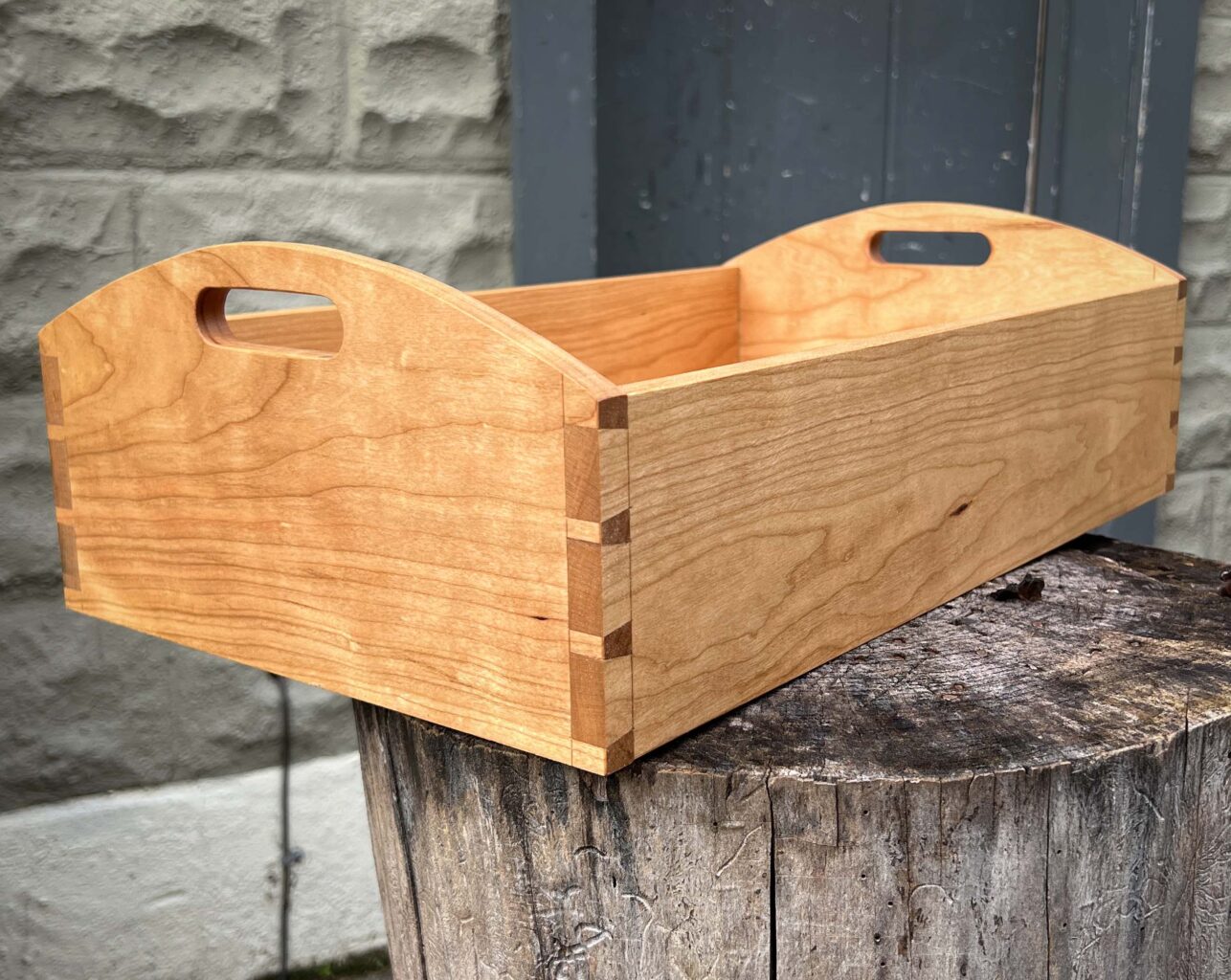
I promised my Pine Croft students last weekend an online lesson on leveling their pins and tails (the glue hadn’t set up enough to stress the joints before it was time to clean up). So I’m sharing it with the rest of you, too.
Even if you set your marking gauge/cutting gauge to the exact thickness of the mating board when you mark your through-dovetail baselines, odds are excellent that you’ll still have to level the pins and tails to the project surface, before you can smooth plane the outside to clean up shop rash etc. before finishing.
But end grain can be a bear to plane (though cherry isn’t usually too bad), and you have to be careful to not break out the cross grain. So here’s how I do it.
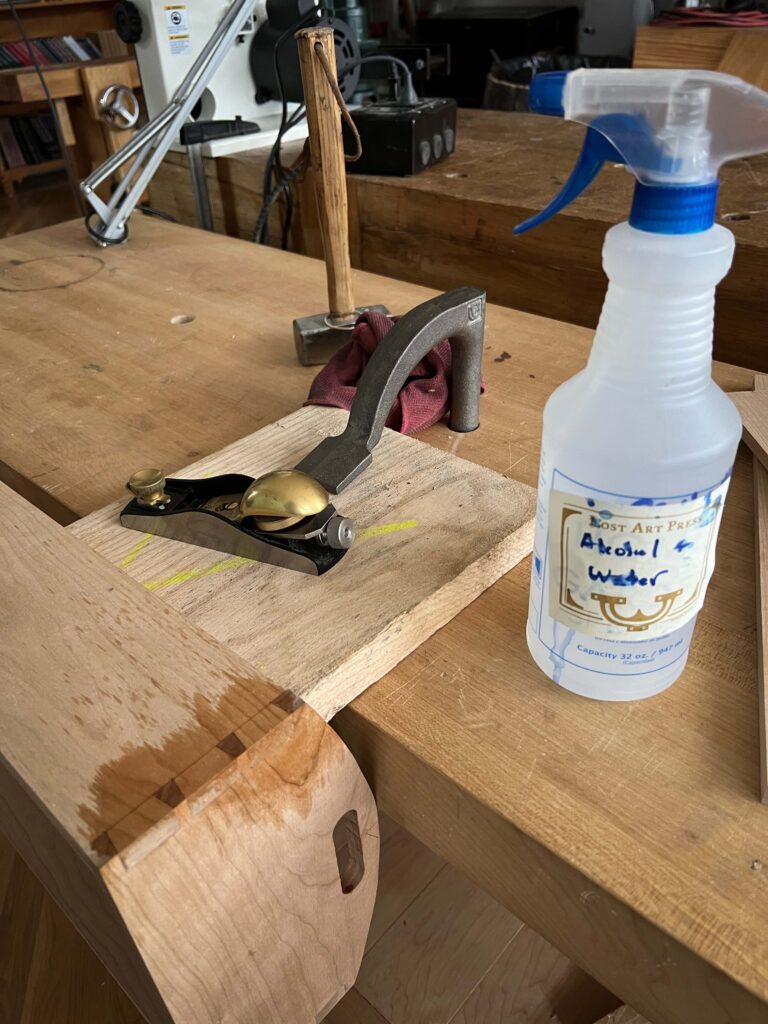
Supplies
1. Mix up some Magic Strazza Elixer (we “stole” the formula from Frank Strazza) and always have it handy. It’s 1/2 alcohol (we use 190 proof Everclear, though isopropyl works too) and 1/2 water.
2. Make sure your woobie is well saturated with oil
2. Sharpen your block plane (and if it has an adjustable mouth, set it for a tight mouth)
Clamp the tray/box to your bench, sleeve it over the end of the bench if it fits, or support it as I have above, on a piece of scrap wide enough to allow you to plane without the workpiece tipping.
Spray the end grain with the alcohol/water mixture and let it soak in for a few seconds. (The long grain will also get wet, and that’s no problem.)
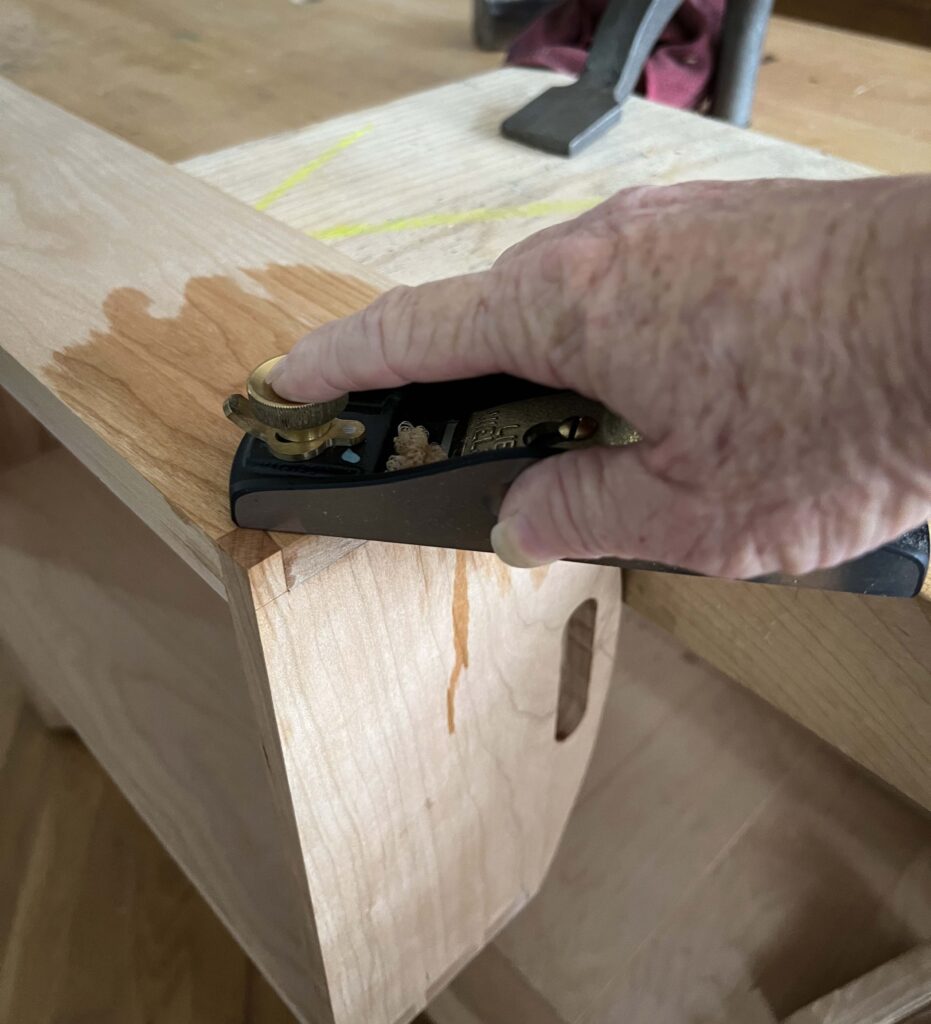
Set your plane for a fine cut. Plane into the piece, concentrating on the proud pins/tails, to level them to the work. You’ll know you’re there when you start to get shavings from the side of the piece instead of just the end grain of the proud joint. Skewing the blade (shown above) as you come onto the work can help.
Once your joints are flush with the work, you may find you’ve left a plane track on the side of the piece. Back off your iron and take a few super-fine stop cuts (that is, plane only a few inches into the piece, not the whole side), lifting up the back of the plane slightly as you come out of the cut. It sounds counterintuitive, but lifting the back will keep you from leaving a hard line at the cut terminus.
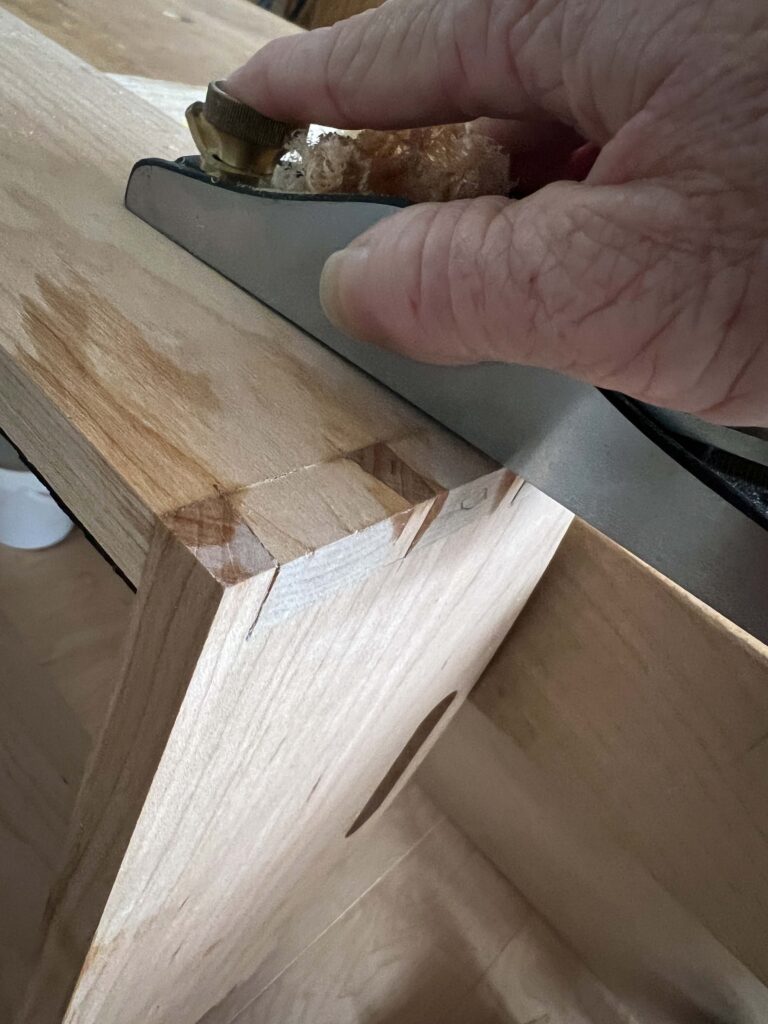
Then turn the box/tray and plane the pins/tails on the next surface, using the spray as needed to soften the wood and make the cut slightly easier.
After you have all the joints level, you’ll likely want to smooth plane before applying a finish. You can plane into the work from both ends, using the “lift the back end” method above to keep from leaving plane tracks at the end of the cut, or you can put a chamfer on the corners of your work, and carefully plane right off that edge. The chamfer removes the corner of the cross-grain pins/tails and protects them from breaking off as you plane across them. Usually. And that’s why I say to plane “carefully.” Take very light cut and keep and eye on that chamfer – once it’s gone, so is its protection. I typically cut a relatively large chamfer – you need to break the edges anyway before finishing, so yay. On the corners, the remaining chamfer after smooth planing means I’ve already done that.
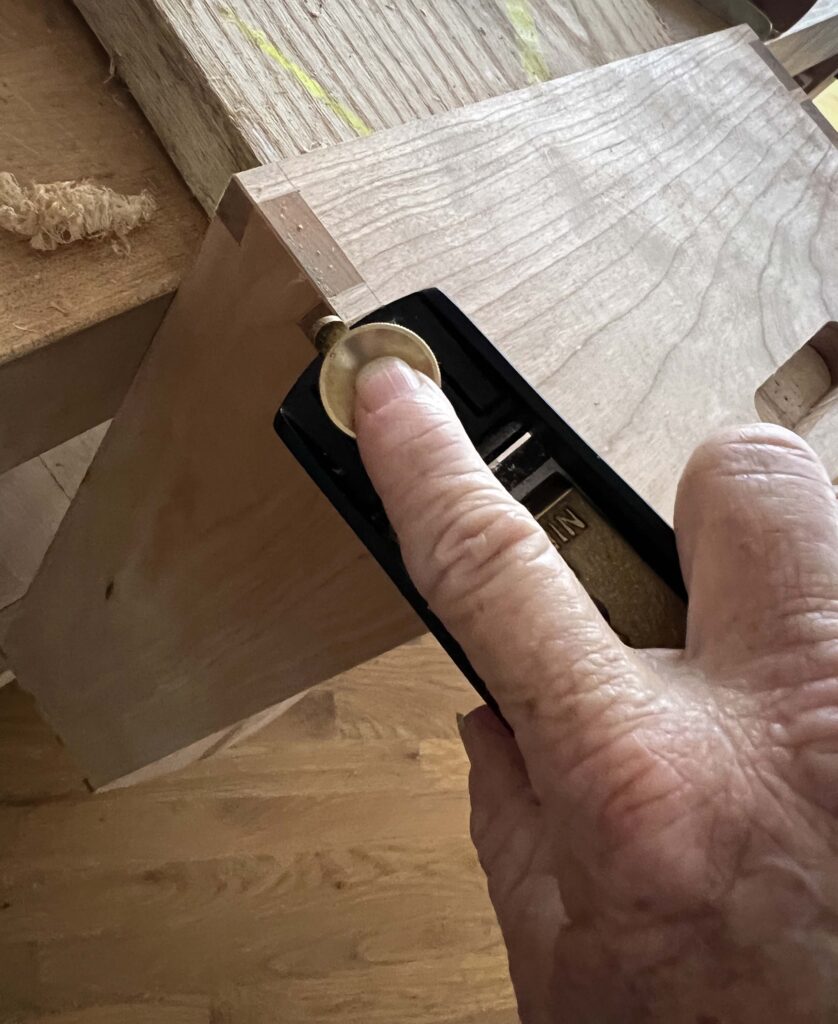
And now it’s time to clean your block plane before moving onto smoothing. Water and steel are not friends – so make sure you get into the mouth of your block plane with a brush to remove all shavings, then wipe it down with your oily rag.
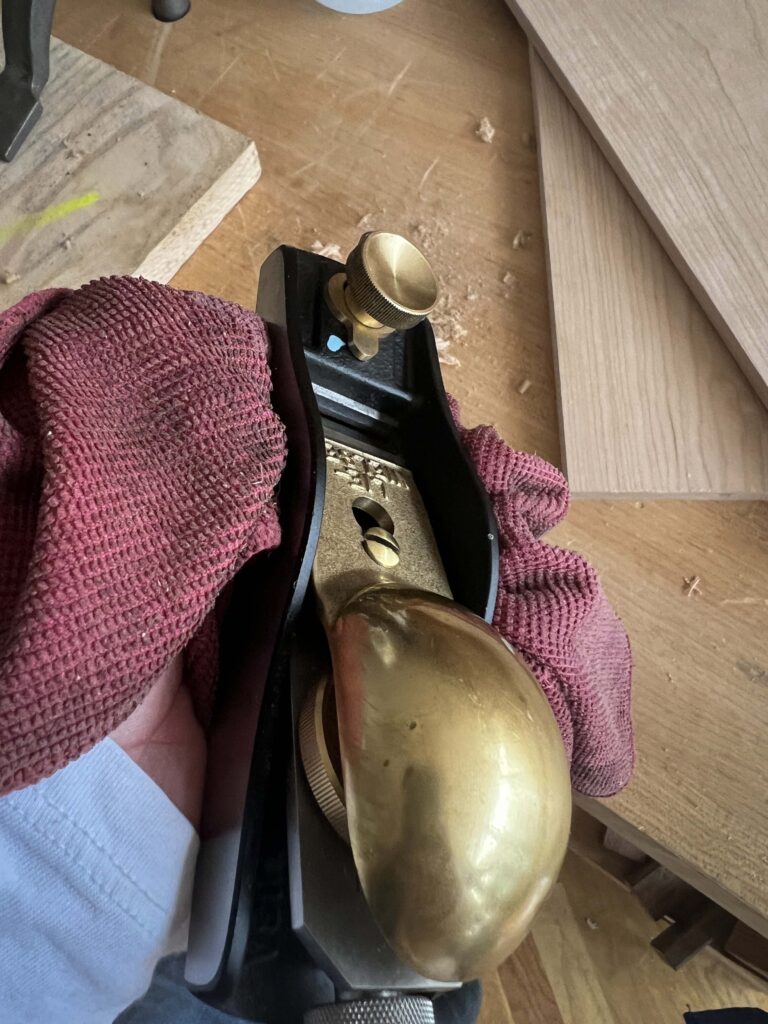
After smooth planing, break the rest of the edges – for that, I usually use #180-grit abrasive. Or #120 if that’s closer to hand.

Then apply a finish. On this one I used “Soft Wax 2.0,” made by Chris’s daughter Katherine. She’s sold out right now, but I trust there will be more available soon, and we’ll announce it here. Or you can make your own.
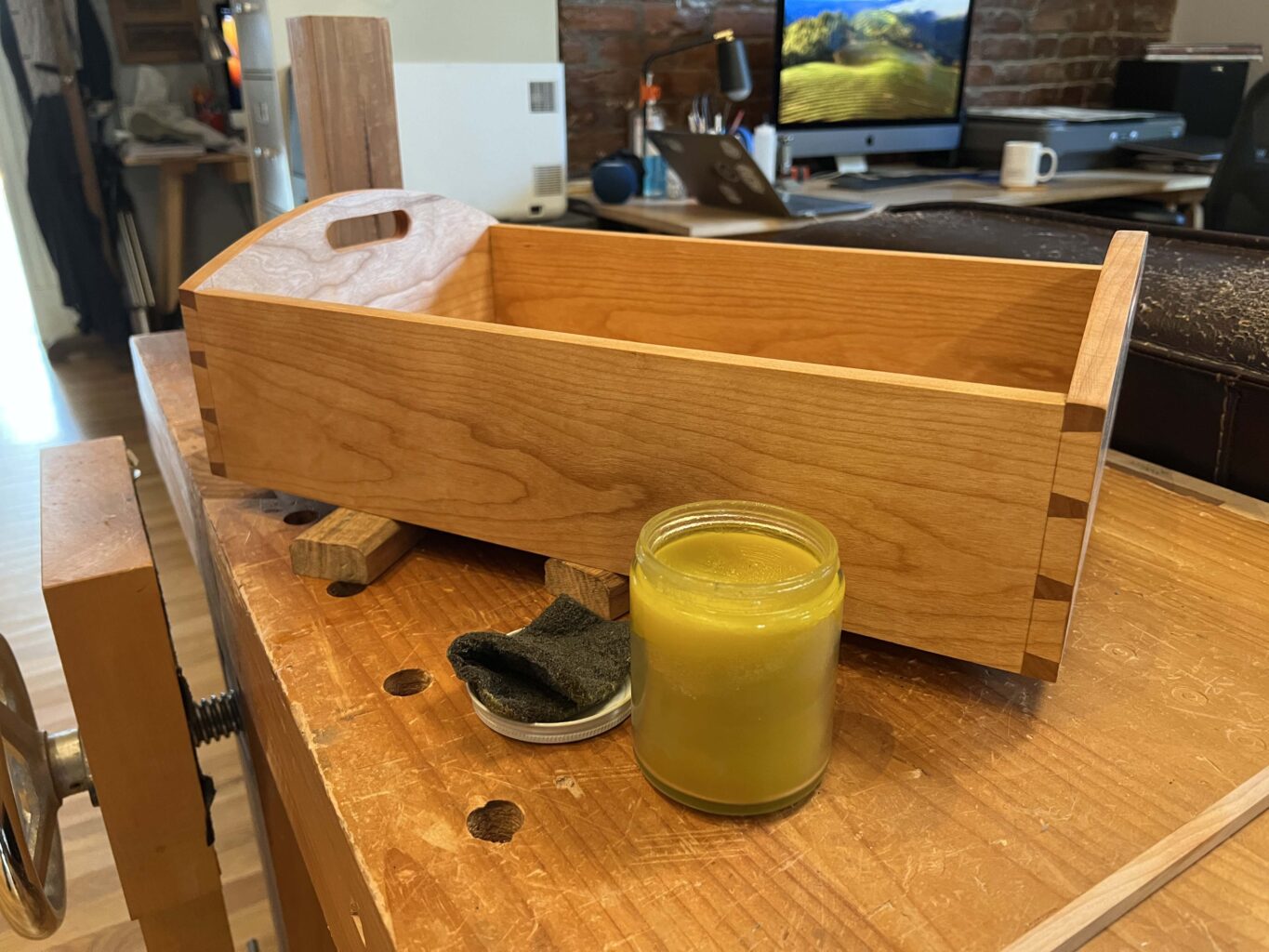
— Fitz
Great !!! blog post. More like this would be fabulous. You brought up things I’ve known but don’t always remember. Thank You, Joe F.
How timely , just finished glueing up a dovetail drawer so I’ll give it a try.
It’s amazing how you can fill gaps in your dovetail joints with sanding dust and super glue.
Maybe with practice the joints will come right off the saw without all the gaps.
Great tips. Thanks.
A great little lesson. And I’m guessing the woobie is the oily rag!
Thank you, and yes on the “woobie”
Woobie??
Oil-soaked rag
Can i use rum and water, like pirates used to drink? That way the leftovers won’t go to waste.
That’s why we use Everclear 😉 (I suspect you’re joking, but in case you’re not: I don’t think rum has a high enough alcohol content to flash off as quickly, plus it’s sugary, so it’ll leave a sticky residue)
Isn’t that how we get sugar pine?
I wish it was that simple! That’d be a good use for rum: turn eastern white into sugar pine!
Thank you, this is a very helpful for us who are just getting started with hand tools.
Thanks so much for this. I have my first box with hand cut dovetails sitting in a corner, waiting to be “adjusted” (there are some gaps that need filling) and smoothed and finished. What do you use to apply the soft wax? I’ve been using my fingers, but that doesn’t seem ideal…
We use a gray or white 3M pad (cut off a small piece – about the size to fit inside the jar, which is where we keep it). https://www.3m.com/3M/en_US/p/d/b40071748/
Thanks. And a rag to remove the excess?
Huck towel, or something else with some “tooth”
https://blog.lostartpress.com/2023/04/30/huck-towels-that-dont-suck-towels/
Approximately how many days outside does it take to start getting cherry to age? I made some boarded bookshelves out of cherry and would like to help the aging process along.
It depends on the finish and the UV rays. The fastest way is to pick a sunny day, and put a coat of linseed oil on the piece (or a finish with linseed oil in it, such as the oil/wax I used). You’ll see a difference in hours. (But it won’t be as dramatic as 8 years of oxidation.) Here’s an article I wrote on it years ago: https://www.popularwoodworking.com/techniques/adding_age_to_cherry/
This one is getting printed out and stuck in the binder. An excellent lesson!
TYPOS: I only mention this because it may help another reader who’s as dumb as me, but the word “place” comes up in a few sentences, where “plane” was intended. It confused my senile brain enough that I thought I’d mention it.
Now to rewatch some great ‘80s movies! Do I start with “Planes in the Heart” or “Trading Planes”? Oh, dear… it seems to be catching…
Yeah…I fixed those in the blog version…I think. Everyone needs an editor! (And auto correct is the devil)
Oops! Seems you’ve already caught the typos since the email went out. Oh, well, guess I’ll watch “Places, Trains & Automobiles” instead…
Not related to the topic at hand, but I have a question about the decision to leave the layout lines. Does that vary by project, or do you always leave them?
I always leave them – or at least I don’t intentionally remove them. Sometimes, if I have to plane a lot, one or some of one might disappear. (I do not put it back.)
Thanks for the how-to guide! Why is it better to break the other edges with an abrasive instead of a block plane?
It isn’t – if the block plane can get there, use it! (I’d already cleaned mine…and needed abrasive for the finger holes where the plane can’t reach)
Thanks!
Thank you Megan!
If it’s 1/2 190 proof and 1/2 water… can’t you just use 100 proof something something? I gave up drinking, still sad but had to. do they have a cheap 100 proof anything?
Seems like bottom-shelf vodka would be about perfect. Gin should work too but your case piece might smell funny…
Megan…thanks for the tips! What kind/brand sandpaper are you using in the image. I know any 180G paper would work – inquiring minds want to know?
Abranet (my fave)
Thank you