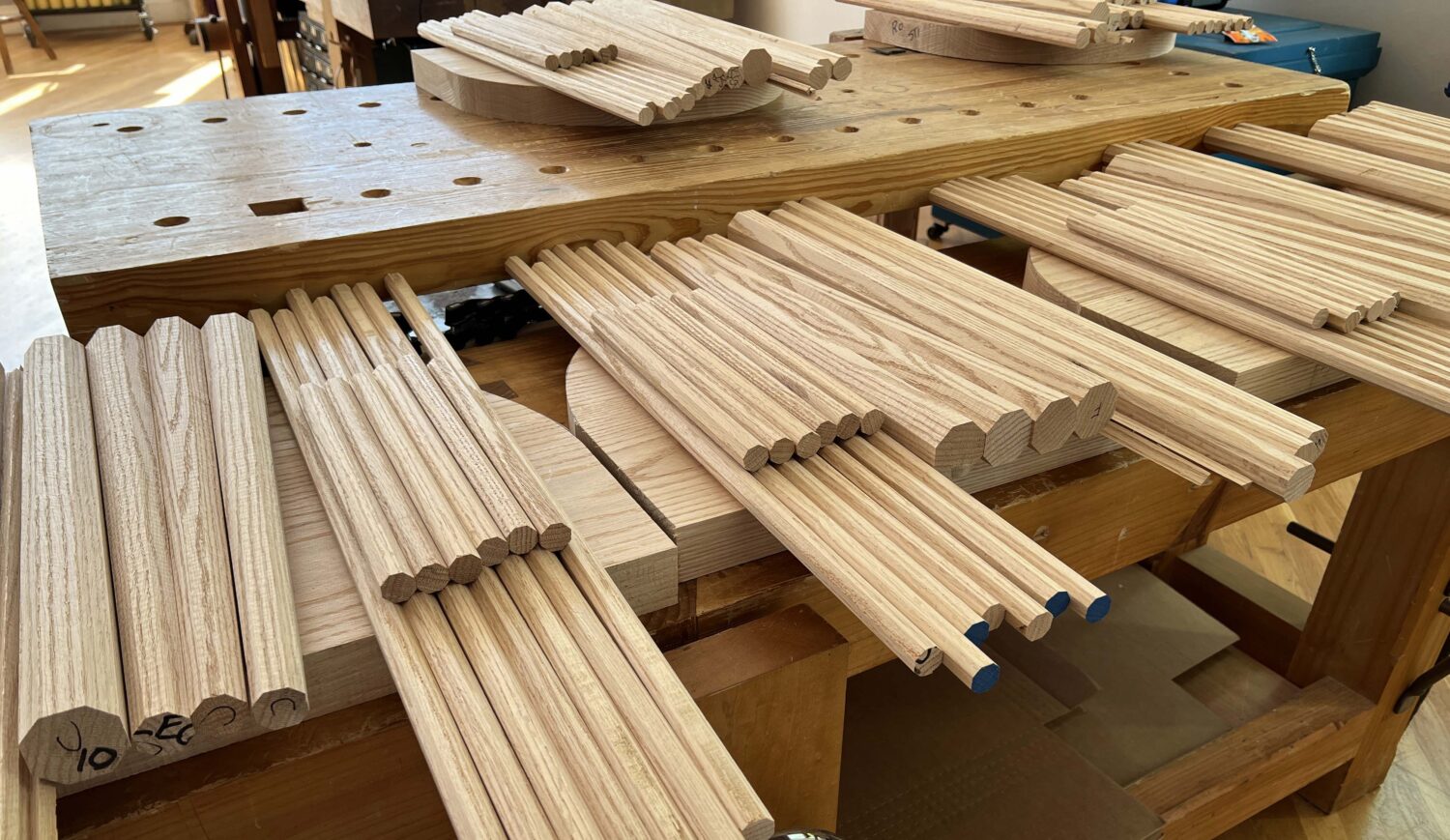
Comments are now closed
Chris is getting ready for a chair class that starts on Monday, and if all goes as planned, I’ll be gluing up panels for a Shaker project…but we’ll be also be online off and on until 5 p.m. to take your woodworking questions. So post ’em in the comments below (as always, brevity is appreciated).
Also, if you’re interested in taking a chair class with Chris, we have two late additions to our Covington Mechanicals Summer/Fall schedule that go on sale Wednesday at noon (Eastern): an Irish chair, Aug. 12-16 and a Welsh-style comb-back Sept. 30-Oct. 4.
– Fitz
Thank you again for doing Open Wire! Question. In smoothing a piece of wood it seems I have at least three choices 1. Smoothing plane 2. 220 abranet wrapped around a cork block 3. Card scraper. Would I choose between them based on what’s at hand or is there a preference for one based on the desired finish?
This question is both cultural and generational.
In the Western tradition, the tradition is to plane the board until you cannot make it look any better. If it has defects, use a scraper to remove them. Then use a fine abrasive to blend the scraped and planed surfaces.
In some Eastern traditions (and in very recent times here in the West) the urge is to use only edge tools – no abrasives.
Either way, the surface looks the same when you apply a finish. So I encourage people to do what their tools, time and desires allow.
Hi Chris,
I’m building an 8′-0″ long French workbench from 150 year old reclaimed 10″x6″ beams that will probably dress down to 9 ½” wide. The top will be 22-23″ wide so three boards required. Could be two full width boards with a thin one in the middle or a full board in the middle and 6½” board each side of it. Your thoughts would be appreciated and given the size of the boards is this an epoxy or PVA glue up?
Thanks and best wishes from Helensburgh, Scotland
I would use two full-width boards and one narrower board to reach the desired width. Then I would arrange the planks so the grain of all the boards runs from right to left (for a right-handed bench; opposite way for a left-handed bench). This will make the bench easier to flatten (either with handplanes or machines).
Then I would arrange the boards into the most pleasing appearance – without changing their grain direction.
Whether you choose epoxy or PVA is determined by how good your edge joints are. If they are furniture-grade and tight, then PVA is ideal. If there are gaps you cannot remove, use epoxy for its gap-filling properties.
I have an oak table top I’d like to use, but it’s a bit shorter than I’d like. I’m thinking about adding breadboard ends to add some length, but I suppose there’s only so much you can add before it becomes fragile, and in any case I would need to cut the tenons on the main piece. Any experience with this? Any idea how much extra length I could add with the smallest possible tenons?
Thanks!
I’ve seen some pretty wide breadboards (8″ to 10″ wide) on old pieces. If you can make tenons that are about 2″ long on the existing table, you can use these wide breadboards.
Some options to consider: Instead of cutting tenons on the end of the top, use loose tenons between the existing top and breadboard. Then you won’t lose any length and the operation will be easier.
Perhaps (even easier) adding drop-leaves to the ends instead of breadboards. Then your changes are reversible and the table will take up less space when not in use.
I’m painting a stick chair for the first time later today, using the method described in Peter Galbert’s book. I’ve been trying to decide whether to paint before or after assembly. Galbert (and I think you, Chris) paint after assembly. John Brown applied finish before assembly. I’d be curious to hear if you have any thoughts on pros and cons here.
My plan for this chair is to apply two or three coats unassembled, then a final coat or two after assembly. The main reason being I can paint the sticks and mortise where they pass through the arm, but also it seems like less fiddling. Then the final coat will clean up any scratches or errors that occurred during assembly.
This is (usually) a British vs. American thing.
British woodworkers tend to finish before assembly. It’s more work (taping off the joints etc.) but you can get beautiful finishes in hard-to-reach areas (the inside of casework especially). Then they touch things up if necessary. Americans tend to finish after assembly. It’s (typically but not always) faster.
I’ve done it both ways, and I prefer to finish after assembly unless there is a compelling reason not to.
Your plane will work fine so give it a go.
Chris for your sharpening video series, can you add the no 80 cabinet scraper? Maybe a quick demo too on how you use it.
Good idea. Just put it on the master list.
I don’t use a No. 80 much now that I own a curved card scraper. But it’s great for large surfaces that need to be scraped. Or to remove paint. I sharpen them the same way I sharpen chair devils, so it’s a good technique to shop in the series. Thanks for the suggestion.
Which bevel direction should a scorp have. I bought an old one and it is bevel down which feels like I would have to really angle the scorp too far down to be effective?
I have seen both. Having the bevel on the outside makes the tool much easier to grind and polish. The bevel is typically very shallow – about 17° to 19°. That usually works with most handle positions. Peter Galbert suggests removing the top arris of the bevel to make the tool easier to use – I haven’t tried this but it makes sense.
Have you found any effective solutions to increase the traction on a wood floor? I put in an oak floor in my shop with just one coat of poly but I find I’m constantly slipping while planing.
Eat more?
I wear grippy shoes in the shop. In time, the poly gets scratched and becomes just fine.
A trick used on wooden boats is to sprinkle silver sand on wet varnish. This gives a non slip grip even on a wet deck.
Chris, have you thought about putting a thin veneer onto a board and then cutting your spell into it, exposing the original wood?
I have not. Will think it over. The effect could be interesting.
When making a bed with mortise and tenon and bed bolts, do you recommend using 8 bed bolts? Or would it be okay/better to permanently assemble the headboard and footboard and use 4 bolts to attach the side rails? Or perhaps I should just ask what is the best way to do it? I suspect the answer is just “yes.”
I used four bed bolts and drawbar the headboard and footboard joints. The only time I would use eight is if the bed had to get through very narrow openings while moving it.
Thank you for the short video on sharpening a tapered reamer with a carbide scraper. My reamer, a 6 degree one, is now sharper than it’s ever been and it takes a fraction of the time using this method.
I’m building a sawbench pair. To reinforce the legs to the base, I pegged each leg with two 5/8″ dowels. I have noticed there are gaps, so I would like to wedge them. I did not kerf the dowels before-hand and now they are glued in place. I have not trimmed the dowels, so they are still a few inches proud. Can I just take a chisel to each in place dowel to create a kerf? It makes me nervous because everything is already together…
Thanks so much for these Open-Wire Saturdays!
Just split the peg with a chisel. Then add glue and a wedge.
You’ve sold me on the idea of soft wax. Unfortunately Katherine’s is not always available: can you recommend a back-up?
Odie’s Oil and Tried and True both have similar finishes. Or make your own. The recipe is on the blog and is quick and easy
Just make some! It’s REALLY easy and much cheaper than buying it, and you’ll end up with a lot more. Plus, it is incredibly satisfying to make your own finish and then use your own finish. The venerable Mr. Schwarz has made the recipe and process readily available all over the LAP multiverse.
If you’re capable of woodworking and/or making pancakes then you certainly have what it takes to make soft wax. Now get to it!
Thanks for the +1. If you want to make it easier to scoop out of the jar, double the limonene/citrus solvent in the recipe.
I’m building one of the chairs in ADB and am at a loss for what to do about the crest rail. I’m on the West Coast so all the oak is kiln dried and the firewood bundles are almond or coniferous woods. Any thoughts on what to do if steam bending looks unlikely?
Just saw the crest from solid wood. It’ll be fine.
Thank you for hosting these! I didn’t initially put a lock on my Dutch tool chest, but now I’m going to need one. Is there a commercially available hasp that you recommend?
Maybe Megan can recommend an off-the-shelf solution. I usually ask a blacksmith to make one. They can be very simple — a hinge and a staple.
Well I do love this one from Horton Brasses: https://www.horton-brasses.com/HSP-4.asp (pricey but fabulous, and blacksmith made). But if you want a less expensive option, I’d haunt the etsy ironongers, or try Van Dyke’s (https://www.vandykes.com/3-1/8-trunk-hasp/p/203533/)
For a walnut chair: oak wedges or walnut wedges? Or is it purely a design choice?
You might get away with walnut wedges. You might not. I always use ash or oak wedges with dead-straight grain because those are the strongest.
I’m making the Japanese Sliding lid toolbox, and it’s my first time cutting finger joints. Any suggestions on getting the bottom of the notch less lumpy and more…bottomy?
Hi Patrick, Chris wrote about hand-cut finger joints here: https://www.popularwoodworking.com/wp-content/uploads/SlidingLidBox.pdf
But what you really want to know is how to get a flat bottom – and one solution is to clamp a “paring block” at the baseline – a flat piece of wood to guide the chisel for a perfect 90 cut.
Thank you, I’ll try that!
Hi Chris,
What are your thoughts on cutting a leg’s tenon shoulder so that it sits flush against the seat bottom? I’d be using the Veritas tenon cutter.
-John
I do it all the time. Coping the shoulders makes for a neat look and improves the strength of the joint.
Howdy folks. My basement flooded and my copies of The Woodworker’s Pocket Book and Doors & Window-Making were ruined. Would it be possible for you to link me to a PDF version? Or if you have any “factory-seconds” for me to purchase? Thanks
Hi Chris and Megan! What is your top choice of wood to build casework with?
That varies tremendously on the design and finish I’m hoping to use, as well as the type of casework (e.g. bookshelves need to be able to support heavy weight over X span). But let’s say it’s going to be painted: Pine or poplar. Clear finish on a Shaker (or Shaker inspired) piece: cherry – or walnut (if my pocketbook can handle it). Arts & Crafts: likely white oak. (And I should mention that I mostly use native species that are easily available in my region.)
If it’s solid wood, I love walnut, cherry, maple, white oak – pretty much all the native hardwoods – for the primary wood. And white pine, basswood or poplar for the secondary woods.
I don’t use much plywood these days (thank goodness because it is so terrible now).
Hello! Lateral adjuster question, especially on cheap versions of #4 (‘handyman’ series, ‘crafstman’ copies, etc.). The ‘rivet’ that is supposed to hold it is loose and cannot be punched further (already mushroomed from previous users or even poor factory assembly).
You can hear the lever click around and the blade changes position when planing, especially when changing direction or encountering a density change in the wood. Tightening the lever cap screw helps a little but not much as it causes difficulty in depth adjustment….
What could replace the rivet after drilling the old one out?
Thanks and have a nice day!
The lever flopping around shouldn’t be enough to change the position of the iron. It sounds to me like your iron isn’t bedded sufficiently against your frog and is moving too easily. You might want to look for humps on the frog or on the underside of the iron/chipbreaker assembly. The iron shouldn’t move unless you want it to move.
So address that first.
Once that is taken care of, the floppy lever might not be a problem. If it still makes you nuts, drill out the rivet and use the plane without the lateral adjust lever.
Or drill it out and replace it with a copper rivet or something easy to peen.
Good luck!
Sharpen a slight curve on the cabinet scraper blade so that it disappears into the body of the thing just on the ends. Don’t need to over think it. Just get a burr on it. I also put a slight angle on it.
Hey there. I just got an old 12” Delta planer and noticed that is planes the first 3ish inches slightly thinner than the rest of the board. Not sure what is causing this or how to fix it. Thank you very much for your time.
This is called snipe. It can be caused by a variety of things. Usually the bed rollers are too high or the feed rollers need to be adjusted. You can usually minimize it (but not eliminate it entirely).
Search for the manual online. It will tell you how to adjust the rollers (if they are adjustable…. some portable planers are not adjustable).
I’m curious – if I have say a 3/4” dowel going into a 3/4” through hole, paint both the dowel and the hole with glue, and assemble, I’d be damned if I didn’t think that all the glue sits on the outside surfaces. On a tight tight tight joint like that, do you know the thickness of the glue that actually adheres?
On a blind hole, I often chamfer the leading edging of the dowel to get a straight start on the fit. Similarly, I feel that the glue either sheds off as I seat the tenon, or the glue just sits in the negative space of the chamfer and the hole. Too much glue, and even might sit 1/16” off my line because the glue in the bottom.
My question overall is what is the minimum glue thickness for a strong joint, and how do you validate that on really tight fits other than hope and experience. I certainly can’t break the joint apart, so there must be enough, but I do wonder the science behind it.
You can scrape off most of the glue if the fit is too tight. But glue immediately absorbs into the wood (that’s the water in the glue at work). So in tight joinery, that little bit of glue is usually enough. You don’t need a lot of glue in a tight joint.
I don’t have numbers to give you. If you want to dive into that you should try to get in touch with the glue technologists at Franklin International who study this sort of thing.
From a practical point of view, you have to work at it to starve a joint with a tight fit.
As far as worrying about the glue at the bottom of a mortise, don’t. Glue is 40 percent water. Most of it will get absorbed into the surrounding wood – one way or another. Again, you have to work at this to make the glue not work.
If you are concerned about the fit being too tight, paint a thin coat of hide glue on the tenon. Let it dry. Then paint wet glue in the mortise and drive the joint together. The wet glue in the mortise will activate the dry glue on the tenon. (This idea came from Jeff Lefkowitz).
Sorry I’m not a glue technologist.
“From a practical point of view, you have to work at it to starve a joint with a tight fit.”
I have felt like that trace “skin” amount is what it takes, thank you.
This is a gem there, as I’m really just concerned with the practical bit, although I do, in my wandering moments or insomnia moments, think about the thickness and shear strength, I’m really mostly just an “in actual practice” guy,
Just my 2 cents. You have to remember that you are working with wood. Compared to a metal, wood is much more forgiving and is also relatively porous. It’s the pores that help with adhesion. The pores also allow the wood to adapt to the requested hole size. Metals can’t be squeezed as easily and are more difficult to glue. (E.g. steel would require clearance between the pin and the hole, and would need a weld)
Good morning.
I am moving forward with my first stick chair build and using your video on TWW. Since I am unable to attend a class, this is the next best thing to being there. My question is concerning dowels. I live in an area where it seems that if I want hardwood dowels, I can pick from poplar or poplar and none seem to have a grain structure that would work.
You recommended Midwest Dowel as an option and I am asking if I purchase from them, should I get a couple extra per chair?
Thank you very much for your time.
Midwest Dowel does good work. You might want to call when you order and tell them that you need dead-straight grain. And order a couple extra for your chair as well.
Will do. Thanks
What are your thoughts about using a sawdust and hide glue mixture instead of Timbermate to fill small surface imperfections with dust form the same board? This is for a red oak tabletop that will be finished with Tried and True. Thanks as always for being generous with your weekend time!
I have not found that to absorb any finish – so just be aware that it might draw more attention to fill it than to leave small imperfections.
Good day! I’m slowly gathering materials to build an AWB. Is the benchcrafted classic leg vice hardware still your recommended route? Thanks!!
Yes! With the criss-cross is the best setup ever.
Maybe I missed it in the stick chair book but, how do you decide where to leave the shoulder from the tennon cutter on sticks and where to shave down and remove it?
With sticks, it’s aesthetics for the most part. A shoulder gives you a hard stop when you are driving the arms and sticks together. That’s a minor difference. The tendency now (style-wise) is to remove the shoulder. But it hasn’t always been that way if you look at the furniture record.
So do what you like. You might have to adjust your mortise depths if you remove the shoulder. But that’s a minor thing.
My just-finished-in-humid-California-January bench is starting to change as the weather dries out (though it’s raining today). In particular, the planing stop has started falling out! You mention (in AWB?) shimming with veneer … the mortise? The block? It seems that the block is slightly worn/compressed smaller at the top (not surprised) so maybe just a few strips of veneer tape there?
Thanks, as always.
I would add a plane shaving (or thin veneer) to the block…but make sure you don’t make it so tight that it then sticks in winter (as I might have done on my bench…)
Thanks – a couple of pieces of blue tape are doing the trick for now, so it shouldn’t take much.
Do I need to scrape the BLO off to get glue to work? Is this one of those “if you have to ask, you already know the answer” questions?
Yes. Oil repels the water in glue (both hide and PVA).
The same thing happens with the planing stop in my bench – too loose in the dry, Belgian winter, and just right at the end of summer. I just add and remove as many layers of 2”-wide masking tape as needed to fit the season. The only thing is to not forget to check when EMC starts going up in the summer – I once had to hit that sucker purty dang hard to get it out when I’d left too much tape on for too long.
Good Afternoon,
Thank you both for answering questions again today. I had a question about what you would recommend for routine vise maintenance. I have noticed that my “moving block” style tail vise has started to get rather stiff to screw and unscrew. I didn’t know if this is typically just a matter of regularly lubricating the screw or if there are other considerations.
Thank you,
Jacob
Vises become stiff due to three things:
When I do maintenance on a vise, I first clean the screws and then add a very light machine oil. If that doesn’t fix things, I look for binding/rubbing. If I can’t find any, I take the vise apart, clean up all the pieces and then look for rub marks etc. If you find rub marks, plane them away.
That always does the trick (unless the whole mechanism is sagging….)
I really appreciate the feedback and direction on this, thank you.
Another pesky leg tenon question. How long should I cut the leg tenons for a Gibson with a full 1 3/4″ seat. I’ll be using a Veritas tenon cutter and coping the shoulders. The seats will likely be shallowly saddled. I plan to do a couple tests with defective legs and 8/4 offcuts but I thought I’d ask so I don’t do something stupid.
I tapered legs for 5 chairs and found that it was much easier to do by using blocks and a sheet of plywood to create a standing platform 9″ off the floor. That way I could use my legs instead of my shoulders to push the jackplane through the wood. I also mounted my carvers vice as close to the front edge of the bench, the feet are a half inch back, and midway between the legs. With the vice rotated 25 degrees, according to my Bevel Monkey, I can stand over the vice without my hips hitting the bench and access the leg from each side of the vice. I also put a reference pencil line on the leg where I wanted the widest part to be, centered the leg in the vice, and put another reference line on the vice jaw that matched the reference line location on the leg. Each time I rotated the leg in the vice I transferred the leg reference line to the previously planed face.
That should be vise not vice. Apparently I’ve been reading too much news.
The tool is spelled “vice” in English, except in the US.
(Like “defence”, “colour” or “rebate”).
So many pun possibilities!
I usually make my leg tenons 3″ long, and that seems to handle almost all chairs. Better too long than too short. You could draw it out full-size on paper if you are worried about material. But I always make my legs overlong so I don’t have to worry about that.
Good luck! Sounds like quite the adventure.
I have a walnut veneered dining table thats seen a lot wear and tear. I believe its original finish was oil. If I want to freshen it, could I just wash it in soapy water, wipe it down with citra solve, let it dry and re-oil, or would it be better to also sand it down lightly? 220 grit ok? Thanks for all you all do!
If you wash it with water, there’s a good chance that you will raise the grain. If it’s an oil finish, you can scrub it with mineral spirits – this will loosen the old oil and grime – without raising the grain. Then you can apply new oil.
If you do want to wash with soap and water (nothing wrong with that!), then you will want to lightly sand any raised grain before applying oil.
You’re coming to Germany soon! Your thoughts on German vs US beer?
Slightly related question: in German your name “Schwarz” is pronounced the same as “Schwartz” (German letter “z” is pronounced like “ts”, just like in “pizza”).
Do you care much either way when English or German speakers pronounce your name?
I love German beer’s perfection and consistency. A good Weissbier is hard to beat. I love e Americans’ willingness to experiment. I have had some transcendent beers in my life.
I answer to any pronunciation of my last name. Growing up in Arkansas I heard some wild interpretations: Worts is my fave.
I got out my Lucian Avery inshave to tune it up using the process in your Sharpen This video and it struck me that the nice very dark brown, almost black, finish on the handles looks like it would be nice for chairs. Lucian says he burns and oils them. I’m going to give that try plus a bit of wax/oil on red oak. Have you experimented with burning as a finish?
Oh sure. Good for handles. Not so good for things with joinery and glue.
You can touch up any areas that don’t burn well or recede by feathering in appropriate paint and/or tinted glazes before oiling.
Regarding the walnut dining table and oil: I’m in california. No mineral spirits. Just “paint thinner” with acetone in it. Would citra solve be a problem? Thanks again.
It will probably work fine. Just a bit slower.
If you were to recommend hand-tool woodworkers to meet or study with in the Missouri-Arkansas Ozarks, who would you recommend? (Besides Mark Hicks, whom I fortunately will have the opportunity to meet and study with.) I’m focusing on cabinetry, though I also will study chair-making (with Mark). Thanks again for everything you all do for the craft!
Owen Rein in Mountain Home is a fantastic chairmaker and basket maker. I worked with him while I was at PW.
http://owenrein.com/
Get to meet Doug Stowe.
https://wisdomofhands.blogspot.com/
I don’t know Missouri as well. Sorry.