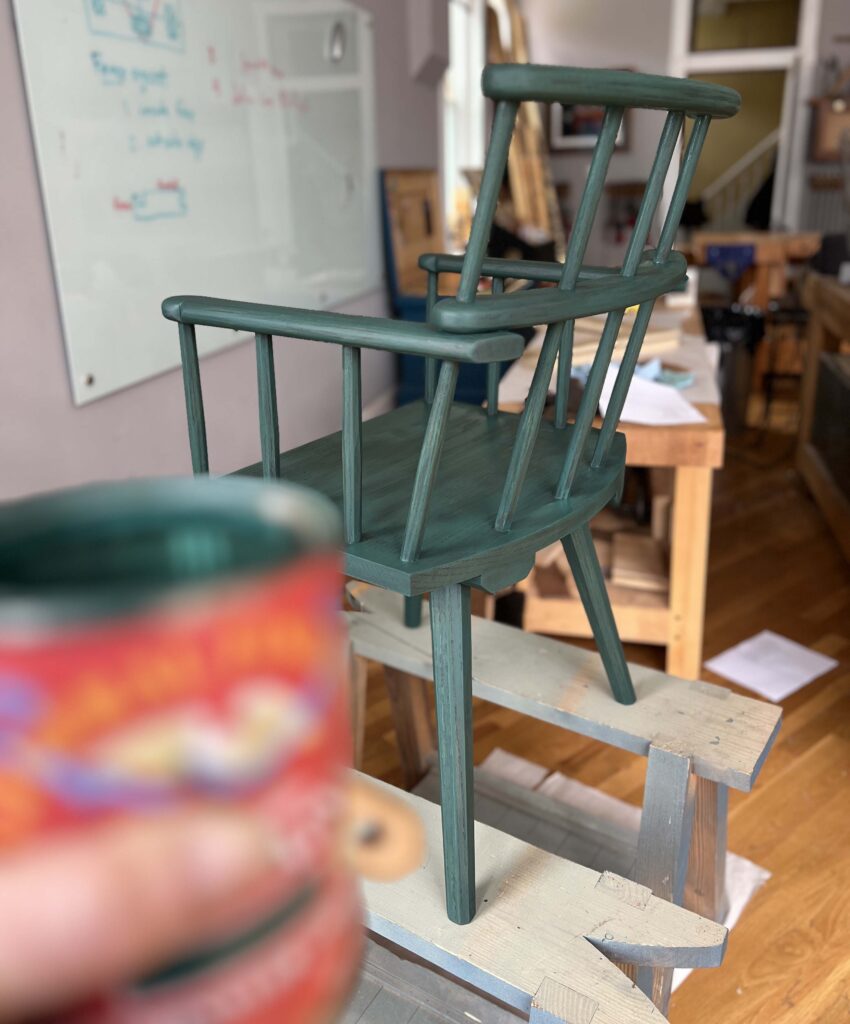
Update: Comments are now closed.
My Saturday goal is to get the final coat of paint on this chair. I just I assume it’s going to need a third coat after Friday’s second coat, because this chair hates me (this is General Finishes “milk paint” in Westminster Green – no longer available, unfortunately). But my other goal is to answer as many of your Jane Austen questions (just to change things up!), cat questions and woodworking questions as I can. Chris is busy teaching a class in making a peasant coffer (featured in his forthcoming book, “The American Peasant”), so he won’t have much time today to get on the computer.
You know the drill: Leave your questions in the comments field below (as always, brevity is appreciated), and I’ll answer (there will likely be a delay between your asking and my answering). Please hold your crazy metallurgy and arcane chair questions until next week.
Comments will close at around 5 p.m.
– Fitz
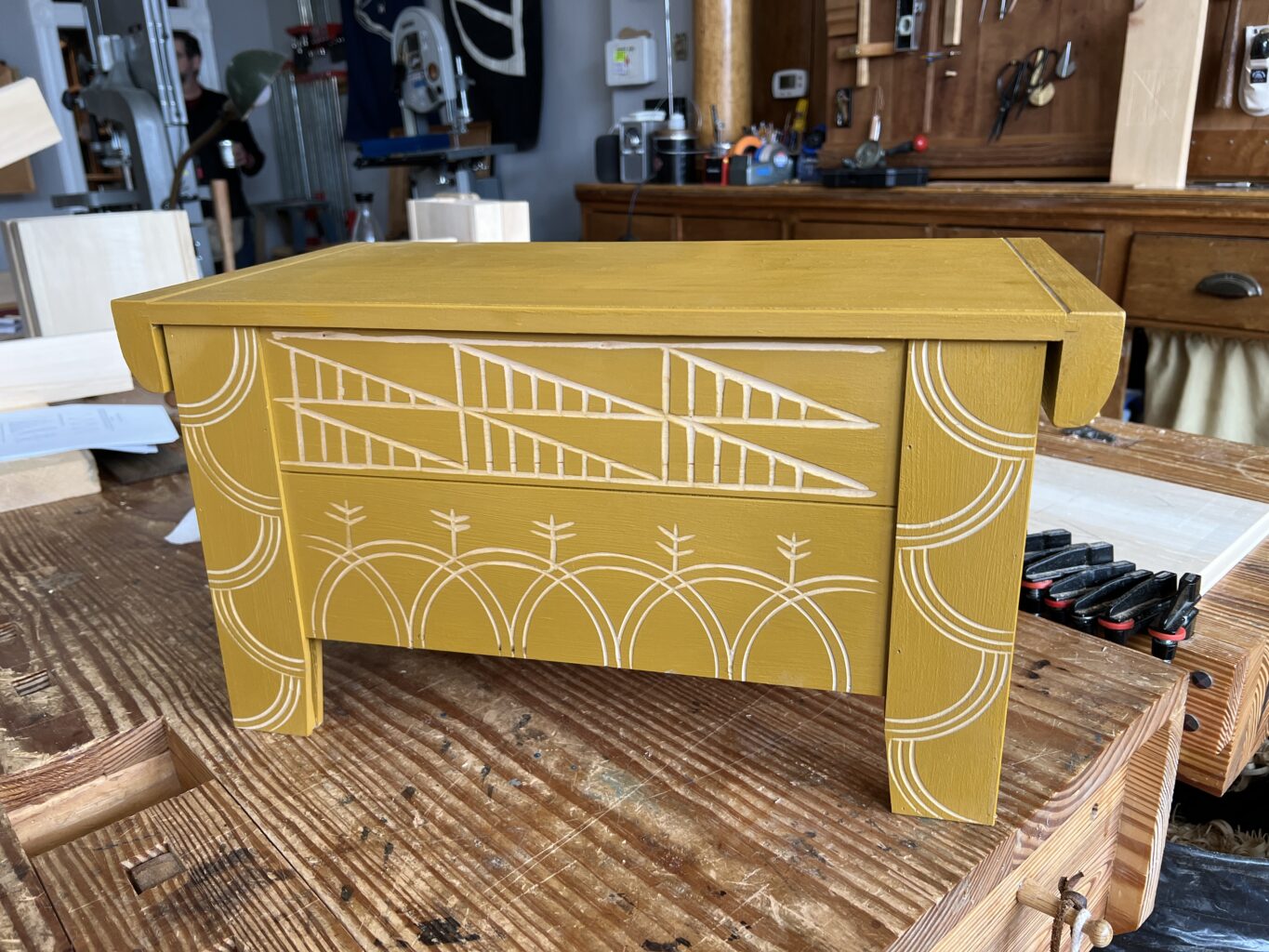
Good morning. Do you use the golden ratio in your design?
Some of my work has ended up adhering to it, but I’ve never set out for it to do so. (And I’m sure Chris has used it in design once or twice, but I can’t recall him using it since I’ve known him.)
Hi Megan. Re Chris’s blog post on canceling the Crucible hammer project. Leaves a void in the market as these Plumb hammers are few and far between. Will Chris perhaps reconsider? In the meantime is it possible to bid for one of the prototypes? Thank you.
They’re not few and far between enough to make it financially prudent for us at the price we’d need to charge to cover time and materials. And the prototypes are aluminum – not good for hammering nails! (So, no.)
Yeah. I’ve spent all morning looking and the first one I found? $95.
I’d rather buy new from a known source than try to hunt down a good used one, taking a chance that I get a lemon. Been burned too many times, wasted too much money.
Ours would have to be significantly more than $95. We don’t think many people (enough people, anyway) would be willing/able to pay that. And FWIW, I find them all the time at antique malls, typically at what I think is too high a price, but in the $50 range.
In Matt Cianci’s saw sharpening book, does he cover straightening saw plates?
Typically, when you have outside instructors teaching, do you contact them first, or do they offer and you accept?
His book has a chapter on fixing problems, including fixing wonky plates. Our outside instructors these days are pretty much only our authors – we extend an invitation to them, but we don’t bug anyone to come teach. It’s challenging to get the book/video/tool work done when there aren’t classes going on, and impossible when there are (no matter who is teaching).
You have built one or two dutch tool chests. What tool layout do you recommend for the interior of the standard DTC?
I remember you mentioning a few hardware resources in the past but I couldn’t find one that might address my specific need. I’m restoring an old rocker that is over 100 years old. It used a few slotted flat head screws that were unfinished. One of them had broken. Do you have a source for vintage hardware such as these unfinished slotted flat head steel screws? Thanks for all you do!
Hey Tad! I did some poking around and couldn’t find unfinished steel wood screws. Places like McMaster, Fastenal, and Bolt Depot carry a variety of sizes of slotted flat head wood screws in 18-8 stainless steel and it looks like there are ways to age/patina stainless steel (if you want to match the existing hardware).
eBay’s selection of NOS wood screws seems to be mostly zinc coated.
If/when I plan ahead, I get all my screws from blacksmithbolt.com (and yard sales on occasion if I get lucky!). In a pinch, I’ll buy at the hardware store and stripe the zinc with citric acid or vinegar.
Here’s a link to the flathead screws: https://blacksmithbolt.com/pages/slotted-flat-head-steel-wood-screws
A fast way to strip zinc from screws is to soak them for 20 min, or so, in a toilet bowl cleaner that contains hydrochloric acid (the Lysol product that I use has 9.5%).
In Anarchast Tool Chest you suggest getting a portable 12″ or 13″ planer, I am wondering if you have a recommendation? There seems to be a range of options from $300 up to $1000. Instead of trusting the internet, I thought I would ask #neversponsored.
For what it’s worth, I have a DeWalt 735. Used the 733 and seized the height adjuster after a massive batch of SYP, too hard to clean. The 735 solves this with exterior threads. Uses three blades, easy to change and sharpen, adjusts well, and a decent built in dust collection system. Have used friends’ smaller/cheaper models and been frustrated by various limitations.
I also volunteer at a local wood studio (Indianapolis area) that has a 15″ Powermatic with helix head. Strangely I actually prefer my home DeWalt. I can consistently run stuff down to 1/8″ thick when I was making backs for ladder back chairs and was struggling with shaving them by hand. Tried on the Powermatic and it was ?too powerful or something. Caught the pieces every time, activating the antikickback safety and destroyed the piece. Defer to LAP of course but that’s one user experience. Best of luck!
For a portable, I’d likely choose DeWalt … and were I feeling flush, I’d get it with a helical head.
I have a Riobi. 13” I got on sale 15 years ago. With a sharp blade it does just fine for the roughing. If I have have some extra cash and nothing else ahead in line I can outfit it with a helical head. I’ll probably do that rather than buying. A different one. Look on face book market place and buy used save some money.
I snagged a barely used 13″ Porter Cable planer for $245 on Craigslist back in January. Keep an eye out on those second hand markets.
Last week I asked about rule joint on end grain and you or Chris suggested vernacular. You lost me on that one???
Ah – no rule joint, just hinges. So the leaf butts up to the top when engaged, instead of a mating cove and ovolo.
I prefer stainless steel litter boxes due to the plastic absorbing that lovely ammonia smell from cat pee. Am I crazy to ask for a wood species and finish to handle a bespoke cat litter box lol
Yes; crazy. (But I can see making a nice-looking box to put around the litter box.)
Good morning! I’ve been trying to hunt down plans or a photo of Chris’ father’s Japanese-style garden bench that Chris has mentioned. Would he be able to share? Thanks!
https://www.popularwoodworking.com/projects/japanese-garden-bench-2/
(Apologies if this shows up twice; I think I lost the connection just as I pressed the “Comment” button on my first attempt; at least the comment hasn’t turned up yet.)
Hi Megan (and Chris),
I’m pretty sure that by now I have read or watched (numerous times) everything you ever put out there on the ATC, and can’t recall having come across any reference to drawboring the lid frame, either to say you considered it but didn’t do it, or that you actually did.
So, have you ever done that particular deed? If not, was there a reason behind that choice? And if you have, what considerations led you to not make it part of the standard procedure?
Cheers and all best,
Mattias
PS. No prices will be handed out for figuring where I’m currently at with my build.
It is not drawbored. The 4″ long through-tenons are plenty strong enough on on the original (and we build them in classes with 12mmx140 Dominos). If you do drawbore it (or peg it), be prepared to see the round (or square – whatever) ends of the pegs on the underside for time immemorial. Plus, most of the force on the lid is downward pressure, either when dropping it to a closed position or sitting on it – drawboring will add more strength to a side-to-side or front-to-back force situation, neither of which is likely to happen to the lid. But if you like the look or for some reason don’t want to use glue, go for it!
Thank you, Megan! I rather suspected that might be your thinking, but asked anyway in case there was something I was missing. I’m doing the 4” through tenons, and at least the first one (which is as far as I got before I had to go out and mow the grass) is a nice, tight fit.
I love drawboring for the way it pulls everything tight and (if the shoulders were done right) square without clamping (although I tend to combine them with glue). However, my internal jury has been decidedly undecided on how it thinks those peg ends would look in this situation (not least on top of the lid, if/when they start sticking up above the surface as the wood of the surrounding frame moves)) and as per usual, if you have to ask the question (in this case, “would it look good?”), you kinda tend to know the answer already.
I’ll mull it over a little longer, but most kielt will decide against.
Cheers and thanks once more,
Mattias
I’m looking for a way to improve the grip my crochet has on a workpiece.
It’s often tricky to set up a long board for edge planning with the left end slipping up and down in the crochet. Have you ever tried or heard of anyone trying to put Crubber (or something similar) on the crochet? It could be either on the crochet itself or on the face of the bench immediately behind the crochet. Thanks!
Hmmm – I have not. But I’d probably first try adding some “tooth” to the inside of the crochet with rasps (’cause that’s easier and cheaper). And, be sure to jam it into place as hard as you can before clamping the other end (if you’re not already!). That said, I suspect crubber could help a bit.
Good morning, Megan! What are the advantages of using western style saws over Japanese style saws?
I don’t know that I’d say one style is more advantageous than the other in the shop as far as end results. I think it comes down to what you’re used to. Except that it’s easier for my arthritic hands to grip a Western handle, because my grip can be looser.
But for gardening work, I absolutely prefer a Japanese-style saw– much easier to use when working overhead for, say, taking down a branch.
I really like my Japanese saws, and I’m pretty good with them now. If you decide to get a Japanese saw, build a set of Japanese saw horses to use with it. Makes all the difference. Especially with a Ryoba style saw which is what I use 99% of the time.
I built a pair of these, and I use them all the time:
If the link is wonky, search “Rex Krueger Japanese sawhorse” on YouTube.
Also a guy called lemongrasspicker on yt did a project on these, check his out as well.
My local library system (Kent District Library in Michigan) allows users to recommend books for the library to purchase. I recommended one of your books, Backwoods Chairmakers. The request was denied because the book was “not available from one of their accepted vendors”. Do you sell many books to other libraries? Do you know any other way they can acquire your books?
We are happy to sell direct to libraries, but because we don’t distribute through the usual channels (such as Ingram and Baker & Taylor) some can’t acquire our books because of their internal policies. If they’re willing to go around their usual process though, they can send a note to help@lostartpress.com and we will be happy to help.
Chris, can you comment on the Woodriver carver’s vise relative to other similar products on the market?
We haven’t used it…but I gotta say it looks exactly like all the other dark green carver’s vises, down to the screws and crappy softwood jaws (we replace those with hardwood when they break – and they will break). I suspect it is, in fact, the same vise rebranded.
I bought a WoodRiver vise a couple weeks ago after taking a chair class at Lost Art Press. The vise is pretty much identical to what we used in class – and yes, the jaws are softwood. Works great – just make sure to tighten up the bolts on the side rails (after about a week I had a bolt nearly fall out and noticed they were all quite loose).
And – they’re on sale right now for $115 (although they will probably hit you with $20 in S&H unless you can pick it up in store)
When you apply the Milk paint to wood, do you apply it to the bare wood, or do you use a primer, etc first. If you only go with the milk paint, does it raise the grain of the wood? Thank you.
On bare wood, and I do not use a primer. Yep – no getting around sanding after at least the first coat with a water-based paint. Even if you “raise the grain” then sand before painting, you’ll almost certainly have to sand after at least the first coat.
I resawed two 5/16″ thick x 5″ wide pieces of quarter sawn oak for ATC till bottoms, but they moved a lot after resawing (moisture meter looked good, but there was internal stress). Hoping the nails will remove the cup/bow, but was wondering if you’d recommend gluing the half-lap joint, so the two bottom pieces don’t move independently. Working with thin stock has been the hardest part for me. Thank you!
I almost never resaw…because rarely am I happy with the results (as you’ve just experienced. But no, I would not glue the half-lap, and I’d fit only one of the bottom pieces perfectly the runners; make the second one a hair shorter. That will cut down on fitting problems.
I looked at an eclipse map this morning and saw that Covington is right on the edge of totality. Lucky you! Do you have your eclipse glasses?
I do! We’ll be at I think 95 percent or so in Covington – 100 percent about 25 miles north. (Have you read Twain’s “Connecticut Yankee?” Eclipses always remind me of it.)
Now we just need the weather to cooperate – no rain predicted, but at the moment, it’s showing it will be cloudy. 🙁
It’s probably over thirty years since I read “Connecticut Yankee”. I have to admit I don’t remember the eclipse. I guess it’s time to re-read.
Drive the 25 miles. Totality is an order of magnitude different from 95%. I heard someone describe it as “at 95% it’s like a nice sunset. At 100% it’s like the sky is broken”. It’s that different!
As someone who saw the total eclipse in Munich on August 11th 1999 (on an otherwise beautifully sunny summer’s day) I can but agree – the full fat version is quite something to behold!
One more piece of advice: don’t bother trying to take photos or to film it. You will lose a significant part of what is a very short moment anyway, just to get a set of photos that are likely to be rather meh.
I was planning on taking pictures of the crazy folk crying that the disappearance of the sun heralds end times.
Take pictures of the shadows things throw. That’s the most mind-bending thing to me.
I second this: In 2017 I wasted too much time on a lousy picture. Still an amazing moment.
Obligatory XKCD reference: https://xkcd.com/2914/.
Thanks, now I don’t have to post the link.
In the Stick Chair video, Chris uses a Mikita orbital sander with a dust collector attachment. Rockler has an attachment, but it is both pricey and bulky. What is he using and where did he find it?
That’s the hose of the Festool dust extractor (pricey), with a hose clamp (30 cents) tightened around it to keep it attached to the sander’s dust port.
I’ve had great luck finding cheap 3d printed plastic couplers on Etsy.
The dust port of my Mikita sander mated perfectly with the top of a plastic sofa-pop bottle. I epoxied that into another bottle that matched my shop-vac hose. Cost about a nickel, easy to mount and remove, has lasted years. Ugly as sin, but … meh 🙂
Elizabeth Bennet or Anne Eliot?
Would Mr. Collins have made a good woodworker?
Elizabeth (but I like Anne a lot, too…after she grows a backbone).
I suspect Mr. Collins would never pick up a tool. The condescension of Lady Catherine De Bourgh would never extend to having a rude mechanic at her table, plus it would take too much time away from his arranging of little elegant compliments.
Nice. I agree through and through. I don’t know if I could hang with Elizabeth, though. She’s too clever. Anne has more patience.
I think Collins is a craftsman at heart. All that energy for stupid little compliments… he should have ditched seminary and put it into a chisel.
Hi Megan! How do you set the lateral adjust for the Veritas shooting plane? I have already discovered that when I tap the iron with a hammer it loosens the tension on the lever cap, so I tighten the screw after each tap and was finally able to get square ends on 7/8″ x 1″ walnut picture frame miters. Now I’m working on 7/8″ x 2″ white oak picture frame miters, and I’m really struggling to get square ends on the miters (relative to the reference face). I got it close enough for me, with a small gap on the back side of the frame, and tightened the set screws that are supposed to lock in the iron’s position. I was able to shoot two sides of the frame, but when I moved to the next two, I was again getting an out of square end with a gap on the front face of the frame. I’m not sure if this is due to how the iron is set, how I am holding the workpiece, or both. Also, do you use those set screws? I guess it is possible that tightening the set screws could nudge the iron a little bit after you have it set perfectly.
I have never tapped the iron on the shooting plane. We set the set screws to square the blade in the mouth a thousand years ago, and have not touched them since. The set screws help to get the blade back exactly in place every time (with the Norris adjuster perpendicular to the blade). Then tighten the lever cap screw. If the blade is moving on you (and you have the set screw perfectly set), my guess is that you need to tighten the level cap more. Also, make sure the blade is honed straight across – no camber on that iron! And take light cuts. It’s also possible the workholding (the shooting board) has some dust in it, or… It’s difficult to diagnose this one in absentia.
Thanks! I found the Norris adjuster hard to dial in since it is very stiff, but might just have to break it in some more. Same with the knobs for opening the mouth. Good to know about the set screws.
I live in Cincinnati and I’m going to Indianapolis Monday for the eclipse. They (where I’m going) heard that the Indy Racetrack is expecting 100,000. I’m leaving earlier than first planned.
Jay that would be now, I did in KC a few years back.
Are you still reading?? get going
And don’t plan on getting home quicker than 6 hours per 2 hour drive
Hey Megan- as a follow up from couple weeks ago when we picked our favorite top 3 Wilco songs. What is your favorite album? Mine is Yankee Hotel Foxtrot. Reason I’m asking is that I’m planning on seeing them in June at the Beacon in NYC so I have Wilco on my mind more than usual lol
I saw them there in 2017! Wilco hates Philadelphia, unfortunately. Not that you asked me, but over the years I’ve said Summerteeth, A Ghost is Born and Sky Blue Sky, recently even Wilco (The Album). A bunch of local artists are doing a Ghost is Born 20th anniversary show near Philly, so even if I don’t get to see Wilco here I’ll be happy about that.
Just like how any time somebody posts a picture of the marina towers anywhere on the internet there has to be at least 2 comments about YHF by law, if I see a Wilco album ranking comment I am contractually obligated to reply. Sorry.
No apologies!!! Love it!!! And as a follow up imo I think Schmilco very underrated
Hi Fitz,
I teach at the North Carolina School of Science and Math, which is a STEM high school. I’m trying to get a hand tool woodworking course going so the kids can actually touch something besides computers! I did a pilot with some success (and a lot of my own tools!) but am struggling with getting together enough benches, tools etc. Do you all have any suggestions for foundations or similar who might want to support getting actual tools in the hands of the future? It wouldn’t cost that much . . . Any suggestions are much appreciated. I enjoy the work you all do very much.
Neal
Where can one find a ‘dictionary’ of these spells?
There are books specific to various traditions – Chris mentions many of them in “The American Peasant” (and he discusses a bunch of spells and their meanings, of course).
Some of the source books are:
Gyenes Tamás “Ácsolt ládák titkai” (Google translate is your friend!)
“Ukrainian Design Book: Book 1” by Natalie Perchyshyn
“Latvian Design” by Aleksandra Dzervitis
In England, Timothy Easton, M.J. Champion, C.J. Binding and L.J. Wilson in papers for the academic and popular press
Romania: Anamaria Stanescu, “Pristolnic: Orthodox object of worship in the traditional household”
are all places to start (until the book comes out!)
Thanks!
Good morning, Mrs. Fitzpatrick. Jane Austen or Charlotte Brontë? Or some other? Pride and Prejudice, or Jane Eyre? Or other?
I am sorry that chair and paint gave you such a bad time this week. I am curious what makes the decision to go with a “milk paint versus a linseed paint in green? Did you get a bad batch?
jeremystoltzfus79@gmail.com
P.S. I used the formal greeting above because it sounded Victorian.
Jane Austen. I love her work (I reread her oeuvre every couple of years for relaxation – not that impressive since there are sadly so few of them!)
We used the GF “milk paint” ’cause no time or safe space to wait for the linseed oil paint to dry (we’ll have visitors in the shop all week, so we can’t leave a project sitting around that needs to be dust-free for days). Also, after all the trouble, I wanted a predictable result. I know exactly how the GF milk paint will look/dry/lay out.
I got a bad bottle of Titebond hide glue (super sticky, won’t fully harden, fails block test). Anything I can add or do to the glue to make it fully harden? I have no problem with and fully intend to trash the bottle if not, but thought it could be fun to experiment.
Is a wax warmer or sous vide the best way make small batches of DIY glue? I tried with a water bath on our gas stove but found it nearly impossible to keep the temp consistent over that long of a time and ended up overcooking it (wouldn’t harden, basically just made gummi bears). I’d prefer not to buy yet another gadget to cook glue and would love to figure out a method using the stove that works. But if an electric warmer is the best way to keep the temp consistent, so be it. I really like the idea of a clear hide glue and want to try it. Just wondering what’s worked for others.
Thank you!
Do you have a Crock Pot? If so, heat some water on it and use a cooking thermometer to test if you can get it to hold a temp of 140-150° F
I’d toss the bad bottle – you’ll never trust it. (And I don’t know if there’s a way to fix it)
They sell little fondue sized crockpots, but I recently bought that little Lee Valley glue pot and warming plate; now kicking myself for not getting it years ago. Will probably rarely use anything other than fresh mixed animal glue again ( I WILL be trying gummy bear glue when I gave a chance on something I don’t mind risking it on).
I’m looking for guidance on sizing a tusk tenon – in particular, a horizontal one. I’ve found few horizontal examples in “the literature” and no advice on how to size one…
I’m making the American Trestle Table, but knockdown, so the stretcher’s tenons extend past the leg. Since the stretcher is quite high, I would have to remove the top to tighten a vertical tusk, which seems … Unfriendly. So, a horizontal.
The tenon is 3″ wide and 3/4″ thick. How thick does the tusk need to be to be “safe”? Can it be Doug fir like the rest of the table, or should I prefer a hardwood? Should it be about an inch wide, based on the rule of thirds, or is that a red herring here?
Waring says nothing about this joint, and I haven’t found it in Hayward, though perhaps it’s there.
Thanks.
I’d make the tenon 7/8″ or 1″. Hardwood to match the project. Just be sure to make the tusk’s mortise extend into the through-mortise in the case by maybe 1/8″.
1″ wide and … how thick? Or 1 x 1? Sorry if I’m being dense, but I want to make sure I get it.
Yes, I understand the importance of the tusk’s mortise extending into the through mortise.
Thanks so much!
Kinda depends on how long the tenon it is. The tusk is overkill so mostly what you are trying to do is scale it so it looks right.
Ah, ok. I made a sample tenon that is extra long to try to figure that out. I just don’t have a sense of how thick the tusk needs to be to be strong enough.
And presumably there is some minimum thickness beyond the tusk to keep the end of the tenon from breaking out. I don’t know if that’s like a half inch or an inch, I guess I could put in some kind of bracing in the end- I’ve seen that mentioned at least once, but it really feels like overkill.
This post really helped me out when dimensioning some tusked through tenons:
https://wp.me/p4bMK1-5v
Hope it is helpful in your case, too! Hard to find info on this joint…
Hey Megan!
Do you and Chris have a good method for traveling with your sharpening stuff?
Throw the whole messy boot mat into the back of your Subaru and hope for the best? Maybe yeet it into a Rubbermaid first if you’re feeling extra fancy?
Just wondering if you’ve got a system that’s a little more… elegant than my borderline chaos.
Thanks, and have a great weekend!
Mine (Shapton Pro) stay in their cases, and fit into the bottom of my tool chest. Once in awhile, I’ll put them in a separate bag if I need the tool space.
Good morning, Megan!
Do you agree that “Silly things do cease to be silly if they are done by sensible people in an impudent way”?
I resolve not to engage in silly things before receipt of your reply.
Your Humble Servant,
Bob Kauten
Emma said a lot of silly things…mostly when she needed to excuse her own questionable behavior
I’m hoping you’ll permit two questions. I’ve lost access to the stick chair video, and seem to recall the resultant angles being different from the book. Can you confirm the resultants you used in the video?
Also, I’ve noticed some elbow pain when I’m planing. It is in my right elbow and I’m right handed. Any thoughts? Feels like tennis elbow…..perhaps a height issue? If so, which way do I go?
Thanks!
Send a note to customer service and we’ll get you hooked back up with the video. The resultants for front and back legs are both 23°.
Welcome to the land of plane elbow. There is PT you can do that helps immenesly. It’s worth a Google.
Not to take up space on the thread, but If you’re only experiencing pain from the act of planing, and don’t have a pre-existing tenderness in your elbow, it could also be your mechanics. I see plenty of folks only using their arms when pushing a plane. It helps a lot if you don’t extend your right arm until the plane has already been set in motion by pushing off of your back leg and slightly rotating your upper body. A bit like throwing a punch, I can only imagine. As well, obviously, having a super sharp iron and wax on the sole will reduce the energy required. Lastly, as you’ve mentioned, it could be height. If your bench is too high, even slightly, you could be wasting energy by not being able to get your mass above the cut. I’m 5’8” and our shop benches are 32” high.
Cheers.
A second on the mechanics. Wear a pedometer, and if you’re not astounded by the number of steps you’ve taken, then you’re probably doing it wrong.
All true. But Chris Williams and I also struggle with tendonitis after long sessions making sticks. You have to use your arms. I have tried many many things to avoid injury, but I have concluded that – like tennis players – it can happen when you do this all day every day. Even when you do it right. Just my experience.
I know Chris has done a lot of work around finishes that aren’t trying to kill you. What do you all use for mineral spirits? Have you ever tried natural turpentine?
I just bought a fresh bottle of Diamond G turps, but I haven’t yet used it as a thinner. We use low odor or no odor mineral spirits from the hardware store. I don’t know of any small biz no/low odor mineral spirits, or we’d get that.
We get ours from the local art supply store. I’m not sure how indy the mineral spirits scene gets though.
If you haven’t read them already, the annotated works of Austin are beloved by my wife. They add a lot of context to the stories.
Who is your favorite Mr. Darcy? Matthew MacFadyen… Right? (Although, he doesn’t get a bathroom scene.)
Colin Firth – by a country mile.
I studied Austen in grad school and read all the footnotes. These days, I read just for the story and escape.
Did Chris’ sister really get bitten by a moose?
Does anyone have a preference between the Stanley original adjustable circular plane (#113) and the Stanley Victor adjustable circular plane (#20)? According to the Stanley 1914 catalog (thank you, Chris and Megan, for publishing it!), the virtue of the original is that it is said to be able to produce concave and convex curves of the same arc, because of the graduated scale of the gears, but I don’t know how well it does such. A defect (again according to the Stanley 1914 catalog) of the #113 is that because it has more parts, there is more lost motion, which makes it work less smoothly. I looked in The Anarchist’s Tool Chest and didn’t see any mention of them. Thanks again for hosting this open question and answer forum!
I’ve used both, but not a lot. I dislike the 113 a lot. The only place to grip the front is the knob that adjusts the curvature of the sole. It’s uncomfortable, and it’s easy to turn the knob and change the curve. The number 20 was actually a later design, and is more comfortable, in my opinion.
Thanks!
Hi,
I currently only use metal planes, but i was thinking of trying out wooden planes – specifically the Krenov style planes from the wooden hand plane book. I notice neither you nor Chris seem to use these kinds of planes. Is there any specific reason beyone preference?
Thank you very much.
Technically, you’d want a benchtop even lower than what is needed for metal planes, in order to get your hands and weight over the top of the tools – and that makes the bench awfully low for efficient and comfortable sawing. With metal planes, it needs to be not quite as low…but still too low for the best sawing, which is one of the reasons I like a Moxon vise. It raises the work off my bench to a good level for sawing. But also because they just feel funny in my hands. Like so many things, it’s what one is used to.