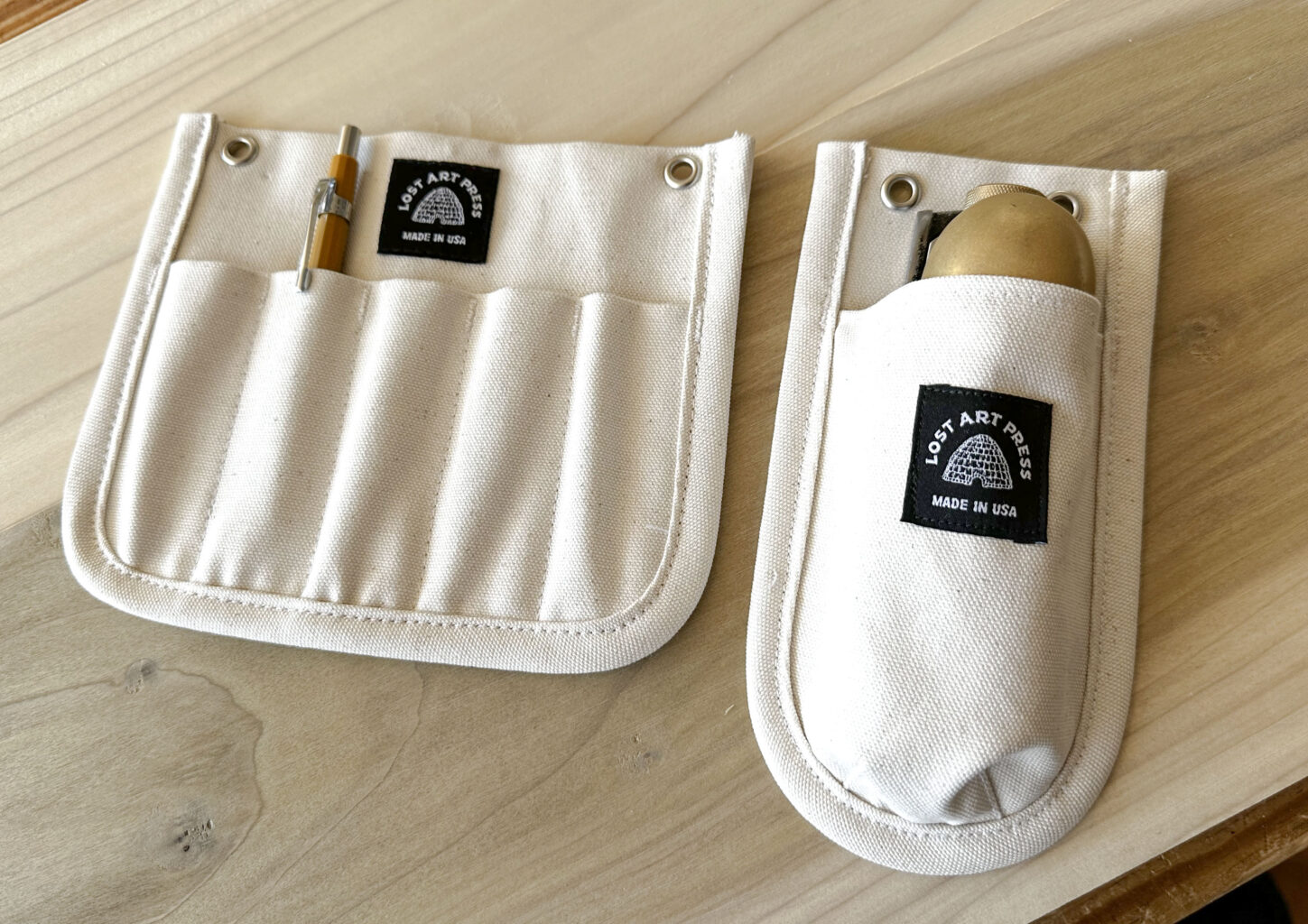
Comments are now closed.
Above are prototypes of two new tool-storage items – the Pencil Pocket and Plane Pocket – that we’ll have available in 2024. They are heavyweight canvas, with grommets that allow you to screw them almost anywhere in your tool chest, on your bench legs or back, or on your shop wall. They will be made across the Ohio River in Cincinnati at Sew Valley – the same people who make the Lost Art Press Chore Coat and Moleskin Work Vest. OK – enough with the product teasing. Sorry.
If you have a burning question about chairs or chair-shaped objects, best to ask it today – Chris won’t be here next Saturday; you’ll be stuck with me…so it’ll be all dovetails and cats. But today, we’re both here, awaiting your Open Wire questions.
Type your questions in the comment field below, and we will do our best to answer them. Comments will close at around 5 p.m.
– Fitz
I want to make Chris’s banjo jig for a drill press so I can get consistency with a set of chairs I’m planning to
Build this winter. I am also
Shopping for a drill press so I’m wondering what specifics he recommends for drilling chairs. In particular any specific size I need? Would a good bench top one work? Tables need anything specific to mount the jig? Wanna keep it as small as possible since I’m running out of shop space. Thanks!
A small benchtop drill press will do the job with no problem. And it doesn’t need a lot of reach. If it were me, I’d try to find an old vintage one (like an Atlas). Or buy a Grizzly. Grizzly started its business in drill presses and do a really good job with them.
https://www.grizzly.com/products/grizzly-8-benchtop-drill-press/g0925
Not sponsored etc. Had a Grizzly drill press for many many years.
I just got a Grizzly and and am blown away with the quality, especially at the price point.
I like the new tool storage. Will it be available in blue? Seriously. I’d have white canvas looking like crap in a heartbeat.
Just a thought….dye them? Possibilities are almost endless. Might be hard to achieve a dark color from white but it’s an option.
One person’s “crap” is another person’s “patina.” I love the way my waist apron looks now. I’m afraid we can’t offer them in different colors – this project is already difficult enough already. But vegetable dyes are an option….
What do you think about shop made wooden holdfasts? Thanks.
I’ve cut a few from branches (I wrote about it years ago). They worked OK. But not as good as metal ones.
Hi, I am looking forward to the “American Peasant” book. Will it include any tips and tricks on using the Linseed Oil paint? Just curious.
There will be an entire chapter on the stuff. How to thin it, brush it on and then re-oil it at the end.
does this mean we can’t ask about cats today?
You can always ask about cats.
Well…what about cats?
They are delightful sociopaths.
I tried making the soap finish using your recipe and the pure soap flakes you recommend, and it never game together into the proper goopy consistency. Came out thin and watery the soap didn’t fully meld together. Tried adding more soap to the mix and that didn’t help. I had the thought that it might be the hard water coming from our well but haven’t tried using distilled water yet. Curious if you have ever encountered this problem or have any suggestions.
How old were the flakes? If they were more than a year old, I haven’t had good luck getting the waxy solution. Another option to get started is to buy the cream soap, which is ready to use as a finish. https://puresoapflakes.com/
Didn’t realize they sold the cream soap! I will try that, thanks. The flakes in my case were pretty fresh.
Can you give me techniques for using a rasp well? For example for the ATC, the saw till, I blew out some of the wood. How do I get a nice square edge on the hole?
In thin materials where I am squaring an edge, I usually “draw-file” the surface. (Look up draw-filing for a video or illustration. But basically you don’t move the rasp laterally as you work.)
Rasp with the grain. Start at the bottom of the arc and rasp up. Make sure the work is well clamped. No vibration. And start with “easy trials” – meaning light cuts – as you begin.
Thank you I greatly appreciate this
I am finishing a lot of white oak in a staircase. Its grain raises impressively with finish. I use mineral spirits to raise the grain then sand it off. It works. What do you prefer for raising grain? Water would be cheaper and friendlier to the environment, but it dries slower.
The surface is machine planed by a Shelix helical head, followed by random orbit sander using 150, 180, and 220 grits. I used floor varnish on the treads but Heritage Natural Finishes Original for the risers, hand rails, etc. Heritage claims to be a descendant of cult favorite Monarch. It is a citrus solvent, tung oil, linseed oil, and beeswax mixture. Lots of solvent, pretty thin mixture.
Water is the best at raising the grain. You don’t have to hose it on or even soak the wood. Wipe a thin coat on and it will dry pretty fast.
I had to zoom in on the image of the Plane Pocket. At first glance, I thought it was a potato.
It will also hold many kinds of potatoes
The pencil holder works with French fries.
Will there be one for curly fries?
Good morning
I am building a low back stick chair, I read last week’s question about shave horses and found on that clamps to the bench top. Have you ever made your stick chairs with round’s instead of octogons?
Sure. Just keep planing away the facets until it looks round. Very common in old stick chairs.
Any plans or progress with a book covering Scandinavian Style furniture?
Caleb James is working on a book on this. It will take a while, but it will be fantastic.
Know of a reliable source of quality hickory bark seat materials?
https://www.newberryandsonschairs.com/200_hickory_bark.htm
Back in spring of this year I cut down a small forest to clear for a shop. From the cuttings I harvested a stack, 10’ L x 4’ W x 5’ H red and white oak 5/4 boards. These boards were stickered stacked and lightly covered in a well ventilated outdoor location. I read oak takes about 200 days to air dry. Question, now that the wood is ready which is best for future storage, leave in place and use as needed or move inside? If move inside is correct what is proper storage method? Thank you
You need a moisture meter to answer your questions. Recommendations on “drying days” are the roughest of guidelines. A moisture meter will tell you where you really are in the process.
First use the meter to find out what is the equilibrium moisture content (MC) for the oak in your shop. Then meter the wood outside. If it’s less than 20 percent MC, then you can move it inside. Then use the meter to monitor when it has reached the target MC for your shop. Then you can use it.
When you move the wood in – now or later – has to do with your space constraints. If I had lots of space inside, I’d move it inside as soon as it hit 20 percent MC so it will be ready to use sooner.
When I do move inside is flat or standing storage preferably? Thank you
Sorry I missed this one in a flurry of comments.
I prefer to have the stock standing if possible. It’s much easier to page through the boards to get to the one you want. But you need a tall ceiling and a dry floor. We store our stock flat in the cellar (we have only 6′ ceilings there).
Have you used the Veritas power tapered tenon cutter? Any thoughts? Thanks
I have not. For my kind of work the tapered shoulder isn’t necessary. If I were making willow chairs again, I’d probably check out the tools more closely. Sorry.
I’m getting ready to nail together the six-board chest — sphincter tone is high. I plan on making test pieces before I start on the actual chest but wondered what depth pilot you generally consider optimal for rivierre nails? The wood is poplar, and the front boards have a 1/4″ deep rabbet on 7/8″ thick board, so essentially joining 5/8″ front/back boards to 7/8″ thick side boards. The pilots will be 1/2″ in from the end/edge. In the FWW article “On Nails”, you mention pilot depth of one-half to two-thirds nail length, so I imagine with a tapered bit you can go a little deeper and still get the holding power you want. Maybe a depth of 40mm or so?
Do you ever add a little liquid hide glue to the rabbeted/nailed joints? Or liquid hide glue to the bottom board dado?
Thank you for any insight,
Adam
Hi Adam,
A test joint will give the the answer on the depth. The shallower you go, the stronger the nail holds. So I’ll start with a pilot that is one-half the length of the nail. If the joint splits, increase the depth until the test joint holds.
As to glue, I’ll add glue to any nailed joint that isn’t designed to be replaced. So I will not add glue to backboards or bottom boards in cabinets and chests. Especially in chests, those have to be replaced from time to time.
I am building a Moxon vise/joinery bench. It is about elbow-height, made from 1 3/4″ thick Ash. I want to use bullet tenons to connect the top to the legs (4″x4″ Doug Fir).
From what I understand, I should use 1″ dowels and leave them proud of the base by about 1″, then round the tops. How far into the legs do you suggest I put the dowels?
Any suggestions to drilling down through the leg end-grain? My limited experience doing this with a brace & auger bit lead to rather loose & wonky holes, drilling into end-grain just doesn’t seem to work very well.
And to send the movement of the Ash top to the back – make the front holes in the top tight, but the back holes in the top loose. How loose & any suggestions on how to do this?
As always, thanks so much for everything that you do!
Hi Drew,
I’m not the biggest fan of bullet tenons in benches. I move my benches and I hate when the tops pop off. If I want the top to come off, I’ll use angle brackets and bolts.
But to your question, I’d probably make the tenon extend into the leg 3″ or so. To make it fit tight, I’d drill the hole, then shave a tenon to fit tightly in the hole (so the wonkiness of the hole is immaterial).
As to shifting the wood movement to the back, again brackets and bolts would allow this automatically. But if you want to go your route, then drill the hole into the underside of the benchtop, then turn it into a slot by chopping it out with a chisel. Adding 1/8″ on either side of the hole is probably fine.
Nice and useful additions to your LAP inventory and a future purchase for me. Thanks.
Chris,
I was at my local Habitat store a bit ago and saw a chair from across the room. It looks like, I think, a pretty old Windsor (or a very abused not so old Windsor). Anyway I left but couldn’t stop thinking about it. I was reading “Intelligent Hand” at the time and thinking about the prototypical chair DS kept in his shop. I went back and bought it for $25.
On further inspection there are things that make me think its old, low stretcher in the undercarriage, wedged tenons, plenty of damage/patina (things I’ve picked up from you in your “Chair Chats”). But it also has some things about it that make me wonder: pretty smooth bottom of the seat where I would think there would be scrub plane marks & a plasticky finish, although that certainly could’ve been thrown on later in its life.
Anyway, its pretty rickety although it holds me fine and there are a few pretty substantial cracks in the one piece seat. Have you ever “restored” an old chair? I’m hesitant to ruin it but I’d like to shore up the cracks and maybe tighten it up so it doesn’t feel like it might fall apart, I also wouldn’t mind stripping off the plastic varnish maybe. I’d appreciate your thoughts since you’ve been pretty open about your love of chairs, especially vernacular ones.
Its a pretty unique shape, at least to me, more shallow and wide than what I normally think of for a Windsor and I want to make a stick version of it someday. I can send you pic to use for a chair chat someday when you get some free time again.
If it’s a really comfortable and beautiful chair, then $25 is a good price to pay for the lesson. And you would get to take the chair apart, reglue it and learn about the mechanics.
If it’s neither comfortable nor beautiful, then let it be.
I have fixed old chairs. It’s not my favorite thing to do. But it is always enlightening.
Any chance of you putting up a “Discontinued” section on your website for products you’ve made but no long offer? For historical reasons.
We don’t want to encourage collecting, nor do we want to be pestered about re-issuing discontinued items (which all have been discontinued with good reason), so no.
Good Morning , In the stick Chair Book it mentions a pommel being from 1/4 inch to 1 inch long , but most of the pictures of seats in the book seem to have longer pommels ( 3-4 inches ) ? Not sure if I am misreading something . Any chance of a contour map of one of your typical seat patterns , perhaps in the next stick chair journal ? My first attempt at saddling a seat went OK but trying to get a little better prepared for the next one ! Thanks for your help
The peak of my pommel is 1/4″ The hill up to is might be 2″ or 3″.
On a contour map, I’ll be honest, that’s something that’s a little more technical than the spirit of the form demands.
Make a flat bowl for the butt cheeks about 1/2″ deep or so. Curve it up to the spindle deck around the edge of the seat. Rough out the “cups” at the front of the seat about 3/4″ deep. Blend the area between the cups and the bowl. Sit. Look for weird bumps.
That’s all I ever do. Not meaning to sound grumpy here. Just trying to be true to the form.
Can one take all possible precautions to avoid a panel glue up from twisting and warping and yet the panel still explodes? (i.e. let wood acclimate, proper joinery to allow wood movement, pay attention to growth rings, etc.).
I’ve built three shaker side tables (i.e. per your LN video). The first two in cherry were perfect. No issues with the tops splitting cracking or warping (after a year). The third I recently built from Maple. The top exploded just a few weeks after I delivered the table to my daughter in St. Louis (I live in Virginia, similar climate, humidity, etc.). The middle board twisted, breaking and splintering open the glue joints, and the outer boards cupped. After reading much of your writings, I think I know the answer to my question above, which is ‘yes!’.
I wasn’t going to ask such an obvious question, but after reading today’s Earlywood posting–about your correct view that the predominant doctrine is not always true–I laughed out loud so hard. I alternated the growth rings in the table’s top to avoid panel warp. That technique did not prevent warp. Also, I chose heart side up for outer two of the three boards in the top. Guess what? Those heart side up boards cupped, they did not bow! Just like you wrote—‘ridiculous’. I am indeed finding my own way the way out of the paradox….bad things can happen with wood no matter how careful you are.
Sounds like your wood was drier in the shop than the environment it went to. When the heart-side cups, that means the board took on moisture in its new location. When I have to send something like this to an unknown environment, I use quartersawn material for the wide pieces.
Also, always remember the caveat: Wood is weird and will do what it wants to. Sometimes boards have tension that gets released and can cause problems.
Will the new website allow for searching the Open Wire archives? There is a ton of useful information here. When I’ve tried to go back to things (I think) I read in Open Wires, I’ve had a hard time finding it again.
They are separate sites; the blog is WordPress; it remains unchanged.
I’ve had reasonable search results by going to google and entering my search term plus “site:lostartpress.com” (without quotes)
I save them to a file in my google mail. I don’t know for how long this can go on, but it works for now.
I’m planning to make a shelf whose edges has a convex curved profile, but I’m not sure of the best tool for doing that. Would you recommend a spokeshave with a concave blade, a moulding plane, or something else?
A curved-bottom shave can do some of the work. Usually that’s a job for rasps. First a cabinet rasp to get it to shape. Then a modeller’s rasp to refine the scratches. Then a card scraper to finish the job.
Thanks! Any tips for how to get an even, consistent profile with the rasps?
Other than practice? Take your time. Have a line drawn on the piece to work to on both faces of your work – and a square to check your work. But it’s all practice because this is freehand stuff.
Hmm, might be a bit more than I can handle. Maybe I’ll just stick with a nice chamfer haha. Thanks again!
Good morning Chris and Megan,
Is there a good reason to avoid making tool or blanket chests with tongue and groove panels as opposed to glueing up the panels?
No problem at all. (Chris is making many pieces in that manner for The American Peasant)
Didn’t some instruction for the Dutch tool chest suggest tongue and grove or ship lap for the back as a viable option? (Full disclosure: I made mine from leftover maple plywood)
Either works! (As do nailed butt joints, if that’s all you have the tools and/or time to do)
I made an aumbry from The Anarchist’s Design Book. I finished it using Tried and True. Someplaces the finish is shiny, others it is not. It is mostly not shiny. However, the board above the door is shiny. When I stand with the window at my back everything looks fine. On the other side, this top board reflects light and looks much lighter than the rest of the aumbry. Why is that, and what can I do to fix it?
Glossiness can build when you add finish to the boards. So perhaps that board got more finish than its neighbors.
I would try applying a coat of paste wax to the entire project. That usually evens out the sheen. Another option is to rub out the glossiness in the top board. A very fine sandpaper (automotive – 1,500 grit or 2,000) and some mineral spirits. That can knock back the glossiness. You might have to rub out the entire piece to make it consistent.
A cheat is to find some flatting spray at a photo store. We used this to photography very shiny objects. It would selectively lower the sheen of whatever you spray it on. It is removable.
But really, try the wax first. If you want it to look flat, use beeswax.
For me, T&T oil does not add much gloss. I end up with a satin finish.
Maybe you sanded the surfaces to (very) different grits? Maybe you did an excellent job planing the shiny area? Maybe the boards have very different grain or color? After oiling, face grain can look shinier than vertical grain.
I would “wet sand” the entire piece with more of the same T&T oil. I prefer scuff pads for this. The green or maroon pads work well for me. I apply and “sand in” a generous coat of oil, let it sit for half an hour, reapply to dry areas, let it sit for half an hour, and then vigorously rub off all excess oil. I find it easier to wipe of excess than to apply the extremely thin coat the instructions recommend.
I try to wait for a day or more before applying a second coat. After two coats, I end up with an even satin “finish”. There is no visible surface film, but the oil definitely changes and protects the surface.
If you have applied wax, you can simply apply the T&T over the wax. The scuff pads will easily cut through the wax. A little wax dissolved in the T&T oil has made no discernible difference in my finishes.
In areas where the grain changes quickly or on end grain, I try to start with a wash coat of shellac. That mostly avoids dark areas where the grain might absorb more oil. It does not seem to change the final sheen.
Good luck!
I made a dovetail saw with a thin sawplate of spring steel that catches (hangs) at a certain spot during the stroke. Can you suggest a site/published work that can help me correct this?
Don’t know about books but there’s a group on Facebook called “Saws, using collecting cleaning and restoring” which includes a number of very talented contemporary saw makers. You might get some good answers there.
Unless the plate has a bad kink, it seems more likely that some of the teeth are catching.
Eyeball the teeth and see whether some of them have way too much set. If so, correct that.
See whether the teeth are otherwise misshapen.
Absent obvious problems, I would try lightly stoning the side of all teeth. That can correct small inconsistencies in set.
Curious if Gibson chairs might be typically found made of more than one type of wood, or usually one. Also are they typically painted? I have some nice elm for chair seats but maybe not the rest. I don’t mind bucking tradition, but wonder what it is.
I can’t say for sure. I see a lot of them that are painted. And a lot that are unfinished. Did they start that way? On the woods, I would say: Use what you have.
The Gibsons were made in large numbers by two or three shops, so I am sure there are real answers to these questions. I just don’t know.
Good Afternoon,
Thanks for taking the time to answer questions again to day. It’s been exciting to read about everything in the works at Lost Art Press recently. A few months ago, you mentioned that you were planning to film an instructional video on building a Hobbit chair. I was curious if this was still in the works, and if so, any unexpected release date?
Thanks,
Jacob
It’s on our list. Our new warehouse has completely consumed all our time that we devote to videos like this.
Is Chris interested in engraved furniture not from Eastern Europe? I know of two engraved chests from the Mary Rose (British ship sank 1545, raised 1980’s), and can send a pic of the archeological drawings in “Before the Mast, Life and Death Aboard the Mary Rose”
Oh sure. I have lots of sources from the U.K. and early American. And they will be mentioned. I am focusing on the Scandinavian and Eastern European forms because they are more advanced in their decoration. And they have been largely unseen by western woodworkers.
I am making maple backsplashes for our kitchen and some need to have some curvature removed or added to fit the wall. These are about 1/2″ thick and 4 1/2″ wide by around 25″ long. If I use a hot water bath should the water be boiling and how long should they soak?
Usually in these cases you leave the backsplash straight and then add a scribe strip to the top that is scribed to the wall.
When you bend wood by steam or with boiling water you usually only have a few minutes to get it secured in place before it sets up. Another option is using cold-bend hardwood, which bends cold (Google for a full explanation).
I’ve never bent maple. But usually when I bend wood it is green, dead-straight grain and boiled for a couple hours.
Any advice or resources for shipping furniture cross country or to different climates?
We build crates using 5mm underlayment plywood and ribs made from 1″ x 1″ pine. Then we wrap the furniture in furniture pads or bubble wrap and secure it to the crate with more 1x1s. Step by step here: https://blog.lostartpress.com/2018/09/17/one-way-to-build-a-crate/
As far as shipping to different climates, it’s difficult. Wide panels will warp. Doors and drawers will shrink and freeze up. Sending a piece to the equator, for example, is asking for trouble. If you have to do it, use quartersawn material as much as possible. Kiln-dried (it moves less). And plywood for interior bits whenever possible.
And be ready for the phone calls….
Chris,
I know you’re not excited by rocking chairs, but do you foresee a Rocking Stick Chair book from LAP anytime in the future, whether by you, Peter Galbert, or someone else?
Thank you,
Tim
Won’t be from me. Peter Galbert is going to cover rocking chairs in his next book from us. So I’d look for that.
Hi Chris and Megan, I would like to make the French wall rack discussed here: https://blog.lostartpress.com/2011/01/01/the-last-project-of-2010/
The link for the sketchup drawing says server cannot be found. I downloaded the linked file but that also would not load. Im not sure if the issue is on my end. Is there a sketchup available still or a place to find suggested dimensions? If not, I can use my best judgement. Thanks, Claire
I don’t know what’s up with the link on our site, but you can register (free) at PW and see the drawing there. https://www.popularwoodworking.com/projects/i-can-do-that-easy-tool-rack/
and my pot-rack adaptation:
https://www.popularwoodworking.com/wp-content/uploads/pot-rack_IDCT.pdf
The model is still int the Trimble 3D Warehouse:
https://3dwarehouse.sketchup.com/model/361bffaed1e32475310af74324aae27f/French-Tool-Shelf-from-Popular-Woodworking-Magazine-April-2011-Issue?hl=de
Oh! I was thinking of this as my next project in line after finishing my workbench and building a packing crate and schoolbox. But I’d like to do it as Thomas might have, rather than with power tools. What are the right joinery choices? Through tenons for front divider, and … nailed lap for the back? Dado and nails for the top, or double tenon (which seems like big leap for me, but they won’t be very visible…)
Thanks!
For shop furniture? All nails. Good tapered nails.
Any special considerations with white pine seats on stretcherless stick chairs? I’m trying to make the Irishy curved backrest chair and a Gibson using white pine for the seat. They will finish out around 2” thick. I plan to bevel the bottom edge to make it look thinner.
Thank you.
I haven’t used white pine in a chair without stretchers. My gut says to add stretchers. Or switch to poplar for the seat. But I am always cautious with these things and tend to be conservative.
I’m still working on a small secondary anarchist bench. I think I did a bad thing… there was a seemingly good deal on 8/4 bass and I had a lapse in judgement. I bought it to make legs thinking it’d be a breeze to flatten etc. legs will be 4″x3″. Will it be too soft for good joinery at corners? Will converting to double tenons make it less likely to fail down the road? the top and stretchers are western maple. Maybe I should take up chip carving and go buy real wood with the $25 I saved. In the scale of decision making I’m giving it solid 2/10.
Basswood is fine for the legs. No changes to the plan necessary.
Any update on that random article button for the blog?
I totally forgot about that. Will try to remember….
I have an antique chest of drawers with wooden knob pulls. The pulls have threaded wooden tenons. The tenons have stripped to the point that during the winter the pulls dont stay in the drawer, but during the summer, they are fine. Otherwise, the pulls are in good condition. I would like to keep the pulls removeable. My current idea is to paint some hide glue on the pull and the tapped hole (and maybe put a little saw dust on them too). Then screw the pull into the drawer but remove it before the glue sets. My hope is that the extra glue (and maybe sawdust) will build up the tennon and tapped hole enough to hold on its own. Does this sound like a good idea or do you have a better one?
Hide glue will fill some minimal gaps, so it might work without the saw dust. (Might not.) Another option I have used is to paint a plane shaving with hide glue and wrap it around a loose tenon. I’d probably try that dry first, though, in case it makes a mess.
A round head slotted screw into pull’s tenon from inside of drawer with a washer wider than the tenon – easy to remove if you want to take the pulls off.
Hey Chris, thanks as always for doing this.
I’m building two Gibsons right now per your video. I’m getting ready to drill the holes for the back sticks, and unfortunately I didn’t notice until now that you’re using the extra long spade bits in addition to the bit extender in order to accommodate the distance from the template to the seat.
I have the GoDrilla extender but only a standard length spade bit. Is there any other way to drill these holes at the correct angle without having to order new bits and wait for them to arrive?
You can buy a longer 1/4″ hex rod to extend the shaft of the GoDrilla.
Hi, one of you mentioned that you were checking/testing the Rikon 10” band saw.
What is your take on it. I don’t have a shop, not a chance of having one. I think if it’s good it may be good for me. I was thinking on the deluxe model, just because it has a little more powerful motor.
Thank you very much for doing this
It’s a good little saw. A that price it is hard to complain about it.
I have it (the non-deluxe version) and I have no complaints, especially for the price and finding it locally (thanks Menard’s!). I haven’t had it long, but it has handled everything I needed it to do and wish I’d bought it a long time ago. But then it would have cost more, I suppose.
Domo time ago I bought the templates for the stick chair book. Is any chance I can get a DXF or another vector electronic form so I can cnc or laser cut the templates out of 1/4 ply
Just sent them to you
This is a great idea. Could I get them as well? Drawing/cutting my own patterns worked great and I wasn’t looking forward to redrawing all the ones from the book.
Try this link: https://www.dropbox.com/scl/fo/ax7wxzmtqkqs7jsm53ste/h?rlkey=egdumqi9gdoxgz6c087qjdvr7&dl=0
For general use, what blade length & TPI do U prefer for Crosscut & Rip Panel saws? Thanks.
I like panel saws 22″ long. Rip at 6 or 7 points. Crosscut at 7 or 8. Some people also like a 12 point crosscut saw. I don’t find them all that useful.
Hey guys! I’ve been trying to up my sharpening game by adding cambers to my blades. One thing I never understood is when edge jointing boards for panel glue ups aren’t you creating a small hollow when mating two boards that have been planed with a cambered blade? Thanks!
Not one that is significant enough to affect the joint. If you camber is correct the edge will read as square – no light under it. That’s good enough for me.
A tornado took off the top of a large shagbark hickory on my property, so I’m going to harvest it this fall.
My immediate thought was Chris’s suggestion I read once about using shagbark hickory for a workbench top.
So my question is about Chris’ placement of tongue in cheek when writing that, and how much will I curse or praise myself for taking those words to heart and making it into a slab and parts for a workbench?
Shagbark should be classified as a soft metal. Not a wood. It would be a great workbench material. But it will fight you all the way to the end (your end or the bench’s).
I’ll take that into consideration. 😉
The tree is 22 in diameter at my chest, and has 15 to 18 ft of lumber before I get to branches, and my dad warned me he used to use it for target practice when he was a kid… but based on your comment I doubt I’ll notice any lead shot ( or other soft metals).
I will probably ignore lots of other perfectly good advice from The Anarchists Workbench too… so I will remember to hold its author blameless as I build the bench.
In one of his books on basic skills Joshua Klein uses a flat drill bit to drill tenon holes (1/4 inch hole) do you know where these flat drill bits can be found? I don’t think it was a spade bit.
Hmm…could a spoon bit or a center bit (or some other flattish bit that’s not springing to mind). But spoon bits (which aren’t quite flat, but close) are available at Tools for Working Wood and Lee Valley Tools (among other places, I’m sure). For center bits, though, I don’t know any modern makers, so an auction site or used tool monger is your best bet (ie hyperkitten, Pat Leach, Jim Bode…).
I just went and looked at the book. You might ask Joshua directly, but it looks like a shell or gimlet bit.
Thanks for answering questions today! With the change in your website, my downloads section for my pdf purchases disappeared from my account. Is there someplace else on the site I should look? Thanks again.
We fixed that Friday afternoon. Try clearing your browser’s cache and logging in again.
I’m sorry. I should have checked before asking. My downloads are now back on my account. Thanks!
piglet-no-wiggly (that’s autocorrect for you)
I made a batch with Knox brand gelation. Little packets. Probably the most expensive option. It passed the wack test- wood broke not at glue line.
Generic house brands of gelatin are available. Do you think, or have you tested, any other brands and are they as strong? I assume you have since you are making it at an industrial volume.
Is skimming the foam necessary or cosmetic?
Keep up the good work.
Will there be another run of dividers (in time for holiday gift giving)?
I hope so.
We skim the foam. As long as the bloom strength is clearly stated, then I am sure that “generic” is fine. We buy ours from an industrial restaurant supply, so it’s not “brand name.”
Not a woodworking question, southern cuisine instead. Grits.
Did you once write a blog here or at PWW about a decent brand of real southern style grits & rice? If so, what source were you recommending? I no longer travel on a regular basis to Greensboro, NC, so I’m not filling up my check-on luggage with Guildford Old Mill grits any longer.
Marsh Hen Mill are the best. Especially the heirloom varieties.
I want to be a better writer. As long as I’m flying solo, as far as I am aware I will be my own editor. Are there any suggestions you two (Fitz and Chris) might suggest for how best to edit?
Fresh eyes are the best. If you can write something, put it aside for a month and then edit it. If you can’t spare a month, even a week or a day makes a huge difference.
In building stakwed stools how deep is the slot for the wedge relative to the thickness of the seat
It’s about 3/4 of the way through the seat