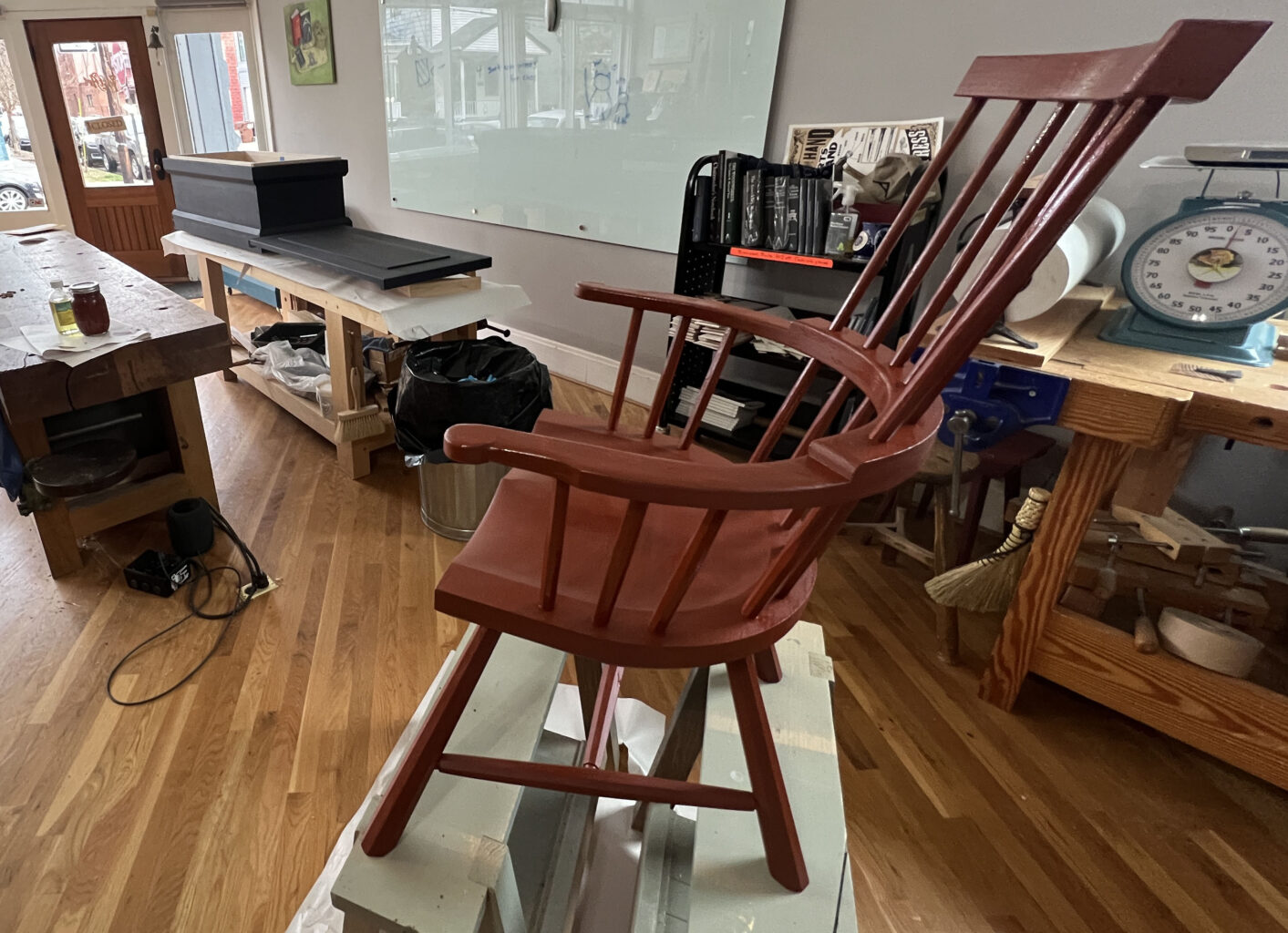
It’s time for our (almost) weekly Open Wire, where you can pose your woodworking questions in the comments section below and we’ll do our best to answer them.
Note that there may be a lag between your asking and our answering. Chris has a class starting Monday and a trip to Colonial Williamsburg for which to prepare (he’s presenting at the Working Wood in the 18th Century conference), and I have the innards of a tool chest to complete (hopefully before Monday, because my bench will be commandeered for the class).
Comments are now closed.
– Fitz
What projects do you hope to do in the future that are outside your comfort zone?
Nothing sexy…my kitchen. And this time, I’ll try to build it more like a kitchen instead of furniture.
Hello! Is it white oak or red oak for anarchists’s workbench drawbore tenon pegs? Or does it matter? Also does grain orientation when driven in matter?
If I have a choice, I will use white oak. But red is fine. Grain orientation doesn’t matter in the real work for this operation.
Kitchen cabinets never end.
Meaning… what? What are the differences that YOU see? (Inquiring minds want to know.)
AND, I should also ask… why is that not a sexy project? Why not make it a sexy kitchen?
Speak at the Working Wood in the 18th Century at Colonial Williamsburg. Public speaking is my least favorite thing. It doesn’t make me nervous, I just don’t enjoy it.
Building a stick settee. I finally have a design I like. I just need to make it.
Sorry I won’t be able to be at the conference in Williamsburg. There was an interesting discussion about the conference on Fine Woodworking’s Shop Talk Live podcast this week with Bill Pavlak and Dan Faia.
I anxiously await your take on the stick settee. I already have a spot in our home for one.
Wahoo! I can’t wait to see what your version of a stick settee will look like.
I’ve been waiting for this!
The settee, I mean.
I have some trouble sourcing (roughly) 250 bloom gelatin powder locally to try your Piggly No Wiggly recipe. Will gelatin leaves of that strength do the trick, and should I run them through a blender first?
Alternatively, I’ve found a museum conservation webshop that sells 360-380(!) bloom cow gelatin. How would this affect the recipe, do you think? If the higher bloom strength increases glue strength, might have to name my batch something else. Piggly Stuck as F***, perhaps.
I don’t know about locally, but here’s some on the unavoidable empire site: https://www.amazon.com/Knox-Unflavored-Gelatin-1-lb/dp/B001UOW7D8/ref=sr_1_4?crid=2DD3H7MWY8HSE&keywords=gelatin+powder&qid=1705151953&s=grocery&sprefix=gelatin+powder%2Cgrocery%2C67&sr=1-4
Heh, won’t deliver to my location. I’ll have to try and find a good EU brand for this. The Amazon subsites around here are absolute garbage heaps, but maybe a local forum or FB group might know a place…
I’ve had good results with the stuff that is sold at https://knochenleim.de/Hautleim/. Type 840 and type 666, specifically.
Whoa, looks like they almost tripled their prices in the last year or so. What the …?!
Thanks for this. Would never have found a site in German. But these bloom strengths are insane. Over 400?? Clearly there’s consumer stuff and whatever industrial stuff this is.
Half a kilo of this lasts me forever, so even the price isn’t that big of a deal.
Yes, gelatin sheets will work. I don’t know if a blender will pulverize them to the point where you can use the recipe by volume. You’ll need to convert it to weight (there are cooking website sites that will do this for you).
I’ve never heard of a bloom strength above 300. Might be a typo? Or I’m unaware perhaps. As the bloom strength increases, the glue becomes brittle (but stronger). I find 250 is a good compromise for joinery.
You can buy Knox gelatin via the mail and in bulk. It’s 250 strength.
Wikipedia agrees with you about the bloom strength; I need to e-mail that shop and ask what’s what. But good to know that sheets will work in a pinch. Thanks!
Good Winter Morning, in the past y’all have addressed wages related to a local auto mechanic’s hourly wage plus materials. How does one go about pricing when being commissioned to build a chair or other furniture item? Thank you.
From this Substack post: https://christopherschwarz.substack.com/p/make-money-making-things
“So I record my hourly time on projects and multiply that by the hourly rate for the mechanics at Auto Foreign. In 1990 it was $60/hour. Now it’s $125 or so. Then I add in the cost of materials. And then I make any subtractions or additions to the price. Is the customer an asshole? There is an Asshole Tax in my business. Is this a customer I enjoy working for? If so, I’ll round down some of my estimates. Did the piece eat up band saw blades? Did I get to use scrap material that was paid for by some other customer? All these things tweak the price.
“But mostly: (hours x $125) + materials.”
This is really helpful to keep in mind and is something folks can relate to; another hands on skill.
Hi Todd,
For what it’s worth, if it’s a real business, a good way to think about things is figure out your actual overhead, and then divide that by your actual labors hours per year, which will give you an hourly. This is not all inclusive, but add up: rent, insurance, web costs, shop consumables, utilities, etc for the year. Then also add how much you need to make to survive – save money, personal expenses, etc. add those numbers together and you have a big old number. This is reductive and not thinking about taxes and other things. Then assume that if you are running a business, you’re only actually working in the shop say 50%-70% of the time, so call it 25 hours a week, and call it 46 weeks a year. So take your big overhead number, and divide it by your actual labor hours and you’ll find your hourly shop rate. Very likely you’ll also find that building custom furniture is a poor way to make a living unless you’re fast, with wealthy clients. All reductive of course, but there is real math to finding what the hourly shop rate needs to be.
I am currently refinishing and am going to weave new seats in 2 rustic style ladder back chairs that I built around 25 years ago. Other than the finish and seats the chairs are still solid as they can be. I used saplings that I cut down and used them in the round. The bark was stripped off and I dried the rungs but not the post and used interlocking joinery when putting them together. You mention in some of your writings about old chairs using found wood. Have you ever experimented with this type of construction in your stick chairs?
I have used bent branches in chairs before – as the front post under the arm. Looks nice. I am drying some sticks now that I cut from a riverbank that will become backrests someday.
Chris Williams and John Porritt both use found branches to construct their arms. These usually begin life as quite big pieces of wood and are sawn down to become the arm, or a part of the arm.
Do either of you compose on a typewriter? If so, any comment on the experience? What machine do you use? Thanks!
I have recently acquired a manual machine to replace the one I used up until 1990.
https://blog.lostartpress.com/2023/01/14/thinking-like-1987-again/
I use it for thank-you notes. I might do some writing with it in the future. It’s how I wrote for many years before I owned a computer (boy am I old).
I have an IBM Selectric somewhere in the house, leftover from college. I hope to never write on it again. I also have a circa-1920 Corona 3 given to me by a friend. I might use that one for thank you notes, if I could find the ribbon, but I haven’t tried very hard – the century-old office supplies store that I once frequented is now gone 🙁
I was a high school principal in a prior life. We had an IBM Selectric sitting on the shelf in our office and a student asked my assistant what that was on the shelf. This would have been around 2008. How quickly we forget. By the way, the historian/author David McCullough did all of his writing on a pre-WWII typewriter. He said that a computer was too fast and preferred the slowness of the typewriter.
Morning! I have a go-drilla and star-m bit. I’ve had a bit of wallowing of the holes that I’ve drilled. Would dulling the sides with sandpaper help? Any other tricks? Also curious if you recommend the bbtools trident bit even if you have a star-m. Thanks again
Definitely try dulling the non-cutting surfaces and give it a go. Mostly, it’s about practice – use a slow and steady speed. Don’t let the bit get away from you. Brace the drill against your body. And drill 100 holes or so.
My review of the Trident lays out why I have them in the shop.
https://blog.lostartpress.com/2023/12/26/chairmaking-bits-extension-from-bb-custom-tools/
It’s not an either/or proposition. It’s about availability and what my students are capable of using.
When painting a piece that also has cut or forged nails, do you do anything to prevent paint on the nail heads? Some like the wrought heads from Tremont or the Rivierre are quite nice and I worry that the paint might diminish their appearance.
Megan- as it happens I’m also finishing a tool chest with general finishes milk paint – grain is raised a bit. I’ll knock it down with a 3M pad or sandpaper, but do you add a top coat on your chests? I’ve got one coat on and like the way I can still see the grain, worry that a second coat will obscure it entirely. Thanks!
-Chris
I (and Chris) paint right over the nails. The paint will eventually wear off, or you speed the process by taking it off with fine grit sandpaper (sounds laborious…faster than masking the nails!).
I don’t add a topcoat (i.e. wax or shellac or whatever) on the faux milk paint. Two coats and done (usually). It doesn’t completely obscure the grain, but it does cover most of it. So it you like the look with one coat, stop now and call it done.
I paint the heads. It’ll wear off in short order.
Good morning. What are the chapter titles for the window portion of the “Door and Window book” that y’all sell? Unless I’ve missed it (not unlikely!), the sample only has a TOC for the former. Thanks!
Casement Window Frames.
Casement Sashes
Cased Sash Frames
Vertical Sliding Sashes
Horizontal Sliding Sashes and Frame
The Bay Window
Venetian Window
I have built several replacement windows following the guidance in this book. This is the best description of traditional window construction that I know of.
What’s your experience with how long it take for the linseed oil paint to “cure” or dry?
2-3 days to move it. Longer to knock it into things. I need to pane off the top of a stool I painted, for example. I’m waiting at least a week – possibly longer – so the paint doesn’t gum up my plane.
Any plans for a make-a-Gibson-chair class?
Maybe in the second half of 2024. I ran one class in the Gibson and learned that I needed to add a drilling jig to the process and also refine some of my other processes so they are suitable for a classroom.
Hi Megan. Quick question about y’all’s drill press in the electric horse garage. I was wondering the brand and model number. If I remember right, it’s an older powermatic.
Powermatic 1150.
I have some of the piggly wiggly glue – first generation – small bottle – – I haven’t used it yet but there is a layer of bubbly surface…when I warm it up should I just mix this into the rest of the glue ?
I would use a small spoon (or something else) to skim it off. And my apologies for not doing so before sending it.
Not a problem…thanks
Just asked for hide glue at an English shop and they gave me “rabbit” glue … Same stuff? How do I make it up in small batches?
Yes. Rabbit glue is hide glue. Is it granules? Beads? Powder?
In any case, soak it in equal parts water overnight and cook it at 140° F (60° C)
Question -I plan on painting a portion of a chair seat. Just the spindle deck and the underside of the seat. The actual sculpted sitting/saddle area will reman natural. I’m concerned that the paint may bleed into the portion of the seat left natural . What type/brand of paint would you recommend. I’m hoping to gloss up the painted area with shellac toggle it some gloss. Any suggestions are very much appreciated!
I would use an acrylic (such as General finishes “Milk” [not milk] paint). They leave a very sharp line without bleeding. Tape off the saddle as best I could. Paint the deck. Remove the tape. Then scrape or sand the transition area to get it looking right.
Are you painting before assembly? I would if possible – it’ll be a lot easier to not hit the spindles that way! I’d test whatever you choose on a offcut of the same species by masking a stripe of then painting up to and over the top of the tape. Let it dry then pull the tape. That’ll give you an indication of it will bleed. But I have not noticed any bleeding on pine, red oak or linden with the General Finishes “milk paint.” That’s the only paint I have enough experience with on masked surfaces to feel comfortable saying I don’t think it will bleed. (Oh – also latex…but I don’t think you want latex here.)
Good morning!
Regarding the Trident drill bit….do you find that it makes clean exit holes? Or do you need to back up the hole with wood?
Thanks!
Back up the holes.
I’m making the Strong Trunk from Campaign Furniture. Should I tape off the recesses for the brasses before applying shellac?
Nope. The shellac won’t affect the fit of the brasses (in my experience). Unless you put the shellac on Really thick.
How does Moser spring the back sticks on their Eastward Chair?
Are you ask how they bend it to a curve? Not sure. It looks steambent to me from the photos.
Yes, the curve. I always assumed the sticks were steambent but in a recent comment from Moser they mentioned “springing” the sticks. Of course that comment could have come from there marketing department.
The stick might just be cold-bent. I do that all the time with dead-straight stock.
Their website says the Eastward stool has “a back crafted of a steam-bent cherry or walnut rail” so probably the others in the Eastward line do too.
Good morning Megan and Chris!
Thank you for doing this with incredible endurance, the open wire has become a well beloved Saturday routine for me.
Question about sharpening drill bits. I recently tried bit and brace and I really like it for certain occasions. As in Germany the flea market for used bits is small and usually you get them in horrible conditions I was happy to find newly produced FISCH drill bits jennings pattern at a big and reliable webshop in Germany. But I had to find out that unfortunately the FISCH bits lack a lot of quality consistency and even though the guys at the webshop were very helpful and supportive (and already aware of the issue) we were just able to find four diameters out of two sets that worked as it should be. The other ones wouldn’t start, or wouldn’t cut through, some didn’t cut at all. Seems as if producing the cutting edge geometry isn’t as simple as is seems in hand drill bits. The guys told me they already unsuccessfully tried to fix those bits by filing and sharpening, so having watched your sharpening series already, do you have any recommendation how to fix drill bits when the cutting geometry is way out of order? (Which would apply for new ones and flea market ones apparently)
Alternative bonus question: where do you get your hand drill bits/where do you get hand drill bits that work reliably, regular standard sharpening assumed?
Have a good weekend and all the best for your weekend missions!
Augers can be tricky. The lead screw has to be right. And the spurs and cutting lip have to work together to move chips up the flutes. When I sharpen augers, I simply replicate the existing angles on the tools. I try not to modify anything. So I’m no help when it comes to modifying angles on augers.
Have you looked for WoodOwl in Germany? These Japanese bits are inexpensive and well made. If you are looking for traditional augers, my advice would be to get them from a vintage seller. Look for NOS (new old stock), which means they have not been used. Old NOS Irwins and Jennings are pretty common (especially here in the States and in the UK).
Sorry I’m not much help here.
How toxic for users (that is, people who use the products once they are delivered or purchased) are the various finishes that woodworkers typically use: polyurethane varnish, oil (such as tung, linseed, etc), shellac, lacquer, wax, paint? I’m thinking not just of, say, cutting boards but anything.
Not toxic at all, really. It’s the solvents and driers that are toxic (for the most part).
Kelley, this article may be helpful to you.
https://www.finewoodworking.com/project-guides/finishing/food-safe-finish-considerations
Good morning Chris & Megan.
For my next chair I’m contemplating the comb-back with bent arm bow, (using the “Cold-bend” hardwood for the arms — I’m not brave enough to steam bend at the moment). My question pertains to the compression strap. This will have blocks at either end to support the bend and compress the wood. Is the distance between theses two blocks the same as the original length of the board being bent or is some allowance made for the outside dimension of the finished piece? Specifically, in the bend, is the outside portion of the board stretched, or is the inside portion compressed?
(If this was in the “Stick Chair Book” I’m sorry I missed it. I looked first. Honest.)
Good luck with your chair class next week. My week in Covington last January was the highlight of the year.
You don’t need a strap for the cold-bend stuff. Just cut it and go. The key is to do it as soon as the wood arrives.
Thinking about your design process & the way you take a deep dive into whatever subject area you are currently working on.
1) can you recommend any good online image/picture repositories of furniture (or digital books on furniture)?
2) all the pictures you take at museums – how & what program(s) do you use to organize them?
3) how & what program(s) do you use to organize your notes on all of this?
Lastly, you have mentioned there is little left for design with the more popular periods of furniture – Shaker, Arts & Crafts, etc. Any tips on how to take existing pieces of furniture from these periods and tweak them a bit to make them our own?
Find examples that speak to us, find out what they share in common, tweak those examples just a bit…
As always, thanks so much for everything that you all do!
Hi Drew,
Question 1 is like asking me where I get my ideas. It’s almost too broad for me to answer. There are some good furniture collections on the web, mostly in museums like the Smithsonian and the Rjiksmuseum (https://www.rijksmuseum.nl). I find databases to be cumbersome unless I am looking for something very specific (such as a painter’s name, or a city). General inspiration comes from visiting museums and seeing what you weren’t looking for.
If I have notes, they are also in these folders.
Once you study a furniture style a lot, you will find it easy to design in that style because you know the visual “rules” after seeing so many pieces. I speak A&C pretty well. I can design a decent Morris chair without referencing old ones. But until I was really good at A&C, I would find five of my favorite Morris chairs and use them to create the new one. Frankenchair, I guess.
If you’re interested in period furniture, look at SAPFM. They have a lot of research tools for members, with access to furniture databases at places such as the Yale Art Gallery, Winterthur, Boston Furniture Archive, Chipstone — on and on. For Shaker furniture some of the bigger museums have tons of photos of their collections. The Met has free digital downloads of out of print furniture books on their site.
There is a gazillion things out there.
Hullo, thanks for the goldmine of woodworking information that is Lost Art Press. My question is on marking out after stock prep, specifically the orientation of face edges. Is there a convention for which way the face edges should face e.g on a door frame would the face edges all be towards the middle of the door or towards the outside?
Many thanks,
The true edge should face the carcase to ensure accurate hinging. Same with the true face – it usually should be inside the cabinet.
The orientation of true faces and edges are easily understood when you think about mating parts. Mating parts should be true. So the underside of a tabletop should be true so it will meet the base (the show face does not have to be true). The top edges of the aprons need to be true because they mate with the tabletop.
Hope this makes sense. It can be confusing at times.
Plane blade and chisel sharpening guides. I have, like many, an Eclipse knock-off that works okay. It seems that the narrower the blade, the fussier my particular guide can be to provide an edge square to the tool. From The Almighty A, I bought a Saker “Honing Guide Tool- Upgraded” for $26. (It is their second generation of the tool.) It uses a wide roller to prevent side-to-side tipping, esp. with narrow tools. I’ve put a couple plane irons and a couple <1″ wide chisels onto it and so far I’m quite happy. If you depend on the tippy feature of the Eclipse style to massage away the end tips of plane blades, this Saker won’t allow for that, but that’s easy to do with a hand held stone or similar. I don’t think I’ve seen it mentioned by LAP Staff before. If anyone else can comment, great, but otherwise I think it’s worth trying. Amazon, or here, but get the Upgraded version.
https://www.smartsaker.com/products/saker%C2%AE-honing-guide-tool-upgraded-version
I’ve been using the entry level guide from Woodcraft, but I’m always fighting it’s lack of grip on my cheap chisels that are thick on the edges (but are beveled), will look at this -thanks for tip.
I use an Eclipse knock-off, and it works so much better after filing it a bit. Here’s a very helpful video, but there are more: https://www.youtube.com/watch?v=ojzzCXq5ook
A helpful suggestion showing a simple solution that significantly improves the gig. Thanks
I find that I can round off the end tips of plane blades using my Veritas sharpening guide just by exerting more pressure on the ends while planing. There’s no need for a tipping capability unless you want to create a more aggressive curved blade.
I haven’t seen that guide (there are too many to count). Looks like a good value. The only downside is the wide roller. I camber all my bench plane irons, so I need a narrow roller.
Chris & Megan, thanks for all your inspiration. I’ll be in London for an upcoming football weekend. 😉 After the game is over, what is one thing I should try to see that could provide additional woodworking inspiration.
The Victoria and Albert Museum
Chris is correct…but if you still have time, then Sir John Soane’s Museum.
Have you ever used white glue (Elmers) in your chairs? I used this in the rustic chairs I mentioned in my previous question. I think Drew Langsner used to recommend it.
Oh sure. The Elmer’s stuff is preferred by some woodworkers, such as Jennie Alexander and Jeff Headley and Steve Hamilton. It’s also PVA. Just a different formula of it. I have found that Elmer’s seems thinner than Titebond I & II. And Elmer’s doesn’t sand as easily when dry. It’s gummier.
I’m building a version of your staked worktable. I’m wondering about drilling the mortices. They are 2 inches, which is big. This means I prob need to finally bite the bullet and get a drill press…..what do you think. I can’t think of an accurate way to do the angle otherwise. If I go that route, I’d like to get one that will allow me to use your banjo jig. I can’t get sense of (1) how much power I need to drill and (2) how much physical size I need to reach the mortices with the jig on chairs and tables….I would only drill in wood (chairs, staked furniture and the like). Would like to perhaps be able to follow C. Becksvort’s advice and turn some shaker knobs as well. Do I need a 14 inch floor one, or would, say, a 8-12 inch bench top one be big and powerful enough? Thanks so much for your help.
The small benchtop drill presses have enough power to cut these mortises with no problem. It’s more about sharp tooling and holding the work steady. I’d opt for the 12″ drill press. It will have the reach and throw you need.
James,
I bought a low-end drill press meant for metal working and I couldn’t be happier. It was only about $300 more than the “equivalent” one meant for woodwork, but it is more powerful (it will turn any bit you ever want to use, including router bits), I’ve found the XY table to be so, so helpful, and a 6 inch metal-working vice is amazing. Plus, I can use it for simple work milling metal (which does pop up in woodworking once in a while).
It’s not for everyone; it does take up more space, you’ll need another 240V outlet, you will find yourself buying more tooling, etc. etc. etc., but I would never switch back.
Is there really a magic allure to sinker cypress? I born and raised in Louisiana have a local place that sells sinker cypress lumber they salvage under the water. How much of this is marketing and have you used it?
I haven’t used sinker cypress I’m afraid. Sorry!
Hello Megan and Chris,
I have two oil stones, a soft Arkansas and a Hard Black Arkansas. At some point, I lost track of which was which. Now I don’t know. I THOUGHT the black one was the one that was, surprise, all black, but I have since seen some “hard black” that were multicolor. So I’m not sure I’m using them in the correct order.
Is there any way to tell them apart? Any test I can perform? They both look and feel about the same to me, I can’t really see the scratches that either of them makes on steel, and they both seem to remove steel at about the same rate, as far as I can tell.
My tools are still sharp, so it’s not the end of the world, but I would like to do a proper hone and polish on them.
And yes, once I figure it out I will be sure to label them.
Signed,
Confused about my stones
Huh. I’d try looking at the scratches with a magnifying glass? (That’s the only way I can see them…)
One stone might be cutting slower because it is glazed. I’d try soaking them in kerosene for a coule days and then do a side-by-side comparison.
Hello to both, and thanks so much for doing this! Any advice on scooping out an ash seat? It’s so much trickier than the maple and cherry ones I’ve done before, and doesn’t look nearly as clean as the one you just posted on IG.
There’s no trick I’m afraid. Ring-porous woods are difficult. Sharpen up, take light cuts, work across the grain as much as possible.
And don’t be ashamed to sand a little at the end (I did).
Thank you!
Looking for ideas for drilling plumb holes into end grain for tool handles. I made a few new handles and their length+bit shank exceeds the max I can drop the table of the dinky cheapo bench top drill press I bought before I knew any better.
I tried a couple free hand free hand. One wallered out pretty badly and the other was ~2-3 degrees off plumb (just enough to be maddening on a screwdriver).
Tips, quick jigs, etc welcome from any source
You should be able to rotate the head of your drill press on its post. That way you could swing it over and drill into the end of just about anything. That’s what I would do.
The other option is to make a V-block jig that holds the handle you want to drill horizontal. And the V also guides the bit.
Megan,
I purchased a tool chest, 39 x 24 x 24 .I was thinking thinking of cleaning it with Murphy’s oil soap,after a through drying. I would like to treat it with an oil to condition some of
Unfinished bottom floor wood. The rest of the tills and inside of the lid are finished walnut and mahogany. What oil to condition theses surfaces without altering hue?
Thanks, DonR
I don’t know of any oil that won’t change the hue at least a little bit. Also, I don’t like finish on the inside of things, because of the lingering odor…so the trick is to find something that doesn’t stink. I’d probably go with the most purified, lightest linseed oil I could find/make. It will still add a little yellow over time.
Shellac !!! Add a pinch of gum benzoin and will smell delightful every time you open a drawer
Good morning Chris, just a quick question about a detail on the anarchist’s workbench. On the diagram on page 208 it show the planing stop located 10 1/2 inches from the end of the bench. In the text on page 219 you say to put the planing stop 11 inches from the end. Am I reading something wrong? Does it even matter? Thanks!
That’s an error. Good catch. But it doesn’t matter much. I just measured the position and it’s 10-1/2″ from the end.
After building the folding bookshelves (fun project, thank you) and trashing countless screwheads with my current slotted screwdrivers, I’m finally going to pick up some of the Grace ones. Two questions on them:
1) Chris, you seem to have the wood screw set, while Megan you apparently have the “gun care” set — any different between them (other than the price, which is a fair amount)?
2) I can get five of the wood screw drivers — #2-#10 — from Lee Valley for a decent price. How often do you end up using a #12 or #14 driver? It doesn’t seem like you can buy them separately if I change my mind later.
I don’t know what the “gun care” set is, or what the differences are. You might ask Grace. I have never used a #14 driver. I think I’ve used a #12 once.
They are great screwdrivers. Well worth the money.
I use the #12 on my chip breaker screws. It’s just the right size for those. The #14 looks nice in my wall rack.
I’ve used the 14 a handful of times. Its not one of those tools thats a must but its super nice to have when I need it.
The Grace website has been upgraded to give more detail on the various sets including the thickness of the blades in the various sets. They are great for slotted screws since they are flat ground instead of tapered; but I’m still figuring out a good system to mark them for various uses. I do use the #12 and #14 for repairing old oak office chairs that often have slotted screws under an oak cap. And if you are a purist, you can get new screws from Blacksmith Bolt Co.
Chris: I assume you are fluent in French, given that you have been translating Roubo’s work. I am curious if you learned it earlier in life or when you got interested in the historical woodworking volumes.
I am not fluent in French. I took it in high school. And I have been dabbling in it ever since we started the Roubo project about 2007. I get by OK. And with Google Translate helping me, I can produce a passable translation.
I know you’ve covered this before, but I’m feeling a need for reassurance…
Given a veneered dining table top whose finish (shellac?) is wearing through, what’s recommended refinishing? Clean with soapy water and apply another layer or two? Strip.with alcohol and a scrubber and apply shellac de novo? Other?
Yup. Just clean it. Then apply more shellac. The alcohol will dissolve a bit of the original coat and all ow the new stuff to stick.
Sounds good. Not to mention relatively easy. If I didn’t have a cat who would want to “help”, or had doors around the dining room, I’d consider just putting papers under it and doing it in place.
Hi Chris, Megan,
I have too many duplicate vintage tools. I don’t need five sets of chisels. I’d like to downsize.
1. Do you recall what are the organizations that take vintage tools and put them in the hands of craft folk who will use them? My likely route.
2. Should I decide to sell them, do you have a feel what percentage of retail value I’m likely to get if I go through someone like Jim Bode or other such as Hyoerkitten? They gotta make a living but I don’t want to get ten cents on the dollar hence more inclined to donate.
Many thanks for the help.
Sincerely
Joe Leonetti
If you want to donate, Chairmaker’s Toolbox is a good place to consider. On selling them…I’m afraid I have no idea. Sorry.
Agree with Fitz here. I know Pat Leach at Supertool also buys tools in smallish batches.
http://supertool.com/
There is also Rob Cosman’s Purple Heart Project
Hi,
I’m preparing to build my first chair. If I plan to start out with tapered leg joints, can I do all of my operations with the tapered tenon cutter? Would the 5/8 hollow auger be useful as well?
Thank you!
You’ll need a way to make the tapered tenon and the tapered mortise.
To make a tapered tenon, you can turn or shave it to shape. Or get it close and use the tapered tenon cutter to finish the job.
To make the mortise, you will need a 5/8″ auger and a tapered reamer.
This is covered in detail in “The Stick Chair Book,” which is a free download here.
https://lostartpress.com/products/the-stick-chair-book
A hollow auger will make a straight-sided cylindrical tenon. So it won’t help much with tapered joints.
Awesome, thank you. Would I be able to use the 5/8 tapered tenon cutter for my stretchers and spindles as well?
The stretchers and sticks don’t have tapered tenons – just plain cylindrical ones. Sorry to push you back to the free book, but you will find all that information there — and in greater detail than I can do here.
Hey Chris and Megan,
Hope you’re having a wonderful day 2 hopefully quick questions.
1) Somewhere Chris describes how to make hexagonal legs from a rectangular stick instead of a square stick. Can you tell me where that article or chapter is? I know I read it but I can’t find it.
2) When you make tapered octagonal chair parts do you make a straight octagon and then taper it, or do you make a tapered square and then turn it in to an octagon? I’ve done both, and I’m not sure I have a preference. Just curious what you guys like to do.
1) That is in The Stick Chair Journal Vol. 1
2) I make the sticks octagonal, then taper the flats. Both methods work just fine.
I’d like to build a bench stool for my tiny workshop and this would be my first attempt at staked furniture. I’m considering either the low staked stool or the high staked stool from ADB. My shop is only 5ft wide with 3ft between the front of my bench and the wall behind me, so I’d like a stool with a fairly small footprint (front-to-back). My inclination is to build the low staked stool and just use longer legs (workbench is 34in high). Are there any other changes I would need to consider for this design? Does my thinking make sense?
You’ll want to reduce the resultant angle if you just lengthen the legs. You might go study a high stool at a furniture store to see what angle they use for a tall stool. And they usually use box stretcher (not an H-stretcher as on the low stool). Modifying seating height is something that I usually do full-size on butcher paper. It answers all my questions about the project’s footprint.
I am approaching completion of my epic timber frame staircase. As a fellow student and practitioner of staircase construction, what is the historically correct way to celebrate, dedicate, christen, or cut ribbon for a completed staircase?
Congratulations! And, er, having not yet finished my staircase…I do not know.
I purchased the 4 Bernard Jones books “the practical woodworker.”
Popular woodwork books on bottom of spine.
Are the first four Charles Hayward books the same?
Or just similar titles?
I haven’t compared them topic for topic, but they cover a lot of the same areas – much like with 6 woodworking magazines in a 5-year period, all will run a “Ultimate Router Table” article…but the Hayward are the gold standard
I want to try out some “belligerent” finishes from John’s recent book but I’m hungup on sourcing nitric acid for the initial oxidizing. Any insights on a similar acid that is more easily sourced? From the hardware or farm supply store? (I’m in Canada and it seems they will only sell it to you as a school or institution)
Vinegar for oxidizing. Might produce a different color and take longer. But readily available. Do a test, of course. Possibly sulfuric acid; less readily available, but anywhere that sells automotive batteries. Glacial acidic acid used to be common in the wet photography days. Even if you found some, it would probably have an orange indicator dye and not much use for your purposes.
Unfamiliar with the book; on my list, but if you’re wanting to pop grain with heat on say, maple, the traditional aqua fortis method can be accomplished a lot safer with ferric nitrate crystals. Amazon sells. And if you were down here in the south, I would give you nitric acid. Stupidly got some before I learned about ferric nitrate crystals. Just walked into a chemical supply house and purchased a gallon. No questions asked. That place was in a residential area and had a phosphoric acid leak (!!!!) and eventually shut down.
Chemist here. There are some chemicals that have their effects on wood because they are oxidizers and some that have their effects because they are acids. Nitric acid happens to be both. Sulfuric acid and vinegar (which is basically acetic acid mixed with water) are acids but not oxidizers. You need to be very careful with things that are both oxidizers and strong acids. The reason that there are regulations around the sale of nitric acid is that if you don’t know how to handle it, it can make things go boom unexpectedly. (Once the Mythbusters TV show did a story on exploding overalls.) Whatever you choose, it would be a good idea to use both nitrile gloves and eye protection with side shields and to work in a well ventilated area.
Yes, my over-caffinated brain leapt over a whole section. Vinegar, iron and (for low tannin woods) tea. A different look, not a true oxidation, but might serve. I use this for boring (plain) oak turnings. The sulfuric acid suggestion was likewise uncalled for.
Thank you for real expertise. (And hopefully keeping us from blowing up.)
I am planing up some cherry for a table top and found surface checking limited to two growth rings on a board (I’m guessing the early wood, but I’m new at this). The checks are small, and not all of the lines in the images linked here are actually open. The ones that are are not wide. I can fit the corner of a single sheet of paper about 1/16″ deep. I’m guessing it’s just surface and not structural. Perhaps these two growth rings had a higher moisture content and dried at a differential rate? The rest of the 9′ board was fine. Unfortunately, this isn’t in an area I can cut around and maintain enough length. Does it seem like I’m reading this right?
https://www.dropbox.com/scl/fo/kmg1a29z2to58mfb39vzb/h?rlkey=jzhbi4y0fxdij4hbz92vofjn4&dl=0
Fortunately, I have more stock I can use, but if I didn’t, do you think there would be an issue with this in a table top outside of cosmetics?
Thanks so much!
I would have no problem using those boards for a tabletop. They look entirely cosmetic.
In a recent open wire someone expressed concern that their legs would fit appropriately and Chris said that you can make yourself confident by compressing the tenon, wedging it, and pinning it. I haven’t really heard of pinning a leg before, is that just putting in an oak peg (or maybe a nail) at an angle opposing the angle of the leg or what?
Use a long wooden peg (or a bamboo chopstick). Drill a hole and drive the pin in. Furniture restorers hate it because it makes the legs hard to repair. But if you are looking for insurance to make sure the chair survives its baby years, I will use one.
I like the “asshole tax” idea. I’ve encountered that idea at an antique/flea market venue that I’ve set up at a few times (not selling my wood work there). I have a repeat customer of my wood working that has commissioned a few pieces and a buys already made pieces of mine. I always try to give her a discount, but when she hands me the check, she always adds on a very nice “tip”.
I’ve done that. And had that done to me.
1) The instructions for the Crucible Super Woobie suggest using camellia, jojoba, or machine oil. Is mineral oil also OK?
2) Did you ever run part IV of the jack plane series from November 2019? I haven’t been able to find it in the blog archives.
Any oil is fine for the Woobie, including mineral oil.
And I think I totally forgot to do part IV. Pandemic fog, I suppose. I’ll try to look back and see.
I’ve heard of folks adding wood to the underside of commercial tops to increase mass. I want to put a commercial top on legs like the ones on the 1505 Holy Roman bench. If I can glue 2 1/8 of yellow pine, or maybe oak, to the bottom of the top, I can get the full 3 1/2 thickness, but is it reasonable to run a through mortise for the staked tenon legs after that?
If the joints between the top and the pieces that thicken it are good, then it should work. This approach is used in chairmaking all the time, especially with Alpine chairs.
I received an old stick chair from my mom that was her parents. It’s a cool chair with a tacked leather seat (like a toilet seat with a solid piece of leather tacked into the middle). The chair is very loose and needs of being glued back together. The problem my grandfather did this once already with several of the legs and the stretcher only he used construction adhesive. Any recommendations on how to deal with that? The only thing I can come up with is drilling the mortise out, plugging, then re-drilling. But that doesn’t address the crusty mess on the tennon. I’m thinking my only real option is to use it as a pattern and make a new one with the parts that can be salvaged like the leather and maybe the arms.
Sometimes soaking the joint – dunking it in water – will make most adhesives give way. (Even “waterproof” ones.) If you can get it apart, scraping the joints becomes possible. Then you can refit things. Wrap loose tenons with shaving to tighten the joints. Or plug mortises and redrill them. In any case, even if the experiment fails, you will learn a lot about chairmaking without an investment in more wood.
Vinegar helps soften most glues so you can clean the joint surfaces
Good suggestion. I neglected to mention that.
Are either of you aware of a precedent for shaping the cross section of the board to control wood movement? I am thinking of a concavity or ‘scoop’ cutting the face of a cathedral along its long axis in the hope that it might help relieve some internal tension in the board-and look cool doing it.
I can’t think of any account historically (if I understand your question correctly). I do know that there are some old timers who SWEAR that if you rip a wide panel down the middle and glue it back up that it will greatly reduce the board’s tendency to warp.
But that’s black magic.
Thanks.Just so I am understanding the language of the spell-Rip it through the wide dimension of the board like a resaw cut or through both faces as if you are joining a top?
Not resawing. Not through the thickness.
Rip it like you were making boards for a tabletop. Just glue it back together.
I’m in here waiting for glue to dry. I have to say, Chris, you have become skilled at chair making. I have most of the pieces for the Gibson roughed out and am awaiting the confidence to take the plunge. Quite possibly yet this afternoon.
Awww. Thanks Jerry. Good luck with the Gibson!
Lol
I painted a bookshelf with milk paint a few years ago in yellow. In my new house the hue just doesn’t work that well. Have you ever painted over milk paint when it’s been dry for 4 years? Any prep ideas I should know about. I’d like to paint over it with linseed oil paint, which I’ve done and it looks amazing, but it took 3 weeks to dry so I think I’ll stick to milk paint for this one. I’m planning on a blue over the yellow. I also put the Allback’s finish on top of it, do I need to sand it well because of that?
If you are going to add more milk paint, then first wipe down the piece with mineral spirits to remove any wax left over from the Allback. Then you will be down to bare paint and can coat it as per usual.
I’m about to start the base of a trestle table out walnut and have two questions:
1) my largest mortise chisel is 5/16; is that wide enough for the joinery or should I look to another method?
B. I have an 5/4 rough board I could use for the center board connecting the two trestles but it has a large crook (2” at the center of 12’). Will it be stable enough after planning straight? * it will be about 6’ long
1) You can always make a mortise larger. But 5/16″ is good for joining 1″-thick stock. Drawboring the joint will help as well.
2) A crook is a variation in width. Is that what you mean? If so, then the answer depends on how wide the board is now. If you mean a bow (the two flat ends are higher than the middle) then that’s pretty serious. Try to find the 6′ area of the board that is the least bowed and try using that. It’s kind of hard to answer without seeing the pieces and the plan.
I do mean along the width. It’s 6” wide iirc. The 2” gap I’m talking about as I set it on edge from the waddle to the floor. I’m not going off any plan per se. I started with Chris’ plan but I’m adjusting off of it for not using 2x material. The center board can be the board I’m talking about or an 4” wide 8/4 board I have.
I’d probably use the 4″-wide 8/4 board.
Megan,
I recall something about you doing an LVL bench that was fine but over time it’s started to sag; I worked on a “bench” that was 4×6 LVL’s clamped together for awhile and i’m zombifying that table in to a surface for my bench top lathe and jointer. I’ve since built an anarchist’s workbench and I’m going to do this one in a similar fashion, I’ve jointed and laminated the LVL’s for the top and I’ll tenon and pin the legs in with one or maybe two levels of stretchers and attendant shelving. My questions for you are, “should I attempt to mitigate any future sag now?” and, “do you have any quick and dirty thoughts about what that might look like?” I’m thing I shouldn’t worry about it since I just need it to be a place for some machines and shelves, but I’m still curious. Thanks and sorry this is so long-winded :]
Huh – don’t know where you read that…but mine is not sagging at all, and it’s still dead flat after 15 years. And the legs are 6′ apart or so. So I don’t think you need to worry about that.
Thanks as always for sharing your knowledge here – every Saturday I see useful answers to questions I hadn’t even thought of 🙂
Is there a plan to add PDFs for any more of Nancy Hillier’s books to your catalog? After reading the sample of “making things work” I’m looking forward to the rest of the stories, but my bookshelf runneth over…
I know that Nancy’s husband is working on getting her previous books back in print. But I don’t know any more than that.
Thanks Chris – I’d been thinking more about purchasing a PDF of “making things work” but it’d be great to have more options for her writing 🙂
How do you care, clean, and store the DMT diamond flattening stone? Anything special?
Thanks
We keep it clean and washed. And we keep it face down in our sharpening tray.
Hi. I bought the pdf patterns from the stick chair book but they keep being 3-4% too small when printed. Any advice?
I have tested those 100 ways from Sunday. They are full size. There is something in your software or printing preferences that is shrinking them.
Make sure you print window is set to 100%, NOT to fit.
25 years experience as a CAD drafter
I would like to try and make that beautiful green chair you made. It seems like a cross between your gibson but with straight sticks at the back like your other chair from the book. The arms don’t touch the sticks like they do on the gibson. Did you peg those? Any other tips I’d need to know (if you’re okay sharing?) also please make a settee video if you can. Thanks for your amazing books/videos/free tips ☺️
The green chair is a light adaptation from “The Stick Chair Book” – a free download here. Page 445.
https://lostartpress.com/products/the-stick-chair-book
I lengthened the back sticks about 2″. The ends of the backrest are coved instead of straight-angled. And the legs have some taper.
For what it’s worth I clean my diamond stone with a white Pentel, synthetic, white pencil eraser. This was at Trends recommendation – I clean the plate running water , let dry and scrub it well with the eraser – no issues so far after three years & it works well.
Any other woodworking or craft blogs/substacks people are into? I’m currently reading The American Peasant, Follansbee, Peter Galbert and Ed Sutton (when he posts 😀). All fun but would love to diversify.
Hi Megan and Chris,
I’m ready to purchase a carcase saw.
I have both crosscut and rip panel saws I’ve had for years along with a Japanese saw.
Is an 11” or 14” saw going to be my best option.
I have a bookcase and desk/work table on my project list so dados and sliding dovetails will figure into the purchase.
I know there is no such thing as you can only have one🙄😂
I like the longer ones. And they are more common (so other people agree with me).