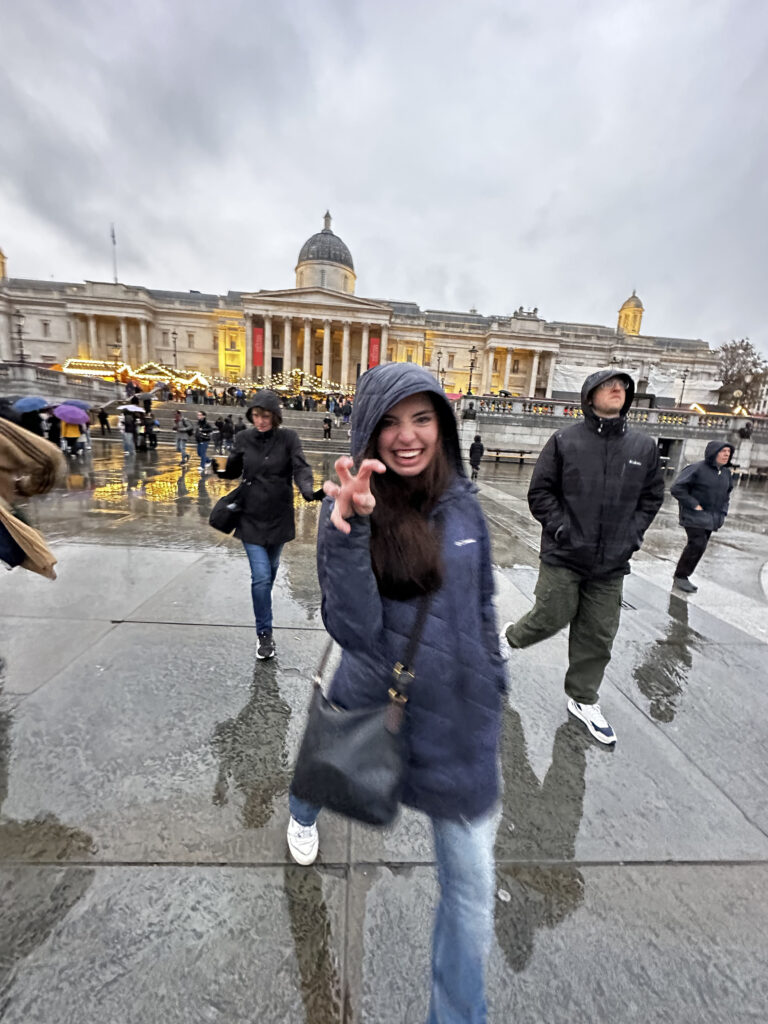
Apologies for the late start today. Chris and his family got home late last evening from England so he’s recovering from jet lag…and I slept in today and had a leisurely morning coffee for the first time since they left. Then once the caffeine kicked in, remembered I forgot to post this.
You know the drill: Post your woodworking questions in the comments section and we’ll do our best to answer. Comments will close at around 5 p.m.
– Fitz
What’s the meaning of life?
You are in a cheeky mood this morning
when i realized i had a chance at the 1st question of the day i panicked and couldn’t reach my towel.
42
The only answer there is.
Good morning! Any plans for a new “Sharpen This” video? I would certainly appreciate one on skewed blades.
Oh lord, skewed blades are the worst. Usually my first question is: Why do you need a skewed blade for this operation?
We do need to make some more videos…. thanks for the reminder
I am considering upgrading my rusty ol’ rebate plane (Stanley 78?) to a fancy-pants Veritas. But the skewed blade is giving me some hesitation. The blade on the 78 is already a PITA to sharpen (too shallow for my honing guide) and I haven’t had a great experience with it overall. So I figured, what the hell? Might as well get the instant gratification of a new tool and hopefully struggle less.
Ah. Well the Veritas is a good tool. But it has a lot of adjustments that can be fiddly.
I mostly use a straight rabbet I got from Matt Bickford. Happy to show you how to use it both with and across the grain sometime. I love that plane. So simple.
i have the veritas skew rabbit and love it. my observations: 1) i don’t need to sharpen it very often. unless you are using it to raise panels, it’s not making show surfaces. 2) i free hand sharpen (the guide is to slow for my taste) so don’t find it that much more difficult than a straight blade.
It’s no trouble until you sharpen it a little off angle, which happens eventually. THen it’s a life of misery.
I need to glue-up chair seats and want to use tenons to ensure that the joint stays together. Chris uses 4” x 1/2” tenons, which seems really big. What is the smallest size tenon I can use and still have a “life-time” joint? Do you see any issues with using pocket screws instead of tenons?
The minimum I would do is 2-1/2″-long tenons – that’s 1-1/4″ into each half of the seat.
Pocket screws, like any metal fastener, can come loose when stressed. So I prefer loose tenons. But if pocket screws is what you’ve got, use those.
Over the years you guys have said you use jojoba oil to protect the metal surfaces of your tools. To your knowledge, is jojoba oil jojoba oil? I bought “100% natural, pure cold pressed jojoba oil, Grade A” from a cosmetics site online. When I use it on tools it gets tacky with time like, say, linseed oil would if it’s not curing properly. Am I doing something wrong? Am I using the wrong kind/type/style/? of jojoba oil?
We have bought it from a variety of sources and have never had this problem. How thin are you applying it? We are trying for the thinnest coat possible. Just a wipe with a rag.
Maybe someone else has some thoughts?
I had a similar problem with jojoba oil.
If I lightly oiled the tool, and then didn’t use that tool for several months, it got a bit sticky.
I have since switched to Camellia Oil and, so far, nothing has gotten sticky.
The Camellia Oil was something I found on Amazon.
Other brands may behave differently.
Do a search for:
KUROBARA 100% Pure Tsubaki Japanese Cutlery Knife Maintenance Camellia Oil
To extend the jojoba oil rust prevention conversation started in the 10:00 hour…
I would agree on using the thinnest possible coat of whatever oil on rust-prone metals. No need to coat it with a heavier layer. It should be almost imperceptible after the wipe down.
I’m using a rag lightly dampened with 3-In-1 Oil. A quick swipe and I’m done.
A light wipe with food or pharmaceutical grade mineral oil (at your local pharmacy) will [should] also serve the purpose. Has anyone got experience using this type of mineral oil to prevent tool corrosion?
I’ve had that problem when I’ve not used my tool for a while – I got a sticky saw blade when I was too busy going to meetings to do any woodworking at PWM 🙁 But it’s easy to fix – wipe the offending area with mineral spirits to remove the oil.
Now that I use my tools and planes a lot more often, they don’t go sticky.
I tried jojoba oil in my unheated garage shop. Once the weather turned cold, the oil crystallized. Caveat emptor.
Fitz, any chance of a Dutch Tool Chest series with the Wood Whisperer?
Maybe? But first, I’m finishing the book.
Hallelujah
I’m looking for a catalog of touchmarks on (preferably vernacular) furniture. When I ask Google, it only wants to sell me touch up markers. Y’all have any recommendations?
try this:
https://cse.google.com/cse?cx=e07a93217e4e84f6a#gsc.tab=0
It’s a google search engine that eliminates many of the big box stores/retailers from the results including IIRC amazon, ebay, etsy, and the US big box stores (it does not eliminate sponsored results). I got tired of searching for something only to be flooded with 10 pages of retailer hits.
I forget how I did it, but google has a way to create search engines for your website to limit results. You can have it keep the results within your site or restrict specific sites. Not too difficult to do. I forget how I did it but google it and you’ll find it.
Touchmarks? Do you mean signatures or stamps?
Very few vernacular pieces are ever signed. So you are unlikely to find much there. If you do, bravo!
As far as furniture marks, there are people who collect images like this. One is Joshua Minnich. His Ephemera books are not about furniture, but are about labeling in general. https://joshuaminnich.com/shop
Sorry I’m no help here.
I have been constructing a book case from Poplar bought at the sawmill/lumber yard. I am in the finishing stages. I have taken it through the following to make it ready to use and prepare it for finishing: planer, belt sander (80 then 120), orbital sander (80, 120, finally 220). After I have smoothed it down to what appears a smooth surface and I leave it alone for a few days it seems to fuzz up again and need sanding again. I have been through the sanding process a couple of times now before finally giving up and moving forward. Do you have any thoughts what might be going on? I am guessing it is a humidity/dryness issue. This is a time when the ambient humidity changes quite a bit and I am not sure how dry the wood was to begin with.
Thanks,
Scott
Hi Scott,
Chances are that humidity in your shop is raising the grain a bit. The best way forward is to apply the finish. The grain might get raised again, but you can then knock it down for good with some fine 320-grit stearated sandpaper or fine steel wool. Then apply another coat of finish on that leveled surface.
Some woods are inherently fuzzy and difficult to finish. So don’t be too surprised if this poplar fights you back.
Thanks very much
Thanks for taking the time to share your knowledge and experience with us, Megan and Chris.
Among the woodworking tools, the rasps and files are somewhat of a mystery to me. Do you have any advice on which ones to buy for a beginner?
I use two rasps almost exclusively:
What’s more important than the brand is that the rasps be hand-stitched. These cut so much better than all the machine-cut rasps I used. Yes they are expensive. But they last a lifetime if cared for.
On files, I use those for metalwork mostly. Some woodworkers use them for wood. But I can’t help you there.
Planning on making both to play with them but you talk about two different sized does feet: a long narrow one (~3”x24”) and a short chunky one (~6×16”)
Which do you use more?
I have so many under my bench I couldn’t say. Mostly, I differentiate them by thickness. Sometimes I need thin ones for dealing with thin stock. Or thick ones for holding chair combs or weird big stuff.
Definitely make both. And when you get stuck, make some more….
Good day to all. Today I am moving shops for the second time in my life. First time it was cross country and easy since my tool addiction was at its very beginning. I find myself moving again this morning, only across town, but my tool assembly is vastly greateR! The number of boxes has quadrupled, including all of the planes, specialty planes, braces, spare parts, cutters, chisels, spokeshaves, panel saws, backsaws, handsaws, and single bandsaw.
So if you’re still with me after this lengthy introduction here’s my question. Is there a system, or process of elimination you use to determine what stays and what goes/gets donated/ sold when you decide to “downsize “ and make your life easier?
PS. I also have two workbenches, one Nicholson, and a 2×4 with a plywood top. Those stay regardless. One is mybwoodworking bench, the other is my machining/grinding/belt-sanding work area and I love having them separated.
Have a wonderful weekend y’all!
Graham Blackburn has an excellent system for rooting out unnecessary tools. If he hasn’t used a tool in a year’s time, it gets sold. I have followed that advice for years and totally am on board with it.
However, I work at the bench every day. A home woodworker might want to consider a two-year grace period.
Mostly, look for redundencies at first. I have one smoothing plane, one jack, one jointer. The best of each. I have three band saws because we teach classes. I have three cutting gauges because that’s what it takes to layout dovetails and mortise and tenons.
Every tool has a reason for being in my tool chest or shop.
Good luck!
Does soft wax work as a dining table top finish? What do you prefer to use for dining table tops?
https://blog.lostartpress.com/2023/11/12/a-finish-for-the-top-of-a-dining-table/
Can a Hickory work for a cutting board?
Sure. My take on cutting boards is non-conventional. I prefer softer woods (like poplar), which are easier on my knife edges. And I don’t mess with finishes on my cutting boards. But mine are butt-ugly.
Two questions if you will permit. First, I was wondering what you recommend by way of a mobile base for a bandsaw. I have a 14 inch like the one you have, and I’d like it to be stored out of the way when not in use.
Second, if you had your choice of wood for a gibson chair, what would it be? Anything that would be particularly historical?
Thanks!
I made my own mobile base (home center casters and 2x4s) because I wanted to increase the height of the table a bit.
I’ve been satisfied with Grizzly’s mobile bases in the past. They are a good value.
On a Gibson chair, if you are going for historically correct, look to what woods are in Ireland and would have been imported to the country. Oak, ash, maple (what they call sycamore) were all common construction materials.
Would love to have a beading plane but not wanting to restore an old one. Would you think the Veritas combination plane would be a good choice? Pricey but also has more uses than just a dedicated beading plane.
The decorative irons for all combination planes were designed for carpenters working on moulding in houses. As a result, they sometimes struggle to produce perfect profiles in harder woods because the combination plane does not have a mouth. If you are working in pine or poplar that will be painted, a combination plane is ideal. If you can pick your wood with upmost care so the grain is running perfect for the bead, you can use a combination plane.
I recommend you buy a dedicated beading plane or make a scratch stock (very cheap and easy) if you don’t plan to make a lot of beads.
Old beading planes can be difficult or impossible to restore. So unless you know what you are looking at, I usually advise people to buy a new one from someone like Matt Bickford or Red Rose Reproductions.
The Veritas combination plane is fantastic. I have one. But I don’t use it for beading.
I need some advice about finishing. I’ve made a small box as a gift for a friend to hold letters he is receiving from friends in honor of his birthday. The box measures 9” x 11-1/2” and uses two types of wood – cherry and hard maple – joined with dovetails. The long front and back pieces and the bottom are hard maple, and the side pieces and lid are cherry. The end grain of the pins of the cherry sides contrast nicely with the light-colored hard maple. The only fasteners are two hinges for the lid. I want to use a finish that doesn’t change the color of the wood and perhaps might even allow the cherry to darken over time. I’m thinking of wiping on a 1:1 mix of polyurethane and mineral spirits, but I’ve also read that a 1:1:1 mix of poly, mineral spirits, and boiled linseed oil might be better. Any thoughts on that? And also, given that the box won’t be subjected to any heavy use, how many coats do you think I should plan to apply? Would three coats be enough, or should I plan for four or more? Thanks.
All finishes change the color of the wood at least a little. If you want the minimum color change, your plan to use a wiping varnish (50:50 mix) would be best. The oil will add more yellow to the maple.
Wiping varnishes should be applied very thin to the wood. Like as thin as possible. Wipe it on and remove the excess. Let it dry. Level the finish with some very fine 320-grit stearated sandpaper. Then add another thin thin coat. Two coats offer enough protection. But perhaps not enough lustre. Where you stop is more about looks than protection (after two coats).
Good morning and thanks for doing this!
I am making some staked cherry kitchen stools. Just managed to drill an oversized and slightly conical stretcher mortise into one of the octagonal legs. The 5/8” tenon has a full 1/16” of wiggle room in there.
Could I put a blind wedge into that tenon to fill the space? Anything else I should try, or shall I just make a new leg?
Hard to say exactly what should be done. One approach is to make the hole 3/4″ with a Forstner. Plug it. Then re-drill for the 5/8″.
Hi,
I am working on saddling the seat on a chair and find that the arthritis in my hands has gotten to the point I can’t effectively grip the scorp. I watched a couple of videos on using an angle grinder and a carving disk. Have you ever tried this and how did it work?
I have used an angle grinder with a round cutting disk to shape work. It’s dangerous. Period. There is no guarding that can protect you.
If you want to learn to do it, check out Charles Brock’s website. He uses these tools a lot and has recommendations about what he likes and doesn’t like.
Good luck!
Checked it out, thanks. I went to harbor Freight and bought their cheapest angle grinder ($14) and a $19 cutter. Tested it out on a seat blank, armored up gloves, face shield, dust mask, and hearing protection. 15 minutes and it worked better than I hoped for, a couple more practice blanks and I think it will work.
Good morning and thanks for doing this! I received my Mk.2 Crucible Bench Square a week or so ago and have a design question: after figuring out how to register at an edge and draw the various angles, I attempted to try an edge – that is, hold the inside of the big 90 against a board corner. I was surprised that this doesn’t work – the drilled corner of the 90 is inside the “handle”.
This was surprising. But, looking at the online photos, it seems consistent, so I’m wondering why? The best I’ve come up with is that you can’t draw a 30 or 60 line to the edge of the board if the corner isn’t below the edge…
There seem to be several carefully thought out features on this version of the square that I can’t quite grasp (like the small squared off tips). Maybe a video is needed!
Get some rest, or at least more coffee…
That was intentional. If you want to use the inside 90° to check edges, simply pare away the part of the handle that interferes with the operation. I use a big chisel. It’s a five-minute operation.
I concluded that it was intentional – but why? What do I lose (if anything) by paring away that section? I mean, I have other try squares. I’m trying to understand the design choices (to be clear, this is not in anyway a complaint).
Because of the assembly process – that was how we were able to fully seat it…push on the center of the blade.
There was no way to get the intersection of the two angles exactly coplanar with the handle 100 percent of the time. It is wood. We could
1) Put the intersection below the handle (which is what we did). This allows you to mark the inside angles on your work right up to the handle. And the user can modify the handle if they want to use the tool to check edges.
Or we could put the intersection above the handle. Then you cannot mark the angles right up to the handle. And you cannot modify the tool to fix that problem.
Hey Y’all,
I really enjoyed Claudia Kinmonth’s Irish Country Furniture and Furnishings. Do you have a recommendation for another book in the English/Irish country furniture style?
Try:
“Scottish Vernacular Furniture” by Bernard Cotton
“English Vernacular Furniture 1750-1900” by Christopher Gilbert
“English Country Furniture 1500-1900” by David Knell
Those books and their bibliographies will keep you going for a long time.
Awesome, thank you!
For my first workbench, I’m thinking of building a Roman workbench (4-leg Herculaneum workbench) out of home center SYP. Do I just laminate two 2x12s together heart side to bark side? Does it matter which side is the top? And if I’m making the bench with four legs, will the leg dimensions need to change if they’re made of SYP?
Yellow pine is excellent for this sort of bench. Laminate the boards as you planned. Use the heart side as the working benchtop. For the legs, use tight-grain SYP that is very straight and you will be fine.
Hello. Getting setup in my garage for hand tool only work (no space for machines). I already bought ATC, but I’m looking for a book with a bit more specific help with hand tool setup & use. “Wearing” or “Hayward”, to start? Thank you 🙂
“Essential Woodworker” is a great starting place. The Hayward books are like having a set of encyclopedias in the shop. You’ll get to the point where you need/want it. But start with Wearing.
Good morning Chris & Megan
Two questions:
1. What is your go-to fry-pan/skillet?
b.. Do you roast your Thanksgiving turkey with stuffing?
Have a great holiday weekend (anarchists celebrate Thanksgiving, don’t they?)
I use Harbor Freight kitchen tools.
I have an All-Clad skillet we got when we were married. Copper core. It’s the nicest pan I own (besides the French Dutch oven I inherited).
I roast the dressing in a turkey bag. That’s so it gets crispy. And we can make 200 pounds of it.
I have an old, cheap, no-name skillet I bought years ago at a kitchen supply store. I really should get a new one.
Dressing…not stuffing (that is, not inside the bird.)
Hey folks! Thanks as always for this saturday activity.
Two questions:
I am making a pair of gibson chairs soon. I plan to use oak or hard maple for the legs and sticks. I am thinking I might use clear Douglas Fir for the seat and backrest and arms. Does this make sense or should I use a harder wood for any of these pieces?
Related, I made a pair of saw benches as discussed in ATC (or maybe ADB? one of those.) I made them all out of dimensional DF. They work but a couple of the legs wobble like a loose tooth. Maybe the oak wedges should have been bigger? Maybe I should have made 100% sure the shoulders of the legs touched the body? Maybe I somehow didn’t use enough hide glue? I know I’m not giving you enough to go on here, but any suggestions on common mistakes for legs would be helpful. I’m happy with the sawbenches but I really don’t want to make that mistake with the chairs
You can use Doug Fir for the seat. You need tight joints. Well-wedged and fit. Lots of glue.
But if you have maple for the seat (soft or hard) that is the superior choice, especially in a chair without an undercarriage.
I’m not shameful or embarrassed to say I am a caffeine addict. With regards to you waiting for your caffeine to kick in, how do you drink your coffee? Black? With cream or milk? Flavored creamer? I just discovered French press coffee and it has opened a whole new world to caffeine consumption. Highly recommend.
Espresso. With a little brown sugar.
Nice!
With milk (pref 2%), no sugar.
Less than two years ago, I bought the BT&C dewaxed shellac flakes, blonde and garnet. I’ve used denatured alcohol before but decided to use the Everclear grain alcohol (150 proof is what I can get in PA). I pulverized the flakes down to very fine flakes, almost powder. I’ve mixed both a two pound and one pound cut both stirring and the shake the jar often method.
In past experience with Hock shellac flakes and DNA, I’ve had some flakes not completely dissolve, but with the BT&C/Everclear mixture, I had a small layer of undissolved shellac on the bottom of the jar, with about a quarter inch layer of a very light colored “pudding” texture on top of that. I’ve never had this issue before. The look reminds me of Zinser “waxed” shellac when the wax settles after sitting for awhile. Of course I strained the mixture through a coffee filter to remove the goo. Any thoughts? Could the flakes be old?
150 proof has too much water in it. Use the 190 proof.
We’re your flakes exposed to heat? I have 30 yr old garnet, orange and brown shellac flakes that dissolve readily in 190 proof. Always stored in a cool dry place.
Blond dewaxed shellac can oxidize. This gets worse the more surface area is exposed. I store my flakes in Ziploc bags with most of the air squeezed out. No problems so far with flakes which are four years old. I had some ground shellac that behaved as you described, even with 99% ethanol.
As the others mentioned, try alcohol with less water but if that doesn’t work your shellac may indeed be off.
AFAIK this is only a problem with blond dewaxed.
One more question: Fitz, you sure you drank enough coffee? The title of this post is Nov 14 haha
Clearly not.
I am making two backstools (Anarchists Design Book Chapter 16). The arc of my crest rails has a longer radius than the arc of the back edge of the seat and the arc of the spindle mortises.
What, if any, adjustments should I make to the resultant angles for the outboard spindle seat mortises crest rail mortises?
Or reshape the seat to match the crest?
Or make new crest rails?
Or make a rectilinear dovetailed box instead.
You are designing a new chair, really. When I do this, I mock it up. Make some scraps that can hold the comb where it will go over the seat. Then use dowels and sticky putty to mock things up. This will help you place the spindles at the right locations in space.
Measure the angles (rake/splay) for the outside spindles. Drill those. Make the spindles that go in those outer mortises. Then make a thin plywood template the shape of your comb. Screw it to the ends of the outside spindles. Now use that template as a drilling guide to drill the mortises in the seat.
Use the plywood template to mark the mortise locations on the comb. Drill those.
Or change the back shape of the seat as you suggest.
Thank you. I will make some new crest rails. I may even try bending them. Being available and willing to take these questions is a service beyond measure.
Trying to get away from the nasty denatured alcohol for my shellac and, as I posted earlier, can only get 150 proof grain alcohol in PA. Anyone ever use the “culinary” grain alcohol?
Thanks!
Drive to the state next door, and stock up.
You can also use 100% isopropyl alcohol in a pinch. It’s worked fine for me when I ran out of denatured alcohol, which is no longer sold in CA.
I have not used culinary grain alcohol. Sounds interesting.
There are many options if that doesn’t work. Chemical supply companies will sell you pure ethanol if you sign a certificate that says you aren’t going to drink it. As I recall it was easier to do than it sounds.
I have, in a pinch, put the alcohol in the freezer overnight. The water froze. The alcohol didn’t. That helped.
Hi,
After years of trying, I finally have a shop. The building is complete, and with a little luck I’ll have electricity in a few weeks. I’d like to add dust collection. I’ve read articles and looked online, and ads make everything sound great. The shop space is about 23’X38, and I plan on having the usual complement of machines. I’m wondering if you have any recommendations.
look for a system with a back purge to keep the filter cleaner. Also, a can before the system can also help reduce filter changes. Highland and Grizzly both have some good systems. Determine where you are going to locate it (or make it movable), verify how many amps and voltage it needs. Last but not least, how loud is it?
Dust collection is one of those third-rail topics that I simply will not engage in. We use standalone dust collectors with canister filters. I have lost too many hours unclogging central systems. I’ve chased down too many faults and shorts in electric gate systems.
We keep it simple. Short runs. Manual gates. Good canisters.
FWIW, I have an Oneida cyclone and love it. No more fine dust all over the place the next day.
One of the short LAP videos I watched recently had a fiddle tune background that Chris identified as being from “The Mountain Minor”. I had never heard of the musician or the film before, so I hunted it down. Thank you SO MUCH for this – especially for leading me to the amazing voice of Elizabeth LaPrelle.
When you paint your chairs with General Finishes Milk Paint, do you apply a top coat to the paint? Wax perhaps?
Thanks
No topcoat is necessary (I never use one)
Two questions, if permitted:
1. Any update on when the dutch tool chest book is going to drop?
2. Are there any drawings for the saw holder that’s attached to the inside of the lid?
Soon. And no – those break…so I’m showing other solutions.
I need advice on how to make a board an eighth inch wider.
Board widener.
Move to the Amazon.
Any updates on lump hammers for the holidays?
Gosh I hope so.
Hmm, not exactly informative.
Looking to purchase them for my crew, it would be nice to know if it’s a possibility before I purchase something else from someone else.
Will there be any more classes on making a sector?
Not by us. Brendan Gaffney taught that class and he is in New York now.
Hi folks, thank you for everything you both do! Quick finishing question as I gear up to build my ATC. Do you use a topcoat over the General Finishes milk paint?
No topcoat needed (I never use one)
Thank you!
My chair build questions posted at 1:06 have failed to elicit any replies. Have I failed to understand how this works. Ought I to have addressed my questions to Chris? Should I have mentioned my cats?
Hi, I am ready to get into boxmaking (I have a tiny 5 foot bench I built for my apartment). Christ listed Drawer Lock Chisels in his list of essential tools for the Anarchist books (I think). LN stopped making them, can’t find any modern makers of repute. was wondering if there are workarounds? Think specifically for smaller boxes like jewelry…
Thanks!
A blacksmith can make you one easily.
I will use a butt chisel and remove the handle when working in tight spaces.
Hi friends! Two sharpening questions.
1. I bought the peasant cutter and have been avoiding sharpening the other side. You recommend the topin oil stones. However even the smallest diameter stone doesn’t quite fit into the tip of the cutter, which seems like the spot you most need to access. What am I missing??
Not sure if you remember but in the chair class I took in September I brought my eBay scorp to class. It was close but not quite sharp. Chris you were going to show me how you sharpen it but we all ran out of steam. Do you mind sharing what you would do to such an item??
Bonus question. You’ve mentioned black wax here and there but I never figured out what that is. Automotive wax is what shows up when I look for it.
On question 1: you have a defective cutter. There were a few that were not pear shaped. they were arrow shaped. Send a message to fitz@lostartpress.com and we’ll send you new ones.
On 2: I use a table saw with a metal disc in it. No way to explain it here in a blog comment. Here is a video I did for Fine Woodworking on the process: https://www.finewoodworking.com/2023/08/28/how-to-sharpen-a-scorp
Black wax. It’s colored wax. I use Liberon Black Bison Wax in Dark Oak.
https://www.rockler.com/liberon-black-bison-fine-paste-wax
Afternoon Megan. I’ve noticed on the ATC’s that you nail on the bottom rather than screw it in. Any other reason other than historical and time has proven it works well.
Gibson Chair question (s)
I recently found @thecidermillslane 2017 IG posts. On the joint between arm and back stick, were many of the chairs in his collection with a birds mouth? Do you know the order of operations to get it to fit so snug? I was imagining planing the stick after the cutting the vee in the arm.
Thank you
The way I do it in the video is to use a 1″ dia. washer on the bit extender to scribe the position of the stick on the arm. Then there is a little shaping on the stick to get a tight fit.
Thank you.
And on the birdsmouth…. I didn’t make a count of what the intersection looked like on all of the chairs. On some the arm didn’t intersect the stick. There was a good deal of variation.
A theatre trick we used to make a board wider… cut the board in question apart with a shallowest angle across the board, then slide to two parts uphill to each other….as they climb the angle the board is widened…
FYI, I am the “you probably feel idiot” who suggested you want to consider a work vest…lol