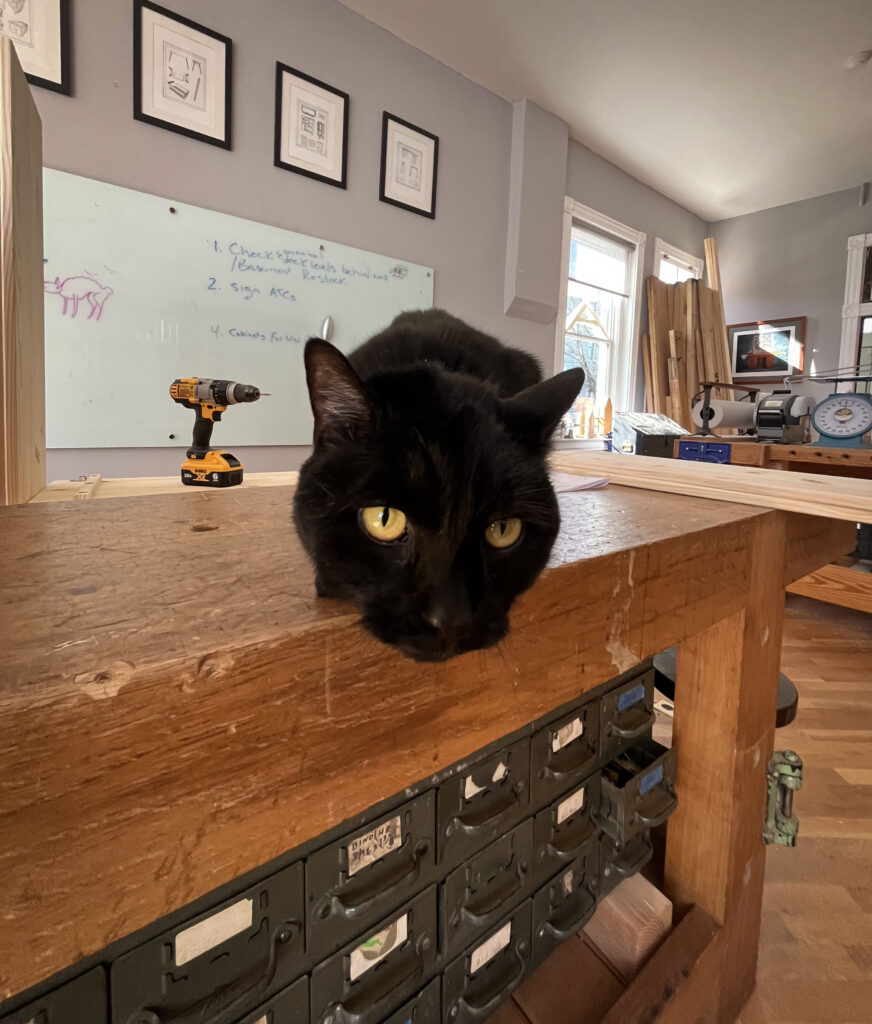
Comments are now closed. We’ll circle back after hours for any unanswered ones.
Psssst…or pspspspsps… You. Yeah, you! You got a woodworking question? Ask in the comments below, and my amanuenses (Chris and Megan) will do their best to answer. At 5 p.m. Eastern, though, they have to stop. It is then time for treats.
Good morning, hope the storms didn’t cause any issues. looking forward to new books. Soon I hope?
Matt Cianci’s book on saw sharpening is all but done. It will go to the printer in a couple weeks, barring any unforeseen disasters.
We got some nasty rain. But otherwise….
Hey guys! I will be making Chris’ nailed bookcase from the Anarchists Design Book as my next project but I will be increasing the length to 60″ and the depth to 16″. Would you add a vertical center partition to keep the shelf from sagging with these dimensions or will the nailed back still provide enough stiffness even at this length? Follow up, if you would add a divider what joinery would you use to attach it to the carcass and the shelves to it? Thanks!
As always, it depends on the load. Visit the Sagulator and play with it:
https://woodbin.com/calcs/sagulator/
My gut reaction to your scenario would be to simply add a dropped edge to the upper shelves. It will stiffen up the shelves and not complicate construction.
I am looking to build a pair of the saw benches described in the Anarchist’s Design Book. In it, you recommend six degree tapers on the leg mortises. Lee Valley has chuckable reamers and pencil sharpener style tenon cutters, similar to those pictured in the book, but only at 12.8 degrees. The only six degree tools I’m finding are the wooden (and pretty expensive) hand variety on sites like Tim Manney’s. Do you have any recommendations on six degree tools similar to those in ADB?
Thank you for taking the time for these open wires; they are much appreciated.
Just use the Veritas versions. Both 6° and 12.5° work fine. There are some small makers out there who make a 6° power reamer, but that’s not necessary for this project.
The LAP reply is spot on. Going from 3′ to 5′ span is a huge change in terms of deflection of the shelf (which is what you need to worry about, not so much the strength). The formula for the sag is proportional to the cube of the length. The Sagulator is great and if you are going to fill the shelves with LAP books (or others I guess…), I suggest you weigh a foot’s worth of them to get an idea of the load.
A few months ago (or maybe years?) Chris was experimenting with a hollow auger for making tenons. What was the verdict?Any thoughts on this tool?
Something like this:
https://www.jimbodetools.com/products/stearns-hollow-auger-88077
I like hollow augers and had good results with the A.A. Woods version. I switched to the Veritas Power Tenon Cutters for speed’s sake. (I still use a spoke pointer for a lot of things…..)
Hi Chris and Many Thanks,
I am trying to get my panel saws together and found a 8 ppi/7tpi from Thomas Flinn in a 20” size (I’m a 5’4” lightweight) that has a tapered plate (.006”), hand sharpened and also Breasted which the late David Savage seemed to have loved (I read on your blog and the Rowden website) even keep it over his LN panel saw when he put tools in your ATC for the winner of the Chest..
I spoke with TF (they also carry Elemen’tary now), and they will make me a 20” 6 tpi rip as well as there standard cross cut in 7tpi. Their standard rip is 4.5 tpi which seems to course for cabinet work.
Yes, I can sharpen a saw that’s in decent shape not needing resizing, reshaping, etc… but I have to send off for major work which as you know with shipping is usually over $100. Bottom line, a good vintage saw restored will cost me twice what a Pax will cost and I’d only have to touch up the teeth now and then.
The Question is:
Does a Breasted saw plate and a tapered plate make a smoother cut as claimed? I’m also curios history wise about breasted saws since it does make sense to me but that doesn’t mean much! Thomas Flinn taper grinds the plate .006 from top to bottom AND breast the Pax and Roberts and Lee saws s well as hand sharpens them. Actually their Lynx brand is also the same plate but not rested or hand sharpened (an easy touch up in my saw vice) and ugly handles. Any experience with their saws recently?
Thank You!!!
I haven’t used a Flinn saw in many years. I’m sure the steel is still great. But the handles look the same: very uncomfortable. Look at vintage handles. They have been full rounded over – usually by hand. It makes an enormous difference.
Vintage saws are worth seeking out and paying for. That’s really my bottom line on this topic.
Taper-grinding and breasting are all very nice things to have in the big saws. They were standard on old saws. I’m not knocking Flinn or PAX or any modern maker. It’s just tough to compete with old Disstons or Atkins.
It seems funny that, along with easing corners, flattening backs, adding secondary bevels, etc., it’s not also common to put in a bit of rasp time on the handles of new (to us) tools. Put another way, “I sure like this object, if only this piece of wood on it were shaped slightly differently”.
I’ll modify any wooden tool that comes into my shop. I’m annoyed when a manufacturer makes a tool that hurts my hands.
For new tools, I spend more time on modifying the wooden handles than on improving the attached steel.
As Chris pointed out, rounding the handles on new western saws makes them much nicer.
Even when I don’t reshape the wooden handles, I strip the factory lacquer and refinish with linseed oil. That feels much nicer to me.
Thanks Christopher. Hard to find 20″ vintage saws but I’m sure I will eventually.
Why do you need panel saws in particular? They are rare even in New England. Why not use 26″ handsaws? That’s what I used for many years until I could afford and find panel saws. Panel saws don’t cut better. They are just smaller and easier to store.
I bought the Osborn and they never showed up after 10 days, called and they promptly sent another set out and I am very happy with them. I said I’d send the first order back if I ever got them). They were a pleasure to deal with. I needed a pencil compass, other than my architectural tools, and am waiting for the final chapters of The American Peasant Book to use with your engraving tool – after I order it! – and thank you for the chapters you sent as a North American Peasant member. I enjoy the subscription and have lots of laughs while learning:)
Yep, smaller and easier to store is the reason. I can hold off and use what I have. I’m building the Dutch Chest to store all my tools (after a sewing table based on your Breakfast table for my wife’s studio).
Hello all, I was recently watching one of Chris’ chairmaking videos and he mentions using a curved bottom spokeshave to refine some of the edges. Is this a Boggs style spokeshave like Lie-Nielsen offers?
Veritas: https://www.leevalley.com/en-ca/shop/tools/hand-tools/spokeshaves/112212-veritas-roundspokeshave?item=05P3374
Thank you!
Good Morning and thanks again for answering questions.
I am building a dining room table with a 1” thick top, 3” apron and I intend to build a set of stick chairs to go with it. If the table top is set at 28” high, the bottom of the apron would be 24” off the ground. With the stick chair seat at 17” (or even 16”) and the arm bow 8”, the arms will run into the apron instead of going all the way under the table. Is it typical for arm chairs to not slide all the way under the table but hit the apron?
I have considered just building side chairs. What modifications to the stick chair are needed to build them without an arm?
This is why side chairs go on the sides and armchairs go on the ends (under the tabletop’s overhang). Check out the Staked Backstool in the Anarchist’s Design Book (a free download) for my take on a stick-chair side chair.
https://lostartpress.com/collections/all-books-1/products/the-anarchists-design-book
Hi Chris. For the staked stool, what were the two sizes of Veritas tenon cutters that you used? Thanks.
1″ for the seat and 5/8″ for the stretchers.
I will be visiting OH from out of state next weekend and will be driving by Covington next Saturday. Is it okay to knock on the door or are you back to being open only on specific dates?
If we’re here, we will welcome you in (we’re usually here from about 10 a.m.-4:30 p.m….unless we’re at the lumberyard or something)
Don’t kill me if this question has been asked 100 times but what is the best way to fill small cracks, nail holes, or boo boos short of a Dutch repair.
Are you painting? If so, Durham’s Rock-Hard Water Putty.
Have y’all ever done a boxed set of the Anarachist books? I have a couple of people I’d like to gift them to.
Thanks for all.
Not Chris, but a custom wood box made by you would have more meaning. Order the books and then figure out the size. Leave some room for finger grip on the books. Lid is optional.
A mini Anarchist’s boarded bookcase would be appropriate.
Make it a book sleeve, not a “box.” That way the spines show so you know which book is which and they can slide out easy. Have made several using1/4 inch cherry, laser engraved on one side, as gifts for friends.
We have not. It’s something we will do at some point. But the design book is not the same form factor as the other two books, so a slipcase is difficult if not impossible.
Respectfully, sir, I never thought I would disagree about anything woodworking with Chris. So, maybe we mean different things by book sleeve, or slipcase, but I see no problem, certainly not difficult or impossible, in making such for the 3 books. I just looked at them to make sure I wasn’t thinking of a problem, but I certainly don’t see any problem in making a slipcase for the 3 of them. Yes, all 3 books are not all the same size, but, I don’t see that as an issue. It’s not the same neatness of a slipcase made for a single book, but . . . Just imho.
Maybe a version of The Packing Box, with hinged lid?
I’m building a Gibson chair. In the video you used a spade bit for drilling the arms – do you still use spade bits for that? I used the Wood Owl auger-style bits and ended up breaking both arms during the drilling step… trying to decide what to change next time for better results.
I use spades and WoodOwl Overdrive bits these days. I’ve also switched to 3/4″ bits for mortises in the arm and seat. That makes things easier.
Thanks, that makes a lot of sense – I presume the legs are still 1″ tenons, right?
Yes.
If my feebleness with all things digital wasn’t a daily occurrence, I might develop a complex about it. I downloaded the alternate arm jig plan from the Gibson chair video. Upon attempting to open it, I was told it is an unsupported file type (.skp). I did my research, and downloaded Sketchup. Created an account and logged in. Still an unsupported file type. I rebooted the machine, a Chromebook to no avail. I am clueless as to next steps. I have yet to attempt the last two steps on the iPad. would I expect better results there?
Hi Jerry,
The cutting list for the jig is here: https://blog.lostartpress.com/2023/07/06/a-jig-for-drilling-gibson-chairs/
I made a screenshot of the orthographic view of the jig with dimension you can download here:
https://www.dropbox.com/scl/fi/6cymzv1bty5p84j2ryppu/Screenshot-2024-03-16-at-10.48.54-AM.png?rlkey=0s351a4yy05rzpgzl24817rt6&dl=0
Between that and the photo on the blog you should be able to make it work. Sorry you are having trouble.
Wow. I don’t remember ever seeing this one. I was expecting to see the washer trick in action. I know I had possession of that at one time, but I haven’t a clue where to look. Memory is truly a terrible thing to lose. I speak from experience.
Try this.
b5980a9766
What panel saw would you recommend for resawing that is currently available on the market?
Thank you
I’m the wrong guy for that question. I wouldn’t resaw with a panel saw.
If I had to resaw by hand, I’d use a big frame saw. Or I would rive the material if possible.
I did it once, with 26” rip saw I paid $15 dollars for and filed myself for the first time. Switched back and forth between it and a new pax rip, didn’t notice a lot of difference the new Pax 26” 5ppi was a bit faster. Peter Follansbee wrote about it, the technique he described helped. I believe Roy Underhill describes similar using a rip saw also.
https://pfollansbee.wordpress.com/2011/02/08/re-sawing-walnut/
Thanks again for everything you do to support hand woodworking. I have made many stick stools and feel quite comfortable. But I’ve never put a back on them. I’m about to make a set of stick side chairs . An armchair has “structure” forward of the back contributing to strength and stability, largely lacking in a side chair. What are the considerations in designing the back of a side chair? There is an excellent explanation of HOW in the Anarchists Design Book but not WHY. I looked through the Stick Chair Book and also couldn’t find answers. Thanks
I’m sure someone could give you formulas, (six back sticks up to a sitter of 275 lbs. etc.) but I cannot.
Side chairs/backstools don’t receive the same forces that armchairs do. Mostly you need to support the sitter’s back. At worst, you need to support their entire weight if they are evil and tilt the chair onto its back legs only.
When I design a side chair, I use dead-straight oak/ash for the back sticks. And I add enough sticks until my prototype feels right. I usually get really close to bang-on by imitating surviving examples. I don’t do more than that.
Is it important to release the tension on your bandsaw blade when you’re not using it?
I was taught it was important to do this. But now I don’t believe it to be true. I haven’t released the tension on any of ours in years….
I don’t either. My bandsaw is my Dad’s 1960
‘s or 70’s Powermatic 141. I glad to hear this as my arthritis makes it very painful and slow to turn the top knob 30-50? times to release then retighten the next day. Glad to hear!
My Rikon comes with a top knob which just lifts off. I took it off and made a small wrench of oak with a steel rod across it which gives me more than enough leverage to easily up the tension.
I was told that this is a holdover from the days of cast babbet bearings that would deform under the constant pressure. Not sure if that’s true or not.
With older rubber bands with the blade tension on might take a set, leaving an out of round wheel. The newer bands are better and less likely to take a set. There is another reason though. Not all of us have air conditioned and humidity controlled shops. Moving the parts that can be adjusted every once in a while reduces the accumulation of dust and eventually rust. Suggest once a year deep clean and re-lube.
Good morning- I’m currently building my fourth stick chair. First three went surprisingly smoothly. With this one, as I was dry fitting the arm bow with the sticks using a hammer to gently fit everything together, I cracked one of the arms. I immediately glued it up and it looks good as new. I tried again and same thing happened to other arm. Glued it up. Looks good as new. My question- how many times will you save/salvage a part of the chair before you decide to turn it into firewood? I’m just wondering if the wood gods or maybe stick chair gods are telling me to build a whole new armbow. Thx!!
If you have cracked the arm twice, you likely have some misaligned mortise that are stressing the arm too much. Lately I’ve been doing a “preflight check” with student chairs before the glue comes out. Here is the briefest explanation:L
Hope this helps!
Thanks much!! Will give it a try!
In your most recent “Earlywood: Cut the Cord” post, you mentioned “early on” your wife had health insurance you could depend on. Private insurance is very expensive. Is that what most independent wooodworkers use? Or do they also often depend on a partner who has health insurance through a business? (Our whole health care system traps those who want to get out of their corporate jobs. Health insurance is the only reason my wife and I have decided to keep going in our jobs until we can get premium subsidies in a couple of years.)
A lot of us use Obamacare/exchange for insurance. We now are members of the local Chamber of Commerce, which has a group plan. There are alternatives out there.
Thanks! That’s a great help. If anyone else uses other alternatives besides the ones Chris mentioned to private insurance (in the US), I’d love to know.
Have you had trouble with milk paint (the real stuff, not acrylic) not sticking to Durhams water putty? I used a very old piece of pine for the front of my DTC and filled in a defect, and the milk paint doesn’t want to stick to it.
I haven’t – but that doesn’t mean I won’t some day. Brush on a lick of shellac over the putty, and paint over that.
Good morning. I hope you had time for a good, nourishing breakfast sandwich this morning.
Could you recommend a specific Starrett compass/divider for use with the Crucible Engraving tool? I recently got a Starrett divider from Patrick but the “leg” is much longer than the mounted tool.
Thank You and have a great day
The Starrett 92-6 works great with our engraving tool. My budget choice is the C.S. Osborne 104-6.
https://osborneleathertools.com/product/extension-divider-104-6-104-8/
It’s not as refined a tool as the Starrett, but it is well-made in the USA.
Hi! I found an old set of Stanley dividers, model 58 I believe – and it has done really well in my first few tests with the engraving tool. It isn’t Starrett, but this solution works for me — and it’s a solid pair of dividers otherwise.
In the few years since I first read the Anarchist’s Tool Chest, I’ve grown less and less happy with the IKEA bookshelves throughout my house – a suite of Hemnes in the office, and then a pair of Billy in another room. I’m not proud of this, but I’m willing to bet I’m not alone!
Moving forward, I’m keen to build at least one boarded bookshelf the Anarchist’s Design Book as it is designed, so I wonder if there are modifications to that design that you would recommend for a taller bookcase of, say, 8 feet that I could build to replace the IKEA shelves. Or is there another Billy-killer design that I should consider?
Thanks, as always – I’m glad you didn’t have any tornado damage.
I’ve built a couple versions of that bookcase – the one modification I might make to the shelves in my tiny bath is to add a face frame that uses the same sorts of mouldings as are on my window and door casings, just to make it look like it’s always been there. https://www.instagram.com/p/Cm1u0sXugtP/?igsh=NnU5dnJ4NTB5YXFm
But I’ll likely never get around to it.
When I get into bigger shelving situations, I always turn to built-ins. This is how I go about building them in their most basic/simplest form.
https://blog.lostartpress.com/2021/07/05/covington-mechanical-library-shelves/
There are lots of ways to complicate it if you like. But when you do big shelves, make boxes and fasten them to the walls.
Are there alternatives to the LN drawer lock chisel since they are no longer made by LN? I have seen some from the UK but not with the flat surface above the bevel to strike. Have you considered a Crucible version? I noticed it being used in The Joiner And Cabinet Maker.
The alternatives are to use a butt chisel. Or do what we do: remove the handle of our socket chisel and do the work. Drawer lock chisels are required in few situations. In fact, I didn’t need one for that small chest. But I had one so I used it. I sold mine years ago and have never wanted for it.
Hey Chris I was wondering how you would go about shipping a full size chair (ex. A six-stick-comb-back) to a client across the country? Is there any way to introduce some rock solid knockdown joinery (that would be relatively easy for a client to assemble themselves) for a piece like this or would you just have to suck up the exorbitant shipping cost associated with such a large sized shipment?
We make crates for our chairs. Here’s how:
https://blog.lostartpress.com/2018/09/17/one-way-to-build-a-crate/
I can’t imagine a knockdown stick chair design that I would be comfortable shipping (not without CNC accuracy for the parts). Assembling the chairs takes some skill – even in a perfect situation. It is an interesting intellectual exercise, however….
Hello..
When building a workbench and you want it to be as stable as possible, is it better to add mass to the base (i.e thicker legs and stretchers) or have a thicker top?
Also, any general advice on face glueing two large-ish (12″ x 48″ ) pieces of (soft) wood?
Thanks…
Lino
I hate to be that guy, but I think you should read a book on workbenches to answer your questions for yourself.
You can download this one for free and get all my thoughts on benches from the last 23 years.
https://lostartpress.com/collections/books/products/the-anarchists-workbench
Im sorry if this question has been answered extensively but I have struggled to find the information in the depths of the internet….which direction should you orient the grain for a chair seat? Specifically a dining style chair seat that rests on top of a skirt and does not interact with the back slats?
There is no hard-and-fast rule. They can go either way. You just have to accommodate wood movement between the frame and seat.
Hi Chris, hi Megan. Just wondering why electric routers with all their different bits are not part of your toolkit. Thank you.
While some people think the world is divided into hand tool and power tool camps, I see it differently. There are router people and no-router people. I used routers for many years at Popular Woodworking and realized I am not a router person. So I design my furniture in ways that don’t rely on the tool.
Routers are amazing tools. I totally get them. But I don’t want to use them.
Amen, I sold mine! I hate the noise, dust and safety issues. Now,
only a band saw.
I hate loud noises, and I hate fine dust. Routers produce both.
Hi Chris. Thanks again for doing this.
I’ve built a few stick chairs based off the design from your video. I’m now planning to build some armless versions to save space on the side of our table.
Do you have any tips or advice for building an armless version? I’m concerned about getting the comb to float in the right place, and wondering if I should create some sort of armless-armbow/lumbar support, but worried that it might look too funky.
What you are describing is more like a fanback Windsor chair. This form isn’t common in the stick chair world. Take a look here:
https://www.dutchcrafters.com/Amish-Asheville-Fan-Back-Windsor-Dining-Chair/p/3355
You can see there are thicker posts beside the spindles, and that’s where the comb gets its strength. If I had to build a tall backstool like this I would take dimensions from a fanback and stick-i-fy it (octagonal parts etc.)
I have built quite a few side chairs out of maple, cherry and walnut with 5/8 dowels made with the veritas dowel maker. The design is a smush of the welsh stick chair and Peter Galbert’s fanback chair. Octagonal legs, a hardwood seat and just the 5/8 dowels. They are remarkably solid and have no need for oversized outside sticks.
Thank you for this, I like the simplicity and I can see a path to stick-i-fy this.
Another somewhat unrelated question: are you aware of any shop-made benchtop laser holders? I’m thinking of taking your video from yesterday a step further and using two lasers, and I’m trying to avoid reinventing the laser stand. I think Greg Pennington does it this way but I can’t find any info on his in a search.
If you search through Greg’s feed you will find images of his shopmade laser doohickies. Basically they are platforms that pivot on a tightly driven dowel. I’ve used them and they work great.
How big is a wee-tad?
More than a frog hair. Less than a skosch.
May I suggest a look at Chris Buchanan;s democratic side chair?https://www.curtisbuchananchairmaker.com/store/p32/PDF%3A_How_to_Make_a_democratic_Side_Chair_%28digital_download%29.html Price is “pay what you can” and a look at the pdf prices for LAP books should give an idea what is reasonable if you aren’t down to your last nickel. You don’t have to make octagonal bamboo turnings but it will certainly give you an idea of sizes for parts. The seat is also a bit of a break from Chris’s but you could easily put his seat into what is basically another stick chair design with fancier sticks. Guess what’s on my round tuit list 😉
Esther the 73th knight of Windsor who isn’t into the steambent parts for another Dunbar NYC side chair…
Hey there, I recently bought some “Fine Finish” cut nails in 4d and 6d sizes, and I noticed there were a handful of nails in each that were twisted or missing a head. Is that typical for cut nails, or did I get a bad batch? Thanks!
Sadly it is common now.
Not Chris/Megan 2 cents. TL;DR = earlier industrial production processes are imperfect. I’ve bought hundreds of the Tremont and Clouterie Rivierre (very different processes). At least a few malformed Tremonts per bag, sometimes more. Two “headless” out of the twenty 1” brads I used Tuesday, for instance. (This style works fine for me without the head.) Almost never a malformed Rivierre, but length varies. I can always pick through to find a shorter one if needed.
Good morning and thanks for being here to start the weekend!
I’m building “The American Trestle Table”. Chris, you mention drawboring the bridle joint, but don’t give details. (The pointed-to article on drawboring isn’t in the collection of Woodworking articles, sadly.) My initial thought it that one 3/8″ peg should be strong enough, but I am not happy with putting that through the glue line. And a single peg doesn’t really help the joint resist rocking.
Did you use one or two? What would you do today?
Thanks.
I used two 3/8″ pegs. Drawbored. I’d do the same thing today.
Thanks! That makes sense, and it’s nice to get confirmation that I’m thinking the right thoughts…
Hi, Chris and Fitz!
I acquired an old ATC from approximately 100-125 years ago.
The owner died and the family kept it for a couple of decades and did nothing with it. When they found out I liked old tools and tool chests the gave it to me.
It’s in pretty good shape all things considered and I am going to try and rehab it.
The bottom, sides, skirts, and too is in good shape. However, the lid was apparently allowed to fall backwards many times (apparently a stop or chain was never considered to be installed) and the hinges tore out so many times it was re-drilled until no wood was hardly left.
The owner later used water putty to plug the holes and then cut new mortises next to the old ones to re-install the hinges.
They then allowed the lid to fall back a few more dozens of times until the wood in the right hand side spit a few inches deep.
The holes also became so “wollared” on both case mortises they will barely hold the screws.
My thoughts run to splicing new hardwood in (the ATC is painted 7/8 old growth pine with 22 inch wide boards) and recutting new mortises,
or drilling deeper down into the screw holes/mortises and gluing in hardwood dowels to hold the screws.
Any advice you have would (wood) be appreciated, as always!
I’d cut out the bad areas and glue in a patch – and maybe also install longer-than-necessary screws (belt and suspenders).
Thank you!
Wollared holes are a common issue in wooden boat building, especially when screws are sunk into softwoods. I know it isn’t a 17th century technique, but epoxy has been used for over 45 years to distribute the fastener’s load over a greater area and diameter. See the link below for detailed instructions.
I have some vertical grain old growth Douglas fir from 300 foot-tall 1000 year-old trees that I’m building a tool chest from – the wood was recycled from a 1940s book shelf. Because it it is vertical grain it seems likely to split. My solution is to do what Chris did to repair the arm of the Gibson chair that blew out. I’m going to resaw thin pieces on the bandsaw and laminate them to the boards to create two-ply perpendicular grain plywood at the ends where they are fastened together. You might be able to do something similar to the top in the areas where the hinges are located and possibly at the ends.
https://www.westsystem.com/instruction/epoxy-basics/bonding-fasteners-and-hardware/
Thank you for the idea!
I come for the solid cat-related content, but often stay for wood stuff. 🙂
Megan, thoughts on citrus thinner with linseed oil paint when intending full coverage in 1 coat plus touchups? (Mattias if you’re reading, with artists oil paint for translucent glazing?)
Thank you to Megan for your updates/comments including sheen variation with odorless MS, Mattias for the ingredients of the Ottosson glaze oil and techniques, and Steve Voigt for the BLO info.
There are many “citrus solvents” containing things other than citrus. Semi-locally I have Eco-House #115 Xtra Mild Citrus Thinner from Ohio. Ingredients: Isoaliphatic hydrocarbons with less than 0.001% aromatics. Food-grade orange terpenes (d-limonene, lambda-limonene)
I haven’t tried it yet, so I have no opinion.
Niether have I, so I fear no firm opinion from me either. The scenic route to finding out is of course to try it on some scrap, and see what happens.
That said, top of my list of things to try for a one-coat full coverage is to thin the paint with (Ottosson, as that is what I have and use for now) boiled linseed oil to something like 90/10 or 80/20 paint/oil. Please note: I haven’t had a go yet, so dont know what it would be like. Again, the scenic route is always open for traffic, although I agree one does not always have time for the detour.
As for mixing your own glaze oil, if that is what you are thining of, I have no idea what would make a good recipe, but yes, at least according to the label, the Ottosson glaze oil contains some sort of citrus solvent. You don’t have to use artist’s oil paint for the colour, though – regular linseed oil paint works just as well. But there is indeed a wider range of colours available in artist’s oil paints, plus a little goes a long way with a glaze oil mix, so it might be less costly to buy the paint in tubes rather than tins or cans.
Neither …
Thank you for your thoughts. I have sample boards planed and jars in a range of ratios. And a notepad. Art underpinned by science : – )
Thanks for sharing the knowledge!
Hide glue, yours or other stuff, does it work & cure if used on wood that still has a fair bit of moisture? I know gorilla does but I think that stuff is pretty nasty.
Thanks!
Poly glue requires moisture to cure. PVA and hide glue cure as its moisture evaporates. That is why poly glues are great for wettish wood.
I forget what the exact number is – maybe 12-13 percent moisture content – above which where water-based glues won’t work.
Good afternoon! I have a “Creepie” with a broken leg. I guess my ash sticks weren’t as straight as I thought. Is there way to replace the leg if it doesn’t have reversible hide glue?
You can do a lot of things. Drill it out, inject some vinegar into the joint, which can loosen yellow glue. If it hasn’t been too long, try plasticizing the glue with a heat gun….
Usually with a broken component, I drill out the tenon with an undersized bit. Then get in there with vinegar and heat and pick away at the tenon.
Hi Chris , I just finished building the Curved-Back Armchair . I added two inches to the seat width and included a double medial stretcher . The big sweeping backrest and chair geometry make this such a comfortable chair . My favorite stick back chair ! Thanks for sharing this design ..
I’m building two of those today. They are fun to build. Thanks for the comment!
There’s no such thing as awomanuensis?
Perspiring minds want to know!
Base root is manu = hand
Just picked up Ingenious Mechanicks, loving it. Unrelated to work holding, why does the colophon on some of your books have an “E” between the dividers, and others don’t?
Depends on its size at which its being used. Too small, and the E doesn’t reproduce well.
The designer forgets or remembers to put it in.
Another question on designing stick side chairs, please. Is there an advantage to an arc in the spindle locations on the seat versus straight across? Is there advantage to having the posts forward of the spindles on the seat. Is there sufficient benefit from placing an additional spindle “aft” inserted into a tongue on the back edge of the seat to justify the complexity. Or is there simply enough strength in the glued/wedged tenons to keep the back from loosening with time and wear? Yes, by the way, I’m an engineer, fully versed in “failure mode and effects analysis “.
Wood is flexible and has some give. And that is as important as the placement of sticks and the quality of the joints.
I arrange my sticks in an arc on the seat to mimic the back and start the curvature that continues up to the shoulders.
Putting the posts forward of the spindles? No clue. Too many factors to take into account. Such as what supports the sitter’s back? The sticks? The post? The comb? That’s where I get my answer.
I’ve never used the back-support sticks. On paper they make the back a triangle, which is stronger. Is it necessary? Depends on your posts and spindles.
We have all seen a lot of chairs and we know what works with rake, splay and sticks. If you design something and you won’t sit in it, that should tell you something. I’m not interested in working at the margins of material failure, so a lot of these questions are outside my area of expertise.
I have an Alaskan sawmill and a field full of trees. That just blew down. Since I’m not cutting for any particular purpose. Can anybody recommend a good size for generic slabs be used later
8/4 and 5/4 with keeping the cut as straight through the grain as possible. That’s what I would do.
Is there a faster way to tell if liquid hide glue is still good than gluing up test boards and letting them dry overnight?
Thanks!
Nothing as definitive. You can spread out a thin coat on a piece of paper and see if it sets up hard (should take about four hours). Some people put a little wet glue between their fingers and pinch and pinch and pinch and see if it gets really really sticky and hairy as the glue gels.
The three-block test is the only one I use.
I bought and half read “Joiner and Cabinetmaker”. The book said that the preferred wood for chisel handles in England was beech, your commentary was that the wooden mallets were normally made of a softer wood so not to damage the chisel handle. What woods would you use to make handles and mallets in North America? Specifically the East Coast, say from Kentucky eastwards.
American beech, hornbeam, maple, hickory, black locust. All of those woods are good for striking tools and tools getting struck.
When you do a table top do you worry about grain direction first or the way it looks?
I try to make both work. If I can’t, the aesthetics are more important than grain direction in this case.
Good day. I am gearing and wooding up to attempt my first stick chair build. Where I get nervous is adjusting the sizing as I am a bit bigger than your average bear. Primarily, I am needing to widen and probably deepen the seat as the point-to-point width on my hips is 21″ (wider than the 20″) and am 6’8″, so need a little extra depth to the seat, but I want try to keep the look of your design as that was what made me want to make one (or more). Does a 23-24″ wide and 18″ deep seat sound OK aesthetically? Still trying to source seat, sticks, and comb wood in Central Texas.
I suspect my undercarriage will need buffing as well to stay in proportion and not a skinny tall person.
Hi Bill,
That sounds like a good starting place. Bump up the legs and stretcher sizes by 1/8″ if you can. Mostly it’s about making room for your body. The chair should be strong enough if the wood is straight.
Hey what’s your favorite stick chair for a long reading session?
The comb-back on the cover of “The Stick Chair Book” is hard to beat. Lots of support for your shoulders and arms. Lots of room to shift around to get comfortable.
Hi,
My wife and I live in a 1924 bungalow that has had its original exterior doors replaced with ugly contractor grade steel doors. Are there any resources you recommend for building wooden doors in vintage styles? Any wood species to consider?
Widows and door making book,
I have not built one but it is a great resource.
https://lostartpress.com/collections/books/products/doormaking-and-window-making
Our book on windows and doors is the best source on traditional sash and door work. As far as species go, a bungalow would ideally have white oak doors and windows. White oak, while expensive, is an excellent exterior wood. And its aesthetic is right in line with the A&C movement.
If you were making a stick chair seat from riven wood, would you saddle it (or at least rough out the saddle) while the wood’s still green? (The wood in this case is hard maple, and I’m used to carving bowls while the wood’s still wet.)
Or is that inviting irreparable twisting and/or checking as it dries?
You can scoop out a fair amount when it’s wet and then finish it when it’s dry. You might lose a seat or two to checking and unacceptable warps. But I do know that people do this!
Thanks!