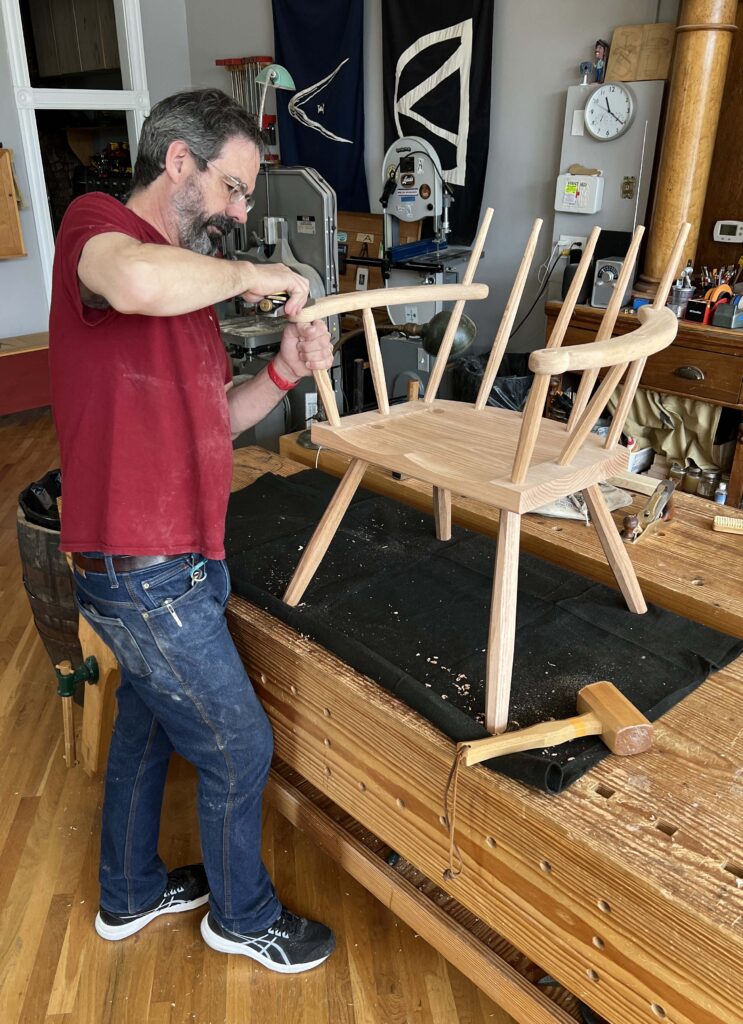
Update: Comments are now closed.
Chris should be done with the chair above by the time you’re reading this. As I write and schedule this post, he’s doing the “make pretty” on the arms, legs and seat, and the backrest will be installed by lunchtime. Then he’ll spray a coat or two of shellac and rub on a coat of black wax…then decide he’s unhappy with that look, strip the wax and do a few tests to find a paint that will cover it. If that’s successful, he’ll spray the paint, and hopefully get two coats applied before it’s time to head to the bar. It’s Friday; on Fridays, we go to Crafts & Vines.
If the spray approach doesn’t work, I’ll be wear painting togs Saturday, with my brush in hand.
All that to say Chris, and possibly I, will be available to answer your woodworking-related questions. Please leave them in the comments below. And please know that if the question – or your response to our answers – is longer than the preamble to the Constitution, we will glaze over and be mildly annoyed. And we will roll our eyes in your general direction. “Brevity is the soul of wit,” said Polonius. And while in his mouth those words are ironic, he’s not wrong.
– Fitz
p.s. The chair will be posted for sale on the blog just as soon as we get the blog fixed (assuming Chris is happy with the finish by then). No one is getting the RSS feed or notifications right now. It is vexing.
What’s your favorite Wilco album?
“A Ghost is Born.” Tweedy had to play al the guitar parts. And was suffering immensely from an addiction to pain pills. The result is a document of someone who is working at their physical and mental limits. I would never wish his situation on any artist. But he should be proud of what he produced.
I think I have to agree with this, and was happy to see that Wilco has been playing 5-7 songs from A Ghost is Born at every recent show, more than from any other album.
For any Ghost is Born fans, I would recommend a trip to Philly (Ardmore, where certain Amtrak trains from NYC stop) to see some excellent local musicians celebrate the 20th anniversary of the album.
https://ardmoremusichall.com/seetickets-event/philly-loves-wilco-20th-anniversary-celebration-of-a-ghost/
I don’t have Campaign Furniture to hand. What was the finish used on the original pieces and what does Chris use now? Thank you!
Shellac and wax on most pieces that I’ve seen.
What is the best way to strip a wax finish?
Mineral spirits removes wax. Flood the surface with one rag. Scrub and wipe with the other.
Good morning- I’m in the middle of building my fourth Stick Chair. I’m using ash for the legs and sticks and I’d like to ebonize them. In the past I’d always used Minwax stain but I’m trying something new where you put steel wool in a jar filled with distilled vinegar covered for a few days where it’s supposed to break down the wool and create an amber color. Before applying, depending on the species of wood, you’re supposed to add tannic acid to the wood and then apply the vinegar/steel wool concoction. It’s supposed to be a safer application than dealing with stains, etc. Have you guys ever tried this before? And if so how did it come out? I read it’s a much richer darker finish. Thx!!
I have used it a couple times and haven’t been particularly happy with the results on red oak. It was almost impossible to get the vinegar solution into the pores. And the color (even after a few applications) wasn’t what I would call ebonizing. I know Andy Glenn uses this process with great results, so I need to talk to him next time I see him. Sorry I don’t have. abetter answer.
I’ve had good success on smaller pieces of oak (picture frames, specifically). What worked best was not leaving the steel wool in acetic acid for too long, leaving the solution almost entirely clear. Three to four days worked best. Keeping the steel fully submerged (with a magnet underneath the glass jar) also helped. Lightly sanding all surfaces helped tremendously. My planed surfaces did not take the stain at all. As Chris said, open pores can require some patience.
I also tried it on ash, which turned slightly brown, not black. There are recipes on the web which use various types of ground tree bark in addition. I’ve heard that they work on ash as well.
If you’re shooting for jet black, rather than the slate tone you get from iron tannate, go for India ink.
I used black Fiebing’s leather dye and it worked wonderfully.
I’ve had success with India Ink. Paint it on, let it dry then seal it with shellac or whatever.
I have done the tannic wash (strong oak bark tea, 2 or 3 applications, allowed to dry between) and ebonizing with vinegar/iron solution (2 or 3 times, allowed to dry between). It worked quite well on white oak.
The method I used was described in Richard Maguier’s “Industrial Desk” video series and mine came out as dark as the one on his site.
It’s so nice of you folks to do this. It’s a big chunk of time for such busy people.
I wish I had a question. Even a dumb one.
How would you like to be a guest on an Open Wire day? You know all this stuff. It would be great for readers to hear another perspective.
Sure! I’ll start looking up synonyms for scatological.
You’ll be hearing from us!
When talking with the backwoods chairmakers, ask them if they are content, or always trying new approaches.
How long did it take colonial woodworkers to complete a typically project for a customer? I know they didn’t work 9-5 and with different labor laws but were their shops open for certain times of day and they just work all day/night?
We know the answer(s) to this question because of the published price lists. These lists detailed the amount of time each operation should take and what the woodworker should charge for it. Start reading about the 1772 Philadelphia price list here:
https://archive.org/details/1772philadelphia01unse/mode/2up
This book answers a lot of the questions you likely have.
Did you change the blog software? The emails now only contain part of the post. They used to have the entire post.
We are experiencing a massive problem with our DNS records. The technical efforts to fix them have wreaked havoc with all aspects of the blog.
We have not changed to emailing out a digest. But some people are getting only a digest. Most readers aren’t getting anything at all.
DNS is some arcane incantations. Maybe after American Peasant is published, someone will come up with a DNS protection spell.
If you are still having issues and need assistance, I am a network engineer and have been dealing with DNS for almost 30 years. Happy to help if I can.
I might send you a note. We have an engineer on the case. The problem seems to be with the blog’s subdomains. WordPress had us update our DNS records, but the update doesn’t seem to be doing anything. And we are running out of ideas.
Oddly enough, my friend who’s visiting us just asked me about a DNS problem he’s having. 🙂
vstraylight at gmail dot com
Yikes.
Hi Damon. Sent you an email yesterday, but I don’t know if anything is going out right now.
Let me know if you are available to look into our DNS problem….
THanks. Chris
Working on my ATC tills. I have a little extra material for the bottom, but not enough to make them one piece. Should I make the rabbet wider for the ship lap or keep it around 1/2” ? Thanks!!
A 1/2″ lap is more than sufficient. No need to make life harder in this instance.
Hello Chris and Megan,
I’ve been making hot hide glue the last few month, using the Don Williams recipe (3 parts water, 2 parts pearls and 1 part table salt). In case I’m doing this wrong (apologies for the length of this query), here’s the method: Soaking the pearls overnight, then the next day adding the salt and cooking at 60C for 2 hours, putting the mix straight into the fridge until the following day and then cooking for a further 2 hours.
The glue has been holding great but I seem to have an amount of undissolved salt at the bottom of the jar. Have you encountered this before? Do I need to add more water? And will adding more water affect the strength of the glue? I’m concerned that if the undissolved salt was to get into the joint it would be getting in the way of the adhesion by holding the glued parts apart (however minutely).
Thanks for any help, it’s greatly appreciated.
The order of operations is important. We use hot hot tap water (120° F). Then we stir the water as we add the salt, allowing it to dissolve before adding the glue. Add the glue gradually while gently stirring. Then heat the mixture.
Here is our recipe:
• 8 ounces gelatin (by weight). Metric: 226 grams
• 24 ounces (by volume) of hot water. Metric: 710 ml
• 6.5 ounces (by weight) of noniodized salt. Metric: 184 grams
I am planning to build a table that will be finished with linseed oil paint. Do you have a wood recommendation?
If I were trying to show off the features of the paint, I’d use a ring-porous species. You can see the grain in the paint. If that’s not important, any species will take the paint just fine.
I built a small Roman-style bench awhile back. The legs were left loose w/o glue or wedges so I can remove them for transport. I whack them in with a mallet when setting up but during use they’ll loosen to the point where they fall out if I pick up the bench. Are you aware of any historical solutions to this problem?
I’m currently considering driving something (that can be removed) in from the side of the bench into the mortice to secure the leg. Something = a peg? a screw? a bolt? a nail? not sure.
Thx and have a good weekend….I’m painting the shop.
If you use a tapered mortise-and-tenon, that will usually do the trick. Alternately, you could kerf the tenons and drive in wedges – leaving the wedges proud enough to be pulled out.
Or one of the solutions you suggest with a peg from the side etc.
What’s a good size brush for painting chairs? I’m trying linseed oil paint on some ladderbacks. Thank you.
I usually use a 1-1/2″ angled sash brush.
Have you ever tried this style?
https://www.jerrysartarama.com/nat-bristle-7600-rnd-oval-sz-8
Seems to be popular with painters from England. I think they look cool but not sure how they perform?
They do look cool. But I have not.
Hey Chris, you are embarking on your next journey – building Shaker side-tables with the perfect form(s). You look at example after example to get some ideas/concepts in your head. You start building. You want 20 complete builds in a year (I’m guessing here, but you seem to get chairs out all the time). How do you approach this efficiently?
Do you make lots of mock-ups & prototypes, with very few seeing the light-of-day as a complete build?
Assuming standard M&T joinery with a dovetailed drawer, what are you using machines and hand-tools for – machines for the milling and M&T, hand-tools for dovetails, etc.? What dictates the machine vs. hand-tool split for you?
You are so productive, I’m trying to glean a little bit of how you operate because I feel extremely slow in my shop!
Honestly, I don’t feel very productive.
I don’t make mock-ups or intentional prototypes (though things get regularly trashed/given away when they don’t work out). Mostly I draw, draw, draw. Then I make a piece that is as close to that drawing as possible. The next version is an iteration of the first. I keep a list of things I want to change on future versions. I take pictures of my work and draw over them to try out changes (i.e. drawer height/leg dimensiosn etc.)
I always about two pieces in the works. And I spend any slack time tinkering with those parts.
If I am after a form, I’ll use machines for all stock prep and mortise-and-tenon joints, rabbets, dados etc. Dovetails I do by hand because I don’t have a dovetail jig (nor do I want one). Handplanes finish everything.
Basically, machines do things that people can’t see. Hand tools for things they can.
And mostly, I just don’t stop. I work at the bench every day, even if it’s just an hour. Sundays I devote to a full day in the shop. No visitors. No interruptions.
I don’t know if this is at all helpful…..
Won a classic tool chest at auction! Original builder made the mistake of aligning all the panel joints so that a single joint line circumferences the case (about 8” from the floor). Back joint is already split and it’s started to come round the corners. I don’t want two chest halves. Any thoughts on repair? I thought to replace the skirt with a 10” skirt (bridging the split) and adding a few mending plates inside.
Sounds like a bad glue joint. You might try first regluing it with hide glue and see if that fixes the problem. If the split continues, a skirt and some mending plates could shore things up.
Have you ever seen a blue-greenish color show up on red oak after applying a soap finish? If so, any guidance on what to do about it?
The red oak was smooth-planed and the soap is the premixed cream from Pure Soap Flakes.
I have not. But I haven’t used soap on red oak. I use it mostly on light-colored woods (maple, beech etc.).
I have. This is a reaction from the acetic acid in the red oak (also present to a lesser concentration in white oak, cherry, and elm) with copper in the water used to make the soap. You can mitigate this by using distilled water.
More on music- it seems bluegrass and related may be part of the LAP realm. In Minneapolis, public radio Jazz 88.5 FM does all “roots” shows on Saturdays. 5 hours of bluegrass start at 8am E/7am C, from Bill Monroe to today’s newbs. Listen live at https://www.jazz88.fm/
(Regarding the jazz during the rest of the week- no elevator music will be found here. It’s the real deal. Great stuff in the workshop.)
Do you have any thoughts on the Woodpecker owned Blue Spruce Line? Specifically the mallet and marking knife, do you know if the quality holds up or if there’s another similar caliber option out there? Thanks!
I like a less flexible but still small marking knife, which is no longer made by BS (but Dave also stopped making it long before he sold the company, so…). Kale was gifted a new mallet (2, actually), and while it doesn’t have a lot of miles on it, it seems just a good as the pre-WP version. Oh – I also have a newer one, but it’s a backup for travel (I don’t take my beloved blue one on the road anymore, because it’s irreplaceable). I’m sad the company stopped making the coping saw – it’s amazing – and I think a chisel plane does not belong in a furniture shop (but BS isn’t the only maker of chisel planes, so people must buy them). I think the dovetail chisels are too damn fancy – I don’t like the scalloped edges (I find them harder to hold), but they are the sharpest chisels I’ve used out of the box, and they are nice. If you’re fancy. So yes, I guess I have some opinions!
I was at the Fine Woodworking Show in Connecticut yesterday, and asked the Blue Spruce people about their discontinued coping/fret saw and the small 4″ bevel gauges. Both are discontinued. But I have both, and love them.
They said they simply didn’t sell very many. They still have the tooling, and they’ll likely make more, maybe next year. But they have backlogs of things they can’t keep up on, and for now they need to concentrate on those products. And really, that was the same thing that’s been happening at Lie Nielsen for the last few years, though they’re catching up.
I recently had some issues with an order: my 16-oz mallet was just a hair over 13-oz. I’m down for “nominal weight” but that seems far outside of the realm of nominal. They very kindly replaced it.
My marking knife blades came with a huge burr on them. Nothing a little bit of time on the stones couldn’t fix but still disappointing for the price. They did offer to send me replacement ones.
They handled both situations well but seems that they have some quality control issues over there in Ohio now.
Standard disclaimers: n=1, anecdote isn’t data etc etc
I have some with Dave and post Dave items, the quality is still there.
Hi all! Give Pony Bradshaw a spin. That is all, enjoy your Saturday.
Andrew
I messed up some seat mortises (incorrect angle) and I want to plug them and re-drill. I have a 1” plug cutter. Can I just plug them with a dowel (exposed end grain) or should I make a plug (face grain)? The chair is destined for paint now, so I assume a dowel is fine?
I probably would make face grain plugs. Most end grain plugs will show a different texture through the paint.
I’m curious about the publishing business, and normally love to hear war stories — but (from this reader’s chair) it seems like LAP authors would make for easy, reasonable collaborators. So, looking even further afield at your collective experience: have you ever worked with authors who, once the editing was complete, insisted on dabbling in deckle edge or other such ridiculous frippery*? If so, did you talk them down from that ledge, or give into the urge to push them off of it?
Bonus question: speaking of Fripp or thereabouts, does prog rock get much airtime in the shop?
Hi Eli,
This is the topic of my Sunday Substack on “The American Peasant.” The quick answer: Yes, we have had authors who were difficult – almost impossible. The way we solved that problem is now I won’t sign a publishing contract unless I’ve had a meal with the person and have backgrounded them personally.
We do spin some prog rock. Hell we have Taylor Swift on at times. During classes, I get the students to start a station on Apple Music that begins with their favorite artist. It’s a great way to keep my mind open.
how would you modify your soft wax recipe to create more of a paste wax that you could use over a film finish?
Jesse- just leave out the oil. Wax of your choice plus solvent of your choice equals homemade paste wax. Or use any store-bought paste wax of your liking. It doesn’t have to be fancy-schmancy $40/ 4 oz stuff either. $10/ 16 oz can from your local hardware store will work just fine. +99% of the wax you apply gets buffed off anyway, when properly applied.
Omit the oil. Increase the solvent. If you want more shine, substitute carnauba for some of the beeswax.
You didn’t say what the film finish is. I would test anything you use on a test surface as the orange oil/limonene is a solvent and when very concentrated, is sold as a weak paint stripper. I got Howards at HomeDepot, carnauba/bee’s wax/orange oil, and it goes a long way. The harder carnauba wax makes it more protective and the bee’s wax makes the carnauba tougher. https://www.howardproducts.com/product/citrus-shield-premium-paste-wax/
I have a copy of the Anarchist’s Tool Chest that I received as a gift around 2016. I think it was bought at a Lie Nielsen open house. There are 3 signatures in the book but the only one I recognize is Chris’. One is MADAY and the other looks like it starts with an M and possibly ends with a B or a T. I have always been curious; who are the other signatures? Thank you for all of the inspiration.
The one you can’t read that starts with an M is likely mine.
Maybe my daughter Maddy signed it? The other one… no clue. Sorry.
I keep seeing advertisements for the new (to me at least) Melbourne Tool Company. I’m also wanting to add a large router plane to my expanding kit of tools. Any experience with or thoughts on their tools?
I have not seen them, I’m afraid. Their router plane is an adaptation of an Old Woman’s Tooth router, a form that I don’t have any experience with. Maybe someone else here can chime in…. sorry.
They look similar to Woodriver.
Might have the Anglo-Australian label to gloss its China origin?
The spokeshave looks interesting…
I need to make a 12’ ladder for our living room bookcase. I was thinking of drawing from chairmaking joinery and making the rungs with wedged tapered tenons.
Is this a bad idea?
Or are there any historical ladder designs you could point me to?
I’m sure there are other historical designs out there, but I like the ladders in “Farm Shop Work” by George M. Brace and D.D. Mayne. Use elm for the uprights (it won’t split) and riven white oak for the rungs. Cylindrical wedged tenons.
Roy Underhill made a copy of Jefferson’s library ladder. I always thought that was pretty cool. I think it’s in one of his books, in addition to his show.
It’s also shown in the back of “Calvin Cobb: Radio Woodworker. A Novel with Measured Drawings.” It’s one of the drawings 🙂
Hey folks! I just completed my first chair (Gibson) and am pleased as punch. I am planning to do a soap finish atop the paint (since BLO / paste wax has a kind of yellowing effect.) I got the soap flakes and tried to follow the instructions in the ADB (boil 4 parts water, mix with 1 part flakes, after a few hours should be thick like mayo.). Sadly, despite getting the flakes just last week, it’s still fully like bathwater. If you have ideas let me know. I already also got the soap cream since I thought this might happen, and my wife agrees to use the soap flakes in laundry, so all is not lost, but I wanted to know if there was more I could try if I wanted to mix my own.
Huh. Well, I’d try the other “recipe” in the book, which is 1C boiling water, 1C soap flakes, and see what happens.
I’ve had this happen a few times recently as well. And I’m at a bit of a loss. I don’t know what has changed. I need to experiment with the flakes and see if I need to decrease the water.
Sorry I’m not a help here. But you aren’t crazy.
I have had consistently good results so far by mixing water and soap flakes in equal parts by weight.
You are correct (as per usual). Weight is key. Soap flakes vary greatly in size.
Two questions.
Tenon wedges for legs. I have some fast grown red oak that I saved for the wedges. But when I look at the ring structure at the end of the wedge that gets hit I’m concerned that the late wood will shear off along the early wood at the narrow end of the wedge for “flat sawn” wedges compared to vertical or angled grain wedges. Is this a possible problem? I have some black locust that I’m tempted to use instead for both strength and visual contrast. I’m guessing that the red oak wedges will be easier to pry out if a leg ever needs repair though.
Moisture content. Red oak again. I had to buy some new pieces of 8/4 for one seat because a hidden check opened up in the blanks during the two months that they acclimated in my shop. I live in coastal California at the edge of the fog zone so April through September is our humid season. The new pieces are at 7% MC and the acclimated pieces are at 9% MC. Note that the planning stop in my Bench Crafted work bench tends to swell and bind with humidity changes so a 2 percent MC swing seems significant. Do you think it is a good plan to let the blanks acclimate until they are at 9%? The octagonalized legs are probably at 9% and my plan is to try to dry them back down a bit before I cut the tenons and show them to the seat mortices.
A huge thanks to you and your crews over the years for all your videos. All the cutting edges of my tools are per your Sharpen This book/video. I made the Gibson and regular stick chair jigs and trued up the faces and edges with the tools. It was like magic to be able to make the jigs stand up nice and square by dialing in flat and 90 degrees using the stopped cut and shifted curved blade techniques.
On wedges: You might be overthinking it. But it’s hard to say without seeing the wedge itself. When I worry about a wedge, I’ll try a sample out in a test joint. That always gives me answers about what is going on inside the wedge.
On moisture content: You could use the drier stuff for sticks and stretchers, now and the swelling will be to your advantage. Red oak acclimates pretty fast, so it might do the job before you can get around to it. A lot of post-and-run makers will over-dry their rungs to 0 percent. Then tenon them and assemble. This works really well. I rely on compression of the tenon and try to keep all my pieces at equilibrium MC so I don’t have to run a kiln or monitor the wood constantly as I work.
Follow up from a question last week… when you use huck towels to apply linseed oil, or buff out soft wax, do you wash them right away, or lay them out flat to “cure” before putting them in the laundry?
We hang them to dry. Typically, I’ll get at least a few sessions w/a huck towel before it needs washing.
I have a beautiful board of wide 4/4 walnut hanging around. Could I use it for an armbow or am I really better off going to the hardwood store for some 5/4?
Uh….the not-chairmaker here thinks you should use that beautiful wide piece of 4/4 walnut for a tabletop or the like. And, Chris writes in “The Stick Chair Book” that with a strong species such as oak, he’ll accept 7/8″ for an armbow, but with a wood that isn’t as strong, you need a full 1″ – I’d be worried that the 4/4 wouldn’t finish at a full 1″?
Considering it’s starting at 15/16th I’ll wander my happy butt back to the hardwood shop. Thanks!
Hi Megan and Chris,
Do you aim for a certain percentage of your time spent on shop improvement, or is it more organic (i.e. see a need and fill it)? The tool board/bookshelves on the bar are a good example of what I’m thinking about.
It’s easy for an amateur to go down a rabbit hole of shop improvement and lose track of creating something that will leave the shop.
Cheers,
Alex
As long as I can find everything, I’m happy. My shop at home isn’t nearly as nice…but everything has a place – that’s what I think is important. But I don’t get visitors, so…it doesn’t have to be pretty.
Shop improvement is an ongoing task. I have a long list of things we want to accomplish. But those have to be wedged in between projects that make money. It can take months (or years) to finish a major task. We just finished the last stage of our machine room, which was an ongoing process for eight years.
But I try to do something – no matter small – every week. Add another coat of wax to the countertops, fix the shop door, hand some hooks for our keys. Little stuff adds up.
Hi guys. In the ATC, the till runners are nailed and glued to the inside of the chest. In the video for finishing the inside, the lower runner is screwed and the two above it are glued. Is there a reason to use glue rather than just screws on the the runners? If it’s okay for the bottom ones, seems like it would be okay for all three sets. It would allow me to replace them and my grieving relatives to remove them.
You could countersink and glue all of them – I just worry that without glue holding the thinner runners (which is what the till bottoms run on), they might bow the teensiest bit…and that teensiest bit would be enough to keep the tills running smoothly. But hey– if that happens to you, you can always add glue later if needed!
Nails, screws or glue alone is fine. I think we vary based on our mood, or what we have on hand at the time.
Chris, on a prior Open Wire you mentioned that your hand crank grinder is set up for molding planes and other unusual profiles, unless I’ve misremembered. What does that mean and how did you shape the wheel? My only way to adjust the wheel at present is my wheel dresser from Lee Valley. Thank you all, and happy Saturday!
I shape the wheel with my diamond wheel dresser. You can also do it with a scrap drill bit.
Not a question, just a comment. I needed a scorp, and all the ones Chris suggests were not readily available. I found one on Etsy, ForgedCraftTools, that looked well made, though not the ideal shape for chairs. It was on sale for $47! Sounded like a scam, but the maker was in Ukraine and I figured I could afford to donate to them if it came to that. It arrived in less than a month, beautifully made. I’ve used it on 6 chairs so far. It works, but I have nothing to compare it to.
I’ll pick one up and see how it works. Thanks!
The RSS feed is working again, here at least. This post came through on my reader.
The full post? Or just a preview graph? (Just curious)
I’m finding your blog RSS feed isn’t updating any more. Apologies if this has been addressed.
Thanks. We are having lots of problems with our DNS and RSS. We are trying to fix it, but we aren’t having much luck.
I’m building a Gibson chair and watching your video. You’ve added some snappy theme music to your video. Every time it plays I smile and get up and dance a little jig. Can you provide any background on this music? Who wrote it? Who is playing? Anything else?
I purchased the Lee Valley Tapered Tenon Cutter and it was not not set up properly as it came so I wasn’t able to cut a reference tenon. I have absolutely no clue how to set this up from scratch to match my reamer. Is there a method to follow or is this simply trial and error? Thanks!
Hi Deke,
There are lines cast into the body of the cutter. A good place to start. Lock down the iron so:
This will get you really close in my experience.
What’s the proper response to someone what has the inevitable comment after I’ve finished a nice project in pine, “looks good but you should have used oak.” Or, “I’d like it better in cherry.”
“Then by all means, you should feel free to make one in cherry.”
Perfect!
My response is: What don’t you jump up your own butt?
Haha, hands down made my day!
This kind of a lame question, but I’ve been hung up on it:
When using water stones that need to soak, what do you do with the waste water as it accumulates swarf and filings?
For the Shaptons that you just spray and use, you wipe them off with a paper towel that you then throw away (presumably in the garbage, not compostable).
But a tub full of muck and filings seems like something I’d want to avoid dumping into the storm drain…
I don’t worry too much about the muck and filings. It is mostly clay and some steel. You can pour it in the drain without making a huge impact on water quality. Or pour it on the driveway and let it dry and blow away….
I have a similar issue when emptying the water tub on the Tormek; I don’t want to pour neither the swarf nor, in particular, the particles from the wheel down a drain, where they would be likely to form a nice, solid blockage quite quickly. Instead I filter the waste water through a #6 (.i.e. large) cone coffee filter (with matching filter holder). The same cone is good for several uses, but when it’s not, I just throw it in the garbage. It doesn’t have to be a #6, of course, but I had a spare, and it’s large, so …
Hi, Chris! My family needs a side table (or two), so I’m planning to build a staked low stool to serve double duty as a table for coffee and books and as a stool for our bottoms. The scrap I have available is redwood, so I’m not sure that a 5/8″ tapered tenon for the legs will be strong enough. (For 14″ long redwood parts that are 5/8″ thick, I calculated rupture is 138 ft-lb/sq in and shear is 326.) You recommend sizing up by 1/8″ if we’re worried about strength, but I’m not sure what to do for tenons. Should I go up to 1″ cylindrical tenons? If so, do those also get kerfed and wedged? Or am I over concerned given that the stool is short and stocky? Thanks!
“Redwood” is extremely variable. The stuff now in most stores is like balsa wood. Modern heart wood is a little better but really expensive. The old growth stuff that was harvested before 1970 is gorgeous but still splits easily and often has cross grain. My 80 year old house in the East Bay has external window and door trim that is the good stuff. But it splits really easily. If you have a nice piece for the top I’d suggest building it like the Germanic/Swiss back stool on paged 93 of the SCB. I’d use 1.5 inch tenons into a hardwood batten and screw the batten, instead of a sliding dovetail, to the top. You can taper the legs in the Germanic/Swiss style so they don’t look chunky. But I’d test the leg blanks by giving them a rap to see if they break. The 300 foot tall gigantic old growth trees sometimes hit the ground hard when they felled them creating hidden stress fractures in the wood. If they are used just for light duty side tables, and only very infrequently and carefully for stools, you could probably get away with tapered tenons that are 5/8th at the end. Just my 2 cents from experience making nonfurniture things out of redwood and western red cedar.
Are the redwood parts 5/8″ thick? Or is the top 5/8″ thick. Sorry I am thick and not following.
If the top is thick and the legs are thick (1-1/2″ to 1-3/4″) you’ll be fine as long as you don’t dance on it.
Sorry, the lumber is 1 1/2″ to 1 3/4″ thick. My question was about the leg tenons. Sounds like I’m probably good with 5/8″ tapered tenons. In any case, I’ll try it and see how it goes. Thanks!
Absolutely fine on the tapered tenons.
There was talk of Amana possibly selling ATC board kits to us regular people, did anything ever come of that? Or rather, is there anything else like that out there that would prevent me from spending the next month or two glueing up panels?
I have not pursued it. So as far as I know, no one is making kits. Get thee to gluing!
What is a good way to get a square cut on the top of a circular post, besides wrapping paper around it? For example with a JA Chair, the front post. Any trade secret way from the days of yore?
I’m not sure what you’re asking… if you mean getting it parallel to the floor, a saw and a shooting board, as needed.
Yes parallel to the floor. It is particularly difficult because it is assembled and then trimmed so laying out and obtaining a circular mark is beneficial.
Ah. After assembly. Mark the entire cut all the way ’round, then follow the line, same way Chris shows when leveling a chair – that is, start the kerf at a number of arcs around the leg, then join them. (We hold such add-shaped projects in a High Vise (Benchcrafted) or carver’s vise tor that type of work.)
Thanks for taking questions. Does anyone there have experience with Bad Axe saws? I’m wondering if their dovetail saw is worth almost twice the cost of a Lie Nielsen.
I have two BA dovetail saws. To me, it is worth it because I can order a handle that fits me. If I had hands the size of whatever the tool world has deemed as “average,” I’d get the LN. It’s an excellent saw – just not comfy for me for all-day work.
I use the Lie-Nielsen saw and it fits my hand like a glove. That (and the balance) is more important that the initial configurtion/sharpening of the teeth. That will/can change when you sharpen it. I have Bad Axe saws, and they are great. But I started with Lie-Nielsens, they are perfect in every way.
Thank you both for the replies; Very helpful.
Thanks for another interesting Saturday discussion. Much appreciated.
Saw sharpening service. I have a PAX tenon and a PAX dovetail saw, both are 45 years old and are in need of sharpening and a reset. Could you recommend a place to send them for sharpening?
In the U.S.?
Matt Cianci. https://www.thesawwright.com/
Mark Harrell: https://sawsharp.com/
Megan and Chris: Have you observed any yellowing over the years on any piece(s) you finished with your soft wax? if so, could the raw linseed oil in the recipe be swapped out for pure tung oil to mitigate the yellowing? Thanks much!
Yes, it yellows. Yes, you can use tung oil in the recipe (I have). You also can use purified/refined linseed oil to reduce yellowing.
“Beginners fear”-question: first bookshelf I build, four shelf units, so 5 upright glued up panels which are 245x33x2.9cm in definitive dimension, all done by hand (I’m open minded even to machines but have absolutely no space in the basement).
Now as those are really big faces, do you have a secret spell or trick to get all the five panels planed down to one uniform thickness with parallel faces with the least amount of fussing and handwork after the glue up? Or is this a really dumb overthinking thought and I should just go for it and see where it takes me?
Thanks a lot! Have a good evening at crafts and vines!
The question is: Do they need to be all the same thickness? Do the faces need to be perfectly parallel?
One of the great aspects of handwork is that you fit one piece to another. The parts do not have to be interchangeable.
Handwork is only difficult when we try to imitate machines. So the “trick” is to make flat only the faces that absolutely require it. Most boards only need to look flat, which is much easier.
When I dimension stock by hand I use a No. 5 with a curved iron. When I start with rough stock, I use a scrub plane.
Another possibility as you get started: Call a local cabinetshop and ask if they will joint and surface the panels for you. We do this for friends whne we haver the slack time.
I got a dovetail plane for PF German chair. Is that plane only used for sliding dovetails or are there other joints it’s used for? Maybe there is an article out there I couldn’t find any. Is a lot of fun to use.
I don’t know if any other uses other than sliding dovetails, but it is a great specialty tool.
I simply must get up there to see your shop…I mean, to commiserate over a good glass of wine. About the chair design…one [possibly both heretical and ugly] would be to extend the two side sticks through the top, so that Uncle Bubba would have something to hang his hat on while lounging. Love your work!
Sure. Or a a second or third medial stretcher below to create an ersatz shelf for le chapeau du Bubba.
you’ve probably answered this before – so telling me a term/terms to search for is just fine. What characteristics should a chair have, if its purpose is for sitting in and reading books. I guess i want to be able to sit for 1-2 hours, without discomfort but without so much comfort that sleep occurs. I accept that behinds/bottoms vary. Thanks
Probably a 2- to 3-finger lean (depending on your fingers…), and put this on the seat:
https://driftlesstannery.com/shop/bark-tanned-sheepskin-nissan
And, you’ll find some discussion on this in the comments here:
https://blog.lostartpress.com/2021/12/01/the-insanely-low-bar-for-chair-comfort/
And here:
https://blog.lostartpress.com/2016/09/28/where-chair-comfort-comes-from/
And here:
https://www.core77.com/posts/90066/Rethinking-Chair-Comfort?utm_source=core77&utm_medium=from_title
And here:
https://blog.lostartpress.com/2024/01/21/even-better-stick-chairs/
For reading chairs I like a 5 degree seat tilt and a 20 degree back lean with a curved backrest. The Irish armchair in The Stick Chair Book is an example.
Warning: sharpening question incoming ….
I believe Chris once mentioned that he doesn’t like Shapton glass stones. Why not? No stake one way or the other, just curious.
On a related note, I have used up about 1/2 of my Ohishi 1000-grit stone from Lie-Nielsen. When I replace it, is the Shapton 1000x Orange Ha-No-Kuromaku Ceramic Stone your pick for honing?
You will find those answers here:
https://blog.lostartpress.com/2022/09/29/my-personal-sharpening-kit/
Ah, there it is:
“Just my opinion, but the glass stones are mostly a waste of money. You will use up a 1,000-grit stone in a year.”
Thank you!
I have to put a new coat of finish on a dining room table and have to do it in the house. I’ve been using pure tung oil diluted with the orange solvent on smaller pieces and I’m happy with the look, the ease of application and the inoffensive odor. But it this durable enough for a dining table? If so, are two coats enough?
It’ll be fine. Tung oil is easily repaired by adding more tung oil. I think it is a great finish.
Hey LAP!
I’m making a Roman workbench from SYP 2×12. After glue up and trimming off the factory round overs, I’m at 10 3/4” in width. Should I scab on a ripped piece of 2x material to add another 1.5” or just go with it. In Ingenious Mechanics, one of the benches is 11” of oak but others are wider.
I’ll be using it more as a bench and for green wood carving of bowls/spoons. And maybe chairs one day. And as I age (I hope).
Any advice is appreciated.
Keep it at 10.75”. You’ll be just fine.
Good afternoon LAP,
I’m looking to do some experimenting with plywood seats, arms, and combs. Will it’s layers of glue damage my scorp or travisher?
Thanks,
Aaron
Not if you can sharpen. The glue will do minimal damage to the blade.
LAP, I have some wooden hand screw clamps. They have some cracks, small med, lg sizes what type of glue should I use and should there be clamping?
Also there is paint on some, I am going to use mineral sprites with 0000 steel wool to get back to original. What should I apply, wax?? what type? oil??? no!! I don’t want to use your wax as that is for drawers, chairs. Ralph
I’d use yellow glue to repair the cracks. Clamp the jaws while the glue cures. The traditional finish for these clamps is straight linseed oil (to repel glue). The more coats you add the better the resistance. I usually do three or four light coats.
Hi! Thank you for doing these! I’m looking for some suggestions on finishing an ash table top. I’m not expecting a perfectly smooth finish since it’s ash, but is there something I can use that can help fill the grain a bit without obscuring the color and figuring? I will experiment on scraps, but I’m looking for a starting point, and I’d like to avoid nasty things like polyurethane. Thank you!
Consider a white or whitish wax. It will fill the grain a bit with white pigment and keep the color of the ash.
Thank you
What species of wood best suits American Peasant projects?
Whatever is common and inexpensive in your community. For me it was poplar and linden.