a band saw). Metal frame coping saws have wussy frames that will take a set if you leave them tensioned. But it’s easy to bend the arms back so they will tension the blade.
I have a basement shop and I’m very conscious of dust (my daughter has severe allergies…has been hospitalized for this before). This means good dust extraction on all the power tools and also a HEPA filter. I use tools basically for milling and do all joinery and finish work by hand. The thing I struggle with most is sanding. Right now if I need to do it, I simply lug the stuff outside and do it there. Not convenient, especially in the winter months. I’m considering getting a Festool setup and wonder if you have any experience with this? In part I see a world in which I can save space by ditching my table saw (I have a band saw I use much more) and getting a track saw, but in the meantime, I am wondering your thoughts on the Festool sanders and extraction. And, on the chance that you have experience with them, any thoughts on the best sander for furniture making? I’m thinking the 5 inch Rotex but wonder if that’s too big for casework and small pieces.
Thanks for any thoughts you have.
We use a Festool dust extractor (two of them, actually) and Mirka sanding disks. The dust collection is excellent with that setup on the Makita sanders we have. At home, I have a Mirka 5″ DEROS – I think the dust collection is even better with the Mirka disks on that sander (and the Festool extractor). And Chris just got a Festool sander – I don’t know if he’s used it enough yet to comment on whether or not it increases dust collection efficacy. But yes – the Festool extractors are the cat’s pajamas.
The Festool vacs are the best I’ve ever used. I recommend them without any reservations.
You can make any sander dustless by using interference pads and a mesh sandpaper (such as Abranet). We get no detectable dust when we sand with this combination.
https://www.rockler.com/mirka-abranet-5-in-pad-protectors-9955rp-2-pack?country=US
The Festool sanders are excellent. But you don’t have to own them to create a dust-free experience. I use and old Makita BO5010, interference pads, Abranet and a Festool vac.
Hi James,
In the class I took with him, Chris said that the festool dust extractor was the best thing the company made. On his recomendation, I bought 3 for the woods lab at my school. We have one permanently on the over arm collector on the sawstop (which used have just a shop vac), one at the belt sander station, and a floater for palm sanding. The difference has been noticable. Dust from palm sanders is virtually nonexistent, and the belt sander dust greatly decreased. The one on the sawstop works better than the shop vac it replaced, but still throws dust (I am convinced the perfect solution on that machine will never happen). My only regret is that I didn’t purchase a handful more for when a bunch of students are sanding at the same time.
I can’t remember the model, but it is one of the self cleaning ones. If you want, you can email me and I can look up the info when I get back to school on Monday.
If you want a cheaper, but also scientifically supported general solution to grab some of the stray airborn particles your current system might miss, look into making a Corsi-Rosenthal Box.
https://www.filtrete.com/3M/en_US/filtrete/home-tips/full-story/~/how-to-make-a-diy-air-purifier/?storyid=e1cfeb36-75fe-4ac9-8727-37e911234ce4
I’m the crazy person that is making the chair for a 4 foot 7 inch lady and have a couple more questions. BTW thanks for the earlier help, I found a study on chair ergonomics based on user height that simplified determining dimensions.
the seat and undercarriage are good but the geometry of the arms seems all messed up.
Should I make an arm bow fixture for this chair? Armrest height is 5.5 to 6 inches
Can you share where you found that study on ergonomics?
It is at http://www.mdpi.com the article is called “Chair Design Based on User Height” and it is free
I would have the person sit on a flat surface and hold their arms like they would in an armchair. Then measure from the elbow to the surface.
Unfortunately the chair is a surprise gift for her birthday so I’m using the formulas in the article
I have some gorgeous QS yellow pine that I’m making a workbench from. If I laminate it normally, the worktop won’t capture that oh-so-lovely grain — so I’m thinking of laminating 4 inch strips like a normal tabletop panel, then laminating three of those panels together to make the top at least 3 inches thick. Worried about wood movement along the width of the bench (~28 inches) and between layers of the top. I’m silly to worry about this, I’m crazy to do it, or maybe a happy middle ground?
It just sounds like a lot of work for a workbench. I cannot even tell you what my workbench top looks like (except for the fact that it’s reasonably flat). You could make a lamination like you suggest, but there is a lot of opportunity for gaps in the lams (which would bug me).
Hello! If I’m making a 3-legged back stool from the ADB but want a larger seat – can I keep the angles and sight lines the same and just extend the leg holes further so they are the same distance from the seat edge as the original plans? This makes sense to me, but confirming. Thank you!!
Sure. As long as you don’t do anything extreme (just a few inches here and there is fine).
Hi,
I’m making a small table out of some walnut I had on hand (8×10 top; 20 inches tall) to place my coffee/beer..hopefully to be paired with a future stick chair build in the coming months. I wanted to use this table as an opportunity to attempt drawboring mortise and tenon joints for the first time.
However as I started riving the pegs out of some oak (already cut/fit the mortise/tenons) I realized I may not have planned ahead very well for such an operation as there’s only 3/8 inch between the back of each rail and the back of its two connecting legs….and my understanding is that you’d typically want at least 3/8 (edge buffer) + 1/8 (half bit width) + some fudge >= 5/8 so as to not run into the adjacent rail on the back side with the pins.
To keep things short I won’t list out all the crazy ideas rolling around in my head for how to proceed…but rather simply ask what your recommendation would be (even if its just glue it up and save drawboring for a future project)? Thanks very much for your time in sharing your knowledge…really appreciate it.
If I understand the problem correctly (no guarantee there), why not just use shorter pins that pass through the leg, then the tenon, then slightly into the leg meat behind the tenon?
ok, so don’t go all the way through the backside..i was slightly worried as a newbie that i’d have a hard time getting the pin taper just right with a hard stop on the back to make things snug when the pressure is on during the glue up…but i guess if i do a dry run and assume some amount of required clearance to the back stop before hammering them in..what’s the worst that could happen 🙂 thanks for the help!
I sent a link to my brothers of the Irish stick chair that you had up for auction. The largest brother commented he would be afraid the legs would splay too much and his ca-rear would be on the floor. I pointed out the red oak legs… to no avail.
And, you would say?
If you can fit between the arms, the chair will hold you. The oak legs are rived. The joints are incredibly sound. This design is based on chairs that have survived fat-ass people for centuries with no problem.
Good morning C, M, and hivemind.
We are moving! Finally leaving Nebraska and relocating to the Twin Cities.
My goal is to be better at building/finding community this time, so I was wondering if anyone has info on decent woodworking communities/clubs/orgs etc.
(Will also take recs on anarchist collectives, left leaning churches, awesome restaurants, you name it)
Congrats Don! (And I will reply to your email.)
The twin cities have a very vibrant woodworking scene. Check out the guild there and get to know Mike Siemsen. He’s the godfather of wood up there. Great guy.
https://www.schoolofwood.com/
And the twin cities is home to the American Association of Woodturners, if turning is of interest.
Minnesota Woodworkers Guild https://mnwwg.org/
Also checkout the local Area A of Midwest Tool Collectors that has three meets every year https://mwtca.org/ here.
There are several maker spaces in the metro area like https://tcmaker.org/.
I second the Mike Siemsen recommendation wholeheartedly.
Too many good restaurants to even pick a favorite. Too many breweries but my number one is Barrel Theory in St. Paul.
Hi Don! Connect with the Fireweed Woodshop folks!
Do you think an engraving on the seat of a stool would aggravate the sitter? My family is Irish so I want to make a vernacular stool and either engrave or paint “Grandpa’s Creepie” on it.
I have engraved the stools of several seats. I can’t feel the engravings. Maybe someone with a sensitive butt could, but I doubt it.
Just so you know, the RSS feed has been working for me this week after the outage. Not to discourage your search for a better setup for the blog.
Also, Japanese tools are awesome. grin
Any chance you could post a tracing of the handle for the Plumb claw hammer?
I scored a head for 50 cents and need to get around to making the handle for it.
Here are two dead-on photos with a ruler for scale.
https://blog.lostartpress.com/wp-content/uploads/2024/05/IMG_6071-scaled.jpg
https://blog.lostartpress.com/wp-content/uploads/2024/05/IMG_6072-scaled.jpg
Hi there Chris and crew from sunny AZ!
You mentioned in a post about diamond stones to use windex as the substrate. My two part question is, can you use windex on the diamond wheels for the Tormek? It comes with its own version of hone-rite so that the wheel doesn’t rust. Does Windex prevent rust as well?
Also, do you think hone-rite is a “needed” option for whetstone sharpening? Or will water be just fine so long as I dry the tool off quickly…?
As always, thank you.
In my experience, you can use oil/water/or something else on almost any sharpening media. What we now call “oilstones” were commonly lubricated with water in days of yore (Moxon mentions using spit….).
The only real problem is that once you use oil on a porous media, you are pretty much stuck with oil with that stone unless you take drastic measures.
I have seen zero advantage using anyone’s honing liquid. I won’t say it’s a scam. But I won’t say it’s not.
Do you have strong opinions on making lamps? I want to make a 5ft tall floor lamp inspired by the projects in the ADB and am curious how you would go about it. I feel like there are drawbacks to both a staked and boarded design.
Interesting design question.
I would probably use staked construction. Likely I’d stake legs into an octagonal post for the base. Then place a second post on top in a wooden hinge to hang the light off of. I’ve built a few lamps, but haven’t tried one lately.
Gonna think on this awhile.
Ran into a Megan reference in an unexpected place this week… https://youtu.be/qpzG-4J_QxY?si=6kL0zMFdukWbTYUw. I know you guys often mention using blacksmith made items, and I don’t think folks generally know just how many blacksmiths there are out there. ABANA.org has a list of blacksmith organizations around the USA, and they can help you find one. https://abana.org/affiliates/directory/#!directory/map
I love those chest handles! (Kinda want another set for my chest at work…)
In the video, he said he only has a couple left of the plasma cut backs. If you get in touch with him quickly, you might be able to score another set. When I first saw the link, it was called “Megan’s cat handles,” and it made me think of you. Then I watched the video and saw that it WAS you!
Oh…I watched it. I’m resisting though! (I think a different design would be better on my LAP chest…just to be a little less boring!)
A follow up question to the earlier one about sanding. I haven’t heard you talk much about refinishing. Like you, I’ve switched to a Linseed Oil/Wax formula for, among other things, health reasons. I have an old Stickley chest (cherry) that needs a redo. I’m going to finish it that way, but need thoughts on getting old finish off. I hate idea of toxic strippers….any thoughts on whether it’s okay to just sand away the old finish. Or, is this violating a taboo that I’m totally unaware of (Very possible)
I’d probably sand (with good dust collection and maybe a mask…who knows what you’re sanding off!). But, know that sanding old cherry will make it a LOT lighter in color, and the oxidation process will have to start over. That’s why I haven’t refinished my cherry coffee table, despite the many cat scratches on its top.
I’ve not done enough refinishing to have a valid opinion. When I have to remove an old finish, I usually hope it’s shellac so I can remove it with alcohol. You can sand away the finish, but you will also be removing any patination/color that has accumulated (which is key with cherry).
My approach with good-quality antiques (like a Stickley: Leave it cruddy and leave it alone.
Do you know if there is a complete compilation of all of the articles John Brown wrote for Good Woodworking magazine that can be purchased somewhere? I have read through all of the ones in Chris Williams’ excellent book ‘Good Work’, which left me wanting more!
I do not. This has been a project that Nick Gibbs (JB’s editor) has been working on for years. Out of respect for Nick, we have steered clear of this project.
What kind of glue would you suggest for edge gluing cold bend (comp) wood before resewing (on bandsaw)?
If the comp wood is dry then any glue will work (PVA, hide). If it’s wettish, you’ll need epoxy or another specialized adhesive.
I would be gluing while wet, then reading and bending. I was thinking that clear gorilla glue might be a possibility. What do you think?
poly glues are moisture-activated. So it would be worth a try. CAVEAT: I’ve never done this.
Reading should be resawing.
Earlier you suggested planing the top of my staked side table to eliminate the ragged mortise edges. The part I didn’t mention is that the legs are already glued and wedged(!). Do you have a suggestion to support the top for planing now that the legs are attached?
Clamp them by a leg, with another leg braced against the bench (we usually use a carver’s vise or Benchcrafted Hi Vise for clamping things with stick-style legs). Or, if there’s enough room between the legs, clamp a board to your bench (with enough of it overhanging it to hold the table) and sleeve the table over that if you want better support for the top.
I usually clamp one leg in my face vise with an adjacent leg pressed against the front edge of the benchtop, and the top touching the benchtop. That is usually enough to allow me to jack and smooth a surface. Sometimes you have to work around stretchers, but this is almost always doable.
Hi Chris, Megan. There are a number of vintage tool reseller out there (Jim Bode, Hyper Kitten). I have more vintage tools than I need or some things I bought to try and feel indifferent to and want to sell them. Do you have a feel how much one typically gets paid by these resellers. For example, if a fair market value for something vintage is $100, how much might I expect to be paid? I totally understand they need to make a profit and tools don’t always sell quickly, etc. Any general ideas on expectations would be helpful. Thanks.
Hi Joe,
Here’s my understanding of the used tool market. Most of those sellers buy tools from estate sales, old tool meets, box lots at auctions and other places where they can get a reasonable price for reselling. Companies like Brown Auction buy big collections from individuals, or individual special pieces at times.
You can always ask Josh at Hyperkitten if he’s interested. But he might not be able to pay you what you want.
If I were in your situation, I would put them up systematically on eBay with good photos and descriptions. And promote the piss out of the sale on Facebook, Instagram and wherever else I could log in. Selling direct to the end user is worth the extra effort.
Good luck!
I buy and sell tools and normally I pay 50-60% of retail (sold prices, not asking prices, on eBay) for common tools. Rarer things I can pay more for, but I can’t pay $40 for a plane that might only sell for $55. Hope that helps.
Forgot to mention that on eBay, as an occasional seller, you can figure on eBay taking about a 15% cut.
I’m making a table to go outside. It’s made of 8/4 hickory (mistakes were made, but I’m not stopping now.). I’m planning on nailing battens to the bottom. The battens are more 8/4 hickory (I can be convinced to just not use these for battens or even to rip them “flatter”.). Anyway my question is, when using cut nails how big would you aim for to join together 8/4 stuff like this? I was thinking 10d minimum, and maybe going as big as 16d. Any suggestion on if I should use something weird like a boat nail, since the work will be outside?
You need the tip of the nail to go through at least half the thickness of the top. You can use copper nails if you want, but steel ones will last a long long time.
Thanks!
Hey Chris! I like the cabinets you installed in the electric horse garage. How did you hang them on the concrete wall?
There is a 2x cleat attached to the wall with Tapcons. Then the contractor (Bill) added a wooden cleat to the interior of the cabinet (below each cabinet top). Then he screwed through that and into the 2x.
Another chair maker to consider it mark soukup (I went to high school with him). https://www.windsorchairsbyhand.com/writing-arm-chairs
Thanks. Chris rembold (amateur on chair #6)
IKEA has a kit for that! Please find it on aisle 495 shelf 154 section 95 sublocation ZZ. Please don’t forget to pickup some delicious Swedish meatballs on the way out of the store!!
Thanks for the sale. Just spent another $100.
Hey Folks…
I cannot find the link to the video Chris made on how to assemble the English Framing Square. Can you please post it here?
Thanks very much.
Thank you!
I’m getting ready to move into an old chalet (I’m Swiss) with my pregnant wife and I’m currently trying to fill it with nice furniture that should last generations I hope. You’re a big help for knowledge and inspiration in this undertaking. Thanks!
To still ask a question:
I’m hoping to use a natural finish on my projects, but I’m slightly worried about my kitchen countertops and a bathroom cabinet (holding the sink) that I’m making out of oak.
Will linseed oil and wax suffice? Or should I try to add some tung oil as well? Or is this maybe asking too much of oil?
We use wax and oil on our countertops. They still look great after five years of use and abuse. I have reapplied the wax/oil mixture twice in the last five years. And it’s easy to repair. Scrape the affected area, apply more finish.
I think of my countertops like I think of my workbench top. It is not a piece of fine furniture. It is a work surface. I don’t try to beat it up. But a few scratched and stains are part of the bargain (and I like patina).
I sure as heck wouldn’t use a film finish on a countertop. When that fails, repair is impossible or very difficult.
Any update on ‘Set & File’?
We have had delays at the printer. The book should have been out this week. But because of events outside out control, they are estimating it will ship the last week of June or the first week of July.
Because of these delays, we have been backed up on several other titles. It’s frustrating.
Hi Cris, long time ago, many years, you talked about a marking thing, it was similar to a skew chisel in one end and a long pointy thing on the other, I bought one, I don’t remember if from you or someone that made it for you. Unfortunately it went the way of all my tools, (Davey Jones Locker) do you have the name of it, and maybe where I can get one? It could be a cool tool to have made that you guys could sell.
You are describing a “striking knife,” a common tool in the 18th century.
https://www.popularwoodworking.com/techniques/the-striking-knife/
I made mine out of a dull 1/4″ spade bit. You can learn to make a proper one here:
https://store.popularwoodworking.com/products/digv-forging-a-striking-knife-dl
Or hire any blacksmith to make you one.
Hello all! Long time listener, first time caller.
The covers of several of my hardcover LAP books are starting to curl. Hayward vol. 3 is looking especially jaunty!
Any ideas what is causing this? And how do I best correct it?
This can happen when there has been a change in the relative humidity. You can usually flatten the boards out by returning the book to the original humidity and then pressing it flat for a time (weeks sometimes….). We do by stuffing the offender into a bookcase that is tight (probably too tight). Sorry you are having trouble. The Hayward books seem more prone to this than our other titles. The factory cannot explain why.
i have a LAP polisoir (sp?) that has hardened with age and no longer works. is it possible ti revive it? if do, how?
I don’t believe we ever made or sold polissoirs. But you can revive yours by trimming away a layer of the broom corn with a knife (or a fine saw). Then apply more hot beeswax to the freshly exposed fibers.
Another question. At some point in the past, you shared the trick of wetting end grain with an alcohol and water mixture to ease shooting. I shot a bunch of end grain last weekend with my 51, including some 8/4. In some cases I was lazy with the saw so had a bit of stock to remove. I used straight alcohol and it worked amazingly well. Shooting with the 51 is a joy but this made it effortless. Thank you for the great tip!
So my question–any other shop tips to share? That end grain one was so helpful I am eager for more!
Glad it worked well for you. Wish I had a book filled of all the little tricks I know. I wish everyone had a book of their tricks to share…
I just finished my second chair, the irishish design from the stick book. I am very appreciative of all the r&d that is available through your books and blog. A big question I have is I would love to use my local forest for material, however it is all redwood and doug fir. Do you have any experience or knowledge using conifers to build these chairs?
Old growth redwood is excellent. The new stuff it too lightweight and brittle for a chair. Vertical grade Doug fir is excellent chair material. Strong etc. Just a little no fun to saddle. Having a quartersawn seat helps.