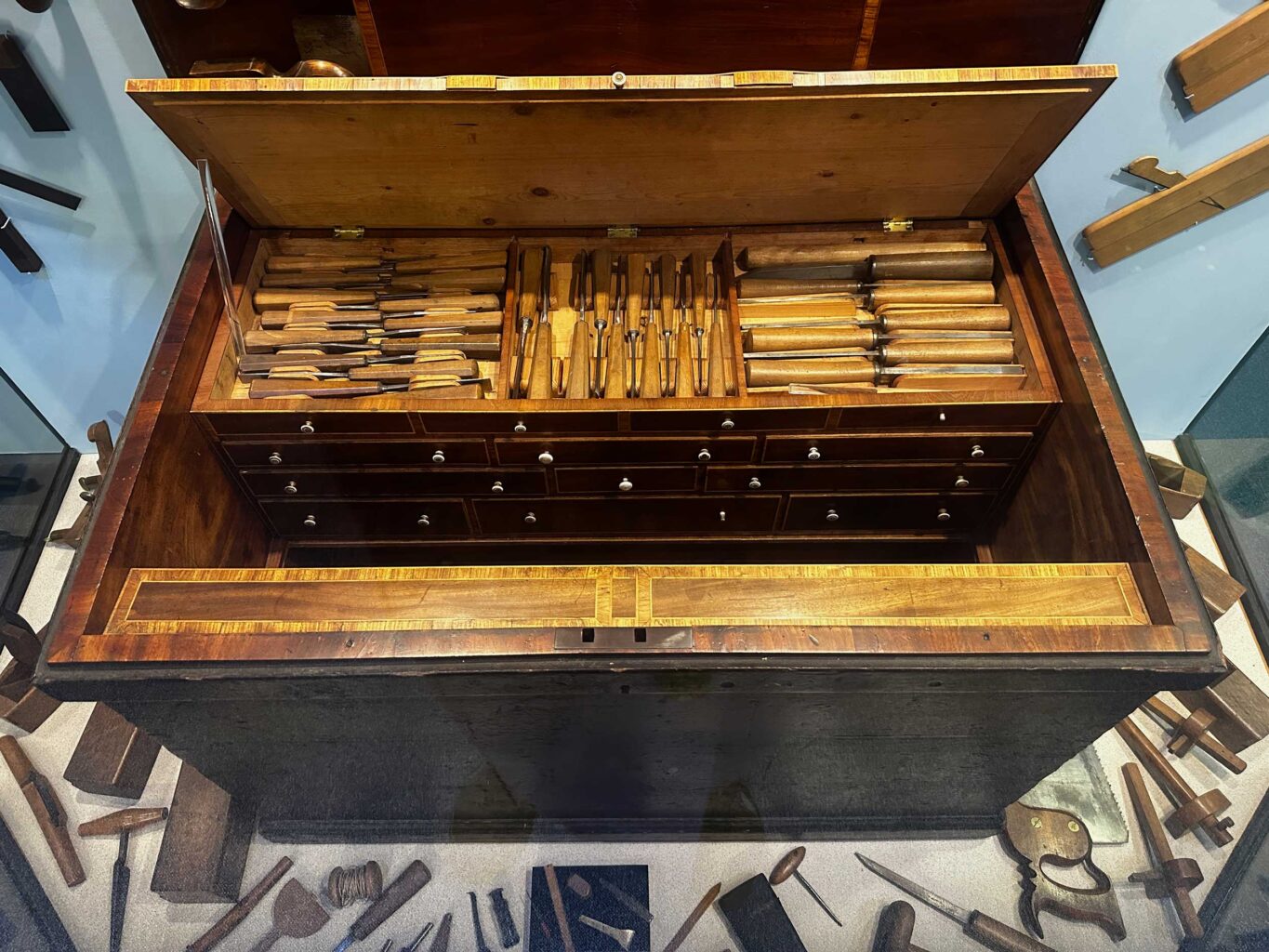
I am back from a fruitful trip to the U.K. where I got to see (finally) the Benjamin Seaton Tool Chest at the Guildhall Museum in Rochester. (More on this tomorrow on the blog).
As you can imagine, things are bonkers here this time of year. Megan, John and I have all been pitching in at the Anthe building to fulfill holiday orders. We are happy to do it. Honestly, I kind of missed it (I have always loved manual labor).
But today we are here to answer your questions. If you are wondering about what to finish a dining table with, click here. If you somehow have some other question for us, write it in the comments field below, and we will do our best to answer it.
Note: Comments are now closed.
— Christopher Schwarz
What are the “greatest hits” for you and Fitz? That is, the questions you get asked most, and wish people would read an FAQ first. Such as, “How do I finish my dining table,” or “Is wood X OK for a workbench?”
You have listed my top two already.
Also: Can I put (this finish) over (that finish)? Can I use (this wood) for (that thing)? What do you think of (woodworking celebrity)? What height should my workbench be?
For me, it’s “when is that book going to be done.” It used to be “what wood should I use for..” I’ll be happy when it is again”what wood should I use.” (The answer, BTW, is soon)
I am craving the next issue of the Stick chair journal. Will there be an issue this year? And if so, will it be available in Europe?
It won’t be out this year. Purchasing and fixing up the Anthe building took up an immense amount of time. I have several of the stories written for the next Journal. I just don’t have the time to finish it.
Good morning all. I was curious if anyone has tried filling small gaps or low spots on a finish with your piggly no wiggly glue. This occurred to me as I read it dries clear. Would it sand and polish, perhaps take more finish on top of it? I know people do this with ca glues and shellac sticks. Thanks.
I have not tried this. When I repair a finish, I use a finishing product. I’ll give it some thought, however.
I have a Ridgid (Home Depot) job site box that is 2’ x 2’ x 4’. I have an idea to line it with fine veneers and fancy tool boxes and tills like the Seaton chest. On a scale of mildly amusing to pure anathema, how would you rate the idea?
It’s amusing. Then maybe decorate the inside of your F150 with fine silk curtains and lacy pillows.
Way ahead of you. Did the curtains on the windows and fringe on the bumper when I got the truck back in ‘99.
I am building a Roman workbench with 2×12’s glued together. I was thinking of using round dowels as the legs. Can I use poplar, with straight grain, and what diameter do you recommend? Should the holes be tapered or can they be through holes?
Thank you
Using large-diameter dowels would probably be OK. I’d use at least 2″ diameter dowels and a tapered joint. I’d be more confident if they were oak dowels.
Welcome home!
I love your books and planning to build The Anarchist Workbench this winter.
I make cedar strip canoes and SOF kayaks but bench building is new to me.
I have a question (technically 2) about about a deviation to attaching the top to the base and 1 question about the stretchers.
You briefly mention that a downside to making a through tenon as opposed to a blind tenon is the need to occasionally flatten the surface of the top as it shrinks and may expose the tip of the tenon. Are there any other downsides to: 1.) attaching the base legs with through tenons? 2.) creating the mortise for the base legs tenons during glue up as is done for the plaining stop?
It’s not vital but I like the idea of visually seeing the presence of the leg tenons on the bench top if it works.
On the stretchers, I wanted to eliminate the front one to allow storage of bulky item under the bench, are there any structural concerns to eliminating one or both stretchers aside from the moral failure of eliminating the possibility of a shelf?
I’m guessing you’ve tried nearly every possibility in your quest and appreciate any brief insight you could give.
Thank you for sharing your skill and knowledge and for being accessible.
Hi Adam,
I’ve made many benches with through-tenons. The only disadvantages are the ones listed in the book. If you want a through-tenon, do it. And You can definitely make the mortises using the laminations. I’ve done that many times before. It adds complexity to the glue-up, but it works.
You can eliminate the front stretcher. Most of the bench’s strength comes from the connection between the legs and top.
What do you think about applying finish to the inside of drawers? Yay or nay?
I prefer not to. I like the smell of wood and the look of a plain planed surface.
But if the customer wants them finished I usually use blonde shellac.
Good morning all,
Just as I think I have an understanding of the world, I get thrown a knuckleball…
In a recent Gift Guide for tape dispensers and clipboards, the source is a supplier called “Puebco”. In my quest for finding unique gifts, I visited their web catalog as they do seem to have interesting products. One item they have listed is a “Lumberjack stool”. Does this make sense? Or is this just the new “live edge” (which isn’t anymore alive than the rest of the plank).
Any reassurance that I haven’t been wasting my time improving my wood working skills would be appreciated!
Wow – $450 for a stump. I’ll sell you one for $400.
It was $650Aus . I don’t want to know the cost of shipping.
Question about which Wood Owl bit to get for creating the holdfast holes in my workbench build – Just ordered two of the holdfasts and saw the video where Chris uses a long Woodowl bit for the holes. It looks quite long – I can’t tell whether it is a 1 inch by 12 or 18 inch. Wanted to be sure, since these are pricey bits. ?Same bit for creating dogholes? Thanks
You don’t have to have the long one to make holdfast holes.
I wasn’t sure – 4.5 inch bench top, plus ~ 6 inch tall shop made alignment jig, plus a little extra
Why doesn’t veneer split (or cause the underlying wood to split) when it is glued cross grain?
This is a complex topic. Some quick answers.
Sometimes it does split.
Usually crossbanding is narrow, so there is little wood movement.
Many times the substrate is white pine, which moves very little. Or MDF, which doesn’t move.
The glue is somewhat flexible and it allows movement without failing.
Sometimes the back of the piece also has a piece of cross-grain veneer. And you have therefore made three-ply plywood.
I have the very neat “Book of Plates”. Is there a companion book (in ‘Merican 🙂 ) which is the companion book that provide the descriptions of the plates?
Thx
As of now we have two books that have translated sections of Roubo:
https://lostartpress.com/collections/all-books-1/products/with-all-the-precision-possible-roubo-on-furniture
https://lostartpress.com/collections/all-books-1/products/to-make-as-perfectly-as-possible-roubo-on-marquetry
And the same team is working on other sections. It is a slow process.
Does the Royal Pawn have a tool section? Any good finds ?
They don’t get a lot of tools, oddly. The other pawn shop down the street seems to get all the DeWalts (and it’s mostly DeWalts).
I will probably be building the AWB sometime in the next year but it will need to be against the wall. If I want to build some chairs using it would it be beneficial to make it wider? (Since I won’t be able to get at it from all sides) I measured a bunch of chairs and was surprised to find the footprint on all of them was smaller than I thought. I’m just thinking I don’t want to get into the situation where the comb is touching the wall and the front legs are off the front of the bench.
When I had my bench against the shop wall, I would just pull it forward a bit when I has some weird piece of work on the bench. If that’s not an option for you, make it 36″ deep and you’ll be able to handle most comb-backs.
Thanks to your wonderful stick chair book I just completed two bent arm stick chairs. They are very comfortable for my wife and kids who are on the small side. I’d like build another one for someone about 6′ and 250 lbs. Do you have any suggestions on what dimensions to change to make it more comfortable for a larger person?
Make the seat wider – maybe 2″ to 4″. The seat doesn’t need to be any deeper. And I’d make sure to use an undercarriage.
When you make stick chairs for clients do you normally wedge the sticks into the seats on the bottom of the seat?
Sometimes I do. When I feel like it. It makes repairs harder to do. But it looks nice. You also have to have every hole looking perfect on the underside of the seat, which doesn’t always happen.
I am looking to purchase my first bandsaw (110v) and don’t feel confident in restoring a vintage Delta and the Jet metal/wood bandsaw you recommend is a little outside my price range. Do you think the cast iron powermatic would be a decent substitute or would you suggest something else?
https://www.rockler.com/powermatic-14-bandsaw-w-2-piece-stand
We had the Powermatic in our shop, and I wasn’t impressed with its bells and whistles. The quick-tension lever was always slipping or breaking. The fence is less than ideal. It’s nothing like the U.S. made Powermatics.
I’d get the JET 14″ instead. It’s basically the same saw (JET and Powermatic are owned by the same tool company). But without the flimsy add-ons.
Chair joinery question!
I really like the elegance of attaching legs directly to the seat. But I also like the look of legs being flush with the seat edges, rather than being inset, as with a staked construction. Here’s what I mean, but with nonsense joints and stock that’s too thin: https://i.stack.imgur.com/xo7gH.jpg.
Is there any joint to achieve this that stood the test of time? And does the answer change for the front legs on a chair with no armrest?
A few things I thought of:
— A Maloof joint
— A similar but simpler housing joint (https://ollypj.wordpress.com/2012/07/27/lets-take-a-seat/)
— A bridle joint (or double tenon, depending on perspective), similar to what is used to attach a Roubo workbench leg, but in the corner
You are basically describing a typical frame chair that has been modernized with a solid seat. Traditional rail-to-leg tenons will work just fine. Then you just need to put the solid seat inside the frame. A Maloof-type joint can work if there is a lot of glue surface. The other solutions don’t seem like straightforward approaches to the problem. The housed joint you linked to is overly complex and wild. The the Roubo leg joint wouldn’t work at the corners of a chair seat. I think you’d need more meat around the tenon.
Thanks! I confess I’ve been avoiding the thought of the frame construction, for two reasons:
1) rail geometry with rake and splay scares me (less so than cutting housings at an angle into the seat… maybe I am crazy!)
2) putting a scooped seat on top of the rails seems to add too much thickness visually
I have not seriously considered putting the seat inside the frame. If I may ask a follow up question, how would you recommend to account for wood movement in this case? I guess it could be frame-and-panel-like, but then I need to have visible transitions between the rails and the seat? Or would I add a thin “lip” to the seat to go on top of the rails, the rest of it being thick enough for scooping?
(I meant to say “more so than cutting housings”)
Lots of ways to do it. A floating frame in a groove will work, as you suggest. Another possibility is to make shop-made plywood with three layers (the top layer thick enough to saddle). Then you don’t need to worry about wood movement.
Hi, I have a question about plow/plough planes. I bought an old wooden one which came with a few irons, but the slot in the plane is 5/8″ wide while the tangs (?) of the irons are closer to 1/2″ wide. Have I got a problem?
Maybe not. Most plow irons have a groove that fits on the skate to hold the iron centered on the skate. If the wedge holds the iron in place, and the iron fits on the skate, the plane will work fine.
Old wooden plough irons look the same, but they are not. They are not necessarily interchangeable. The groove, the with, and especially the thickness of the iron near the cutting edge all matter. As Chris said, if it fits it will work. But many irons will not go into a different plane at all.
In the Anarchist spirit each holiday season I try to make gifts for friends and family. This year using scraps from chairs and other projects I am working on door stops and chop sticks. I am looking for ideas on small simple items for holiday gift giving. Have either of you ever done these types of projects? Is there the potential for a holiday gift guide here? Thanks
I often make Shaker trays, in whatever proportional sizes my scraps will allow (and I match the size of the dovetails to the thickness/width/length – i.e. tiny DTs for small/thin trays).
This year I’m making engraved icons for people. They are all one piece of wood, cut on the band saw. Then painted and engraved. And I’m making glue gummies in the shape of pigs (these will be gifts for woodworkers).
In past years I’ve made Shaker oval boxes (always a fave) and even pencil cups (odd scraps bored out with a Forstner).
A second question if it’s allowed. I recently bought a big box of old tools because of a drawknife and a rusty record 073 I saw. When I looked through the box there was an old no5 and no3, 1890s, can’t remember the type. Both are nicer than what planes I currently have but have split knobs/totes. The rosewood is beautiful, is there anything special about glueing and clamping them together to fix them? I’ve heard rosewood doesn’t like glue
Rosewood doesn’t always like to be glued. Some people use epoxy, which works better than PVA on oily woods.
You also can clean the breaks with acetone or lacquer thinner (which removes the oil from the joint temporarily) and then use PVA/yellow or hide glue.
Even if you muck it up, there are lots of gorgeous rosewood replacement bits on the market.
Good luck!
Chris,
I’m on the “make pretty” day for a couple Gibsons. Due to an unsteady hand while drilling, there are a couple gaps between the short stick tenons and the arm mortises. What is the repair that is likely to look the best on the finished product? Leave the gap, fill with glue and sawdust, try to make a small plug to fill it in? If you would recommend a plug of some sort, would you make the grain match the arm or the tenon?
Thanks as always for doing this!
Very small gaps can be filled with colored wax. We use this FastCap kit: https://www.infinitytools.com/22-pc-softwax-wood-filler-kit-w-custom-tray
It is a butt-saver.
You can try the glue-sawdust thing. But it never looks great when the wood changes color and the glue doesn’t. But for small gaps? Sure.
For big gaps, I’ll use a Forstner that’s slightly larger diameter than the tenon and drill a shallow recess (1/8″ deep) and inlay a fake plug. The plus are usually the leftover waste bits from cutting tenons flush.
Or I patch it with water putty and paint it.
I have a block of bee’s wax. What do I do with it to use it to finish wood?
You can melt it with some citrus solvent to make a paste wax. Or you can heat it with linseed oil and citrus solvent to make a nice Soft Wax.
Here’s our recipe: https://blog.lostartpress.com/2021/07/12/cook-your-own-linseed-oil-wax-finish/
Morning Chris (and Megan). Thanks for continuing to do this. My wife and I are discussing if we want to move when we retire. Given our daughter is growing up in the current home, there is some angst about selling and moving. Did you have any thought pattern that helped when you get past this? It may not come to pass as we really like the community but aren’t fond of local politics/mindset and would like more room for our hobbies (woodworking for me and art for her).
We chose an urban area where we can walk to get everything we need. There are lots of other artisans in the city, so it’s easy to get materials and subcontracting. The less time we spend in the car, the more time we have for living.
Other considerations: We chose the Midwest because it’s very inexpensive and friendly. And we chose to remain in Kentucky to have access to the Appalachian hardwood forest. So wood is inexpensive.
We are 10 minutes from an international airport. And access to all the major freight lines for sending out furniture.
And because we teach students here, we needed a decent food scene.
Even with all those things working for us, this is not an easy life…. but I love it.
If I am batching out sticks like you showed in the Stick Chair Video, but with hand planes and a band saw… I start with a flat face and square edge. Can I keep running the band sawn edge against the fence, or should I square the edge of the blank before each pass? And likewise when I turn the resulting stick blanks 90º to cut in half.
The green Merterks level I’ve found will only self-level if the device is already very close to level, maybe 2-3º. Do you use a different one for when you are using the self-leveling feature (tapered legs/sticks, etc)?
Hi Max,
1) I’d have no qualms running a band sawn edge against a fence for a chair stick. It is going to get shaved and tapered, so it doesn’t have to be perfect.
2) I use the same laser level for all operations. I just have to find a place in the shop that is close to level when using the self-leveling feature.
Chris, Megan and crew,
Hope everyone is doing well. And, y’all had a wonderful holiday with family, friends, etc..
I hate to ask, especially since I own a copy of every workbench book you’ve authored, but I have two (2) workbench questions; albeit, I beleive the questions to be outliers.
1) 2-Day Workbench – Leg vise: Would be see an issue with boring a hole through the seam of the composite leg; for the installation of a (+/-)1″ metal screw? Or, possibly a (+/-) 2″ wood screw (say Lake Erie)?
2) Henry Boyd Bench – Fasteners: In reviewing the blog post photos, it appears most of the fastening is nailed. Could you elaborate on style, size, etc., of the nails? My, apologies if I missed this info is within the body text.
Many, many thanks!
btw Chris,I really enjoyed your latest AP post regarding the coffer. Very inspirational.
Hi Matt,
1) No problem boring through the leg whatsoever.
2) We used large Rivierre nails. I don’t remember the exact sizes. But they were almost classified as spikes.
Excellent.
Thank you.
You talk about chair repairs being easier with hide glue. Which is why I use it. But a video or description of how you go about a repair would be really helpful. I’ve never had to make one yet. And I’m just unsure about say a typical loose tenon on a leg or stick. Am I heating up the old glue? Am I scraping the old glue off? Am I heating up the old glue left and just simply adding more glue?
Hi Scott,
We’ll put that on the list of videos.
For shallow joints, a wet rag and a clothes iron will loosen the joint. For deep joints, I wrap the area with a wet towel and use a heat gun (which gets much hotter than an iron). In both cases, the heat reverses the joint. The water can carry the heat or protect the wood from scorching.
After the joint is apart, I make whatever repair is necessary and just add more warm glue. With hide glue you don’t need to scrape off the old stuff.
Thanks!
Good Afternoon,
Thank you for taking the time to do this again today. I really enjoyed your post on the Seaton Chest saws. I had looked at the Blackburn Tools kit a year or so ago, but got busy and never ordered one. Your recent post got my gears turning again. I noticed that the plate is not taper ground like most modern hand saws. I was curious if the lack of taper grinding would cause any performance issues, in your experience.
Thanks,
Jacob
Chris, just a reminder. You have (I think) two panel saws that are virtually identical except one was taper ground and the other not. Might help answer the question: Is there a noticeable difference?
There is.
Yes, taper grinding makes a difference. The saws are heavier and there is more friction in the cut. I prefer a tapered plate, but if you aren’t making a living with your saw, I wouldn’t worry about it too much. Both forms work. One is just a little more tiring to use.
I appreciate your response and perspective. Thank you!
I recently made 2 stick chairs from your TWW guild course (which was a fantastic introduction to chairmaking btw) and, as forewarned, I’ve been wanting to make some more. I’m most interested in the staked chair from the ADB for a set for dining chairs and have some reservations about the crest rail. I can’t find any reliable sources of air dried wood and am hesitant to try and steam bend kiln dried stock. The other option is a bent lamination, but I’m sure that comes with its own challenges/issues. Should I just get over and ‘go for it’ RE steam bending or will a bent lam work out fine?
A bent lamination will work. Or make it easy on yourself and cut it from solid. Most of the backrests/crest rails were either steam-bent, cut from solid or used a curved branch from the woods.
Will there be a table in The American Peasant book? I know you are homing in on the finish line there and can’t remember if there was any table talk included. If there is a table project, can you recommend a finish for it? (Too soon?)
I wasn’t happy with the cottage table I built for the book. I might make one more stab at it.
I appreciate that you (all) follow your gut when it comes to this stuff instead of pushing out something you aren’t satisfied with.
I’m nailing the bottom of my tool trays together for ATC. What is a good method of holding the bottoms in place in the proper position, that is in place and keeping the frame square, on the tray bodies for pilot hole drilling? When nailing should I proceed one nail at a time and slowly shape the frame like you do sometimes when framing?
I always turn the tills upside down on the bench, then align and firmly clamp the bottom piece(s) in place (one at a time, if more than one piece), and drill the pilot hole at one end, sink the nail, check the alignment (fix as needed), then drill and sink the nail at the other end. If all remains in place after sinking one nail at each end, it’s safe to go ahead and drill/drive the rest. I leave it clamped, though, so the assembly doesn’t skitter around.
Thank you Fitz.
Chris Williams stick chair question…
I saw a picture of Chris (from LAP class) with a long stick part-way into the test hole in a wood block (clamped in a vise). It looked like he was pulling on the stick.
Was this to check overall form and size or to see where the arm now would stop? Something else?
While traveling for Thanksgiving, I read Good Work and then read through many blog entries after searching “Welsh chair”. Thank you for publishing the book and all that info in the blog.
“Arm bow” not “arm now”…
I suspect he was testing the tenon on the stick. He does that in a hole in a block clamped in a vise.
Long sticks and their shape are tested in the arm bow itself.
When you make your own paste wax, where do you get the raw linseed oil?
Amazon seller – the hardware store nearby sometimes carries it, but only in the quart size, and Katherine needs it by the gallon.
What are your secrets for gluing up an armbow without gaps? I’ve been working on my second four piece arm now, via Stick Chair Journal description. I think my mistake is that I tried using curvy grained wood that naturally flowed around a knot for the two outter arm pieces, and no matter how “flat” I plane the glued up bottom lamination, and how flat the shoe is, the two do NOT want to lay flat to one another. My first one I glued up and have just a few small gaps (I need more clamps), but my second one is appearing worse. I’m tempted to just clamp the bejeezus out of it and hope the hide glue erases the mistakes. I do imagine this would be easier if I’d used simpler grain pieces to begin with.
Try a thinner shoe – 5/8″ is strong enough. It’s much easier to clamp out gaps. And I do clamp the holy moley out of the armbow when assembling it. You’ll get there. It takes some practice. My first armbow was garbage.
If I don’t need to peen over a proper cut nail, will a sorta old “concrete” nail hold as well? Any related wisdom I should consider with it? Thanks much.
I would not use those for furniture. One of the superpowers of not-concrete nails is that they bend, allowing for expansion and contraction of the pieces they are securing. Concrete nails do not bend.
Thanks much. I figured if they would you folks would have mentioned such. Also thought maybe I had missed it if you did.
They also have a much bigger taper than the furniture nails. They love to split wood.