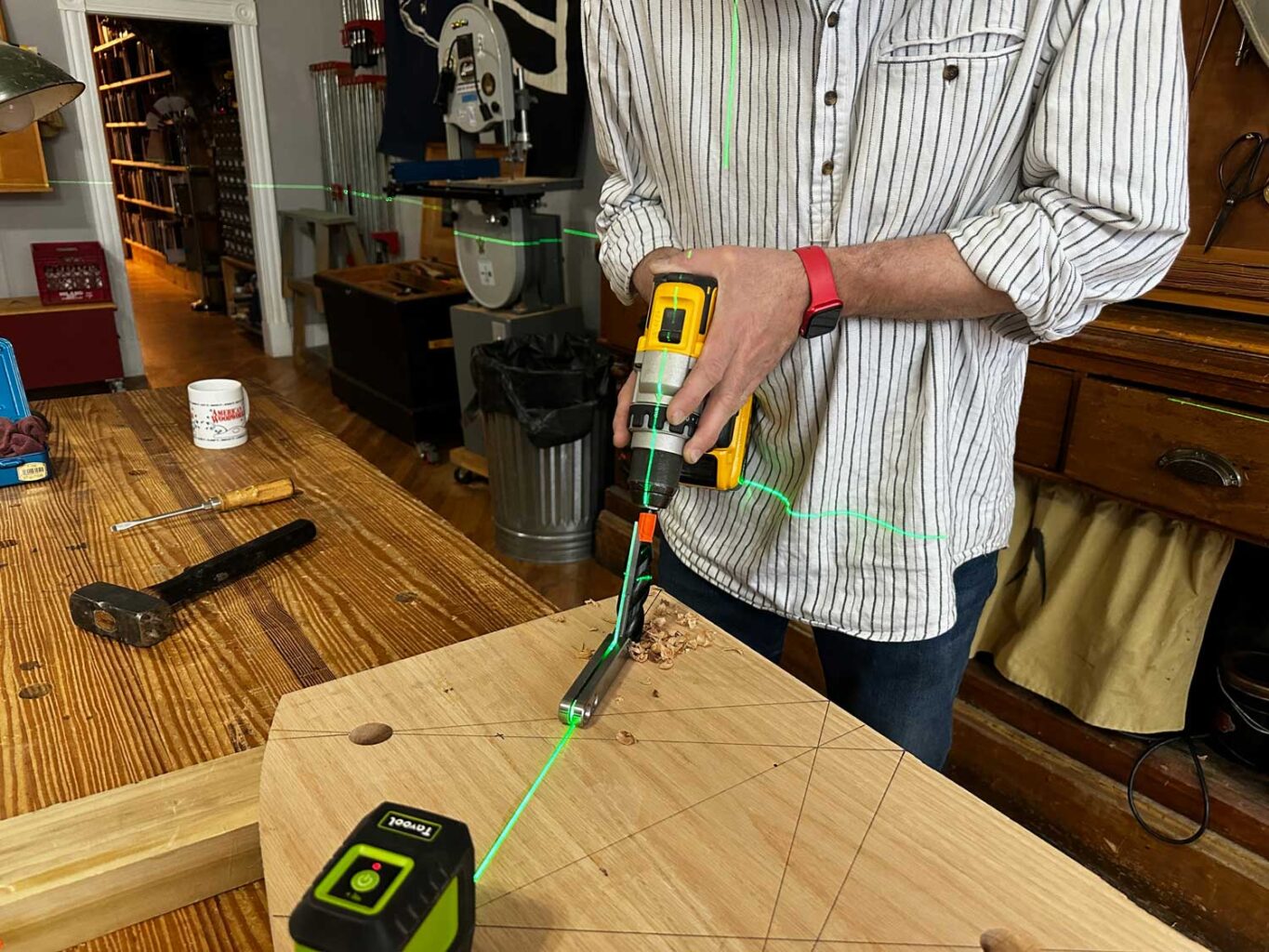
Every single vernacular stick chair I have studied uses cylindrical tenons. None have tapered tenons and mortises.
Yet, I teach many first-timers to use the tapered joint. What gives?
The tapered joint requires some special tooling, but you get a few chances to dial in the final angle. So it’s forgiving for beginners. A cylindrical mortise uses only a drill bit. But you get only one chance to get it right.
Personally, I prefer the cylindrical joint because it looks right to me. But both survive just fine in antique examples. You can make up all sorts of reasons that one is superior to the other, but the furniture record is clear: Both work.
Yesterday I legged up two Irish chairs I’m working on, and Kale Vogt (our new assistant editor), shot this short video that explains the steps I take to get my mortises just right.
This method is a little different than what I show in “The Stick Chair Book” (a free pdf download). I have added my cheap construction laser to the process. The laser makes the process so easy, that I’m considering using it in future classes.
— Christopher Schwarz
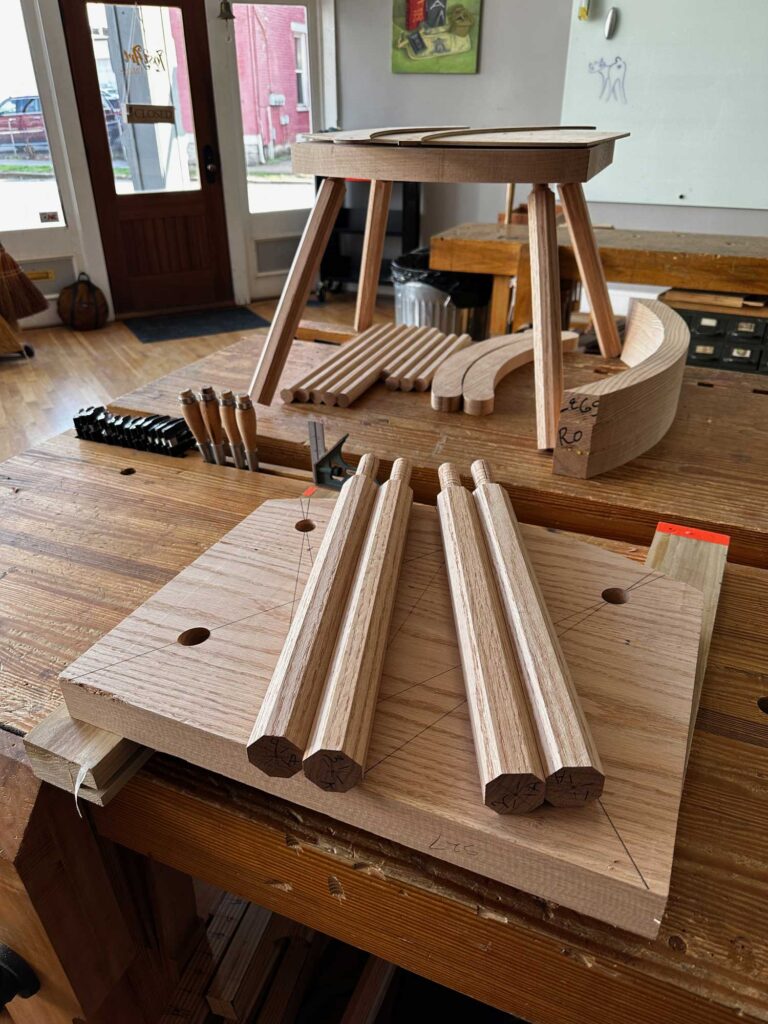
Thank you.
I plan to ask this again on Saturday, but how did those old school chairmakers make round tenons? Chairmakers probably had dedicated rounding planes but weren’t like, farmers making chairs just to sit on?
The first pair of stick chairs I made were following along with Chris’ course on the Wood Whisperer Guild (American Welsh Stick Chair). Asked him a similar question and he said to drill a test hole in a piece of scrap from the seat as a tester, and cut/shape the tenons with a chisel, rasp, and block plane, checking as you go. Worked great and the wedges helped to cure any slight irregularities.
yeah that’s exactly the trick I’ve been doing! It’s just enough work that I feel like I must be missing something. Maybe I need to stop using the chisel when I get closer (today I use the chisel almost exclusively.)
I’ve had good results on 1” round mortises for legs using Peter Galbert’s drilling jig recently.
https://youtu.be/KIEmkZgx1xk?si=OiPoykJhbnPRXiS2
https://www.petergalbert.com/pdf
It takes a lot of the randomness out of the process, which may not be as… exciting, but it also isn’t as… pants encrappening. Have you tried this technique? Any thoughts?
I’ve seen it in action and it works great.
My problem is I don’t get on with jigs much. We use some jigs that are just one piece of wood. But when they get to any level of complexity, I lose interest. I don’t know why I like a laser – maybe because I use it for so many other things around the house and shop. I’m just weird.
Jig making is a different thing I reckon, kind of like pattern making. A jig for a one off is usually a solution looking for a problem but a well thought out and elegant jig for production work can be a thing of beauty and an expression of considerable skill.
The Galbert jig doesn’t take much effort or skill to make (especially for someone who is building, you know, chairs). It’s adjustable to something like 35° backwards or forwards without any effort, is easily repositioned to any specific direction as required, and can be used with any diameter drill bit (up to maybe 1½”). So while it’s really designed for just one thing—accurately drilling holes at a specific angle, pointed in a specific direction—it’s hardly a single use tool. Four accurate holes at two different angles in four different directions in just a few minutes on every chair seat you make? (Plus staked tables and stools?) Yes please!
Thanks for this! I’m making a low staked bench as practice for the chair course in Port Townsend next month. Just getting ready to start drilling.
I don’t know why I never used a laser for that once daunting task. So simple!
Finding Mr Langsner in the comment section is like catching a glimpse of the loch neck monster. Will you be teaching any classes ever again??
I imagine the cylindrical tenons are less likely to split the seat than the tapered tenons when you pound them in, too. I’ve had a bit of trouble lately with one whack too many.
Kale’s editing is a huge step up. Lots of tiny little changes that add up big.
Nice!😊
I’m pretty sure you have a seat reaming video, but I can’t find it. Can you post a link?
https://youtu.be/bpLBoicBY4I
Excellent. Thanks. That one always bears reviewing. It’s really very little reaming. The inclination is to overdo it.
Exactly.
Hi Chris,
Have you ever used a second laser for the resultant (kinda similar to how you drill the sticks) aligned with the bevel? Wondering if it would be overkill to have two lasers AND a bevel for the 1″ tenons or if that would just be kinda lame 🙂
You can use a second laser for the resultant. I have tried it and it (of course) works. It’s just a mater of how much PITA setup you are willing to do.
The timing of this video is of mind-melting perfection! After too many practice holes to count, I finally arrived at the laser helper. So glad to see you also use the 1″ auger bit. I was struggling to get a clean hole with the 1″ Star-M, F-style. Thank you!
*mind-melding.
Funny I set the laser up for the angle with the big protractor didn’t think of switching it next time I will try this way
This is such a “duh” moment. It’s ingenious and so helpful, but it seems so obvious. I guess all the best techniques work that way. It just takes someone to think of it. I’m glad you continue to explore a better way to do things. I’ll never not do this in the future.
I was just reading the Anarchist’s Design Book, and I’m thinking the drill press technique you use in it is more repeatable with less chance of errors. So why have you switched from that method?
I try to offer as many alternatives as possible in order to lower the entry bar for people. Some people don’t have drill presses. I love the flexibility of a cordless drill. I am happy to use it all
Whats next, sharks with lasers on their heads? Well, guess I need to get a new laser, my last one died after a few years, i only ever used it for hanging pictures and shelves etc, but this looks like a great use!
So far, I’ve only used cylindrical tenons on a couple of benches I’ve built. I made them with a saw, chisel, mallet, and a hardwood test block with the right hole in it. Is there a better way?
You can use a 1″ plug cutter (I have one from CMT). I clean up the ends of my octagonal legs so it just fits, mark a shoulder line with a cutting gauge, and then cut the tenon with a drill. Its a lot faster but not necessarily better? Its easier to make the tenon off-center but practice and/or lasers also help with that issue.
I suppose a, slower, alternative would be to use a brace with the owl auger? If time is not a factor, would it be easier or more difficult to control? Just curious….
That’s the way I I did it for years. A brace is not easier to control. It’s just slower. Both operations require skill and a little strength.
I remember learning much from Christian Becksvoort’s revelation of his 3×5 card system for documenting time spent, notes, etc. for the projects he completed during his time in business.
Wondering if you’d consider a similar revelation of your system of documentation in a future blog as it pertains to chair making? Formatting of notes of
iterations/developments of previous designs and of experiments etc.
I’m confident I will develop my ideas of what is important and what isn’t but am still curious about your process. Especially as I’ve a couple copies of your newly released ledger and I’d rather not fill it with useless drivel while I work my way into a system of my own!
Oops. Meant to post this on the open wire…
I record my chairs in an old daybook (used for accounting). It was the inspiration for our LAP Workbook. I refer to mine all the time for dimensions and angles used on older chairs.
https://lostartpress.com/products/lost-art-press-workbook
Hi Chris,
What do you think the spread is in the furniture record of 1″ tenons versus 1 1/4 ” tenons? Is there a time if ever you would choose to go 1 1/4? Or is it too beefy? I also have a thought about cylindrical tenons. I love them. Not a fan so far of the conicals. It is said that downward pressure makes the cylindrical tenons tighter when they are done well. Most definitely this is true. Is this not true of the cylindricals as well? The angle is not as pronounced. Especially with the tenons made by hand with a plane or the ones made on the inexpensive plug cutter then cleaned I end up with a taper. That downward pressure is going to push the leg ever into the mortise just the same right? Also I love driving that wider wedge into the top of the leg. It feels solid. They are both solid. I also dig the doevtailing effect when that wedge is driven. If I am all wet here that’s ok. I can’t keep my brain from falling down these rabbit holes and wondered what you thought.
I haven’t seen a lot of 1-1/4″ tenons in folk chairs. Probably because the 1″ bit is far more common and easier to drive with a brace.
I say make yourself happy on the sizing of the tenon.
On the self-tightening aspect of cylindrical joints, it depends. I use a hard shoulder on my legs and wedge the stuffing out on the other side to trap the tenon between the wedge and the shoulder. But that’s not self-tightening. Also, a ramped shoulder can also act as a wedge and split the seat in time (I’ve seen this happen in the real world). In theory conical tenons can do this, too.
There are a lot of factors and things to think about…..