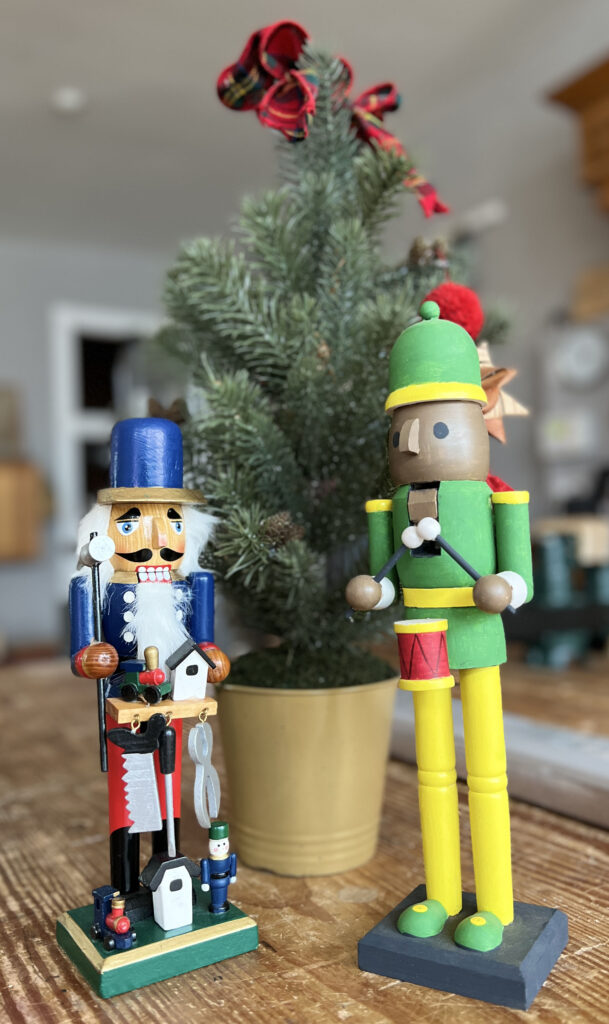
Comments are now closed. Happy Holidays!
With family things happening here this weekend, the storefront doors will not be open until around 11:30 a.m., and we will close at 4 p.m. – just in case anyone is planning a visit for a last-minute woodworking gift (and you might instead consider a Lost Art Press gift certificate – no need to venture out!).
We will, however, still be answering your Open Wire questions throughout the day. So leave your question(s) in the comments below, and we’ll do our best to answer. Comments will close at around 5 p.m. Or possibly earlier (so don’t wait until the last minute)!
Also, Chris has a post scheduled for 3 p.m. that includes, among other things, what’s planned for 2024 – so all questions along the lines of, “When is X going to be published” will be referred to said post. And yes, that includes the Dutch tool chest book and Issue 2 of “The Stick Chair Journal.”
– Fitz
Merry Christmas, y’all.
In many of the “Sharpen This” videos, your wrist can be seen wearing a handsome watch and strap. What kind of a strap is that and who makes it?
I believe that is my Hamilton.
https://www.hamiltonwatch.com/en-us/h69449961-khaki-field.html
For years I wore my dad’s Hamilton that was issued to him in Vietnam. That watch finally bit the dust beyond repair. The Hamilton Khaki Field is the contemporary version of that watch. I love it.
Thank you to all of you for making Lost Art Press available to all of us. MERRY CHRISTMAS !
I also wish you all a Merry Christmas and a Happy New Year.
Sounds like an exciting day!
What band saw blade size and type do you prefer for the stick chair process?
When they’ve replied to this question in previous weeks, it’s the Wood Slicer from Highland Woodworking.
https://www.highlandwoodworking.com/wood-slicer-resaw-bandsaw-blades.aspx
I’m sure they can chime in with more context but wanted to give a link in case you wanted to order one. Happy chair making!
A 1/2″ Wood Slicer from Highland Woodworking. A little expensive, but worth every cent.
Wishing you and chair makers everywhere a Holiday filled with Joy, Grace, Peace and Compassion!
Hi, just wondering if you still receive fan mail from wives against Schwarz? Hope you have a wonderful Xmas and new year! Looking forward to making more drinking chairs from the anarchist series in 2024.
I do not! That stopped when I stopped reviewing tools for Popular Woodworking and the blog.
Good to hear! But, have you seen the price of a ‘non-premium’ no.5 type 11 these days on eBay?
I’m not the only one who loves Type 11s.
Happy Christmas to you and yours only thirty hours to go here.
When I sharpen I reestablish the primary bevel on a diamond stone then hone and polish a secondary bevel using just a few strokes on each grit. I usually use a honing guide. One thing that puzzles me is that, when grinding, I can feel a burr on the back of the blade before the old secondary bevel is completely removed. Not a major problem since I get my blades sharp enough to take fine shavings off end-grain.
However I am curious as to whether you experience this and have an explanation.
I have never experienced the phenomenon you describe. A burr is created only when a zero-radius intersection is achieved. I can only guess at what is going on.
Sorry!
How did you learn how to use Roubo curves? Trial and error? Are there tutorials? I’ve purchased a set and am eager to use them properly. Thanks.
Those are, of course, just large French curves. There are lots of tutorials on how to use them (especially in the sewing world. But basically, the layout for them is three dots, or points, that you wish to connect. You select a curve of the right size and rough shape. Then rotate the curve until you can connect all three dots. Then connect them.
There are many other applications that are more like: I just need an irregular curve here on this chair part. Search YouTube and you’ll find lots.
You can also mark on the edges with a pencil and then flip to have a matching symmetrical profile.
Hope you guys have a great holiday! Looking for a recommendation for a first rasp for chair making. Any suggestions to get me started?
From “The Stick Chair Book”: “Here’s where to start. Buy one rasp: a cabinetmaker’s rasp with a half-round profile that’s 9″-12″ long. With a #9 to #12 grain. That rasp will teach you how to shape wood. It also will show you what rasp (if any) you might want to buy next. A rattail with coarser teeth? A modeler’s rasp with #11 or #15 teeth? You’ll figure it out.”
Auriou rasps are the cat’s PJs (and if not that brand, get hand-stitched if at all possible)
Thank you!
What is the brand/size drill being used in the picture with the GoDrilla on your web page? Any guess when the GoDrilla may come back in stock? I’m set up to be notified.
Merry Christmas.
Thank you
See here for it info: https://blog.lostartpress.com/2022/09/24/a-bit-of-information/
All the parts for the GoDrilla are on order – so we hope to have them available early in the new year.
Hi Chris and Megan,
This is not so much a “how-should-I-do-it” question as a “how-would-you-do-it*” one, in part out of curiosity as to your druthers, in part to serve as a basis for reflection on my own practices.
Context: producing the main four panels for an ATC; starting from roughsawn 4/4 white pine boards; aiming for a final thickness somewhere around 7/8″; all jointing and dimensioning done by hand.
Question: in the above context, would you prefer to dimension each board to a common (though not necessarily final) thickness before glue-up, or rather leave the non-true faces rough (or only just cleaned up) until after the panels were done? And why would your preference be what it is?
Cheers and wishing you and all of yours a very Merry Christmas!
Mattias
Hmmm…Chris might have a different answer, because he has much longer arms. But I have trouble planing on the far side of a wide panel – so I usually plane with my offhand, working on the other side of the bench for the far side of a wide panel. And I prefer to do as little of that as possible because I’m not as efficient a planer that way. So, I’d try to get them all cleaned up and flat before panel glue-up, then do a few final passes as necessary after the glue dries. Note: The dead flat side in this project needs to be the interior, so that the tills slide nicely. I wouldn’t be as worried about the exterior being dead flat, except where the skirts attach.
And a very Merry Christmas to you, too!
Of course, it depends. If the wood is rough-sawn and flat, I usually joint the edges and glue up the panels rough. Then dimension them. It’s efficient because the work is mostly traversing.
If the boards are surfaced and all about the same thickness, same approach as above.
But if the boards are different thicknesses, I bring the thick ones down first with traversing. Then glue up. Then finish the panels.
Hope this makes sense.
Many kind thanks to you both for the above – it does indeed make sense!
In the current case, I’m in the situation where I have already planed each board to have a true face and a true edge, with also the opposite edge of each board jointed and as near parallel to the true edge as makes no difference.
The thinnest corners left after that are at just over 15/16″ and the thickest at about 1-1/16″. So yes, some initial traversing of the reverse faces to bring them all closeish in thickness to a full 15/16″ before glue-up will be a good idea.
And I had indeed planned on having the true faces on the inside, not least because of the tills, although I suppose purely from a till sliding point of view it is really only the short sides that have to be truly dead flat and parallel?!
Cheers and all best,
Mattias
Yup. The end pieces are the most critical for parallelism.
Looking forward to SCJ#2. #1 was great!
Hi Chris! I didn’t see you respond to my question last week (about order of operations for assembling chair sticks) until after comments closed. Just wanted to say thank you for responding! Keep being awesome.
Have you ever tried to do dove tails in Baltic birch plywood? All I ever see is box joints but I’m curious if dove tails would work.
I’ve done it once, just for fun. The exterior layers tend to chip at the corners when you start sawing. So, if you’re going to do it, start sawing at the front corner, and be gentle in starting the cut.
You did that for FUN????!!!!
I’ve done it. The glue in the plywood will cause your dovetail saw to explode.
Just kidding.
It is easy to dovetail. In the early part of the 20th century most of the magazines showed it being dovetailed a lot, especially for drawer sides. We’ve gotten away from it.
Chris, Have you ever considered making a video of the pieces featured in your portfolio that would include brief commentary? I was looking through your portfolio and found myself imagining what you might say about this chair and that table, sort of like the artist lectures I attended in my college years. And it might have come from seeing you talk about the Durer square you made from “Melancholia” (which sent me on my own internet tour of 16th century engravings.).
Not a bad idea. Megan, put it on the list!
Cool! And Merry Christmas to you all!
Let us start with your Willow Phase.
We can start even earlier than that. Will require alcohol to make it interesting.
Would that be alcohol required for you, for the viewers, or both?
For best results, both.
Skål!
Merry Christmas and Happy New Year to the kind and generous people at LAP
Aww, thanks Keith. Same to you and your family.
Making a few work tables for the local ice rink to use for nacho breaks for the kids.
Trying to keep costs low, is it a terrible idea to use spruce for the conical mortise battens? Solid birch legs.
Also using the the big (still small) conical tenons, instead of the 2″ round tenons. Any thoughts on if this collapses in a week?
Merry Christmas, love the substack.
Nick,
It probably will be fine. Good tight joints and wedges will almost always save the day.
Wondering if there are uses for hollows and rounds besides fancy elaborate mouldings (not my thing). Trying to decide if any mouldings planes would be useful for me. Thanks!
I’ve used a large round plane for some coopering operations. And some hollows to ease edges. But in general, mostly mouldings.
I use a large hollow and round pair for making ogee bracket feet. But that’s really just a big type of moulding.
Do you have antique hand saws with features like nibs, split nuts, etches, and thumb hole handles?
My panel saws are antiques. Not sure if they have split nuts or not. I don’t think any have any nibs…. But they work.
Happy Holidays, and thanks so much for continuing to share your knowledge here!
I made a polissoir yesterday, following Fitz’s instructions from a couple of years ago. I’m a little fuzzy on how much beeswax should be exposed when it’s ready to work – in the wax-impregnated version are you also meant to be adding wax to the finish or is that just to give a little more structure to the tool? Just letting the excess drip back off I ended up with 1/8” wax cap on the business end…
The beeswax binds the corn fibers together and provides a little lubrication at the outset. As you use the tool it will settle in to the right combination of wax and fibers. So I’d rub your tool against some scrap wood until you reach that point. A lot of that extra wax will come right off.
Thanks!
Do you ever re-wax them, or do the fibers wear down as the wax wears away?
Usually using them rewaxes them. But if they start to scratch the wood instead of polishing it, I trim the long fibers that are making the scratches and add more wax.
Thanks Chris!
In the the Sharpen This video chapter on grinding you explain using a popsicle stick to set the the toolset for the bevel angle. If I setup at 25° this way a chisel would give a different result than a plane iron since the chisel is tapered in thickness and the plane iron is not, right? Does this even matter? Or, should I just set it and forget it?
That depends on how persnickety you are. Because I use a consistent secondary bevel, the primary isn’t all that important as long as it’s 1) Lower than the secondary 2) Steep enough that it won’t break. There is a huge range of angles that fit that bill.
I have my tool rest locked at one angle and almost never alter it.
How do you determine the final length to cut the long sticks to before installing the comb?
It’s different every time and depends on the fanning of the sticks and the tilting of the seat. In general, the center stick is about 1/2″ shorter than the outside sticks. So I graduate them from the outside in.
The height of the comb is always a subjective thing, depending on how I want the chair to look and sit. I don’t have any guidelines other than mocking up different heights to see and feel the difference.
Merry Christmas and Happy New Year to everyone at LAP!
I am wondering how your spindle deck transition to the seat saddle is so sharp (well defined)? I saddled my first seat and there is a gradual slope from the spindle deck to the seat that seems a little sloppy. I don’t have a Travisher so used a Scorp, Spokeshave and scraper to make a shallow saddle.
Appreciate all your time and sharing of knowledge!
If there is a shelf/fillet on the spindle deck, then I used a router. I haven’t done that in years, however.
Nowadays, it’s all travisher work that creates the hard line between the spindle deck and the saddle. So practice….
I just wanted to thank you (all) for your time and effort you put into this. And for answering all these questions, even the ones that aren’t related to woodworking. You are a massive help to our community and, in the spirit of the season, gratitude and grace to that for which we are grateful. Thank you.
Hey Chris and Megan,
I need to widen the mouth on my Jack to accommodate a thicker Hock blade. I thought I had once read a blog post about filing open the mouth, but I can’t find it. Any tips on opening the mouth?
Thanks and Merry Christmas!
-John
It’s probably hidden behind a wall at PW.
1) Disassemble the plane.
2) Mark a line with a permanent market that represent the point where you want to file to
3) Clamp the plane toe-side down in a face vise.
4) Use a coarse file held horizontally to file to the line.
I just watched some of your older videos on YouTube. In one of them you talk about the crisscross vise and how it is your favourite. I was wondering if this would work if the vise chop is at an angle of maybe 20 degrees? Or will the torck/forces/physics prohibit the cross from working properly?
It will work fine as long as the lower bits of the Crisscross stay in the groove in the chop and the leg.
I took the pdf template for the improved arm template from Stick Chair Journal #1 to a printer who said that at 100% it would need to be printed on a 34 x 46 inch sheet of paper which didn’t seem correct. I had the Gibson chair template printed at the same time and it fit on a 24 x 36 inch sheet.
Did we I something?
I just looked and the page is 34 x 22. Try downloading it again here:
https://www.dropbox.com/scl/fi/ji6m0qazicehxz5777okb/SCJ-Full-size-patterns-22x34rev1.pdf?rlkey=v9jmpffgjo00e30057ued5lqa&dl=0
Hey Chris
In the staked low stool you use cylindrical tenons and in the high stool you use tapered tenons. Any technical reason for using non tapered tenons in the low stool? I’ve made many of the high stools with tapered tenons and am going to build some low stools. Thanks!
I use those joints interchangeably. While there might be differences mechanically on paper, both the joints show up all over the furniture record and they all survive fine. Use what you have, or use what you like.
Hi Fitz and Chris – thanks for spending your Saturday this way! I’m finally ready to turn my knock-down Nicholson table into a workbench – that is, I’m laying out holes in the top and apron. The article is pretty exact about the top, but not so much the apron. I’m wondering how close to edge of the laminated 1×10 I can get before risking disaster? There must be some rule that applies here, but I’m not certain.
I don’t know of any rules. I keep them 3″ from the top edge. I know that works fine. I have never wanted them lower or higher.
Thanks! And how far down (how close to the bottom of the 1×10)? This will be my first time trying viseless work holding, so I don’t have any experience to fall back on.
Merry Christmas and Happy New Year!
On ours, the closest to the bottom are 2-3/4″ on center
Recently re-watched Chris and Will Myers build a Roubo and it’s an excellent video. Any chance we will see you two in a future collaboration?
Merry Christmas and thanks again for this series!
That would be fun. I greatly enjoyed making that with Will.
Will is quite busy with family, work and woodworking. And he owes me a book….
In your opinion, what style of dining table would look best with the “staked chairs” from chapter 17 of the ADB? (Or – what style of dining table would look stupid with those?)
Those are fairly contemporary-looking chairs. I’d probably build a simple apron table and try to match some of the details. Keep it simple and it will look great.
Merry Christmas to the entire LAP family. 🎄
New subscriber to The American Peasant. Where do you purchase the gelatin for the piggly no wiggly glue? I need to find a something less expensive than Knox gelatin. Thank you.
We get ours from: https://www.webstaurantstore.com/unflavored-250-bloom-pork-gelatin-10-lb/101GELPORK10.html
You can get it on Amazon and etsy for less. We need to buy it in 50 lb. bags.
I’m curious what your thoughts are on building a stick chair out of sapele. I have quite a bit of quarter sawn sapele left over from a project and was wondering if that would make a good stick chair or if I should just stay with domestic hardwoods. Thanks!
It will do well and look beautiful. I built a lowback out of mahogany (some really old mahogany from the 1950s that fell into my hands). Shellac and black wax. It came out beautifully.
https://blog.lostartpress.com/2023/03/24/for-sale-mahogany-low-back-stick-chair/
Great! Thanks!
Is it unreasonable to expect a chair I’ve just finished to be quiet?
I’ve built the three-legged backstool from the ADB, sizes and angles as near as you wrote them as my skills allow. It’s made out of red ash and glued with titebond 3, with the legs attached with conical mortises through the seat and wedged. The sticks for the crest are cylindrical tenons (shaped by hand with chisel, knife, and scraper) into blind mortises.
The legs are solid. The joints for the sticks creak as I lean back, but they hold. I’m going to pay more attention to getting a tight fight on those sticks next time (gonna get access to a lathe soon too), but how reasonable is it to aim for all the joints being so firm that there’s no creaking? The noise makes me think that they’re a little less solid, but worse that they’re moving and stressing the glue. But is a little bit of creaking just one of the results of handwork, like dawks on secondary surfaces?
That’s a good question. I’ve never had a new chair creak. I suspect it is because something is moving and rubbing to create the noise. It will be interesting to see what happens.
Thanks, almost guaranteed a couple of the joints were just too loose for a good glue bond. I’ll focus on making those fit better next time.
I hope the whole crew gets some rest and festivities over the next stretch.
How often do you clean the swarf from your waterstones? I’ve recently got a set of Shapton Pro stones and I’m not sure if I should be cleaning them after every use? At the end of a session in the workshop? longer? Thanks!
I think it depends on how much you’re using them, but I flatten and clean after every sharpening session (which typically involves a couple chisels and at least 1 plane blade, if not 2-3)
I have received and read your book “Ingenious Mechanicks”. It is a great book and I will make use of the information that you have shared though it when I build a low bench of my own. Thanks again and I hope you all have a very Merry Christmas and a prosperous New Year!!
Thank you, Jeff!
Hello,
I’m making a shaker style side table in cherry. My top ended up on the thin side, at 1/2” thick. When fastening the top, how deep into the top should the screw go, as a rule of thumb?
In your case, as deep as you can without the points poking through. People lift small tables (and large) by the top.
I would say there is no rule of thumb. It depends on the woods and the application.
I am sitting in my daughter’s 1908 Edwardian style townhouse in DC with parquet floors and her growing collection of Hepplewhite style furniture. I am feeling the urge to learn cross banding and shell inlay. Resist or give in?
“…You must discard the word Fancy altogether. You have nothing to do with it. You are not to have, in any object of use or ornament, what would be a contradiction in fact. You don’t walk upon flowers in fact; you cannot be allowed to walk upon flowers in carpets. You don’t find that foreign birds and butterflies come and perch upon your crockery; you cannot be permitted to paint foreign birds and butterflies upon your crockery. You never meet with quadrupeds going up and down walls; you must not have quadrupeds represented upon walls. “You must use,” said the gentleman, “for all these purposes, combinations and modifications (in primary colours) of mathematical figures which are susceptible of proof and demonstration. This is the new discovery. This is fact. This is taste.”
— Thomas Gradgrind in “Hard Times,” Charles Dickens, 1854
I am sort of like a batting practice pitcher lobbing softballs to the pros. Merry Christmas,
Hi Bean! (And Chris and Megan),
I finally finished my anarchist’s workbench top but had to make it 6” shorter length-wise due to space considerations. When I go to build the base, do you advise I scale all of the other components down by x% or just make one or two adjustments (IE move legs 2” inward but keep the other dimensions the same). I’ll do whatever makes the better bench even if it drives me nuts. Thanks!
Shift the base’s position 6″ away from the face vise. Having that substantial overhang comes in handy when planing down dovetailed cases – you can sleeve the case on the end.
Thank you so much! You saved me a lot of head scratching. Merry Christmas and Happy Holidays to you and your loved ones!
LAP have anyone use the rocker drill angle jig?
We have not. Sorry…
Thought you’d like to know that you’re helping start another generation right. We gave our daughter “Sharpen This” for her birthday (she likes it, thank you very much) and her 2 year-old daughter insists on having it read out loud. Seems like a good start to me.
Thanks for all you guys do and have a wonderful holiday!
Wow! THank you.
Is Bean now an “only cat”?
Nope – he just got a little brother (featured in the last Soft Wax post): Billy.
On a tabletop, like, say, for the American trestle table, would you leave the bottom scalloped from a jack plane? Or maybe smoothed a bit more than that? (I’m getting closer, guys, thanks for the help!) Happy holidays!
Chris would probably leave the scallops…I would probably leave the scallops in the middle, but smooth at the ends and edges where people might grab. Or just take finer jack plane cuts and leave smaller scallops…
I leave the underside all cross-grain dawks. Unless the customer objects.
I love the texture and will leave it wherever I’m allowed.
Fitz, I want to wish you a Merry Christmas! I took your Dutch Tool Chest class at Berea last year. I loved the class and use the tool chest I built all the time. It continues to hold almost everything I need for daily woodworking. Thanks!
Hi Jason! I’m glad it’s working out well for you. Merry Christmas to you, too!
Three questions about the shellac process on campaign furniture:
1) Do you sand between coats of shellac, and with what grit?
2) How long do you wait between coats?
3) How long do you wait between the final coat and applying black wax?
Thanks!
1) If the dried coat of shellac is rough, then yes. I use a #320 grit sanding sponge or #320 stearated sandpaper
2) Depends on the environment. 30 minutes at most.
3) Overnight.
If I just now looked at my engraving tool and realized that I ended up with the too narrow tips, how can I go about getting a replacement? I went to look for the blog post with the specific email address on this issue, but it looks like that post is gone (or I don’t know how to search the internet, which I will accept is possible).
We shut down the blog post after received more requests for cutters than we had shipped out in the first place….
Send a note to fitz@lostartpress.com and she’ll send you new cutters.
Hello! Any tips on scaling the length of the Anarchist workbench down? Due to shop size I need to scale down to 6′ or 7′. Just wondering how to shrink the overhangs so it’s still useful, but doesn’t make the bench tippy.
This very question was asked at the beginning of today’s open wire…. Shift the base away from the face vise to keep as much overhang as you can on one end. This will allow you to sleeve casework over the cantilever and lever dovetails etc.
Thank you! sorry for the repeated question!
I know you’re a proponent of using moisture meters to assess wood moisture levels. Price points on these vary widely. Is there a particular style and brand you’ve found adequate? Pins or pinless?
Merry Christmas to you and yours!
We like the Lignomat meters. They have never let me down. There are a lot of cheap ones out there that are really unreliable.
https://lignomatusa.com/
Basically, you get what you pay for.
Hello everybody,
I’m interested in the book “Hide Glue: Historical & Practical Applications”. Does anyone have an idea where you can still get it? There is an offer on Amazon USA but according to the Amazon website the seller does not ship to Germany, where I live. Unfortunately I cannot contact the seller.
All the best and Merry Christmas
We have a copy in our library. You are welcome to come visit and take a look. After the author died, Megan reached out to the family to see if they would be interested in us republishing it. They were not.
A lot of the information in the book is now out there on the internet. Things were a lot different when it was published.
Happy holidays, Chris and Megan, and all the LAP crew! Thanks for everything. Hope you and your families have a great break and a great coming year.