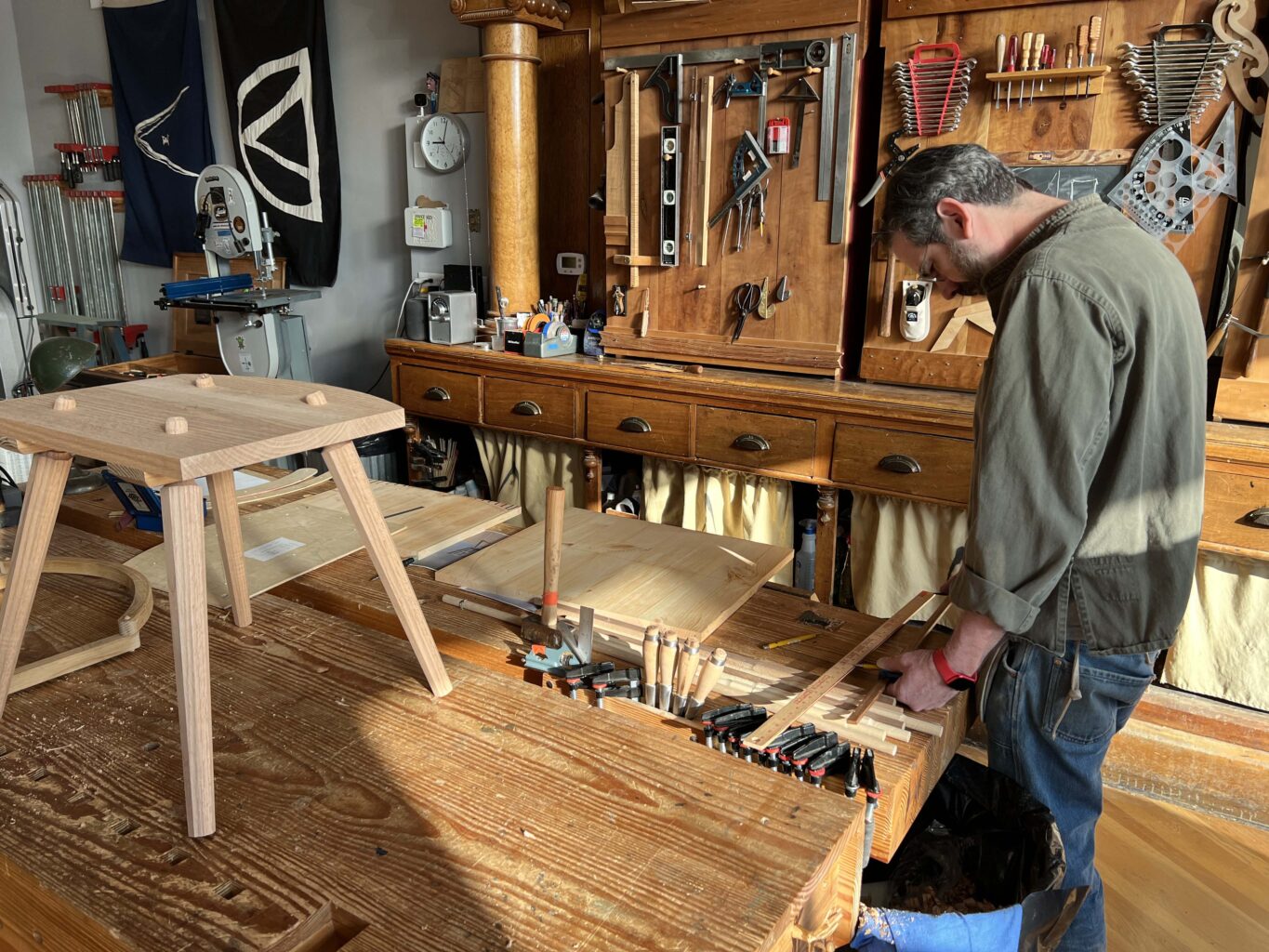
Comments are now closed.
Chris and I are here all day to answer your woodworking questions – in between some work at the bench, of course. You know the drill: post your (succinct) question(s) in the comments field below, and we shall do our best to answer. Comments will close at around 5 p.m.
– Fitz
Are you going to ship to Europe now that you have your own warehouse?
Perhaps some day we will, but it’s not a pressing goal. We have great distributors in Europe who carry all our books. Buying from them is cheaper for you than if we shipped it to you. I know that our distributors don’t carry apparel and some of the weird things we make. But you can still get those through a mail forwarding service.
https://blog.lostartpress.com/2021/12/23/my-bonnie-lies-over-the-ocean-a-way-to-shop-at-lost-art-press-from-outside-the-u-s/
I hope we will ship overseas some day. But right now, our goals are much smaller (getting all our inventory into one place).
Any problem using white oak for interior of an ATC (till bottoms, saw rack etc). Will the tannins react with the iron tools or is that overblown? Thanks!
Nope. The bottoms of my tills are white oak. I’ve never had a problem.
Good morning! My insect (ADB bed) progresseth. I’ve not yet glued the legs we discussed last week but I’ve done trial assembly etc. The slats are 4/4 KD red oak; the battens are laminated 8/4 KD red oak. It’s queen-sized so I added a 3rd batten down the middle as you suggested in the book. My brain extrapolated that a third batten implied 3 more legs, but this thing is solid with legs only on the two outer battens. An on rereading I realized you never really /say/ to add 3 more legs. I’m inclined to put a post in the middle and be done with it, though it doesn’t seem to need even that. If you were building it, how many legs would your insect have? (And what do you call a bug with 7 or 9 legs?) Cheers!
A post in the middle is likely all you need.
In an earlier blog post Megan writes about using Durham’s Rock Hard Water putty, and in another Mattias Hallin uses linseed oil putty. Have you done a deep dive into putties, like you do with paints and tools? I’m wondering if there are properties that would recommend one over the other for specific tasks. Also, is linseed oil putty the same as glazing compound?
I’ve used Abatron in the past for architectural stuff (works well, costs lots)…but now I usually cut out bad wood and install new for anything structural. I’ve also used DAP wood filler for painted things. Works fine, but costs more than Durhams, and doesn’t last terribly long after opening. I’ve had the same can of Durhams at home for going on 2 decades now. It’s still good, and it still works. (But only under paint). I’ve never has success with a putty under stain or clear finish. (But I haven’t tried them all.)
I have certainly not done any kind of filler/putty deep dive; at the most, I’ve dipped a toe or two at the shallow end of the kiddie pool.
That said, for filling or repair that I’m going to paint and that I want to be able to work after it has set, I have had good results with Milliput, which is a two-component epoxy filler that sets completely hard. It takes three to four hours to set, so has a long open time, and can be smoothed with water before it sets. Once hard, it can be worked and shaped with any edge tool, or sanded of course. Because it sets through a reacion between the two components, it will harden equally fast and well no matter how deep the repair. It also has excellent adherence qualities to most materials. With wood, I would only use it where wood movement isn’t likely to cause a problem, though, as it has zero flexibility when set.
The linseed oil putty I use is Rubinol, which is not a glazing compound. There are indeed traditional, linseed oil-based glazing putties, and you are supposed to be able to use them as general fillers too, but I’ve yet to put that notion to the test.
Rubinol can be had in 20 different colours, so at least in theory could be matched to a wood, although I have absolutely no idea how nicely it would actually match, or how well it would deal with the wood changing colour over time (probably not all that well, is my guess). In any case, I have only used it with linseed oil paint, so haven’t had to worry about that aspect.
Another vote for Durham’s (under paint). I still use a container of the stuff that was in my father’s workshop when I was a kid (maybe 50 years ago?). It has a price sticker on it from a store that’s been out of business for decades. It fills, it sands, it paints. An it lasts.
Hi Folks, I’m going to cobble together a ~6′ long low bench for sawing, general seated woodworking tasks, mount for my Grizzly-style carving vise, etc. I thought of SPF 2×12 2-ply lamination for the top, and same SPF 1.5″ x 1.5″ with round tenons for legs. (SYP is not readily available here in MN.) In your view is this sufficient for legs, or should I scrounge up some 6/4 (maybe 8/4) oak/ash/etc. for legs? Thanks!
I’m building a low Roman bench now with a laminated top made from construction lumber. The legs are 8/4 red oak that I rived out from kiln-dried boards. You probably could get away with legs from construction lumber if the stuff was slow-growth and dense. But why risk it?
Hardwood legs they shall be, thank you.
Lowes carries it as wider construction lumber in the Twin Cities. Check the 2x12s.
After seeing the last chair you posted for sale, it feels to this observer that some “Gibsony” ,or would that be “Gibsonish”, elements are being blended into some of your chair designs, but you’re not calling them Gibson chairs.
So that prompts me to ask: What makes a Gibson chair, a Gibson?
For me, a Gibson is defined by the angled back sticks that create a W or M. And that the angled back sticks intersect the arms.
Will there be any more Sharpen This videos?
I hope so. This year has been a S%$-show because of our new warehouse. We hope to get our books and videos back on track in short order.
I have an easy Sharpen This request for you: a video of you using a carbide sharpener to tune up the LV tapered reamer.
I am putting it on the calendar for Monday…which means it will happen. Probably.
Bonus points if you do it with an Arno burnisher or tell me it’s not the right tool for the job. Because I’m struggling.
I don’t think the Arno has a sharp enough tip. We use a carbide sharpener with a square edge.
https://www.leevalley.com/en-us/shop/tools/sharpening/files-and-hones/66738-universal-sharpener?item=09A0332
Knife stores carry these, too.
That’s a very useful sharpening device. Perfect for garden implements and miscellaneous jobs around the house. But why not sharpen the tapered reamer on stones or micro-abrasives like a spokeshave iron?
Because it’s a huge PITA. The universal sharpener does in seconds what takes about 10 minutes with abrasives. You need a keen edge, but not something that produces a finished surface.
I hope so! This is definitely an area where having the video and being able to watch the action is very helpful.
A maybe-related question: as I’ve gotten better/more consistent at sharpening my plane irons, my surface finish and overall performance has improved. Now I’m thinking about other aspects – like mouth opening.
My bench planes are all old Bailey pattern, in good nick. The mouth opening is adjustable, with some hassle. How do I figure out the “right” opening – in particular, how do I get my #3 to do a better job with complicated grain, Knowing it’s as sharp as I can get it?
Thanks, as always, for spending part of your weekend with us!
For tricky grain you have three options:
You can’t do all three. I usually use only one strategy. All work just fine.
Then take light passes on difficult grain. That’s about it.
Hello gentlemen… I’m in the process of building several moravian work benches and I wanna cut the threads for the leg. Vice myself any particular techniques that you would recommend to cut accurate threads for the leg vice. I would appreciate any recommendations you might have thanks. Mike.
When making wooden screws, we use the tap and die from Dieter Schmid. These are excellent tools:
https://www.fine-tools.com/gewind.html
Roy Underhill show how to do it manually in “The Woodwright’s Guide” (great book). If you prefer video, here’s a good series on the process:
https://www.youtube.com/@CartersWhittling
Good morning and thanks again for all you do. Is there a way to search the LAP blog comments? I feel that these Open Wires are becoming one of the best resources for WW knowledge on the web. Yet, when I search the blog, I get blog posts and not the comments. Searching comments could be a great way to find out: “oh, they answered that already!”
You can try using most search engines and the flag “site:https://blog.lostartpress.com” along with your search terms. That should restrict the search engine to only searching the blog, but how well your terms hit what you want is very much a YMMV scenario.
Yeah, that helps. But it would be nice if WordPress’s search engine allowed you to search comments. They say it can, but I have yet to see it work correctly.
OR you can save the complete open wires to PDFs, then search the pdfs.
Good morning, While waking through the woods the other day and seeing all the maple saplings, I wondered if using saplings for stick chair or table legs would be a good idea. I mean they are already round(ish) and the grain would be straight( I think). Thank you, john
There is a long history of using saplings or branches for components in furniture. Sometimes the saplings or branches from larger trees were tied to shape in the forest to “train” them into particular shapes. I’m experimenting with some of this stuff. I have a stack of interesting branches drying int he basement.
I’ve built a few stick chairs this past year and when it comes to saddling the seat around the spindle deck I always end up with a gradual curve from the concave area I’ve saddled out to the flat spindle deck. I’ve seen several chairs that appear to have a flat edge around the inside of the spindle deck around 1/8” or so and was curious if you had any suggestions on how to do that. Thanks in advance!
In “The Stick Chair Book” (a free download) I show how to do this with a router and a template. You can use a straight bit or a bullnose and quickly get a very sharp and well-defined edge.
Perfect! Thank you!
I have been looking into this question. There are apps we can add that will allow searching comments. I haven’t found one that I like yet. Sorry.
I am looking for stocking up on a few common screws and a set of countersink bits and wondered if you still recommend Snappy 40030 with the straight bits or another set with tapered bits? Doesn’t the tapered bits provide a better hold for the screw? Also, if I use screws for the Dutch Tool Chest (or one of the others) what size screws should I have on hand since I have to order flat head from LV or…? Here in Atlantic Canada’s local hardware stores they are 99% Robinson/square head and I hate the loo). Lastly, I’m assuming black screws are the way to go for a tool chest? In The Woodworkers Pocket Book, it shows the thread hole the same diameter on p.32 but the screws are tapered.
I’d probably use No. 8 x 1-3/4″ screws for the carcase. (Note that you may longer or shorter lengths to attach lid battens, depending on their width (and I’d probably use No. 10 there), and shorter No. 8s for the fall front battens and catch.
And on bits, I don’t typically worry about tapered. The pilot holes aren’t as deep as the screw, so the screw tip grabs plenty tight when you drive it in (in my experience). I love my LV HSS brad point bits. I have the small set at the shop and the large set at home. (But I am not seeing the sets on the LV site right now)
Thanks Fitz,
And the straight bits in the countersink okay rather than tapered?
The sets are listed in the drop down menu under the individual sizes. An odd place to put them.
Ah. Yes…a bit odd, but there they are! (Expensive but worth it.)
I have been so pleased having 1/64″ increments. For a long time they disappeared on LV site…from my eyes. Glad they exist even if hidden. Have considered buying set(s) for special friends/family. Now I know they still exist. Guess I should have written LV, but big thank you to Jason.
Here they are:
https://www.leevalley.com/en-ca/shop/tools/power-tool-accessories/drill-bits/42247-hss-lipped-imperial-brad-point-drills?item=07J0103
Scroll down for the sets.
Megan can weigh in on the screws she recommends for the Dutch tool chest.
In our shop, we stock No. 8s in lengths from 1″ to 2-1/2″, which covers most of our needs. The most used size is 1-1/4″. We use slotted unplated screws from Blacksmith Bolt. https://blacksmithbolt.com/
We also stock Torx construction screws (self-tapping) in sizes from 1″ to 3-1/2″. These are for constructing crates and jigs.
I still use the Snappy countersink bits with the straight drill bits. I have used the more expensive tapered Fullers and honestly didn’t see any advantage.
I am in the process of planning a dining table. I have found a few references that say bread board ends are an unnecessary over complication. In your experience do these really help keep a table top flatter. I will be using kiln dried material.
You don’t have to use them if your material is at equilibrium with the environment in your home/shop. In some cases the breadbaords might help the top stay flatter as it dries the last little bit. Mostly, they look nice and conceal the end grain of the top.
Good morning,
On the staked work table in the ADB, can you elaborate on the attachment of the drawer guides to the top? What peice of the guide gets screwed to the top?
Thanks!!
Hi Derek,
Sorry for that omission. The drawer runners are glued to the drawer guides. The drawer guides are pocket-screwed to the underside of the desktop.
Good Morning, Megan and Chris. I’m settling in with my morning coffee and thinking about feet. My feet, your feet, everyone’s feet! What kind of footwear do you prefer in the shop? Especially when you know you are going to be on your feet most of the day?
I have a boring answer: tennis shoes with silicone heel cups. Basically, what I need to wear to deal with a pinched nerve in my back. Before that, I adored Trask boots (the domestic-made ones).
Until it’s too hot, Blundstone #510s, but I replace the provided insert after about two months with Dr. Scholl’s “Work Inserts,” then I replace those when they start to feel not as comfy. And in the summer, I shouldn’t admit publicly to what I wear…but: Birkenstocks (Arizona)…unless I’m teaching, and then it’s Sambas.
Proved me wrong, I pictured you in high heels with little cat heads on the toes,
Only on special days. Which I could prove, if only the pictures from old posts on PW weren’t missing…there used to be some pictures of me there in 3″ heels, but no cat toes. #goals
Do you use the golden ratio in your designs?
Good morning. My question is: bevel up or bevel down? When do you use that and is there a certain plane that you use for that? (Or is it for any plane?)
Bevel-up vs. bevel-down is pretty just an argument for people on the internet. The differences in the planes are at the margins of performance. Both forms do the job really well. Bevel-ups are simpler tools and usually a little less expensive. Bevel-down is the traditional tool, and is what I learned. I have no problems switching between the two (some of our student planes are bevel-up jacks).
So make a choice and stick with it. You’ll be fine either way.
1.Whats your go to Waffle House order?
2. Is there a particular film/movie that you appreciate for the historically accurate depiction of the funiutrure of that time?
My Waffle House order? Coffee…and only if I’m desperate.
2. “Wolf Hall” – amazing set design https://www.youtube.com/watch?v=gYnnsPvrTq4
Fitz, did you read the last book in the series?
I heard that they it will air in the U.K. in 2025 Then on to PBS.
I have, and am eagerly awaiting the BBC rendition. (If you haven’t read her “A Place of Greater Safety ” – highly recommended!)
Hello Chris & Megan, Do you have any thoughts/tips/experience with table top rule joint on end grain? Thanks, Joe
I’m afraid I do not. When I make drop-leaf tables I go full vernacular (no rule joint). There are entire articles written about laying out and making rule joints. I think the only downside to an end-grain application of the joint would be the spelching at the end of the cut (whether by machine or hand). Sorry I’m no help here.
Regarding Piggly No Wiggly Glue – I added fine salt to a full glue container for the added open time. Worked well. Can I assume the next time I warm and use the glue the added open time benefit remains, sine the salt is now part of the mixture? Thanks much!
Yup!
Constructing legs for the ADB Drinking Table and Worktable: Do I need to find some straight-grained 12/4 lumber to get to the thickness, or can I laminate up from thinner stuff? (My lumber sources in the DC metro area are limited, good 12/4 is hard to find.)
For the ADB staked low stool and chair, I’ve used the Veritas 1″ cylindrical tenon cutter successfully, but the 2″ cutter seems like a beast, can you recommend the 2″ cutter? (I do not have a lathe.)
[Thank you again for these weekly Q&As. I hope you realize how helpful these are!]
Definitely laminate up the top from thinner stuff.
For the 2″ tenons, I would saw and pare them out. Then round them with a rasp. It’s easier than it sounds. I’ve not used the 2″ tenon cutter.
Brandon, you can also come by my shop in Cleveland Park DC and use my lathe. Plus, I’ve made that table and you can have the backup leg I didn’t use. Here’s a dummy email address: little.home0618@fastmail.com.
My stick chair needs a new coat of finish, the simple finish you always use. My question is how would you address the chips from my toddler and the small teeth marks on the legs from when my dog was a puppy? Would you sand them? Use a scraper? When you done with repairs do you wipe it with mineral oil or just clean it well with a cloth?
My guess is that Chris will say don’t bother “fixing” them unless there are loose fibers/sharp edges, in which case sand or scrape them until they are no longer a threat, brush off any dust/shavings then reapply the soft wax. Life is beautiful – keep its decorative touches.
I keep maintenance to a minimum. I scrape off anything that makes the chair uncomfortable to use (a hard edge from a chip, for example). But otherwise, clean with water and apply another thin coat of soft wax.
Another thought is to just leave them. They are the living history of your family interacting with the chair. We have saved a couple wooden toys and the baby books that my kids chomped on, no puppy was involved, and it still makes me smile to see the marks from when my now middle-aged kids were wee-uns.
For the teeth marks, you can try ironing them out with a wet cloth, the steam will straighten the fibers. Of course, only if this doesn’t damage the finish.
Hey Chris, have you read Seeing Like a State? If you want to get mad and feel righteously anarchist it’s a good option. On the other hand who wants to choose anger these days when it’s so often thrust upon us?
Yup. Good book. I am trying to keep my blood pressure down this election season and focus on working with other people of all persuasions. I’m much happier that way.
Could a 12″ Marples or other English turning saw work as good as the Gramercy? I read where Bob Rowaieski converted a Marples to accept Gramercy blades. The Marples can be had for much less for the frame and knobs than the Gramercy but wonder if it can work as a coping dovetails and as a turning saw.
I’m interested in the results here. I didn’t see a marples blade with 10tpi tho so I think at least some of the blades still must come from grammercy
I haven’t used the Marples. I don’t even think I’ve ever seen one in real life. But Bob is a very knowledgeable guy, and I trust his opinion and his work.
I would like to obtain the deepest possible (and most durable) finish on a mahogany veneer auto dashboard. A common finish for this would be a number of coats of (real) tung oil with a generous amount of hardening time between coats, followed some weeks later by some coats of (real) spar varnish with light sanding between coats. Would you suggest another approach to this?
As long as you are using a true marine varnish, you should be OK. There will be maintenance just like with a boat. UV is murder on film finishes.
If it were me, I’d probably keep apply oil over and over until it polymerized like a gunstock finish. But that’s a PITA to do.
Hi Chris: I’m wrestling over whether to build the Roubo Anarchist’s workbench or the English joiner’s bench. It will be my first workbench, and would like it to be my last. I bought 2 Crucible holdfasts and a the planing stop in preparation. I have no interest in end/wagon vises or bench dogs so there’s no issue with having to reach under a wide apron to push up dogs. The singular deciding factor in your choice seems to be that you like to clamp stuff to your top with short f-clamps a lot, and a wide apron prevents you from doing so. What numerous operations make that so imperative that can’t be done with a holdfast or longer bar/sash clamp?
You have found the one flaw in the English design. Clamping stuff to the top is less convenient. Other than that, it’s a great design. Less expensive. And very quick to build.
On my English bench, I only put an apron on the front – the back has a rail about 2″ in notched into the legs. The ends are also free to clamp to. If I need to clamp to the front, I use a long bar clamp and hook the end under the apron. It’s less than ideal but works.
My Benchcrafted workbench takes up a lot of room in the small space that I have for a workshop. So I use it for a lot more than just chair and furniture making. I wouldn’t give up the ability to clamp to the front or back edges of the top for anything. All kinds of unexpected uses including making a sled for my bench grinder so I can store the grinder and then clamp the sled/grinder combo to the top to grind, and motorcycle maintenance such as fixing a skid plate – shhh.
Have you ever used a Compass plane?
Are they useful or dust collector?
I tried one once, and it made cuts. I watched Will Myers use one, though, on his Shaker Candlestand. In his hands, it worked gangbusters.
I have used one a few times and they work as-advertised. But I am more of a spokeshave person because they will do so much more.
Can you put shellac on top of spar varnish and have it stick?
Thanks
Yup. Shellac will stick to dern near everything.
I live in Indianapolis and just recently visited your store for the Lie-Nielsen event. My daughter mentioned to me that Indy has an organization called Chairs for Vets that does what the title says. Do you have any insight on this group?
A little. We had a student in a chair class who donated the chair he made to the organization. But that’s all I know. It woulds like a very worthy cause!
I made the stick chair from the cover of The Stick Chair Book and the worktable from the design book for my wife, she loves them! But now my son has annexed them with his gaming rig, saying it is better than his purposefit gaming chair.
So, I need to make more chairs. The only complain my wife had was that the chair was a bit too laid back for extended computer work, which is pretty much all she does at work these days.
Any suggestions on seat and back angels for extensive keyboard work?
Try a back lean of 10° to 12°. And a seat tilt of 3° or so (one finger, as explained in “The Stick Chair Book.”)
Do you use a riving brake in your shop? If so, how is it constructed?
Nope. We split short stuff here where a brake would be much help.
I’m considering a counterbore for the vise screw nut on my almost-completed bench, to get a little more opening space for the vise. The leg is just over 5” maple, so it’s plenty stiff/strong. Is this a terrible idea?
Also, to anyone on the fence about the Benchcrafted hardware and Crisscross, it’s pretty amazing – thanks Chris for the recommendation 🙂
My inclination would be to counterbore the nut in the leg by 2″ or so. That will leave enough meat behind.
Thanks Chris!
A historical workbench question… my great grandfather’s workbench is serving as my kitchen island in its retirement. It is somewhat Roubo like, with an end vise and a leg vise, both operated by big ol wooden screws. The top is laminated – walnut I think. It is about 3 inches thick and each of the boards that make it up are about 3/4” thick. It has a commercial planing stop mortised into it.
My great grandfather was a farmer, not a cabinet maker, and there is no indication that he possessed the skills or tools to make the big ol wooden screws, or the laminated top. My guess is that the top and vises were commercially made. Do you know if off the shelf workbench tops and vises were available in Ohio around 1900?
The bench in question:
https://pasteboard.co/vLLi9hdONbRI.jpg
Manufactured wooden screws have been sold for centuries. I can’t recall, however, ever seeing an old commercial advertisement for workbench tops. From the looks of the photo, the entire bench was made by someone highly skilled. The entire workbench might have been made by a workshop or commercial entity. Hard to say without an in-person examination.
Well next time you are in NE Ohio you are welcome to pop by 🙂 It’s an odd beast – some aspects seem very professionally done, and some very amateurishly done.
A lot of those old farmers had skills you wouldn’t dream about. My grandfather was a farmer, carpenter and a cabinet maker.
Can you tell me what this is? It’s in the visitor center of an Irish castle.
https://www.instagram.com/p/C5GK_6Go-x6/?igsh=MTJiYnlqaWZlemZiZQ==
https://www.leevalley.com/en-us/discover/what-is-it-articles/whatisit-witch
Thank you! The castle is called Athlone Castle, in the midlands on the Shannon river.
Good Morning ,
I have built a small bench using Poplar for the top and Red Oak for the legs . To get a consistent colour I am going to paint it with General Finishes Milk Paint . I would like to get a higher level of sheen than the flat finish that the GF Milk Paint provides . Any suggestions on a topcoat that might give a satin finish ? Thanks ,
Blasphemy, I’m sure, but sprayed lacquer (which is what’s atop on my tool chest at home). But I’d also consider oil/wax, over completely dry and cured milk paint. Do a test board.
For expert milk paint instruction (including a lovely dull glow sheen) though: https://vimeo.com/ondemand/galbertmilkpaint
I recently got an old lathe up and running but I’m at a loss about tools/accessories. Any recommendations on where to look for total beginners advice? It seems like a whole different world and I don’t want to waste a bunch of money on useless tools or accessories while I’m learning.
We are basic here. I learned turning on a pole lathe with traditional tools. Now I use EasyWood Tools because I’m a furniture maker who turns. Not a turner who makes furniture.
Among the turners, I am a big fan of Alan Lacer. He is a great teacher, nice quy and has put out a lot of good basic information.
https://stores.alanswoodturningstore.com/
Do you have something in mind to make or just want to get a feel for it? Regardless, the tool sets are usually lacking real-world usefulness. A good bowl gouge, maybe ⅜, a ½-inch spindle gouge, a ¾-inch skew, some form of parting tool, a roughing gouge, a couple scrapers. All these tools are useless unless they are properly sharpened. I would direct you to the videos of Tomislav Tomasic. Croatian dude; speaks excellent English. Internet protégé of Richard Raffan, who also has great videos. Tomasic is a bit more comprehensive and someone who is very new to turning couldn’t do better, barring hands-on instruction.
Stay away from the easy tools; horribly expensive and ultimately time-wasting. Unless you happen to love sanding. “Easy” for any beginner to use immediately and without any experience. But then comes the sanding.
and everything else he has to say.
Can you provide any advice or tricks if I wanted to batch out a number of stick chairs, say 4-6, for a dining set? Do I start by making a big pile of parts to mix and match, or take a more linear approach? The wood will be whatever I can find for good, strong legs. They will likely be painted, if that matters.
I buy wood, then transform all of it into parts. Then I usually build two chairs at a time. But I’m not trying to create a dining set where they match. If I were doing that I would make all the parts and build them all at once to ensure the angles and details were consistent.
In AWB, you recommend adding the planing stop and holdfast holes before flattening the bench. Should that order of operations change with an unlaminated benchtop on a Nicholson bench? My benchtop is rough cut 2x12s thickened with 2x10s underneath. Will the holdfasts hold if the holes are drilled when the benchtop is fairly flat but hasn’t been completely flattened?
Either way is fine as long as the top isn’t super wonky. Getting holdfasts to grip 100 percent of the time is mostly a matter of getting a close fit between the shaft and hole. Yes, a true perpendicular hole helps too, but not as much as a close fit.
Thanks!
Just a thought and observation about a post from a few weeks ago about mystery burnishing marks while planing.
I’ve always associated those sort of tracks with wood fibers being stuck in the plane’s mouth. I especially get a lot of those when traversing with a relatively rank cut. They are pretty obvious since I have to pick out the wads of wood before I go back to work.
But when I see the burnished tracks in the wood without finding fibers in the mouth, I just assumed that there are smaller wads of chips/dust/fibers just being pushed along with the planing cut, but they fall away as I brought the tool back for another pass.
Do you have a peasant recommendation for a magic plane to deal with high figure or difficult grain? I know Chris has an infill plane with voodoo like properties. Is it due to some geometry of the tool that can be replicated by changing blade geometry or frog pitch (a la Lie Nielsen 50* or 55* frog) of a metal bench plane? Or is it purely magic? I understand and appreciate the attraction to infill planes, they are beautiful tools.
Infills aren’t magic. They are just very well-made planes. I can set up any decent bench plane to deal with figured woods. The peasant solution is an aftermarket chipbreaker (like the Veritas). Getting the chipbreaker super close to the cutting edge is my preferred solution.
Thank you. I needed to hear this. Off the ledge of tool envy abd back to work.
As always, thanks for you, Megan and all the experts for sharing your knowledge and experience on a Saturday.
When using General Finishes “milk paint”, do you ever add anything as a top coat?
If I want more sheen, I’ll add a thin coat of wax. But it’s not necessary.
I know you folks like western saws, but as far as technique goes, would using a Japanese saw be very different? Thanks!
I switch back and forth all the time between the two forms. I honestly do not even think about their differences. The Japanese saws cut faster. The Western ones are less likely to get kinked by students. I like both, but you don’t have to have both.
In today’s photo the tool wall next to Chris shows a profusion of spanners and box wrenches. Do you ever use them? As I can’t recall any of your designs requiring a bolt of some kind. Thank you.
Those are for maintenance of the band saws and the metal bench vises. Also, sometimes people need one in the neighborhood for a car repair.
You probably don’t chop many mortises with chair making being the focus, but I’m wondering if you prefer regular mortise chisels or if you use the beveled edge bench chisels? Also, is there a trick to getting the mortise perpendicular to the surface you’re chopping it in?
I use mortise chisels all the time for casework. I LOVE the Ray Iles ones at Tools for Working Wood.
By coincidence I watched Jeff Miller’s “Using the Versatile Chisel” last night. It’s a combination about how the chisel interacts with the wood fibers in various directions, body orientation, and practice. You set a square at the side as a visual alignment. I highly recommend Jeff’s video for the sections where he is actually using the chisel.
Look up mortising by Paul Sellers. He has a jig that uses a piece of oak or plywood with either a hard plastic or brass face set into a half lap.
The jig is made to the width of the board needed and relative to the mortise width.
You clamp the jig and piece of wood to be mortised into a vise, or with a clamp and placed on the bench top, and then reference the side of the chisel next to the brass or hard plastic.
You do all your chopping and the jig keeps your chisel in line all the way down the cut.
Very simple jig and works great.
Hi Chris,
I’ve built a Roman bench following Ingenious Mechanicks (love the book!) and with a notch, a couple of dogs and holdfasts and a hand screw clamp it works great for sawing, planing, drilling, etc.
I have a couple of questions about how to get more out of it.
1) What’s the best way to complement it for planing long (8’) boards, aside from starting over with a Roubo or Nicholson style bench? Edges are fine (I do this: https://i.stack.imgur.com/X8Mi5.jpg). But traversing faces rocks the bench, and sitting on the work for long strokes with the grain is a little awkward. For traversing, I found a workaround: bracing a shorter and flimsier bench against the wall (https://i.stack.imgur.com/EVabJ.jpg). What are some time-tested alternatives for the long strokes? Japanese sawhorses?
2) Between a green carver’s vise and a twin screw/Moxon, what would be a more useful addition (for general work and for stick chairs)?
Thanks!
Hi Nick,
For long strokes with a plane, I start at the planing stop and plane the section of the board I can reach. Then I scoot back and plane that section. A Japanese planing trestle would be another solution. When I was working on the floor of my back porch in the 1990s, I used our dining table as a bench for long stuff (clamp a yardstick to the end to act as a planing stop).
I use a green carver’s vise on mine and love it. But I do a lot of chairmaking.
Thanks for the quick reply!
I’ve tried scooting but was not confident in my ability to blend the sections to make the board flat… For the last section, do you turn around and pull the plane?
I feel like a Moxon, placed along the bench, could clamp many of the same things (even if more cumbersomely), but outside of some of your and Peter Follansbee’s posts I don’t really see it used that way…
What’s your favorite way to secure a glued half-lap – pin with dowel, tapered wooden peg, cut-nail, etc.? I have a project waiting on this, I like the look of all-wood joint, but feel that the cut-nail is the simplest & most secure…
In a sawbench project, I cut the joinery & glued the legs to the base. After this – to reinforce the joint – I drilled two large 3/8″ holes per leg and hammered in wooden dowels. But now I have noticed there are gaps as I had to drill these holes at an angle so I did not get perfect circles. Any ideas on how to fill these small gaps between dowel & hole?
One thing I can think of is to wedge the dowels, but ideally I should have sawed a kerf in beforehand. But from what I read, I may be able to split the end of the glued-in but still over-sized dowel with a chisel, then jam a wedge in it (a technique common to Windsor chairs). What do you think?
Hi Megan and Chis!
When I replace the stock blade on my Rikon 306 chairmaking/ripping band saw, is there any reason that I wouldn’t want to use the 1/2″ Wood Slicer? I thought I saw somewhere that you were using a narrower blade for your Rikon, but now I can’t seem to find that.
Also, I have my tool chest shell from the Woodwright’s School that is waiting for me to do the final steps. The stock is 5/8″ poplar and the chest is 17″ wide. I have 4 butt hinges from etsy that are 1 1/8″ wide (from the tip to the end of the barrel), and 2 1/2″ long. Can I get away with using these hinges? The mortise would have to go all the way through the edge of the case with no lip in the front to enclose the hinge, and there would be quite a bit of overhang in the back. Lastly, for these hinges, or if I should use others that are a more appropriate size, could I get away with 2 hinges, or should I use 3? I would rather have it overbuilt, and will have my scorp and maybe some other tools attached to the lid.
For making the tenons on the legs and stretchers of a staked stool, could one use a Ray Isles rounding plane instead of a Veritas tenon cutter?
Yes you could, if it’s carefully set.
Do you ever hand sand after using the smoothing plane?
Oh sure. Sometimes a plane just doesn’t cut it (ha). See also: scraper. (Then sand to meld all the surfaces together if necessary – ’cause plane/sand/scrape all look different)
For a planed and scrapped surface with some touch up sanding like this, do you do multiple grits, or just go right to the final grit (180?)? And do you go over the entire surface with the sandpaper in the melding step, or just certain spots where you think necessary?
Final grit – and I usually go over only a discrete area. Say – a lid, or a single panel. But Chris tested three different surfaces last week (sanded, scraped and planed) with a finish he was trying, and we say no difference. So if I’m in the same situation again, I might do a test piece. Maybe the melding isn’t necessary?
Is 1/4″ too thin for a loose tenon for chair seats? I only have a 1/4″ mortise chisel. I can certainly use a drill to make bigger mortises, but was curious if that would work. Thanks!!
Should work fine, says Chris.
Good afternoon
I’m getting into wooden planes and molding planes. Was wondering what you would recommend for a starter plane : type and size?
Also what size are your wooden rabbet planes?
Thanks
Brian
Hi Brian,
My straight rabbet is 7/8″. I keep a small set of planes – a pair of 6s, 8s, a couple beading planes (1/8″ and 3/16″). Plus a couple of my favorite dedicated profiles: a square ovolo and an ogee.
Matt Bickford’s book “Mouldings in Practice” is the single best introduction to these tools. And he discusses starter sets. His FAQ is also quite helpful.
https://msbickford.com/contact-orders/
Thank you so much for your time and knowledge.
Thanks for reprint on screws on 3/26.
Do you treat plywood as hard or soft wood?
What about mdf, particle board and other sheet goods?
Do you recommend hardening with CA glue?
Thanks.
Most plywood has softwood cores. So I do a test joint before I make a call on pilots and clearance holes. Same with the other sheet goods. Their density varies quite a bit. I’ve never used CA glue in a screw hole. (But I don’t use CA for anything. I dislike the stuff.)
Dear Chris and Megan,
Thanks for doing these Open Wires every Saturday. They are always informative.
I have been wondering about the status of Don Williams’ A Period Finisher’s Manual. I know there was some talk of it in 2019, but COVID, inflation, recession, general decay of humanity, etc. has been prolonging everything.
Best regards
Don recently retracted it from our publishing schedule (his call; not ours). I don’t know if he is looking for another publisher or is abandoning the project. In any case, I’m sure it will be good if/when it comes out.
Will you be considering putting the carved designs you have been working on, on your chairs? Under the seat or on the back seat rest? Protection spell for the sitter? Ward off evil energy?
I have put a few on chairs and stools (by request only). I have found only a few example of them engraved on chairs in Sweden. These were frame chairs and they were on the posts.
I have been thinking about Kale’s “secret sauce” as a maker. I have two “pretty sure it helps” and one strong suspicion.
“Pottery classes” and art classes imply some pretty good hand-eye coordination and manual dexterity which must help. I think hand-eye coordination is strongly related to if not the same as “eyes in the ends of your fingers” which is probably a form of proprioception. As a new service rep (first adult support myself job) I was impressed that the experienced rep I traveled with seemed to have eyes in his fingertips because he could assemble things without having to see them. A few years later I realised I was now doing the same thing.
The further possibility is the pottery, how much was hand building and how much was throwing on a wheel? I have done some throwing and some pole lathe turning, and they are conceptually very similar although both require practice. Throwing is particularly a proprioception kind of thing, one hand is on the outside and the other on the inside when you shape the pot, and you have to have a sense of the thickness of the wall that you can’t see when shaping the wall. I suspect a little of that would go a long way for turning, also I second the ides of no preconceived notions being a serious plus to learning.
When wedging the back and arm spindles to the seat do you wedge all spindles or only the outside major ones?
I have noticed that you only pin the outside spindles to the chair back top rail.
Sometimes I don’t wedge them below the seat at all. It kind of depends on my mood. Historically, not a lot of them were wedged. But some were.
On pinning combs and backrests: I am imitating what I see in the wild. Most are pinned only at the ends. But other times, all of them are pinned. Almost anything goes with this form. And few things are “wrong.”
Getting ready to build the staked work table from ADB (in cherry).
Planning to make the top 28”x60” instead of 24”x52”.
Any tips on adjusting the location of the leg mortises in the battens, especially if I want to bring the legs a little further under the top?
I wouldn’t change their location too much (without a mockup). It took me a long time to get the worktable’s stance looking right. Too much overhang would alter the look. Just my 2 cents.
I just want to offer a sincere “Thank you.” LAP has helped me in my woodworking immeasurably. I learn a great deal by reading (and of course especially by doing), and LAP’s books and other resources are truly second to none in my book (pun intended).
Amen!
Thanks Russell!
Is Locust wood suitable for any furniture type projects?
Honey locust is lightweight and easy to work. Black locust is very hard and dense. If you could make a workbench out of it, it would be amazing.
Do the Ray Iles rounders replace the need for a power tenon cutter? Thanks!
Yep
Found an interesting supplier of cast iron hinges, latches, etc. Look nice. They have a downloadable catalog. https://jwright.com/about-us/
I do not know them. Will take a look.
I have a yellow cordless drill that’s about 2 years old. Recently, bits have been slipping in the chuck. Is this a maintenance issue (and if so, what do I need to do to fix it?) or is just time to replace it?
Thank you so much for doing these!
Sounds like the chuck is mucked up. It happens. I don’t know of anything you could do to repair it. But it can be repaired at service center. Sorry.
Just wanted to let you know that I enjoyed reading the new Never Sponsored substack… I really appreciate the honesty and upfront nature of the writing style.
Just got back from a trip to Baja. I found many examples what seemed to be baja vernacular stick chairs. Gibson-ish, mostly made with found wood, minimal tools, definitely not commercially made or even made by anyone that talented at woodworking.
They sat great and they are delightfully wonky.
I have lots of pictures, I think they make an interesting addition to the vernacular chair family, and though modern, made with what seems like lots of the same tradition of those in wales a few hundred years ago.
Have your people reach out to me at jace.c.mullen [at] gmail [dot] com if you want some pictures.
I’m going to be making some table tops out of air dried walnut. I can’t avoid using a mix of sap wood and heart wood. Any suggestions for evening out the color? Dye made from Van Dyck crystals maybe?
I think you would have difficulty controlling the dye (any dye). Normally, I’d just live with the sap wood and use it to its best advantage.
But when I have done before, I use one of the aerosol toners, which go on after the finish. They work gradually in the way they are applied. You spray. Evaluate. Spray again.
https://www.woodworkingshop.com/product/M1010207/?gad_source=1&gclid=Cj0KCQjw8J6wBhDXARIsAPo7QA_ek2v-8BOOIsCML_v-wgT8gv6ZY2HJsN9KRaEmi9Zg6c3mR_vBR7QaAgJZEALw_wcB
I had a minor accident while wrangling stock in my current tiny shop recently, but fortunately the only casualty was the pride of my toolchest, my vintage Stanley No. 8. The plane body and all components are fine, but the iron got bent and slightly twisted. My attempts to straighten the iron have been fruitless, so I’ve decided to replace it. I’m not precious about keeping the whole thing vintage so I’m considering a modern iron. Are there any in particular you’d recommend? The plane sees fairly regular use as my usual projects are tables of various sizes. Thanks!
I like the Veritas PMV-11 replacement irons for Stanley planes best. They are lapped flat (big time-saver). The steel sharpens like O1 but holds a great edge. And they are thin enough that you don’t have to file the mouth open.
Very much appreciate all the great advice shared here. Two quick questions. What’s the best way to chop an angled mortise, the rectangle sort for a table, not a round one for a chair. And I’m curious about advice on how to cut the female side of a sliding dovetail for a carcase. Thank you
I show the process in “Ingenious Mechanics.” I’m making a square compound-angle mortise for one of the benches. I first drill out any waste that I can. Then I use a sliding bevel – one for for rake and one for splay – to guide the chopping. It’s actually no harder than a vertical mortise if you take your time.
For sliding dovetails, I saw out the walls of the socket. I usually use a strip of wood with a beveled long edge to act as a sawing guide. (This is shown in “The Anarchist’s Design Book” in the Worktable chapter. That book is a free download.
https://lostartpress.com/collections/all-books-1/products/the-anarchists-design-book