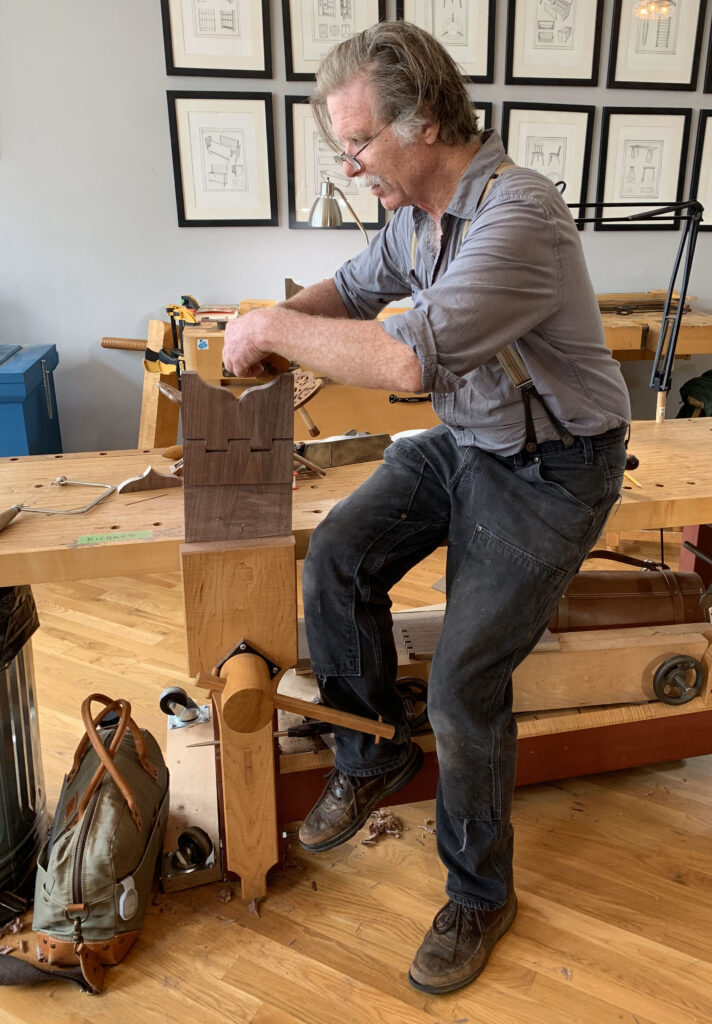
NOTE: We are having technical difficulties with Word Press’s commenting system today. Our replies are not posting. Or they are posting and then disappearing. (Both Megan and I are having this trouble on separate machines.) We are trying to get your questions answered, but it’s frustrating….
The fellow above is here this weekend teaching a class in making traditional sash, so Chris and I are twiddling our thumbs and awaiting your questions about woodworking, cats, LAP books, Shakespeare, the Anthe building restoration (we’re finally on to the stuff that should be done, rather than must be done – so that’s exciting!) or Wilco songs.
So type your question in the comment field and we will do our best to answer it. And know that concision is much appreciated.
Comments for this entry will close at about 5 p.m. Eastern.
– Fitz
Ever tried Osage orange for a chair seat?
It would work but realize it’s very heavy and eventually will turn brown No way to keep the color change from happening. Keep out of sun to slow down.
I have not. We used it to build some cabinets once. It is like sawing and planing rocks.
Say hi to Roy for me.
I have about 16 linear feet of clear 21″ wide pine (species unknown). I have been saving it for a tool chest, but I have started to rethink this as I am pretty much the only person that will ever see it (why flex if it’s only for myself?). If you had that kind of material, what else might you suggest that would make good visual use of single width wide pine? It has a nice wide stripe of heartwood down the center.
How thick is it?
About 1-1/8″. It’s S2S, though very old and dusty. I can reliably get it down to 7/8″.
It would make a beautiful blanket chest, six-board chest, mule chest, etc. Or even a carcase (with uninterrupted grain) for a chest of drawers.
Andrew Hunter made a few different pieces including a blanket chest from some wide pine that he had that have appeared in FWW
Good morning! Thanks as ever for your time & input!
I’m /slowly/ building a confident insect (ADB staked bed) out of kiln-dried red oak. It’s been months in the making due to limited shop time. When not being worked, the wood resides inside my central-NC home where the RH has been 40-50%
I bored the mortises and turned the tenons several weeks ago. At the time they were a moderately-snug fit (I could insert and remove them with just a little effort). Now, however, the tenons fall into the holes and even wiggle a bit. How concerned should I be? Do I need to start thinking about fox wedges?
Cheers!
It sounds like your tenons might have lost some moisture and acclimated to a drier environment. You can always tighten up a joint in a situation liker that by wrapping the tenons with plane shavings and some glue. Fox-wedging is an option, as you mention. But adding a layer of shavings is simpler and less risky. Good luck!
I like the plane-shavings idea! Thanks!
If making cylindrical tenon for chair legs, what controls the depth the leg goes into the seat? Tenon shoulders? How would I make sure I get same depth at final assembly as when drilling and sizing under carriage? Thank you.
Yes, tenon shoulders hold the leg in position. As to the next part of your question, I hope I am following it here. The tenon shoulder on the leg is a hard stop. The legs will go to the same location every time. So your undercarriage will end up in the same place every time as well.
I have a substantial pile yellow pine squirreled away for an AWB build.
There are several pieces which are very resinous. Very heavy, kinda each feeling, and very much like “fatwood” fire starter. But beautiful, straight and knot free…
I wonder if you’ve had experience with yellow pine like this? Would it glue up okay with yellow glue or should I avoid these pieces in favor less resinous options?
Thanks to you both for taking the time to do this. Your generosity with your time, knowledge and experience is an example worth following.
Kind waxy feeling… I’m a bad proof reader.
The resinous boards are my favorite. The resin resists water-base glue, but you can get around the problem. After talking to some glue technologists at Franklin International, they recommended using PVA for these boards but keeping the assembly in clamps for four or five hours. I’ve followed that advice since (this was about 2005) and have been very satisfied with my results.
Hi, I am a prolific customer of your books and tools and just received an order with three more books. Up to now, I thought that my favorite book was Peter Galbert’s, but I just spent two hours with Andy Glenn’s “Backwoods Chairmakers.” I love reading those stories and, subtly woven in amongst them, there is so much good chair making technique too. Thank you!
Thanks Mike. Andy did a hell of a good job!
Just finished assembling a Gibson chair from your excellent video. A couple questions:
1) Over time, your chairs have gotten a bit wider (24″->25″ seat) and the short sticks for the arm seem to have gone from nearly vertical to splayed outward a bit – is there a particular reason? Just for comfort or something else?
2) I noticed on one of the chairs you have a dowel/pin holding the arm in place on the rear post – was this only because that arm had broken and been repaired? Would you recommend pinning the arms or not?
Thanks!
Hi Mike,
My first Gibsons were built from photos alone – I had never seen a Gibson in the flesh/lignum. Then I went to Ireland and measured a bunch of them in a private collection. My later Gibsons are based on those real-world examples.
And the pin is actually a Miller Dowel. I had shaved the post a little too much and the arm wiggled a tad. I didn’t like that so I pinned the sucker.
Your passion for chair-building, and for stick chairs in particular, is obvious. From here it looks like you’ve mastered the art, but interested to know where you feel you’re at in your chair-building journey, what you are striving for, and what motivates you to keep building what, on the face of it, appears like a similar form.
Hi Steve,
I am trying to get each form to a place where I don’t think I can improve it. I’m there with my low back. I am close with by comb-back. I am just a couple chairs away from it with my Irish box chairs. I have a ways to go with my Gibson.
Then I need to dive into backstools, settees and a large armchair form I am attached to.
I am propelled forward by my visits abroad. The more I travel, the more I am inspired to build.
Good morning. How does adding casters to an Anarchist’s Tool Chest change the concern about bottom rot? I’m assuming it removes the need for the rot strips. Other than it being in a flood deeper than the casters, would you still be concerned about the bottom rotting?
If you have casters, then you can omit the rot strips. However, someone in the future might remove your casters….. then what?
Belt and suspenders- if future-proofing is a concern, I’d install rot strips that are wide enough to accommodate the base plate of the casters, and mount the casters to the strips.
Building a low bench from face glued 2x12s. How best do I orient the growth rings.
1. ((
2. ()
3. )(
4. Does not really matter
Cheers ! – You guys rock.
Optimum: No. 1. But I have gotten away with all those other orientations.
The original Skansen bench has a () pattern that I have always though looks very striking from the end. Assuming the current low bench is that original that Chris built for popwood back in the day, I would hazard that the orientation didn’t really hurt anything.
Question about thermal modified Ash. I have been buidling primarly shaker type furniture using Ash as it was relatively inexpensive. But it now has increased significantly in price and I have now converted to Black Cherry.
I understnad TM Ash is rather brittle. Can you share with me its characteristics and workability.
thanks,
John Vogt
Falmouth ME
I have only minimal experience with the stuff. As I understand it, it’s fine for casework. But I’m not sure I would use it for chairs….
Episode 53 of “Shannon’s Lumber Industry Update” podcast has a segment on thermal modification.
Good morning y’all – making a twin bed and was wondering if you’ve had any experience with any of the hook hardware available such as the metal casted type. The boards need to be able to disassembled for transport, etc. the head board and foot boards will be fixed .
So – is a mortise and tenon thru joint going to be better than traditional hardware against racking and loosening over time and if so, any tips? Thank you so much.
Hi Craig,
I’m old school on beds. I use a mortise and tenon with a bed bolt. I don’t have any experience with the hook hardware. Sorry.
I’ve used the hook hardware from Rockler for a couple of twin beds and it works just fine. If you’re worried about racking make the bed rails a little bit wide. Just center the hooks on the ends of the rails. The hook hardware simplifies construction and makes it easy to breakdown the beds if you ever need to move them.
Same answer as Chris.
Build a frame with mortise and tenon joints and bed bolts, and you can land a helicopter on it.
Preach!
As you know, chairs and beds are subject to stresses and strains that no other kinds of furniture are subject to. So the joinery really needs to be indestructable.
I’m saddling my fourth seat and I’m having a hard time keeping a crisp edge, especially near the spindles. Is there any trick, beyond practice?
Also, is there any reason for the pommel other than aesthetics? My dishing is fairly shallow and the pommel rounded, but a friend found it uncomfortable.
The crisp line I use around the spindle deck is the result of practice. It’s not necessary. Antique stick chairs didn’t have it.
Pommels are also aesthetic (in my opinion). They can restrict movement with some people. Eliminate it if you like.
What Wilco songs since 2019 should I be listening to more? Cruel Country notwithstanding, I’m starting to love that one.
I think there’s only one other post 2019 album…and I haven’t listened to Cousin enough to have a fave yet. But I’ll bet Chris has…
Including Ode To Joy! I’ve listened to it a handful of times, but nothing stuck. WARM is my favorite of any Wilco/Jeff Tweedy album in quite a while.
I was going to suggest “Normal American Kids” but then I looked it up and saw it came out in 2016. Once again I forgot my rule to add three years for Covid. I still can’t believe it, but I was lucky enough to see Jeff Tweedy perform a house concert. I requested that song and he said he had just re-learned it. He told us he was practicing the lyrics at the dinner table and his family told him it was the weirdest version of saying Grace that they’d heard.
I so appreciate the finish on the red legs of Megan’s bench and red DTC. Can you let me know the process, i.e. number of coats and kind of primer (if any); number of coats and kind of red paint and if Milk Paint, ratios. And number of coats and kind of final protective coat. Thanks.
Those bench legs are two coats of Old Fashioned Milk Paint co. “barn red,” with a coat of paste wax on top. And I can’t swear yo it…but I think thats the same as on the tool chest, though it might be varnish over the top of that one, as I know our “shop finish” (wiping varnish) was used on the lid. (https://blog.lostartpress.com/2020/01/23/our-shop-finish-recipe/)
Good morning C&M,
We recently inherited a set of stainless steel pans and have been using them instead of our old nasty “nonstick”. Why is it that when you put a protein in a heated pan it immediately sticks, but then releases when done? My working theory is that it has something to do with the maillard reaction.
I don’t know. But the Maillard reaction is meat’s sweet, sweet candy coating.
On sharpening – sorry – I have a downloaded copy of Sharpen This and and found it the best book and video out there referencing microns instead of magic. I went to the non splash stones and am very happy with the way they give feedback or whatever and they are also definitely easier take up less space and are less less messy.
On angles, and I know it really doesn’t really matter for the most part but I just received my Veritas small plow and skew rabbit planes and setting them up this weekend:
Do you recommend a 35 degree honing angle on the skew rabbit blade which is 5 degrees above the 30 degree initial grind and I’m assuming you don’t waste steel and re-ground to 25. Those PMV-11 blades are amazing with no back flattening needed or recommended. I will free hand hone.
The Plow Plane cutters came 35 degree and I plan to simply polish and leave at 35, again, freehand. Okay?
On my LA Block Plane and Large LN Shoulder plane – Grind 25 and Hone to 30 or 32?
Many Thanks!
Hi Stephen,
Sorry for the delay. Some of our responses are heading to the ether.
On the skew rabbet, don’t regrind. Just hone at 35°.
Plow irons: Agree. Polish the whole bevel.
On the block plane and shoulder plane, I do those at 35°. I want consistency and speed. Sharp is way more important that 3° here.
I was very inspired by The Anarchist’s Design Book. I am in the process of build a storage cabinet out of poplar with forged nails. There will be 2 doors in the front 28” high and 15” wide. When researching building furniture with nails I couldn’t find much information on building doors. I plan to use clinched nails nailed through the front into 2 battens on the inside and clinched on the inside. Are these doors too wide for this type of construction or am I overthinking this?
Planning and starting to build this made me realize that there is very little information out there. When I design something, I look at as many examples of what other people have done and take a little bit from each one I like to come up with a design I like. The only good sources I found were Chris Schwarz’s books and magazine article sand Andrew Hunter’s articles in Fine Woodworking. This could be a great opportunity for Lost Art Press. There must be someone who could write a project-based book on nailed furniture. It could include things like kitchen cabinets, general storage cabinets, rustic doors.
Battens and clinched nails will be fine for this application. Thanks for the book suggestion.
Good morning! – what better way to start your rainy Saturday morning over strong coffee (here in the Hudson Valley of NYS) than to discuss Jeff Tweedy and company? What are your top 3 favorite Wilco songs? Mine are 1) California Stars 2) Via Chicago 3) You and I
1) A shot in the arm 2) How to Fight Loneliness 3) Jolly Banker
“Misunderstood,” “War on War” and “Sunken Treasure”
With you on California Stars, the version with Billy Bragg.
Billy Bragg’s The Internationale” is one of my all-time favorite albums.
“Normal American Kids”, “Passenger Side”, “Handshake Drugs”
Not in order and not comprehensive… Radio Cure, Pot Kettle Black, Hell is Chrome/At Least That’s What You Said/Theologians.
Jeff Tweedy was on the Stephen Colbert Show back in January. For those who missed the actual show the interview is available on the show’s YouTube channel. There are two separate videos for the interview.
I am making some open cherry shelves, not unlike the pine ones in the LAP office, in an alcove in my kitchen. Could you recommend a food safe finish that is easily repaired/refinished? Thanks!
Soft wax.
Of course, thanks!
Practically speaking: is better to restore and old handplane or but a new one? (Assume handplane is, say, a pre-WWII model bought for $30)
I think the answer has to be “it depends.” How much restoration does it need, and what’s the plane’s job? I’d be more inclined to restore a jack plane than any other bench plane. And I know plenty of people restore smooth planes, but even nice new ones are fussy to set up perfectly…so I would not try to restore an old one. But I prefer working on wood than on tools; your joy may vary.
Do you have a lot of time or money? That’s what it comes down to for me. When I was starting out, I had time. So I fixed up old Stanley planes. Now I have more money than slack time, so I would rather spend my time making furniture than grinding plane soles.
With linseed oil paint or General Finishes paints do you always use just a brush or also a foam roller? Seems hard to find a roller with a smooth finish. Thank you.
I use a foam roller (4″ or 3″) for wide, flat surfaces with the GF (and a brush of course) ; I have not used a roller with LOP.
Good morning. Would it be possible to order a signed copy of Roy’s book? Thanks
I’m afraid not. Your best bet is to buy a book and have him sign it the next time you run into him.
Will there be another Woodright’s Shop physically or more TV episodes?
Not that I know of.
Good morning from Atlanta!
I’m curious about y’all’s time management and work-life balance. You’re both so incredibly productive (Chris wrote on Reddit years ago he worked 40hrs at the bench and 40hrs on LAP per week??) – building, teaching, publishing, writing, renovating a commercial building and a house, all in addition to family and social lives. Are you preternaturally energetic? Sleep only four hours a night? So enamored of the work that it’s nonsensical to think of a work-life balance because it’s all the same? Focus on the work to the exclusion of other pastimes? How do the both of you structure your lives to do so much work so well?
Chris works a lot more than I do — I used to be more productive…but I’m tired. But, neither of us is good at just sitting around/resting (I’m practicing, though!). I used to be able to work all day then go home and work on my house for 6-8 hours. I can’t do that anymore…and when I try, it knocks me out for days afterward.
When you run your own business, work and life are same. I’m always working and always not working. I work seven days and enjoy the hell out of it. Part of the productivity comes from experience. After 28 years of woodworking and 34 years of writing professionally, you get fast. And a lot of things are automatic.
Hi Megan, what is the current status of your Dutch tool chest book? Thank you.
Cheers,
Michael
I will be turning it in to Chris shortly.
Thank you. Good things are worth the wait, looking forward to buying it.
Cheers.
Hi Chris and Megan! Two quick questions:
1) I’m building a bathroom vanity for our house (the first stage in Project Replace All Our IKEA Furniture With Handmade Ones): have either of you ever made one, and if so, do you recommend a finish that would work well in a moisture-rich environment?
2) Do you have a favorite film adaptation of Hamlet (since Shakespeare was a topical option)?
Thanks again,
Jake
I built all the vanities for our last house. Paint is the best finish. After that, conversion varnish. After that, many coats of wiping varnish.
I built the box for a bathroom vanity out of red oak plywood 20 years ago and finished it with Minwax spar varnish (which I would not use outdoors). It’s held up extremely well. The vanity top is NOT wood and I don’t think I’d trust the Minwax there.
I built mine; it has our shop varnish on it, and is holding up just fine so far, 3 years on (I think it’s 3 years, anyway?) https://www.instagram.com/p/CEefeJRB4Ly/
My fave Hamlet is Branagh’s (but I’m also awfully fond of “Strange Brew”).
Thanks! And really well done on the vanity (and the Strange Brew shoutout) 🙂
J
Just wanted to say I would be interested in the make your own plywood for a stick chair. Wouldn’t it carry over to a lot more design possibilities thanks and maybe cheaper. Did you ever think you will do an Arts and Crafts book? That would be cool and the ones out now seem like they could be better could be a series lol take care enjoy your time with Roy
Laying up your own plywood is a real experience (without a vacuum bag). So I don’t know if I would say it’s cheaper. But the results will be better. I likely will try to find a high-quality lumbercore plywood for my experiments. Then go from there.
Whats the best resource (book, video, article or something) for getting good at dovetails? And Shakespeare wise.. whats the best way to get into Shakespeare if you’re not already into Shakespeare? Thanks!
I found both Chris and Megan’s videos on laying out with dividers great. As far as a book – The Jointer And The Cabinet Maker is also detailed for how too on both tails first and pins first including chopping out or sawing waste. The shoulder registration using a rabbit/shoulder plane can be used on both methods. Looking forward to using my new skew plow plane for the dovetail registration. I’m also slowly going through Christophers videos on building a Dutch Chest and Shaker Table for tips since I’m going to be building both but haven’t got to the part on dovetails yet but confident there will be very good instruction within those videos as well (streaming from Lie Nielsen site).
https://youtu.be/E8SrH6HbDdQ?si=H67Uq_IuTPiVYXLX
Rob Cosman is probably the best trainer for dovetails. But be prepared to enter into his particular world of tools.
I think the best resource is what Chris said in “A Dovetail a Day” years ago: cut one joint every day (maybe two/three tails), and identify the problem(s). Work on fixing one problem for the next day(s). When you have that licked, move on to the next one. By the end of 30 days, you’ll be pretty good.
And on Shakespeare, watch some of the better movie versions (the plays were meant to be seen!) – and start with the comedies. “Much Ado About Nothing” (1993) “A Midsummer Night’s Dream” (1968), “Twelfth Night” (1996). And Kenneth Branagh’s “Henry V” is amazing, after the comedies have you hooked 🙂
Do you have an opinion on the 1995 movie Richard III?
Massive thanks, as always, for doing this!
My ATC question: is it imperative that the runners for the sliding tills go all the way to the bottom of the chest? I miscalculated and find myself lacking timber.
I saw in the ADB that in some chests, the runners are just narrow strips screwed into the sides of the chest. Would the same work for a tool chest, or would it be too risky given the expected load on the tills?
In the latter case, I assume supporting the runners with perpendicular strips of wood (to act as “posts”) should distribute the load as intended, right?
I hope this was understandable. Have a great rest of your weekend!
I think your plan of some perpendicular supporting strips sounds perfect.
Should pinch dogs be sharpened? Points are nor what you’d call sharp but maybe they are not suppose to be “awl sharp? I got some from LV for a table top and used civic acid to blacken and rough up. I swas urprised coming from LV they were made in Taiwan.
I’ve had to grind the points on some pinch dogs to make them work. They should be pointy like an awl in order to grab. Dull ones bounce out.
I built mine; it has our shop varnish on it, and is holding up just fine so far, 3 years on (I think it’s 3 years, anyway?) https://www.instagram.com/p/CEefeJRB4Ly/
My fave Hamlet is Branagh’s (but I’m also awfully fond of “Strange Brew”).
Hi Chris and Megan,
Chris showed JB’s turning saw on Instagram a while back. Aside from being a beautiful tool from a certified badass, I was wondering what you would use a turning saw for in your current workflow. A quieter bandsaw? Traditional coping saw…? Can it replace a coping saw?
Thanks for everything you do.
It’s closer to a coping saw size. Cutting out chair arms and their details. A little bigger one (with a coarser blade) would be good for cutting out seats.
Morning. I’m getting ready to finish a chair and I was wondering if you guys have tried using a rag to apply linseed oil paint? I’ve painted 2 chairs with it and a few other projects with good results, just a lot of effort. My biggest issues were minimizing the brush streaks and also when I touch up with the second coat, it leaves glossy areas that I have to buff out a bit to get it to blend in. The other day I was painting some sample colors on scrap wood (same wood I used for chair) I didn’t have a brush handy, so I just used a rag. And it looked perfect from the get go. Very easy to get the paint even, much faster (including dry time), and no streaks. I was thinking I’m going to use a rag for this next chair with linseed paint. What do you think? Am I missing something?
Thanks a lot for your time!
I have not – but I know that Travis Curtis uses a piece of sponge, and his results are fabulous.
On
I have used the sponge method with great success. One grout sponge cut into various sizes and shapes can do a lot of finishing. For fine work, I have had very good results with cosmetic sponges. They tend to have a very fine texture and leave a very smooth finish. Best of all, you just let them dry and toss them in the trash when finished.
I have not tried that, but now I want to.
Thank you once again for doing this. Just reading all the answers every Saturday makes me a better woodworker. Makes me a better carpenter too, which is how I make a living. So thank you.
I have a couple(ish) questions today:
Which domino do you use for chair seat glue ups? I’m planning to get one in the near future and I’m trying to make the most versatile choice. Currently I’m thinking of getting the 700 and the Seneca adapter that will allow it to cut 500 sizes. I don’t know whether this is a good plan or not.
The mortises in the tops of my armbows have small gaps. They’re small, and not all of them have it, and I’m possibly the only person who notices, but I’m wondering what it comes from (drill wobble?) and how to improve/eliminate it.
Thank you again from a Los Angeles union carpenter and aspiring chairmaker.
I did some research on the 500 vs the 700. The gist according to the various testers is that the 700 is a much bigger and heavier tool meant for the largest dominos. The 500 will do something like 95% of what the 700 will do and be a lot easier on your body. Google comparing dominos 500 verses 700. Bigger capacity is not always better or more versatile. Caveat, I have no first hand knowledge of either tool.
We have had no trouble with our 500; the 700 has been less reliable. Might be a personal problem, of course. (Chris uses the 500 for seats)
My opinion is the 500 is just a better machine. Our 700 has been in the shop four or five times. And it’s never been as good as our 500. I’d sell our 700, but I’d hate to foist its problems on some unsuspecting clod.
For chair seats: use the biggest domino the 500 can make. You’ll be fine.
If you make passageway doors and such, get the 700 and hope you get a good one made on a Tuesday.
Hi Chris,
Gibson chair updates? I’m about to turn a pile of square sticks into round sticks. Earlier in today’s posts you wrote that you are still tuning your Gibsons and I believe last week you wrote that you changed the tenon sizes for the sticks into all 3/4″ instead of 1″ and 3/4″. Could you please do a bullet point of your updates here? Thanks!
The change you mentioned. Plus a drilling jig: https://blog.lostartpress.com/2023/07/06/a-jig-for-drilling-gibson-chairs/
The video has a couple updates (reinforcing the arm and the “washer trick.”
My Gibsons look correct. The path ahead has to do with making the construction process foolproof for students.
I asked a couple of weeks ago about Elm as a preferred wood of choice for chair seats. I was directed to a page that had some info on it, but never told me WHY Elm and similar woods (interlocked grain) were good for seats… Would you please try to expound upon what makes certain wood species good for seats? TIA
Frank
This is merely a guess…and possibly one of more reasons…but the interlocked grain won’t split as one drives in the legs.
Makes sense….
I have a single big thick English Elm board that I am planning to use for my first stick chair.
Beautiful wood.
With species that have interlocked grain, the grain spirals up the tree clockwise for a year. Then the next year it changes direction. and grows counterclockwise. That is why you can’t split it. As to why it grows this way, you’ll have to ask an arborist.
I have a request from a friend to make his wife a chair, he is rather Falstafian while she is a pixie at under 5 foot I am familiar with antique ladies chairs (rocker and overstuffed). Do you have any recommendations on proportions for such a chair and a possible side table to accompany it. I don’t yet have any measurements but in a regular chair her feet are almost 4 inches off the floor.
For shorter people, seat height is the most important dimension. I have no problems lowering seats to a sitter’s popliteal height. They might have to deal with their dining table’s height a bit, but 18″ is too damn high.
For larger people, seat width (left-to-right) is key. And sometimes depth (front-to-back). Seats that are 24″ to 25″ wide are a good place to start. However I don’t like to increase the depth unless the sitter is huge AND long-legged.
I’m making a stick chair using construction lumber. Have you ever done that, Chris? Perhaps as a prototype? Did you ever keep one? What do you think of its long-term prospects?
I’ve made prototypes from yellow pine. If it’s slow-growth stuff, it’s as strong as maple. If I were short on money, I’d use yellow pine or vertical grain fir (and paint).
Go for it! My daily sitter is 2-by SPF construction lumber. What looked like spruce for the seat, two layers face glued. Each layer of two flatsawn pieces. Joints staggered. Denser, pitchier legs. Straight octagonal. Lee Valley 5/8” tenons. Green QS birch crest rail poached and bent in MDF form Chris wrote on. First try with fir back sticks: fail. A couple sheared off when installing. Success with red oak. I’ve made sawbenches, the ADB Trestle Table, and sitting benches from spruce 2-by. And other crest rails and seats bandsawn from laid-up slabs of well-chosen 2x4s.
I made my first (and only) stick chair with poplar for the seat, arm rests, and crest / backrest and southern yellow pine for the sticks. I picked through the big box stacks to find the clearest pine I could. It worked well with draw knife, spoke shave, and plane. The only place I had a problem was the reversing grain around a knot I could not avoid. And the I painted the whole thing.
Best clear finish for indoor windowsill (single pane = condensation). Wood is probably old-growth CVG Douglas Fir.
Marine varnish from a boat store, not the home center.
Linseed oil (purified or refined). Apply it every year and it will get better and better.
Thanks as always for taking the time to share your knowledge. This one’s not just for you LAP folks, but for the hivemind. I’m in the process of building out a new 12’x16′ shop, a shed on a crushed stone foundation. Overhead lines dictate a lean-to roof which is fine because the roof will face south for eventual solar power. (I’ll pull from the house until I can afford the components for the solar rig.)
I think I’ve included the features for a great shop in my planning – as much natural light as I can manage, a double door for loading in/loading out, wood storage, a sturdy floor (used oak flooring from our local architectural recycler), insulation, power, climate control, room for a handful of power tools for milling and a decent band saw. And a solid 8′ bench, natch. (Water is a no-go, unfortunately.) But I still worry that I’m missing something that I’ll regret not planning for in the building stage. FWIW, my main goal is furniture, typically tables and some casework like bookshelves.
So – am I forgetting something? Or is there a nice-to-have feature that I might want to consider? Thanks in advance.
Geeze, sounds like a better shop than ours.
Northern light is my favorite for working. My guess is you have that covered.
Do you have HVAC? a mini-split is great for controlling humidity and making things bearable in most climes.
I live in Maryland, so a dual mini-split is what I’m going to use for climate control. The tall wall will face almost due north so I’m planning some clerestory windows on that wall, which I’m hoping will give me the best of both light and storage worlds.
What I meant to say there was “I live in Maryland, where AC is a necessity, so a dual-mini-split etc.”.
I’m sure you’ve thought about power 120v and 240v, and probably are already considering a sub panel in your shop from your house. Having recently done a solar array on our garage, I’ve learned that it needs at least two data lines. Pair that with limited WiFi coverage in the garage and I would strongly recommend laying a conduit for data when you trench for a sub panel. And run at least three lines when you do it, two for solar and one for your own use. So much easier to do all at once. I wished I knew that before our install. Instead I was trenching by shovel myself this past winter to fix a broken Cat5 cable that was direct bury.
I hope Roy has a copy of your Workshop Wound Care book.
We gave him one when we were in Pittsboro last year.
Signed in my blood!
https://www.instagram.com/p/CmKgeIgOX59/
My second drinking table from the Anarchist Design:
•a six board glue up for the top and about 3 inches where there is a tiny but visible gap. How to best hide?
•using Curtis Buchanan’s black over red milk paint finish I was thinking of using soft wax on top instead of oil. Will that work?
Thanks for this wonderful forum.
Do a test board. Always. And make sure the paint is all the way dry. (But it should). And, the wax will quickly attact dirt etc to the gap, and hide it 🙂
https://www.hingeoutlet.com/products/softwax-wax-filler-system-for-wood-sold-as-kit
Dear Megan,
Thank you for your and Chris’ time answering questions. Allow me pick your brains on the Bard’s work…I’ve read several of his plays this year for the first time (Scottish Thane, Othello, Hamlet). The endings seem rather Tarantino-esque. Can you recommend any of his dramatic works that don’t end in the entire cast being slaughtered ?
Well those are all tragedies! Most of the comedies don’t involve (a lot) of death. Try “Much Ado About Nothing,” “A Midsummer Night’s Dream,” and “Merry Wives of Windsor” – and “The Tempest” if you want a “problem play” instead of a comedy (it’s one of my favorites!). Definitely skip “Titus Andronicus” – so much gruesome!
Thank you, I’ll grab a comedy next.
Does your daughter sell her soft wax stickers separately? I’d love to have a couple for my toolboxes, but I’ve never been able to get one off the lid successfully. Love the way the wax works and looks! Thanks.
She doesn’t. But you can make you own sticker with this pdf (this is what she uses to make the labels):
https://www.dropbox.com/scl/fi/ln4s98eblbiyc5zqdy663/NEW-BEE_roll_label2inch.pdf?rlkey=xzf7xdxcfd6rumf09n0d63gf7&dl=0
I am restoring my grandfather’s slant lidded tool chest. I am replacing the lid which fits inside the opening with solid sweet gum. (The original lid was birch plywood). The rest of the chest is made of pine which I am going to paint lamp black. The gum lid and base moulding will be finished with a natural danish oil. My question is what kind of hardware to use specifically to latch the lid shut. Granddaddy used a hook and eye but I want something lockable and I don’t want a bright brass but something that matches from the hinges to the handles on the ends and the lid latch or hasp. Any suggestions?
The lid hinges down by the way
Would a half-mortise cupboard lock work? Those would be mounted on the inside of the lid and not have to match (except the escutcheon). It sounds like the lid is basically an inset door. Otherwise a hasp would work (with a nice vintage padlock).
I recently read one of your old blog posts about 3 legged stools where you mentioned engraving spells on the seat. I love this idea but have never tried carving. What is a good introduction to methods / tools to add this to a stool?
“The American Peasant,” once it’s printed 🙂 You might also have a look at Jögge Sundqvist’s books, “Slöjd in Wood” and “Karvsnitt” – but the type of carving Chris did on the stools is part of what he’s exploring in “The American Peasant.”
Also, some of the entries in that category (drop-down menu on the right rail of this blog) talk about it:
https://blog.lostartpress.com/2023/10/26/engraving-tools-in-stock-a-new-video/
I was all set to drill my long stick mortices for a Gibson chair, and my Godrilla got hung up and twisted the shaft. I did not have any spare hex-stock on hand (I now have a few 3 foot pieces on hand in case of another such situation…), so I dropped a stiff wire through the hole instead, and took a sight line and set a resultant on a sliding bevel, and drilled from that. They turned out to be the most accurate I have done. Just sharing, in case anyone else might find the approach helpful in an emergency. I also found that setting my drilling rigs under the arms makes it easier to see when the arms are level; I can never seem to get a tape measure in a spot that doesn’t have me measuring on an angle.