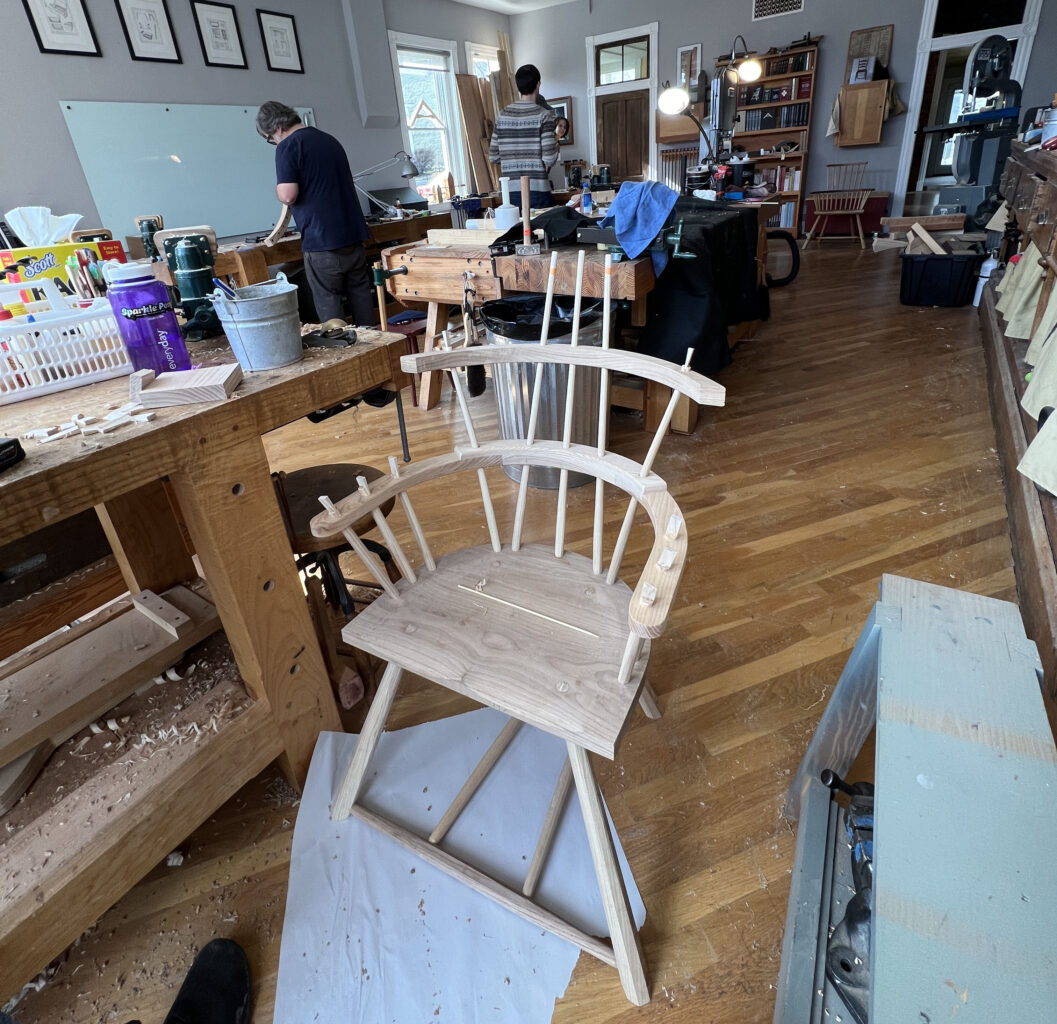
Comments are now closed.
It has been a crazy chair week here in the shop…so no different than usual (except we had eight people working in here instead of the usual two). So today, we’re happy to take it a little easy and answer questions at the computer.
You know the drill: Post your woodworking question in the comments, and we’ll do our best to answer. Comments will close at around 5 p.m. (and there may be a lag between your asking and our answering).
– Fitz
Morning. Any hint if Lie-Nielsen will have any surprises for us? How is Anthe building doing?
I don’t know of any surprises from Lie-Nielsen. We’re just happily surprised they are resuming these events.
We will have a big update on the Anthe warehouse this week (I hope). With any luck, the material lift will be operational next week and we will finally have the building fully operational.
How many mortises before you need to sharpen your tapered reamer? And diamond paddles on the flats? Do you shoot for a burr?
And thank you for being so generous with your time!
The tapered reamer needs sharpening every five chairs or so. The diamond paddles are too slow. I use a carbide tool sharpener. A couple licks on each cutting lip turns a burr. Then I remove the burr from the outside of the cone with a fine stone.
What joint did you use at the top of the table leg to the cross piece on your table in Earlywood this morning?
Also, how does the top attach to the trestle?
It’s a bridle joint. The top is attached with table buttons. You can download the article for free from PW:
https://www.popularwoodworking.com/article/american-trestle-table/
Got it!
Thanks
How do I turn off the email Q&A?
https://blog.hubspot.com/website/disable-comments-wordpress
Thank You for your time. I have a LN 73 Large Shoulder Plane which is great to use (and look at). I also have a wooden moving skew Fillister rabbet plane which is finicky to set up but works fine once set up. Is it really possible to use the LN 73 for all rabbets, dovetail pin board rebate – love this method!, fielding panels (which I’ve not tried yet).
You can use an 073 for those operations. But it is cumbersome. The escapement isn’t designed for lots of material removal. And you will have to gauge in the lines to guide the tool. I have done these operations many times with an 073 when traveling without my moving fillister.
Good morning, and apologies if this has been asked before. What joinery did you use for the Mechanical Library? How do you prevent raking without a backing board? What’s the best breakfast sandwich?
It’s assembled with screws alone. L-brackets fasten it to the masonry wall with long Tapcons. English muffin, fried chicken plus a little sausage gravy.
Yum!
Good morning! As always, thanks for taking these questions! There’s a “Roman work bench” I’ve seen in the stick chair video, or maybe the Gibson video, or maybe both, that I think you discussed elsewhere as not being a workbench at all but started life as furniture. Can you point me to that discussion? I’ve looked but can’t find it again. Cheers!
I have no idea where we discussed that. But after both of my Roman workbenches went to new homes, I drafted a sitting bench I had made years ago into service as low workbench.
Here is the bench:
https://www.popularwoodworking.com/projects/i-can-do-that-skansen-bench/
I added a palm, a Hulot block, a twin-screw vise and holdfast/peg holes. It has held up quite well, and we use/abuse it all the time.
That’s the bench! I don’t think that’s the article I was recalling but thanks for the link, and the confirmation it works!
I wonder if it may have been this blog post you were thinking about: https://blog.lostartpress.com/2021/01/25/djurgarden-meets-rome/ ?!
And just to be clear, no, I don’t know the entire LAP blog history by heart, but I could recall that the conversion from piece of furniture to workbench was linked to the first virtual-only (for pandemic reasons) Colonial Williamsburg Working Wood in the 18th Century conference, which I attended, and know was in January 2021, so I just went through the blog posts from that month, and found the above.
Furthermore a search of the blog for “Skansen” also turned up this post: https://blog.lostartpress.com/2020/12/20/getting-ready-for-working-wood-in-the-18th-century/.
Cheers,
Mattias
Ding ding ding! It was the second link I was remembering. Thank you!
How durable is the linseed oil paint you were testing? The previous posts about the paint have me curious if it would be better than milk paint for a roll top desk refurbishment I inherited (the desk was previously painted and had been stripped before it came to me).
We have found it far more durable than latex and acrylic. It ages very well.
How do you ship your chairs to customers? I’m curious both about the crate design that you ship them in and the method of shipping.
I work as a carpenter and, thanks to your book and video, I’ve been building stick chairs when work is slow or it’s raining. I’m hoping to someday sell them to supplement my income.
There’s a post on building crates: https://blog.lostartpress.com/2018/09/17/one-way-to-build-a-crate/
We ship the chairs via common carrier. We now use Old Dominion.
Old Dominion is great! I saw them in concert just before Christmas.
(Or do you mean the trucking company?
I am building the anarchists workbench and was wondering what the grain orientation should be for the shelf boards and vise wood. Both are flat sawn. Should the grain peaks be down (smiley face with grain) on the shelf boards, up (frowney face with grain), or alternating. And for the vise, should the grain peaks face the bench or away?
With shelf boards, I don’t think it matters much. With the vise, I usually put the bark side toward the benchtop (heart side toward the user).
Where do you purchase seat blanks? What type of wood is used in them?
Thanks
Stick chairs are made with whatever material you can get. So I use elm (my favorite), oak and ash. I get my lumber from C.R. Muterspaw in Xenia, Ohio.
https://crlumber.com/
Someday you’ll try Outdoor Living Group in Moraine Ohio (Just south of Dayton). They have whole trees cut into slabs. Lots to choose from. No exotics, they use locally downed trees.
Hi
I have bought tons of stuff from LAP since the very beginning of your business and enjoyed all the books and tools you have offered.
However, (whenever there is a “however” or a “but” after a compliment then trouble is coming) I recently purchased a bottle of Piggly No Wiggly glue and the glue was solidified, about a third of the way down, with a white foamy looking substance.
The bottle was only a few months old, was still unopened until I went to use it this week, and it was stored in a cool dark place.
It was warmed in a Hold Heat pot and removed to use it after the water was heated.
Any thoughts or suggestions?
I have used Old Brown Glue in the past without issue, as well as started using hide glue in the powder form.
Thank you for any input you might have.
Send a note to help@lostartpress.com and we will ship you a replacement bottle ASAP. I have no idea what happened to your bottle, but it sounds like something went wrong.
Thank you very much! I have done so and included some photos in my replacement request! Always a pleasure!
I have followed Christopher’s recommendations on tools from the ATC, your many blogs and Open Wire and have been very happy with every tool including your Crucible planing stop, Monkey Bevel, dovetail marker and Lump hammer, LAP books, etc… from Lee Valley… Love the Lump! The only area I went a little further is with a 1990’s LN No.5 from Patrick which now has a LN original W1 iron with a whale back chip breaker and a LN A2 blade and new chip breaker. I went with a premium no.5 since I will use it for maybe some roughing but mostly shorter trying/jointing and larger smoothing. Christopher recommends a premium plane with two or three irons for that in The ATC.
I do need a trying/jointer plane since I only have my Dad’s old Powermatic 141 which I love, but do not have the space or want of other power tools.
I really can’t justify an LN no.7 at $500 USD + $146 shipping USD (LN won’t just ship USPS and claim there is lees chance of additional charges, which didn’t exactly work out) and customs charges at around $75 CAD totalling $720 USD or $975 Canadian. Used LN is going for as much or usually more than from LN but less shipping cost.
Jointer Plane Options if you think there is a valid option to an LN No.7?…or No.6??
a. I have spotted Stanley No. 7’s with two or three patent dates in decent condition between $150-$200 USD. As much as I didn’t want to ever restore an old plane again, this may be exactly what I should do? I do have the 10mm 30” float glass and a Starrett straightedge along with my shop made wooden one that I use 95% of the time and am confident I can get a long sole flat. I have every David Charlesworth DVD via LN streaming account, his books. I did this on my wooden jointer which worked perfectly but the plane is too high and heavy as it was a dense heavy wood, not beech and almost 10 pounds in weight which I couldn’t balance on a 3/4”-1″ board edge very well.
b. A newer lighter ECE wooden – still higher than metal planes though I won’t use everyday…or maybe I will. I doubt I’ll have many projects over 4’ mostly up to 32” or so. However, I’m partial now to metal planes and their adjustments.
c. A Juuma no.7 from Fine Tools/Germany which would set me back just under $300 Canadian shipped from Germany and not require as much fettling according to the late Mr. Charlesworth. Machined beds, not linished, bronze, etc…yes, probably an LN copy.
d. Other suggestions? A Veritas No.6 which seems to be the only larger Veritas plane that has the look of a more traditional design but is reasonably priced plus a PMV-11 cutting iron? I really don’t like the look of their Custom planes. The different aesthetics look like a yacht from a contemporary Italian naval architect rather than a New England Atkin ketch.
I hope the one possible option above does not cause a flurry of not supporting local tools makers, being a communist or right wing or what ever. I try and love most of their LN tools and many LV tools but it seems LN makes it difficult for Canadians and I just don’t favour the newer Veritas bench plane aesthetics.
Thank You!
If I were faced with this set of constraints, I’d buy a nice old Stanley No. 7 and fix it up myself or hire Mark Webster to do it (https://www.instagram.com/mwebster51/). There are other people who offer this service as well.
The best place to buy old tools is at a tool meet (I know there are some in Canada). And there is a Canadian Facebook group for old tools: https://www.facebook.com/groups/721283508069957/
When you buy in person, you can usually get lucky and find an example that doesn’t need its sole flattened (which is the most arduous part).
I’m not a fan of the Asian-made premium planes. The quality is inconsistent.
Thank You Christopher for the sound advice and contacts as always!
Tools of the trades show and sale Pickering Ontario Canada
SPRING SHOW APRIL 7, 2024
10:00am – 3:00 pm
https://ontarioantiquetools.com/
Not sure where in Canada you are but this is one I have been to. Didn’t buy much because I bought lots new style Veritas planes and love them before I found this sale but the years I went they had lots of old planes wood and metal and many specialized planes for coopering etc.
Here’s my list of vintage tools vendors in Canada… you may find something there.
https://workingbyhand.wordpress.com/vintage-tools/
I bought a type 15 No. 7 from a local tool meetup (PATINA tools near DC) and sent it to Mark. The iron was extremely bent, so he replaced it with a Hock iron. This was about two years ago, and the total price was still quite a bit lower than what LN was charging at the time, including shipping back and forth. It is an unbelievably stunning tool, and certainly matches everything you would expect from a LN plane. It might be a while until you get off Mark’s waiting list, but if you can wait I can’t recommend it enough. I also did not want to have to do any work on a plane that long/large myself.
I fixed up a 1910 Stainley Bailey #7 two weeks ago following Chris’ instructions in his “How to Super Tune a Plane” video. It was a well used tool with a 1992 blade. From my experience, it isn’t worth the time to mess with an old blade and chip breaker but it is relatively straight forward and fast to flatten the bottom on 80 and 120 grit 4×24 belt sander paper if you remove the frog and leave the handles on. Brush the sandpaper frequently with a steel wire brush to clear the grit of the cast iron or the paper will stop cutting – it isn’t worn out. – I got a small one from Home Depots painting supply section that cost $3. The blade takes a lot of time and expensive sand paper to flatten. Don’t get me started on how long it takes to get a chip breaker to properly seat. I gave up and bought a Hock blade and chip breaker set for it. The Lie Nielson set is too thick for the blade adjustment yoke to engage. Check the brass blade adjustment knob for wear where it contacts the yoke. Mine had worn to paper thin and I had to replace the knob. Unless you have another plane for parts the knob will run you $25 or so.
Good morning Megan. Is there some trick I’m missing when painting a piece carved with spells when I want contrasting colors? Or is is simply a matter of painting the base color, carving spells, and then carefully repainting the carved spells the contrasting color? I cannot figure out another way, but you guys constantly surprise me with tips & tricks.
Thank You as always for the open wire. It is a treasure trove of information.
Hi Paul,
Megan may know a trick to masking (Paint, mask, engrave through the tape, paint through the mask, remove tape), but I am just painting and then cutting through to the raw wood for contrast.
I’m afraid I don’t have a magic masking solution. Chris’s idea might work, but it would use a lot of tape and I suspect there might be paint bleed under the cuts. @danielclay on Instagram has been doing a lot of chip carved color studies – might be worth looking through his posts.
You could maybe do it with something like Oramask?
Never tried this, so beware; but I wonder if it would work to paint the spells, wax them, then plane to bare wood. Then paint the background, with the wax helping to keep the background paint out of the spells
I’ve had success (assuming it’s a flat board) with using a hard rubber brayer roller to topcoat without getting paint into the carvings. With a little practice getting just the right amount of paint on the roller, it went way faster than screwing around with painter’s tape and having to touch up all the bleeding.
Hi. I recently acquired an antique tool chest full of tools. Pretty nifty. I plan to keep and use the tool chest and the tools to make hand crafted projects….but would love to have information or speculation about the chest. Where would you turn?
It has very fine inlay work on the lid and tills.
The moulding planes are American—mostly Sandusky Tool.
Any suggestions?
I would join the Mid-West Tool Collectors and the Early American Industries Association.
https://mwtca.org/
https://www.eaia.us/
Both organizations are filled with people who have deep knowledge about old tools and their history. Take some photos of the tools and chest to one of the meetings, and I’m sure you’ll find lots of people who could help.
Hi Chris: How often do you sharpen your Veritas Power Tennon Cutter blades? Is it fairly obvious when they need to be sharpened?
They pretty much stop cutting when they are dull. I don’t sharpen them – I replace them (I know, shamey shame on me). I get more than a year out of a blade….
Hi all! Chris, I have your sharpening video and itis excellent– fun to watch, entertaining and you learn something along the way! I have taken 3 greenwood stool/chair classes from Andy Glen in Berea and about to take a fourth this summer. How about a tutorial on sharpening drawknives and spokeshaves????
thanks! dale
The Galbert Draw Sharp is the best method for a razor Sharp drawknife. Benchcrafted sells them. https://benchcrafted.com/products/drawsharp
For spokeshaves I use the long jaws that Lie Nielsen sells for their sharpening jig.
Hello. I am a huge fan and have learned so much from your books, videos, and the blog. My question is this: how to you stay confident in your work? I have built stools and 3 chairs (stools and 1 chair from the Anarchist’s Design Book and 2 chairs from the stick chair book). And I have moments of wow, that’s not bad…followed by jumpin’ Jimminy Cricket, WTF am I thinking when I see a weird gap or it went together less than smoothly and required some influencing to fit the comb, or I actually drilled the mortises less than consistently and accurately…and I want to burn it to the ground. haha.
so how do you stay upbeat and confident?
Thanks, hoping still to take a class from you guys some day.
Chris
Most normal people are insecure about their work – I’m no different. And I have dismembered a few chairs that were making me crazy.
But I also keep in mind that the early chairs were made with gaps and defects. And I love them for that/despite that. So I try to focus more on the form that the tiny details.
This probably isn’t much help.
If you just use the object for 6 months you might be surprised to discover that you can’t really find most of the things that originally bothered you. Admiration from friends that don’t believe you made it can accelerate the process. This applies to anything you make; clothes, socks, hand crocheted snowflakes, whatever. Use the same rule as for cooking: DO NOT mention anything that went “wrong” unless it is totally obvious (liked burned to a crisp). No one normal looks as hard at what you made as you do. (you are free to tactfully ignore the abnormal)
There is no such thing as perfect. If I remember correctly there are always small things wrong with things made by Japanese master craftsmen. I used to fuss and worry about not being able to produce a perfect piece, until I really looked at some old items (furniture, ceramics, quilts, any handcraft) and realized there were no perfect pieces and now just do the very best I can and generally am satisfied with my work.
I have tried to purchase the pure boiled linseed oil (without chemical dryers) that you recommended in an earlier forum but can’t get them to ship it to the US (the site won’t let me). (Sorry, forgot the name of the manufacturer.) I’ve found another provider, Atlas Preservation that makes Swedish cold pressed boiled linseed oil: https://atlaspreservation.com/products/swedish-cold-pressed-boiled-linseed-oil
But it’s also, for some reason, available through Walmart (don’t know if it’s the same quality): https://www.walmart.com/ip/Pure-Swedish-Boiled-Linseed-Oil-1-Quart/374118998?wmlspartner=wlpa&selectedSellerId=101061646&adid=22222222222532866055_1189672322928512_pla&wmlspartner=wmtlabs&wl0=e&wl1=s&wl2=c&wl3=74354627840411&wl4=pla-4577954164905299&wl5=&wl6=&wl7=&wl10=Walmart&wl11=Online&wl12=374118998_10001081018&wl14=Swedish%20linseed%20oil&veh=sem&msclkid=3bb949ef882c1434b7bd2c280c637910&gclid=3bb949ef882c1434b7bd2c280c637910&gclsrc=3p.ds
Would this also work? Or will it possibly turn rancid or have other problems? Not sure about the process of how they make it. Thanks, you Chris and Fitz for everything, once again (and again and again).
I haven’t used that particular oil, but Ottoson is a very reputable paint manufacturer.
Here is another source we use:
https://www.earthandflax.com/product-page/viking-purified-raw-linseed-oil-32-oz-glass-bottle
Or try https://www.solventfreepaint.com/cleaned_linseed_oil.htm (been in business for a generation or more, earth+flax is their daughter/succession plan. If you want a traditional text heavy information website go to solventfreepaint; if you want a more “modern” site heavy on videos and light on text, earth+flax.
Hi Megan and Chris…I’m building a chair and about to cut wedge kerfs into the legs. I understand wedges must be perpendicular to the grain of the seat, but if there is an option for the wedge to be cut with or across the end grain of the leg, which is better? I’ve seen it both ways in photos. Does one lock-in better with humidity changes? Many thanks!
Scott
In theory, yes. You should orient the annular rings of the legs so they are perpendicular to the grain of the seat. So the kerf would therefore be parallel to the annular rings in the leg.
However, the furniture record shows that a lot of early makers did not do this.
Thanks! Appreciate it.
Good morning Chris and Megan! It is awesome you guys do this. Thank you! I have a set of your chair template printouts and am transposing them onto some plywood to cut them out. How do you use the geometry layout on the paper? Do I duplicate that on the wooden template too? If so, how do I use that to transfer the location of the holes from the template to the chair parts? Thanks again!
Josh
The easy way is to apply the paper template to your plywood (we use spray adhesive) and cut it out. The drill small holes through the template at the leg locations and where the sightlines cross the centerline of the template.
Then you put the template on the seat blank, trace its shape and mark the locations of the legs and where the sightlines cross the centerline. Then remove the template and join the dots to replicate the geometry on the pattern.
For a full explanation of the sightlines and resultants, check out the free download of “The Stick Chair Book.”
https://lostartpress.com/products/the-stick-chair-book
Hi Chris, I’d like to self publish a book- It is sentimental only. My wife has hundreds of pages of her writings and it would only be for the family. Of course I’d like it to be nice but I’m not holding out for LAP nice. While investigating the process I’m faced with book printing questions I can’t fathom. paper weight, gloss, white or cream etc. My Ideal would be a final look similar to your Campaign Furniture. Can you point me to a book printing service or a beginners guide for idiots that will get me off on the right foot. Any direction would be appreciated. Thanks
Lulu.com is a good site for self publishing (and it has some answers about publishing terms/choices). “Campaign Furniture” is printed on #80 matte white.
If you’re up for a bit of a challenge and only thinking 1 or two copies I’d suggest you consider binding it yourself. If you have access to a laser printer (the most economical choice) and don’t mind something around the size of a paperback it is pretty fun to bind your own book. If you’re a woodworker (presumably you are if you’re reading the Open-wire!) there’s a surprising amount of overlap between the tools and skills. Check out Das Bookbinding on YouTube.
Howdy,
Long time listener, first time caller! Is there a “Anarchist Hardware Chest” kinda list of good bits to have on hand for furniture building, etc? I just placed an order with McMaster-Carr for a variety of flat head, brass wood screws and am curious what yalls recommendation is for what hardware to keep on hand? I imagine, once upon a time, a woodworker would just amble down to the smith or shop for some screws? I hate to keep placing small orders with Tremont Nail or McMaster for whatnot.
Rick
I hate to take you elsewhere…but: https://www.popularwoodworking.com/editors-blog/how-to-stock-up-on-traditional-fasteners/
I am starting a bent lamination project and wondering what you think about using the gelatin glue recipe y’all have generously provided for such a project. I am sure making enough quantity would be a project in and of itself, but that is something I am willing to tackle if I can expect good results. The lams will eventually form a shell type seat and back. Would you be willing to share some of your adhesives research as I move forward? Thanks
Hi Barry,
Our gelatin glue has too much “creep” for a bent lamination. I recommend you use plastic resin glue (which sets slowly) or a super high strength (300 bloom) hide glue with some salt. Those adhesives are ideal for bent laminations.
I know thaty some users use plain old PVA on their laminations and way it works fine. But I haven’t tried it.
Hi Chris. I have seen a few videos showing the finish Sam Maloof used on his rocking chairs. One part BLO, one part Tung Oil, and melting in beeswax. I’d like to stay away from the BLOs and Tung Oils that have driers and VOCs. if I were to use Raw Linseed Oil and Pure Tung Oil mixed with beeswax, would that take forever to dry and thus cure given there are no driers? Not sure if this would be a good way to go or if it would make finishing interminable?
A purified linseed oil and beeswax finish will cure just fine if you use thin coats and buff off all the excess (we use Huck-weave towels for this). I’m not an expert on tung oil, but I imagine it plays by the same rules.
Hi Megan and Chris,
Thanks so much for doing this each week. I am building the Anarchist Workbench with my high school sculpture students. It’s a first for all of us and we are using the book as a guide, so far so good! My question is about moving it around once it’s finished. We won’t have to move it far, but might have to shift it regularly due to the variety of the work we do in the studio. Have you had any luck with retracting casters? Megan, I think you mentioned this in a post not too long ago. Thanks for the work you do and for any advice you can offer.
Nate
Even the heaviest benches here aren’t that hard to move. We simply slip a moving blanket under one end (one person can lift it enough for that, while the other wields the blanket), then it’s pretty easy to slightly lift from the non blanketed end and move it. Or, we just push it and scratch the floor… There might be an excellent retractable wheel solution on the market, but if so, we haven’t tried it.
I’ve moved mine with a furniture dolly under each end by myself. I just threw a piece of 2×6 on them that was long enough to span the legs. When done, the dolly is kept in the garage.
I am finishing my second drinking table from the design book and this one is in cherry. The top boards have some variability in color that I know from reading should fade over time with the darkening of the cherry but I have noticed in the blog that you use Black Bison Wax to enhance and darken a piece. I know you recommend a wax finish for most tables and was planning to use Soft Wax 2.0. Is there a way to combine the two? Can I put Soft Wax 2.0 over Bison Wax? My sense is no, that they are two different types of wax and are not compatible. Thanks.
Black waxes don’t really look good on diffuse-porous woods. The wax looks best on ring-porous species, such as oak. Adjusting individual boards for color is possible. It’s takes a little practice. The typical process is to apply a film finish (such as shellac). Then tone it using aerosol toners (I use Mohawk toners).
https://www.mohawkproducts.com/Toners-s/1174.htm
Then a final topcoat of finish.
Honestly, I usually recommend patience. Finish the table with some linseed-oil product. Put it in the sun to jumpstart the UV process.
I’m sorry, but since ya’ll are considering possible additional courses for this summer and fall (the one fall I might be able to come up to Kentucky from Missouri until 2027), if I might make a small request–would you ever consider overseeing a project (like a small cabinet, table, or desk) with dovetailed drawers? Maybe that’s too boring (or complicated), but still, I’d love to work on such. I’m not near any hand tool schools that would do anything like that. Just a wish upon a star.
We’ve both taught a Shaker side table with a drawer in the past. I’ll put it on the list of possibilities. (But I should stipulate that we are only adding classes if other plans fall through…and we hope they do not.)
Thank you again for taking our questions. Two weeks ago I asked about the staked worktable from the ADB, and your answers were a huge help. I am still somewhat of a beginner woodworker and this is the first piece of actual furniture I’ve made (not counting my workbench). I have two follow-up questions I’d like to ask today…
1) I’ve decided to go with 8/4 stock for the legs (red oak) and am getting started now on tapering and octagonizing them. I had asked about having 1-1/2″ tenons, and was reassured this should be fine. Before I shape the tenons, I just wanted to make certain: Will I still be fine going with round tenons here, as opposed to tapered, even though they are undersized compared to the plans? Also, I am only supposed to bore through the battens and not the tabletop itself, correct? Sorry if these questions are very basic and obvious. I’ve put in a lot of work so far and don’t want to make an irreparable mistake.
2) I am doing all the shaping of the legs with a hand plane. Could you give me a sense of roughly how often you would stop and hone your blade if you were doing the same? For example, after finishing one complete leg? Or, even sooner than that? I am sure I don’t sharpen enough, but it would be really helpful to know how a professional does it.
Thank you very much!
This will work fine – 1-1/2″ untapered tenons are very strong. Especially for a table. And yes, they go through the battens only.
If you start with a good edge and the steel is decent, you should be able to taper all four legs with one edge. Use paraffin wax (canning wax from the supermarket) as a lubricant. Then sharpen the edge when the legs are done.
Hi Chris and Megan! I’m actually just really curious about the chair in the photo above–double decker look with floor-scraping stretchers…thoughtful reasoning behind the design or just lots of fun?
That student has made several chairs – so he tried something new! And we think new is cool – as long at it still fulfills the brief of “chair”
I am about to start on the TWW American Welsh Stick Chair as a first chair project. I have the templates. Is there anything you’ve learned since producing this course (I’m thinking of Even Better Stick Chairs and the BB Custom Tools bits & extension) that you recommend as adjustments to the design and process? As always, profound thanks for doing Open Wire. It is invaluable.
If it’s your first chair, I recommend over-compressing the tenons for the sticks a bit. They should go in tightly when uncompressed, but slide in very easily when compressed. That makes assembly much easier. You can pull the arm and sticks into place with just a few mallet taps.
Any tips on using the sorby sizing tool on a lathe?
Other than those tips, it’s a cinch tool to use.
Hi Chris and Megan,
When joining two boards for a chair seat my boards are not perfectly at 90 degrees but they do match up with no visible gaps.
Am I risking these boards coming apart once the chair is assembled?
I haven’t glued them yet because I’m not certain if they will hold.
I hate to ask a second question but have either of you used Pinus Radiata in place of white pine or sugar pine.
My local home center carries it and it’s beautifully milled, straight grained and knot free.
Thank you for your time
Ray
If the two edges come together seamlessly when you clamp them, the joint will be fine. You could then flatten the seat after gluing – if the angle isn’t too wonky.
Radiata pine is mushy when you work it. The wood also crushes easily when you chop it. I might use it for trim in a house, but it’s not a great furniture wood.
Thank you.
I used Radiata pine, our native Monterey pine here in California, to build a book shelf. Beautiful wood but as Chris says, it is challenging and crushes easily. I was in New Zealand last year and saw their forestry practices. It is grown in dense monocultures and the trees are limbed to 20 feet early in their life so the wood is straight and knot free. But it is extremely fast growing, I think it is cut at 25 to 30 year intervals, which is why it crushes easily.
Another question from the blog archive –
Chris mentioned purchasing a pair of moccasins from Arrow Moccasin company. Were those moccasins suitable for wearing most of the year? Is Arrow still your preferred moccasin company?
Thanks for doing this every week!
I love those moccasins. But at my age I now need more orthotics. I had one pair for warm months and one lined pair for cold. Beautifully made.
Good morning!
What ratio of flakes to alcohol do you use when mixing Tiger Flake Shellac? What is the standard recipe?
Thanks!
We use a half-pound cut – 1/2 lb. flakes per gallon of alcohol. You and scale that up or down as you like.
Greetings!
Thanks for taking time on Saturdays for hosting and fielding questions.
Sort of “off topic” … I just received and read the latest Quercus magazine. Near the end, it kinda sorta suggested maybe that it might be the last.
Just wondering if you have heard anything regarding this?
Yup. Nick has closed shop. I don’t know what’s next for him, but I’m sure he’ll turn up again.
That’s a real shame, but not surprising. It’s such a hard business. But it was a great run, and they should be proud.
Top of the morning to you, LAP. Chair question: Am I making a mistake if I make a stick chair from clear, vertical grain doug fir? How about Alder? This is the most plentiful 8/4 material in my area…
Fir will do nicely. Tight growth rings will be a plus. It won’t be fun to saddle….
Alder is OK. If it’s straight it will be fine for the structural members. And a pleasure to saddle. You might consider a chair where the sticks, stretchers and legs are VG fir and the rest is alder (and paint it).
Good morning, I live in a northern climate where it can be difficult to find days that are warm enough to set linseed oil painted furniture outside in the sun to help cure them. So this time of year projects tend to sit unfinished for a few months until the weather changes. I have been reading that you can cure linseed oil paint using UV-A light in a fraction of the time. I was curious if you have ever experimented with that?
We have not. Sorry. I would check out the painting recommendations published by the Swedish paint makers, who deal with this problem all the time.
I have a vintage Stanley no 5 with a very loose feeling lateral adjustment lever. Any tips on tightening it up? Or is this something to just accept and live with?
You can peen the rivet that hold the lateral adjust lever. I use a nail punch and a hammer. That will tighten things up.
I’m making a chair based on the stake chair in the ADB. I made a model and tweaked the legs, and that worked fine, but in fanning the sticks to the crest I’m not having success. I want 10 degrees back, but fan out about 5 degrees. I tried drawing sight lines like the legs, but it seemed to bind up in a half scale model. Is there a trick/method for this?
I make changes such as these when I have the arm up on the drilling jigs on the seat. Then I use sticky-tack (the stuff for hanging posters) and bamboo skewers to try different arrangements of sticks. Once you get an arrangement you like, then drill the mortises. You can even leave the bamboo skewers in place to help guide your drilling. This is shown in the free download of “The Stick Chair Book:”
https://lostartpress.com/products/the-stick-chair-book
Thanks. I did read that. This chair has no arms. I marked the angles on the crest and it’s close, but I don’t feel comfortable risking good wood so I’m going to make a full size model.
Both of you are advocates of using nails, particularly cut nails, as historically correct and practical fasteners. In most cases, I would reach for a coated deck screw instead. They are covered with a plug if appearance is important. My choice is dictated by a weak ability to strike a nail cleanly and drive it straight. Would you discuss the merits of screws versus nails?
It’s all personal taste. I like to use furniture hardware to make furniture (cut/blacksmith nails and slotted screws). And deck hardware to make decks. Both approaches work. It’s just about what you like and what you like to do.
I’ve seen lots of period-style furniture made with Torx screws, so you aren’t alone.
Dear Chris,
I am making a Roman bench this moment and wondered what you do with the underside where in my case the square legs meet the underside only at one edge since they are splayed and Raked? I’m using 1-7/8″ square Birch for the legs and rounded the tenon after cutting the waste away with a tenon and carcass saw with a couple rasp. The tenon takes some time getting it right but I’ve got two done this morning so far. All round mortises drilled per your instructions on rake and splay, etc…. I wanted to leave the legs square with maybe a chamfer. Do I shape the leg just under the bench top more roundish almost eliminating the shoulder so you can’t see the exposed flat shoulders? I’m not sure if a picture could be posted or if this makes sense?
You don’t have to do anything. The tenon will be trapped between the shoulder and the wedge. If you want it to look really nice, cope the shoulder so it meets the underside of the benchtop. But with workbenches, I wouldn’t bother.
Thank You!
I did something similar for a different project. After fitting the tenon and inserting the leg as deep as it would go, I scribed around the square leg. Cut the scribed shoulders with a handsaw, then continued to shape the round tenon to the cut lines with a chisel. When you turn it over the square leg is flush with the bottom on all 4 sides and crazy strong. The top you see a wedged round tenon. It is much easier and faster than chopping out a square angled mortise.
I’m going to take two red maple logs to get milled soon. They are around 18-20 inches in diameter. Do you have any recommendations for how to get them cut? I’m thinking one flatsawn at 8/4 and the other quartersawn at 5/4.
Depends on what you are making. But that is a good strategy for tables and chairs, which have both thick and thin components. For casework, I’d add some more 5/4 into the mix.
Thanks
Are there any wood expansion considerations with the “Big Box” wide panels, mostly made up of pine and sized 48’L x ~~24″W? These are usually made up of 2″x ~ 6 to 8″ pieces of wood glued together like a puzzle. You can even get some that are 6′ to 8′ long.
The panel will move as a whole, but not horribly so. Pines (especially the white pines) don’t move once they are dry.
Maybe 5/32″ during a typical year.
Use this calculator to plug in more specific numbers on moisture change in your area:
https://www.woodweb.com/cgi-bin/calculators/calc.pl?calculator=shrinkage
If the panel is all one species, then the little blocks should all move about the same.
Be careful if there is any chance the panel will be exposed to water. A friend made a couple 6 board chests as tournament prizes (medieval recreation) with those panels and had a top split when it was rained on. The panels were handy for describing how to build one without dealing with glueup, but we are now trying to invent a 2-part team taught class, one how to glue up and the other for the joinery. 6 board chests are a gateway “you can do this and it isn’t that hard and you don’t need weird tools and can buy the wood at the local bigbox” introduction to woodworking.
For jointing the edges of chair seat blanks with a #7 jointer plane, do you advise honing the blade to a camber or dead flat. I ask because Galbert’s book says straight and in your furniture video you show how a camber helps you adjust the edge to 90 degrees – but that is a much thinner board that the seat blanks.
I always use a camber. It is so slight that it makes no difference to the finished joint, even in 8/4 stock.
Some woodworkers use a straight iron. Also works. But that’s not how I learned it.
As someone who loves woodworking, I’m constantly on the lookout for tools that make the process easier and more efficient. However, my weakening grip strength has been making it difficult for me to apply enough pressure to hold things securely. That’s why I’m reaching out to you for a recommendation – could you suggest a brand and model of F-clamps that would allow me to work more comfortably and confidently? Thank you for all your help in supporting the woodworking community.
Burgeoning arthritis makes it difficult for me, too. There are several clamps that help me work more comfortably…and with wooden-handled clamps, I sometimes drill through the handle to add a tommy bar (from 1/4″ or 1/2″ dowel). If you don’t need to exert a lot of pressure, lever clamps are nice, such as these from Bessey: https://www.bessey.de/en-us/bessey-tools-north-america/products/clamping-tools/lever-clamps
For heavier duty, these: https://www.bessey.de/en-us/bessey-tools-north-america/products/clamping-tools/premium-all-steel-bar-clamps/extra-heavy-duty-(7200s)
My ideal for K-bodies is older, wooden handled clamps that I can modify with a tommy bar as noted above. I think there used to be parallel jaw clamp on which the handle position could shift to allow the user to generate more force…but darned if I can find it.
Also, sports tape on the handle helps. https://blog.lostartpress.com/2022/11/08/2022-anarchists-gift-guide-day-2-hockey-tape/
Thank you for your helpful reply.
In addition to above suggestions I have slipped bicycle handlebar grips over wood handles. Great grip and makes handle diameter bigger which helps arthritic hands…only problem is everybody wants to borrow them.
Improving grip helps. Could try adding hockey tape or baseball bat grip tape. Easily removed if it doesn’t help. If still need a monster grip…try a clamp with a “T” handle, and use a length of pipe over the T.
A reader reminded me of these. I don’t love them…but you can tighten them more easily…once you get used to them!
https://www.leevalley.com/en-us/shop/tools/hand-tools/clamps/bar/72719-anti-slip-parallel-jaw-clamps
Lie Nielson plane info. During my fettling of old Stanley planes two weeks ago, I emailed Lie Nielson with a question about a jack plane replacement blade and some questions about the instructions that came with my LN 62 low angle jack plane that were confusing. To my great astonishment Sam called, yes called me, and I hadn’t even provided my phone number so he must have gotten it from an old order I placed. Sam confirmed that the instructions are confusing and they don’t hone the blades the way the instructions suggest anymore and he will ask that they be revised. He said they now hone the bevel of the blade to 25 degrees, and set up that way they make great longish smoothing planes. (25 degree grind, 25 degree bevel up, plus the slope of the bed make for a steep cutting angle. Also, because of the geometry of the bevel up blade, cambering it isn’t effective. He said they also hone the toothed blade to 25 degrees but that doesn’t make sense to me. The toothing effectively narrows the width of the plane to make it easier to push with deep cuts. He said he finds the toothed plane great for scrub plane use as it cuts flat and doesn’t leave curved trenches and ridges. Taking diagonal cuts also creates a hatched target to plane to when you smooth the rough but flat surface.
I meant to write 25 degree grind, 25 degree hone, bevel up, and sloped bed make a stee cutting angle.
Hi John,
Sorry. Am I missing a specific question here?
We use a No. 62 all the time here. We camber it like a jack plane with a 25° grind and 35° hone. Works fine and has for many many years. It’s a great lightweight jack plane that is simple for beginners to set up.
I have used the toothed iron, too. I find it slower than a cambered iron.
I’m not disputing Lie-Nielsen here. Just reporting our experience.
I hate to ask a question about finish like it hasn’t been asked and answered, but I was recently surprised.
I just finished a dining table with soft wax (cue the eye rolls from the crowd)- I used the recipe you provided with linseed oil, beeswax and limonene. Dried it until it was dry and then buffed it again- about ten times. I also added a second coat after about ten days.
The first time I cleaned it with a slightly damp rag it raised the grain. It still looked okay, but it got rough and lost some sheen. Is this normal? I’m not expecting waterproof, but I’m afraid I have almost no resistance to water.
Is the raised grain expected or did I make a mistake somewhere? Thanks for all you do, and sorry for asking two great woodworking minds a silly question.
If you never before introduced water, then I’m not surprised this first wiping raised the grain. sand it back, and add more soft wax; it (probably) won’t happen again!
Have you done any work with hard waxes like Rubio and Odies? Is there a reasonable substitute like the Anarchist’s Daughter’s wax? Or is that a completely different thing?
Odie’s is a lot more liquid, but is all natural, no driers. So it is in the same vein. But it costs a lot more. I don’t know enough about Rubio to comment.
Would you remind me of the name of the wood fill you wrote on a few weeks ago? I have an ‘oopsie’…
Durhams Rock Hard Water Putty.
Durham’s Rock Hard Water Putty.
Hello. I am adding a french cleat to a 30×30″ cabinet. It is 13.5″ deep. Cabinet is made from white pine- cleat will be red oak. The inside has 4 shelves and is intended to hold shoes, so not too heavy. It will be fastened to drywall.
Do you have any suggestions on how wide the cleat should be? Is it worth adding two? One on top and one a third a way from the bottom? Do you have any suggestions on anchors if I can’t locate the studs? Thank you.
One cleat will be fine. Mine are typically 3″ to 4″ wide. When I fasten cleats to studs in drywall I use 3″-long self-tapping screws. I’m not a big fan of drywall anchors. The anchors aren’t the problem – it’s the drywall. Maybe someone else can recommend a good drywall anchor….
With this cabinet you should be able to catch two studs.
In addition to the cleat you’ll probably need a board near the bottom of the cabinet to keep the cabinet positioned correctly without the thing tipping forward.
How do you know when you need to replace an old Stanley blade. My #5 is about an inch from the slot, but still seems to hold an edge for a while. Is holding an edge the tell? Or is there a general rule for how much of the blade is hardened? Googling seems to yield mixed results. Thanks!!
It’s about edge life. If the blade holds an edge as well as it did in its early life, you’re fine. As soon as edge life drops off, recycle the blade and get a new one.
Good Afternoon. I’m going to be building a 3-legged stool for use at my workbench. Just a shallow seat, about hip-height, to plop my butt on when doing repetitive tasks. I want to hang on the wall Shaker-style when not needed.
My question is this… At what angle should I make the seat so that it doesn’t feel like I’m sitting on the edge, and my tushy won’t become numb over time?
Most work stools are parallel to the floor. Here is the one I like, which can be raised to a nice height.
https://blog.lostartpress.com/2021/01/25/plan-for-a-sheffield-cutlers-stool/
Tens of thousands of these were used in Sheffield.