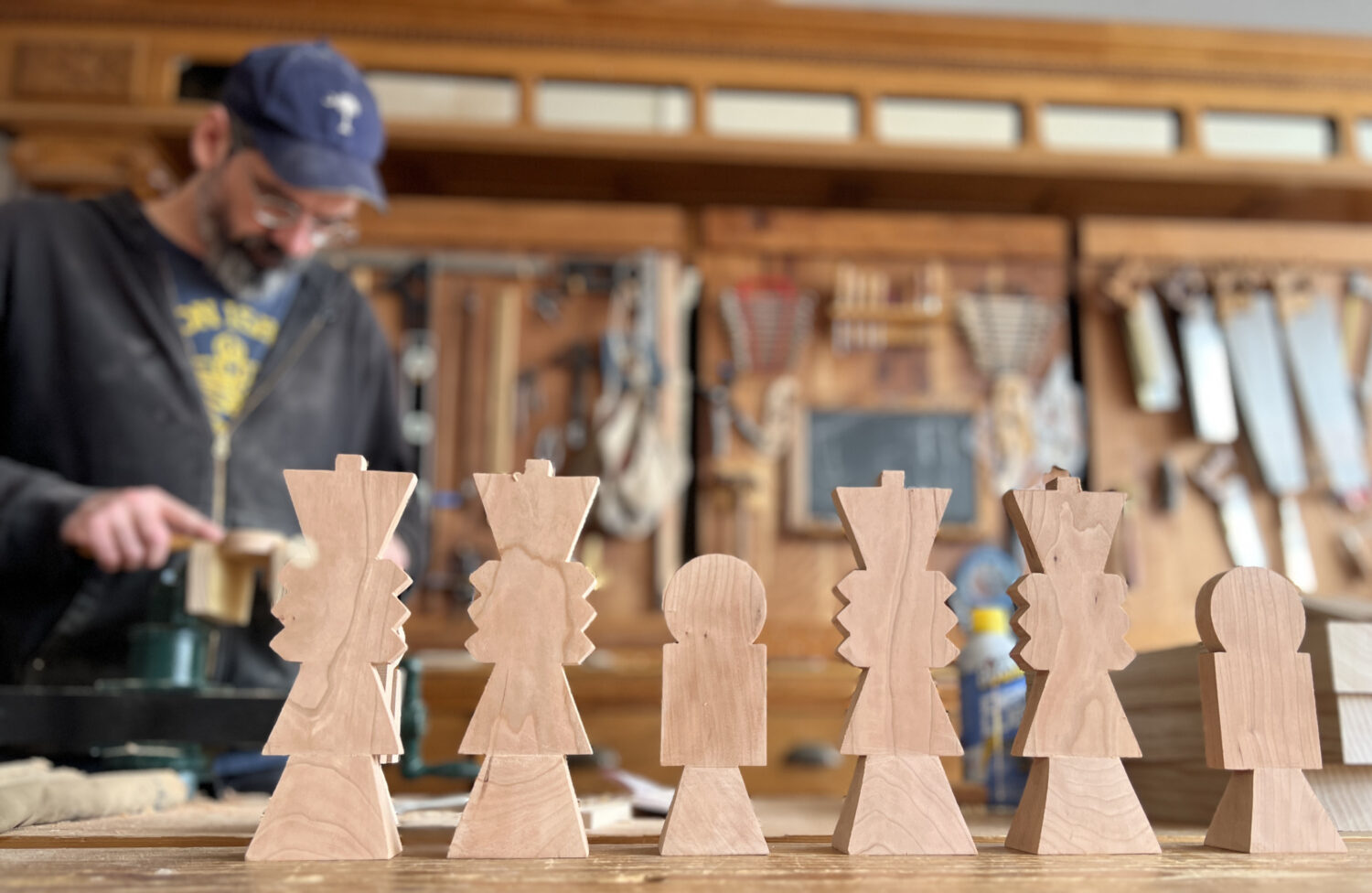
Here’s how it works: Type your woodworking question in the comment field; we will attempt to answer it. It is that simple.
It’s time for our weekly(ish) Open Wire, hosted this week by me and Chris (mostly Chris…he’s faster at answering and gets up earlier than do I, plus he knows a lot more than do I about what seem to be the favorite topics: chairs and chair-shaped objects – but do ask him about his Pristolnicul/pristolnice).
So here we go…. Comments will close about 5 p.m. Eastern.
Note: Comments are closed for this session. See you next week.
– Fitz
I was out in the country the other day at my favorite lumber supplier getting some wood for chairs and he mentioned that he has had some “wide” genuine mahogany stashed away. Took me to a barn and showed me two 16 foot 8/4 boards that are 26 inches wide. Had them for fifty years and wants them gone. They are pattern grade and beautiful. I have no idea what to do with them (thought seems a good reason to have a go at some campaign furniture), but I have the definite urge to take them off his hands and figure it out. I think Chris has said many times if you find wood you like, buy it. So, I’m going to. Can’t think these are easy to come by. So, today’s question: How on earth, if you wanted, could you resew 8/4 26 wide boards for case work thickness? Roubo frame saw? Light saber? Mind power? Or, do you find uses for them in 8/4 (that’s a lot of chair legs cause its all dead straight). My bandsaw can handle 12 inches, but seems real crime to rip them down to resaw only to glue back up.
Thanks!
Do you have a jigsaw?
Congrats.
The thought of resawing them makes my butt twitch. What if there is tension in the boards that is release when they are resawn and you end up with two potato chips? This stuff is gold. I would try to find uses that embraced the 8/4 – like a dining table.
But if you are brave, find a person with a band saw mill. They can resaw them easily. Or if you are anywhere near Hearne Hardwoods, they have immense resaw capacity.
Firstly, thanks so much for doing this every week.
I’m making a low Roman bench with a top around 2 inches thick. And I’m now at the point of deciding between cylindrical and tapered tendons to attach the legs.
In ADB you describe the process for each and I understand your preference is for tapered.
However I don’t have a lathe or any tenon cutter. So is there a design or mechanical advantage to a cylindrical tenon that would make you choose it over a tapered one. Other than the speed and convenience of being able to use powered tools?
Thanks in advance.
I use both kinds of tenons in my work. Both will work fine for a Roman bench. Use whichever appeals to you or your tool set.
The mechanical differences are at the margins. Both forms appear in the historical record.
When making octagonal legs, is there a preferred grain orientation (two sides flat/two quarter vs no faces flat)? And which way should the growth rings in the leg be oriented with respect to the leg mortise?
The science oriented woodworkers will give you a chapter in reply to this question. My reply relates to the furniture record. They did it all sorts of ways. They all work and survive. Yes, there is a theoretical way to do it best (consult “Chairmaker’s Notebook” and “Make a Chair From a Tree” for details).
But I do it this way: make the legs look their best. Make the joints fit tight. Wedge the ever-loving piss out of them.
First out of the Gate! Good Morning. When building a drawer with dovetails corners does the shape of the tails add or subtract from the final strength of the drawer? The drawer in question will be 35″ x 20″ x 9 1/2″ tall using pine lumber. Thank you
The short answer is no: the slope of the dovetails (within reason) is pretty insignificant. Mostly it’s fashion. Some people like bold slopes. Others like subtle ones.
Dovetails are an overkill joint. That’s why we can vary the slopes.
Good morning,
I just received the gift of your chair making class from my wonderful wife as I turned 50 on Wednesday. Can you suggest some exercises or projects that would be beneficial to help prepare for the class? I’m a hobbyist so I haven’t made the time to hone my skills, and I want to be as ready as possible before making the trip to Covington.
Read this free little pamphlet: https://lostartpress.com/collections/all-books-1/products/the-stick-chair-book
Get your tools sharp. Your block plane and jack plane need to be ready to go when we start class. We don’t have time to teach sharpening or tool set-up.
Other than that, comfortable shoes. Tylenol. Brown liquor.
Congratulations. This is going to be an epic week for any woodworker.
Read the book, watch the video, and, unless you aren’t a desk jockey, walk every day to build leg strength & stamina. Also, read this post from my classmate Sam Sankar – it’s spot on.
And have a great time.
https://blog.lostartpress.com/2023/02/19/what-to-expect-when-youre-expecting-to-visit/
Awww, thanks Paul. I hope you find the time to come back for another visit!
Hey Chris and Megan! With you both having so much going on throughout each year, how do you plan for it all? Do you use a planner? Or a shared calendar? I know phones have the capability for this but I imagine you prefer planning with pen & paper.
I had a paper desk calendar for years. But when you have to coordinate the way Megan and I have to, we opt for a shared calendar.
But only Megan and I can add anything to it. Once other people can put stuff on your calendar, you are doomed.
Hi Chris! How’s your Pristolnicul/pristolnice?
Cheers!
Right now they are painted such bright colors that my eyes hurt.
Help, my cheap store-bought ‘hobby’ workbench is unexpectedly & quickly dying (I know you have a good article on prolonging the lifespan of these). I picked up a 96″ long slab on the cheap (but only 1 3/4″ thick) and I have some massive 8″x8″ cedar legs. I just want to bolt the legs to the slab and be done with it. Questions:
1) what bracket orientation from the legs to top would you use?
-two brackets per leg, one in front of leg, one in back, running lengthwise to the 96″ slab
-four brackets per leg, two in front, two in back, lengthwise
-four brackets per leg, one in front, one in back, two facing the middle of the top
-etc.
2) when bolting a top with brackets, how is movement of the top accounted for – do I need brackets with slots for the far-side legs (either store bought with slots or filed/elongated by me)? I guess this question is somewhat dependent on the answer to question (1)…
I’m going to go with no stretchers and see what happens (I know you have mentioned this before too).
Well if you don’t have stretchers you don’t have to worry about wood movement. And brackets bend. Cedar is soft and can easily waller out around the fasteners.
You are describing your second short-term bench. Even woodworkers who were living hand to mouth took care to make a bench that would survive and not fight them. Unless you have a woodworking emergency and need to make this bench or die, I’d recommend stretchers. And tenoning the legs into the top.
I am all for expediency. But I wouldn’t consider what you are proposing. Sorry!
All good points – I’ll slow down and build it right (following all that you have written on the topic). Thanks so much for the advice & all that you do!
What’s the most effective way to fix a bowed desk top? It’s a 1 1/2″ solid red oak top. It is screwed to a sit/stand desk frame and is finished with wax (if any of that actually matters).
I read about and I’m thinking about placing the bow up and, using clamps and battens with spotlights (for heat) and wet towels, let the bow slowly straighten. Is there a more effective way? How long does this take? I have a short break from work before I have to use my desk again. 😉
How long should I let it acclimate after the bow is out?
I meant “cupped” not bowed. I couldn’t find a way to edit my comment. Sorry… I’m a doofus.
Bob Flexner wrote an excellent article about this years ago. It’s free, but you have to sign up for PW’s marketing:
https://www.popularwoodworking.com/editors-blog/a-method-for-correcting-warps/
It’s worth it. I’d basically be quoting his article.
I’ve recently been watching some videos about steam bending. It’s pretty amazing what shapes you can coax wood into with moisture and heat. So this got me thinking: resawing boards tends to bring out all kinds of wackiness when the tension is released, and it can be hard to get two flat 20 mm boards from an 8/4 board, for example. Could you use steam bending to straighten wood that cupped after resawing? Steam bends seem mostly to be along the grain rather than across it, but some more complex bends I’ve seen do involve cross-grain bends as well.
Intuitively, this seems like it could work: the point of steam bending is to force wood into shapes it wouldn’t naturally want to be in, after all. But is there something special about cupped wood that would resist this?
I’m afraid I don’t know the answer here. The plywood and veneer industries use heat and steam to process the thin plies. No idea how that would translate to thicker boards. And honestly, thinking about the press that would be needed to keep the boards flat as they dried makes me want to look for another solution. Like resawing over-wide and planing the boards flat.
No worries. The Bob Flexner article you posted as a response to another question deals with a different cause for cupping, but I’m going to try that with some of my resaw-cupped boards to see if it has any effect on those…
Never completely satisfied with my wax finishes. Have tried multiple waxes from Johnsons paste wax to Katie’s to my own version to the expensive Europeans. Now have the buffing kit from the Anarchist’s gift list. Searched among your writings for how you use this kit but with no success. Could you either point me to a reference describing your use or share a brief outline of how you use this kit? TIA
I apply the wax with one of the sponge pads, usually the black one. Then I immediately follow up by buffing with the woollen one. That’s about it.
Good morning, I am considering adding lasers to my chair making tool box. Any recomendations or suggestions you have as to brand, capacity etc would be greatly appreciated.
Rob
I can’t really recommend any brands because the ones I like are all white-labeled from one or two factories.
I like:
https://www.amazon.com/Leveling-Motovera-Brightness-Adjustment-Waterproof/dp/B0B56BB51R/ref=sr_1_7
Fitz or Chris: have just about assembled my Anarchist Workbench of yellow pine. What is the best finish, since we don’t want a super-slick top?
Probably no finish. But I like to provide some protection against water, so I use straight linseed oil.
Good morning. I was wondering if you’ve ever done a video, or class, showing how to visit your local hardwood dealer to select wood for a project. I find it the hardest hurdle to overcome when getting started on a new project.
Perhaps it’s also because my local hardwood dealer won’t let us into the warehouse. Instead they bring a small stack of boards out on a fork lift and expects us to select from what they bring out.
My Build a Stick Chair video covers picking wood for a stick chair. But I haven’t done a video on picking wood generally. I learned to do it under the tutelage of experienced professionals. Which sped me along. You might see if there’s a woodworking club near you. Usually the members are very forthcoming with their knowledge. They might even know of a better lumberyard….
Go to lumberupdate.com and wait for the pop-up. If you sign up for Shannon’s email list, you’ll get access to a video that he made on the subject.
He works for J Gibson McIlvain, and teaches hand tool woodworking.
Thanks Matthew! Good resource!
I have an Ash tree in my basement shop. It has been more than two years getting there having been cut into (mostly) two inch slabs and stacked outside for drying. Now that I have managed to get it inside before the first snow, I am looking for stick chair parts. So far the boards I have milled for seats appear very similar to the Ash you picked up yesterday. My question is about seats. If I cannot get enough eight-ish wide boards, would it be possible to use three boards for a seat? If so, what widths?
Thanks!
Sure. You can make seats from three boards. Just orient the boards so that the leg mortises don’t pass through the edge joints in the seat. Yes, glue is good and should be stronger than the wood around it. But what if your edge joint isn’t perfect? Then the leg acts like a lever in the joint. Good luck!
My son and I built a full size Nicholson workbench a couple of years ago and we use it viseless and love it. When my middle son moved out he took my shaving horse with him so I bought a green carvers vise from grizzly to mount on my bench. As I am aging I am missing my shaving horse just because I could sit down and work. What is your opinion on building a low boarded bench in the Nicholson style and mounting my carvers vise on it instead of a shaving horse assembly? I have some 2×12 yellow pine that I can use.
Sure. Do that or make a staked low Roman workbench. Four legs. Four holes. Done.
My apologies if you announced this already but have you picked a date for the Anthe Building open house yet? Thanks!
We will be announcing that soon. Keep Feb. 23-24 open on your calendar….
Hi Chris,
I built a mule chest a couple years ago from your design book plans, and painted it with a forest green milk paint and a finish of 1:1:1 beeswax, gum turpentine, and linseed oil. It has held up well (great design!) but the surface finish needs refreshed.
Would you suggest that I use the same soft wax, or would a coat of linseed oil be better at this point? New to furniture, and this will be the first piece I’ve had long enough to refinish.
Thanks!
A finish with some wax will give it a little more lustre. I’d probably use the same stuff you finished it with the first time.
Going to work in a new roubo sttyle bench and have given thought to adding a tail vise. In theory it sounds like a good idea, but I’m not sure in practice I’ll get as much out of that device and I’m thinking.
What’s your take in the inclusion of a tail vise?
As always, I appreciate you both taking time to answer questions tossed your way.
Some people love tail vises. I rarely want for one. It’s just a different way of working. Both are valid.
I always opt for simplicity.
But to answer directly, a tail vise will work fine on that bench.
Since I found the doe’s foot I always use that for face planing and work holding on top of the bench. It’s less fussy than a tail vise, much less expensiv, and you can easily remove the work and put it back to continue working. I know Chris has written some on the doe’s foot. Richard Maguire of The English Woodworker blog has written and done a bunch of videos about it. I only use a tail vise to hold another higher vise for carving and such.
When I built my bench a few years back, I also hesitated about putting in a tail vise, but because I’d already bought the hardware (a Benchcrafted wagon vise), I figured I might as well install it as part of the build, to save myself the extra effort of a retrofit if I came to regret not having it.
I have now worked on that bench for two years and a bit, and know three things that are true for me:
I don’t need the tail vise. Other methods (that I also use) would give me the same (or close enough as makes no difference ) workholding results.
There’s not a week goes by that I don’t use the tail vise, and every time I do I send a thought of thanks to me-that-was for putting it in. I find it particularly useful for holding smaller stuff both on and perpendicular to the bench. It is perfect for holding my sticking board in place, and for steadying pieces when marking with a gauge. And more.
The only real drawback for me has been that the left front corner is partially lost for any clamping, as the clamps hit either the hardware or the cavity on the underside.
Your milage can and most likely will vary.
Cheers and have a great bench build,
Mattias
Any plans for an 8-10ish ounce warrington hammer?
Not currently. Next up is our 16 ounce claw hammer.
Aloha, do you recommend any particular books, websites, etc. with good resources for outdoor projects such as storage chests, deck boxes, and mini-sheds? I’m hoping there may be some hidden gems that I’ve missed.
Maybe Megan or other readers have some ideas. I have done very little woodwork for the outdoors and garden. Sorry.
Rodale press used to sell a book called The Backyard Builder. The only thing I built from it was the tool tote but there’s lotsa stuff in it.
On what types of furniture in the past have you used varnish oil or Danish oil successfully and why did you choose either of those over, say, a linseed oil & wax combination (such as Tried and True’s “Original” finish or something like it) or even lacquer? Thank you again for all you do. Rage, rage against the dying of the light.
I like varnish when I need some protection and sheen. Tabletops (when the customer requests it). Doors. Floors. Kitchen cabinets.
It’s not a mutually exclusive choice. Both oil/wax and varnish are appropriate. It just depends on what you or the customer is looking for with the end product.
Good morning! I’m curious to hear, how did the Heron linseed paint work out? How’d it compare to Albec?
It looks like Heron ships to many of the states that Albec & Lee Valley do not, so I’m hoping it’s a good option for those of us in those areas.
Heron Paint is made in California, which I understand is the state that regulates things shipped thereto the most, so that’s one hurdle cleared already. I haven’t played with it enough yet to render a confident/considered assessment. I used it “full strength” the first time, and it felt a little thick to me – bit so did the Allback; that’s why we started thinning the Allback by 10 percent with mineral spirits.So I asked Travis at Heron what I should use to thin his product (he hasn’t used mineral spirits, but didn’t tell me not to!)…but until I follow his thinning advice and apply the paint, I won’t know how it performs in an apples to apples comparison. But I do love that it’s made in the US, and Travis is incredibly responsive and helpful, which I greatly appreciate. And the colors he mixed for me are gorgeous.
I’ll report on our blog once I have a little more experience with the paint.
I have recently discovered another US linseed paint supplier (within 10 miles of my house) http://solventfreepaint.com/linseed_paint_by_viking.htm. They carry Viking at much nicer prices but no blue, Ottesson, and list Allback but are dropping it and only have what is currently in stock. I specifically asked about shipping restrictions and they don’t have any in the US. They are a mom+pop been around for a generation with a daughter prepared to take over when they retire (she is https://www.earthandflax.com/viking-linseed-oil-paint for those who want a more “modern” looking website). I won’t actually use it until spring since my winter heated workspace is also my living space. Their specialty is serious traditional housepaint so they have been under our radar although they are vaguely aware of us; I am the second person to mention Chris Schwarz and LAP.
The deal is I gave them money and they gave me paint, no other connection.
Thanks Esther!
Apologies if this is a duplicate, first one didn’t appear and I think this newer address has been seen before.
I have recently discovered another supplier and another brand of linseed oil paint; Viking from http://solventfreepaint.com/linseed_paint_by_viking.htm (local to me). Prices nicer than Allback and Ottoson but the color blue conspicuous by its absence. They are a mom+pop business with a daughter to take over when they retire, if you want a more “modern” website hers is https://www.earthandflax.com. Their specialty has been house paint so they have been under our radar, I was the second person to mention Chris and LAP. They list Allback, Ottsoson, and Viking, but are dropping Allback and only have what is currently in stock. When specifically asked no problem shipping anywhere in the US (surprised at the question). I bought some paint but haven’t used it yet, my winter heated work space is my living space and I don’t care for linseed as an air freshener.
The deal was I gave them money and they gave me paint, no incentives here.
Pristolnicul/pristolnice – I was clueless, I googled and a rabbit hole opened before me. But, before entering I need coffee
I was aware of the square/round stamps for altar bread but the “chessmen” icons are a new universe! And more my size to make….
Hi! Building a small shaker side table, was playing with resawing and bookmatching the top but after glue up and planing it I noticed a very prominent chatoyance effect with the two board. I understand why it happens but do you have any tips for how to prevent it when picking the wood, during dressing, or finishing? And is it considered a faux pas or generally accepted as a normal part of furniture making. Thank you!
Book matching is a love it or leave it thing. I prefer slip matching to avoid the differences in shimmer. Basically make sure the grain is running the same direction in the top and that all boards are heart-side up. That will give you a more calming grain arrangement.
I have a laminated hard maple slab about 2.5”x30”x108”. It was a prep counter in a commercial kitchen and has a depression maybe an inch deep on one end where I believe it was routinely scraped for hygiene. The rest is rough but could be hand planed flat. It also has all thread rods every foot or so to keep it from delaminating that prevents ripping. It could be crosscut if done carefully. I have to either figure out some use or throw this thing out. I have had it for probably 40 years. What can be done with it? Wild and crazy ideas are preferred.
It would make a fine workbench top. Just flatten the area where you need flatness. Or use it as-is for the top to a kitchen island. Or make a low assembly bench for the shop.
One more question if I may be so greedy. Building my first project, it’s a small shaker side table in walnut. It’ll be used to put small items, maybe a drink with a coaster, remote, etc. So it doesn’t need to be bombproof. What kind of finish would you recommend that’s easy for a novice to apply, provides some durability, and looks good with walnut. Thanks again for doing this every week!
I made a walnut side table for my cat to sit on and look out the window. I used an oil/wax finish, which makes the walnut look gorgeous. And it holds up pretty well to the cat, too. I’ve reapplied the finish once in the year or so since I built the thing.
Thanks Megan! Would that be an oil/wax blend or something you apply separately? Sorry for the basic question. And any specific product you would recommend? Thanks again.
Hi I made a small cricket table in black walnut and put some leftover teak oil I had when we had a sail boat. I put coffee and a glass of water on it and read the paper (still need that feel and smell) after about a year I just put a refresh coat and still no rings.
“Shop Finish” (oil/ varnish blend) and wiping varnish are also easy to apply and look great. You could just play with the different options on scrap and see what you like best.
Hi- would you consider it completely insane to try to build a stick chair (my fourth) out of curly bubinga? I’m in my shop looking through my sparse lumber supply and came across a beautiful piece of curly bubinga and a light (probably a dim one) went off in my head to use it on my next chair. I would use it for the seat, comb and armbow. Legs, sticks, undercarriage would be ash ebonized. Has my fifth cup of coffee altered my thought process or is this doable? Thanks!
I haven’t worked with bubinga, but it would be fine for those chair parts. It will be “fun” to saddle it.
After spending way too much time refreshing or repairing edge tool bevels on granite with sandpaper I have finally decided to up my game and get a bench grinder. I love your advice in the “Sharpen This” video about using a simple 6″ grinder with a good wheel so I went looking… and looking, and… They are all junk! The tool rests are not only flimsy but don’t adjust for angle and in one case where it is adjustable the motor was bigger than the wheels which would work OK for chisels and plane blades but not for, say, restoring a draw knife. Is there anything wrong with an 8″, 1750 rpm grinder? My understanding is that the surface speed of the slow 8″ grinder is similar to the full speed 6″ grinder. The only real difference would seem to be the amount of hollow.
Help! I can’t seem to find my way out of this rabbit hole!
I’ll advocate for a slight step up from the Sharpen This approach: one of the benefits of a slower speed grinder like that is that it’s the ideal machine for a CBN wheel. I have one from Woodturners Wonders on an 200 mm (8″) machine and I freaking love it. (I’m not a turner, I strictly do straight blades with it.) Stumpy Nubs on YouTube has a few videos on the topic that are worth a watch. Not the cheapest combo out there, but I would say it’s superior to both your typical 6″ grinders as well as Tormeks.
Sure. An 8″ slow-speed grinder is fine. It’s just more money for the extra windings in the motor and the bigger wheels.
But no matter what you buy it will be LOADS better than sandpaper and granite.
AWB chop: I know you prefer maple, but do you have a hard vs soft maple preference?
I do not.
Do you have caster wheel suggestions for the ATC? Maybe anything will do, though i am on concrete so not going with all metal!
Just glued up the skirt last night and prepping the bottom boards today for final fit and nailing. Thank you both for the great resources on this build process.
Chris likes vintage iron wheels…I like poly locking swivel casters, 3″. The ones I was using don’t seem to be available any more, but these look pretty much the same. https://www.amazon.com/Tactzen-Polyurethane-Furniture-Workbench-Casters/dp/B0B48TMH11/ref=sr_1_1_sspa?crid=3V5VHV2XEZKB0&keywords=3%22+swivel+casters&qid=1702135390&s=industrial&sprefix=3+swivel+casters%2Cindustrial%2C84&sr=1-1-spons&sp_csd=d2lkZ2V0TmFtZT1zcF9hdGY&psc=1
This is where I get my vintage casters: https://www.instagram.com/iconicironandoddities/
Or from some nice Canadians:
https://www.leevalley.com/en-ca/shop/hardware/casters-and-wheels/112498-heavy-duty-polyurethane-swivel-locking-casters?item=00K2131
Another choice from Lee Valley. https://www.leevalley.com/en-us/shop/hardware/casters-and-wheels/74189-spoked-aluminum-casters
They perform well and look great with the black-on-red milk paint finish on my ATC.
Hey Chris. I’ve been struggling through a dry-fit of your lowback stick chair design. Getting six sticks simultaneously into deep armbow mortises feels like a challenge. And I’ve tossed out a lot of sticks already because the tenons didn’t seem straight or centered enough.
What I want for Christmas is for you to say: “lowback chairs are inherently stronger than full-height stick chairs, so don’t worry if a couple of your sticks have to be a little wiggly in the mortises in order to get the thing to start going together–as long as the whole thing is tight as a drum when complete.” And/or “feel free to ream out the bottom half inch of the armbow mortises to give you some extra room.”
Absolutely yes. Ream slightly until the thing goes together. If it’s tight at the end of the assembly, you have succeeded.
If you want to add insurance, you can fox-wedge the tenon that go into the backrest.
My scorp says thanks. It was tired of waiting.
Chris,
In your book, your method for tapering chair legs is: 3 cuts at 4”, 3 cuts at 8”, 3 cuts at 12’, and a full-length shaving. Whereas in your video, you take a single cut at each of the four sections. I am curious why the difference in technique.
Also, I can’t justify the investment in a Festool Domino Cutter for a couple old chair seats and don’t want to cut 2” deep mortises for tenons in the seat joint by hand. I ended up using the Rockler Beadlock system, which drills five overlapping holes and uses matching tenons. It seems to have done the job. Any thoughts or experience with this cheapskate option?
Earl
Question 1: Probably my mood.I’m not dogmatic and am constantly switching things up to find a rhythm. Both work.
Question 2: The beadlock is great. I have used it many times. However you get a loose tenon in there is great.
My younger brother (17) has severe dyslexia and other learning disabilities, he hated school until taking wood shop last year and now this year he is in the advanced class. These classes finally have him wanting to go to school. He will be a senior next year and wants to pursue a trade / woodworking school. I was wondering if you knew of any geared toward those with learning disabilities? If it matters we live in Michigan.
I do not, I’m afraid. Perhaps the readers here have heard of such a school. Good luck!
One place to start looking might be the Learning Disabilities Association of America (ldaamerica.org). There’s nothing on their website beyond general information but they may be able to put you on to some resources. Another place to check is community colleges; some still have trade-vocational programs that aren’t exclusively IT oriented.
Michigan folk school is a good place to start but shorter term classes. Penland School of Craft in Asheville North Carolina has semesters and longer programs. Berea College is one of the top in my mind for woodworking schools and I wish I would’ve gone there myself. In my thinking it would be good for him to choose a school that teaches compassion and kindness for each other and a balanced healthy view of the nature. Those things are not a given in most conventional woodworking schools and other trades. The ones I listed would I think be good places for a person with disabilities myself included to learn.
I need mortise and tenon advice.
The Project: I am building an outdoor garden gate using sapele. It will be a double door (each door 30” wide x 52” high x 1 3/4” thick) on pintle hinges with 22” hinge straps (beefy). The stiles are 4” wide. There are 4 rails. Top rail 5” wide. Middle rails 4” wide. bottom rail 8” wide. I will be using mortise and draw-bore tenon construction.
The question:
I read that on outdoor gate construction should use draw-bore through tenons without any glue. Allegedly is allows for expansion/contraction and permits the joint to fully dry out (no trapped moisture in a blind mortises to cause rot.
Thanks for your thoughts.
That sounds like BS to me. I would absolutely glue and drawbore it using a water-resistant glue (such as epoxy or Titebond II or III).
Ok thanks. TB3 it is.
Any chance you have any of those H O Studley tool cabinet posters left for sale? Or have any idea where I may find one? Thanks!
We do have some. We will put them up for sale once we get out of the holiday shipping monsoon.
Framed and hung for my tool cabinet to see. Hopefully giving my cabinet something to aspire to.
Any suggestions on soft close hinges for the Anarchist’s Tool chest? (If possible brand/type of hinge?) Im making a toy chest, using your design and trying to save small fingers from being pinched. Thank you.
I’ve used these many times and so far my children still have all their fingers.
https://www.leevalley.com/en-ca/shop/hardware/chest-hardware/stays/40648-lid-supports?item=03K2006
Thank you!
I built a toy chest for our friends’ son many years ago and used these – or something like it that Lee Valley had at the time. They worked great.
I just got a Rikon benchtop band saw. In researching how to set up band saws, I found videos with Alex Snodgrass that recommend setting the tracking so the bottom of the gullet of the teeth is centered on the wheel. First, do you do this for you band saws, or you center the blade on the wheel? On the Rikon I have, the wheel is so narrow, if I center the gullet, there is only about 1/8″ of space showing on the back of the wheel. What would you recommend in this case?
That is a tiny difference. I want the teeth (and their set) off the crowned wheel. So either of those approaches will work if the teeth are not biting into the wheel. Hope this makes sense.
Morning,
I just finished building a one of your curve back chair designs. Overall, im way happy how it turned out except for the seam in the back rest is super visible. The grain patterns of the two pieces of 8/4 flow together really nicely but there is a bit of brighter wood right on the seam that when I put on a wax finish it really stands out and that’s all I can see when I look at the chair. Ha.! any ideas how I can possibly camouflage the glue line? I was thinking, maybe some black wax? if it matters, the legs and sticks are grey Elm and the seat, backrest and hands are ash.
Thanks a lot
Black wax will help the mellowing/blending process along. Time (or paint) will be the ultimate force in the equation.
What’s your favorite Bourbon? Makers Mark, Jim Beam, or Woodford Reserve?
This is a Megan question. I drink bourbon once a year, as required by Kentucky law.
Blanton’s…but I don’t like paying for it. So Bulleit 10-year.
Chris, you wrote about moccasins years ago. Are you still wearing them? How are they holding up? I’m thinking about getting a pair to replace my tennis shoes for everyday outdoor and indoor use (in the city/suburbs). What would you recommend?
Sadly, my back and my feet don’t allow me to wear those anymore (except when lounging around the house). I love them dearly and keep them in the hopes that medicine will fix me so I can use them again.
Good morning LAP experts,
I hoping to tap into your vast knowledge of traditional construction techniques with this question. I’ll soon start work on another 6 board chest (dovetailed). The ones I’ve made in the past relied on stays (usually chain) to keep the lid from falling over the back of the chest. I’ve never been too impressed with using stays as they always seem to get in the way.
I’m considering making the lid for this chest a bit wider so there will be an overhang on the back (beyond the hinge pins) that will act as a stop. I’ll be using mitered breadboard ends on the lid so these should mitigate/minimize the issue of a long grain failure of the lid where that extra portion of the lid meets the back of the chest when the lid is fully opened. I’ve used this technique on other chests with satisfaction but they were not very traditional forms.
I’ve looked at lots of chests in the “traditional record” but haven’t seen this technique used very often. I’m curious why that is?
I’d appreciate your thoughts and experience on using this technique on a traditional form.
Thanks,
Brian
Hi Brian,
What you describe is a common thing with tool chests. Sometimes the rear edge of the top has a slight bevel so it rests/stops against a dust seal at the back.
https://www.dropbox.com/scl/fi/jb4evwrmizl4svsjt2vs9/IMG_2923.jpeg?rlkey=af79mpq2ohkehhjl7654mnlq3&dl=0
Other times the lid extends back and contacts the chest body.
I can’t remember the details of every chest I’ve seen, but I would have no reservations on doing it to a traditional piece of work.
Good Morning Chris & Megan,
I recently acquired a small but sturdy workbench at an estate sale. The cost was much less than the cost of the lumber to make a lesser bench. The hardwood top (Maple, I believe) is 60x24x2 7/8. There is a slight delamination (approx. 1/32) between the 6th and 7th boards running about halfway down the bench. Should I attempt to split this section off and re-glue or just fill the gap with epoxy prior to flattening? If I should split/re-glue, any words of wisdom?
Also, a plug for non-algorithmic shop music, The Don Was Motorcity Playlist always delivers. Stream anytime at wdet.org
If there’s no danger of the lamination splitting off, I’d probably mush some epoxy in there, flatten it and hope for the best. It’s a bench, so function is more important than looks.
Hi I was looking at the specs for Tage Frids classic stool and the looks to be only about 7/8″ thick, unreinforced underneath. Most of the seats in your stool and chair designs run around 1-1/2 to 2″. Why do they need to be so thick?
My stools are based on historic examples. Frid’s is a new form. I’m sure all the joinery in the stool will keep it together. I prefer to stick with the old ways and use thick stock, which looks correct to my eye.
Hi Chris and Megan,
After watching the John/Jennie Alexander video on making a chair, I would like to give working on a shave horse a try.
Is there a simple design you could recommend?
I know you’ve said you don’t use them and if I correctly recall some of that has to do with how much room they would take up in your shop.
Using one looks like it would be quicker than using a carving vise.
As always, thank you for your time.
Hi Ray,
I like the English-style shavehorse that JA uses. You can find free drawings for it here:
https://web.archive.org/web/20200927041500/http://www.greenwoodworking.com/ShavingHorsePlans
“Country Woodcraft: Then and Now” also has plans.
I have a few (quite a few) cut nails inherited from a late cabinet maker. I would like to use some of them on a six board chest, as I like the idea of adding some interest to the nailing. How do I avoid splitting the ends or having the ends “pushed out” by the nails. I think a pilot hole would be proper, but I’m not sure of what the size should be. Any thoughts or guidance?
Check out the nailed tool chest in Anarchist’s Design Book. There’s a great discussion is exactly this issue.
Yes, you need a pilot hole when nailing near the ends. I usually do a test joint before nailing the real thing. Select a pilot that is the same diameter as the tip of the nail. Drill the pilot so it is two-thirds the length of the nail.
If the nail bites and hold and doesn’t split, you are good. If the nail holds weakly, reduce the pilot size or the depth of the pilot. If the nail splits, increase the diameter of the pilot and/or the depth of the hole.
Good morning (still morning here) and thanks for doing this. No question this week, but a request: I’m enjoying all the new-to-YouTube content and often find myself wanting to hear more of the background music. Could you please add music credits in the description? Thanks!
A lot of the music we use are just incidental piece like “Guitar No. 6” in varying lengths. Try Shazaam on your phone (if you haven’t already). I’ll try to remember to include credits in the future.
Bandsaw blades: do you sharpen, or just replace? Not sure how much wear and tear all that high speed bending around the wheels causes…
Replace. We use Wood Slicer blades from Highland. https://www.highlandwoodworking.com/wood-slicer-resaw-bandsaw-blades.aspx
Good Afternoon….
I’ve built a few chests using building center pine, with good results. I’m thinking of making a “special” chest for a special wedding present. I’m looking for any ideas that would help spiff up my work. I could go to a hard wood (oak?) or add some marquetry….(I’m experienced with both)… in your experience, what have you seen that makes something Uber special? (Maybe I should pay more attention to the new peasant series?). Any ideas?
I’d take a look at painted wedding chests, particularly among the Pennsylvania Dutch and German populations. Gorgeous stuff.
I also like the ornament done by engraving spells that are particular to the couple. I just did a wedding chest for my oldest daughter and added spells for eternal love and protection from disease and misfortune.
Marquetry was also a traditional way to embellish special pieces.
I’m sure readers could suggest a few other ways. Epoxy. Glitter. Bedazzlers….
Many thanks!…I’ve got some researching to do. Rest assured the only live edges will be used to keep me warm this winter!
“The thought of resawing them makes my butt twitch”
Must remind myself to take a sip of coffee after I read comments here – this one caused me to choke on said sip of coffee….. LOL
“Is this comment how you want to be remembered?”
Why, yes, my name’s not that important. I hope that everyone will remember that I said this.
Thanks!
First, Happy Holidays to all at LAP!
How many habits, not going to address them as “bad” (perhaps needless) but how many habits of wood workers have, that stem from a Jr/middle or High school wood shop class. That seem to be carried on into one personal shop space that really isn’t necessary? ie. “place the plane on it’s side, never face down on the bench.”
I don’t know because I never took shop class. I was drafted into Mechanical Drawing instead.
There is so much misleading dogma in woodworking that it’s hard to get to the source of it at times. I don’t blame shop class. Those teachers were doing their best with what they had at the time.
Instead, when someone tells you something, try it. Try the opposite, too. Most of what I know is from reading, then experimenting and then practice.
I was lucky. Only good habits related to safety. If you visit any of the various woodworking forums or watch some Utube videos the disrespect for any fundamental safety practices is rampant. No efforts to minimize exposures of all types.
I recently built the shaker tray Megan has been posting about and it was quite enjoyable! I do not have much time for woodworking and am wondering what other small projects you might suggest that can be fun, completed in a shorter amount of time, and actually useful in the house or as gifts. (Other than cutting boards and mitered boxes)
Shaker step stool; candle box, pencil box, tool totes
Stick Chair seat question – I found some 4/4 Red Elm & before i buy I was wondering all your thoughts on laminating two together to get a 2″ seat?? Am first starting with stool so no carving the seat, but for future seats I will carve . . .
I really loved the red painted lettering on Megan’s ‘first production dovetail marker’ in her ATC contents writeup and I have tried now with two different paints (to no success).
Chris – what paint/process did you use to get it to stick in the engraving?
TIA!
Red spray paint, then he removed the surface coat w/high-grit sandpaper
Thank you! I actually had half success with model-painting acrylic that I let dry overnight last night but it has to really be worked into the engraving with a fine brush. Spray paint sounds easier.
Stick Chair seat question – I found some 4/4 Red Elm and before buying I am wondering all your thoughts on laminating two together to get a 2″ seat?? I am first starting with stool so no carving the seat, but for future seats – I will carve . . .
ah gheeeez, I doubled up on this post, please ignore!
You can. But it’s a bit of a pain to do it right (lots of glue and clamps). But why not? Give it a go.
My wife would like me to design and make a few pieces of household furniture in the Mission style, but after some online searches, I’m not really sure what Mission style actually is. Can you explain, in a nutshell, the difference between Mission, Craftsman and Arts & Crafts styles? Or better yet, do you know of any good books or other resources on the styles?
Hi Jason,
I collected A&C furniture in the 1990s before building it. Arts & Crafts is the overarching term for philosophy and decorative objects produced during the period. “Craftsman” is usually applied to piece by Gustav Stickley, though it can also be used to apply to the entire movement. “Mission” seems to be used to describe the mass-manufactured stuff.
But all those are fine distinctions (in my book, anyway)..
There are so many amazing books out there. One of my favorites for inspiration is “Arts & Crafts Furniture” by Kevin P. Rodel and Jonathan Binzen. Plus, you can get some of the cheap Dover reprints of Stickley catalogs to get a feel fro the style. I you lived close, I’d tell you to just visit our mechanical library here. I have at least 100 books on the period.
For cutting arcs with the engraving tool, are there feasible alternatives to using a compass? I ordered the tool last week and am hopeful there is a poor man’s way to cut arcs without a stout compass as shown in the video. Maybe a trammel and beam?
Sure. You can make a simple trammel. You also can make a wooden compass that will hold the tool. What’s important is that the distance between the engraving cutter and pin are well fixed. And that you can easily move the cutter smoothly through the arc.
Large arc (8″ radius and larger) are difficult no matter what tool you use.
I’m making a DTC and today looked through my scrap pile for a nice piece to make the tool rack. All my pine is too short but I found a nice little piece of white oak an appropriate size. I’ve read that oak and steel react; would it be a bad idea to use the oak for a tool rack? Dry oak but it gets plenty humid in the summer where I live.
If you wipe your tools down with oil, put a finish on the rack and use the tools regularly, then no. No problems.
But oak and iron create black stains when moisture is present. So I wouldn’t use oak for long-term storage in a humid/wet area.
Thank you Megan and Chris for sharing your weekend time so generously. I was wondering if you have some general advice about order of operations when you start on a piece, whether it is casework, tables, chairs, etc. Do you prepare all part ahead of time, then assemble, or do you prepare components of the piece as you go? I’m trying to optimize my limited time to make some tables, ahead of building a chair or three. Thanks very much!
Hi Ed,
I generally rough-cut everything to length 1″ overlong. And rip to width everything 1/4″ over-wide.
Then I figure what surfacing I need to do to complete the first component, say, the carcase. I surface everything to the thicknesses I need. If other parts from future assemblies use those same thicknesses (say, face frames or doors), I put them in with that batch as well.
Then I rip and crosscut to finished width and length and assemble the first thing (carcase in this case).
If I need to make adjustments to the cutting list for the second assembly (because the carcase changed size, for example), then I have pieces that are over-long and over-wide that I can alter. (Rarely do thicknesses need to change).
Then I surface the wood for the second assembly. If there are pieces in the third assembly that are the same thickness, I put them in with the second batch.
Rip, crosscut and built the second assembly.
And repeat.
May be a little late, but thanks! This is very helpful.
Have been reading Cricket Tables and I am into the first project. On page 77 is the following:
“To finish the assembly drill a single hole close to the shoulder
line of each joint on one face only, without the mating part in
place. Have some scrap on the back side of the hole to avoid
it bursting out. Now lay up a pair of components and using a
bradawl or point-tipped drill make a light mark through the
hole onto the surface of the mating part. Now separate the
two parts and take the same tool and re-mark that spot frac-
tionally closer to the shoulder and farther toward the centre of
the frame.
This has confused me. A single hole?…looks like two per joint. But mostly the very last part…”fractionally closer to the shoulder” I get that part. It is the “farther toward the centre of the frame” that I not sure I understand.
Is the centre the empty part inside the triangle? Would not this pull things apart and not together?
I’ll try to answer for Derek, but you might want to reach out if you don’t believe me.
First, yes there are two drawbores in each joint. Derek is dealing with them one by one.
As far as the offset goes, we are talking about tiny movements. So a bit toward the shoulder and a bit toward the centerpoint of the frame. So diagonally in. This will pull everything tight.
Try it on a sample joint to prove it to yourself. Sometimes drawboring confuses at first….
I just scored Megan’s video on building out the interior of the big-A toolchest—awesome, helpful and inspiring me to want to tackle this long-planned and much needed project. I have a stack of 3/4 inch hard maple in the garage… would this be a good choice for the chest? I think the plans usually call for something thicker but wondering if I’d regret going a little lighter. Cheers to all the Covington Anarchists!
For the exterior? That’s gonna be a heavy tool chest. The plans call for 7/8″ thick because eastern white (or other white) pine is the recommended species. If you’re building out of maple, 3/4″ is plenty thick. And put that thing on casters ASAP!
What species of woods have yielded the best results with the engraving tool? Normally I would try some clear northern white pine but it is currently unavailable where I live and the junk pine sold at the big box stores isn’t cutting it. I received the replacement cutters yesterday. Huge improvement, thanks for sending them out.
I like poplar, cherry, walnut, maple, beech, basswood. And stuff with straight grain. White pine tends to crush if you use too much downward pressure. Oak cuts well when your cutter is sharp.
Just got the Anarchists Design book, love it! Great information presented well. I really like how its printed, it annoys me when I try to read a book and all I can see is light reflected off a glossy page, so the matt finish used in the book is something I am really enjoying. Any chance of you making some videos with Roy Underhill?
Thanks. I was on his show several times. You can find these videos at PBS stations to watch for free.
Roy’s show has been canceled, and Roy has pretty much retired (he’s earned it). He’s coming here to teach next year, but I think his main focus is on a family research project.
Have either of you got a preferred method of marking out a chair seat blank? If you use paper plans how do you transfer the details? Do you hand draw each time or make templates out of something?
I make templates out of 5mm-thick underlayment (which is what we also use to make crates). Hardboard or Masonite are also great choices.
What size and type of bandsaw blade do you prefer for make long chair legs?
Wood Slicer 1/2″ blades. (From Highland Hardware)
Side note, recently, I was looking at the 1/2″ carbon steel in Highland Woodworking. It gave references to some Fine Woodworking articles where 1/2″ blades were rated. Either the Wood Slicer or the brand of high carbon steel they sell ranks higher depending on which 2 of the 3 criteria of the cut matter more.
The 1/2” Woodslicer does a great job on my 14” Grizzly BS. My only disappointment is that they seem to dull quicker than some other brands, but those other brands leave a rougher surface.
Huh. I haven’t noticed they have a shorter lifespan. But if that’s the case, I’m fine with it.
Not a significant difference, but why I always load up on them when HW has them on sale. For feed rate and quality of cut I have not found an equal.
Hi Chris, Megan,
I like working with different wood species just to see what they are like. I’ve noticed there are some torrified woods out there. They look pretty and I’d like to try them in a project or two, just because. Do they behave like the parent woods or diferent and if so ,what ways. Thanks.
Second question. Though I like almost all woods, my favorite is cherry. Mostly I like the way it ages and for hand tools it’s not too bad. Do you have a favorite wood and if so, why?
Many thanks,
Joe
Torrified wood is fine for most stuff. But it loses a little strength during the process. So I would be cautious in using it for a chair or stool or something people sat on. But for cabinets, tables, small projects…. go for it.
I pretty much love all the domestic woods and enjoy working with all of them except cottonwood and osage orange. Cottonwood works like wet spaghetti. And osage orange works like soft brick.
Chris, do you happen to remember which brown pigment stain you used on your campaign secretary? I’m planning on building one and love how the two tone turned out that I see in your book, campaign furniture.
Thank you
I don’t have a record of it, but I believe it was one of the off-the-shelf Minwax pigment stains. One of the brown ones (not the reds).
Any medium brown stain will make mahogany look great. It’s difficult to miss.
Sorry for another finish question…
I’m staining some red oak. It’s taking lighter and darker as expected depending on the grain. My ret top coats are all turning the light areas too “yellow/amber”. I tried oil varnish and tung oil. Suggestions to avoid the yellowing?
Almost all oil-based topcoats are going to add yellow. The only way to avoid it is to try water-base finish, which is generally water-white. It’s so white that it can even look a little blue when applied to light woods such as maple.
When using durhams water putty, do you typically mask off the area around the gap? I haven’t used Durhams yet, but sith “Real Wood” brand filler I’ve noticed it seems to fill grain and change the way it takes up paint.
I do not. But I use it only under paint, so that’s not an issue. Durham’s will fill pores.