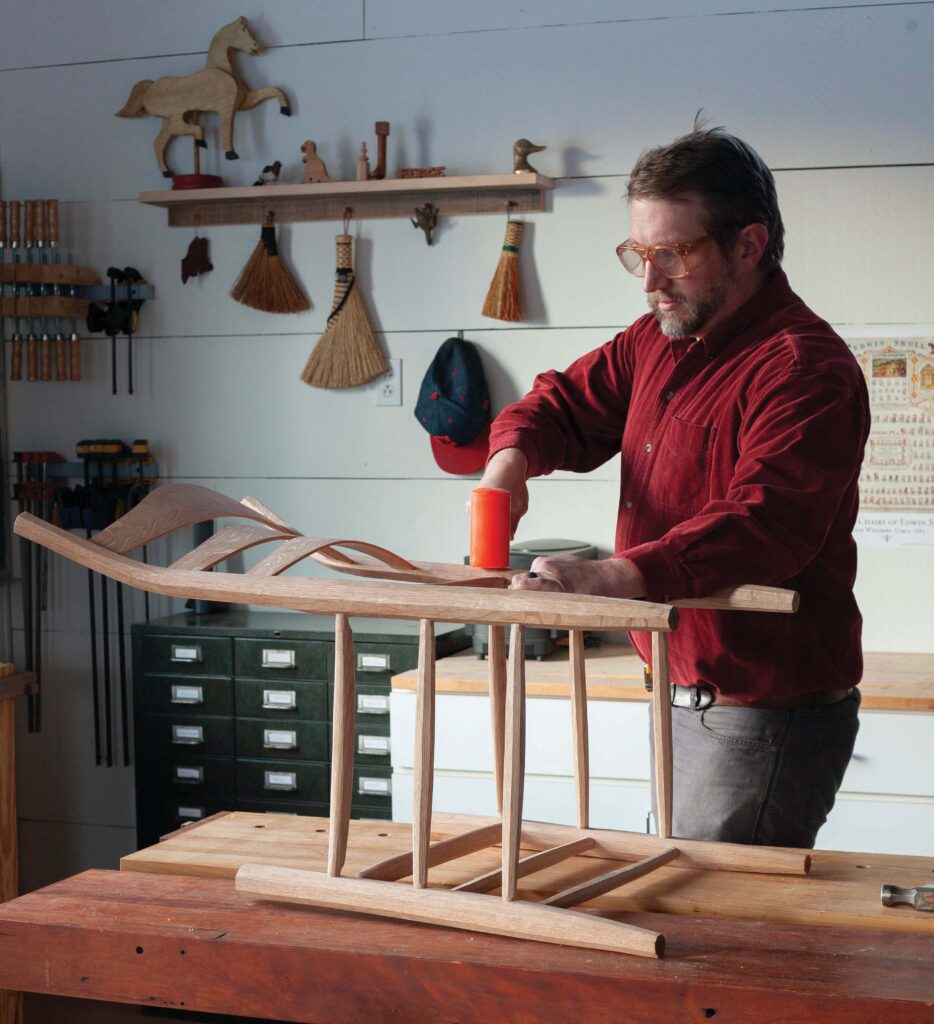
Update: Thank you to Andy for handling today’s Open Wire! Comments are now closed.
Today, we are delighted to have Andy Glenn, author of “Backwoods Chairmakers,” here to answer your woodworking questions – particularly those relating to post-and-rung chairs of the Appalachian region, as that’s the core of his new book. But, he’s a long-time woodworking teacher who trained at North Bennet Street School, so he’s certainly qualified to answer on many woodworking topics (ask him about his CNC*). And in case you have questions about any of our books, videos, tools etc., I’ll be checking in from time to time to answer as needed. As always, there will sometimes be a lag between your asking and our answering.
And I thought this might be of interest: If you want to make a greenwood ladderback chair (aka post-and-rung chair) but have no access to appropriate logs, or the simply don’t have the time to split out your own stock, Andy sells chair kits on his site. And, here’s a link to his teaching schedule for 2024.
But you can learn from him now: simply post your woodworking questions below. Comments will close at around 5 p.m.
– Fitz
* He does not use a CNC. Don’t ask him about CNC.
Thank you Andy for giving your time today to answer our questions. I have two. In your travels did you encounter any chairmakers using saplings or smaller limbs while in a rustic post and rung chair? There was a few makers in the foxfire books that made a pretty refined chair this way. I have made several this way myself in the last 30 years. I am not talking about the log furniture you see in cabins.
Also, what style of shaving horse did you see the most of? Dumbhead or English style?
One other question. Are there many makers in Appalachia using corn shucks or cotton webbing (shaker tape) or other seating material besides hickory bark?
Hi Jeff,
I’d guess about half the chairmakers used hickory and half something else. Shaker tape, paper fiber, flat reed, and sea grass among the alternatives. The bark weavers had solid access to hickory and the commitment to put in the labor to obtain it (the other weaving materials are commercially available and most always in stock).
Randy Ogle in Gatlinburg, TN has and can weave in a corn shuck seat. But he says it takes too long relative to what a customer wants to pay for the chair. So he replicates his shuck seat patterns with sea grass.
Hi Jeff, regarding smaller limbs; I came across Tom Lynch in West Virginia making a rustic style (alongside his refined Shaker-style chairs). I believe he used rhodadendron, since the bark wouldn’t flake off over time. He was the only one working in this way and developed a method of design and work when using winding, twisting, irregular parts. The rest of the chairmakers (I came upon) used the log, and nearly all of them the straight grained sections of it. Terry Ratliff and a few others used the sweeps and wavy grain in their chairs, shaving the parts to follow the grain.
With regards to shavehorses, it was split pretty evenly between various styles. Probably a few more dumbhead horses out there than english. I attempt to photograph as many shavehorses as I could. One maker didn’t use a shavehorse….he used a “pin horse” and made square(ish) parts on it.
Started reading you book last night and think it’s well written and surprisingly funny, ( Welcome-Keep Out). Will you be sending a copy of the book to the chairmakers themselves?
Also, a number of years ago I gave you a cottonwood slab for your students to work with. Did they learn anything from it?
Thanks.
Thanks Eric. Nice hearing from you. I hope there’s a little humor in there.
Yes, each family/chairmaker received a book. I’ve heard back from a number of them. They’re excited to be part of it and love the beauty and quality of it. I visited them a few years ago, so the book most likely came out of the blue earlier this month.
Thank you for that cottonwood slab. Two students split it between them and designed/made tables from it. They came after their work shifts to make furniture for their apartments. My hope is that piece encouraged a couple students towards continuing with woodworking.
The dog and I are road tripping from New Hampshire to Texas and back in April. I’d love to add a few woodworking detours to the itinerary, and would be grateful for any recommendations you (or fellow readers) have for shops, makers, museums, and so forth. (I’d love to sit in an actual stick chair, if there’s somewhere I can do that!)
Southbound, I’m going via Appalachian Ohio, Kentucky, Missouri, Oklahoma, Dallas. Northbound: Houston, Louisiana, blue ridge mountains.
Thanks, and congratulations on the new book!
Hi Rob,
Thanks for the note. It still feels a little surreal that the book is finished and into the world. I now understand the tortured writer stereotypes, because I think I traveled through them all along the way (self doubt, anger/frustration/discouragement, the hope that no one would ask “how’s the book going”, thinking it was nearly done though it was nowhere near done…….and now elation/gratefulness).
A few thoughts on your road trip. In no particular order: Shaker Workshops in Arlington, MA; the Kentucky Folk Art Center in Morehead, KY, The Southern Highland Craft Guild along the Blue Ridge Parkway in Asheville, NC, Lost Art Press/Covington, KY, Shaker Village at Pleasant Hill, Herrodsburg, KY, and The Colonial Homstead (antique tool shop), Millerburg, OH.
One other note: There’s an exhibit happening titled “Hammer and Hope” at the Center for Craft in Asheville, NC around the chairs of Dick Poynor by artists/chairmakers Robell Awake and Charlie Ryland. I hope to make it later this summer once I trek that direction from Maine.
Shaker Workshops was sold after about 50 years of the original owners. The new owners moved production to Sandwich New Hampshire. But the original location still houses Old Schwamb Mill, which woodworkers should definitely visit.
Rob – I’d also recommend the Shaker Village in Pleasant Hill, KY, and Larkspur Press in Monterey. Tricia is spot on about the Artisan Center and Berea.
Hi Rob,
You may also wish to check out the Kentucky Museum at Western Kentucky University in Bowling Green, KY. Excellent collection of local vernacular furniture, a couple of log cabins, and excellent folk exhibits. For a totally different experience, the National Corvette Museum explores the evolution of the iconic sports car in American culture. https://www.wku.edu/kentuckymuseum/ Bon voyage!
Hancock and Mount Lebanon Shaker villages. Yes, both. Even if you’ve been to Canterbury and New Gloucester a dozen times.
And Enfield NH, though it’s probably not on his way south. They just made a major purchase, requiring original Shaker buildings and lands that were sold off 100 years ago. They also have two floors of the great stone dwelling that has been converted into a hotel of sorts, for those who want to stay where the Shakers once lived.
Just yesterday I picked up a book about Canadian pre-confederacy furniture. There was a chair that used gut for the seat, much like a snow shoe (do you have snow shoes in America?). Have you seen that in the Appalachian chairs? It was pretty cool.
Hey Marc, I think I can envision the hexagon weave pattern of a gut seat. That sounds incredible on a chair. I didn’t come upon anything like it in my travels. I visited people with those skills and know-how, but I never heard (or saw an example) of this method. Stretched rawhide or woven leather were the closest that I came upon. And a few rough chairs used twine and wire.
My wife has a rocking chair that her great grandfather bought right after the civil war her grandfather put a fresh cowhide seat on it in 1937 it is still tight and is in front of our fireplace!
Andy- my copy of Backwoods Chairs just came in yesterday. I’ve been reading the PDF in the meantime to get things ready for when I attempt your three slat design. I got some MDF glued up for a bending form for the back slats but the distance of the bend from the top isn’t indicated, just the overall length. I figured this was a pretty critical part of the geometry and before I cut out the form I wanted to see if you have any recommendations.
Fitz- a couple weeks ago I asked about paint over nails and you mentioned you use two coats where I had stopped at one. I ended up putting on a second coat of General Finishes Patina Green after your comment. It looks great, added depth to the color that wasn’t there after one. I’m glad I did. Just wanted to say thank you for your time.
Hi Chris, thanks for the question. I don’t completely follow. Would you send me the page number or image number in question?
My general process was as follows: overbend the slats on the form, then relax to match the slat radius. I measured the slat lengths with the dummy rungs in place to get slats that exactly fit the chair. There’s usually a little discrepency in bending, drilling, and slat length…..so I measure for slats as the chair is coming together. Though this may not be relavent to your question/issue……..
So sorry, I said slats and meant back posts. It’s the coffin-shaped bending form at the end of the chapter.
No worries…..and nice catch. The bend is 9″ from the top of the post. We’ll make a note to include it in a future printing.
Rob – I can recommend the Kentucky Artisan Center in Berea. I was there about 2 years ago and they had a stick chair with a hickory seat. They have a website, daily business hours. I really enjoyed it. Berea is a great little town – known for folk art. And the Boone Tavern Inn is a great place to stay.
Hi Andy, I just received my copy of “Backwoods Chairmakers” yesterday and am looking forward to absorbing it cover to cover. I grew up in East Tennessee and remember chairs like these on my grandparents porch. Thanks for taking the time to write this book to share this little piece of history.
Best regards,
Lynn Barnett
Thank you, Lynn. I appreciate the note and I hope you enjoy it. -andy
Hey Andy! I keep having conflicts with scheduling the hickory bark class in June. This year it’s an Arrowmont bowl turning class. About hickory bark. I bought one of Eric Cannizzaro’s prototype chairs mainly for the hickory bark seat. The bark is so uniform and of a very thin thickness. It’s beautiful. When I have used hickory bark it has been much thicker and less uniform. Is it scraped, split or what? Oh, my print edition of your book is arriving today and I have a good Curtis story for you sometime!
Thanks Brent. I’m looking forward to crossing paths again sometime (hopefully soon). Commercial bark comes in all quality levels. Sometimes it takes hours to prep before it’s ready to go into the chair. Refined/uniform bark is usually processed futher in preparation for the chair.
This is a generalization…..but thinner bark comes from smaller diameter trees. Big trees produce thick bast that needs split or shaved before going into a seat. As you know, the mineral striations crack around the posts on the thicker stuff. I find it tough to get a perfectly uniform width when peeling on the tree. That natural wander of the knife isn’t a problem in my view….I think seats with a little natural variation look right to me. I’m almost thrown off by something too perfect. And I always appreciate a good Curtis story.
As mentioned by someone else here, a lot of the chairs you have written about are used as front porch rockers. Are the any major differences in techniques if they are intended to live outside under a covered porch?
Thanks for your time.
Good question. No, I didn’t come upon the chairmakers making decisions based on whether the chair was inside or out. Brian Boggs does with his outdoor line of furntiure and chairs….but I think we’re talking about the traditional work.
The chairmakers in Cannon County expected their chairs to receive a coat of paint. They’ll likely end up outdoors. Those chairs were made of soft maple or poplar.
Some of Sherman Wooton’s chairs have lived on covered porches for 20+ years. I helped pull the mice nests from the seat weave before photographing them. Other than the bark bleaching yellowing and the cherry fading, I couldn’t notice any issues of water or weather damage.
Hey Andy! I really enjoyed the book; congrats! While traveling, did you have any good shop visits that didn’t end up making the final edit? If so, why did you end up excluding them?
Hi Lewis, Thank you. My criteria were: 1) made ladderback chairs, 2) derived a portion of income/livelihood from chairmaking (non-hobby). Of those I found and visited, they all made the book. One showed me the door after 15 mintues, but they’re all in there. And I’m certain there’s more chairmakers working away in their shops. I just didn’t come upon them during my search. In fact, I wish I’d found more, but plenty of rumors/leads went dry before I could find the chairmaker.
Hi Andy. I just got the physical book in the mail yesterday, but have been going through the pdf for a while. It’s a fantastic accomplishment, and you should be really proud.
I’m curious — how did you end up in Waldoboro?
Thanks John. My books came on Monday. I feel proud, and grateful, to have worked on this project the past couple of years and to shine the spotlight on this tradition.
Our family has lived in a few places. We’re Ohioans originally, so living in Berea, Kentucky for four years brought us closer to our family. But we missed Maine (we lived in Rockport before KY), and came back to the midcoast a few years ago. I have a shop behind our house and can get to the ocean for a lunchbreak after a 15 minute drive.
Midcoast Maine, from Boothbay up to Bar Harbor, is my happy place. Whenever I want a break, that’s where I go.
Hi Andy,
Like the others have said, the book is simply amazing and such a joy to read.
My question is on sourcing shaker tape. My partner works with a small craft school that’s been using shaker tape on some stools and chairs. They bought a larger quantity to keep it economical, but part way through the roll, there was masking tape connecting two parts of the roll, and that joint failed on a students stool.
So the question is, do you have a recommendation on where to source shaker tape? And with the stuff they have, is the fix for these poorly joined parts to stitch them together with thread? Or is there another fix you’d recommend?
Hi Jacob,
I’m guessing the tape was only to get the correct linear footage within the roll. I’ve put in a few tape seats and I stitch at the start and when adding a new roll. Shaker workshops has been my go-to so far and I’ve been happy with the quality.
Andy,
I’ve just had a chance to browse through the physical book, I can’t wait to sit down and read it.
I know your teaching classes in your shop in Maine, but any plans to teach at Pine Croft? You know I always trying to recruit for them, since it’s close to the house.
Thanks
Matt
Hi Matt, I’ll be back at Pine Croft in Berea, KY this summer. We have a Saturday hickory bark harvesting class planned and a week long greenwood chairmaking course. I believe they’re planning to list the summer classes soon.
Hi Andy
Congrats on the new book. Can’t wait to read it. Question: how do you approach finishing a ladder back chair?
Hi Chris. Thank you. I finish a ladderback much like I finish other pieces of furniture. I scrape/sand, then oil, then wet sand with oil, and finally a topcoat/wax. I need to sand anytime I scrape a piece. I find it helpful to oil everything before weaving in the seat (especially if it’s fiber rush or cotton tape), so I don’t have to worry about running the weave with a misplaced drip and so that the seat rungs receive the same depth of color as everything else.
Hi Andy.
My copy of your book is on its way. Looking forward to reading it. Thank you for the study.
Here’s my question about your research. People in Appalachia are a much studied social and ethnic group. Their customs, music, language, and crafts are subjects of many anthropological studies, much to their amusement. There is a longstanding tradition of offfering some whopper of a tall tale to these researchers usually starting with, “Don’t tell anyone I told you this.” Did you ever hear this phrase?
TW
Hi Thomas, I know a few chairmakers had some fun with me. I was nicknamed “professor” during an early visit. But I didn’t hear that phrase. I was obviously an outsider…..and was well aware outsiders often don’t treat Appalachia well. I found often the most important part of any visit was the initital introduction and subsequent conversation. The chairmaker needed time to size me up and get a sense of what I was doing. So we’d sit and talk a stretch when I’d first arrive for the interview and photographs. A number of the chairmakers used Chester Cornett as a test. If I knew of Cornett, then I’d done enough to continue the conversation. I think it helped immensely that we shared a joy for chairmaking and that I could converse about the nuances and details of thier work. Of course, I won’t be surprised if a chairmaker got a story or two over on me, but most whoppers don’t involve chairs.
Hi Andy – thanks for taking time out of your weekend to do this!
I’ve got a long setup for what seems like a simple question… I’m still trying to form a workable mental model about how boards cup. I’m building Chris’s knockdown Nicholson bench, and I know I got this wrong on the workbench aprons, but I also seem to have some counterexamples, so I’m confused.
The easiest explanation that I’ve heard is that the board tries to bend away from the heart – that is, the curved lines try to straighten. OK, that’s easy to understand.
The rule of thumb that I’ve heard fitz say more than once is that you put the heart outside on case work. I guess I understand this as the corners want to push in towards the center of the case, so the joints at the edges of the case will get tighter, not looser. And, I guess, you hope that there isn’t so much movement that the “middle” of the edges get looser (or that’s not as worrisome).
So … now I’m making a shelf for the workbench. It’s just two lengths of 2×10 ripped to fit between the legs. They get butted together, and then some battens go across the bottom “to help keep them from bending”. But … on which side? Heart side up? Heart side down? One of each? Why? Does it matter where I put the screws?
Am I trying to have the screws pull the edges down, or keep the center from rising up, or am I thinking about this all wrong?
Hi Chris, Good questions. The fact that you’re asking it means you’re on the right path. I find with these things that being intentional is the most important aspect. So, for your example, I’d think to have the boards both cup upwards, so the battens hold down the widest parts of the top. I’d screw it with slots in the battens to allow for movement and I’d want to consider how I’m planning to use the bench (where are the vises, dog holes, holdfasts, etc. In furniture I often make cosmetic decisions (knots on the underside, best face out, etc.). So I don’t always follow a hard and fast rule, but, as you mentioned, there will be movement and I want to take that into account during design.
The top will move over time and you’ll find yourself planing it flat whichever way you go. I wouldn’t want the screws within a 1/2″ (or more) of the top, knowing I’ll be planing closer to them over the years.
Thanks for the reply! This is a lower shelf, hanging between the end stretchers, so I’m not too worried about planing down to the screws, but I will keep that in mind!
I have two questions about projects in the Anarchist’s Design Book…
1) My first question is about the staked worktable. I have completed the top and battens and am preparing to make the legs. My table top is not as long as the one in the one in the book (44″ vs 52″), but in all other respects I have followed the plans (thickness of top and battens, position and depth of battens, etc)
The problem I have run into is that I can not find any stock larger than 2″ thick, and the plan calls for the legs to be made of stuff 2-5/8″ x 2-5/8″. Would it be possible to use 2″ stock with 1-1/2″ tenons for the legs, or will this end up being too weak for the table? And if it will be too weak, do you have any suggestions how to get around this problem?
2) My second question is similar to my first, but relating to the sawbenches. I am planning to build two sawbenches and I have two pieces of poplar planed to 2″ thick for the bench tops. The plans call for beefy tops, 2-1/2″ to 3″ thick, to provide enough mating surface for the mortise and tenons for stability. Will I be fine using 2″ stock here? Or is gluing another piece 1/2″ to 1″ thick to the face of the 2″ piece a workable solution?
By the way, if anyone knows of a dealer that sells stock 10/4 or larger in southern Wisconsin, please let me know in the comments. I have asked everywhere and 8/4 is all I can find.
Thank you very much for reading my questions.
Hi Josh. I want Chris to weigh in on the leg strength question (he’ll check in later tonight). But, you can face glue two pieces to get to the specified thickness for the legs, and for the top on the sawbenches. The more meat around the tenons of those sawbenches, the better – if you plan to use them to hold up lots of weight. I have one at home with w 2″-thick top though, and I use it as a stool. While I think I weigh far too much, I do not weigh too much for the thinner-topped sawbench.
Thank you for the suggestions, and I’m looking forward to hearing Chris’s input later tonight too. I think I will face glue another piece to the bench tops to increase their thickness so I won’t have to worry later about overloading them.
Hi Josh, I’ll let Chris and Megan answer some of the specific Design Book questions. Regarding materials – I’d suggest seeing if Hood or Paxton deliver up your way. I know they have a large delivery footprint. Also, if you have a relationship with a local cabinet shop, inquiring if you can join in on an upcoming order.
You can use 8/4 stock for the legs no problem. Strength isn’t the issue. It’s appearance. I wanted them bulky up under the battens. If I were building it out of 8/4 I would experiment with using less taper (it might be a stupid idea).
Same answer on the saw benches. 8/4 will work fine.
Hi Andy, Congratulations on the book, looking forward to reading it. I was lucky to attend your weekend hand tools class at the North Bennet Street School. That class put me on the road less traveled, “and that has made all the difference”Thanks and good luck.
Very kind, Rick. Cheers.
Hi! My question is very general indeed… And perhaps directed to the community as much as the kind moderators. Given the chance, which premium plane maker would you buy? Veritas, Clifton or Lee Nielsen? All seem to be in a similar price range and I assume they all stand for great quality – so what sets them apart?
Cheers!
Familiarity, I think. I started out borrowing LN planes, so that’s what I bought as far as bench planes. But my favorite joinery plane is the Veritas skew rabbet.
Lie Nielsen- no fussy “improvements” to classic look.
BUT only offered with A-2 blades and not my preferred high carbon steel. Great no62, various block and shoulder planes. Pre WWll Stanley for typical bench planes- much more affordable!
Hi Julius. Good question. I’d second Megan’s remarks. I live two miles from Lie Nielsen, so I’m a little biased. I’ve used all of them…..all are quality, just as you mentioned. My suggestion, if it’s possible, is to hold/try a tool before committing. You may have an immediate response to one maker.
That’s close to Moody’s Diner
The gateway to Waldoboro.
We’re headed there for dinner tonight to celebrate the book release.
Hi Andy, I enjoyed stopping by your booth at Handworks in September. Beautiful chairs. My non-woodworking friend from the area who tagged along with me couldn’t believe the combination of strength and lightness.
My question is about the finish. The finish on yours seemed perfect to me — facets from edge tools but smoothed just enough with sanding. You mentioned you wet sand, something you mentioned again in comment above. I am a novice woodworker so that term (“wet sand”) is unclear to me. Can you elaborate a bit more for the rookie here — what type of abrasive (something like steel wool vs wet/dry paper), what grit, same oil you use to finish the chair?
Hi Louis, Thank you for stopping by during Handworks. You nailed it with wet sanding. I prep the chairs and sand them to 220 (not heavily, just enough to remove scraper roughness and any grain raised during glue cleanup). Then I’ll coat with linseed or tung oil. After that dries, I’ll go over it once more with 400 or 600 grit wet/dry paper (found at the hardware or automotive store). It’s a light sand with a light mixture of linseed and citrus oil – the same as before, just thinned a little more – and I dip the sandpaper in it before going over the chair. It polishes the chair nicely. I usually add a washcoat of thinned shellac, then buff on some wax. It’s a number of steps though each are quick and I love the final feel of things.
Thanks, Andy! The end result definitely caught my attention.
Follow up: Favorite wax and shellac for red oak like your chairs?
Favorite wax (right now): feed-n-wax. I’ll put it on the night before and it’ll level by the next morning.
For red oak, I usually use a darker stain….like the milk paint dark tung oil. Red oak is a little too pale if I finishi it clear. And I like to use a garnett shellac.
My premium planes sit on the shelf. My type 11 stanley 3, 4 and 5 do all my work. Original blades are easy to sharpen and the planes are lightweight. And they are cheap compared to today’s premium prices.
Hi Louis, Thank you for stopping by during Handworks. You nailed it with wet sanding. I prep the chairs and sand them to 220 (not heavily, just enough to remove scraper roughness and any grain raised during glue cleanup). Then I’ll coat with linseed or tung oil. After that dries, I’ll go over it once more with 400 or 600 grit wet/dry paper (found at the hardware or automotive store). It’s a light sand with a light mixture of linseed and citrus oil – the same as before, just thinned a little more – and I dip the sandpaper in it before going over the chair. It polishes the chair nicely. I usually add a washcoat of thinned shellac, then buff on some wax. It’s a number of steps though each are quick and I love the final feel of things.
One other question. White oak vs red oak? I know white oak is more rot resistant, which would be beneficial for porch chairs, but any other differences? Finishing? Your preference?
Sorry, Matt! I closed comment before Andy saw your question. I’ll try to get an answer from him and post it. (But me? I like white oak – the smell of red oak while working it is to me off putting.)
I love white oak. Given a preference between all things, I’d likely go for it (mostly because of the color and it’s more closed grain). But I had trouble getting white oak logs in KY….while veneer quality red oak were abundant. And it’s nearly the same in Maine. I have access to great red oak and the white oaks are few and far between. So I enjoy using red. I love how it works. It dries quickly. It takes the iron staining/ebonizing beautifully. I usually add a bit of color to the finished chair but that’s about the only difference.
I’ve experienced way more ornery white oak….poor drying, face checking, honeycombing, and brashness. But a good white oak is a joy.
Also, to Megan’s mention of red oak stink/ammonia smell. I get a good deal less of it with fresh material. And I’ve grown to like the stink.