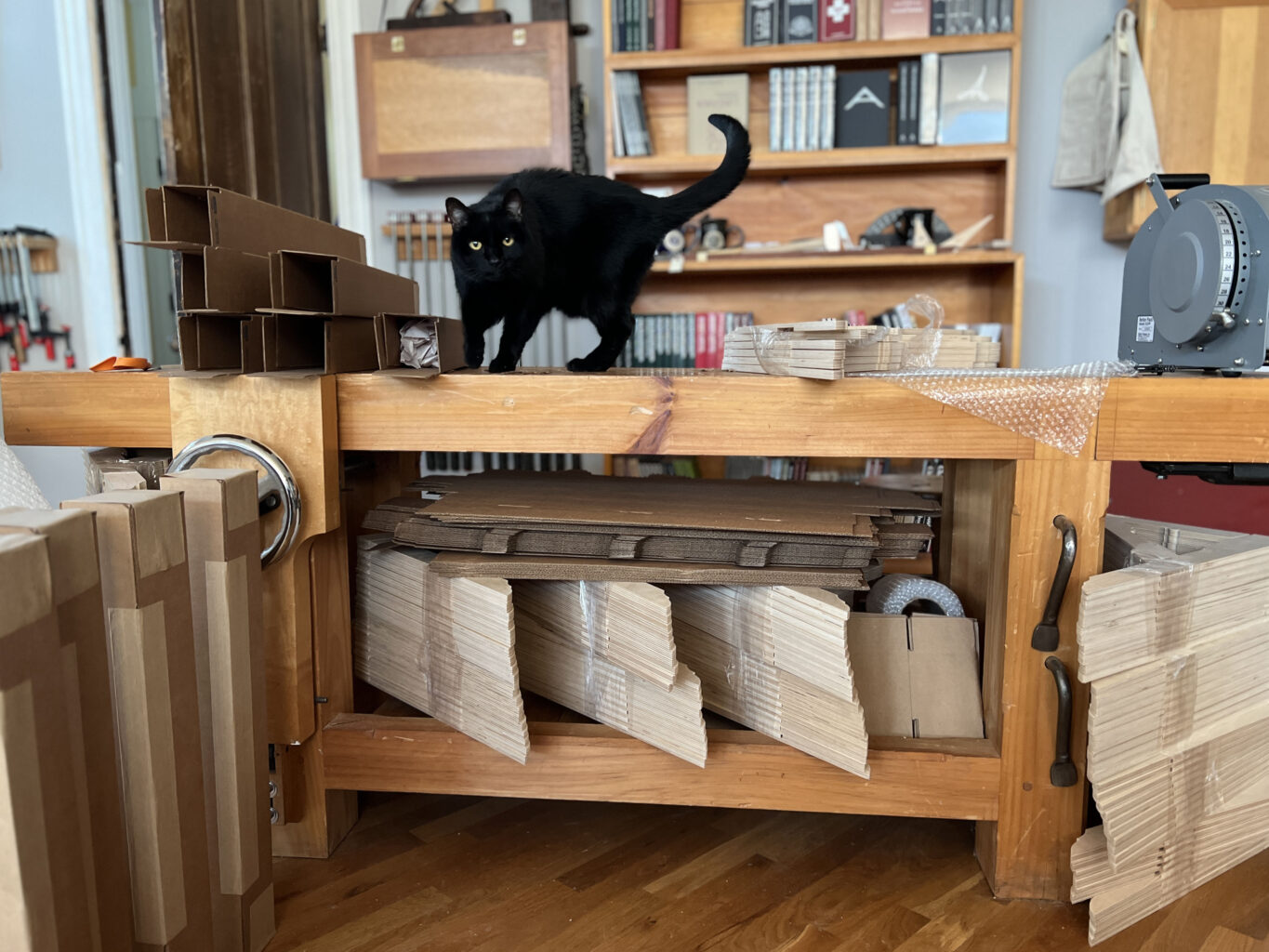
Update: Comments are now closed. Chris will check in to answer sometime today, tomorrow or Monday the questions I couldn’t , and you’ll be notified of the response. Thanks for a fun Saturday!
Concurrent with making more Piggly No Wiggly glue and packing Anarchist Square Kits, I’ll be hosting Open Wire this week all by my lonesome – at least that’s the plan. But because Chris just can’t help himself, he’ll probably chime in from time to time, even though he’s supposed to not be working today (he’s visiting with old friends).
So, ask your woodworking question in the comment field, and I will attempt to answer it. And if I can’t answer (i.e. it’s a stick chair head-scratcher), odds are good Chris will be along at some point to do so – though it might not be until Sunday (you’ll be notified if/when an answer is posted).
Comments will close early today, at around 4 p.m. I, too, am hanging out with old friends this evening, and have to scurry home first to wash off any spilled glue and make a dessert.
– Fitz
Good morning, I am hung up on the Dutch Tool chest or I guess you could say I am infatuated with them. I have built a few and just love the simplicity of them. My question is, when will your book become available? I heard you and Chris discussing it briefly in one of the Q&A’s you did some time back.
Thanks
Mike
Adding to Michaels question, are you done with building or are there some more DTC features you are working on that need to be done to finish the book?
I’m the problem – nothing else.
I think you are being hard on yourself. I also haven’t finished “The American Peasant.” We have taken on more scholarship classes this year and have been working part-time at the Anthe building almost every week. There are only so many hours in a day.
It isn’t a problem if it is delayed. We all know lost art press goes for quality over speed!
But for those of use waiting for the book just drop us a quarterly update so we know it isn’t forgotten.
You guys are unbelievably productive.
From where I’m sitting, there is no problem.
I appreciate you
I recently built a temporary (but probably not) countertop for a coffee/booze cabinet and used some fairly pink red oak. I wished I had white but didn’t, so I slathered it in a few baths of soap finish to see how it would look. A was pleased with the result and so is everyone that touches it.
I had always obeyed the advice to leave soap for the very light woods, but now my clean smelling finish habit may be unstoppable. What woods are you guys soaping up these days?
I have soaped red oak chairs and been happy with the results. Where is looks odd is on dark woods such as walnut. Oak can go either way. Beech, birch, maple are all ideal for soap.
I built a table out of Pecan, finished it with lacquer and , of course it looked like crap in no time! Stripped it to the wood and soaped it and it looks great! By the way I only used the sap wood so it is a white color. Thanks for the tip: I don’t think of it as a finish, I think of it as maintenece
.
Good morning. Is there a rule of thumb when nailing a rabbeted joint – slightly shorter nails? Nail through the full thickness piece? Pre-drilling of course. Thanks!
The rules of nailing don’t change. If you have reduced the thickness of a 3/4″ board by adding a 1/4″-deep rabbet. Then you are nailing through 1/2″ stock and need a 4d nail. (A 3/4″ board would need 6d nails.)
The only additional thing I do is that I cheat the nails a little away from the edge to avoid splitting. I usually make a test joint if I using unfamiliar woods or nails. And, as you mentioned, pilot holes.
Happy holidays. Quick question about the hacking knife you have from Jennie Alexander’s shop. Do you sharpen it? How keen an edge does it need? Thanks for answering questions each week. If only we had an index to the many, many answers…
It’s like a froe. The edge doesn’t need to be polished of particularly keen. Just consistent and smooth. I have never sharpened a hackling knife. The only time I would bother with it is if got damaged and the steel were mushroomed.
This is a style search that I use sometimes.
site:lostartpress.com jennie knife
Good morning!
I have two questions, if you will indulge me.
Could you outline your process for “make pretty”?
Do you have any tips for adjusting an ill-fitting lock on an already-finished-and-delivered school box?
😸
Trent,
There is a chapter called “Make Pretty” in “The Stick Chair Book” that is a free download. Here’s the link: https://lostartpress.com/collections/all-books-1/products/the-stick-chair-book
It discusses the ideas and the tools.
And as far as adjusting a lock, usually it involves filing the strike plate until it mates properly with the box of the lock below. THis is a common thing you have to do in a project like the schoolbox when the lid is a solid piece of wood.
I’ve narrowed down a carcass saw purchase to the lie Nielsen or Gramercy tools saws. Do either of you have any opinions on them since I’m not able to actually get either in my hand before buying? Thanks!
You aren’t going to lose with either. Megan can confirm, but I believe the Gramercy saws have handles that are ideal for smaller hands. The Lie-Nielsen saws (which I use) suit bigger hands. But I am fine using both kinds – the differences are slight.
The Gramercy has a thinner handle, but it’s long – so while I can grip all the way around it, my hand slides around in it a bit. The LN has a bit more handle girth, but isn’t as long. They are both good.
So, do you have some sort of formula for length vs girth?
This sounds like the start of a blue joke… But no. Most saw handles fit most men (and a lot of women). I have particularly small hands.
It ain’t the meat, it’s the motion!
Thank you for mentioning the Bob Dylan song Paths of Victory. Saw it in Earlywood. Beautiful. Moving song for me.
What dessert are you thinking of making and will bourbon be an ingredient?
Not sure yet…but probably!
I heard somewhere that honey vinegar pie is oddly awesome. 😉
I am going to build a gigantic toolbox, about 10’ long and styled like a Chippendale chest. It will have multiple flip up lids for access to the top level of hand tools and deep drawers below. You and Chris are great at coming up with catchy names for tool chests (and chairs and tools and books). What would you name this style of tool chest?
Really, 10′ long?
“Long Dong Silver’s Tool Chest”
Clarence would be so proud to be remembered thusly.
😂
Sarcophachest
Nice
I tried to come up with a question. Or a witty comment. I got nuthin.’
Thanks to both of you for doing this. Personally I think you were nuts for coming up with this. You both have far too many irons in the fire already. But good on ya.
Being accessible is important to us. This is a much more efficient way of answering questions than private e-mail. Honestly, Open Wire saves us time. And it makes the Q&A we get constantly available to others who might benefit.
Hope you are recovering well!
Thanks. If I don’t saw and nail something pretty soon I’m going to go bonkers.
Time to take up carving?
I’ve been making some leather sheaths for my favorite Stanley 1299 cast iron utility knives. And some turkey wing brooms. Stuff I can do from my posterior.
You can do that with your posterior?
I stand impressed.
I really appreciate this aspect of it. I have spent time in the last six months reading through the entire blog and most of the comments. There’s an immense wealth of information tucked away in the q&a (and things to make me wistful) and absorbing it in that way was very different than reading it in an edited book. Works for my brain… Thanks for keeping it all online.
My wife ordered me a copy of Ingenious Mechanicks for Christmas and it came yesterday. I have been reading it since it arrived. ( I told her she could put it in a gift bag before Christmas morning and I would act surprised)!!! While reading the chapter on paintings, I looked up several times to a painting that I have in my living room of Joseph working at at tall timber frame workbench with mallet in hand and The Christ Child playing in the floor beside the bench with 3 Roman nails, the sunlight forming a shadow behind the Christ Child in the shape of a cross. I can email you a picture of it if you would like. I hope all of you have a merry Christmas!
Sure. Feel free to send it to fitz@lostartpress.com
I’m wrapping up my staked backstool from the ADB. When I started to assemble the crest, seat, and spindles I was temporarily stymied by the conundrum of the inner two spindles vs. the outer two. Since the spindles lean back and the crest is curved, the outer two need to cover a longer distance to reach from the seat to the crest. The result is, their tenons won’t completely disappear into the mortises, even if the center spindles are tight. I told myself, “just glue it up and don’t worry about it.” Anything you would have done differently?
Hi Ben,
Qt the beginning of the journey, the answer is: yup, just glue it up. As you begin to notice details like this in the process, you can figure out what you want to do about it. You can lengthen some tenons, shorten some stick lengths or do nothing. As long as there is enough glue-to-wood contact in the outer-most mortises, you’re good.
Have you ever been approached about publishing a book on traditional home or building construction of some kind? To me that would be super cool. Love what you all are doing, best of luck to you all with the Anthe Building, and I hope you have a Merry Christmas!
I’m afraid we aren’t qualified to edit a book like that.
What we have found in our business is that the closer we stick to furniture-making, the better the books sell. That’s a function of our audience and our skill set, I think. I love timber-framing. You might do what my parents did and check out the Shelter Institute.
https://shop.shelterinstitute.com/
The do have the knowledge and the passion to offer you information/books on this topic.
I’m finally getting around to making my tool rack for my atc. Is there any merit to mounting the rack to the back like a Dutch chest instead of the front?
I like it at the front so that I don’t have to reach over anything to get to tools I use every day (awls, chisels, dividers, gauges, screwdrivers). If I did have a rack at the back, I would keep tools there that I don’t use much.
Thanks for the response my thought was being able to see what I’m grabbing without falling into the chest. I wasn’t sure if I was missing something that made it a bad idea.
I understand it might be a pain to keep up to date but have you considered a “Sources” tab for your site. I can search through your blog but at times I am looking for a specific item and I don’t have any idea who might sell it or what it is even called . “Thingy” is an important part of my vocabulary. Thanks
Hi Casey,
I can’t imagine how we could maintain that with our current staffing. Perhaps that is something AI could handle one day for both of us.
I just received my large square parts and would like to use it as a template for other wood. Please suggest other species of wood that would be appropriate for this square: stable; easily cuts through the half laps; and allows nice shaping of the various curves. Thanks.
I have made this square out of maple, cherry, walnut and mahogany. I look for quartersawn or rift -sawn material to reduce wood movement.
I’d avoid oak unless it is quartersaws (flat-sawn oak moves too much).
As a modestly experienced Windsor chairmaker who hasn’t made a stick chair, I was surprised when reading the Stick Chair Book that you assemble your sticks into the arm and then install that whole assembly into the seat. I do t think I’ve ever seen that done by a Windsor maker. Is this just a personal preference, or is there a technical reason why that order works better for a stick chair? I was thinking maybe it’s because the heavier sticks are less flexible, so you can’t as easily bend them into their positions in the arm if you put the sticks in the seat first, but that’s just a SWAG.
Stick chair makers do it both ways. Chris Williams seats his long sticks in the seat and then drops the arm over the sticks.
I learned to do it the other way and couldn’t imagine switching.
So I don’t have a good answer for you.
Hi Team,
I feel like I never can get my smoothing plane set up to take cuts from either grain direction and really get that tear out minimized. Downy shavings don’t happen either, but I am more concerned about the actual result not the shaving.
Could you walk us through a setup? How far the chip breaker is back from the blade edge, how open is the mouth, etc.
Thanks for all you do… been a supporter for decades, and you guys got me started on the hand tool path.
This video shows you: https://www.youtube.com/watch?v=WAYcwubAO2E
When is the dutch tool chest book coming out?
See above
In the stick chair video, you talk about breaking down stock at the lumberyard to fit in smaller vehicles. Do you still use the Stanley sharp tooth? Battery circ saw?
Also, any opinion on Ivy Classic spade bits?
Michael,
There’s a Japanese tool store near me (Hida Tool) I bought what they call a framing saw. Z-Saw 333 it cuts through 8/4 boards like butter.
I was buying some wood from a guy and when we loaded my truck he said “I’m buying one of these immediately”
Our lumberyard has a miter saw and they break down the stock for us. A home center will do this as well. The Stanley Sharptooth saws are also good at this if you cannot find electric help.
I’m in the process of preparing to make a trestle table (my biggest and most visible project to date – gulp). In Chris’s American Trestle Table article it mentions that moving the stretcher down reduces strength. Could you elaborate on that?
Also do you have thoughts on making it knock-down or not? Meaning tusk tenons I think, like on many other versions. But they all have lower stretchers, which is partially the reason for the first question.
I built a knock-down X-frame trestle table out of pine a million years ago, and it has survived two moves, six cats and 20 large Thanksgiving dinners over the years (and tool chests and other projects piled atop it). I’ll post it on my Instagram, and the book it came from (which can be found for $1.50: https://www.alibris.com/search/books/isbn/9781558707115?invid=17778682919&utm_source=Google&utm_medium=cpc&utm_campaign=NMPi&gad_source=1&gclid=Cj0KCQiAsvWrBhC0ARIsAO4E6f-jvUtJQMrGGcbE-LGnrTPgBA2q6yhv7qnfijt5Rg68ZQBVQo8woewaAixZEALw_wcB&gclsrc=aw.ds).
Not rushing on the book, I was just curious. I know you folks are pretty busy, hope you all have a great weekend.
Do you ever use a larger 3/4″ pilot on seat mortises to increase the girth of the leg at the point where it enters the seat mortise? This would add 1/8″ of thickness to the leg at the mortise entry. The cutting edges of the 12.8 deg tapered reamers from Lee Valley are long enough to accommodate this on material up to about 1 7/8″ thickness. Of course, this could also be accomplished by reaming deeper.
It seems the weak point in a chair with no stretchers would be where the leg encounters the seat mortise, being that this is both the stress point of the leverage of the angled leg, and also the thinnest portion of the leg. Setting aside other factors like grain runout or brash wood, do real life failures you have observed support this idea?
If this question is too deep into esoterica then just to tell me to bugger off!
I have not used a 3/4″ pilot. You would need a different tenon cutter that produced a 3/4″ tip. Or you would need a different reamer that was wider at the base.
The 5/8″ tapered tenon cutter, 5/8″ pilot and 12.8° reamer are designed to produce a strong joint. Monkeying with one aspect of it will complicate the others.
Use a strong, straight-grained wood for the legs and you’ll be fine. Or go full vernacular and use a 1″ cylindrical joint. I’ve done both methods (with no stretchers) and have been very pleased with the results over the long term.
Two questions:
1) Exactly how does one tighten the nuts on the wheels on a bench grinder to the point of not too tight but just so they don’t slip when installing a new Norton wheel? I used the double nut locking technique on the right side to tighten the left wheel. But no matter what I do to try to keep the spindle from turning, every time I try to snug up the right side the left wheel nut loosens. Metabo bench grinders have an Allen wrench socket machined into the ends of the spindle to hold it while snugging down the wheel nuts which seems like a great idea.
2) I’ve invested in a pile of 8/4 red oak and have broken it down. I’m going to start with two Gibson chairs and am planning to do a mild saddle like Chris shows in the video. Gibson seats are speced slightly thinner than the “standard” stick chair. Do I really need to hand plane the seat stock thinner for appearances or would an under bevel work?
Thanks,
John
1) On our grinder the shaft has a flat on it so you can immobilize the shaft with a box wrench. Does yours not have that?
2) An underbevel is fine.
Hi, I am about to start on my American Welsh Stick Chair. I sourced some great 8/4 red oak for legs and seat. The only problem is that it is just shy of 8″ wide (I did not double check what I needed, lesson learned). So in order to use it for the chair I will need to glue up a blank from 3 pieces, not 2. Any issues? What about growth ring placement? Up – Down – Up? Or does it matter? Thanks!
I know this one!!! Growth rings up (i.e. inside of the tree faces up – just as the inside faces out on casework). And you can make the seat a little narrower if you want, if you prefer a 2-piece glue-up.
I’m a new(er) woodworker, playing around with shellac for the first time. Is there anything gained from doing more than two-or-so coats of a 1-pound cut?
Also I’ve heard some wax and steel wool can dull the shine a little, is the LAP soft-wax okay for this? I’m not sure if the linseed oil will just sit on top or if theres something better perhaps.
Shellac is a film finish, so every coat “builds” – that is, adds thickness. So theoretically, multiple coats will add a little more protections (that is, you’d need a deeper scratch for it to penetrate to bare wood.) With a 1-pound cut, I typically do three coats. The oil will sit on top of the shellac. Regular ol’ wax is my go-to topcoat to dull the shine a little bit.
Allback paint with uneven sheen.
Any experience/thoughts on the second coat of Allback paint, cut a splash with low-odor paint thinner, that’s drying with sections matte and others very gloss? Well-shaken with a ball bearing, stirred while applying. Stick chair: spruce seat, red oak spindles. Put the chair outside in the sun a few days, in at night. Cured well with a consistent sheen. No final sanding or wax topcoat. After a couple months, it looked fine other than the original user errors: some spindle arrises bare and patchy-ness on seat edge (end grain). A second coat would fix those so… sand with 240 grit non-woven pad, wipe off the dust, and paint again. 49 degrees north so not much solar energy now. The very glossy seat patches do not feel sticky but look odd. Do I wait another month or two? Find a UV light? Take the chair on a Southern vacation? Threaten it with bedazzling? Or be-waxing?
Thanks for your books, your public education, and your open wire — both of you.
The same has happened here. Adding a topcoat of purified linseed oil (after the paint is completely dry) and rubbing it out melded everything nicely together.
I checked with Sage about thinning (just curious about what they would say) and they suggested using linseed oil. Have not had a chance to try a side by side comparison. Soon I hope.
When you are doing the pre-coat and post-coat of linseed oil does it matter if it is the boiled or does it have to be the slower purified linseed oil?
I want to reactivate hide glue on a 3 X 8 cherry carcass, joined by dovetails. They did not close to my satisfaction. Is there a technique for this; I’ll need to get to both sides of the joint, and taking the joint apart completely and starting over is not an option. Hot wet towels? Hair dryer? Thanks.
First, I’d try hot damp towels and a hair dryer on high. If that doesn’t work, you can inject hot water into the joints…but that will weaken them. Still, the dovetails should hold it together.
Hi y’all,
I have been playing around with making my Crucible dividers lockable with a thumb screw. The problem I have is that I cannot find a good way to fill the gap that is left after removing the flat head screw plate.. This allows dirt and dust in and I worry about causing wear to the bearing and threads
When you were designing the dividers, did y’all work ever tinker with a thumb screw design and have any advice to fix that?
I’m sure it can be done, but it’s not something I’ve thought much about. Our goal with the tool was to use a driver to lock it, like old dividers, bevel gauges and marking gauges. So the cup was designed around the Chicago screw used in the hinge assembly. If it were me, I’d ask a machinist to make a thumbscrew that fit the hole.
I’ll also add that a heat gun (used for removing paint) is sometimes necessary to get the glue to plasticize. Put a damp towel over the joint to prevent scorching.
Thanks for recommending the batch of Josh Clark/Tom Law saws.
Do you have a favorite refinishing technique for antique handles that could use some TLC?
A little paste wax or renaissance wax does wonders for old finishes.
No question this week, but I wanted to say thank you for the inspiration that LAP has been. The practical and no-frills approach in so many of your books has been the push I needed to take on projects I would never have felt confident enough to do otherwise.
I recently finished up the two Gibson chairs I’ve been working on for a couple months. And in addition to the two full size chairs, a half-scale version of the simple Irish armchair from SCB…
Which will be for our first child that we’re currently expecting! I got everything finished in time to use a picture of the three chairs as our social media announcement, and that felt like a very special way to announce our news to friends and family.
So, thank you for providing the resources necessary to contribute to this special moment!
I have a vintage router plane, and every time I use it the plane leaves excessive marks on the wood from the sole of the plane. Is there a way to clean or polish it so it leaves minimal marking? Thanks
Are they scratches? If so, find out what on the plane it causing them, and either file it/them off (if on an edge) or flatten the entire sole on #80-grit sandpaper affixed to a flat surface (such as a granite tile or the like). (I often have to file off dings from from planes after lending them out in classes – won’t hurt it – I promise!).
No scratches, but lots of black/brown marks left behind when I use it. When I got it it had a fiberboard base on it that I removed. I’m not sure if it contributed to the current problem.
In that case, clean it really well. I’d probably start with mineral spirits. Then wax it after.
I ambitiously mixed up a batch of garnet shellac that is now about 6 months old. I followed the mixing instructions posted to the LAP blog (used Everclear, and a magnetic mixer), but I haven’t used a single drop of it since life got in the way of completing projects. Is this batch toast? It’s going on a sapele campaign furniture-inspired 1:2 size travelling ATC. Thanks!
Easy to test if it’s still OK. Brush some on a scrap of wood. If the shellac dries, it’s good, and fine to use. If it stays sticky, it is not.
This is kind of an oddball question. I’ve got a board that came off the side of a tree where a branch was coming out. So the grain is perfectly ovular. I’m hoping to exploit that grain in a picture frame. Making the outside shape is obvious, but how would you go about making the inside all excavated? I really don’t want to do a bandsaw box sort of cut where I reglue it. I’d much prefer to essentially make an oval donut. Any help or direction is appreciated!
Cheers
Drill a hole, then thread a coping saw through the hole and cut to the line. Clean it up with rasps/sandpaper. Et voila.
Sometimes when I’m using a Japanese flush cut saw (thin, single or double-sided) to trim larger/thicker pieces, like a tenon protruding from a through mortise on a table, it wants to cut down into the work instead of straight across. It’s hard to tell from the outside, because the saw looks flush to the work, but when the sawing is done, it’s concave. I’ve tried putting tape all around the tenon, but then the saw just chews the tape. Do you have any tricks to avoid this? Or maybe I’m just bad at it.
Are you having the bend the blade into the work? That is, you’re unable to keep the handle off the work? If that’s the case, you need to more firmly hold the blade flexed flat to the work, and not let it lift at all (sometimes, shorter strokes out near the bade end can help). If that’s not the issue, amd the handle is off the work, and therefore not interfering with the cut, I’m afraid you just need to be more careful to keep the blade flat to the work (same solution…just typically doesn’t take as much attention and pressure). You could made a collar of sorts from the thinnest scrap you can find (thick veneer would be ideal), and put that over the joint to protect the surface, then finish flushing with a block plane. A rigid piece of of wood will protect the cut better than tape.
You have set in your saw that needs to be taken out simply with a hammer and something that you can use like an anvil
Ah right…I made an assumption there was no set, if it’s a flush-cut saw. But you’re right – some of them do have set on one face.
Thanks! It’s definitely a flush-cut saw and I assumed it didn’t have set. How do I tell if it has set on one of the faces? Would a few strokes on a stone help?
I’ll give those other things a try and do some more practicing!
Grab an old credit card,drill a hole through it the diameter ofthe tenon, stick it over the tenon and saw away. Follow up with a cabinet scraper or block plane.
1) try flipping the saw over, 2) gently and carefully work your way around the exposed tenon then cut all the way through, 3) push down with your off hand farther away from cut
I suspect this has been asked and answered here a thousand times so apologies, but when building a workbench do you install a face vise before flattening the top or after? (The face is square to the bottom already.)
I’d flatten first, thereby avoiding running into the vise.
A quick question about Roman workbenches.
Generally, do the feet fall within the footprint of the top, so they aren’t a trip hazard? Or should they extend a little beyond the edge for stability?
Is there a consensus with the historical examples? My worktop is 12 inches wide if that makes a difference.
Thank you in advance for any pointers
Congrats on making and using a low bench. It’s your choice.
My low bench has one side with the feet right at the edge of the top. I can edge plane doors and other wide pieces by sitting them on the floor and clamping to the edge of the low bench. The other side the extend maybe an inch past the edge of the bench.
That’s a great idea. Thanks!
I don’t think there’s a consensus based on historical examples. The benches aren’t tippy when you sit on them, so you can keep the legs under the shadow of the top if you like. And they’re not much of a trip hazard (in my experience) if they are slightly extended outside the shadow of the top. I have done it both ways and don’t think it’s an issue either way.
Depends on the type of face vise. If it has a big wooden jaw, then I install it before flattening (so the wooden jaw will be coplanar with the top). But if it’s an iron quick-release vise, I install it after planing so I don’t run my plane into the iron bits.
I’m starting oak frame and panel walls for what will become my basement office. Being that the bottom rail at the floor will have to be made of multiple boards there will need to be some sort of joint. Any suggestions on how to join the boards to make them longer?
2nd – I like the look of shellac and black wax on the oak – should I be looking to topcoat with something as well? One of Chris’s other recent posts now has me questioning this. Thanks!
I believe the “rule” in trim carpentry is to cut a scarf joint to join long boards – that is, cut the pieces through the thicknesses at mating angles. Or if you want to go all Roubo on it: https://blog.lostartpress.com/2017/02/09/different-ways-to-elongate-wood/
As far as a topcoat on the wax…I’m 99.9-percent sure the wax is the topcoat. I can’t recall ever adding anything atop it.
Stick chair question. I’ve got a thin seat i want to put battens on. I think I’m supposed to put them in at angles to align the centers of them with the holes i would put in a regular seat for a chair. But I think that might put the battens far towards the sides. Is there a risk in doing so? The alternative is adding more splay i guess and that seems more risky. Thoughts? Also I’m in no rush, ya’ll can party and respond whenever you want. Happy holidays.
Search “brettstuhl” in Google images and you will see how the makers of Alpine backstools used battens. Their answer was more splay.
I am doing a layout for a stick chair and the sightline for the rear legs is coming out at 27 degrees. That is a lot tighter than the angles used for the three designs in the Stick Chair book. Could the tighter angle create excess stress on the rear legs?
I wouldn’t be worried about the strain on the legs. Instead, a sightline like that usually puts the rear legs more to the sides of the chair. You need them to the rear of the chair so it won’t be tippy. That’s why sightlines for rear legs are more like 55° to 75°.
Now, because you asked about “strain” on the legs I wonder if you meant a 27° resultant (instead of a 27° sightline). If so, the answer is no – a 27° resultant is fine for back legs.
Hope this makes sense one way or the other.
I was rereading some of the campaign furniture book recently and the leather working unexpectedly piqued my interest. I see where Texas heritage offers finished leather kits tailored to the roorkie chair design from the book. I would much rather get some basic tools to start making these and similar items myself. Would you (or anyone here) be able to point me in the direction of a decent starting place for tools and basic skills? Is there a “Lost Art Press” for leather working? Thanks
You can get pretty much everything you need from Weaver Leather. They are the Woodcraft of the leather world. Good people and products.
You’ve mentioned that you have individual methods of collecting dust at each of your very few machines, rather than some complex central system. (Yay!) I just got a benchtop planer (Dewalt 735) to complement my 10″ bandsaw, and by necessity, dust collection needs to be as simple and compact as possible.
In your shop, what do you do for dust collection on the planer? Just a shop vac? One of the fancy cyclone separator things? Something more?
Thanks for the sanity check, and happy holidays!
“Vortex Cone” Jet (as seen here: https://blog.lostartpress.com/2023/01/27/dust-collection-in-the-horse-garage-bench-room/)
The Dewalt 735 has a motorized fan that ejects chips/dust quite well, so you might try just having a container/cyclone the will separate the solids and let the air out. The bandsaw will need something motorized, preferably with high cfm and a large diameter inlet. They make a lot of dust that is difficult to capture. And the health hazard comes from the really small stuff, so keep that in mind. Good luck!
A shop vacuum would fill up really fast when connected to a planer. Even with a cyclone in between. We use a single-stage dust collector with a pleated paper filter.
Any thoughts on using Japanese wooden nails to fix mortise & tenon joints? Japanese company Kakuri makes them in various sizes, up to 80mm. thanks!
I have used them in the past. But because my work is Western-based, I stick with trenails that I rive out and run through a dowel plate.
If I made Japanese pieces, I would definitely use the wooden nails. They are very effective.
Chris recently mentioned his pizza dough recipe. I’m always looking to try new options. Care to share?
I’ll dig it out. I’m 766 miles away from home right now.