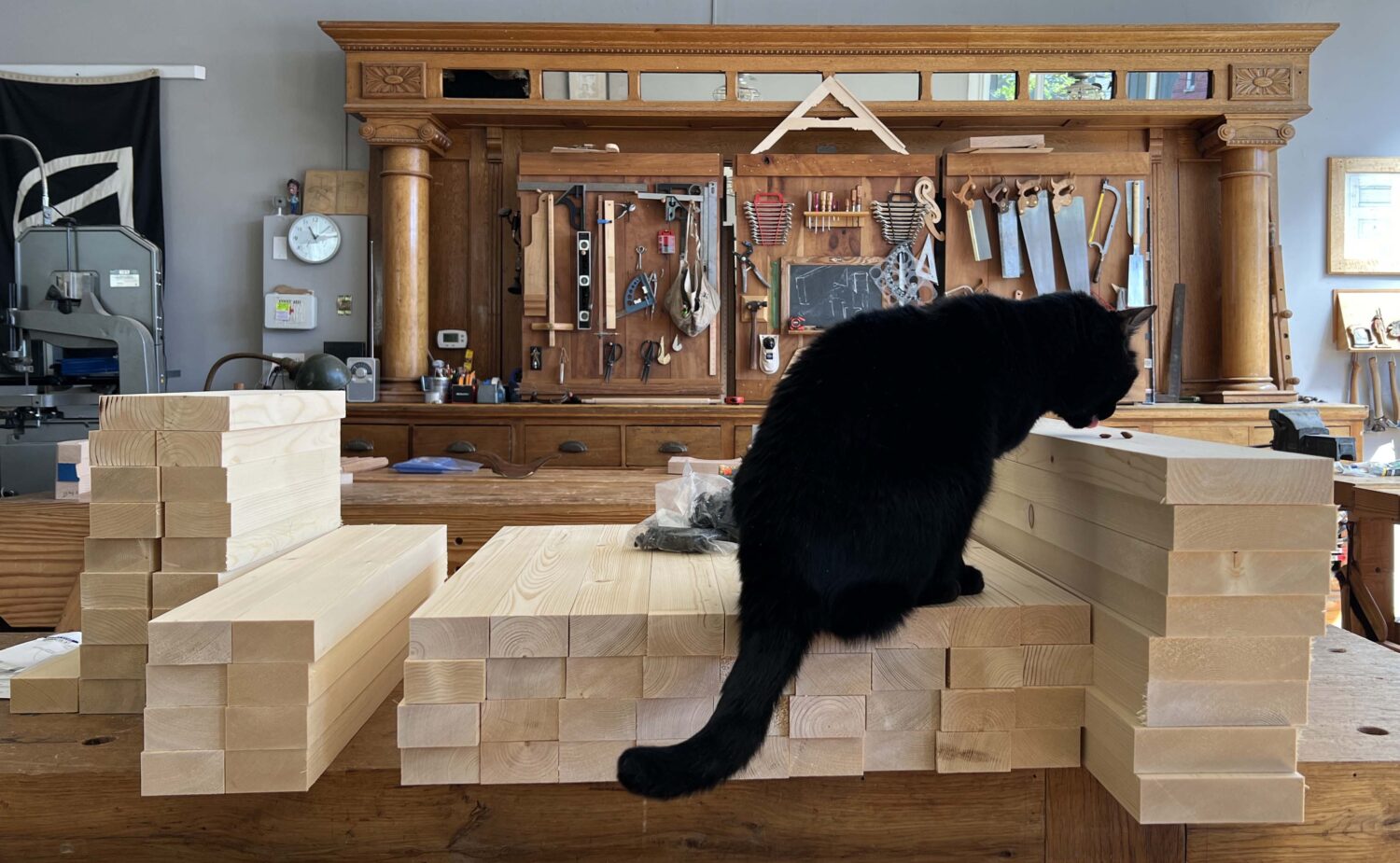
Wally and I are busy today helping students turn the sticks shown above into sawbenches. But Chris is back this week, eagerly awaiting your Open Wire questions.
So, please post your (succinct) woodworking questions in the comments below, and Chris will answer. You can also ask him about the massive wave of relief you might have felt emanating from Northern Kentucky and Central Indiana (where John lives) late yesterday. That was engendered by our finally having all the LAP/Crucible books, tools, clothing and sundries under one (now non-leaking) roof in our warehouse!
Note: Comments are now closed.
– Fitz
I am curious if anything came together from all of the stick chair pictures you required for earning our stick chair merit badges.
I still have them all in a file here in the office. I had hoped to do a multimedia project with them, but fixing our warehouse pushed aside all frivolous/fun stuff. I may get back to it. But I have a pile of other stuff (Stick Chair Journal No. 2) that needs me first.
You could make them part of a stick chair journal if you wanted to.
The 400-page Stick Chair Journal? We got a lot of them….
Well I guess that would be a lot. I was thinking along the lines of a photo gallery that would take maybe twenty pages? Whatever size you’d have to make them. But if you wanna make a proper four hundred page coffee table book I bet every damn one of us would buy one. Don’t know what it would cost though so…black and white would be cheaper probably. Or a pdf we could print ourselves. Also I am perfectly tickled pink with the badge if that’s it. Please note I didn’t say huge poster because I don’t want to send you on this peaceful Saturday. : )
Hi from County Fermanagh.
I plan on making a Gibson using your video (purchasing soon).
I have a big lump of poplar which is about 15″ wide and 2″ thick with plenty of length.
1.) it’s quite hard to see where the straight grain is for the legs. Is it worthwhile planing it some to see grain better?
2.) since it’s 15″ wide, I think you recommend 16″ for a seat. Is it good enough depth for a seat or do I need to laminate a bit more on?
Many thanks
Iain
A 15″-wide seat is fine. I wouldn’t laminate anything onto it.
As to finding straight grain, if you have any doubts at all, rive a section off. The split will follow the grain. Then work off that edge.
Thank you sir, looking forward to it
Greetings from the north!
Not really a tech question, but I was following the rabbit hole of vintage woodworking eqpt this morning (thanks!) and saw listed in the vintage stuff for sale is an “Anthe spindle cutter”.
Seems to have maybe originated from your new building (maybe).
Any idea what these were used for?
I believe the spindle cutters were used for power carving. Though it could also be an early shaper. I need to do more research, but it looks like the Anthes outsourced castings and refined them and assembled the machines here. A lot of their work here was manufacturing the cutters.
I do. And I try at times to photograph them that way, and the photos always fail to see what I see.
Remember at your old house having a power outage and sitting looking at the shadows on your furniture in the moonlight? Do you ever go down to your present shop and look at your current projects in the moonlight?
I saw a pix of you without shoes in the shop
Shame on you
Pretty sure he’s 19 and unlikely was holding a chisel. Maybe a moonlit scene, crucifix and wooden stake for trolls?
Hi!
I have most of the LAP books and many other books on woodworking that I have collected over many years . I have always heard that one of the advantages of hot hide glue was that it was possible to easily disassemble joints in furniture. I have not read any descriptions as to best way to accomplish the disassembly. I assume it involves heat and/or moisture. What is your process?
I have to admit I have not tried to experiment.
Animal glues are, in general, reversible. You need to heat the joint above 140° F or so to take the pieces apart. For shallow joinery (say 1/2″ deep or so) a clothes iron will do the trick (they get to about 340° F). You need to protect the work with a wet rag so you don’t scorch the wood. The water is also an effective carrier for the heat.
For deeper joints, we use a heat gun designed for stripping paint that goes to about 500°. Again, you need a wet rag to protect the work. It can take time for the heat to fully penetrate the wood and get to the glue, so be patient.
Thanks for your quick and detailed response!
I forgot to say that I love all of your books. It is great to have a book with quality in content as well as being constructed for comfortable and constant use.
Hi and apologies for the longish question!
I’m planning the build of an Ulm Stool (https://de.wikipedia.org/wiki/Ulmer_Hocker#/media/Datei:Ulmer-hocker-hfg-ulm-max-bill.jpg).
The original production runs used spruce with beech skids attached with tongue and groove joinery.
Plans on the Web follow this construction and glue the entire length of the skid in place.
This makes me concerned about wood movement and long-term durability.
I’m planning on making my stool from ash, so I don’t really need the skids to protect the
feet from wear. I doubt I’ll find quartersawn pieces which are wide enough for the stool,
so I might need the skids to prevent cupping of sides made from flatsawn stock.
What would you recommend?
1) Make panels from quartersawn material and forget about the skids.
2) Go with skids and glue them full length.
3) Glue only the center of the skids and hope the wax and wane of the
legs does not cause visible “steps” at the ends of the skids throughout
the year.
4) Something else entirely.
Cheers,
Daniel
I like the skids. They dress up the form quite a bit to my eye. I don’t think they will do much to prevent the wood from cupping. If it wants to cup, it will.
You don’t need pure quartersawn material for the wood to remain. Rift stock that has been well seasoned will stay very flat.
If it were me, I use the best stock I could get (dry and clear). I’d glue the skids either in the middle or at one end (and call that the “front” of the stool). You will get wood movement. And it will show at the skids. That is not unsightly at all – that’s just wood.
Hope this helps.
Good points. Thanks, I appreciate your advice!
D.
Good morning! Thank you for taking the time to answer our questions! I’m enjoying making staked furniture. I need a sofa. Any suggestions? Are there any examples or inspirations you could point to for the design of such a thing? Or does a staked sofa even make sense? Cheers!
I would make a platform and back for cushions. The platform could be a solid piece of wood or a frame. Stake the legs into the underside. Stake the backrest pieces (and arm pieces) into the topside. You can get a lot of inspiration for this boxy look from mid-century couches:
https://www.instagram.com/midcenturymobler/
As a starting point, consider the staked bed in “The Anarchist’s Design Book” (page 178) and play with the dimension. You can make it shallower to sofa depth. Make the rear batten wider so it will accept stakes/ tenons to support the back. Finally, if you want arms, make the battens longer than the deck and stake into them.
Would a settee work for you? Try googling Windsor settee for some starting points, and convert to stick chair style, maybe
I have to make a bunch of hardwood dowels – 1 1/4″ and 1 1/2″. What would be the best was to make them. Thanks
If I had a “lot,” I would cut my stock to size and send them to Midwest Dowel. They will make dowels from your stock and do a good job.
If I had fewer than “lot,” I would make them on the lathe.
If I had time but not a lot of money, I would make a rounding plane for each size (directions are all over the internet).
Good Morning.
I recently picked up a copy of Handplane Essentials, which I am enjoying dipping into, I quite like that its a collection of PW articles. I have tried to find a copy of Handsaw Essentials, but it doesn’t seem to be available. Is this the same book as The Essential Handsaw book?
Kinda sorta? They took a bunch of articles out and added in a bunch of other articles.
Honestly, don’t spend your time/dollars chasing Handsaw Essentials. There were so few copies printed that the bots drive the price up to stupid levels. The book is good, but not worth more than its cover price.
I was asked to fix a dresser/mirror combination. The large mirror was affixed to the dresser with two boards which ran on the back of the styles of the mirror onto the back of the dresser. All screwed together. Can you suggest another way of attaching or is this the most common and perhaps best way? Is there a “traditional way”?
That’s not a bad way to do it. The mirror’s stiles don’t take much abuse. And the screws make the mirror easily removable to disassemble and move the unit. I am sure some people have mortised them into a rail at the back, but you still need a way to remove/replace the mirror.
So I’d stick with screws.
Excellent. Thank you.
So, where do you get those no-mar pliers? I can’t find them anywhere
I use the Tamiya brand. Widely available at Amazon and elsewhere.
https://www.amazon.com/gp/product/B01LXDTF23/
As always, thanks so much
I use made in Japan ones, Lee Valley’s soft jaw pliers, they look the same as the Amazon ones, but I don’t have to make Amazon richer.
https://www.leevalley.com/en-ca/shop/tools/hand-tools/pliers/32197-soft-jaw-pliers
I saw you’re planning a chair class in Germany this summer. What types of wood would you like to use for that class? Are there woods from Europe you’ve been wanting to try?
I suspect we will use European oak or beech. I’ve used a lot of European woods (and like them). Swiss pear is a favorite, as is English oak. There are several species I haven’t used before, such as serviceberry.
Hi Chris,
My Tolkien-loving brother Mark is turning 40 this year and what better way to celebrate than by making him a Schwarz “Hobbit-ish” chair. I’ve examined all your posts about it and have a rough idea of dimensions except for the width of the back splat and thickness of the seat before the sliding dovetailed battens. Any help you could provide would be appreciated. Thank you.
The splat is 18″ tall (minus the tenon) and 7″ at its widest (at the vase shape below the armbow). The seat can be anywhere from 1-1/4″ to 1-1/2″ and work fine. This chair will be in the next Stick Chair Journal. I should be starting the build next week.
Do you wash your linseed oil-soaked Huck towels in the same washer you use for your socks and underwear? (Not at the same time, I assume.) My wife Mimi is very supportive of my woodworking activities but she would draw the line at gumming up the washing machine.
We haven’t had any problems in the last 10 years or so. The detergents remove the oil and carry it away.
If you are still not confidant, take them to a laundromat.
Thanks. That’s good enough for me.
I’ve built a staked low stool (Ch 6 in ADB) and would like to paint the seat (GF acrylic milk paint) and just oil (Tung) the legs. I’m curious about how you’d sequence the order of operations. Is it best to oil the whole thing first and then just mask off the legs and the paint seat?
I’d paint, then oil. Oil tends to migrate via capillary action. If you oil first, you might create some areas that won’t take paint. These areas would likely be under the seat so it’s not that big a deal, visually. But typically it is paint then oil with water-base paints.
Thanks for doing these! If you are clinching a nail, would you drill the pilot hole completely through both pieces you’re joining?
I do. It prevents nasty splintering on the show surface of the door/panel.
Thanks for doing these and congratulations on the big move!
Maybe a better topic for “Never Sponsored” – do you have a favorite mortise marking gauge? I’m not loving the one I have, certainly not as much as I love my Tite-Mark.
I use the Veritas Dual Marking Gauge (with the clamp!).
https://www.leevalley.com/en-us/shop/tools/hand-tools/marking-and-measuring/marking-gauges/67466-veritas-dual-marking-gauge
Absolutely my favorite for mortising.
Thanks – that’s exactly what I have. So I guess that, as usual, the fault lies with the operator rather than the tool.
(I think I finally figured out a way to set it accurately to the chisel width, and it’s not by eyeballing it.)
I’ve the older Lee Valley add-on style and use a 2-step process. Might help with the fancy one, given the length of vernier caliper jaws? (1) caliper on mortise chisel; lock. (2) move guides to inside of caliper; lock.
Hi, I’m getting ready to build my first chair. I have a lot of hand tools but nothing really dedicated for chairs other than possibly my spokeshaves. If I had to choose either an inshave or travisher for now and one to buy later, which would you recommend? Thanks!
I recommend beginners get the Windsor Workshops travisher. It can be used as both a scorp and travisher by resetting the blade. Plus, many beginners get on with the tool because it’s more like using a handplane.
https://thewindsorworkshop.co.uk/travisher/
If you stick with chairmaking, then you can add a travisher with a fine mouth if you want. But you might not see the need.
While drawboring my AWB, one leg-to-top peg shattered when it hit the backside of the mortise. It was probably caused by a combination of tilting the brace when drilling through the mortise and not sharpening the peg enough. While it is likely still a very strong joint, I’m wondering if there is any recovery technique when this happens?
You can drill it out with a bit that is slightly smaller than the peg, then pull the remainder of its shattered carcase out of the hole. That usually works – depending on how bad the damage is inside the hole. Then peg it again.
I bought a used scorp, and it feels like the bevel down way the blade is on it won’t work (it feels like I can’t get the right angle to cut). So the silly question is should a Scorp blade be bevel up or down?
The bevel is usually on the outside to make sharpening easier. It’s typically a very shallow bevel (17° to 20°). Honestly, some “scorps” are so poorly designed that they will never cut unless you re-orient the handles and change the geometry of the blade. It’s crap manufacturing. I’ve had some new ones come through our shop in student hands that were hopeless. Or they were designed to hollow narrow staves and the handle position and bevel weren’t as critical as it is for saddling seats.
Recently acquired 200bf of fresh sawn 8/4+ Cherry I’ve now stacked for future chair use in a couple years. My sawyer gave me two 13”+ slabs of Box Elder with some red streaking he had sitting around a while, he wanted them to go to a good use. I’m thinking about making a pair of kid/smaller person stick chairs for the kitchen table, using the Box Elder for seats, arm bows and combs, and painting oak sticks and legs a bright red to match. Might try and get a bench out of it as well.
Have you ever used Box Elder for something structural like a chair seat? Seems to match Poplar for strength properties, so I imagine it should work out.
I haven’t used box elder for a chair, but would absolutely use it for a seat without hesitation.
I’ve turned many boxelder pieces in the past. A very nice looking wood, part of the soft maple family if I recall. But the red streaks don’t stay red forever, they’ll eventually turn a similar brownish shade over time to compliment the overall blond color of the wood. Still great looking but not as red.
I just complete my ADB Low boarded bench and I’m going to use general finish coastal blue paint. First time! Do you thin it at all? Does that eliminate brush strokes? I do plan on using a brush. Was very fun to build!
Thanks!
I don’t thin their paint unless it is too thick to brush. The stuff usually lays out beautifully and levels nicely at full strength.
I hate to beat a dead horse (since I’ve already inquired about these in previous posts) but why do you (have you) not tried compass planes to create curves in furniture? Too finicky? Fitz says that Will Myers uses them but no others she knows (unless I quote her incorrectly.) I thought it might be a quick way to make a curve without having to carefully handle a curved bottom spokeshave. The Victor 20 (or 20 1/2) plane has less loss of motion and is more ergonomic than the Stanley 113 but the 113 has graded gear markings that allow one to replicate convex and concave curves of similar arcs. I’ve never had the chance to try either, unfortunately. (And, Chris, you don’t remark on them in your Anarchist’s Tool Chest.) Thanks for your infinite patience with my question.
I just don’t see the need for them in my work. I saw out the curves and refine them with shaves. I don’t have a need for a precise radius. And I will always opt for a simpler tool over a complex one.
You should ask Will why he likes them. I will, the next time I see him.
I’d be very grateful to know how to contact Will. Or please do forward him my contact information that I listed with my post. I understand your reasoning, of course. Thank you for your reply. (Do you know if he uses the Stanley 113 or Victor 20/20 1/2? If not, no matter.)
I don’t know what he uses. You can contact him here:
https://eclecticmechanicals.com/contact/
The Victor 20 has better balance and the front grip area is solid. On the 113 the adjustment knob is the front grip and you can/will change it while using. As for matching curves, simply lay on its side and draw a template when done. Or trace the curve and then adjust the plane to match. Suggest using lubricant on the sole and alcohol in difficult areas. Light cuts.
Thanks, Eric. From what I’ve seen, other people using the 113 do not grip the knob but instead put their hands below it, front, around, or behind, so as not to move the knob. I’ll absolutely lubricate the sole before using and take light cuts. (I see that the mouth can choke up, since it’s so small and one cannot naturally move the frog.) The 20/20 1/2 has less loss of motion because of its design but some think (believe it or not) that the 113 is more comfortable to use, for whatever reason. What I like about the planes is that one can set the curve and just go to town, without having to check, as one would with a spokeshave, that one is matching the curve. (Spokeshaves, of course, are much more versatile tools and are useful for so much more than making regular curves.) I also really like that I can see the measurement gauge on the 113 and, even if there is a little slop, get my curves (say matching curves on the sides of a shelf) to be symmetrical. Thanks for the help!
A hearty Congrats! for getting all of your stock under one convenient roof!!!
Thank you! We moved 50,000 pounds of books with manual pallet jacks on Thursday and Friday.
So everything is sore. But we are happy!
Hi, can you give us a status report on your Soft Wax, refinished dining table? How’s it holding up? What happens with drinking glass rings? I’m thinking about how I want to finish a pair of side tables in my rec room. -Deke
So far it’s great – no white rings or significant damage. And I haven’t added any more wax. I’ll probably add another thin coat on the table when I add another coat to the kitchen countertops (which are holding up great).
Have you tried the speedball linozip bits in the crucible engraver?
I have not. But Bert Bleckwenn has, and he reports they don’t work well.
Morning Chris, I’ve got my Pure Soap Flakes Co. flakes and I was going to ask about the weight versus volume recipe-measuring (with water), but I’ve decided, instead of asking my question, I’d like to comment instead. I’m going to follow the LAP spirit and just try it myself. I love that you encourage us to experiment. That a better way to learn. Thanks for sharing and helping me to get to this point today, I’ll take it from here. (well, at least for today).
Good luck! It’s a forgiving recipe.
Any hints for using the veritas combination plane for rebates?
I’m afraid I’ve never used it for rabbets. We use it mostly as a plow. I use a 7/8″ straight rabbet for most rabbeting operations. And a Veritas skew rabbet (a moving fillister plane) when we need to make a lot of rabbets all the same size. Sorry I’m no help.
I am building a side table with reverse tapered, octagonal legs which will be tenoned into the top like a chair. I am thinking of going with 1″ cylindrical tenons because I’m not sure how to do a tapered tenon with such a wide shoulder at the top of the leg. I don’t have a lathe but I do have a 1″ plug cutter as well as a Lee Valley tapered tenon cutter. Do you think it would simpler to use cylindrical tenons rather than trying to get a taper in there?
I think you’ll be fine with 1″ cylindrical tenons for a side table. Tapered tenons with wide shoulders … that’s a lathe operation.
If you were limited to only 3 bench chisels, which sizes would you choose?
And why?
Probably 1/4, 1/2″ and 2″.
The little ones are a good size for chopping. The 2″ is good for paring and deepening tenon shoulders.
Honestly, those are the three chisels I use the most. I have a couple more, but I use them only when the other need sharpening, and I’m in the middle of something tricky and cannot stop.
Congrats on the warehouse finally coming together!
Which plane would you choose: veritas skew block plane or veritas skew rabbet?
No contest. Veritas Skew Rabbet. It has the mass and the rear grip that you need to effective make rabbets. The little planes are tricky to hold and keep in the cut.
Thanks a bunch! I really appreciate you folks answering all our questions with expert advice.
I have a Ray Isles 1/4″ mortise chisel. I also have a lot of mortises to make in red oak. The tip of the chisel keeps crumbling off. I’ve tried changing the sharpening angle to make it more resilient, but it only marginally helps. Two mortises in, and yep half the tip is jagged. Any thoughts? Did I just happen to get one made on a Friday afternoon? I have no issues with my LN bench chisels. Thank you
Sounds like it wasn’t properly heat-treated. Holler at Tool for Working Wood, send them a photo and your story. I am certain they will make it right.
Hello. I just finished building a dining room table. I modified your work table design from the Anarchist design book. It turned out awesome! I painted it Lamp Black with General Finishes milk paint. I’m wondering if you have any advice for what to cover the milk paint with to give the table a fighting chance as I put it into service in a couple of weeks.
Well the paint is plenty tough on its own. I wouldn’t add anything over it.
But my aesthetic is that furniture looks better with some miles on it. If you are hell-bent on preserving the look, try adding multiple thin thin thin coats of wiping varnish (half varnish/half mineral spirits).
Do you guys ever get to Wisconsin for demonstrations and/or classes? If so, when and where? Thank you!
I stopped being a traveling show about 2017. Before that, I was on the road 18 weeks a year. Now I only teach outside LAP 1) when I need to go overseas and it helps pay my fare 2) for a charity I support or 3) when they back up a dump truck of money to my door. Sorry.
Good morning all! i have a dining room with hardwood floors which will become my indoor workshop. i wonder what, if anything, you put under your workbench/table/chair legs to keep them from sliding around and/or scratching things up. thanks.
There are many many things that can help. I like urethane rubber because it holds well and is incredible durable. It’s a little pricey.
https://www.mcmaster.com/products/urethane/thickness~1-8/
I’m sure others can weigh in here.
terrific. thanks.
How long do your Wood Slicer bandsaw blades remain sharp before you switch them out and how often do you clean the tires on the wheels? I ask because I roughed out and octagonized the parts for 5 chairs from red oak and noticed that towards the end that the effort to feed the parts through increased but not a lot. Also my saw has a good dust extraction system but sawdust still built up on the tires. Any tire cleaning secretes?
Also I had to change out the blade because it began mysteriously pulsing back and forth. On inspection I found the weld was cracking. Highland sent a replacement under warrantee.
The new blade made a big difference in cutting ease and I noted that it told me something about how parallel I was cutting to the fibers regardless of whether I was cutting across or with the annual rings. While octagonizing the last of the sticks, when the fibers were dead parallel to the blade the sticks almost fell through the blade. The sticks with slightly wonky grain required moderate index finger pressure through the blade. I also found that I could check the octagonized pieces for straight fiber by progressively flexing the triangular offcuts, sawn side on the outside of the bend, until they cracked and noting the effort needed before they cracked.
The last question/observation was that when I cut the arms for the Gibsons from boards where the faces and sides indicated dead straight grain that the grain along the edges the length of the arms appeared wonky because the side view of the annual rings indicated run out. Is this something that you have observed? Perhaps it is just an illusion produced by the curve of the arm slicing through the curves of the annual rings?
Thanks!
We go through about four WoodSlicers per year on each band saw. Their cutting action slows down as they are used, but it’s usually obvious when they need changing. They don’t have that grab-your-flesh feel when you touch the teeth and you have to push fairly hard.
Broken welds are common in all band saws. What counts is how the company responds to the problem. Highland always comes through for us.
On curves, you are seeing an illusion. Straight grain, when cut curved, looks curved. Curved grain, when cut curved, can look straight.
JohnG- I clean my bandsaw tires after each cutting session. With the saw power off (unplugged is safest), I hold my shop vac hose in my right hand right along the tire, and with my left hand lightly scrub the tire surface with a chunk of blue 3M scouring pad (has no abrasive in it) or #0000 steel wool. Usually 2 or 3 spins of the wheel get it clean. Soft wood with sap can leave a real mess on both tire and blade, you may need a cleaner for that. Usual woodworking sources will have bandsaw tire and blade cleaners (Highland, Rockler, etc.).
Woodturners abuse bandsaw blades more than anyone. Here is an interesting discussion thread describing a few ways to get some extra cutting life from bandsaw blades.
https://www.aawforum.org/community/threads/how-to-quickly-sharpen-bandsaw-blades-without-removing-them.22072/
Hello Chris,
Do you have any experience with Ponderosa pine.
I’m in Northern California and can’t seem to locate any sugar pine.
Some friends recently had a huge Ponderosa come down in a storm and we want to mill it.
Would it be a good substitute for Sugar pine or white pine?
Thank you
Ray
I’m sure I have. The real problem with pines that are not in a forest is that you have tons of knots. If the tree has a long section that is completely clear of branches, I’d open it up to see how it looks. Like all the white pines, it is soft and works well with hand and power tools. But the prevalence of knots makes getting clear sections difficult.
Thank you, we’ll give it a try.
This tree is in a heavily wooded property and there are no branches for the first 30-40 feet.
All the lots in the area are minimum 10 acre parcels.
Sounds promising!
Hey Chris, thank you again for creating this open wire.
My question this morning is, could you add a Sharpen This video for sharpening hollow chisel mortise bits?
There are videos online but nothing matches your brevity and your approach (get it sharp enough and get back to work). Also having used your other videos, both for sharpening and chairmaking, I trust you most.
Will add it to the list. Thanks.
I’ve done a couple staked stools using 2x? wood, white pine 2x4s glued up edgewise for the tops and SYP (ripped edges from 2x12s) for legs. Leg/Seat joints are Veritas reamer/tenon-maker. With the thinner stock (1 1/2″ minus a bit for surfacing), I’ve had to add stretchers to get the stiffness I’ve wanted.
To get beefier parts I’m thinking about gluing up the whitepine 2x’s face-to-face and gluing the legs up to get up to 2+” square.
Any gotchas you’re aware of with this approach?
I’ve saddled edge glued white pine before, worked OK. Any opinion on how the face-glued parts will saddle?
Thx,
-Mark
If the chair is painted, you won’t have any problems with your approach.
Saddling or tapering a lamination can look very odd when it has a clear finish on it.
Hi Chris. I’m removing a couple of old chokecherry trees from my property line. They are 9″ and 12″ diameter. My neighbor who is quite handy with a chainsaw is going to drop them, and had planned on just turning it all into firewood. I’ve never harvested wood myself for a project before, so I am lacking in the skills, tools, and space necessary to efficiently mill trees. However, I’d like to try save a bit for future projects, as much of it seems straight grained, and has a beautiful color to it. There looks to be a good 7-9′ of unblemished trunk on each. The cutting is happening tomorrow, so I’m a little short on time for logistics. What would be your recommendation for processing and storing some of this in a garage shop type setting? I have plenty of room outside as well.
First order Sam Sherrill’s book “Harvesting Urban Timber.” After the tree is cut down, buck up the straight section into lengths that are good for furniture: 24″, 36″, 48″. I’d split them lengthwise with a sledge and wedges (metal and wood). Paint the ends with Anchorseal. Sticker them in your garage win an area with good airflow.
That’s the quick and dirty answer. Sam’s book will help you the rest of the way.
Awesome. Happy to add Sam’s book to the collection. Thanks much.
I’m looking for advice on sharpening the blade in the Ray Isles rounding plane.
Specifically, do you put your usual 35 degree secondary bevel on these?
Also, how do you deal with the section of the blade that angles away from the straight part of the blade?
Thanks,
Mark
For that plane I sharpen it freehand and press the entire straight section of the bevel against the stone (no secondary bevel). After I do the straight section, I focus on the curved-away section, again no secondary. Then I remove the burr on the back.
What is your preferred method/tooling for doing breadboard ends on say a dining table?
Plow the groove and bash out the mortises with a chisel. Cut the breadboard’s shoulder on the tabletop with either a table saw or a handsaw against a fence. Remove the bulk of the waste with a chisel, chopping from the end. Clean up the tenon with a straight rabbet and shoulder plane.
If I am in a damn hurry, I will cut the entire tenon with a dado stack in a table saw.
Chris, in you video on scraper sharpening you we using a vise with soft jaws. It seemed to be sitting on your workbench without and clamp. My similar vise would not be steady without something to anchor it. Did you have some way of keeping it steady that wasn’t apparent in the video?
The vise weighs about 50 lbs., so is its own clamp.
Chris, what type of abrasive paper do you prefer? Have you tried Serious Grit paper?
We use Abranet and haven’t spent a lot of time doing comparisons. It works great and we can get it easily.
I have not heard of Serious Grit. Sorry!
What do you use to write on dark wood like walnut?
I knife in my lines, then I follow that with a clay/ceramic fabric pencil (with pink or white lead).
https://leahday.com/products/ceramic-fabric-pencil
I have also used a pounce bag at times (messy).
Excellent! I am happy for your achievement.
Hi Chris , Any idea when Lee Valley might have the Cricket Table book in stock ? I have asked their Customer Service a few times but haven’t been able to get any answers . Thank you
We just sent a huge order to Lee Valley last week (I think). If I remember correctly that book was in the load.
FYI, we are currently trying an experiment with shipping to Canada from our warehouse. You might try buying it through our store and seeing if the shipping is reasonable enough for you.
Excellent news!
Hi Chris,
For attaching cleats to a board composed of 7/16 OSB overlaid with 1/8 tempered hardboard would clinched nails be appropriate, or would you recommend screws? I rarely work with composites, so don’t have experience with how well they hold nails. For reference, the cleats will be holding braces, hammers, and chisels, primarily. Thanks!
OSB takes screws with gusto, and that’s what I typically use when working with the stuff. I suspect clinched nails would be fine, however.
Thanks for taking the time for questions. I’m referencing Fitz’s FWW Dutch tool chest article and wondering if there is a typo in the dimensions for the front. It states 25″ long in the overall and exploded views, but then marks the tool rack as 25 1/2″, which wouldn’t fit inside the carcass. Is the front meant to be 27″, or am I just being dense?
The front should be 27″ with the tool rack being 25-1/2″.
Good morning,
I was wondering have you ever encountered hackberry wood? I am using it for legs of an Irish chair right now. I’ve been enamored with it as a chair wood what with all the two to six inch diameter tree I ve seen in the woods around here bent over where another tree would break and holding up a larger tree.
I haven’t used it, but I’ve seen it for sale at Keim Lumber in Amish country. Looks like elm. I’d be thrilled to find some bent branches of the stuff….
If I find some I will try and bring you some when I come down for Jogge’s class. No promises but I will see. And it does look like gray elm! Works like it too. But the strength rating as far as I can tell is similar to ash. Which brings me to my idea which came to me during my morning chair sit and think. To learn how the Welsh tied stuff to grow it into curved shapes while still in the ground. Need to talk to my wife’s coworker, an arborist and land manager.
Anarchists Workbench question I can’t get a solid answer to:
Is there a range of moisture I’m hoping to reach when I bring my SYP boards home before I start ripping them? I’m also unsure if I should rip them first, then let them dry before planing and jointing them.
Thanks Chris. You’re seriously the best.
Crosscutting to length is the first thing. That exposed the end grain, where most of the moisture exchange occurs.
The target is equilibrium MC. You can determine that for your shop by taking a reading of a piece of SYP that has been sitting in your shop for a few months. Compare the new board to that sample. In our shop, SYP ends up at 8 percent MC. Your shop might be different.
It generally takes less than a week for most boards to reach equilibrium if crosscut to length.
I have a lovely holdfast made by a Slovenian blacksmith on Etsy. It’s solid, and a joy to look at with an oak leaf shape worked into the pad. It’s in the modern standard size to fit a 3/4″ hole.
Recently I came across a vintage holdfast with something like a 3cm diameter (about 1 1/4″). I’m curious to try it, but I’m also a bit worried since I’d need to redrill the holes on my bench, and I’d loose the use if my current holdfast.
I know you’re a fan of 1″ holdfasts over the 3/4″ versions. Is the difference really that big? Is it worth it?
Modern holdfasts are 3/4″. Old ones are thicker – 1″ and up. They rarely use the same size hole with any reliability. You can have two different arrays of hole on your bench, or stick with one size (we do the latter).
Obviously, we like the thicker ones because that’s what we make. The weight and tight tolerance between the hole and tool’s shaft really work well.
The Lie-Nielsen event went pretty good. Do you have any thoughts on holding other similar tool events?
There is nothing in the works. Events like that are expensive for the toolmakers, so I suspect they will be few and far between.
Chris,
This’ll be my last question/comment of the day. Scouts honor. Have you heard the new John Moreland album Visitor? Some of the most beautiful music I’ve heard. Been in our car cd player for two weeks and running now.
Yup. It’s good stuff. I’m glad he turned his back on the Casio synth from the last record.
Big subject, short question:
Post and rung chairs vs. stick chairs (like you make).
What are pros and cons of each? Is it just personal preference and availability of wood? Or is there more to it? Or would the answer take a book?
(Otherwise, just a big thank you for the knowledge you share!)
I think the major difference is the materials and tools at hand for the individuals. They are both folk chairs. They exist simultaneously in many cultures. They can both be incredibly comfortable.
Ladderbacks need sections of dead-straight wood, usually riven. The chairs get their strength from a moist/dry construction between the posts and rungs, and the chairs typically use a paucity of materials (except in extreme cases). They are typically lighter in weight. The seats can be fragile and require maintenance.
Stick chairs need a thick seat, which is where its strength comes from. The moisture content of the wood isn’t as important. The materials can be a bit squirrlier. You need more material for a stick chair, but it can be of a lower quality. The chairs are heavier in weight. But there isn’t much maintenance.
These differences are all pretty obvious, I’m afraid. Wish I had better answers.