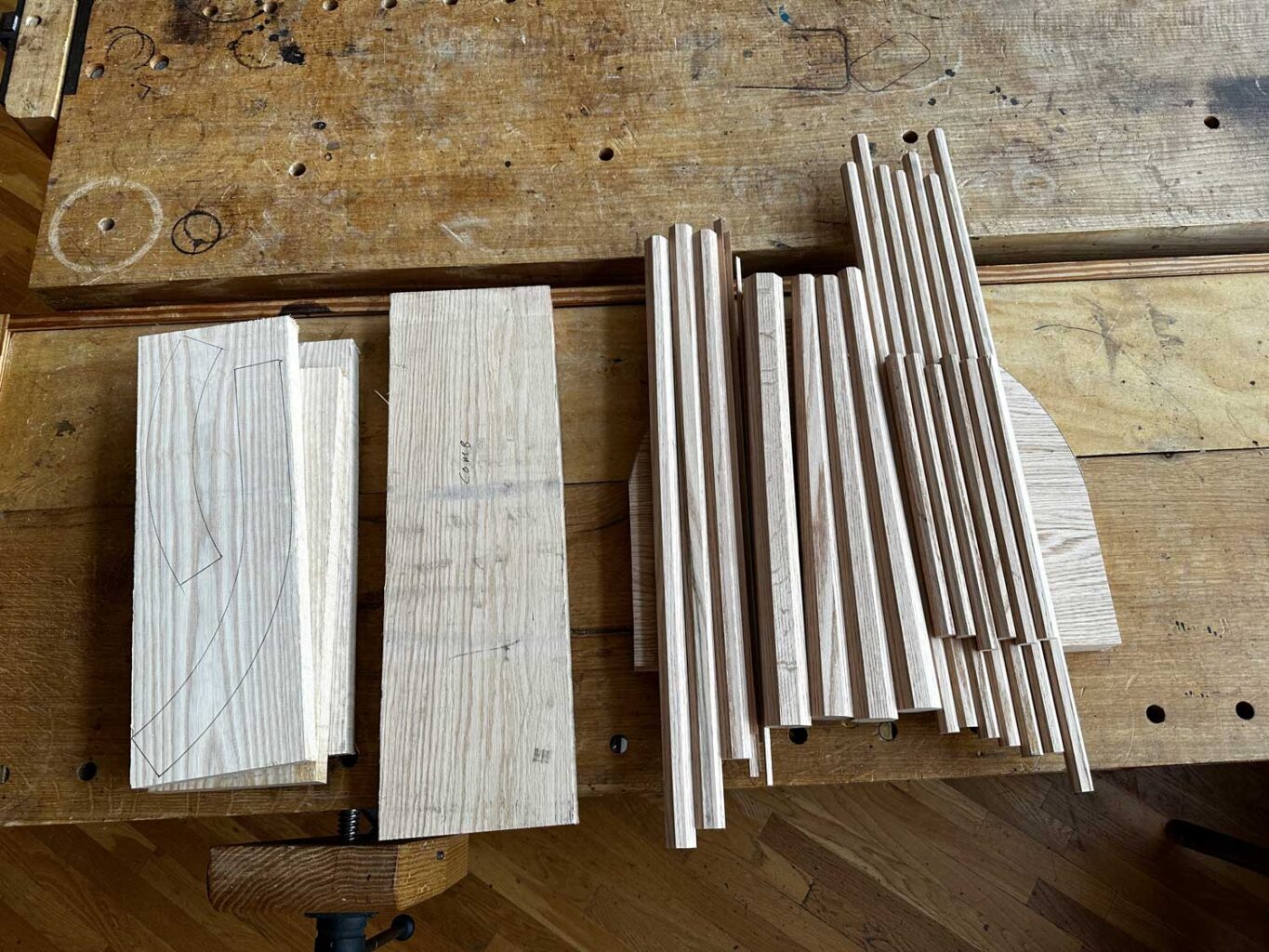
Several people have asked my permission to teach classes in making stick chairs using my designs.
My answer is always: Please do. All my designs I give freely to the public for any purpose, including commercial uses. My book on the topic, “The Stick Chair Book,” is a free download for everyone (you don’t even have to register or give away your email).
So here is what students find on their bench when they start a five-day class in making a stick chair. After years of teaching these classes, we’ve struck a balance between “too much Donkey work” and “not enough Donkey work.” We call that balance: Donkey work.
If you want to teach a class of students (or just your neighbor), I hope this is useful.
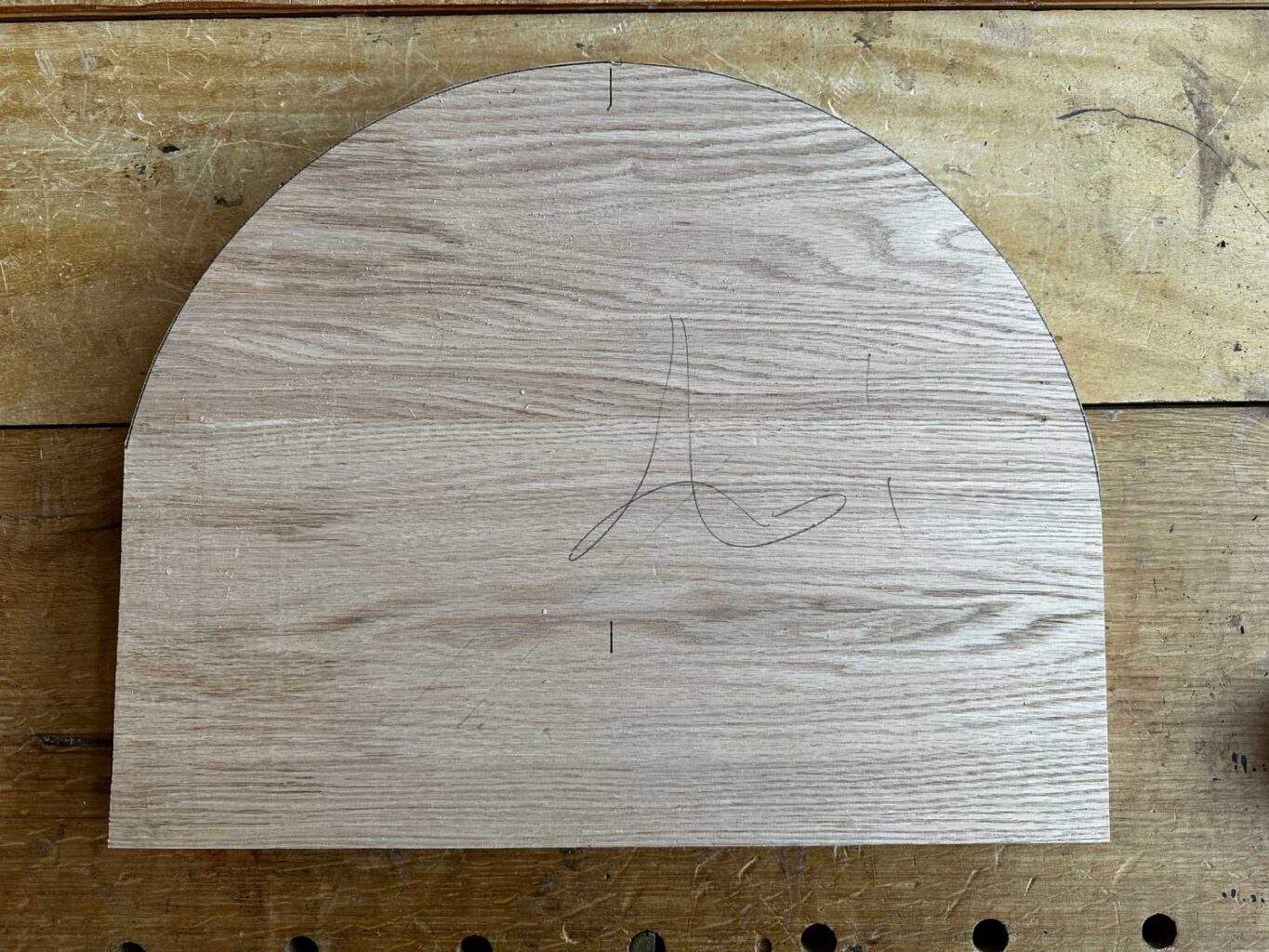
1 Seat: 1-3/4“ x 16″ x 20″
The seat is glued up and cut to shape on the band saw.
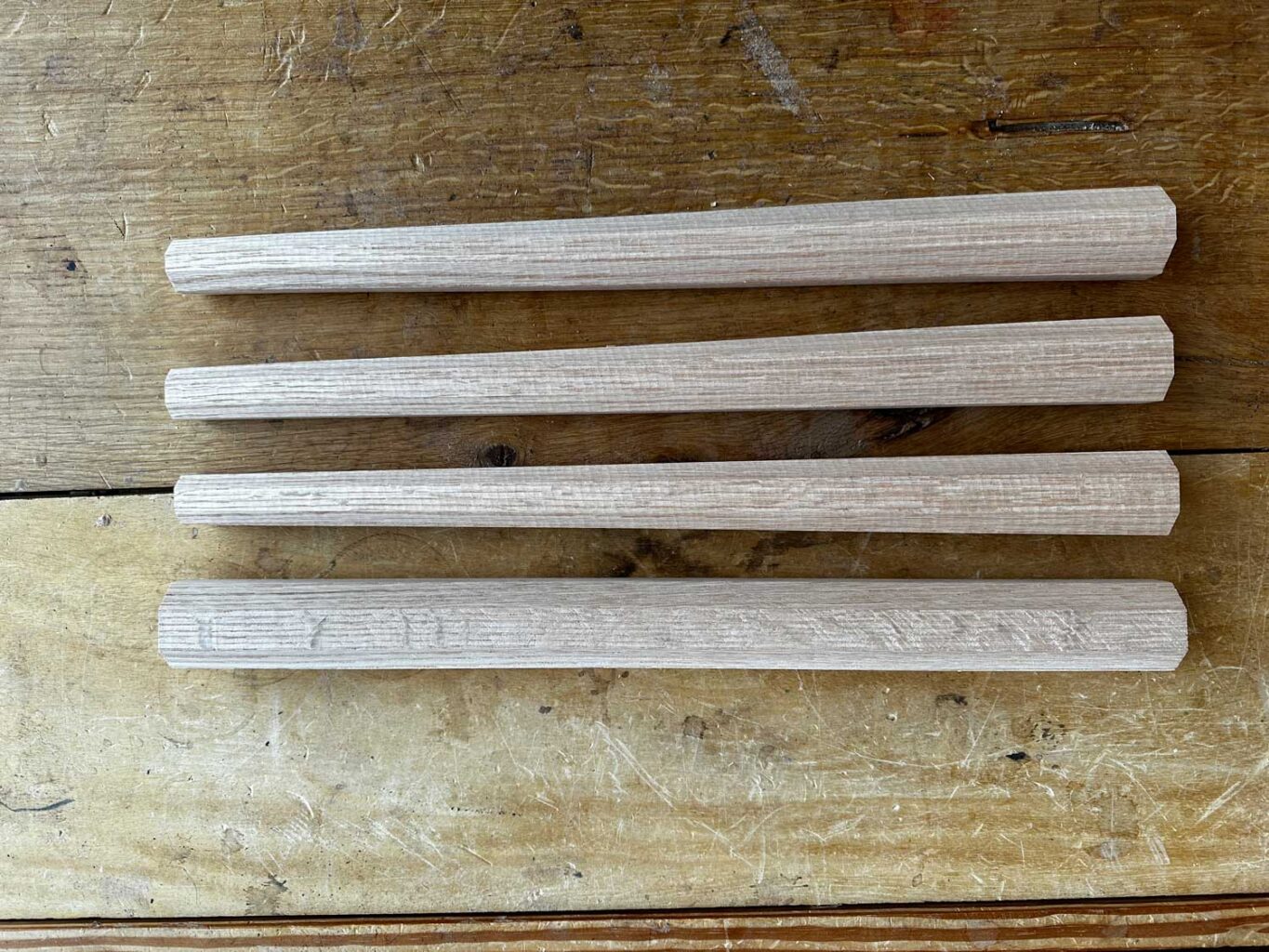
4 Legs: 1-3/4″ x 1-3/4″ x 20″
All four legs are octagonalized. Three of them have been tapered. Students will taper the fourth leg using a jack plane. All four legs need tenons, so there is lots of work there.
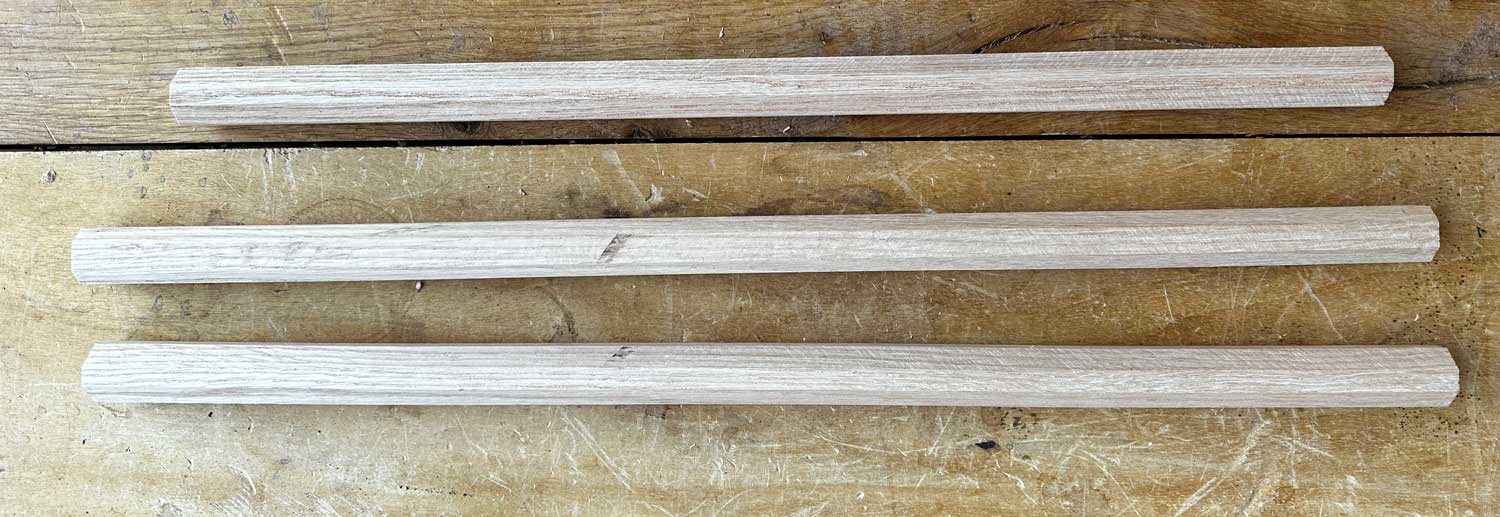
3 Stretchers: 1-1/8″ x 1-1/8″ x 27″
These have been octagonalized. They are overlong (way overlong) because the stretchers are the students’ first encounter with a power tenon cutter. So they practice on one end of the stretchers until they get the hang of it.
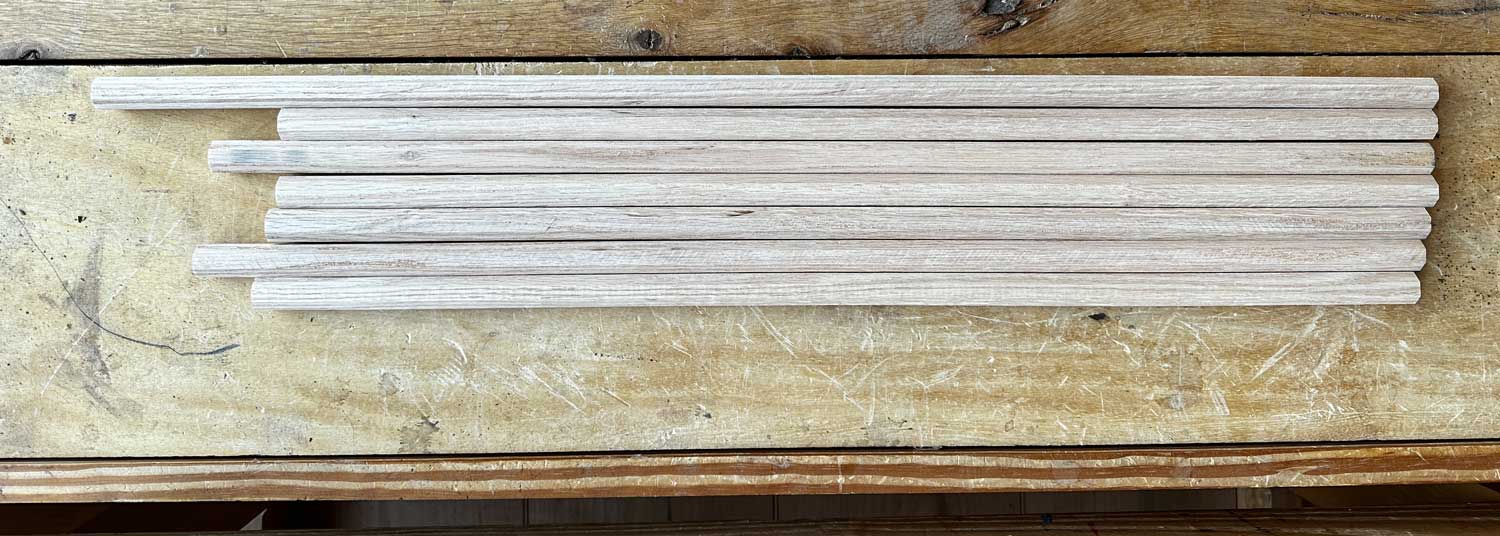
7 Long sticks: 3/4″ x 3/4″ x 27″
These have been octagonalized. Seven sticks allow for a wide variety of comb-back designs. And their lengths permit students to make anything from a Shortback chair to a too-tall comb-back.
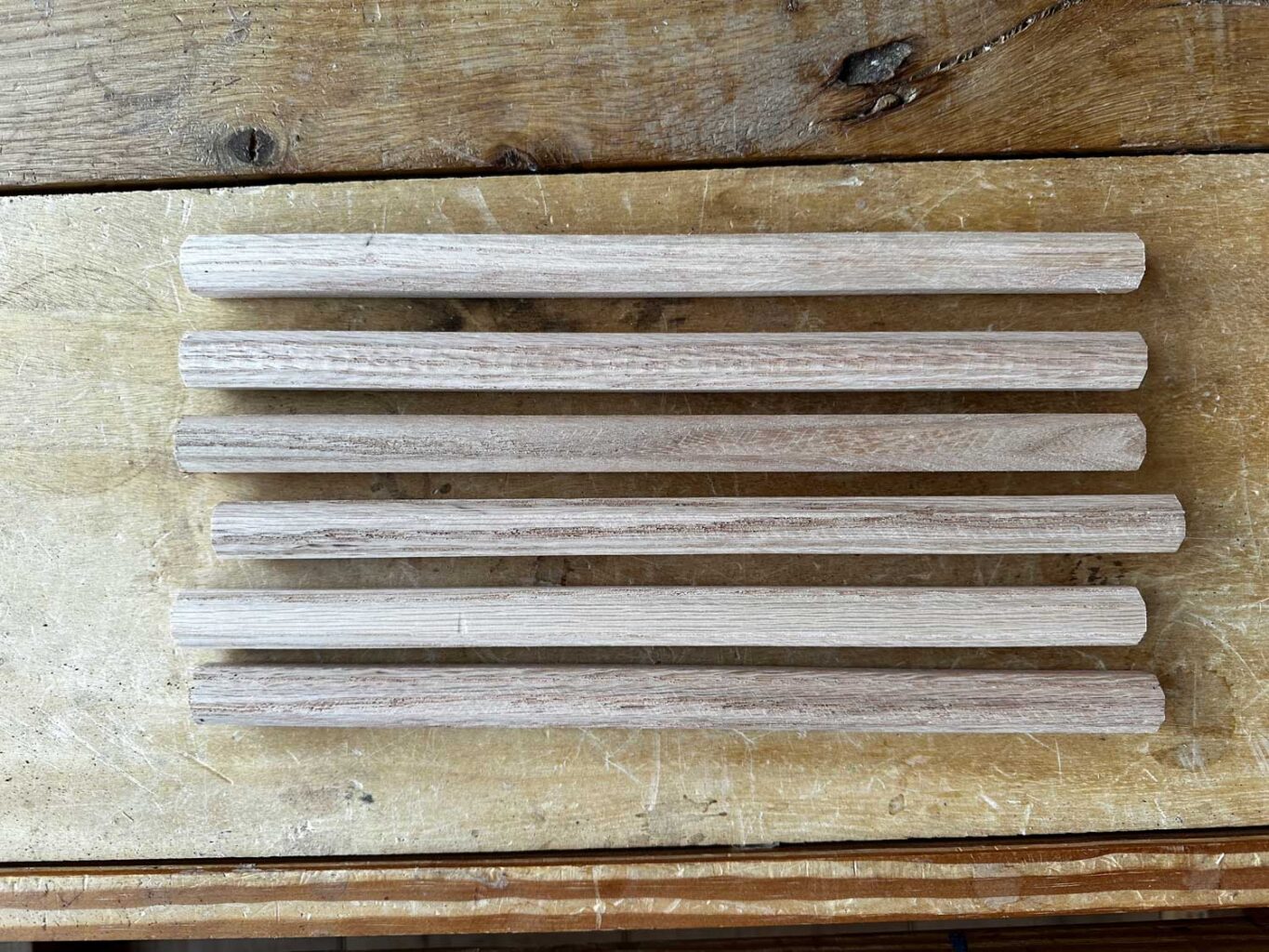
6 Short sticks: 3/4″ x 3/4″ x 12-1/2″
Our tenon cutters make a 2-1/4″-long tenon, so these lengths create a short stick with two tenons that can be trimmed (or not) to do lots of things. They can go through the seat if the students wants. They can be proud of the arm. They can also be used in a lowback chair (which requires a long tenon for strength.
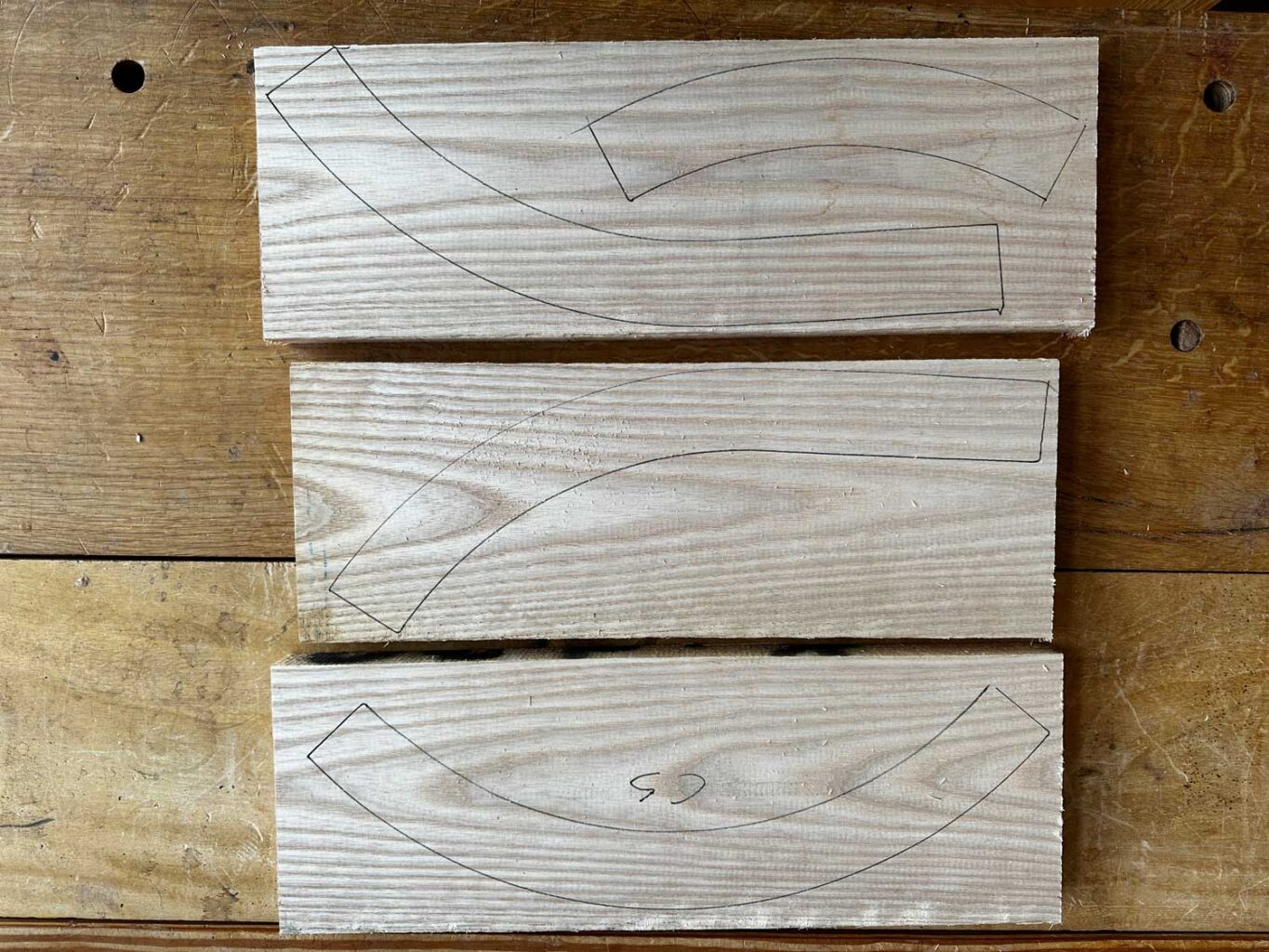
3 Arm pieces: 1″ x 8″ x 20″
These three hunks of wood allow for a four-piece arm that can be wide or narrow. And they accommodate a variety of hand shapes.
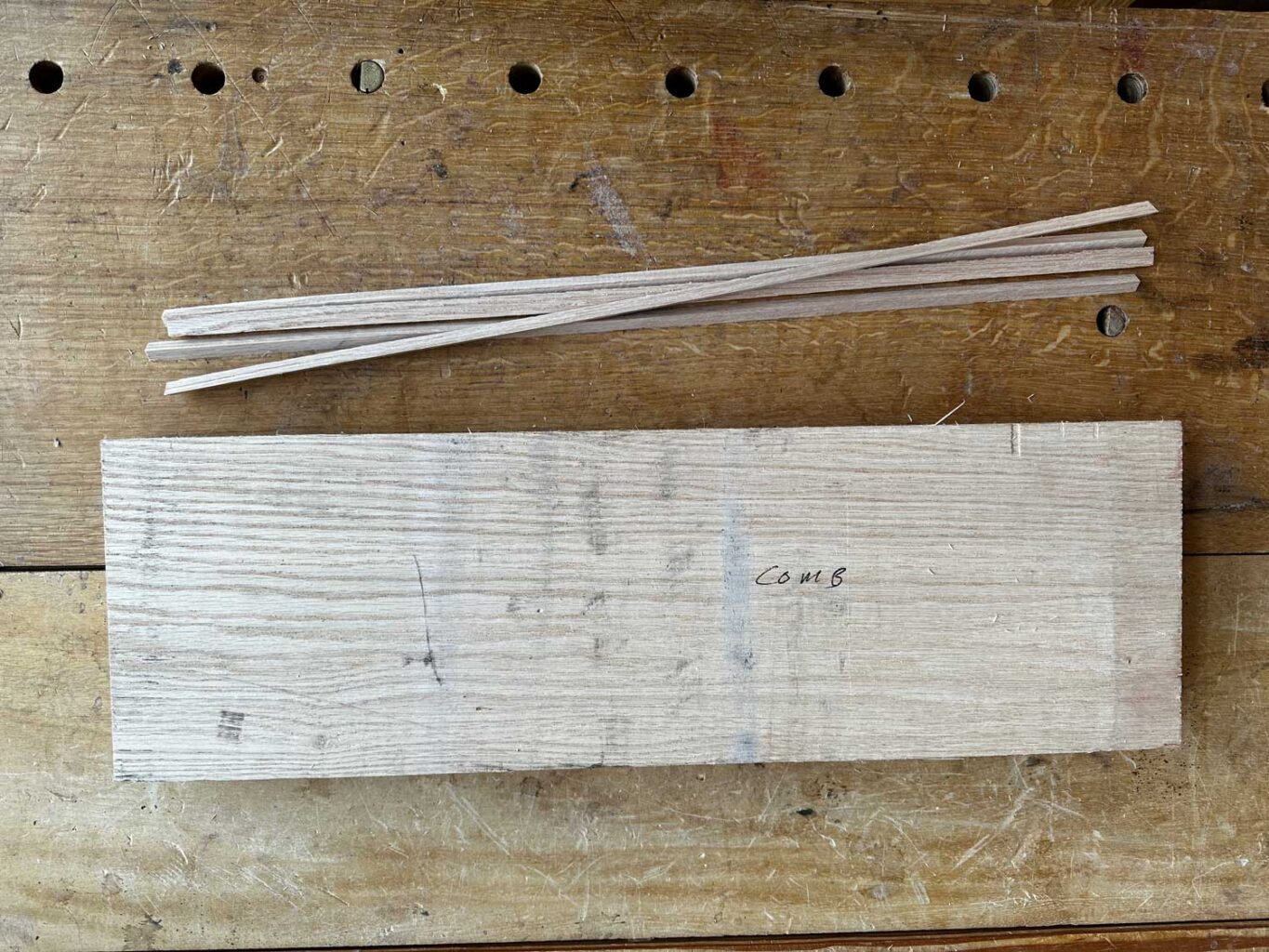
1 Comb: 2″ x 8″ x 24″
This chunk of 8/4 is enough for a student to make two combs to experiment with.
4 Triangular scraps (off-fall from octagonalizing the legs)
These scraps help us measure the length of our side and medial stretchers (this is covered in the book in detail).
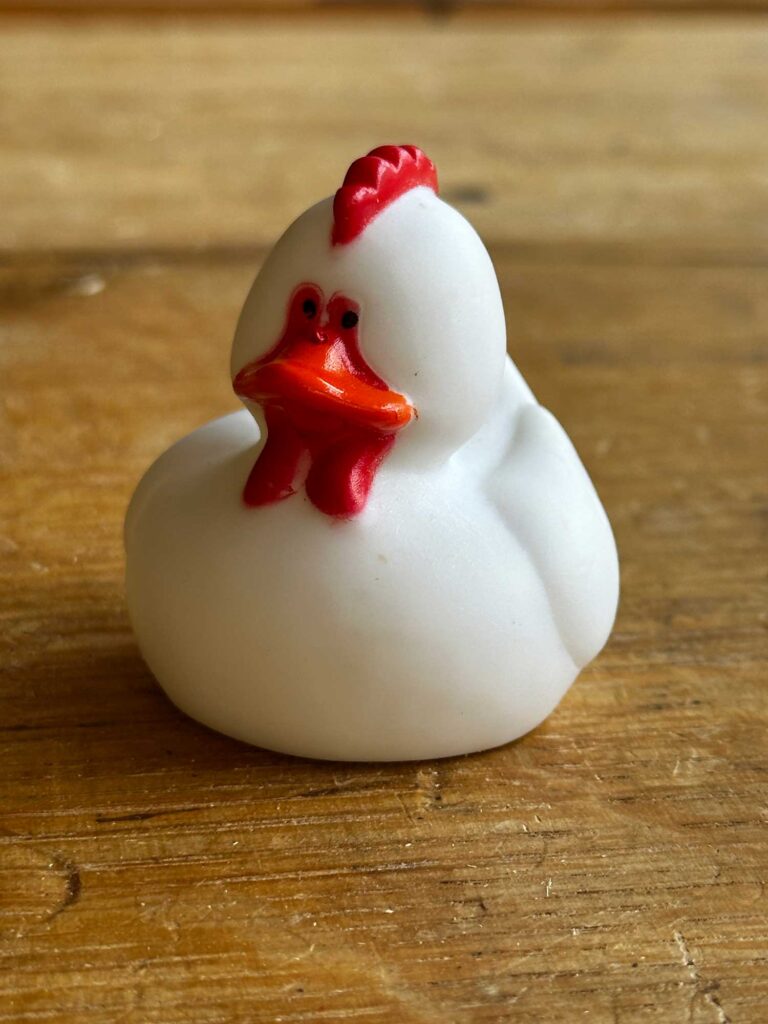
Oh, one more thing for the bench: Usually my daughter Katherine leaves each student a squishy power animal to help them through the week. Never forget your power animal when chairmaking.
— Christopher Schwarz
Now I understand my squishy little green frog!
Thank you for this.
I got this notification email as the full post. No more digest emails for me
We are gradually climbing out of this hole… almost there.
Mine are still digest, that said, I don’t mind clicking the link to get to the full post.
We are still working on that….
If you give a man a stick chair you seat him for a day. If you teach him to build a stick chair, you seat him for a lifetime.
Incredibly generous.
You put a ton of work into these chair kits. Tapering all those legs! There are probably children sewing sneakers in Malaysian sweatshops making a higher hourly wage. But I can see how it makes for a much better class. I’ve seen them where you spend a day, waiting in line, to run rough lumber through a planer. Speaking for myself, I don’t need a class in that.
You and your team are doing a great service to the woodworking community!
How many neophytes continue on to make more chairs on their own because of your influence? Last weekend I went to a local Woodcraft store for a small woodworking show. It was all about hand tools and very well attended. It gives me hope that the craft will not be lost.
It impresses me that there are still people who are interested in helping others and not just getting the last penny out of everything. Thank you.
Is there any reason that you glue up a panel for the seat. Is it just easier or cheaper than buyting the wide stock?
When I can get 16″-wide boards I make a one-board seat. Usually I cannot. Many stick chairs had seats made from two or three boards.
I don’t know anything about your chair design. I made a chair with Curtis in 2008 at Highland Hardware. I love the class and like the chair. However, I like your posts more. Continue the rant or share or whatever.
Thank you.
Daniel Johnson
Thank you for this information and guidance, Very generous.
Wow, I didn’t get a squishy.
Fixing that in 5, 4, 3, 2…..
Thanks for sharing this, much appreciated.
I love my squishy spirit animal.
Are the squishy spirit animals for rubber ducking furniture making problems? Following “The Pragmatic Programmer”, I keep a rubber duck nearby to debug code by reading it line for line and explaining it to the duck. I’ve used the duck for coming up with woodworking solutions as well.
How do you taper the legs for a class on a production basis?
https://blog.lostartpress.com/2023/07/11/cut-leg-tapers-by-machine/
My squishy animal now reminds me to detension my bandsaw when I’m done with it. If you would like to scold her for doing something so pointless with her life, I will drop her in the mail wth a SASE.
Somehow, seeing photos of all the different raw parts that go into making a chair gives me a better idea of what timber to source than a printed list of timber to buy – weird.
Regarding the “power animal”. It reminded me of the bedtime stories I told my kids about the legendary “Super Chicken” when they were little!!
Chair making squishy power animal, aka “totem stress ball”. Love it all.
I spent over a decade teaching seminars at a bunch of Lee Valley stores: One of the classes was a chair class, from my own design (with a bit of Jeff Miller’s inspiration 🙂 , and one of the classes was a staked stool class, inspired by Chris’ work.
For both seminars whenever I taught them, wherever I taught them: students arrived to a pile of pre-prepared parts : its absolutely essential to provide students with an effective starting point.
That being said: I never thought of the squishy toy !
What I loved, when I started to play with the staked stools: was how nice that Chris had made it easy for others to understand his journey on the design: it helped me figure out how I wanted to inspire people to make similar stools.
One of my favourite memories is from teaching at one of the Lee Valley Toronto stores: a ‘squadron’ of staked stools: and not one of them is the same: each student took the parts provided: and then ‘made it their own’. Every time I taught the class: not a single student ended up with exactly the same stool or chair: it was magnificent. I just wish I’d remembered to snap pictures over the years.
One of the best things that any of us who have a bit of woodworking skill can do ? Teach others. Even if you’re shorter on skills? help someone get started.