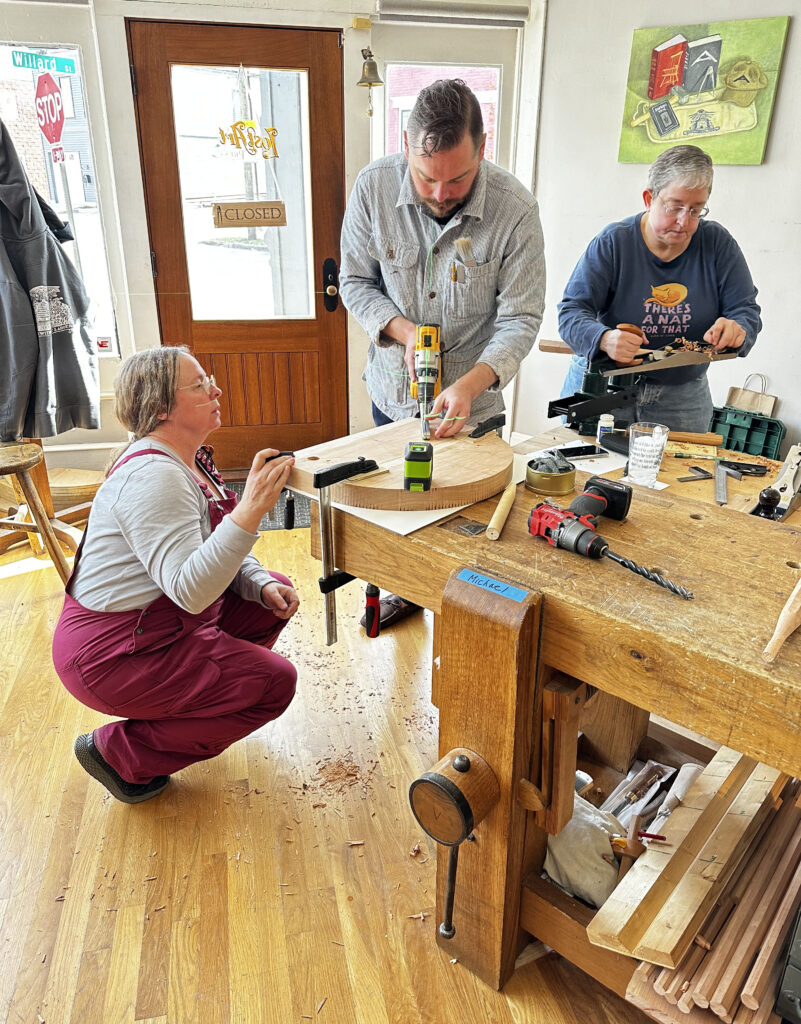
We’ve just finished a stick chair class – so I might actually be able to answer your chair questions in today’s Open Wire! (But who am I kidding – I’ll leave those for Chris.) You know the drill (with or without lasers): Leave your woodworking questions in the comments below, and we’ll do our best to answer (note that there may be a lag between your asking and our answering).
To kick things off, here’s a Jeopardy-style answer – I’ll bet you know the question: “Whatever is heavy, cheap and readily available.”
Note: Comments are now closed.
– Fitz
What is … the best wood to build. A bench with?
“To kick things off, here’s a Jeopardy-style answer – I’ll bet you know the question: “Whatever is heavy, cheap and readily available.””
I can immediately think of two questions that go with that answer.
Have you seen the brand new UK Jeopardy, with host Stephen Fry? It’s great fun.
Last i saw, Stephen Fry showed himself to be a total unprincipled jerk.
What is wood to build a workbench with.
Hi Megan and Chris! Chris after reading Ingenious Mechanicks as well as searching your blog on Roman workbenches, I am curious about something. The benches you built for the book have been loaned out or given away and you adapted a sitting bench that you had for use in your shop. What do you prefer about your current low bench over the historical designs? Length maybe? I think it is shorter. Maybe nothing like I said I am just curious.
I don’t think there’s a preference; it was a matter of necessity! As long as it has the Hulot block for shaving sticks, all good.
Did you ever try making your own linseed oil paint with eggs and pigments like the traditional way in Sweden? How did it work out?
I tend to give things away, that is the reason I had to adapt a sitting bench. I wish I had the Roman bench I copied from the Saalburg fort. It is perfection. Maybe we will do a full-length video on making and using a Roman bench, and that will be the excuse to make a new one.
Here’s a vote for the (eventual) Roman bench video project. When Chris says “perfection”, I get verrrry curious. I’m contemplating a sitting bench to get me out of the basement once Spring/summer arrives, so a “perfect” model would be a good place to start.
If you do, I would humbly offer my accessory for cutting dovetails on a low bench.
What’s the best way to learn more?
If you are talking dovetails on low benches: 1) a vise like Chris put on the Herculaneum bench, 2) an open box clamped at the end of the bench, or 3) a palm that has been changed into an L bracket with the vertical flat side extending past the end of the bench.
How is the apprentice doing? Will they be going to Colonial Williamsburg with you?
I wouldn’t call it an apprenticeship. That is a formal agreement with obligations on both sides.
She finished her first chair and did very well – one of the best first chairs I’ve seen. Next she is going to make a Dutch tool chest with Megan – so she’ll have a tool chest and learn some casework joinery. And she is feeling her way to her second chair’s design.
We are both keeping a daily journal of this process. And I hope in the next month we will have a formal arrangement.
She can’t go to Williamsburg because she has a full-time day job.
Thanks Chris. Tell her that is what vacations are for. Bet she would love it.
My recently completed DTC has developed a cupped lid on the latch side. Would fastening battens on the underneath be a long term viable option for straightening this out? When latched the lid straightens out, but I’m afraid this will put a lot of stress on the latch over time.
Yes. Wide, flat panels do tend to cup…which is why I now use battens in DTC classes. Ideally, you can put them to the outside of the case, thereby also using them as a dust seal of sorts. Screw through the lid (clearance holes) into the battens (pilot holes), screws as long as possible w/out breaking through the battens’ underside. I like oak, 7/8″ or so thick, 1-1/2″ wide.
Agree with Megan and would add: Bolting the battens with through-bolts and washers/or steel plates is a a great way to do a utilitarian (and bad-a$$ looking) fix.
You is steampunk
@fitz – Is this covered in “the book”?
Yes
It 7 degrees outside heading to a balmy high of 17, the snow is 8 inches deep, the ice on the roads is 1 inch thick. The shop is 0.3 miles from the house with 131 feet elevation gain. Should I walk to the shop? Hint: It’s been this way all week and I have perfect attendance so far.
My commute is easier. But if I don’t show up in the shop, I’ll get in trouble.
About the trouble, we’ve been out of wine since Wednesday so me too.
When should we expect American Peasant to be released?
Before June. All the projects are built. Most of the chapters are written. Next month we shoot the beauty shots in Wisconsin. Narayan Nayar, the photographer for ATC and the Studley book, is doing them. I want it to be out in April. But that is pushing it. Let’s say May.
What is the best way to clean up large shavings from the jack and jointer planes? I have a shop vac but it clogs quickly with the larger shavings. Sweeping gets to be a pain because I’m in a small work area and I have to constantly move my bench and toolbox to try to get them.
Thanks!
I have my garbage can at the end of the bench by my planing stop. I direct my shavings onto the bench. When the bench gets full, I push the pile into the can. Then clean-up is just a little bit of sweeping and vacuuming at the end of the day.
I do that too. Gravity can be your friend.
Do you have a particular technique for roughing out tapered tenons on the lathe? Thanks!
I do it with a carbide cutting tool. I have a 3″-square piece of thin plywood with a 1-1/16″ x 1-1/16″ notch cut in the middle of one edge.
Nice, thanks
Using a laser for alignment while drilling is a great idea. I am wondering how the drill is being held in alignment along a second plane. Is the person holding a bevel gauge? I can’t see clearly from the picture what he is holding.
Laser down the sightline. Sliding bevel (and spotter) for the resultant.
Is that different than previously? I remember laser along the resultant and eyeing (or spotter) on the sightline.
The addition of a laser to drilling the leg mortises is new.
Drilling the sticks is the same. Laser for resultant. Spotter to help you stay on your sightline.
Thank you!
Used this method when building a continuous arm chair in Utah with an instructor (name escapes me).
Extremely effective, and rather clever!
If you were building the Herculaneum workbench with 4 legs instead of 8, would you increase the rake and splay of the legs for more stability? And if so, do you have a suggestion for how much to increase the sightline and resultant?
There is no need to change the drilling angles when you remove legs.
Forgive me if I missed it, but did you ever deduce the reason they used 8 legs, like “Those toga wearers were brilliant when they put eight legs on this thing because …”?
Nope.
I think it’s to provide better stability in soft or muddy surfaces. Just a theory.
But don’t remove any legs. 8 legged benches are so much more interesting.
Hey folks!
I’m working on an ATC and I used ash for the skirt and dust seal, because it was heavy, cheap, and readily available (and I had some leftover from a previous project). I’ll be using General Finishes Milk Paint on it. Should I fill the grain on the ash before I paint? Any other tips?
Also, if anyone out there is afraid of dovetails, just built an ATC. They started getting pretty good around #40 and I still have the inside trays to go.
Thank you both for the inspiration, and for being the closest thing I have to a mentor.
I wouldn’t fill the grain on any project unless it was mahogany.
Unlike Chis, I wouldn’t even fill the grain on mahogany.
Hey Guys- For both. Omlets. American, Swiss or cheddar? Or other? Ketchup or commando? And toast. Rye, white, whole wheat?
Some day there will be an AI chatbot out there that know what I would order at an restaurant….
Cheddar. Sharp as heck.
I can’t eat ketchup (something in my childhood prevents it)
Whole wheat.
Cheddar. And ketchup is nasty.
What’s for lunch?
I know you recommend hide glue for a lot of reasons, but how does that work in a hot and humid environment (90° plus, 60-70% humidity)? I’m not talking about the furniture holding together, but how long it would last during a work session in my shop. Seems like I wouldn’t have much working time.
It does OK. The heat keeps its temp up (which slows gelling). The high humidity probably won’t be an issue. But glue a few blocks together and give it a go.
It is a bit hotter and humider here. I glue up my chairs (repairs) and six months later they have hide glue running down their legs and have become death traps. Next time I glue them up (third or fourth time) I will use PVA
Wow. That must be some real heat.
Hi Chris,
Not a question – just a shout-out from Ye Old Black Bull in Stratford in London, where the gang from the London Woodworking Show classes went for a pint (or two) back in November 2019.
Cheers (in every sense of the word),
Mattias
Cheers! I could use a beer right now. Even if it were a warm one.
Are there plans for additional chore coats for out of stock sizes? (Interested in Large). Thank you
We are doing one run a year. That’s all Sew Valley can handle. So it will be summer before the larges are available again.
Thank you.
Good morning. Greetings from the Canadian Prairies.
I have two questions, both related to woods to be used in chairs:
On several occasions, Chris has used ‘poplar’ in his chairs. I presume this is tulip poplar (Liriodendron sp.) rather than the various species of poplar we have around here that fall into the Populus sp. family. Can you please clarify this for me, and perhaps give your thoughts on the use of Populus sp. as a chair wood.
The second question is this: what are your thoughts on Douglas Fir as a chair wood?
Thank you in advance.
Sincerely,
Theodore Leischner.
Similar question from Sweden! I’ve gotten my hands on a load of nice thick Scots pine (2 inches maybe?). I’ve heard things about it splitting easily. Do you think it’ll hold up to 12 degree conical tenons or is it going to crack?
I use tulip poplar (a magnolia) for seats only.
Doug fir can work for legs, sticks and stretchers if it is vertical grain and has tight growth rings.
Hi Chris, I just purchased an “older” Buck in-cannel 2″ gouge with a moderate sweep. At some point someone ground the edge so it is flat (probably removed a nick) and about 1/32 to 1/16″ thick. So what do you recommend for the best way to re-establish an edge? Because the bevel is on the inside of the sweep is it possible to grind? Or is this going to be a lot of work with a dowel and say 80 grit sand paper? This is going to be used for hollowing out larger shrink pots (green wood, long grain) so it needs to be sharp but not surgical sharp. I am thinking about putting a small micro bevel in it first just to see how that works – good idea? Thanks in advance for any advice and thanks so much for LAP Open Wire. It is a tremendous resource. – Frank
Consider a Dremel with grinding stone. Use water to keep it cool.
Thanks Eric – good tip.
Inacannel gouges suck. Ugh. When I grind them I use a die grinder and a carbide cutting tool. That is the only thing that gets it done quickly.
Thanks, as always, for spending your Saturday answering questions.
I’ve been looking through the blog history and found a post from 2013 about prepping for a trestle table class at Marc Adams school.
https://blog.lostartpress.com/2013/07/01/the-dream-of-the-brown-monkeys/
It sounds like you gave students an overview of trestle table history and showed lots of examples.
Are those presentation materials something you could share or revisit on the blog?
Great question – another person looking at doing a trestle table…
I don’t have the text, but here are the images from the three presentations from that class:
https://docs.google.com/presentation/d/0B6iDY4jOXahUdHZjNUFCcGVjSk0/edit?usp=sharing&ouid=114657526184015383563&resourcekey=0-TCj5l_bD-M9ztmtJHW26wA&rtpof=true&sd=true
https://docs.google.com/presentation/d/0B6iDY4jOXahUZldGZnhiRW1hSlE/edit?usp=sharing&ouid=114657526184015383563&resourcekey=0-_0Z6RW_MIGU6S-4slGaFnQ&rtpof=true&sd=true
https://docs.google.com/presentation/d/0B6iDY4jOXahUc25CMEc2YUhCUXc/edit?usp=sharing&ouid=114657526184015383563&resourcekey=0-MV7F5WIogNM4zfak07I8XQ&rtpof=true&sd=true
Thanks! I hesitated to post a question that started with ’10 years ago you said…’ and I appreciate your tracking down the photos.
I bought a Crucible engraver this week and started looking for a pencil divider to pair it with. Most dividers seem to clamp a pencil at the very end of a leg, and the design of the engraver suggests that it would stick out pretty far and result in awkward handling. Is this correct? I’m hesitant to buy a $250 Starrett just to use this new tool to draw circles. I’m wondering if there are other options. I thinking about creating wooden circular templates that I could trace around with the engraver instead of mounting it in a divider.
Try http://www.taytools.com or Groz dividers
There are LOADS of options out there old and new. You just have to search around a bit.
Try looking for CS Osborne extension dividers
https://osborneleathertools.com/product/extension-divider-104-6-104-8/
They list for $96 but I have bought them for as little as $40.
You can trace around circular templates (I have done it). It is cumbersome, unless you are doing very large arcs. Then it is essential.
Hello, back again with a strong trunk question.
Because this trunk is for my son who is currently 4, I installed a gas spring to prevent the lid from falling on his neck. I slipped while drilling one of the stopped holes to install it and went through the exterior.
What’s the best way to fill/patch it?
I’d inlay a dutchman and match the grain (unless you can cut a plug with the perfect grain match?).
Carl can show you how: https://www.popularwoodworking.com/techniques/patching-woodworking-mistakes/
We patch errant screw holes with a toothpick and glue (for small screws) or a whittled peg (for large ones). Fixing the outside is a matter of learning to cut patches. Carl Bilderback did an excellent article on Dutchman repairs for Popular Woodworking.
https://www.popularwoodworking.com/techniques/patching-woodworking-mistakes/
Thanks so much to you and Chris for this service. Wanted to see if you had any recommendations on shellac thinners in California. The state in its infinite wisdom banned denatured alcohol and heavily regulates stuff like Everclear. I’m left wondering what I should use, and the paint stores don’t seem to have an answer.
It looks like drugstores sell 90% isopropanol, but I’d assume that has too much water in it to work effectively.
Ask your pharmacist for 99% isopropanol. I’ve moved to this without issue (from the Lee Valley solvent). Now 99 is on the shelf at my local dollar stores (Canada).
I also use 99% isopropyl alchohol for years with good results, You could make a small test batch with the 90% and see how it goes. It might be slightly cloudy but dry clear. I once diluted a pre mixed batch accidentally with 70% (not sure what % water final mix was but way more water than my normal 99%) and it was slightly cloudy, dried normally, looked the same and has held up. So a little water is ok in my experience.
Isopropanol will work as-is. There are ways to de-water it to make it nicer (freezing it). But 90 percent is pretty good.
I’m in CA, and I used the 90% isopropanol available at CVS drugstores. It worked fine for shellac. 99% ispropanol would be extremely hygroscopic, and wouldn’t stay 99% for very long.
I live in CA and feel your pain. When I’m in Nevada or Oregon or WA state, I pick up a bottle or two of 190 proof Everclear for shellac. You can legally order 190 proof alcohol in one gallon containers via Amazon for shipment to CA. I have no idea why but it is an option. If you go to the Unplugged website (woodworking blog consolidator), someone recently posted about this with more detail.
Who do you know, besides Peter Follansbee, who still regularly uses the froe/axe method to rive and hew boards for cabinets? I’m working on some (oak) logs and would love some videos or pointers on technique about how to efficiently make them. I’ve watched what I can find of Peter’s on Youtube and maybe that’s enough. Thanks again for everything you do for the community. Hope all is well. Garret
I don’t need any more than Peter’s books and videos. Sorry I don’t have a lot of resources to suggest.
If you want Gyenes Tamas’ videos, you will see him split and prep a lot of panels for chests:
https://acsoltlada.hu/index.html
Thank you, Chris!
Any recommendations for makers stamps? I like the look of the simple lettered style that plane makers use, but wonder how practical they are. Thanks!
InfinityStamps.com and buckeyeengraving.com. Chris has the former; I have the latter. Both are great.
Good Morning,
I’m building an AWB and have a couple of clamp questions. First, the vintage bar clamps have gotten pretty pricey. Rusty ones seem to be going for about the same price as new Wilton I Bars. Do you have any experience with the Wiltons? Second, is spacing the parallel clamps about 1 foot apart a good rule of thumb when gluing up the top? I want to make sure I have enough of them.
Thanks for spending your Saturdays doing this.
I wouldn’t buy clamps on ebay. If you are ever looking for old clamps, look at local craigslist listings. Go to garage sales. Follow you local auction site. Heavy iron clamps built this country and they are out there.
I don’t have experience with the Wiltons. But any heavy metal pipe clamps (old or new) will also do the job. Just make sure you alternate the bars above and below the thing you are gluing.
And spacing them about 1′ apart is a good place to start.
Good morning all. I’ve been putting off a side table (bedside night stand) project once I realized the spot I have to put the finished table is directly over an air conditioning vent. It’s in my upstairs bedroom and the ac vents are on the floor. I worry about heat warping and possibly ruining the table in short order. My shop is humidity controlled, but the house is usually humid (I live in a forest near Charleston, SC). So swings in humidity are likely. Is there something I can do to mitigate the changes in moisture content? Do I worry too much? I am using cherry and following the video Chris did with Lie-Nielsen, shaker side table. Thank you!
My guess is you’re worrying too much (but I’ve never lived in SC). But I’d add a vent deflector for your comfort, just to ensure the heat & a/c gets into the room.
I never knew such a thing existed. I will do just that. Now I have no excuse to procrastinate more. Thank you!
If you use kiln-dried stock, you’ll be fine. A lot of my early projects did some time in Charleston when my dad lived there and he never had a problem. Just take normal wood-movement precautions, and you’ll be fine.
Does hide glue really go bad?
I used some liquid hide glue before noticing it was 10 years out of date. It took a bit longer to cure but worked fine. It’s now a few years older, and I plan to do some tests, but I wonder if that’s been empirically tested already.
It can – depends on storage conditions. If in doubt, test. It takes little time or effort to add peace of mind.
It lasts indefinitely if stored well. Titebond has 20-year-old glue bottles that cure just fine.
I came across this book in a grizzly catalogue and I’m wondering if either of you have read it. Or if you all have any tales to tell about their author.
https://www.grizzly.com/products/grizzly-a-bad-case-of-capitalism-book-by-shiraz-balolia/sbbook
I have not seen this book. I have met Shiraz a few times and have found him very impressive, both as a person and a business owner. He created Grizzly out of almost thin air. He’s an amazing target shooter. He loves to make outlandish guitars. I have no doubt that the book is a pretty amazing story. I’ll have to pick it up next time I order from Grizzly.
I just secured a 33″ breadboard end on a cherry table. The tenon is about 11/32″ on a 7/8 top. I used a haunched mortise and tenon, drawbored with white oak pegs. I had a 1/16 offset, tapered the pins, had a nice fit, but they fought back. I split (no complete breaks) only the backside of the breadboard on 3/6 pegs. I didn’t notice until I was done because it was silent and didn’t splinter off. The cracks stop on the breadboard itself, the nearest one is about 1/2 from the edge.
I want to secure this to keep it from splitting wide open. I obviously don’t want to get glue on the tenon or inside the mortise of the outside pegs.
My gut says to drill a small hole to stop the splits and try to glue it. Do I just have to wait for it to fail and replace it? It might be fine for a long time, or it could bust open next Summer, but anything to put it off would make me feel better.
I’d probably inlay some sort of cross-grain patch to try to contain the split. Your simpler strategy of drilling a hole at the end of the split might be enough, however. So I’d give that a go first.
When did domed chest become popular and are there pros and cons of using them? Try to recreate a pirate treasure chest and most lore have the rounded top. Just curious.
I don’t know when those chests arrived on the scene. Very early I’d imagine. They add a complication to the construction process, obviously, but their lid prevents things from being stacked upon it (kind of like the Dutch tool chest). I am not an expert on these chests, so perhaps someone else can jump in.
Jeopardy question: “What attributes am I looking for, in a mate?”
I really don’t want to buy a laser level. But I want to build at least one stick chair. Thoughts? I tried searching the blog for ‘chairmaaking on the cheap’ but could only search by month. Am I missing something?
My sawbenches and daily sitting chair legs were bored with bevel gauge. I’ve since made these. Work fine and cheap : – )
https://blog.lostartpress.com/2022/03/10/chairmaking-on-the-cheaper-part-4-stationary-bevels/
You don’t have to buy a laser to build anything. You can use a mirror to the side of you to check your resultant. You can use a spotter in front of you to check if you are on your sightline.
What are the general dimensions of the peasants cabinet?
I’m trying to make one now, and I’m not happy with the overall proportions
Thank you very much
The one with the aysymmetrical doors? 21-1/4″ wide, 34″ tall, 9-1/2″ deep
Splendid thank you
I had not noticed the doors were asymmetrical.
This is the cabinet I am referring to:
https://open.substack.com/pub/christopherschwarz/p/a-step-forward-or-not?r=1d152&utm_campaign=post&utm_medium=web
Hi Chris, Megan,
Over the past year and half, I have started to bring a painless moisture meter to my lumber store. I’ve noticed that about a quarter of the time, I have found some boards with moisture content well into the 20 to 30 percent range. I simply get another board that is down to the low teens (moisture level when wood equilibrates where I live). It’s a nice store and they will deliver as well as plane the wood down to thickness for me for reasonable fees. I’ve mentioned it to them casually to which they look a bit surprised. Is this a common problem for supposedly kiln dried wood where you live? What would you do? I’ve seen it with several species and over time so it’s not a one off issue. I bring my moisture meter so I can avoid the problem.
Thanks,
Joe
If it’s kiln-dried wood, I think that is unlikely. Sometimes pinless meters get confused, especially when in an envrionment you can’t control. When I get a weird reading, I check the board in several places on either face of the board. I also make sure I have set the density of the wood into the meter. A board that wet would feel quite wet and cool. If the board doesn’t feel wet, then something is amiss with the reading, the meter’s settings, or the meter itself.
Thanks Chris. I do check in several places. It is a lower end General brand meter. At some point, I am going to purchase a better moisture gauge.
Linseed oil paint question: I built an oxen yoke out of laminated poplar. (I teach the oxen classes at Tillers International and thanks so much for your support, by the way!) I painted it with Allback Midnight Blue. Do you think it would be better to put an oil finish on it initially before putting it to use, or wait until it’s been used and refresh the finish later. I’m thinking of using your “shop finish,” as it’s what I normally oil a natural yoke or a milk-painted one. The finish takes a fair bit of abuse just in the normal course of working with it.
I think for items that see heavy use, I’d probably just stick with the paint,. Then add more later, as needed. The shop finish won’t add a whole lot of protection to the already tough oil paint, I don’t think.
I usually apply some linseed oil over the paint. Or, if I want more gloss, a little soft wax (linseed oil and wax)
I am currently building a cabinet out of white pine. There will be shelves that are dado’d into the carcass. Would it be ok to glue the shelves in the full legnth of the dado or should I only glue the front of the shelf to allow wood movement to the back?
Thanks!
The wood movement is likely sympathetic on the two pieces – and if so, fine to glue the whole width
What is your go to source for door hinges? Doors being aprox 15X30.
For cabinet doors, Horton Brasses. For full house doors, House of Antique Hardware
Hi, Megan! Would you be able to share the dimensions (length, width, height) of your Shaker tray? I’m interested in making one but haven’t found anything online (here, PopWood, etc.) about dimensions. Thanks!
Sure!
Two ea of:
Sides 1/2 4 1/4 18
Ends 1/2 5 3/4 11
Bot. 1/2 5 1/4 17
Ledger strips 1/4×1/4, cut to fit
But, the sizes can vary based on the wood available — so if you have scraps of something and it’s just a little short, or a little narrow, go ahead and use it!