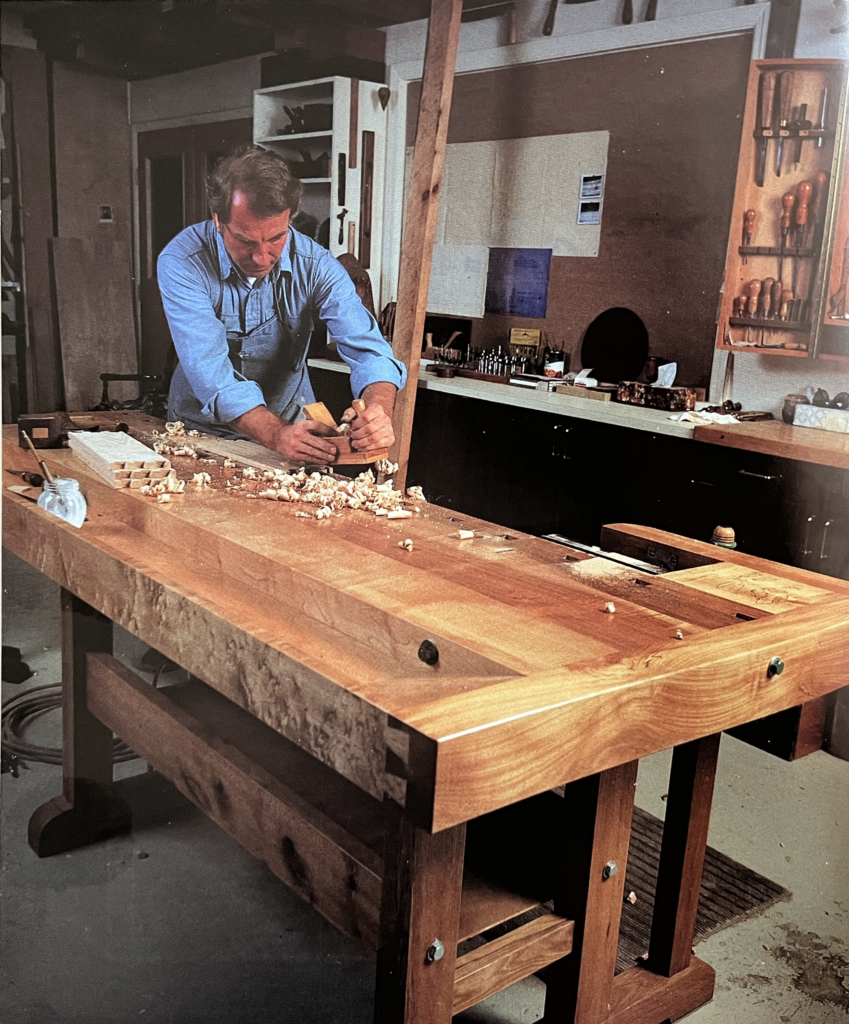
The following is excerpted from “The Workbench Book,” by Scott Landis.
First published in 1987, “The Workbench Book” remains the most complete book on the most important tool in the woodworker’s shop.
“The Workbench Book” is a richly illustrated guided tour of the world’s best workbenches — from a traditional Shaker bench to the mass-produced Workmate. Author and workbench builder Scott Landis visited dozens of craftsmen, observing them at work and listening to what they had to say about their benches. The result is an intriguing and illuminating account of each bench’s strengths and weaknesses, within the context of a vibrant woodworking tradition.
This fully illustrated guide features more than 275 photos of beautifully crafted workbenches as well as complete plans for four benches. “The Workbench Book” explores benches from around the world, from every historical era and for all of the common (and esoteric) woodworking specialties.
This 248-page hardbound edition from Lost Art Press ensures “The Workbench Book” will be available to future generations of woodworkers. Produced and printed in the United States, this classic text is printed on FSC-certified recycled paper and features a durable sewn binding designed to last generations. The 1987 text remains the same in this edition and includes a foreword by Christopher Schwarz.
I met Frank Klausz before I met his workbench. He was seated next to me in the front row during a lecture given by Ian Kirby (Chapter 6). Klausz himself was scheduled to speak about wood finishing the next day. Kirby’s talk centered on his workbench, an example of which he’d brought along. Although the bench had evolved out of Kirby’s own English tradition, from Klausz’s Hungarian perspective it was hardly a cabinetmaker’s bench at all. It had no tail vise and the front vise was of the metal, quick-action persuasion. Klausz fidgeted through most of Kirby’s talk, and at the first break he sprang from his chair and led me to the bench, where he passionately ennumerated his objections.
To understand the depth of Klausz’s convictions, you need to know about his background. Thirty years ago in Hungary, at the age of 14, Frank began his woodworking career in an apprenticeship system that had remained essentially unchanged since the Middle Ages. What was unusual about it, even by European standards, was that Klausz entered into a formal, contractual apprenticeship with his own father. “I paid the highest price for my trade,” Klausz explains. “Once I apprenticed, I didn’t have a father, I had a master.” And a stern master at that. Of the half-dozen workers in his father’s cabinet shop, it was Frank who was taken to task if something wasn’t quite right. Perhaps wary of his own son’s competition, the elder Klausz withheld certain construction tips until the very end of Frank’s apprenticeship. Watching his father work, Frank asked, “How can you do that so fast?” His father replied, “After ten or fifteen years you’re gonna be a pretty good beginner yourself.”
At the end of four years, Frank became a certified journeyman cabinetmaker, on his way to becoming a master (which required one year of work in each of three different shops). Ten years later, Frank and his wife, Edith, packed their lives in three suitcases and left Hungary. Like the journeymen of old, Frank was on the road-except that his only tools were his hands and head, not chisels and saws in a toolbox strapped to his back. By 1969, the couple was living on Long Island, where Frank ran through a succession of jobs – carpentry, casework and so on – trying to find his way back to the work he’d trained to do. It was five more years before he could set up his own shop in a two-car garage in New Jersey. Finally, in 1985, Frank and Edith built the shop they’d been dreaming of.
I went to visit Frank in his Pluckemin, New Jersey, workshop and to meet his workbench in the flesh. My first and most startling impression was of the workshop itself. I had primed myself for an old-world sweatshop, with young apprentices chained to their benches. In Hungary, Frank’s father had two small workrooms-one for the benches and another (unheated, even in winter) for the machinery. When lumber had to be cut from a 20-ft. log, the workers fed it through an open window at one end of the machine shop, across the bandsaw and out again through the opposite window over rollers placed at the sill.
Klausz’s own shop couldn’t be more of the ‘new world.’ The single-story, cinder-block building sprawls a full 100 ft. in length. Painted off-white inside, it is bright and airy, with windows on all sides and large skylights. If Frank had mill a mast for the Constitution, I doubt that he’d even have to open a window.
Frank takes me on a quick tour of the shop to show me their work. While one of his four employees might be building a set of computer cabinets of walnut-faced plywood, another could be restoring an 18th-century English grandfather clock or stripping an office desk. At the far end of the building, we pause for a moment while Frank sprays the handrails for a casket he has built for an elderly client, whose house he has almost entirely restored. In the old country, Klausz explains, there was a cradle-to-grave relationship between the craftsman and his client. As his last commission for the deceased, the cabinetmaker would appear at the funeral, in his Sunday best, to drive the nails into the lid of the box. Clearly, a workbench in this shop needs to be versatile.
According to another old-world tradition, Frank explains, workbenches were passed on from one generation to another. The woodworker was the custodian, not the owner, of his bench – just as he was the custodian of the knowledge of his trade. The workbench took on a life of its own; it became somehow larger than the sum of the men who had planed upon it.
For Frank that chain had been broken. He had brought no workbench with him from Europe, and had to use commercially made benches for years, never having the time to make his own. But, when he found that there weren’t enough benches to go around in the new shop, he decided to build one. “The reason I made one is that you can’t buy one good enough,” he told me. It seemed to Frank that commercially made workbenches were growing smaller and lighter, even as they got more expensive. I also suspect it was Frank’s way of saying he’d come home.
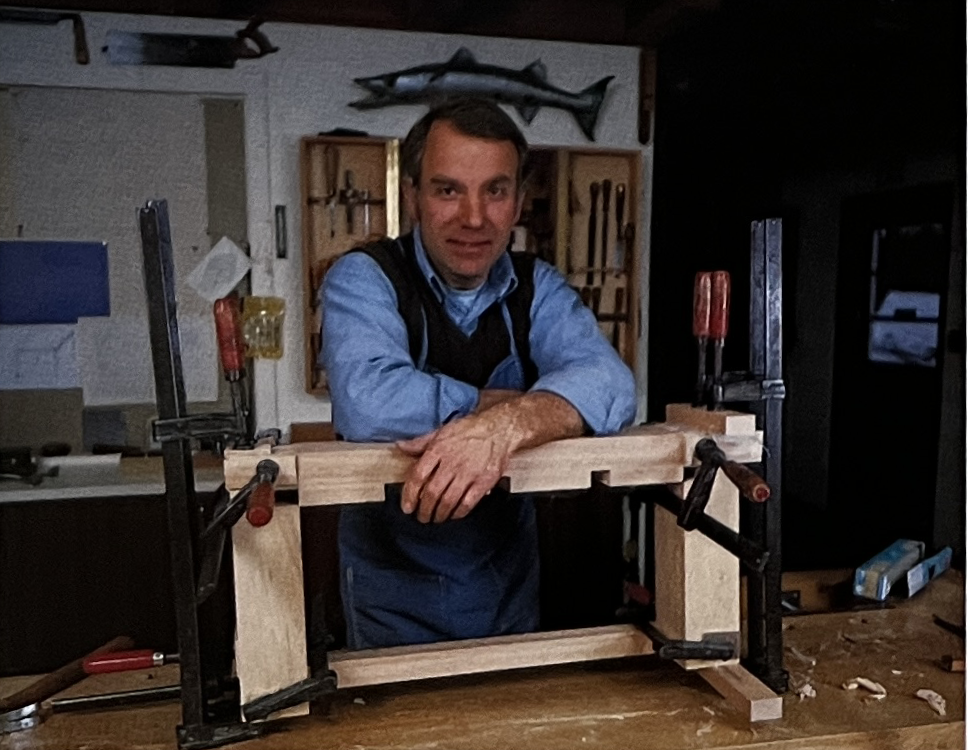
There wasn’t any guesswork or design involved when Frank built his bench. He didn’t reinvent the wheel. “It’s a copy,” he says. He had measured two benches at his father’s shop, a third in Vienna and another in Belgium. They were all within an inch of each other. “Apart from little touches like the stops and oil dish, the only difference I found was that some craftsmen treat their benches with loving care and some don’t …. Except for the metal vise screws, my bench is the same as my grandfather’s…. [The design] is so well worked out – if it hadn’t been good, Grandpa would have done something about it.”
When a customer enters Frank’s shop, he encounters the workbench, which also functions as a desk and business counter. Even if the visitor doesn’t comment on the bench, it’s a fair bet he’s noticed it. If Klausz could fit his workbench in his wallet, he would hand it out like a business card – it is his best foot and he puts it forward.
Klausz begins to explain his workbench by underlining a point too often overlooked-location. As the most important tool in the shop, the bench’s placement with respect to work flow (of materials, to and from machines, for finishing and so on) is crucial. Lighting is also important, and ideally should cast no shadows on the benchtop. Hand tools should be readily accessible. Frank’s are kept in a wall-mounted cabinet, only 5 ft. from the shoulder vise of the bench.
Of equal importance is the auxiliary set-up table near the bench, shown below. This low table is the right size (40 in. by 60 in. by 27 in. high) for all kinds of gluing, assembly or finishing. Anything that’s too messy or large for the workbench can be done on the table, leaving the benchtop free for trimming joints and other last-minute tasks. Rather than cluttering the main bench with drawers, Klausz built open shelves and storage bins in the base of the set-up table to hold hardware, small power tools and accessories.
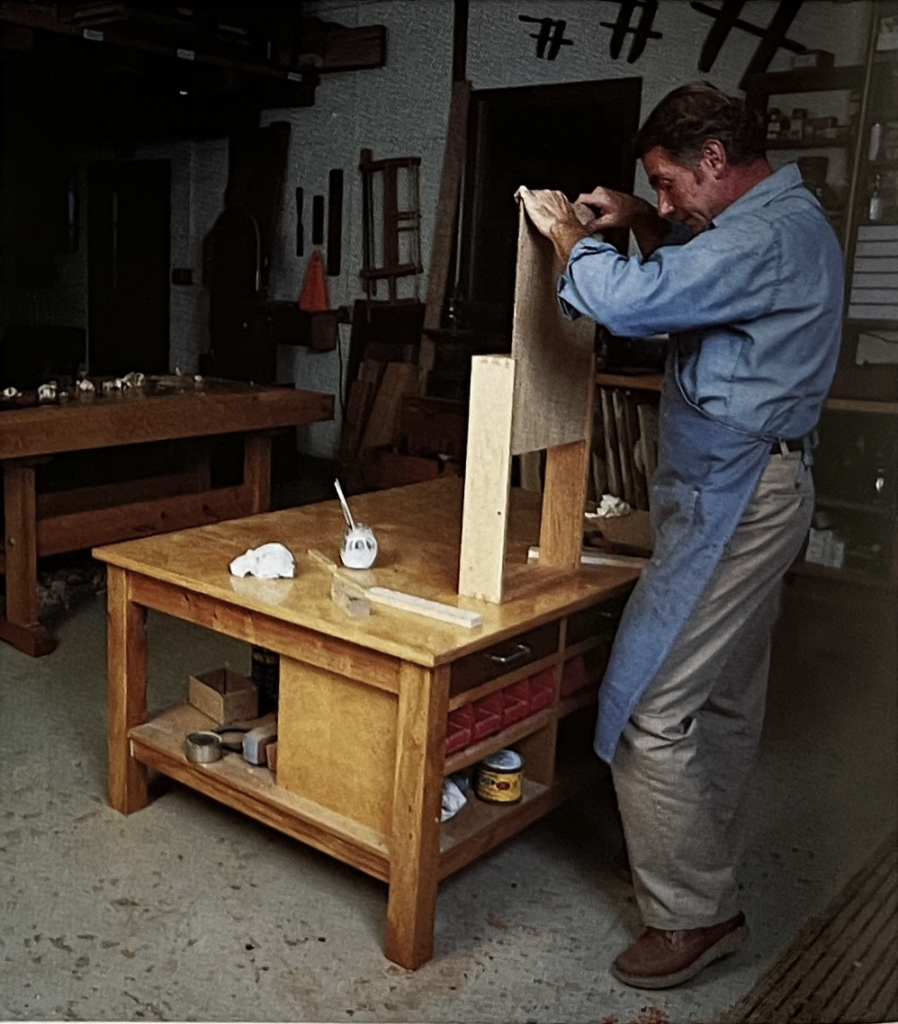
In my travels I’d seen several variations on Klausz’s workbench, variously referred to as Scandinavian, Danish, Swedish and European. These workbenches all have as a common denominator the ‘dog-leg’ shoulder vise. I thought I had heard most of the arguments for and against this vise; as far as I had been able to discover, the only craftsmen who liked it were those who had trained on it, usually in strict apprenticeships.
I posed the same objections I’d heard to Klausz: The vise isn’t strong enough to withstand heavy clamping pressure. It’s awkward to work around the large corner. The pivoting clamping board often has to be held with one hand to keep it from binding as it’s wound in and out. You can’t clamp a board anywhere on the bench for crosscutting.
Frank’s initial response was a reflex: “If you’re a cabinetmaker, if you do casegoods, frames, if you plane, saw or sand wood, if you do dovetails … I can’t see anything quicker or better.” Later, he explained that the floating clamping board grips well on tapered stock, and one end of a long board (or a door) can be clamped firmly behind the screw while the other end is supported by the portable bench slave, shown at right. But it was only when I watched him dovetail a drawer that I truly began to appreciate the shoulder vise.
Through dovetails are one of the traditional cabinetmaker’s preferred joints, and when Frank cuts a dovetailed drawer he puts the bench through its paces. “Good craftsmen,” Frank says, “not only do things well, but do them with speed…. If you want to make a good joint, you can do it just about as fast by hand as with a machine, especially if you’re doing just one.” With the drawer parts milled to length and thickness, Frank uses a mortising gauge to scribe the thickness of the stock across the ends of the boards. Then he slaps the first piece-the drawer front or back – upright in the shoulder vise.
The quick-action feature of a Record vise is nice, Frank admits, but he rarely has to move the screw on his vise more than a single turn. Because there are no guide rods or screws running below the vise, a long board such as a drawer front can be clamped through the opening, not just gripped in the top few inches of the jaw or along one edge. The work won’t twist and there’s no need to block the other edge of the vise to keep the jaws parallel. (The clamping board pivots on the end of the screw to accept tapered work, and it should move freely without needing to be guided by hand.)
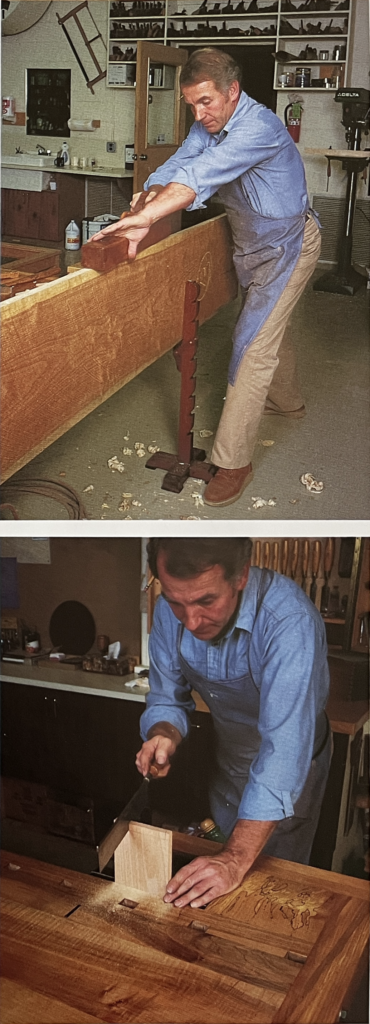
At 33 in. high, Frank’s bench is lower than I’m used to, but the shoulder vise helps to compensate by allowing you to clamp work securely at many different heights. If it’s too high, it vibrates; if it’s too low, it’s uncomfortable. Frank holds the top edge of the drawer front about 4 in. or 5 in. off the bench –
a comfortable sawing height – and clamps the board tight. He wheels around to grab a backsaw from the tool cabinet and begins cutting pins – without stopping to lay them out. In about as much time as it took him to rip a bageI on the bandsaw during a coffee break, he defines all the pins at one end of the board with six sawcuts. Once the pins are cut on both ends of the drawer, front and back, the action moves to the other end of the bench. Frank C-clamps the part to be chopped in front of the tail vise – never on it. The force of the mallet blows is transferred directly through the leg to the floor. Whether he’s working on one drawer or six, all the parts are stacked and staggered, one on top of another, so that he has ready access to all the joints. At one point, Frank demonstrates how, during a full day of this work, he would drop to his knees to rest his back (there’s a rubber mat in front of the bench to provide a cushion). This places the work at his chest, instead of at his hip, and gives him a closer view as well.
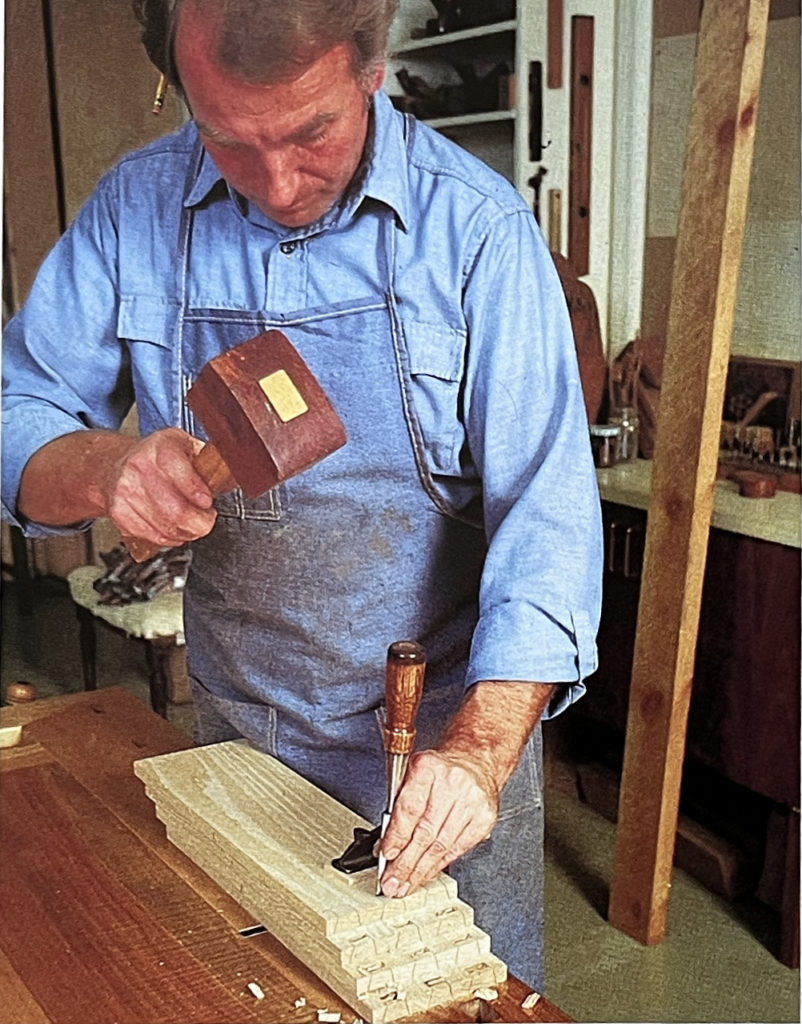
Next, with the parts laid out on the benchtop, he marks the tails from the pins. Then he’s back at the shoulder vise to cut them out. During these operations, the tool tray holds the marking gauge, hacksaw, pencil, square, chisel and mallet-out of harm’s way but easily retrieved. The tray isn’t a repository for yesterday’s project, and Frank keeps it swept clean. Cutting dovetails by eye requires having your wits about you, or it won’t be long before you’re cutting pins on one end of a board and tails on the other. A clean, orderly benchtop is essential.
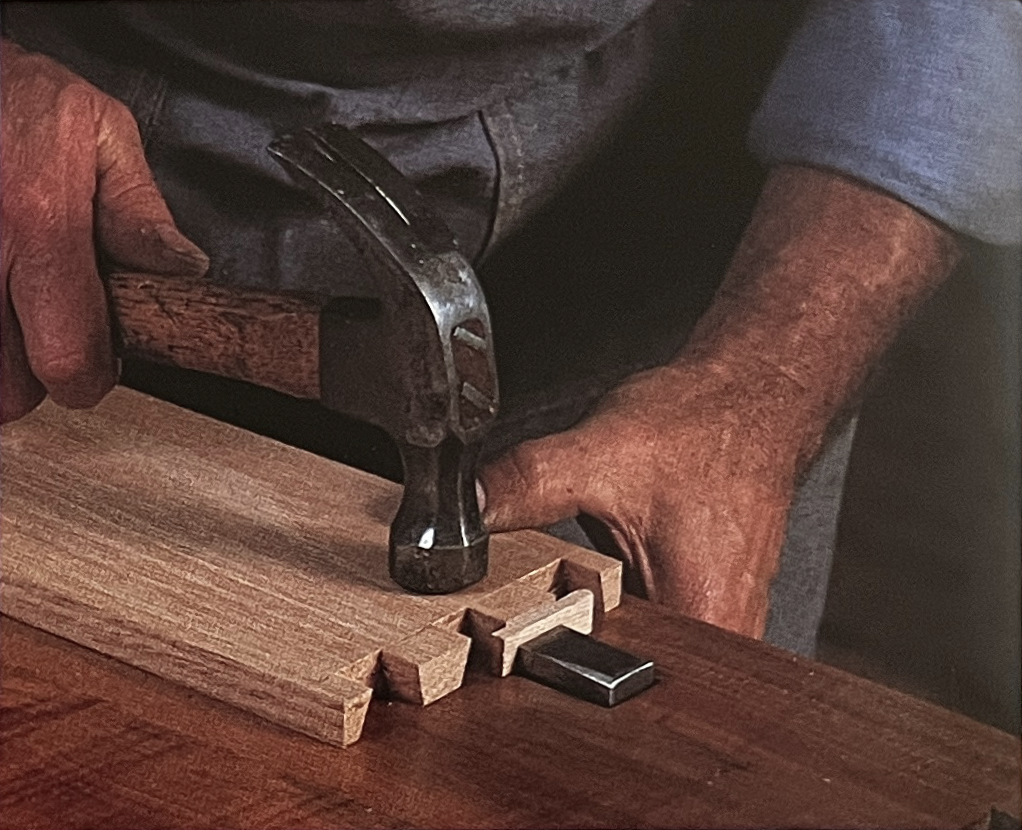
Before the drawer is assembled, Frank planes the machine marks off the inside of each piece. He moves back to the other end of the bench and gently closes the tail vise on a drawer side, using a piece of scrap between the metal dogs and the ends of the board. It doesn’t take much pressure. The benchdogs do two jobs: they grab the wood and, because they’re angled, pull it down. Their down-clamping action is important, especially on thin stock, which will chatter if suspended in midair. To make the most of this feature, Frank taps down on each end of the board in front of the dog, seating it on the bench. He prefers metal dogs to wood because of their strength; they’re more effective at pulling the work down, and he can knock the dogs up an inch or more above the benchtop without having to worry about flexing or breaking them. The dogs can also be reversed and used to pull apart a piece of furniture. For this reason, the dogholes are cut at an 88° angle – any steeper and the dogs might slide out of their slots.
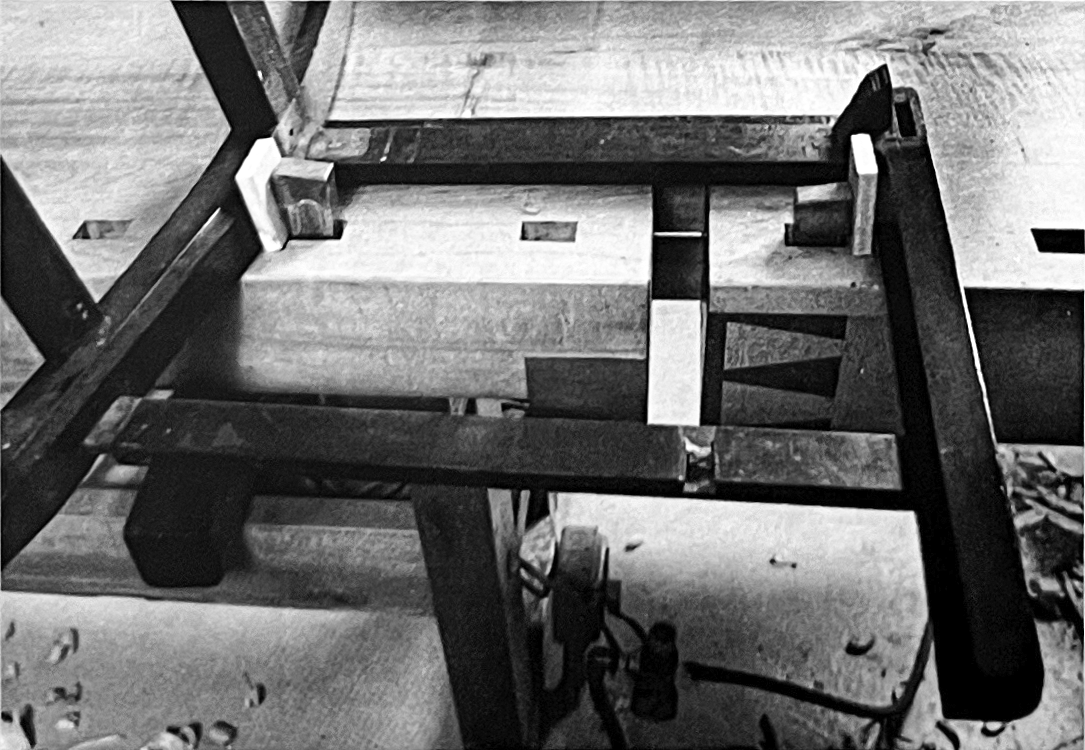
“When I plane, I use my body weight and just push down,” Frank explains. “This gives me hours of easy planing, without pushing and shoving.” The bench has to be the right height for this. To demonstrate his formula for bench height, Frank stands next to the bench with his arms at his side and his palms turned down – the benchtop grazes his palms. He is 6 ft. tall and his bench is less than 3 ft. high. Frank planes in two motions – a long, cutting, power stroke and a feathered return as he tilts the plane slightly to lift the blade off the wood and to resume position for the next cut. The bench doesn’t move under the pressure of his strokes.
Sometimes if a piece is small, Frank glues up right on the bench, spreading a cloth to protect the top. But more often, he turns to the set-up table behind the bench. A quick swipe with a wet rag removes any errant drops.
When the glue is dry, he planes the drawer sides by gripping the frame in the front jaw of the tail vise. The other end of the drawer, which sticks out from the vise, can be supported at any height by the bench slave.
To finish the job, Frank planes the top and bottom edges of the drawer flush. He reclamps the drawer flat on the bench between dogs-using the front doghole in the tail vise when he can and keeping the vise opening small. “You want to have the workpiece on the bench as n1uch as possible, not on the vise,” he says. “It puts less stress on the vise itself. The strongest support is up front, over the legs.”
Klausz’s drawer demonstration answered many of my doubts about the shoulder vise: It doesn’t need to be immensely strong, because the screw is always centered behind the workpiece. Whatever inherent awkwardness exists in its design is at least partially offset by this convenient feature, which cannot be found on any other conventional front vise. The clamping board rarely binds in everyday use, because generally it is adjusted in small increments, and it’s the only vise I know of that clamps non-square stock as easily as square stock.
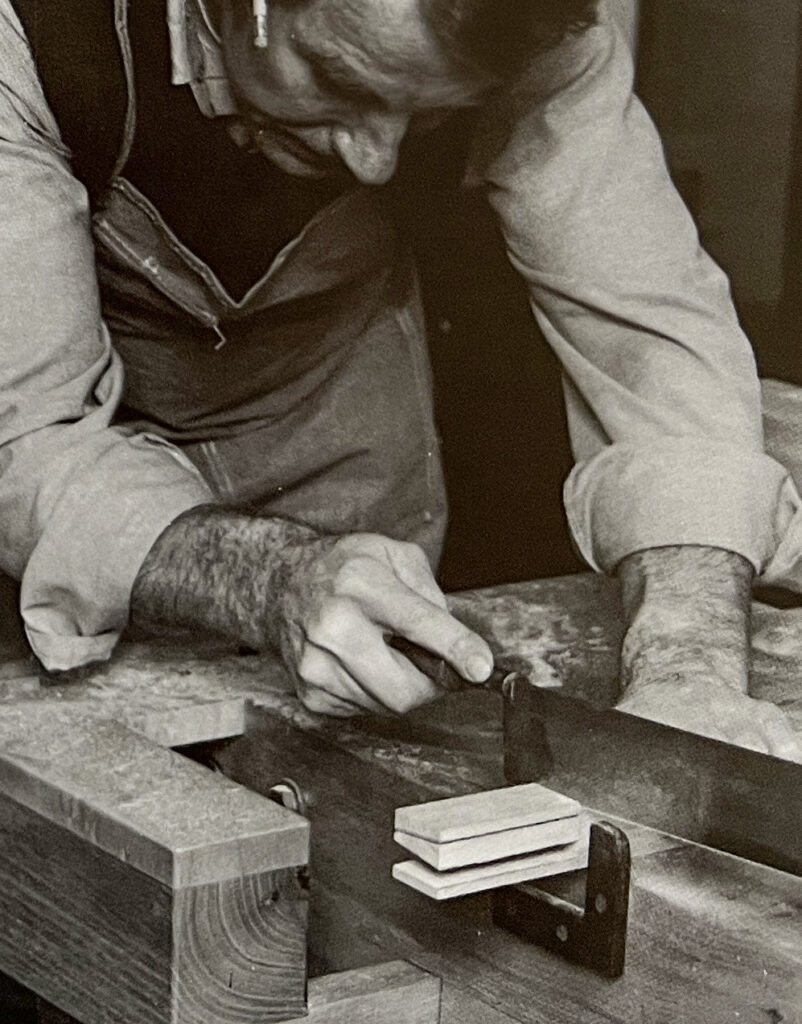
I had one final reservation, though. There’s no easy way to clamp a board for crosscutting anywhere on the bench. “You don’t have to,” Klausz says. All that’s necessary is a small stop, and he flips up the pivoting bench stop at the right end of the bench and pushes a board against it to demonstrate. Its location on the right end of the bench is also more convenient for a right-handed worker than crosscutting off of the left end.
If my own reservations about the bench were mainly resolved, it was clear that Frank had none at all. “If you’re a cabinetmaker, you should have a bench like this,” he said.
I made a similar bench to a design in old pop woodworking by Tage Frid but left handed to suit me and later added a set of dog holes and vice to rear to clamp sqaureframes. I also left out rear tool trough and made a cupboard to a Jim Tolpin design from his book on toolboxes
Mike
Klausz almost had me convinced with his logic on bench design, but then I remembered that by his logic he cuts his pins first.
Interesting.
I bought Scott Landis’s book on a whim in about 1997 or ’98 in London. It was Taunton’s 7th printing, I think and after some deliberation, I made a scaled version of Frank Klausz’s bench mentioned in your article with a few dimensional modifications to suit my needs. It used up some 2-1/2 inch thick waney-edged Beech that I had acquired a few years earlier. We had a monumentally strong storm in 1987 in the south of England that destroyed thousands of living trees in one night and that poor Beech was one.
This was not my first bench – far from it – but one that I made with the intention of it being the last and best….. a keeper, if you prefer.
This was also the first time that I had used very large – 3 inches wide – dovetails on the tail-vice and the corners of a frame around the top, as the recipe demands.
It convinced me that making drawers was a dawdle compared to these scaled-up monsters.
The top uses sets of opposing dogs aligned with the tail vice and has acquired holes for bench-hooks at strategic points in its useful life.
It’s a little darker with age and use, with a few scratches and dings here and there, but still going strong.
What would I do differently if I made it again?
Not much; but on consideration, the original bench calls for a threaded rod through the shoulder section to strengthen what could be vulnerable area subject to the strain of the vice-screw. In the same way I think that I would assemble the top of the Beech 2/12” by 4 inches, but, instead of gluing the lot, I’d use locating dowels and hold it all together with threaded rods which would make re-surfacing and leveling easier if the whole thing could be knocked-down to a set of boards, then reassembled…. just an idle thought.
But, given the reality that I’ve only scoured the top flat twice in 26-odd years of fairly constant use, it is a small point.
A very good book that engendered a very good bench. I good read in its own right even if you’re not looking for a bench.
This was one of the first woodworking books I read when I got interested in woodworking; it looked very appealing on the library shelf. I’ll buy a copy of yours some day since I don’t have it in my own personal library.
I’m assuming the few typos in this post are from the transfer of your digital copies to the web site, and not typos in your actual book proofs?
Almost certainly an OCR error (Adobe really didn’t like the font in this book…), then I missed them. I’d be happy to fix them if you tell me what they are!
My workbench of over 25 years is an exact copy, although with wooden vise screws, of Franks. It is the center of my hand tool workspace and each day I perform the various tasks it is so well suited to. I love this bench.
I’m not sure there will ever be another Klausz — or Frid, or Kirby, etc. But watching how times change just fascinates me.
I think there will, but it will take an odd 20 years working in their craft, for them to get to this point. My great uncle was in the same class as Klamath and Frid, started out woodworking as a youth, in the early 1900s. By the time I was able to spend time with him whilst in college, he was an accomplished skilled craftsman. My only wish is to have been able to spend more time with him before he died.
Cheers
Is it just me or does his bench look rather glossy….like it’s got a varnish finish?
Probably.
Mine’s built up the same type of shine over the years.
Mostly, I tend to finish pieces with Danish Oil.
Then, the used, oiled rags are rubbed out on the bench top and sides before they get a final dunking in a tub of water.
However, in the pictures they were photographing the bench for a book at the time!
A great read. Thanks.
One thing about the bench has puzzled me for years: the “Hardwood stop, 1/2″x 2” inside the line of dogholes and just to the right of being behind the front vise. Intriguingly, it’s slightly canted to the right but I never found mention of it in the article and never understood its function.
Klaus’ bench in “The Workbench Book,” essentially started my woodworking journey. I couldn’t believe something was simultaneously so beautiful and so functional. While I don’t have a dog-leg vise on my bench, opting instead for a twin screw vise, every other aspect of mine is identical to Klaus’.
Glad LAP has published Landis’ book! I have the Taunton Press 1987 first edition, first printing hardback of the book in fine condition with slip cover in fine condition. I found it several years ago while searching other woodworking books and snapped it up. I recommend it highly.
I remember reading this piece in the book at the bookstore. With only aspirations of woodworking, I couldn’t buy the book. All these years later, I remembered it. Thanks for sharing!
I’m looking at my copy of the third printing from 1989. That was six years after I got my general contractor’s license. My wife had given me a beautiful Swiss workbench (I still buy tools from the man who sold it to her!) as a birthday gift in 1981. A few years later, ambition sat me down at a desk where I stayed for most of my contracting career. I’m finally back at that bench, relearning the skills that I had only occasionally been able to practice then, and acquiring new skills that LAP and this community are showing me. You articulate and demonstrate an approach to furniture and woodworking that fits in well with how I view the world. I learn a lot here and I’m very grateful to you all. And I look forward to learning from Kale!
I think Frank’s straight edge is rocking.