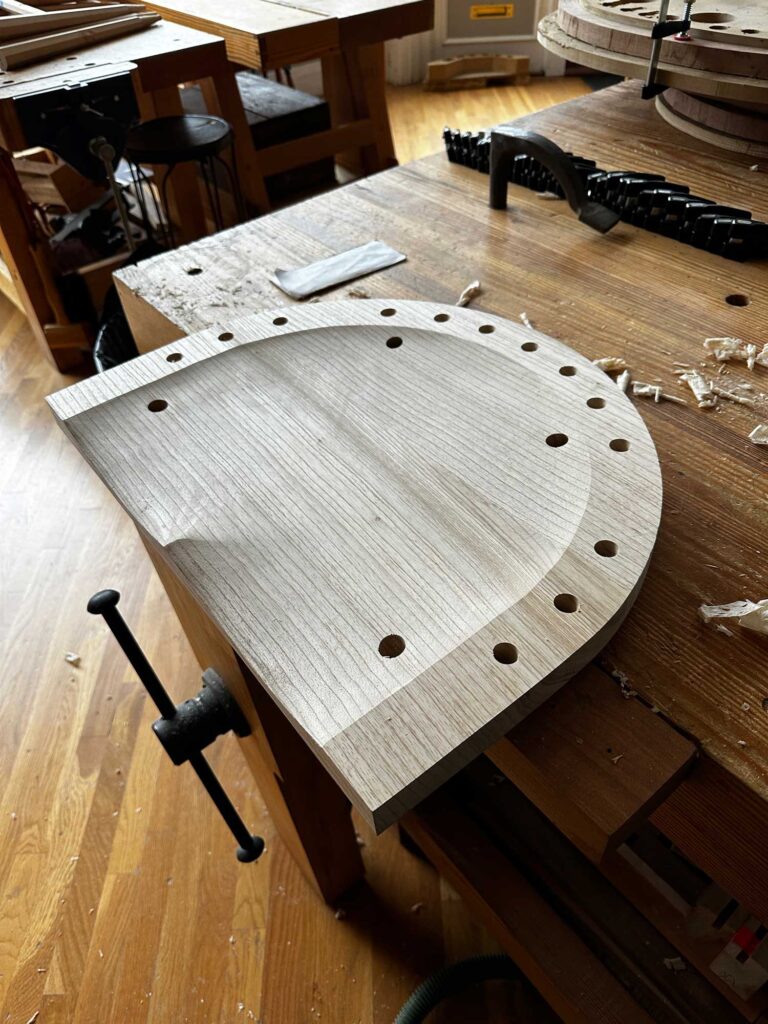
Comments are now closed. Join us again next week!
I’m writing this on Friday night. There’s a small chance Megan and I will not survive to see a new day. We ate dinner at Purple Poulet, and the food there is so rich and delicious that our hearts might simply stop.
But if we do live, we are happy to answer your woodworking questions here on Open Wire. Simply type your question into the comment box below. Post it. We will read it and answer as best we can.
Sometimes there is a lag between the asking of the question and the typing of the answer. But we do answer all questions. Sometimes we answer them after comments have been closed – it just depends on our schedule for the day.
As always, comments will close about 5 p.m.
— Christopher Schwarz
P.S. If we died, know that we died happy.
Good morning, Chris, Megan:
I’ve read that laminated benchtops have a tendency to cup. Mine has a ~1/16” cup down the middle. I read that endcaps help control this. Your opinion and how is best to fasten endcaps? My bench is 92” long so glueing and clamping is impractical
In my experience, the benchtops that tend to warp are made from one slab of wood. Laminated tops are more stable.
I wouldn’t bother with endcaps. I’d just reflatten the top with a handplane and get back to work. I don’t think the endcaps will do much.
If, however, you still want to add them, I have attached them two different ways:
1) Long (6″ to 8″) lag screws with washers.
2) Making the cap like a breadboard end and drawboring it to the benchtop with stiff oak pegs.
I need to thicken my German style workbench in order for my LAP holdfasts to actually hold fast. (It’s the infamous FWW bench from the early ’80s where the plans were published at least twice and had clever errors both times). I plan on gluing a few pieces of maple to the underside to increase the thickness by about 2 inches. Would it be better to glue 8/4 pieces side by side or to stack 4/4 pieces.
Thanks for doing these sessions, they’re very helpful and encouraging.
Hi Casey,
I don’t think it matters. Use whatever you have on hand. If you have a choice, the 8/4 would be less work/time to attach.
Would it be OK to just add square blocks at the dog holes? I’m thinking say a 3″ square, pre-drilled, and glued (epoxy?) and clamped with a long bolt the diameter of the hole. Oil the bolt, so it won’t stick and it can be driven out with a hammer if necessary (nut on the bottom). Of course if one is still adding holes, it may be better to do the whole top with boards.
Holdfasts exert a LOT of sideways pressure. I would try your scheme on one hole and see what happens. My inclination is to use bigger chunks of wood to endure the pressure.
OK, now you’ve got me started! Your advice is sound, although how big? Actually, as I wrote this, I started with a 2″ square and thought “that’s too small”, so I went with 3″. I agree a holdfast exerts a lot of sideways pressure. But that pressure is only resisted by the strength of the wood over the diameter of the hole, at most – say 1″ (my holdfasts are 3/4″ Gramercy’s). I have no idea of the actual pressure exerted by the holdfast – too many variables starting with how hard one hits the darn thing to hold the work down. But whatever it is, at the extreme ends of the hole, the pressure likely exceeds the compression strength of the wood and it deforms a small amount until the rest of the sidewalls of the hole come in contact with the hold fast and it “holds”. (This opens the holes at the top and bottom and is greater if the top is thinner – hence the value of thick tops). So, as long as the adhesive has a shear strength as good or greater than the wood, it wouldn’t take a lot of area to provide the resistance to the holdfast comparable to a solid top. The 3″ square dimension, less the hole, with glue at 2,000 psi (most are greater) shear strength is going to provide 16,000 lbs of resistance. And 4″ would be better, particularly if the thickness being added is 2″ so the force is not trying to pry off the block in bending. I’m thinking a total thickness of 4″ should be good.
For more technical reading on this, I recommend Chapter 4 of Understanding Wood by R. Bruce Hoadley. Jones’s Cut & Dried is good, but I can’t get my head around MegaPascals!
Morning guys. On the assumption that the food hasn’t cause your untimely demise, thanks for doing this!
I have a bit of a woodworm issue. It pops it’s ugly head up occasionally in my stored wood. Sometimes it’s obvious and I can cut it out and dispose, but others it’s hidden until I’m well on with planing down or suchlike. I’ve treated it (fairly) successfully with the noxious DIY store chemicals but do you have any other suggestions or less toxic (to me) treatments?
Cheers
Jamie
I’m afraid this is not a problem I have every had to deal with. We store our lumber in the cellar, which is climate-controlled. And we have our exterminator spraying the foundation monthly to ward away insects.
If I had a problem, my instinct would be to talk to an exterminator about your options. Ours have always been helpful (and practical). They don’t always recommend expensive and nasty chemicals.
I have used some old barn wood in the past to make my reproduction 18/19th century weathervanes and tavern signs. Whether I did or didn’t find evidence of woodworms, I always wrapped the barn wood in plastic sheeting, poured in two or three boxes of moth balls and let it sit for a month or two. That seems to do the trick as I never found any sawdust after that and I figured it was maybe, somewhat safer than using the bug spray. Now if I could find a way to de-worm my firewood piles, I’d be a happy camper.
A friend of mine who makes high-end furniture sprays a coat of Timbor on any wood that comes into his stash.
Two questions if I may.
I made a small side table out of pine and finished it with Osmo. It didy turn outgreat so I would like to refinish it with paint. Can I put primer directly on it or should I sand it first or is it a lost cause?
At the Purple P, did you have the famous fried chicken and which of the many bourbons did you order and approved of?
Thank you. And please remember to pop a few Lipitors to cover all the bases.
If I may take a crack- a well-sharpened card scraper may remove that Osmo from the surface easier than sandpaper. Otherwise, Zinsser makes a few water and oil-based primers that seal and prep just about any surface ahead of a paint coat. A sandpaper scuffing of the Osmo would be helpful before priming for best mechanical adhesion. I don’t know if paint right over Osmo will be successful.
My experience with Osmo is limited to some test boards. The manufacturer says it’s difficult to remove. They recommend: First wipe with their brush cleaner. Then you might need to sand to get it all out.
If it were me, I’d do some tests in an unobtrusive area on the rear of the table. Wipe down a section with mineral spirits, then see if the paint will stick to it. Try acetone then paint. Or lacquer thinner then paint. Try adding shellac as a barrier then paint.
Perhaps others here have more suggestions.
I did eat the fried chicken. The meal should come with a said dish of statins.
Hey Megan/Chris,
As always, thank you both for doing this, great source of information and appreciate y’all making yourselves so accessible!
Any tips for refinishing a repair in a surface treated with milk paint and Anarchist Daughter’s paste wax? Due to an escalating series of errors I ended up needing to refinish a smallish 1”x2” area surrounding a dowel I used to plug a hole on a very visible part of a project. I’ve tried a few times to remove the wax and apply milk paint but the repair is very obvious.
Happy New Year!
Huh. Did you wipe off the wax/oil in the area with mineral spirits before dabbing on the paint, then letting the paint dry completely before reapplying wax? Also, how old is the original finish? If it’s well aged, you might get better results by removing all the oil/wax then reapplying? But that’s a risk…
Another option is to do the repair then wait a month and see if it starts to assimilate to its surroundings. Time wounds all heels, or something along those lines…
Sorry I don’t have a definitive answer.
Greetings from Tennessee –
Per your recent post, I purchased the Rikon 10-305. It is sitting in my basement still in box.
What blade to you recommend?? Any other adjustments/fixes/add-ons you would recommend to get it in good operational form??
I bought a 5/16″ blade from Highland Woodworking. It’s a good-size blade for cutting sharp curves. If you are going to be more focused on joinery and straight cuts, I’d use a 1/2″ Wood Slicer from Highland. That is our favorite, go-to blade for the band saw. And the Rikon has enough power to use it.
There is a lot of bad advice in books, magazines, and on YouTube on setting up bandsaws and a lot of it is because people treat bandsaws like they are table saws. First, because the tires the blade rides on are crowned, the blade angle in relationship to the miter slot changes with the location of the blade on the tire and the width of the blade. So you should set your fence or jigs parallel to the blade not the miter slot. Second, blade tension and tracking are also misunderstood. On the Wood Whisperer channel Alex Snodgrass provides all the information that you need to address both. https://thewoodwhisperer.com/videos/best-way-set-bandsaw/
Good morning and happy New Year’s! I recently completed two bent arm stick chairs. The depth of the seat seems too small for me (5′-10″) but good for my daughter (5′-2″). The seat blank stated out 16″ deep but the stick to front of chair depth is about 14.5.” I want to make another chair and am considering increasing the seat depth by about an inch or inch and a half. Have you made stick chairs with greater depths and are they more comfortable?
Hi Adam,
You can add some depth, but you have to be careful about it. Once the front edge of the chair gets close to the back of your knees, things get uncomfortable for most body-types.
The depth most I would add – without experimentation – is 1-1/2″. I’d encourage you to experiment first to find a depth that works. Clamp a 1″-wide block to the front edge of the chair you build and see if that helps. Measure other chairs that you find to be comfortable. Is it really the depth you don’t like? Or is it the pitch of the seat or the height of the seat? Hope this helps.
When did flattening the backs of chisels and plane blades become the standard for sharpening? I ask because I rehab a lot of older tools dating back to the mid 1800s and most of those blades aren’t flat. Was there a different level of sharpness used by those folks? Have modern sharpening materials allowed us to achieve what previously could not be? Not trying to be snarky, just wondering how we got here.
Dressing the back of edge tools wasn’t as common before the 20th century. I have found antiques where the back had some work. But early discussions of sharpening (there aren’t many) are focused more on the bevel. There is, however, discussion of removing the burr from the backside.
If the back of a tool was finely ground by the toolmaker or even polished a bit, then sharpening the bevel is going to be enough for good work. Though the edge won’t be as durable as if both surfaces are highly polished. Also keep in mind that some antique tools were not wielded by furniture makers. They were also used by carpenters and joiners, and so their soft woods don’t require the same level of fussiness.
Getting the back dead flat is a late 20th century idea, as near as I can tell. Luckily that particular dogma is starting to fade.
Liquid Hide glue question: I used Old Brown Glue that I had not warmed enough to flow well (it was slightly gummy) when spreading. Is the joint going to be weak? I was edge joining two boards to make a shelf. I kind of had to squish the glue on the edge when spreading. The boards clamped up fine and seem to have dried ok (this was a couple of days ago). I’ve since been more patient and let the bottle warm up more. Thanks for these Saturday sessions.
It’s hard to say. It probably will be OK. If it were me, “probably OK” isn’t good enough. First I would try to break the joint without harming the wood. If the joint survived and that still didn’t make me happy, I’d heat the joint to take it apart and reapply glue.
I lie awake at night and worry about glue joints that have gone out to customers. So know that I’m a bit neurotic.
I just tried to break the joint apart (hand pressure) and it held. I’m going with “probably OK” for this because the shelf will be housed in either dados or a sliding dovetail and will end up about 36″ long. Thanks
I started reading ‘ The Wheelwright’s Shop’ awhile back, and then lost it to the ether. Could you re-post the link please. Happy New Year
I don’t know if this is where you were reading it, but it is available on archive.org
https://archive.org/details/wheelwrights-shop/page/n1/mode/2up
That’s it. Thanks.
I had the pleasure of hosting the son of a friend in my shop for an introduction to hand tool woodworking. The young man is just starting out. I showed him all the different tools and we talked about what he needed to buy first. Then we planed, sawed, chiseled, sharpened a chisel, and cut a dovetail. It was great. It makes me want to do as you are doing to hire, not so much an apprentice, but a helper, a young person who needs a part time job and who would learn a little woodworking in the process. We live in the second poorest county in Tennessee and the poorest is 10 miles east. This could be great, but there are risks and liabilities. How do you handle liability insurance and tax withholding for your part time apprentice? I have lots more questions about this but just the insurance and tax question for now.
For liability, I have an umbrella policy. Any injury that happens on your property is a liability. No waiver can deflect that (that I know of).
As to money, you should talk to an accountant. Some would pay the person as a 1099 contract employee, but if the person is working in your shop on your equipment and at your direction, that might not be valid. A 1099 contractor doesn’t have as much paperwork and headache as a W-2 employee. But there are rules….
Here’s an explanation: https://squareup.com/us/en/the-bottom-line/operating-your-business/1099-vs-w2-which-do-you-want
My goal with an apprentice to fulfill my obligation to the craft. I am giving her all the knowledge I have for nothing in exchange.
At some point, she might come work for me. If so, then I’ll either make her a W-2 employee, or a 1099 contractor, depending on the work arrangement.
In many shops, people are paid in cash under the table – with no reporting. This is risky, but it is very common. Other people work out a trade. My father provided medical care to people in our poor community growing up and didn’t charge them. At Christmas, we would receive chickens, produce or even housecleaning services from his patients.
Good luck!
I’m not an under the table kind of person. This type of work situation is a gray area for insurance. I don’t think I could get a small business type of liability policy without being a small business. I currently have a residential homeowner’s policy which might not cover injury to or damages caused by a helper who has regular scheduled hours and wages. I don’t know. As for taxes, I am pretty sure it would it would amount to more than $600 estimated annual remuneration and would require require a W-2. Probably, withheld income tax would be zero but Social Securty/Medicare would not. Being a well meaning person is hard.
Small business bookkeeper/tax preparer here and I deal with this all the time. W2’s have nothing to do with how much a person is paid in a year; it’s all about how the job is structured.
As Chris stated, if the perosn is working in your shop, using your tools, under your direction and during the hours you dictate, they are an employee and need to be paid as such, with you paying and withholding all the taxes and the like.
A 1099 contractor is someone you hire to work for you, at your location or elsewhere, using their own tools, under their own direction, during the hours they decide on, etc. You would need to get a W9 from them, no matter how much you pay them, and issue them a 1099-NEC if you pay them more than $600. I recommend issuing the 1099 regardless of how much you paid them just as a CYA.
In your stated scenario, you’d have an employee and you likely need to register as a business, which can be as simple as a sole proprietorship. There are all kinds of registrations and forms you have to file, and fees you have to pay, as well as the various employer taxes. Many people try to get around this by calling employees contractors (I worked for someone who did this, eventually turning them in), but it’s illegal (for very good reasons) and the penalties can be severe.
If all you’re looking for is some shop help and to pass along knowledge, and there must be some kind of compensation, your best bet is barter of some kind.
Another option is to have your helper build something they want and allow them to keep it in exchange for help time. (Bartering). No money involved. They can sell if they want. Homeowners insurance should cover them as they are “visitors”.
Thank you as always for the advice!
I have recently nearly completed assembly of my first stick chair. When gluing and installing the arm bow one of the short sticks developed a small crack near where it inserts the seat. I’m not sure if there was some run out of grain I didn’t recognize or if I got that angle really far off and the stick wasn’t strong enough. It is about an inch long and I wondering if/what you would do to repair. The crack is not centered in the stick but maybe in the outer 1/3 and facing the inside of the chair where I worry it could catch on clothes or get worse. I know hard to answer without seeing, so maybe just advice on if you have had this happen and approaches you would consider.
Thanks and Happy New Year!
If you can get some dental floss in the crack or a hypodermic needle I’d get some glue in there and try to clamp it shut.
If you can’t get any glue in there, I’d try to ease any sharp edges that might grab a sitter and watch the crack to see if it gets worse or not.
Is there any reason that the benches in Ingenious Mechanicks should not be built out of laminated SYP? I’m interested in trying one (or all) but I’m not ready to take the plunge with a 3+ inch thick slab.
Thanks!
The Roman bench I use now in the shop is made of laminated SYP 2x12s. I say go for it.
Thank you! I appreciate the response. Happy new year!
Does it matter which way the boards are oriented?
Have the heart side of one board kiss the bark side of its mate. That way if/when they cup they will stay together.
Good Morning Chris and Megan. So happy to see you made it through the night!
A question about drilling the back sticks for the Gibson chair. Is there a reason you switch from the bit used for the seat mortises (wood owl auger bit in my case) to a spade bit? Is this in order to get the length of shaft needed to easily line up the holes using the back rest template? Or something else?
Hi Ania,
You need the extra length to in order to drill through the pattern that’s screwed to the top posts. The easiest/cheapest way to do that is with a spade and a bit extension. I don’t know of a bit extender that would work with a WoodOwl auger (though I’m sure it’s out there).
Your ash seat looks amazing. I am still gathering the needed tools for stick chair making, but it’s winter so I have time. I scored some 8/4 birch and ash last year that was free and it’s beautiful. The birch is easy to work, I made a 3 legged stool from it for my daughter. My question do you have any tips for building a stick chair with ash? Since it’s super heavy and dense I wasn’t planning to make a chair with it, but now that I see your seat I definetly will be making one.
Ash is a fantastic wood for making chairs. Very strong and flexible. The only caution is to use a thick seat so it is less likely to split when you drive in the legs. This one is a full 2″ thick (with a strong underbevel).
I am still looking to buy some chair making tools, specifically the power tenon cutters (5/8,3/4,1). Question do you think its ok to drill the seat leg holes with a drill press and make a straight 1″ tenon for the legs or you would recommend the using tapered reamer for this step? The torque on my wrist doesn’t excite me for this part and I have a nice drill press. I think this is the one step in chair making you could use the drill press on.
Chris has written before that the drill press “banjo jig” (see Anarchist’s Design Book) that he uses for shallow resultant angles is not so great for the extreme resultants he uses in some chairs. If your angles are less extreme and you can figure out a way to hold the work, the drill press will work.
I bought Sharpen this. Both the book and video.
Good morning! I need advice about some red oak that is coming unlaminated. On one 8’ long apron for a dining table I’m making, the flat sawn 7/8” thick apron is bending towards the middle of the table along its length. At several points on the inside of the cup (the outer side of the apron and bark side of the board), the tip of a layer of grain protrudes from the apron’s face with a splintered point that grabs the hand if run against the grain. The cupping disappears when the table’s middle cross-support is inserted during a dry fit, but that doesn’t fix the splinters. Planing and card scraping only seem to move where each splinter starts. Should I sand instead? I tried to smother the tips in Timbermate before finishing with Tried & True, but they poked through. I can’t change the apron’s orientation because it already has interior mortises for buttons, but I’d love to keep this board to ensure it matches the rest of the table. If there are any recommendations about taming these splintering spots, I’d be grateful.
Thanks to Chris & Megan for this generous use of your weekend time!
I’ve had similar problems with flat-sawn floorboards, and managed to fix one – for now…no guarantees on long-term…. I used a syringe w/an 18-gauge needle to get a lot of thinned PVA in between the delaminating layers, then put down a piece of waxed paper, topped w/heavy sh&t for a few days. I had a bit of a mess to scrape off the top afterward, but so far it’s stopped snagging my socks. So I’d try a syringe and thinned glue, clamping the repair with a flat block atop waxed paper across entire repair area to evenly distribute pressure. And leave it for a few days. And cross your fingers.
Chris might have other suggestions when he gets back from his Saturday morning walk.
Just finished a Windsor in milk paint and soft wax. Looking back, I should have done another coat on the seat before wax. How would you strip back? Sand to bare wood and start over?
Mineral spirits to remove the soft wax. Then test a small area with paint to make sure you got all the oil/wax up. If not, more mineral spirits. You could also add a spit coat of blonde shellac, then another coat of paint.
In your book Sharpen This (and the video) you don’t talk much about bevel up irons. What angles do you recommend for grinding and honing the iron for a block plane like an LN 60-1/2?
Also, is there a story behind the middle finger sticker that comes with the book?
Thank you.
I use the same grinding angle (25°) and honing angle (35°) for bevel-up tools.
The story behind the middle finger is told here:
https://www.highlandwoodworking.com/sharpening/christopherschwarzhandtools.html
There are two parts. The link to the second part is at the bottom of the page.
I gave this speech at a Lie-Nielsen Open House but instead of saying “Sharpen up or shut up,” as I do in the article, I said “Sharpen this” and flipped off the crowd.
That led to a sticker. And a book.
What is the cleverest small space workbench you’ve come across?
The milkman’s workbench attached to a kitchen cabinet.
It’s been a year since you gave your readers an update about the goings on with Roy Underhill. Any update you can give on his plans would be most welcome.
We haven’t heard much from Roy. He’s coming to teach here in 2024 and we hope he will fill us in. I suspect he is enjoying his well-deserved retirement
I recently bought your glue and want to start using this in place of PVA. I read that your glue is very strong and results in wood breaking, in place of a glue break when placed under stress. My question is, have you done any tests or have any thoughts on how it would do under really large glue ups like building a workbench (laminating the 4” thick top) or a table top glue up with 2” thick pieces? Thanks – Joe
No we haven’t tested that specifically. But we use it to glue up 8/4 all the time and deep mortises in high-stress situations (chairs).
I would have no problem using it for a workbench, though it would be considerably more expensive and slower than PVA. For big laminations such as a benchtop, I usually use PVA because it’s cheap, fast and reversability for repair isn’t an issue (it’s a workbench not a guitar).
Hope this makes sense.
Good morning Chris & Megan
I’m looking to replace the wood jaws of my carvers’ vice. I can handle the wood pieces, but to you have an idea where to source the soft rubbery material?
Best wishes for a safe, healthy and Happy New Year
Item 1867T27 at McMaster-Carr – medium-hard Semi-Clear to Opaque Adhesive-Back Sheets.
https://www.mcmaster.com/catalog/129/4023/1867T27
Good morning. Woodworking adjacent question. Some time back you were selling these t-shirts.
https://blog.lostartpress.com/2021/06/04/new-and-way-better-t-shirts/
This is one of my favorite t-shirts. Can you share the name of the t-shirt manufacturer? I’d love to track down some additional shirts.
Thank you,
Joe
Here you go:
https://usabayside.com/product/2905/
Available retail here: https://usblanks.net/collections/mens-t-shirts?sort=price-ascending
In a recent Piggly No Wiggly post I noticed a Waage heating pot in a photo. With a low temperature of 150F, is one of those suitable for use as a shop glue warmer, or will 150 degrees cook the glue?
Ours does go below 150° F – though the scale on the setting dial is off. So we used a cooking thermometer to set it, and simply don’t move it. But 150° won’t kill the glue – just don’t let it get much above that or it can lose strength, I’m told. (I have not personally tested that statement, but I usually believe Chris.)
In your book “Sharpen This” you mention pulling the blade and do not mention pushing the blade back up the stone. I take this that you do NOT recommend pushing. Correct? Why? Comment please.
I don’t consciously lift the blade when I push it forward…but I do ask students to if they’re using my waterstones (and we have diamond stones in the student kit…I try to not share my personal stone anymore). It’s easy to inadvertently dig into the stone when pushing the blade forward. But if you’re comfortable keeping even pressure and not digging in, you don’t need to lift up on the return/push stroke. And even if you’re not keeping even pressure and are digging in, they’re your stones 😉
Thanks! I also thought about digging in and now I am very of aware of that. So far my waterstones have survived unscathed.
Do you have favorite brushes for painting chairs, and do you use the same brushes for General Finishes “milk paint” or linseed oil paints?
For “milk paint,” I use a nylon/polyester (this one, these days…https://www.woosterbrush.com/products/ultra-pro-firm-brushes/). For the linseed oil paint, I admit to being a terrible person…I use a china bristle once and throw it out (this one: https://www.woosterbrush.com/brushes/yachtsman-brushes/). That costs far less than the time it takes to clean it. I should use good china bristle brushes and suspend them in linseed oil for the next use of the same color, but we don’t have the room for that.
A better but still relatively inexpensive brush for linseed oil paint, says Travis at Heron Paints, is https://www.jerrysartarama.com/global-arts-escoda-natural-chungking-bristle-brushes
And perhaps Mattias can weight in here. He used a lot of linseed oil paint and gave me some gorgeous brushes that he recommends…but they’re too pretty to use until I get better at cleaning them.
I can indeed, Megan! The brushes I gave you, that are the same that I use myself, are from a small Swedish brush making company called Gnesta-penseln (Gnesta is the small town on the outskirts of the Stockholm where they are located, pensel means “brush” and the final “n” is the definite article, so the name translates as “The Gnesta Brush”).
At least some of their brushes are available in the U.S. from Atlas Preservation. My favourite is the one called Oval Brush (#5530), but I have also had very good results and experiences with their models #309 and #609 (“All-round Brush”).
And yes, they are expensive. And worth every penny. But at that price, you should indeed take care of them, as Megan says, either hy storing them in raw linseed oil between sessions, or by cleaning them with linseed oil soap. Typically I would say it takes me between five and ten minutes to clean a brush – they get really loaded with paint, which is of course one of the reasons why they are so good – but the good news is that with just water and linseed oil soap, they get really clean, as do your hands. ‘Tis soap, after all! (These remarks of course only apply when the brushes have been used with linseed oil paint. For other paints, other cleaning regimes will apply.)
There may be other distributors in the U.S. than Atlas, but they were the ones I found through a quick Google search. Oh, and when their website says these brushes are good for “ironing carpentry”, I suspect the blurb in question was machine translated from the Swedish stryka snickerier – the verb stryka can mean several things, including “to iron” (as in clothes) and “to apply something with a stroking motion”, for example paint.
(I wrote more or less the below answer an hour or so ago, but it never showed up; I may have hit the button in the wrong way or whatever. If it turns up after all, apologies for the double entry posting!)
As I was trying to say already, Megan, I can indeed! The brushes that I gave you, which are the same that I use myself, are from a small Swedish business called Gnesta Penseln (Gnesta is the town, south-west of Stockholm, where they are located, and penseln means “the brush”, so “The Gnesta Brush”.)
In the U.S. they are available from at least (Google, and ye may find yet other sources) Atlas Preservation. My favourite is undoubtedly the Oval Paint Brush (#5530), but I have also had excellent results and a good experience with the All-round Brush (#309) and the Moddlare brush (#609). Moddlare by the way is the usual Swedish term for a wide, flat brush.
And yes, they are expensive. And yes, I find them to be worth every penny, not least as they get better with use, provided that you take care of them, as Megan rightly says that you should! With inseed oil paint that means either storing the brush in raw linseed oil between sessions, or cleaning them after use with linseed oil soap. It usually takes me between five and ten minutes to thoroughly clean a brush after use, but is not difficult: just work the soap in between the bristles, rinse with water, and repeat, until it lathers and rinses clear. Plus you’ll have nicely clean hands – ’tis soap, after all! Again, this only applies to linseed oil paint; for other paints, ’twill be whatever is the correct procedure for cleaning a particular type.
What I love about them is that they load and hold paint fantastically well, and have just the right amount of give/resistance, which makes it easy to apply the paint very, very thinly (as one should with linseeed oil paint) but still get a good cover.
Oh, and when the Atlas Preservation website says they are good for “ironing carpentry”, I rather suspect they have taken a Swedish text through Google Translate or similar. The Swedish word for “ironing”, as in ironing clothes, is stryka, a word with many meanings, including “to apply something with strokes”, for example paint.
Hi Chris, Megan: Thanks as always for providing these Q&A sessions! I’m about to start building some short stools per the 4-legged one in ADB. I only have access to kiln-dried wood, and purchased some 8/4 ash which appears to be straight-grained in the visible sides, but probably won’t be as straight as riven green wood. In addition to using a mallet to test for brash wood, is there something I can do to test the legs prior to glue-up?
We use kiln-dried all the time. If the grain on the edge is straight, that’s great.
Can you share the drill settings (or range) you typically use on the Dewalt drills for each drilling step of building a stick chair — legs, reamer, tenon cutter, sticks with spade bits, etc? Also, is there a chance there will be another chair chat class in the future?
Hi Max,
The drill settings depend somewhat on the materials.
5/8″ leg mortise with WoodOwl. Slow or medium speed, clutch off
Tapered reamer: Slow speed no clutch
All spade bit operations: fastest speed no clutch
Tenon cutter: slow or medium speed, no clutch
And I don’t think a Chair Chat class is in the cards right now, but Rudy and Klaus might come to LAP this fall to offer some other classes.
Who did the artwork in your previous post (query season)? Its very nice.
A local ceramics artist, Sara Horn. Chris commissioned that gorgeous tile of the LAP building for Lucy for Christmas.
https://www.sarahhorn.com/
Perhaps others have asked and you have answered. If so, apologies. Do you sell a wood pattern template set for the stick chair that is made in your stick chair video?
Full-size patterns for the seat, arms, shoe and comb of the chair come with the video; they can be printed out at any copy shop, then adhered to ply/Masonite to make your own templates.
I’m fairly certain the patterns for the six-stick chair in the video are slightly different than the one included in the patterns for “The Stick Chair Book” (https://lostartpress.com/products/full-size-patterns-from-the-stick-chair-book) – but that one (pg 484 in the book, which is a free download: https://lostartpress.com/products/the-stick-chair-book) is pretty close.
Good morning. New here. Thank you for running a Q&A like this – it’s nice to have.
I’m building a low bench and I’m reading a couple of your books for inspiration. After using them for a while, what’s your mileage like with the dovetail side notches? Are they useful on a regular basis? I’m after something useful to work on (I have limited space) and my instinct is to skip them – but maybe I’m missing something?
You can always easily add them later if you decide you need them. The low bench in our shop does not have them (it has a twin-screw, like the Herculaneum bench from “Ingenious Mechanicks”). But we typically use the bench mostly for planing sticks, with a “Hulot block.”
That bench was loaned to a woodworker in Northern Ohio and I don’t have any feedback from him about it. Sorry.
Got it. I’ll see where things take me. Thank you!
Happy New Year!
I have a question about a staked leg desk I’m making. The design is similar to Work Table in chapter 10 of the Anarchist’s Design Book. The desk will be made of cherrywood and the dimensions of the desktop is 1 13/16” x 17 x 53 ½”. The legs are 1 ¾” in diameter and about 30” long. The leg ends are tapered to approximately 1”.
My wife does not care for the thick battens that attach the legs to the top in Chris’s work table. My desktop, being 1 13/16 inches, thick do you think I can attach the legs directly to the top. I will have short stretchers between the legs at the ends and one long stretcher connecting the back legs.
Personally I love the battens but I need a compromise or this project is doomed.
Thanks Bob Koch
You’ll probably be fine attaching the legs to the top directly as long as the joint is good and the wood is strong. You might consider a short batten (invisible to sitters) that thickens the area around the mortise and tenon.
I want to make a set of dining chairs. I’ve used floating tenon construction before, and now I’m considering stick chairs. Have you used your methods to make bow backed, un-armed chairs?
“Backstool” in our lexicon: https://blog.lostartpress.com/2015/02/28/the-second-staked-backstool/
https://blog.lostartpress.com/2017/09/21/other-anarchist-designers/
Not bow-backs – that’s a Windsor chair construction. We make backstools. We use a backreast and spindles. Search for “staked backstool” on our blog for photos.
Good morning.
I started building a little shepherds coffer yesterday based off your plans (more or less). I’m using my no48 for the T&G’s for the top and bottom of my boards, then using a rabbit plane for the end grain tongues. It’s working out good, just slow. How did you go about that? Thanks a lot
Not sure what the question is here. I used the No. 48 for all the tongue and groove joints, including the end grain ones. For the end grain ones I used two strategies to get rid of the spelching. 1) starting with a panel that is a little over-wide then ripping off the spelch 2) clamping a sacrificial block to the outfeed side of the panel to take the spelch.
Yes, the end grain is slower than face grain, but not terribly. Hope this answers your question.
Morning Chris & Megan,
Glad to see you survived the night. I’ve been woodworking for 10ish years now and I’m happy with the way things are turning out. I make Shaker style furniture mostly right now. Could you please opine on acceptable tolerances when working with hand tools? The only curse to working alone in my shop is not completely knowing when I am chasing my tail for a level of square and flat on the two reference surfaces. I don’t think I am but always kind of wonder. Same with diagonals and measure for square, what do you call as good enough on furniture? Many thanks.
Sincerely,
Joe
That’s a personal problem. I always tell folks to work to the level of their own satisfaction. But I do shoot for square…because anything that comes after gluing up a carcase relies on that (or causes a lot of extra work if it’s not).
I have a decent plank of eastern white pine that I plan to carve for seats, but it has some small black knots I can’t avoid. The plan is to paint. Nevertheless should I reject it?
Hey folks,
I’m starting a small hand tools only shop and need to build a bench. I’m interested in finding some 18th and 19th century Patterns that are distinctly German, if such a thing exists.
I’ve considered using a commercial top sold by Garrett Wade about 30 years ago. It’s made of Rhodesian teak. The undercarriage is a joke so I’m thinking of building a new undercarriage from scratch.
I’m not at all sure I know what I’m doing so any advice would be appreciated. Maybe I should just build the whole thing from scratch. I could send pictures of the top if that helps.
There are lots of forms of “German” workbench. A very good example is here:
https://blog.lostartpress.com/2016/07/13/workbenches-from-the-empire-of-germanyholy-roman-empire-and-etc/
Also, the earliest Roman bench is from Germany. And early German workbenches were like staked tables:
https://blog.lostartpress.com/2021/03/23/workbenches-1st-15th-centuries/
And then there’s the Loffelholz workbench (covered in detail in “Ingenious Mechanicks”:
https://blog.lostartpress.com/2016/08/27/the-unusual-face-vise-of-the-loffelholz-workbench/
This is a HUGE topic that is well beyond the scope of a reply. My advice would be to dive into the research or just pick a German form that appeals to you and the tools you have and get to work.
Two questions re the Gibson chair video and template. 1) It looks like one of the back sticks is very close to one of the legs on the underside of the seat in the video. I was thinking of shifting the rear legs slightly to the side and will be building half-scale model per No-fear Chairmaking. What are the rake and splay for this chair? Alternatively, I think shifting the back legs rearward along the sight lines by 1/2 to 5/8 might work as might drawing parallel sight lines outward from those for the rear legs. Bot options would preserve the rake and splay. 2) The post mortise for the back post ended up pretty close to the edge of the arm because of the rake of the back post. Any suggestions for getting it slightly more centered? I plan to add the extra piece to the underside of the arm to reduce the chance of cracking.
Glad you survived dinner and thank you for being available for questions, John
1) What are the rake and splay for this chair?
I don’t know the rake and splay. But the sightline is 50° and the resultant is 25°.
2) The whole assembly locks up tight when it’s together. So the hole in the arm isn’t a huge deal. But if you want, make the arm wider at the back to provide more meat around the post.
Thanks, I’ll figure out the rake and splay from the half model, I’d kinda like to know anyways so I can start calibrating my brain. With just the sightline and resultant there are any number of combinations of rake and splay per the Chairpanzee.
Hi Chris and Megan , I plan to build a stick chair for sitting on while playing acoustic guitar . I use a Staked Tall Stool now , but its a bit high and I need some back support . I was looking at the Staked Chair design in the ADB . Perhaps using that general form but with a level seat and a near vertical backrest ? Any thoughts , suggestions appreciated .. Regards
It’s a good design for playing guitar. You might consider widening the seat a couple inches and saddling it so you can play for longer times.
A guitar chair will be my third chair. Right now I’m using a discarded secretary swivel chair with the seat set to its lowest position at 16 inches, but it is padded so probably closer to 15 1/2, and the back in its lowest position which starts 1 inch above the seat. Even when seated I play with a strap and the lower bout of the guitar shifted over my right thigh, I’m right handed. I also nestle my left heel against the top roller of the left front leg which is very comfortable so I might add something to the front left leg to simulate that.
Hi Peter. I have been thinking of this for some time. I build acoustic and classical guitars and would love to offer a guitar, or musician’s, chair designed specifically for playing while seated. I have only seen one other in the wild. My thought was something along the lines of what John Brown called a library chair, or the Irish chair in the stick chair book. Low back that wraps slightly around with no arms. There could also be an integrated footrest on one or both of the front legs. Here’s an interesting three legged version https://americanmusicfurniture.com/shop/seating/george-nakashima-woodworkers/mira-musicians-chair/
I would love to hear more if you end up making something for yourself.
Sorry, I said Irish chair, but I was thinking of the lowback stick chair from the stick chair book – modified by shortening the arms to provide room for an instrument.
Your sequence for making chair legs/tapered octagons out of square stock is to make octagons and then jack plane the tapers. Have you ever tried cutting the tapers first on the square stock (with the band saw) and then jack planing the corners to make a tapered octagon? Probably just a matter of preference/comfort but was curious if I was missing something.
Do you have any recommendations for how to handle curved cuts like the seat back in the Gibson chair video without a band saw? Looking at the Stick Chair book, I see the band saw under “essential tools”, but I wonder if there is an another approach I could use to make do until I can get a hold of a band saw. Thanks.
Frame saw (e.g. a bowsaw)
When mixing shellac flakes, ever clear is preferred. That’s ethyl alcohol. However, for those who live in areas where they can’t buy that high a proof, is Isopropyl alcohol an acceptable substitute? Obviously not the normal 70% stuff found at drug stores, but purchasing the 99% online? Isn’t the alcohol just the solvent/carrier and once it flashes off it’s not bringing anything to the party, as it were. Correct?
The topic came up recently when talking with another woodworker and I just wanted your thoughts on it. Thanks!
Cheers,
Dan
I’ve used isopropanol without a problem. I think anything that suitably dissolves the shellac will work equally well.
What’s your preferred method for trimming larger tapered octagonal legs (e.g. ADB staked high stool) so that they fit into the tenon cutter? I don’t have a lathe, struggled with using a hand plane, spent 2 weeks to find a draw knife… Thank you.
I use a jack plane set coarse to shape the tapered tenon before it goes into the tapered tenon cutter. A drawknife is another good solution.
Hi Megan and Chris –
Thanks again for sharing Saturday with us. I’m finally getting to the point of having a workbench rather than a pile of parts, and it’s exciting. The holdfasts actually work – on to the planing stop mortise and crochet.
As I’m contemplating using the bench rather than building it, I’m wondering about arranging the accessories. Have you developed strong preferences for where to put things like the mallet, brush, square – or where not to?
I’ll probably add a swing out stool eventually. But since it’s a Nicholson, it seems like it needs to swing to the center to be useful for dovetails and such – or am I thinking about that wrong?
Both my mallet and brush hang off a Shaker peg on the outside of the right leg – that way, I always know where they are. (And my square is in a till in my tool chest.)
LEFT LEG: I keep my mallet by the planing stop – to knock it up and down. I keep my bench hooks on a nail on the leg by the face vise, because that’s where I stand when I saw.
RIGHT LEG: I keep my holdfasts in holes in the leg at the far end of the bench. And I keep my bench brush on a nail on the far leg as well because that’s where I start to sweep shaving from the end of the bench and to the planing stop side and into the trash can below the top.
All the other jigs and appliances go on the shelf below.
I’ve never put a swing-out seat on a Nicholson. They are pretty lightweight benches….
Thanks to both of you. This is build to Chris’s knockdown design and is heavy enough that I need help righting it after laying it on its side – and that’s before adding a shelf. But I have a roll around height adjustable still that I’ll start with, in any case.
I will soon be saddling my first seat. I have radiused luthiers planes. And carving gouges 3, 5, and 7 sweeps. And sandpaper. I don’t have a scorp or travisher. I also use only hand tools (no I’m not an elitist). The wood I use for the seat will be either 8/4 pine or Butternut. Can you reccomend a procedure for saddling with the tools I have? Or tell me to just wait and save up for a scorp and travisher.
You can use carving gouges to shape the seat like a scorp and luthier planes to finish the saddle like a travisher. Some people do it that way all the time and prefer it.
Pine or butternut cut easily. Work across the grain with your gouges to get the basic shape. Then bring in the curved bottom planes to remove high spots and smooth things.
Most important question of the day…..which way is chicken best? Setting aside that bears might be best.
Fried like they do at Purple Poulet. Next time you are in town, I’m buying.
And if you’re here when Chris is not, I’m buying. (It’s so good.)
Hi, did you guys ever used Rubio Monocote? I have a Murphy bed and 2 cabinets that I think it will be a good idea, it seems to be a better idea than polyurethane.
Thanks and Happy New Year!!
I have not. Sorry.
Sorry, no.
Good afternoon, Chris and Megan, and thank you.
Which model Waage melting pot are you using? My Hold Heet gave up the ghost and I’m using wax warmers for the moment. The water bath isn’t very deep and I’d like to find something more substantial, especially if the inner pot from the Hold Heet would fit inside.
Thanks.
Cliff
The 4 pint melting pot, 110v.
Is this comment how you want to be remembered?
No.
Could we just forget the whole thing?
Accidentally made my ATC carcass 24” deep rather than 22” which I think is the norm. Would you stretch the tills to 10” wide or keep at 9”? Thanks!
You can go to 10″ – but you don’t want to go wider on the top two than the open depth of the bottom one…if that makes sense. e.g. if the bottom one runs into your tool rack, subtract that tool rack depth from the overall depth. Having full access from above to the lowest till makes life easier. The first one I built (2012?) has wider tills, and they kinda annoy me (not enough to remake them, but…)
I’m working on a walnut dining table top that is 8’ by 37”. My winding sticks are about 18” long. To check for twist I’ve thought about trying to make longer ones or using blue tape and my 38” & 50” aluminum straight edges. Any tips?
A dining table doesn’t have to be dead flat (like a workbench). It just as to look flat to the eye. And screwing it to the base usually pulls out any little twist. Unless you are making a dining table for a machinist, I wouldn’t worry too much about winding sticks.
I’m making a cutting board and read that you prefer softwoods, for these won’t not dull your knives, and a single slab of long grain for similar reasons, and that any wood glue will fail after enough moisture and abuse happen. I’m intrigued by the pragmatism.
Do you put rubber feet on them? I feel like I can actually make one of these in an afternoon with my hand tools. And we really need a new cutting board. Thanks!
Yes – screwed on rubber feet.
A couple of years ago, I made two boxes (both maple & cherry) as a wedding present for him and her. Unfortunately, I made the mistake of putting on general fishes oil based varnish on them. They have been airing out all this time, but the smell never goes away. Is there any way to correct this situation? It would be nice if I can present them to the bride and groom who are now expecting a baby.
My guess is you are smelling the linseed oil in the varnish mixture. It can last for years in an enclosed space. If you haven’t already, wipe out the inside with mineral spirits. If that doesn’t work, try acetone, naptha and/or lacquer thinner.
If you still have the smell, a tin barrier coat of shellac should block the odor.
What’s the best way to dowel or tenon glued joints on a chair seat without a Festool, doweling jig, or any other loud expensive power tools? I read that John Brown doweled his seats. Is there a book, magazine article or video out there I could use for guidance?
Thanks a million!
Mortise chisel. Chisel both edges. Insert loose tenon.
JB drilled the holes by eye. I use dowel centers. Drill a hole. Put the dowel center in the hole. Use it to kiss the mating edge. Drill the hole there.
Another band saw question. I have acquired an 80’s era, 14″ Delta 28-245. While tuning it up, I can get the blade square to the table easy enough from left to right. From front-to-back, along the toothed edge or back edge, the best I can get is still out of square to the table at the top ~1/16 over 6″.
If I use the wheel tilt mechanism on the tensioning rod, the upper wheel rubs/stops against the housing. I can see that the blade on the top wheel is closer to the front than it is on the bottom wheel. I am thinking of adding a very thin washer behind the wheel to buy me little more room from the housing. The manual does not cover this adjustment. Thoughts? Thanks in advance!
My thought is that I’ve never checked this on any band saw in my life.
Yes, you probably could correct it, either as you suggest or by shimming the trunnions. OR…… if the thing is running great at this point, then use it for awhile and see if any operation requires that sort of precision set-up.