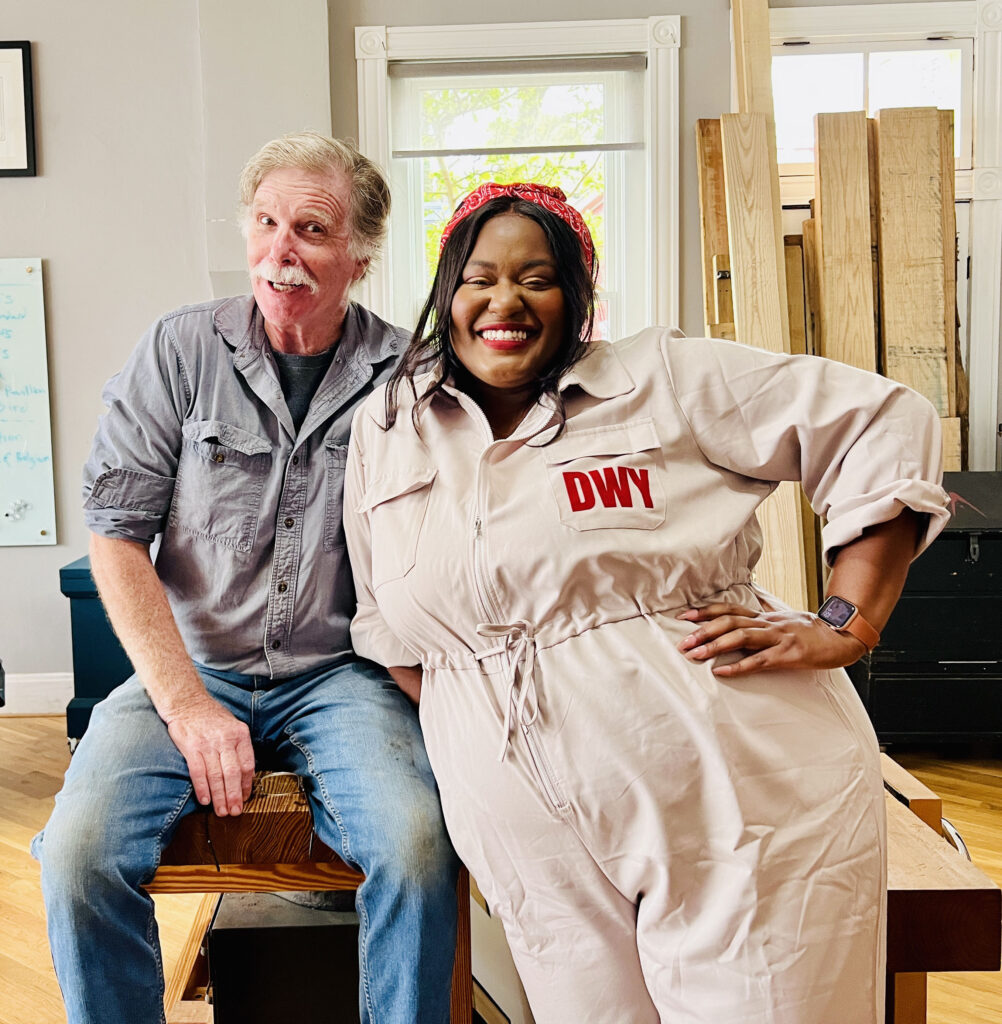
Update: Comments are now closed.
We’ve had a grand week of visitors and video shoots. Roy Underhill made a quick trip to town, then headed a little farther northwest to experience eclipse totality. And Whitney Miller, author of “Henry Boyd’s Freedom Bed,” spent the week recording a video on how to make a Swedish tool chest. Not only is she the video star, she’ll be doing the editing…so you know it will be more entertaining than most of our videos! (Look for it in our store later this year.)
After a busy week, it’ll be a bit of a relief to sit at the computer and answer woodworking questions – so queue ’em up in the comments section below, and I’ll answer. As will Chris, once he’s back late today from a whirlwind trip to the Chicago area to drop off the projects for “The American Peasant” with Narayan for photography.
As always, brevity is appreciated.
Comments will close at around 5 p.m. (but we may answer later in the evening).
– Fitz
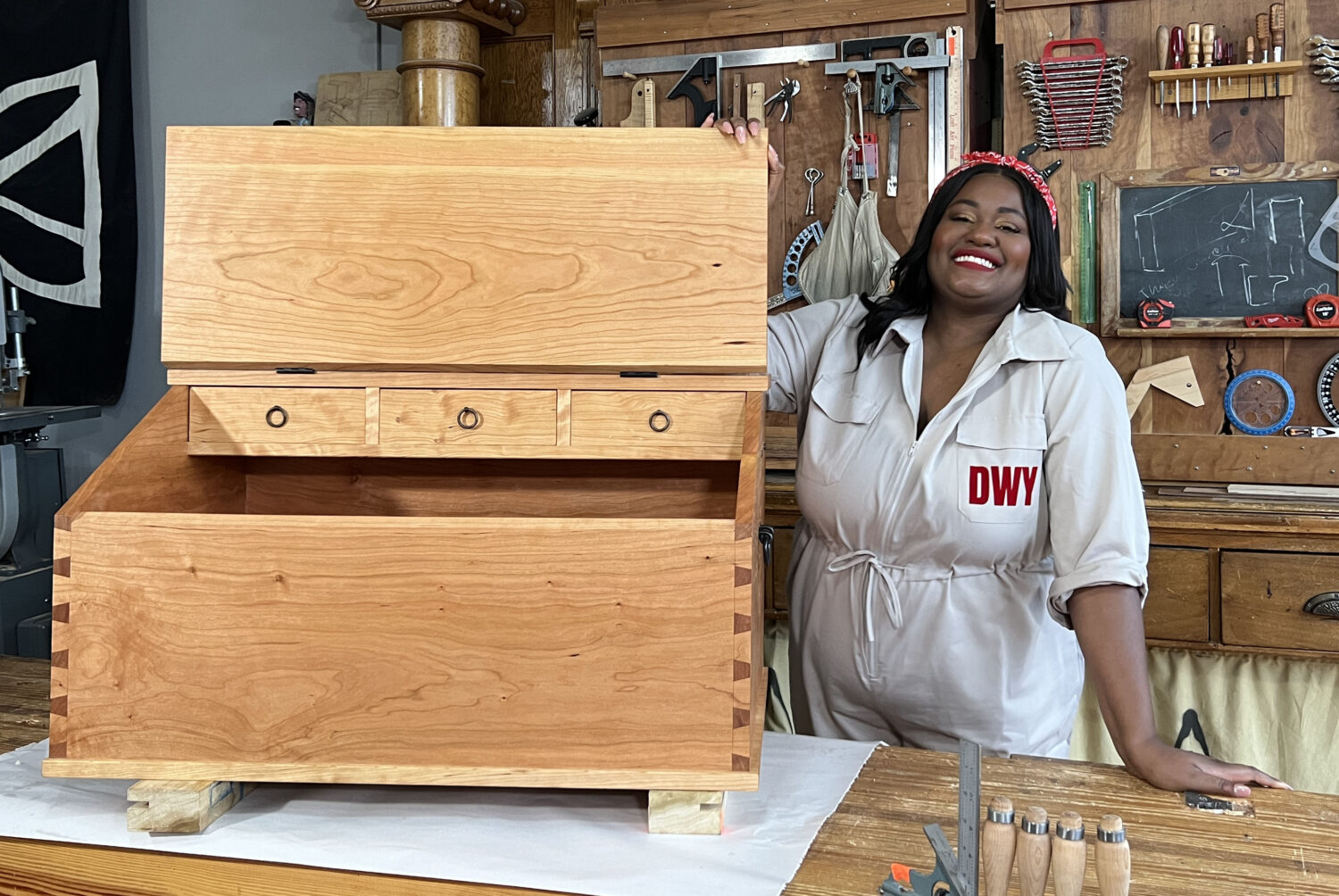
Fitz: are you all going to create a book on the patterns and inscribing techniques that I saw carved in recent painted boxes? I have the cutter but not sure how to begin with the patterns. Thanks as always. Bob
Yep – all that will be in “The American Peasant,” which will be out later this year.
I have a small turning gouge that I rarely ever use. It is made from High speed steel. Would it word for a card scraper burnisher?
Oops, Jeff, see a few messages down for my reply about the turning gouge.
Depends on the scraper and the gouge. Old scrapers are softer and can be turned with a gouge or screwdriver. Newer scrapers are harder and do better with carbide. Only one way to find out…
Hi Meghan,
I’m working on restoring a plane and am about to re-finish the tote etc. I have a leftover batch of the LAP shop finish I prepped a couple of years ago now when I made my workbench which is still fine and I’m considering using a few coats of that (for colour) instead of shellac, and then finishing with some soft wax (also LAP formula) to schieve a nice smooth feel. My question is: do you think that’s a reasonable path or overkill? Should I just pick one finish and run with that? If so, which one?
Is this a plane you’ll be using? I’d probably just go for the oil/wax; feels better. Either (or both) will wear off in use and need more finish, and the wax is easier, so…
In the Anarchists design book, it shows how to drill angled holes with a drill press. I haven’t seen that technique in Chris’s other books or blog entries since then. Is it an effort to make chair making more accessible or was there something about using a drill press that made Chris move away from using them?
It requires a not-dead-nuts-simple jig (I think he named it “Banjo,” if memory serves). And he’s moved away from using all but the most basic of jigs (ie “platforms”) in his current chair work, as well as a smaller set of tools. (She said, putting words in his mouth…)
Do you have any experience with wooden tongue and groove planes? I have a set that seem in decent shape but a recent attempt to use them resulted in monstrous tear out and all kinds of dramatic bad things (unusable boards).
Is there an obvious first thing to focus on? Maybe the cutters aren’t as sharp as I thought? Maybe the cut is too aggressive? Or is it just going to take me a while to get my form right? I’m largely taking Chris’s guidance on using a metal tongue and groove plane and transferring it over.
Love these open wires, I read and lurk every week! It’s an incredible resource and you guys are awesome for doing it.
I’ve only used them a few times, so these are somewhat novice thoughts. But…sharp as possible, and take lighter cuts. Also, make sure you’re laying out your boards so you’re working with the grain. And any wobble can result in a broken tongue or groove – stay directly on top of the plane and don’t move it side to side at all.
Excellent thank you!
I use wooden tongue and groove planes and get good results. The tongue has a slight inwards slant which I guess ensures it is tight on the outside of the joint. See if your blade looks like that and sharpen accordingly. Make sure you start at the far end of the work. Use short light cuts sharp as you can get. Nice square stock to start with. Good luck!
Thanks Roger!
Jeff, I’m a turner. I’d say that as long at the gouge is a harder steel than the card scraper, it would work. HSS turning tools from Sorby or Crown would likely work, low cost “HSS” mystery turning tools from Amazon, who knows. And there is one really easy, free, non-committment way to find out… Even if it doesn’t, you won’t hurt anything trying. My first burnisher was a burned-out valve from an old car engine cylinder head.
Hi! When will the Roman Workbench Build video be released? Thanks!
Later this year (but not much later). Chris and Kale have to finish it, but that should happen soon.
Awesome, Can’t wait to see the video.
I really enjoy the yearly “what’s inside my ATC” articles. Any plans to do similar articles with guests like Roy? Would love to know the story behind some of the tools he uses and why they are in his box.
Well, I know that in the chest Roy brought to his recent class were all the tools needed for sash work (which is the typical pattern with visiting instructors – bring only what you need). You can see a video of his on my IG page: https://www.instagram.com/p/C45sA4-uX37/
I like the idea of the internal drawers of Whitney’s Swedish tool chest. Can’t wait to see more.
The Anarchist’s Design Book says to use a diamond paddle to sharpen the LV tapered reamer. What grit (or grits) do you use for that? I’m looking at a paddle right now that comes in 15, 30, 60, and 150 microns. Thanks!
He’s changed his tune. He finds it better now to use a “universal sharpener”
https://www.leevalley.com/en-ca/shop/tools/sharpening/files-and-hones/66738-universal-sharpener?item=09A0332
Put the reamer in a vise, blade up. Put the flat carbide onto the inside flat of the blade’s edge, tilt forward, then “scrape” forward and you’ll see a little bit of steel coming off. Do this two or three times. Then gently polish off any burr with a high-grit stone or sandpaper (being careful not to change the edge geometry of the blade). Wipe it with a woobie. Repeat on the other blade
(This is one of the “Sharpen This” videos…as of 12 days ago. Not that I’m trying to upsell you – I’m not!)
Good morning Chris and Megan,
As I know that you are regular users of Mirka Abranet for your sanding needs, I was wondering if you have explored/have an opinion on the performance differences (if any) of the regular (aluminum oxide grit) versus the Ace (ceramic grit) version?
Cheers and all best,
Mattias
I have not, nor, as far as I know, has Chris. I try not to explore sanding. I hate sanding.
Good morning. I saw Chris’s post about using the sandwich mortise method to drill the arms and seat of the Peasant Chair. Can that method be applied to the comb-back chair shown in the video ‘Build a Stick Chair’?
Not as-is – the short sticks in the peasant chair go straight up and down, and the angle on the back sticks is straight back. So it will/would take some experimentation (which I believe Chris will work on…but not until we’re doing with current projects)
Slight clarification: You can use the technique for the back sticks of almost any stick chair (as long as the back lean angle isn’t too extreme). The complications come with the angles for the arms. I’ll be writing more about this method. I just need to get a book to press and behind me first….
Regarding the Swedish tool chest, can you share any info about it, such as case and drawer demensions, if you implement any tills, etc? Thanks!
All that information will be in the video, and I’m sure we’ll talk more about it on the blog, too. But not yet.
The Swedish tool chest looks beautiful. I can see it as a piece of furniture, rather than a tool chest. But what does it weigh, in cherry? I’m not sure I could carry it empty, much less full of tools.
Agreed as furniture. Maybe even with an optional legged-stand to elevate it off the floor.
I was thinking of various bases on which to put it. I’d also make that upper unit a few inches shorter if used as furniture. It sure is pretty.
Oh – this one is not for travel. I can’t lift it empty. We planned to use a lighter wood, but the lighter-weight wood available to us that day was not pretty. And the cherry was, so…
Do you guys* make use of the spokeshave in your shop? It was a favorite of J. Brown but I rarely see one on your Instagram feed…? Seems like the perfect tool for chairmaking.
*guys (plural) used to describe a group of people that can also include females.
Yep – the curved-bottom one in particular gets used in some chair classes. And I use a flat-bottom one on the Shaker trays I teach. I guess we just don’t show them much!
I do a lot of seat shaping with a flat shave (a 151). Chris Williams and John Brown modified a curved bottom shave to saddle seats. That was the primary use of that tool for them.
“Folks” works. Except in cities in which street gangs are grouped as “folks” or “people”.
Is there a way to donate used woodworking books to students who received scholarships? I have several books I’m no longer using and would love for them to go to someone who could use them.
I’m afraid we don’t really have room to corral extra books until they might be needed. I’d check with actual woodworking schools – maybe https://schoolofwoodwork.com/ (which has a generous scholarship program)
Not a question, but to comment on a beautiful chest! Gorgeous!
Hi Megan, OCD inspired question. Would you reuse the same paintbrush (eg the Wooster Yachtsman) for the second of paint for some object (after having cleaned it as best possible)? Or do you toss it and use another one? Would you ever reuse it for another color? Thank you.
1) it’s CDO. must be in alphabetical order. 2) I’d reuse unless you’re using a $1 disposable brush.
I’ve started saving them but using them for the same or like color only. Mattias cleans his well enough to reuse on any color – so it can be done.
Is linseed oil wax for a white oak bathroom vanity (including countertop) a terrible idea? Internet consensus seems to be that I should use some marine-grade varnish or epoxy, but I’d rather the wood have a more natural feel.
Huh. Depends on how often you want to rewax it, If the answer is “a lot – I LOVE finishing?”, go for it. (I used varnish on mine…and a soapstone top.) We have soft wax on the countertops in both kitchens at LAP, and rewax every 3-6 months downstairs, and I’d guess every 6 months upstairs. But a bathroom counter will likely see more abuse.
I’m trying to convert a drawer in an existing dressor into a cavalry chest drawer similar to one like this: https://www.campaignfurniture.com/campaign-furniture/campaign-chests/cavalry-military-chest-by-an-csl
I haven’t decided on baize or leather for the writing skiver and am looking for tips on sourcing both. For baize, I’ve only turned up a couple UK websites. i love in Omaha, NE. When I asked for baize at my local fabric stores, they just looked at me funny and had no idea what I was talking about. I did find some 100% wool felt, but that doesn’t seem right. For leather, I’ve no idea where to look besides online and haven’t turned much up besides custom sized and gilted leather skivers that look fantastic but are out of my price range. I almost exclusively use fountain pens or pencils so whatever material i go with needs to be ideal for those and I will often use a laptop on top. So it needs to hold up to a bit of heat.
I also don’t know where to look other than online. But a few of the UK websites I see ship to the U.S. (and some offer remnant’s, which are cheaper). And I see a few “desk leather” options as well, some pricier than others. Sorry I can’t be of more help; we haven’t sourced these.
Hi Jesse, amongst other uses Blaise is the cloth on billiards tables. It might be worth checking for local companies that repair and maintain pool tables and ask if they could supply you. My local yacht club had their pool table recovered recently and the old cloth was still in reasonable condition….
There is a Tandy Leather store in Omaha [Tandy Leather Omaha-127
9007 F Street Omaha NE 68127 USA Phone: (402) 571-3339]. They might have a finished leather that would do for a decent price. I tool leather but that is unfinished and not dyed or finished until tooling is complete. I have purchased finished skins to cover wood boxes and I would think a thin cowhide or pigskin would be possible. Just make sure you cut the piece so it is square and use a good adhesive (I usually used contact cement when covering boxes). As long as the leather is smooth and fairly hard it should stand up to the type of writing implements you said you use. Hope this helps.
As people have mentioned, it can be tricky to search for a specific comment that you remember from a past Open Wire. So I have been going through each one and pulling every comment that I find of particular interest to me, and projects I could see myself working on in the next few years.
Topics include: chairs, linseed oil paint, when is the *** book coming out, chipbreakers, linseed oil paint, finish for a dining table, how to shrink the base of an AWB, cats, Wilco, the shop shavings trash can, how to specifically search for LAP blog comments on google, etc.
Hope sharing this doesn’t break any rules (feel free to delete), and I’ll keep updating it when I have time:
https://docs.google.com/document/d/1xBVagSMHgBw5nrgyVQ7iCkRDmY1caZlbz8L4SU86lPk/edit?usp=sharing
I tried to address this by building a little search engine around the comments. Not sure which is easier m, yours or mine, haha. Megan found that it had bugs that gave her concern since she is worried she’ll be the one who gets complaints (which I def do not want. At least the issues she hit I fixed!)
Oops, link here https://lap-open-wire-search.fly.dev/
Probably yours, but I enjoyed reading through them, and doing a quick control+f in the google doc can turn up a lot of useful information! Also one could scroll to a random page if they’re looking for some quick woodworking knowledge.
Yeah the main reason I did what I did was that I found I was too lax putting LAP content in my own docs. I tried it for a while and then would inevitably be like, “where was that inspiring quote about breaking an arm?” and spent ages looking for it.
Good Morning from Sunny AZ! So here is my question for you that I was unable to get answered in my woodworking class or anywhere online for that matter.
Im building a miter jack. I’ve noticed that the q-sawn white oak faces of the jaws seem to shave off differently and easier depending which direction I plane it across the end grain. Is there a proper direction to plane end grain? Parallel with the grain? Perp? Skewed? 🤷🏻♂️There is plenty of info about planing with the grain on the other faces of a board yet I haven’t seen anything on the end grain.
P.s. we finally learned how to use dividers so my crucible order is on its way! Love the bevel gauge i currently have by you all.
As always, thank you!
Huh. I’ve never heard or read anything about in which direction to plane end grain (which doesn’t mean it doesn’t exist…just that I’ve not come across it). All I know is that sharp blades are key, and to plane from both directions, or remove a small bevel at the exit side to avoid spelching. Oh – and a spritz of a 50/50 mix of water and grain alcohol makes it easier to plane.
Too much grain alcohol and my planing becomes very poor quality.
End grain does have a “direction.” But it’s a subtle thing, as you have found. Think of it like a short-pile carpet. It will reflect light a certain way when you brush it one way. And the reflection will change when you brush it the other way.
I try not to combine directions on the end of a board. But it doesn’t make a huge difference when the finish goes on.
Hi Megan
I just built a six stick comb back chair out of red oak. I had board that was. 22’’ Wide and about 2.25’’ thick so I made the seat out of that. I am in the hinterlands so all I have is hand tools. Any way the chair is great (good plans Chris). But the seat developed a deep crack in the center. I cut a shim the depth of the crack a glued it in. Looks good. Should I reinforce the seat underneath or will the glued shim be enough?
I don’t know for sure w/out seeing it, but I’d err on the side of caution (as I do with most things). I’d put a mending brace or two across the split on the underside. If you want it to look fancy, strip the zinc and add gun bluing to darken it. Or get a blacksmith to make you an iron strap.
Yup. The traditional repair for old stick chairs is a metal plate with four screws or so. That usually does the trick.
Hey there! I have a very novice-level question.
I’ve ripped an 8’ 1×12 poplar board into four equal-width sticks. Are there any special considerations or techniques involved in 4-squaring long, narrow stock by hand?
Not that I know of – same as 4S-ing any board. Flatten one face, then use that as your reference face to square an edge – then those are the two reference surfaces for the other two.
I do it on the bench and against the planing stop. Plane one edge. The plane the opposite face parallel. Then plane the edges square. Gripping narrow stock with a vise is difficult.
Good morning, I’m sorry if any one has asked this previously but have you gotten any feedback on piggy no wiggly from luthiers?
My understanding is that luthiers use a higher gram-strength glue (dries harder but is more brittle). But perhaps there’s a luthier reading this who can weigh in?
Morning Megan,
Where within LAP can I find out more about the the Carpathian coffer and Carpathian wall cabinet? I wonder if they have a relation to the Carpathian Mountain range in Eastern Europe?
My grandmother was from the foothills of the Carpathians in Western Ukraine. The carvings remind me of Ukrainian easter egg decorating with folk patterns. The patterns had symbolic meaning.
This will all be covered in “The American Peasant,” due out later this year.
Howdy!
Now that I’m logged in, Howdy again! I am getting ready to figure out how to attach legs to a coffee table. It would be a good challenge to do it using tapered mortise and tenons. What’s your favorite way to cut these?
Tapered tenon cutter and matching tapered reamer
https://blog.lostartpress.com/2015/03/11/the-staked-furniture-toolkit/
https://blog.lostartpress.com/2022/04/14/tips-on-tapered-reamers/
Good morning Megan and Chris, thank you for doing this open wire. I’ve said it before but I’ll say it again: these Open Wires are invaluable to me as I’m sure they are to others. I recently became a carpenter by trade (I’m 44 and started when I was 42) and I’m a lifelong woodworker. The information you give freely on this platform has boosted my knowledge and helped immensely in my trade and my craft.
I have a chair question today: When I drill mortises for the sticks in the armbow and seat, I occasionally get some wandering. At least that’s what I think it is. The top of the mortise where the bit enters the wood sometimes has a little roundover, which then leaves a gap in the finished joint. The chairs I’ve made are for my family, so at the moment I use wood filler and just live with it, but I’m working my way towards selling these chairs and I’d rather hold a higher standard. I assume the bit is wandering, but I’m not sure. Why does this happen and how can I eliminate it?
Chris will likely have a better answer later, but: in classes, we see this fairly often. And it typically indicated that the person is not pushing the drill forward in a dead-straight trajectory. If they’re leaning at all in any direction, the bit will create that roundover (or tearout) at the top of the mortise. Is the roundover always in the same place in relation to where you’re standing? If so, that can help you diagnose and fix any leaning issue.
But if it truly is wandering, use an awl to locate the starting point and give the bit a place to start. I guess it’s also possible the shaft isn’t straight. Do you get any wobble when drilling straight down? (Or test it in a drill press?)
Good morning and thanks as always for doing this – often the best part of my Saturday! I’m building the Packing Box to improve my hand tool skills. It was going well (really well) until …
Nails. Can’t say I love them. Really glad I did the bottom first, so I won’t often have to look at how much of a mess I made. I figured out a bunch of things already, but … how hard should I have to hit to drive the nail (which tells me something about the pilot hole size)? In Chris’s slideshow, he seems to be using the small Warrington hammer to drive them home, and a bigger hammer to clench. I’m using soft pine and couldn’t possibly drive the nails through the cross piece and bottom with the small hammer, so I suspect that my pilot holes are too small.
Ugh, that wasn’t meant to be a reply, sorry.
That’s what it sounds like to me. It should be cake to drive the nails through the pine. Then it gets difficult when you turn the nail against the steel bucking plate (or use a second hammer to turn the nail). Try a larger pilot in scrap.
Thanks! This has been a great learning project, as you have said, and I agree that it’s worth building. I’ve learned a ton, and in an arena where I don’t mind the flaws so much.
Gaps like this are caused by the bit cutting to the side of the flutes. It happens when you tilt or steer during the cut. You can reduce the side-cutting by sanding/dulling the side flutes. And practice will do the rest.
Gaps like this are caused by the bit cutting to the side of the flutes. It happens when you tilt or steer during the cut. You can reduce the side-cutting by sanding/dulling the side flutes. And practice will do the rest
I am looking to upgrade my old jewlers feet saw that only tensions the blade using the bar adjustment. It has worked over the years for wasting dovetails but is not ideal. There are tons of opnions around frett saw vs coping saw. What are yours? I live in the Black Hills of SD where farm and pig stores are in every town but the nearest woodworking store is 8 hrs away. Thanks!
You might not like my answer: I use both. I like a fretsaw for thinner work (1/2″ or 5/8″…and sometimes 3/4″) and a coping saw for thicker work (sometimes 3/4″, 7/8″, 1″). And when I am actually coping (i.e. using it to cut curves/fit moulding), I use a coping saw (its blade is less likely to flex). I have a Knew Concepts fretsaw that I like a lot…but it’s an early one and I’m not a fan of the knobs KC is now using (I can’t tighten them sufficiently without using soft-jaw pliers). If you get one though, make sure you get the swivel knobs. (And I haven’t tried the latest “heavy duty” version – maybe it’s better– dunno.)
On the coping saw: You can make an inexpensive one work a bit better by putting a split washer under blade holding mechanism where it meets the frame. I love my Blue Spruce coping saw … but it seems to be no longer available. (Too bad – I was planning to buy the fretsaw attachment!) So I guess I’d recommend the KC? It was my favorite until I got the BS. But I have a replacement handle for the KC that’s more comfortable for me.
I very much appreciate your honest informed response! No one tool is perfect for every application. I generally work in thicker woods, so a coping saw it is. I will hold onto my my old jewlers saw for now for the ocassional drawer until the next project is of a scale that it necessitates an upgrade.
Blue Spruce had an “Ultimate Coping Saw” but discontinued it. They are working on a improved version. Might be out by end of year, but hopefully sooner. This saw is sweet in that you can turn the blade while using. Top quality.
Question for Chris; when you post about your chairs and it’s clear that you value something bordering on perfection. Clean lines, extremely few mistakes, etc. I find this hard to square with the historical chairs you write about at times (“this chair looks like the maker had a gun to his head.”) Is it that you can’t give yourself permission to build in that style (casual, sloppy, etc) or you think people wouldn’t buy them or what?
I can’t deviate from my “factory settings,” which are to push everything to the limit of my skills. I suspect the makers of the original chairs were doing the same thing, but were limited by their experience, materials and tools at hand.
Not too many woodworkers are willing to work “sloppy” (at least ones who sell their work).
While I was reading the draft of The American Peasant on the plane to Seattle yesterday I came up with an actual question. But now I can’t remember it. While I was reading, I was listening to Margaret Glaspy’s album Echo the Diamond. The song “Hammer and the Nail” came on while I was reading the chapter about nails. So here’s my question: Have you heard this album? I think you’d like it. It’s easily my favorite album of 2023.
I have not – but I shall have a listen – thanks!
Any experience with the hybrid filing that Bad Axe Saws recommends versus a rip or crosscut filing? Is it easily reproducible for DIY resharpening? Any comment on their saws in general? Also, any experience with LH Noble (Richardson Bros?) saws?
Hybrid filing works OK to cut both rip and crosscut…but not as well as two saws with a dedicated filing for each cut. But if you have room (in your chest or wallet) for only 1 saw, it’s a decent choice. I have two Bad Axe dovetail saws, and they’re the ones I most often use – in large part because the handles are sized to fit me (and as far as I know, BA is the only retail maker that offers handles in different sizes – though many custom makers will fit a saw to your hand). I have not used an LH Noble saw.
And on sharpening at home, as far as Matt Cianci tells me (and will tell all buyers of “Set & File” when it’s available in a few more weeks), hybrid filing is as easy to maintain at home as rip or crosscut, and he recommends it only for backsaw.
I’m building some stools for children and am planning to extend the legs for use at a regular table as suggested in the plans. Should I keep the same rake / splay angles (for a wider footprint), and should I move the stretches down so that they’re still about the same height from the ground?
A quick mock-up in scrap will give you your answer. Usually taller stools have less rake-splay. And they usually have an extra stretcher or two. There’s aren’t hard-and-fast rules. So it wouldn’t hurt to imitate the structure of other stools of the same height that are sold at furniture stores.
Have you considered the construction of the Galilee boat, see for example BibleLandsMuseum.com. The planks are held together with mortise and tenon joints. There is a mortise on each plank and the tenon is a rectangular board. The joint is held together by two pegs, one in each plank. The museum experts think that expansion due to water is what kept the joints tight. Surely, this must be an example of drawbore some 1300 years earlier than Hayward Volume III suggests. Such a joint could also be useful for clamp front chest construction.
Loose-tenon joinery has been around for a long time and continues to be used. I use it in my chair seats and pin both ends of the tenon to help hold seats together. This form of construction (for boats and otherwise) has been mentioned (and found) among many ancient wooden artifacts.
Question(s) for anyone with ideas:
1) are you aware of a side clamp handle that works with the “DEWALT 20V Max XR Cordless Drill?” I think this name might apply to multiple products, but the side clamp handle that I tried hasn’t worked. The drill I have seems to be a pretty compact size.
2) from Ed Sutton’s excellent article about centered tenons (https://edsutton.substack.com/p/better-than-sex?utm_source=profile&utm_medium=reader2) I really like the idea of mounting a long vertical rod along the center seam of the drill. With my high bench + carver’s vise, it isn’t so easy to keep bending over to watch the operation from above. I have a bubble level glued to the top of my drill which lets me easily see the up/down position from behind the drill, and I think if I can get a rod mounted, I’ll also be able to see the left/right position easily as I drill. So any ideas about how I can get a vertical rod, maybe the same hex steel material that works with the GoDrilla, mounted to the top of the drill, along the center seam?
Thanks!
What is the best ratio for the tongues on breadboard ends?
I usually make the tongues’ thickness one-third the thickness of the top. The tenons on the tongues is usually four or five times the thickness. The length of the tongue is typically the same as the thickness (i.e. 3/8″ thick x 3/8″-long tongue).
thank you.
My Dad recently got a sawmill and he has a pile of logs he’s starting to saw up. So far, he’s just flat sawing them, and just kinda feeling his way through the process. I want to get him a book for Father’s Day about sawing up logs. Which do you think is better for him? “Cut and Dried” or “With the Grain”?
Thanks!
I’d probably get him “Harvesting Urban Timber” by Sam Sherrill.
https://www.amazon.com/Harvesting-Urban-Timber-Woodworkers-Library/dp/0941936716
Great book. And aimed at the sawyer instead of the furniture maker.
Hi lads and thank you for all you do!
I am going to be spending some months in the (relative) wilderness away from my workshop and bench. I have a hi-vise (which I am sure I will be able to attach to something…) but I’m wondering if you would have any suggestions I could build to go with this for a relatively portable way to hold work? I’m hoping to make some stick chairs and am wondering particularly about wider parts like seats.
Thank you, and if any of the LAP team are ever in need of a pint or hospitality in the West of Ireland look me up!
Philip
I make chairs on a low Roman workbench and a carver’s vise/hi-vise. The bench is just a plank with four legs that you can knock in and out.
I’ll give it a go – thank you kindly!
Hi Megan and Chris,
I’m looking at possibly acquiring that little 10” bandsaw that Chris mentioned a while back. My questions are, apart from the comb, what other parts of the chair making process do you find it most useful? Any limitations with that size saw in regard to chair making?
Thanks,
Patrick
Patrick,
You can use the 10″ band saw for everything in making stick chairs:
Sawing out and octagonalizing the legs/sticks/stretchers.
Sawing out the arms.
Sawing out the seat
Cutting wedges
Cutting and shaping the comb.
The little 10″ guy is perfect for the individual chair shop.
Thanks!
Hello Chris and Megan,
I’m planning to build a low bench.
I have some 3” thick ash for the top and legs.
If I saw the legs at roughly 3” square, is an inch and a half cylindrical tenon strong enough?
Bench will be 6’-7’ in length and have 4 legs.
Thank you
Yes. Absolutely yes.
Good afternoon! What grinding wheel does Chris use for his hand grinder? I can’t seem to find one for that size wheel. If anyone has a recommendation for a tool rest that I can mount to the grinding bench I would appreciate it.
I use a 6″ Norton 3X wheel in 60 grit.
https://www.sharpeningsupplies.com/Norton-3X-Blue-Grinding-Wheel-I-Grade-P37.aspx
There are lots of tool rests out there. We had this one in the PW shop and it worked great.
https://www.leevalley.com/en-us/shop/tools/sharpening/jigs-mounts-and-rests/32973-veritas-grinder-tool-rest?item=05M2301
I just use the bent piece of metal that came with my grinder.
That’s what I would use but this grinder seems to be missing even that :/
Thank you!
Some of the projects in Anarchist’s Design book call for large round mortises. Only auger bits I’ve seen for a brace stop around 1.5”, not the 2” required. Would an old t-handle auger work or are those intended for coarse work only. Don’t own a drill press. Thanks!
You can use T-augers. I used construction Forstners in a corded drill.
Also consider an expansive bit. The larger ones with two cutters can cut a range from 7/8″ to 3″. Look for ones with a side adjustment screw. Less likely to change size while using.
Good afternoon. I saw that Roy Underhill was there at LAP and was wondering if he is working on any writing projects. Because I miss seeing him on his show, I am currently rereading all of his books.
I know it’s easy for me to tell someone else what to do in his retirement but it seems that a modern book on making windows using the old methods would be of interest to many folks. It is certainly in his wheelhouse although I’m not sure it would be suitable for LAP.
One last thing, I too am grateful for the time you all take to answer our questions.
He is working on a history of his family. After that, we shall see what catches his muse.
Hi I did a search and couldn’t find anything, can you direct me, or elaborate on “Chris Williams and John Brown modified a curved bottom shave to saddle seats. That was the primary use of that tool for them.”
They ground the sole so it curved a bit in both directions. That’s all I got. I’ve seen them. Didn’t measure them.
No question this week, but a recommendation of the book The Overstory by Richard Powers. It was absolutely stunning and became my new favorite novel, and will probably resonate with everyone here – it touches on humans’ relationship with trees, cooperation vs individualism, forest science, environmentalism, the ethics of direct action (up to and including sabotage) in response to environmental destruction in the name of corporate profit, the power of capital and the state, and how we respond to death. Everything good art should concern itself with.
“When you cut down a tree, be sure that what you create is as miraculous as what you have cut down.” A high bar, but a good one to consider.
I love all of Powers’ books…but my fave is “Galatea 2.2.” I’d say “The Overstory” is a close second.
Unpopular opinion but Calzones are better than pizza!
Especially when deep fried.
I’m cutting shallow (not sure what radius I’ll be using yet) curves in the vertical rails between shelves and want to put beadwork on them using the Stanley No. 66. Would you use a curved spokeshave or a Stanley No. 20 1/2 compass plane to clean up the curve? (I don’t have either. Just a Stanley flat spokeshave.) The 20 1/2 could be faster, of course. Thanks again for all of your patient answering of questions. Looking forward to meeting you someday!
The spokeshave – we don’t have a compass plane. (Will Myers is the only person I know who uses one with any regularity.)
When you use cold pressed lumber to make your arm bows with, what form do you use. Is there a reference in on of your books that I have missed. Thank you for your time and trouble. Joe
P 229 in “The Stick Chair Book” shows it