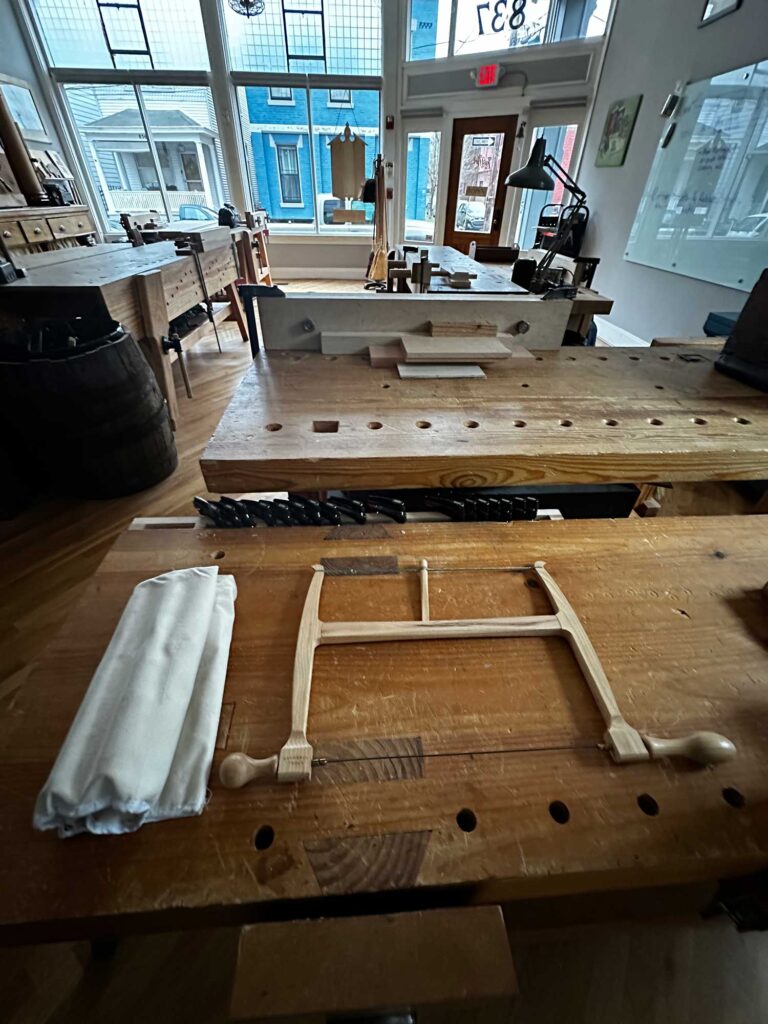
Megan is teaching a class on building a Shaker silverware tray here at the storefront this weekend, so y’all are stuck with me and Wally the cat for Open Wire.
We are happy to answer your woodworking questions here on Open Wire. Simply type your question into the comment box below. Post it. We will read it and answer as best we can. Know that Wally has only one answer to every query: “Treats, in my mouth.”
Sometimes there is a lag between the asking of the question and the typing of the answer. But I will attempt to answer all questions. Sometimes we answer them after comments have been closed – it just depends on our schedule for the day.
As always, comments will close about 5 p.m.
— Christopher Schwarz
What are your opinions on spoon bits? These seem to be popular for chair makers, but I only see one seller offering them new. Thanks!
I’ve used them a few times, including the old Emhoff bits. They are ideal for chairmakers who use a brace. I use a cordless drill.
They have a bit of a learning curve, especially starting them. But they are highly effective because they allow you to adjust your drilling angle easily as you start the cut.
Just my opinion, but the only ones currently offered that have the proper profile are the ones from Tools For Working Wood. Not cheap, but they are quality. Use a rod type ceramic or diamond rod used for knives to sharpen.
Wally, what is the meaning of life?
Chris, when the crest of a stick hair is pinned you do it at the front, which leaves a row of dots. Is there some reason they are at the front or can they be on the back?
This is just tradition. The pins are in the front and typically do not go through. You are welcome to pin the comb in place anywhere you like and anywhere you have enough wood to hold the pin fast.
I have been asked to build a shadow box coffee table with a hinged lid and lock.
What are the best choices for hinges and the locking mechanism?
Almost any hinges will do, from simple butts to a piano hinge. Our stock hinges are from Horton Brasses. They are consistent (so they are easy to install). Well-made (not just cheap stampings).
https://www.horton-brasses.com/brassnickel.asp
On locks, maybe someone else here can weigh in. I’ve not found half- or full-mortise locks that I love (aside from blacksmith-made ones). The ones I’ve bought from Horton in the past (they were English imports) tended to break.
Why does a flat/straight board (edge or face) tend to develop a crown if you keep hand planing too long?
If by “crown” you mean a bowing across the width, that is likely caused by the wood losing moisture and changing shape. The only way a handplane can cause that shape is if the iron is cambered and you are applying too much of the crowned iron to the long edges (where it is easiest to plane).
If by crown you mean a bowing along its length, that is caused by (sorry) bad form. A bowed board is what the plane wants to produce, because it’s iron is proud of the sole. You need to counteracts this tendency by applying downward force during the middle part of the stroke (like scooping out ice cream).
Hope this makes sense.
Dear Chris: My wife and I are hoping to replace all the flooring in our house with rift sawn white oak in the not-too-distant future. I really do not like polyurethane as a finish for anything, even flooring, as when it fails, which it will, it will need to be stripped and redone. Trying to stay away from VOC’s and the like, is there an oil (perhaps Osmo?) which is easily repairable, non toxic, and merely imparts a matte finish on what I hope will be beautiful white oak planks? Thank you.
If I were installing a new floor these days, I would likely choose Osmo, soap or paint. (I love a painted floor, especially as it wears.) Of those three choices, Osmo is probably the one most normal people would apply.
But I don’t keep up with the world of floor finishes. So my answer is kind of lame.
On this note, I applied one layer of poly (Bona Traffic) and didn’t sand afterward per your procedure for putting in your HQ floor. I’m still finding it slippery when planing, especially when there’s a bit of sawdust on the floor. Have you found it got better over time or have you had any workarounds for better traction?
Not Chris…but I’d consider getting a sample of https://www.realmilkpaint.com/shop/oils/half-and-half/ – if my old pine floors had been in better shape, I’d have used it. (I needed a film finish to encapsulate some potential splintery areas.)
I used tung oil on my 100 year old oak floor from Real Milk paint and am very happy with it.
Based on your goals for the floor, Osmo is worth a try. Make a sample board and see how you like it.
I have applied Osmo to old oak and pine floors. I was happy with the process and outcome. The semi gloss finish blends well with nearby worn film finishes.
As for other oil finishes, make sure you wipe or buff the Osmo off before it gets sticky — and don’t expect to build a film in a few coats.
Hello Christopher- I think last week someone asked if you’d tried the Truper brand of spade bits, but I didn’t see an answer (unless it came late). Have you tried them? Images show they are built with knicking spurs at the outer diameter, are made from carbon steel, and have a moderate price. Amazon sells them, among other places (maybe Lowe’s stores?). It seems Truper is based in Mexico and imports/exports globally, so I don’t know where they are made. Thanks.
At Amazon-
TRUPER J-BPT-6 6-Pc Spade Drill Bit Set https://a.co/d/2P9TdWl
I haven’t tried that brand, I’m afraid. They look interesting, and I’ll have to find a source where I can get just a 5/8″ bit.
There are LOTS of spades out there that I haven’t tried. Most that I encounter – ever with the rim cutters – are too thin. They heat up and lose their temper in short order. I’ll keep searching.
Hi Everyone and Thank You LAP!,
I noticed Fine Tool Germany has “traditional” looking spade bits with grinding marks and wings but I don’t know where they are made and if the rim cutters hold up. They also have an extender at the bottom page with allen screws.
Thank you. As for forstner bits, I’m guessing they may not start drilling at the more acute angles you need, but I’ve had great luck with the (expensive) carbide forstner bits Rockler sells.
https://www.rockler.com/long-shank-carbide-forstner-bits-standard-sizes
Harbor Freight sells sets of something similar to the Rocklers, but I have no experience with them.
Would you have any reservations about using poplar for the 4 piece arms of a painted stick chair?
I used some recently and a small crack developed through one of the arms at one of the long stick holes. I pinned it with an oak dowel, and it is fully supported by the shoe so I think it will hold up to use okay.
Wondering if this is something I should expect with poplar, or if I should tone down my inner Thundar the Barbarian while beating the arm into place?
Poplar is a fine choice for the arm. A cracked arm is usually the result of:
Compress your stick tenons that go into the seat. The hot glue will expand them. You can then install the arm with light taps and eliminate cracks.
Second tip: Do a “pre-flight” check with the arm, sticks and seat. Put the short sticks lightly into their mortises. Check the long sticks’ positions and see if they will enter the mortises in the seat. Ream the holes for sticks that need mobility.
Hi Chris,
I am building the curved back armchair from the stick chair book. I changed the tenon size on the arms to 3/4 inch based on having a 3/4 inch tenon cutter. This seems ok except for the back stick that goes through the arm I planned to switch bits and make it 1 inch and of course I didn’t and it is also drilled at 3/4 diameter.
My question is how you would approach this problem that I created?
Taper the back stick to 3/4 so it can go through the existing hole.
Use a reamer and try to widen the hole so I dont have to taper quite so much
Make new arms and start over?
A solution I haven’t thought of.
Thanks for any advice!
Use a reamer. I usually ream the underside of the arm anyway to get a snug fit between the arm and back stick. FYI, I have switched to 3/4″ tenons for that chair for all the sticks — so you are just ahead of the curve.
How long does it take you to make a stick chair from rough lumber? While I know it’s not a race, I’m always curious how long it takes other people to do things as a way to compare my efficiency.
About 16 hours from rough lumber to finished chair. However, that time can be greatly reduced when I use sticks, legs and stretchers I have stockpiled over the years.
Do you have any finish recommendations for furniture such as a bench that will be exposed to the elements and spend a lot of time outside? Thank you!
I would use paint or a transparent deck stain. Don’t bother with any spar varnish or clear film finishes. The UV destroys them in short order.
I have a rocker, factory made, that is at least 50 years old and the maple seat is splitting along a glue line. I saw a tip somewhere to use unwaxed dental floss to work PVA glue in before clamping. What do you think the best approach would be? The balance of the joints are solid at the moment. It was my grandfather’s so I would like to save it from the burn pile.
We use dental floss all the time to deliver glue into tight spaces. A second strategy is to put a bead of glue on the top of the seat and use a vacuum from below to suck glue into the joint.
If the chair is older than 1950, they likely used animal glue to assemble the seat. And so it might be a good idea to use liquid hide glue to make the repair. Animal glue sticks readily to animal glue.
Excellent, thanks for the vacuum tip and the glue pointer!
“Disobey me,” he says. Now, I’m stuck. If I obey, I am disobeying. If I disobey, I am obeying.
So let’s talk about another rabbit hole, sharpening, specifically forming a burr. As I understand the mechanics, as the metal right at the edge is abraded and becomes thin, it deforms and bends up in a thin layer. Multiple strokes build successive layers of metal which is the burr. We remove that burr with the back of the blade flat on stone. My question is about metal fatigue right at the edge. The metal right at the edge has been bent back and forth multiple times, presumably leaving it weaker. We remove some of the fatigued metal when we remove the burr but some is left behind right on the cutting edge. With this thought in mind, I use the lightest pressure possible to form the secondary bevel and flip the blade multiple times to wipe off the thinnest burr possible. This is contrary to some advice to remove the bevel once. My question is whether my technique causes more fatigue or less?
You know this is the sort of question that makes me want to snip out my uvula with rusty pruning shears….
How does your edge hold up? How does the wood look? That’s your answer.
I have done it both ways during the last 25 years (and many other ways, too). I don’t really see any difference and I don’t create a toothy edge either way.
I’ve seen that ya’ll use tite-mark for marking gauges and I have the veritas mortise gauge w/ the wheel cutters. My complaint about the veritas is the wheel doesn’t rotate as I drag the gauge which causes it to come out of the cut and by the end of the mortise I have 3 deviant lines instead of 1 straight one. Does the tite-mark wheel cutter rotate as the gauge moves or is it fixed?
I use the Veritas Dual Marking Gauge with wheel cutters. The wheels aren’t supposed to turn. I have my wheels locked as tight as possible on the stems and check them for tightness often.
Making a Moravian stool this weekend to try out a brace mounted reamer I found in an antique mall a few weeks ago. Also to try out making a seat with battens.
Here’s my question, I know you’ve mentioned battens in the stick chair book, but I don’t really remember seeing then often in your work. When do you consider them and is saddling a seat a concern when using battens?
Most Alpine/batten furniture has no saddling. The seat board is very thin. I’m sure there are exceptions, but generally the seats and stools are flat.
That’s a relief to hear, the handful of tools I’ve seen for saddling are all real expensive, and I’d like to be a bit more sure in my chairmaking abilities before investing in a travisher for example.
I’ve seen a lot of modern benches with some kind of ornament on the leg vise… a date, initials, emblems, etc. Was that common on historical benches you’ve seen?
Nope. Sometimes the hub of the screw is somewhat decorated. But otherwise, most benches are pretty plain.
Any experience/thoughts on using osmo poly x over milk paint for Windsor Chairs?
Almost anything can be used over milk paint, from oil to varnish to wax to poly. It is a porous finish that accepts oils and films readily.
I used osmo over milk paint for a chair and it worked great.
Any lumber yards or other suppliers you can recommend in the central to northern KY area (I live in Lexington) that carry clear white pine? I’m looking to build a tool chest and some boarded furniture but am having a little trouble sourcing good pine at a decent price.
None that I know of. Sorry. Shiels in Cincinnati carries it, but you have to be a commercial shop. And it has knots.
Clear pine is something best sourced from the northeast or northern Michigan and the upper Midwest. You can even find it at the home centers there.
Sugar pine you can source from the West coast.
I just finished my 1st roorkhee chair and had 3 questions for you. First have you experimented with making a taller roorkhee. Just wondering if it would effect the comfort dynamic. Second what about using a heavier grade of leather and finally can I use the scrap of the 3 to 4 oz leather to make the folding the article in Pw suggest 8or 9 oz I think. Thanks
That should be the folding camping stool.
I haven’t made a taller Roorkhee. Sorry. Adding a couple inches in height won’t make much difference. But making a barstool is probably a bad idea.
Heavy leather (up to full grain) works fine. But you need to wet the material to bend it around the sticks and backrest pieces. And I think that 3-4 ounce leather is too thin for a stool. I use that stuff for straps. Scraps I cut into shoelaces or leather loops to hang tools.
Good Morning Megan and Chris! I was wondering if you or your readers had any advice for sore hands. More and more this limits the time I’m able to work in my shop. I’d rather not take drugs, but herbal remedies may be OK. It has recently dawned on me (yesterday) that I also need to stop working in figured ash and make more things out of white pine. Thanks!
A lot of people with sore hands dunk them in ice water. Emmett Van Driesche talks about this a lot.
https://www.instagram.com/emmet_van_driesche/
I’ve done it a few times after long chiseling sessions and I can report that it is helpful.
Keeping a couple bags of frozen peas helps too. For sore feet as well. Also a frozen 1 liter water bottle is awesome for sore feet (like the Nalgene bottles hikers use)
I have thumb joints that don’t work as well as they used to. The things I do that help are: vary the way I hold the tool (pressure and grip), work left handed (even for short intervals), use the clutch when drilling 1-1/4” spade bits, pull the plane instead of pushing it, continually think about work holding and an easier way to work and doing smaller projects.
If the problem is arthritis warm water may be what you need. I soak my hands in hot water in the mornings to get them moving.
I remember you mentioning somewhere (the Woodwright’s Shop?) that dovetails date back to the ancient Egyptians. I’m curious if you know any resources on ancient Egyptian woodworking–any books, any particularly informative information out there? I’m particularly curious about what tools they had, and when, and what sorts of wood they had access to. I know some of the most important early Pharoahs made huge deals of sending trade delegations to Lebanon to get cedar–but the reason that was such a big deal was there wasn’t much by way of native trees, and the cedar was mostly used for boatbuilding, so I’m curious how they’d even have the material to develop dovetails.
Anything you can point me to?
Thanks
Geoffrey Killen’s books are great. He has made reproduction tools and built furniture with them along with his students. Good stuff.
https://egyptiancoffins.org/team/geoff-killen/
Wow, thanks! Perfect!
I was recently able to acquire a bandsaw mill at a great price. Since then I have put a lot of pine through it for construction projects and a few hardwood logs. I am a hobbyist woodworker and would like to mill hardwood on my property for my own projects. I have a small bit of experience as a woodworker and very new to being a sawyer. I would like to learn how to mill these logs into lumber for furniture making. I want to do this in the most efficient way to prevent wasting as muvh of the tree as I can. Would you happen to know of any resources out there out there that could help me get started? Thank you in advance.
Chris
Nope. I’ve only helped people mill wood on a Wood Mizer. They offer some beginner information.
https://woodmizer.com/us/Resources/Magazines-Guides
I’m certain there are lots of resources out there. It’s just not my area of expertise. Sorry.
Not Chris, but you need to consider what type of boards you are after. Flat sawn or quarter sawn? Makes a big difference in how you handle them. Also consider how you will store them while they dry. Outdoors with a cover and stickers between the layers? (Hint, Make all your stickers the same thickness.) Extra weights for the top board, to reduce warping. How thick? If you are after 3/4″ cut them to 1″ or even 1 1/4″. Don’t expect to make finished cuts. You will need to plane them, either by machine or hand.
Port Townsend School of Woodworking has a weekend sawmilling class starting June 1st. Careful though – it is a beautiful area.
I and my partner ran a portable mill for five or so years, back in the 90s. The simplest way of doing it is to take the first slab and then rotate the log 90 degrees. Make a single cut, and rotate it again, continuing like this until the log is finished. This gives somewhat better quality lumber than just sawing it right through, without ever rotating it. Much better lumber comes from quarter sawing . Technically this creates massive amounts of waste, but a modified pattern is to quarter the log and then slice it through, like plain sawing. Problems with warping tend to arise when making these deep cuts. As you get some experience, you will learn when is a good time to launch into quarter sawing, or other modifications to get the lumber you want. It is a wonderful pastime. Enjoy!
Hey Chris
I made an anarchist bench last year and cant say enough about it. I thought I had a nice bench, being a maple topped bench with dog holes, Record bench vice and Veritas twin screw vice. Then I read your book, Realized that all the maladies of poor benches were what I was experiencing. Now that I have used this bench for a few months I realize what a vast improvement it is and how valuable.
I guess my question would be to ask if the inspiration for the anarchist bench could be found at Colonial Williamsburg?
Nope. They use Nicholson benches there. The inspiration came from Roubo at first. Then I got back to the source code in the 1500s.
You can read all about where it comes from in the book, a free download.
https://lostartpress.com/collections/all-books-1/products/the-anarchists-workbench
Hi Chris,
Thanks so much for taking the time today! Two quick questions–are your dimensions for the “short back” chair the same except for the long sticks? And what is your final length for them?
And Megan was kind enough to have a stab at my question last week, but I’m wondering about your advice–on carving the bottom of your pristolnics what’s yr best approach? I haven’t worked up the courage to do the bottom yet, though making the rest of them has been great fun!
Thanks,
Jake
The bottom edge of the comb begins 8-3/4″ above the arm.
And I carve there underside of pristolnics with straight chisels. Stabbing V-cuts. Practice on a scrap. My first attempt was lame. I got better at it on the second. Be sure to clamp the base securely to prevent it from splitting when you stab in.
Awesome. Thanks so much!
I’m milling some walnut splits into blanks for drinking table legs (they are not agreeable to split further). I have a few fine checks in the blanks in the blanks I’ve milled so far, but don’t have much length to spare. My current plan is to seal the ends with watered down wood glue and hope they don’t grow. Should I be more concerned about this?
Example check:
https://pasteboard.co/ALc20quIShsv.jpg
Splits:
https://pasteboard.co/qAAOJPt2ROvj.jpg
Good morning and happy Saturday. I got myself into a sticky situation. I used a tapered reamer for the legs of a stool and I’ve ended up with an elipsoid hole on top instead of round as I was adjusting the rake. Any recommendations to avoid the gap other than filling it in with epoxy? The piece is not going to be painted
Saw your post about the Ray Iles rounding plane. Does this replace the power tenon cutter in your workflow or is this just for shaping sticks? Thanks!
I’ve been making wooden toys/knicknacks between bigger projects with scrapwood. I’m stumped when it comes to efficiently making marble sized or smaller wooden spheres as components. It’s outside your usual scope but do you know of a trick or a resource? Surely traditional makers didn’t buy a bag of mass produced wooden spheres off amazon! Turning on a lathe doesn’t feel very efficient but maybe that’s user error.
This will sound crazy, but I’ve never made a sphere out of wood.
Anyone here?
If memory serves, FWW once showed a jig for making spheres on a belt sander. Don’t remember more than that.
Haven’t tried this but a tip I recall said to build an open-bottom box over a belt sander with a door on the top. Put in a bunch of wood blanks (cubes with cut off corners) and let her run. The high points on the blanks will wear down leaving a sphere. Be prepared for the amount of noise this makes. You’ll have to experiment to see how long to run the belt sander.
I assembled the undercarriage for the TWW American Welsh Stick Chair this week. All four wedges broke off in the leg tenons roughly 1/2” in. The wedges were red oak from the chair offcuts, widely spaced growth rings running from heel to tip, cut to 8º angle, kerfs cut with a backsaw and opened with a chisel before I tried to drive home, and wedges lubed with Piggy glue. I’m not worried about the legs being loose, but any suggestions on how to avoid the problem before I move on to the sticks? Clearly a case of user error – I just don’t know WHICH error I made. Many thanks as always.
Likely the grain wasn’t running straight through the wedge. When I make wedges with dead-straight grain, they will go in like a nail and break only under extreme circumstances.
You had a recent video on a piece of wood that you were given for a seat chair. Not important which wood… but during the analysis of the wood, you made a comment on how you prefer interlocked grain wood ( like Elm) for seats…. Can you explain and expound in more detail? WHich other woods are good/bad?
TIA
Frank
Species with interlocked grain grow in a spiral. And the spiral changes every year or so. This makes the species difficult to split cleanly. Sycamore, elm, mahogany, cherry and walnut are all examples of species with interlocked grain. Here’s a good and quick explanation:
https://www.woodmagazine.com/materials-guide/lumber/understanding-wood-grain
I am collecting the tools in your ATC and have made shorter, nice wooden winding sticks, but will purchase aluminum angle for a couple large 36″ winding stick. Recommended angle size? I have found 3/4″ X 3/4″ X 1/16″ and 1″ X 1″ X 1/16″ at the local DIY. Thank You.
I found the Titemark’s available from Classic Hand Tools UK (as well as my Asley Iles chisels – as I tried both LN and Ashley Iles and found the Ashley lIes a better fit for my hands).
After using the King stones for a few years I’ve upgraded to Shapton’s 1K, 5K and 8K and find they give me better feedback, less mess and give joy.
I found a pre WWI no. 7 Stanley (not being able to get an LN No.7 from LN shipped to Canada from LN for under $150) in very good condition other than a .007″ hollow about an inch wide in from of the mouth which I couldn’t get out. The plane was used a LOT on edge jointing. I walked into the only machine shop in Gander and they machined the sole perfectly flat for $100 plus giving me two new Simmonds files that they used to sell probably worth $50! Shaves like a dream with the Stanley blade slight curve, rounded corners and honed on the Shapton 8K.
I don’t think the height of the winding sticks matters much. Paint one of them black or another color so you can see it more easily.
Cut out a whole gaggle of dados for some bookcases from ADB. One of the 12 ended up about 1/8″ out of place from where it was supposed to be. I’m sure I got lost in the sauce and cut on the wrong side of a line somewhere.
Any suggestions on how to fix this? Or should I just get a new side piece and start fresh?
Glue in a patch piece to fill the errant dado. Recut the dado so the 1/8″ error/patch is on the underside of the shelf. That’s what I would do. Then put books in it to hide the mistake.
Hey Chris. I am building the gate leg table from the article from pop wood you did. I purchased the square leaf hinges from Hortons instead of the uneven strap hinges you used. My question is if you line up the leafs and top to square ends of the hinges the gap between the leaf and the top seems to be around 1/4 inch or so. Is that normal or should I try to cheat it in some? Or is that done for uneven floors and lifting the leaf up? Thanks
Definitely cheat the bits together. Shoot for almost no gap between the top and the leaf when the top is raised. Hope this makes sense.
Chair question: please feel free to jump in if you have encountered this before. I am making the Staked Chair from the ADB. Last night I was dry fitting the spindles into the seat. One spindle was quite tight as I pushed it into the seat’s mortise. I can’t get it out. I have tried like a madman. No luck. I don’t want to cut off the spindle and re-drill the mortise if it can be helped. Does anyone have any clever suggestions?
I don’t know much so I ask; IF the mortise is a through hole you could drill a smaller hole in the spindle’s end, it may need to be 1/8″ smaller than the spindle AND deeper than the length of the spindle in the mortise to reduce the pressure enough & .the spindle is prolly ruined unless it can be shortened.
I have taken a dowel about the size of the mortise and driven it out from above. Generally works with little or no damage.
With your off hand, grab the stick and hold the seat slightly off the bench. With your dominant hand, hit the seat with the biggest mallet you own (best to put a block of scrap between the seat and mallet blow). A few wacks like this usually release any tenon I’ve encountered.
Dear Wally,
What would it take to get you to leak an early copy of The American Peasant or the eagerly anticipated Dutch Toolchest Manifesto?
Large human is posting designed chapters of “The American Peasant” on his substack called “The American Peasant.” Six are there now. More to come soon.
Signed,
Treat freak Wally the Water Waster
Hi Chris,
Have you read Peter Galbert’s new article about using boards as an alternative to splitting logs in which he says reading the edge grain of wide boards doesn’t work for determining fiber direction? Fine Woodworking No.309.
Peter makes the point that he has split hundreds of logs and all of them had some twist because the tree grew with a twist. That’s OK when using split wood for sticks because the split follows the grain. But after Peter switched to using dried boards, he often had problems with sticks breaking. His illustrations on pages 38 and 39 are great but I don’t think the text completely describes their meaning. Here is my attempt at clarifying the text so that it matches the illustrations.
Temperate climate tree species don’t grow during the winter so their trunks contain concentric tubes of wood composed of lengthwise fibers and a matrix. The fibers within each tube do not grow vertically but gently spiral from the base of the tree to its top to a greater or lesser degree. The spiraling is always in the same direction. For these tree species the angle of the spiral is consistent and small but the effect on the wood fibers increases with the addition of each outer tube as the diameter of the tree increases. Think of being on a merry-go-round and the difference in speed between the center and the outside.
The cumulative impact of all this fiber spiraling is that the tree, and splits from it, appears twisted.
If you use boards, this twist impacts your work depending on how long the board is, how wide it is, what part of the trunk was captured within the board, and all of this changes from the pith to the sapwood (merry-go-round effect). The function and size of the part you make can amplify or nullify the effect of the twist. Short sticks from wood just outside of the pith area won’t care much. Long sticks from wood just below the sapwood will be significantly affected.
For sticks, Peter’s technique for revealing the direction of the fibers is to start splitting the board in the middle at one end and run the split to the other end. Then he uses the split edge as the reference edge, instead of the outside edge of the board, to determine fiber direction on both the split edge and the face adjacent to the edge. The fiber direction on the split edge isn’t perfect but it is a lot better indicator of fiber direction than outside edge of the wide board. Recall that Peter uses boards that are significantly thicker than needed for the part. That thickness allows him to follow the edge fiber direction in laying out the part and cutting it on a bandsaw (rightmost illustration on the top of page 39). After you cut out the part, you use that edge as the best indicator of fiber direction, cut the next part, and use that fresh edge, and so on.
For backrests, Peter uses the same techniques for aesthetics to have good-looking grain. My guess is that the center of wide boards with no cathedrals would be the location to shoot for.
Yes. And in the Stick Chair Book, wacking off a split with the froe is exactly what I recommend and show. You also can read the grain and find spiral growth by looking at the rays in ring-porous species (look to the edges of the boards for the silvery lines). I don’t run into too many twisted grain boards (except the obviously interlocked species where twising grain is standard).
I made a three-legged ‘perch stool’ – loosely following Peter Galbert’s design but adopting the Anarchists Design Book model of construction. Wood is very dense, somewhat oily African hardwood (rosewood, likely Mukula … , it’s sold and used as construction lumber here in Zambia, unfortunately). Glued up using PVA (it’s what’s available locally).
18 months on, two of the three main staked joints (legs into saddle) have failed. Failure is entirely and perfectly along the glue line and wood is completely intact. The joints were wedged (also using rosewood) but that doesn’t seem to have helped any too much. Thanks to tapered tenons, the stool is still very sturdy (as long as there is a body on it :-)). I’m sitting (OK … perched) on it as I type.
My gut instinct says ‘wait until the last joint fails, then disassemble the stool, clean the joints and go again. But, once badly bitten, what better glue choice might I make?
Oily woods are very hard to glue. Poly glue is what most people use for oily woods. Epoxy is another choice. Some people recommend first cleaning the wood with lacquer thinner right before gluing. But I haven’t tried this trick. When faced with oily woods, we use poly glue.
Thanks. I was coming round to Poly too. A bit messy but will glue almost anything?
Fundamental glue question: Do you think it matters whether Piggly Wiggly home-made glue is made with beef or pork gelatin? I made a (rather large) batch with beef gelatin and was not satisfied with the behavior of the finished glue (it remained too flexible after setting). Other than the gelatin source, I followed the recipe and instructions very carefully. Any advice?
Both beef and pig gelatin should be equally good. It sounds to me like your bloom strength was too low. We use 250 bloom gelatin. It dries hard, but with a little flexibility to accommodate wood movement. A low bloom strength (150, for example) is great for desserts but not for joinery. It’s too wiggly.
I remember reading a few times that you say modern dining tables are too tall. Is their a set height or a formula you use to determine what they should be?
Most dining tables are 29″ to 30″. Those work well with chairs that have an 18″ seat height. If your chairs are lower, you need to lower the height of the tabletop to make the chairs work.
We have Home Depot chairs now but the hope is to build stick chairs later. How would you handle that scenario. Build it lower for future chairs?
You can always cut down the legs of a table later on.
A little harder with a trestle table
A little, but not impossible. Prop a 28″-tall trestle table on 2″-tall blocks until you are ready to switch to lower chairs. Or make the lower joint to the sled foot unglued so you can disassemble it and cut the post shorter later on and reassemble….
How does your soft wax 2.0 (and other similar finishes) compare to applying oil, letting it fully cure, then applying wax? Is there a situation where you would use one over the other or is it more of an ease of application thing, like mixing peanut butter and jelly together in the same jar?
It’s just a labor saver. To apply beeswax, you’d have to heat it with some solvent (otherwise it’s like rubbing the wood with a crayon….). So if you have to make the beeswax viscous by heating it and adding solvent, then why not add oil and do it all in one go?
Beginning woodworker attempting a first (and hopefully last) tool chest. Reading the Anarchist’s Design Book, my impression is the boarded tool chest in there is your recommendation for beginners like myself. I like the looks of the Dutch tool chest a little better (secret compartments are wonderful) and was curious if you thought that was a reasonable lifetime tool chest for a beginner to make as well or if I’d be better served by the boarded tool chest. I don’t plan to move the tool chest frequently and I have zero tool-hoarding tendencies.
Oh, and thank you so much for all of your time and willingness to share your experience. It really does help home woodworkers like me make better furniture.
Either of those chests is great for a beginner. The Dutch has a few more joinery lessons (including dovetails and dados). We have both forms in our shop here. Both have held up well to daily use. I’d pick the one that appeals to you.
Can you recommend a Welsh design side chair that would work well for a dining table set up.
The staked backstools from the Anarchist’s Design Book (a few download https://lostartpress.com/collections/all-books-1/products/the-anarchists-design-book) are both Welsh-inspired side chairs. The only real change I made was the tapers on the legs. On old chairs the legs taper up to the seat and are skinnier at the seat (like bell-bottom jeans). On my designs, the legs taper down to the floor.
So if you reversed the leg tapers and shaved the back sticks roundish you would have a very typical Welsh backstool.
I would REALLY like to see a photo of Megan’s tray.
Let me start by saying thanks for the great videos and book on sharpening. I bought them a while back and they are fantastic and have transformed my woodwork. Two or three minutes at the stones and I am back to sharp and back to working. Thanks for the super clear tutorial.
With that said, I still struggle to sharpen a cabinet scraper. After following the steps in the video I end up with a burr I can definitely feel, but I always end up just making sawdust as I scrape. I’ve done this a bunch of times now and consistently get the same result — sawdust vs. shavings. I realize this is a stab in the dark, but any tips on what I might be doing wrong?
Could be technique – finding the right angle and pressure to make the tool work. It could be you are using too much pressure when turning the hook and it has curled over.
When you sharpen it, are you removing the old burr first (either with a burnisher or stones)?
These problems can be tough to diagnose remotely, I’m afraid.
Hey all, hope the weekend is treating you well. Arizona weather here is 60 outside and sunny!
I recently purchased the parts to make a miter jack and have finally (a year later), flattened the end grain 45 side to within a hairs width of each other. While using some of my tools which had camelia oil on them from the days before storage, the oil remnants mixed with my sweaty hands and steel of the tool have left blackish marks all over the miter jack. Being that the jack is dimensionally stable, i don’t want to take sandpaper or my plane back to it and lift off the top layer; otherwise I will be doing all the layers next to it.
My question is, what can I use to remove the cruddy black marks before I finish it? Ive tried a white eraser and acetone which did squat.
As always, thank you thank you thank you!!
It depends on what the gunk is. If the gunk isn’t staining your work, I’d ignore it. If it is staining your work….
I’d probably try a variety of solvents. If it’s oil, try some mineral spirits to lift it out. It could be dirt from your hands (alcohol should cut that). Try baking soda (in a little water). Then vinegar. If all that fails try some of the two-part wood bleach.
And if that fails, consider wiping on a thin coat of shellac to seal in whatever is trying to get out.
Hi Chris,
We are moving and the new house has no garage, just a basement so I’ll have to set up shop down there.
I’m concerned about moving my AWB down the stairs, as I’m not sure they’ll support the weight and I also don’t know the logistics of physically moving something that heavy down stairs safely.
Unfortunately, when I built the bench I never imagined moving into a space without a garage, so I drawbored the tenons and used yellow glue instead of hide. So the odds of being able to disassemble the workbench, at least removing the top from the legs, seem highly unlikely.
I suspect I’m grasping at straws, but do you have any insight into making this move possible? Are there other ways to disassemble the bench that I’m not thinking of? I’m concerned that I’ll end up having to sell this bench and build a new, lighter one for the time being.
You can cut the top off with a circular saw (plus a handsaw to finish the job). Cut right under the edge of the benchtop. Then reassemble when you get it to the basement with loose tenons between the legs and the top.
Julian,
I work in freight and find myself moving many heavy and awkward items.
Is the staircase wide enough for the bench?
Can you get a wide 2”x12” the length of all the stairs?
Can you flip the bench upside down?
If so, get a friend to help you and use a rope to ease it down from above. Use the 2”x12” as a slide, it will spread the load over multiple steps.
If the whole staircase is too flimsy, I would want to shore it up even if I weren’t lowering a 350 pound bench down it.
Thanks for the insight Ray, the staircase is wide enough (barely) so that might work. What does the rope need to be secured to, would I need to build an anchor of some kind at the top of the stairs? What about safety mitigation to keep the bench from sliding down the stairs too quickly and hitting someone/something at the bottom?
Moving heavy objects down stairs is not so hard — getting them back up …
Standard stairs can carry oversize humans on one tread. Even a heavy workbench should be OK on stairs safe for humans. But use your judgement. I have not seen the stairs.
An appliance dolly or some boards used as a ramp on top of the stairs can be very helpful. As are ropes or straps to lift and hold the bench as it goes down the stairs. Get enough help so no one person needs to carry much more than 100lbs.
I’m refinishing a butcher block tabletop, and am intrigued by the idea of using a soap finish on it. But if it turns out not to be durable enough, I’ll probably want to switch to a wiping varnish and soft wax.
What’s involved in removing the soap finish? Just wash with water and sand the inevitable raised grain?
Thanks.
Hot water will remove the soap quickly and easily.
On the traditional small Shaker cabinets (with a single door, hung from the pegboard), where the top and bottom extend beyond the sides/front of the cabinet, what is the joinery that attaches the top and bottom boards? Are they simply nailed on? Or dovetailed, then an applied moulding?
I’ve only ever seen these in photos, and don’t have a good way to examine them in person any time soon, so I appreciate your help. Thanks!
Just nails. They are lightweight cabinets, and nails survive just fine.
I’m building the Gibson Chair and the cutlist says “ 3/4”x x 2-1/4” TOE”. Should that be TBE?
Which part are you talking about?
The long sticks. Other than that part the long sticks and arm posts seem the same
Assuming you are asking about the long sticks, both ends should be tenoned just like the “arm posts”. So TOE 3/4″ and TOE 1″ on the other end. See Part 6 of the video at 8:15.
Thanks for the timestamp reference! This helps.
Hi Chris, I am working on designs for a simple round stool and side table to sell at markets this year and am unsure if the joint I want to do is a solid choice for longevity. I need to feel confident it’ll last before I’d sell it. The tops are 1 7/8in thick. For joinery, if the tenons are 1 or 1 1/4in wide for stools and 1 1/2in wide for a side table, set into the mortises ~1 3/8in deep so they do not show through the top, and compressed before using hide glue, would you feel this is a strong joint that will last given frequent use? I’ve fox wedged a stool with 1in wide tenons – more time consuming to get it right but I could continue doing that if it’s the better path. Or if the tenons need more length to them for longevity, I considered adding battens but like the clean look without them for these specific pieces.
A separate question, I got my first power tool, the rikon bandsaw you recommended awhile back and it’s working out nicely. I’d like to get a small belt sander for flats and curves to use for making chairs and stools, like we used in your chair class. Is there a small size model you’d recommend? I appreciate your time.
Hi Claire!
Fox-wedging is a pain. But once you get it dialed in for mortises of a certain depth it is pretty straightforward. I probably would first paint the tenons with a thin coat of hide glue and let them dry. Then compress and assemble the joint with more hide glue. Painting the tenons with hide glue will improve the adhesion in the joint (it’s a trick from Jeff Lefkowitz).
Another option is to dry your legs in a lightbulb-powered kiln until they are bone dry. Cut the tenons, then assemble immediately. The tenons will swell up, taking water from the top. This sort of joint is almost indestructible.
For belt/oscillating spindle sanders, it’s difficult to beat the Ridgid. One machine does both operations fairly well. And they last a long time if taken care of. Eventually you’ll probably want something heavy and indestructible. Look for old Delta (or other old brands of) belt/disc sanders. The old ones can last several lifetimes.
Hope this helps!
Have you (or anyone) tried using lemonene (citrus extract) as a thinner in linseed oil paint instead of mineral spirits? If so, does it work well? I know mineral spirits can leave an inconsistent finish so just exploring alternatives.
I have not. Our experts say turpentine is the solvent preferred over mineral spirits.
I am going to try this this week. 10% by volume. If it doesn’t work, it’s just for the edge and underside of my Roman workbench, and I’ll have a ton left over to make soft wax.
Good Afternoon Chris,
Thank you for taking the time to do this again today. I had a question regarding marking out tenon shoulders to ensure a consistent shoulder-to-shoulder length. In the past I have done this by clamping the pieces together and making all the shoulders at the same time utilizing a square a knife. When I have done this in the past I have wondered about the fact that reference edges edges/faces are either not facing each other or that the square would register on a non-reference edge/face when scribing the shoulder line. I have been curious if it would be more accurate to mark out the shoulders on a single piece and then transfer it to the corresponding parts one at a time. I would be interested to know what your process for this type of work is?
Thanks,
Jacob
If I need to make a lot of identical tenoned rails, I’ll usually make a story stick with the tenon, shoulder and all the other bits marked on it with a knife. This gets rid of the issues of reference edges etc.
The Soft Wax 2.0 recipe lists 2 cups of raw linseed oil by volume. I assume that this is 16 fluid ounces using measuring cup Can you confirm?
Beeswax lists 3/4 cup. Is this a dry measure (e.g. measuring flower) or liquid measure with a measuring cup.
Thanks
FredL
flour not flower!
It’s all by volume. The beeswax is the measurement of beeswax pellets.
I’m having trouble using my scorp to cut end grain, both to level tenons and make a nice pyramidal shape. I can only get it to take really tiny bites. Do you have any pointers to do this better?
It takes a lot of wrist strength and a very sharp scorp. So maybe some wrist exercises? Also, working with the grain running downhill helps. I lock my chairs in the face vise with two legs against the front of the benchtop. And the seat resting against the benchtop (i.e. lots of support). Then I work the leg in the vise only. Scorping from what is the outside face of the leg toward the inside. Sheesh, words are difficult here.
Good day Lost Art Pressers. My question… since you have gone down the Cricut crafter path, what are your thoughts on bench top CNC machines? I am not talking about industrial beasts, but something that is attainable for the masses who have regular day jobs. Have you considered it for LAP or do you just contract out and CNC work for patterns and/or templates. There is much on the interwebular world when one starts investigating. Speaking for myself, I would enjoy the technical aspect and the challenge to learn something new. So…. thats about it from me. Cheers.
I do like the Cricut for making patterns for chair parts. I haven’t thought about CNC for us. Not because I’m not interested. But because we don’t have the space. We just bought a 36″ plotter so we can start making our our printed plans. And it’s going in our bedroom….