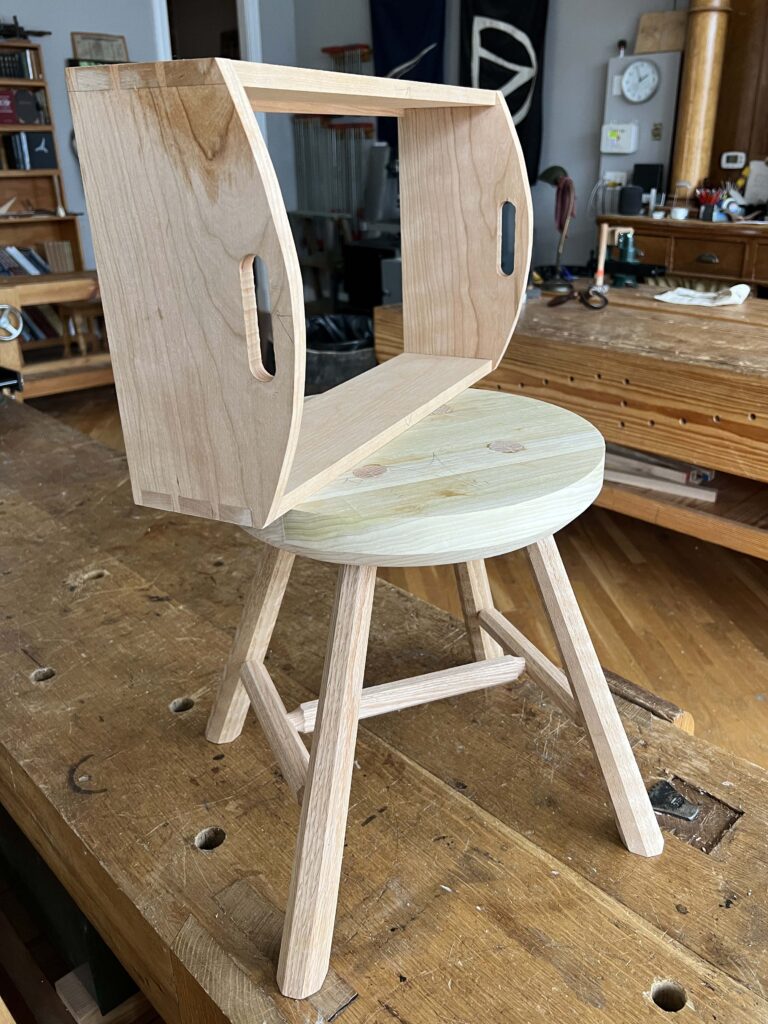
Update: Comments are now closed. Join us next Saturday for more of the same!
Christopher Schwarz and I are back from our respective travels, both with almost-done projects to complete from our classes (work to which we eagerly look forward as a break from staring at our screens). But today, we’re staring at our screens as we eagerly await your Open Wire questions.
Type your woodworking queries in the comment field below, and we will do our best to answer them. Comments will close at around 5 p.m.
– Fitz
How do you make a knock down saw bench, ie. secure the legs so they don’t just fall out, yet can be removed to make storing the sawbench easier? I have limited space in my sm. 10’x12′ shop, which already sports two 5′ roubo benches. I have about finished the legs and am hesitant to glue them in place.
Thank you for your thoughts.
Brad
Hello, I’m looking for advice on avoiding tear out when drilling mortises. Also, why don’t you always drill from the top of the seat so that tear out is hidden underneath? Thanks!
We clamp a backer to any piece to avoid splintering on the exit hole. Typically we use 5mm underlayment ply because we have stacks of scrap of it from building crates.
On drilling from the top vs. bottom of a seat – either works. Neither is better. I drill my leg mortises before saddling. So if there is any splintering, the saddling process removes it.
Hi Brad,
I’d do what Jennie Alexander did. She made staked sawbenches and didn’t glue or wedge the legs in place. She knocked the legs in place when she used the low bench. Then popped them out when it was time to break things down.
Using a tapered tenon/mortise would help with this. But cylindrical joints will work as well.
I’m nobody but I bet you could adapt Will Myers collapsible saw horse: https://eclecticmechanicals.com/2021/04/04/collapsible-sawhorse/
In the ATC you suggest using clear pine because (paraphrasing) all knots come loose over time. I wasn’t able to find enough clear pine but a lot of white pine boards that have some small black knots and larger red knots (“furniture grade”). Does that rule apply to tight red knots as well as looser black knots? Any concerns about stabilizing/filling the knots with epoxy or CA glue? Planning to finish with linseed oil paint. Thank you!
I think it’s fine to use pine with tight knots – my first one has lots of ’em, and I did not glue them. That was 10-12 years ago, and none of them have fallen out yet. So if you glue them, I predict they’ll outlast you.
Thanks! Any issues you’ve experienced with linseed oil paint over epoxy or CA glue used to fill/correct defects?
I haven’t used linseed oil over either of those materials. I wouldn’t expect problems. But a quick test will give you the answer.
I have used linseed oil paint over both epoxy resin and modern acrylic paints, with no issues in either case; that was for outdoors to boot, and worked fine.
But as Chris says, a test piece is always a good idea to make sure that two processes are compatible.
If you are going to paint over pine knots with linseed oil paint, you should first seal the knots, otherwise the resin will eventually bleed trough and discolour the paint. The traditional method is to first paint over the knot with a couple of thin coats of shellac.
Good tip, would you apply shellac over the whole surface to get an even build up, or just over the knots?
When I have done so, I have only done it over the knots. I don’t mean that I’ve painstakingly painted only the knots themselves, but rather that I’ve done a quick, none-precision job of a few thin coats over the knot and the surrounding area, with some very light sanding of the whole after the first coat, and then around the edges of the shellac spots with the following coat(s).
I have had no problems with any uneven build-up showing through, but again: a test piece or two will tell you much more than these words ever can.
I know you guys have been several variations on saw benches over the years. Which do you use in the shop?
Hi Noah. We have two kinds – the “simpler” version that I teach (you can see it here: https://www.tickettailor.com/events/covingtonmechanicals/1009866) and the heavier, through-mortised ones from Woodworking Magazine circa 2007. Both are plenty strong. And at home, I have a staked sawbench…but I use it as seating.
I’ve seen very few in Ohio/Ky. But I usually gravitate toward Shaker stuff, so I could have missed them.
Thanks!
Do U know of any source for quarter sawn pine (in OH or KY)? Thanks.
Shiels Lumber in Cincinnati carries it. But you have to have a wholesale account. Otherwise, try ordering it delivered from Steve Wall Lumber in North Carolina.
Hi Chris,
In one of your blog posts about choosing wood (https://blog.lostartpress.com/2014/08/14/crap-wood-for-good-workbenches/) you said, “I love these boards that are near or contain the pith”. Later you suggest ripping the pith out. This is confusing because often the pith is fully enclosed right in the center of the board. If you rip the pith out, you will have to either split the board in two or it might even become useless. Comments?
My other question is about lumber yards. When I lived in the mountain west, I had access to a lumber yard where you could go in, choose what you want and then pay for it. Now I live in Indiana and I can’t find a lumber yard that will let me choose wood before paying first. Is this the norm in the midwest and the south?
When you have a 2×12 with the pith in the center, then you usually can rip it out and end up with two laminations for a benchtop (the pith is usually near the center of the 2×12).
As to lumberyards, the professional yards usually don’t let you pick through the stock. The retail ones do.
I won’t shop at a yard that won’t let me pick my stock. They are out there – I promise. Have you tried Frank Miller Lumber in Union City, Indiana. They do both wholesale and retail. Great family. More wood than you can conceive of.
Not sure what part of Indiana. I am in the Northeast near Shipshewana. Up here there are two I rely on. LR Nisley Lumber in Middlebury, an Amish run place. He will lift a stack down of a certain species and let me look through. Even better than that is GW Green Urban Forester/Sawyer in Syracuse, IN. He is a saw mill and a woodworker and he really knows his stuff. A lot of his is Solar kiln dried which makes a nice result. I am sure there are others.
Thanks Jeremy. I am in West Lafayette. I will keep the leads you gave in mind whenever I travel. Another problem of course is that most lumber yards in my area (for hardwood) are closed on the weekend.
Good morning,
It’s Fall and “stick chair season”. Maybe I missed it? Any word on Stick Chair Journal #2?
Thanks!
As I’ve mentioned before, I have it about half-done. The Anthe building has sucked up all my time and energy that isn’t devoted to our normal publishing chores. I am committed to it. Promise.
I’m building the American Trestle Table and the article says to pin the bridle joint. Is it pinned through the top of the joint? Or through the face of the leg? Later in the assembly section, the article says to “drawbore both the bridle joint and the mortise-and-tenon joint.” I’m having a hard time envisioning drawboring the bridle joint.
For the drawbore pegs, I have ash and red oak around. Should I track down some white oak instead?
Thanks so much!!
The drawbored pinning of the bridle joint is done through the exterior faces.
Drill through the leg only. Put the crosspiece in place. Mark the locations of the holes on the bridle joint. Shift the locations of holes up a tad (1/16″ to 1/8″). Drill through the bridle. Assemble and drive the pins in.
Oak (red or white) or ash makes for great drawbore pins.
Ah, that makes sense. Thank you for that explanation. I can be dense sometimes!
Thanks for asking this. I’m figuring out the lumber for this table now and hope to build it this Winter. All of the process clarification that happens in these open wires is quite helpful.
I used to live in the Willamette Valley, Oregon, (a very wet climate) and am a scrounger. I came across a lot of formerly rawhide lace bottom chairs. I now live in Wyoming (a very dry climate) these past 15 years and have yet to scrounge a single rawhide bottom chair. Are/were rawhide bottom chairs common in the eastern states area you are familiar with?
I’m a seat weaver in Ontario and I see a fair number of post and rung chairs with rawhide seats from Quebec, less of them from Ontario. My impression is they are not uncommon in northern New England as well.
Being a passionate woodworker I am constantly chipping away at incrementally building up my shop and tools. I think of it as my long term infrastructure program, recently disrupted by the pandemic and related supply chain issues. Who could have imagined suppliers like Lie Nielsen would stop making some planes, chisels or saws? This experience has feulled my ‘prepper’ tendencies and FOMO particularly given what seems like an increasingly uncertain world and growing scarcity of quality tools and supplies. E.g. there are just too many LAP books, tools, and projects on my drool list to be complacent about this. First world problems I know! The acquisition phase is probably largely behind you but I wonder if and how these circumstances have changed the way you think about your tools, and those on your drool list?
My tool acquisition habit is informed not so much by supply-chain issues, but by what might or might not be available in, say, 20 years. ie things made by a single maker or very small business. The tools I love but that are at some risk of breaking (because I lend them out), I have backups for. I don’t need them yet and might never need, but I’d be awfully unhappy to not have, for example, a Tite-Mark cutting gauge.
Yes! I know what you mean. I have three of those….and some extra blades just in case…. Including mortise blades which I’m absolutely certain I will need to use in the future.
Hi- no cheese questions this week. After getting your book, I made my first stick chair ever earlier this year. I’m on my third one now. The first two came out ok (in my opinion) The third one I’m struggling on. To be honest it’s looking more and more like dog poop. Too many mistakes. Ex. Mortises in arm bow too large. Not happy with rake and splay. I guess my question is there a point where you will scrap something you’re building or will you plow through just to finish and try to learn from it?
I usually get the chair full assembled (dry) before I pass judgment on it. If I hate it, I can re-use some of the parts (particularly the sticks). I have to say that some chairs look awful until they are assembled.
I heeded your advice and you know it doesn’t look half bad fully assembled. I will proceed lol
In general, how precise are you with table leg prep – length & making sure the end is true?
I am a novice, working on my second worksop table. It’s taking me forever to get the legs ready – rough-cut to length, true a face & edge, then shoot one end true to the reference face & edge. Cut to precise length from the true end. True up the just cut end.
I’m working wtih 4″x4″ legs for this project, so not typical of a furniture project. Also, all hand-tools.
1) do all 4 legs need to precisely match in length – or is that handled after table construction (planing the top flush, trimming the bottoms so it sits level)?
2) in general, do you make sure your leg ends are true to the reference face/edge?
Thanks for everything you do!
1) Nah. Just get them close (within 1/2″). Trimming them at the end fixes all those problems.
2) I don’t worry about it at all. They are flushed up or hidden. I focus on what shows and what is needed for strength.
I’ve been applying Stick Chair book instruction in the building of a staked hearth stool (to sit on while making a fire in the woodstove). I started with a 2’ offcut of 8/4 walnut I got for free that had been sitting outside on the sun, so badly checked on one end. I cut off 4”, but there’s still a few cracks. I applied tapered dovetailed battens to the bottom to add strength, and prevent catastrophic failure. I’m trying to decide if I should try and stabilize the cracks with epoxy, or just let them be, knowing the battens add the needed strength. I’m not aiming for “vernacular”, but I do think the cracks add to that look long term… I posted photos on IG @johnnygreenakers if you want to take a look at the cracks.
If you do take a look, also curious about a small bit of blowout from one of the dovetailed battens. I’d like to clean it up, but not sure if I should just smooth it live edge style, or maybe add some chip carving of sorts to hide it.
Thank y’all as always! Look forward to sharing finished photos of the stool later this week~
These are aesthetic questions. I don’t mind cracks that aren’t structural. We use epoxy only when we have to.
Chipping is also an aesthetic question. If it bothers you, remove it. If it looks like part of the whole, leave it.
Good Morning,
I’m building a Monticello bookcase and debating what to do with the base to help it match our other furniture. Rather than a plinth, I’m thinking of doing legs tenoned into a batten that is then glued and nailed to the base.
Do you think that will be hefty enough? And do you have any recommendations for the thickness of the legs and battens? I was thinking battens from leftover 7/8 material, and four legs at 2″ with a taper.
Hard to say. If the legs have any rake and splay to them, you will be asking A LOT of them when you load up the bookcase. If they are vertical (no rake and splay, sort of MCM) then no problem. Your plan outlined above should work.
Very helpful, and thank you!
Will you guys restock the Medium size Mole skin vest?
I’m not sure yet – the production cost on the vest has risen significantly, and that may price us out of doing them. But if we do, it will likely be next spring/summer.
I don’t believe so. Prices for the materials and work are now too high for us to do another run and feel like we could sell them
Understood thanks
On your recent blog post about using that big stock tank to boil chair parts for bending, you put that big tank on your stove in your kitchen, and some folks cautioned against heating galvanized steel like that because of the potential zinc fumes.
I got to thinking, and perhaps a better approach would be to use one of these things to heat the water rather than heating the tank:
https://www.amazon.com/Immersion-Portable-Stainless-Thermometer-MotorhomeTub/dp/B09GLMPLTP/ref=asc_df_B09GLMPLTP/?tag=hyprod-20&linkCode=df0&hvadid=532660782899&hvpos=&hvnetw=g&hvrand=7575557623252940165&hvpone=&hvptwo=&hvqmt=&hvdev=m&hvdvcmdl=&hvlocint=&hvlocphy=9018508&hvtargid=pla-1435984028290&psc=1
I then went searching for an affordable watertight container that could handle boiling water, but be long and skinny enough to boil the biggest chair parts without having to use such a huge amount of water. The closest thing I could find was a speed rail, which is a little stainless steel boxy shelf used in the restaurant business:
https://www.centralrestaurant.com/kratos-single-tier-stainless-steel-speed-rail-48-p29n-101.html?gbraid=0AAAAADt7ldX8GIfSmTuqVvL-FQ72IBcou&gclid=EAIaIQobChMIvrbuvKKHggMVVxKtBh2MowfPEAQYAiABEgIUqfD_BwE
Instant part-boiling system for less than $100? Could it be that easy?
I’m mainly posting g this here to get someone else to try it and report back 😉
The Speed Rail looks promising. I would ask if it is watertight. But 48” isn’t long enough for me. I need 54”.
Another option (which I did) talk to Eric Pintar at Shaker Oval Box dot com. They will weld you up one in any size. It’s galvanized. But it is not a problem when boiling water. Promise.
A photo of your kitchen cabinets looked like there was a bead around the whole draw on the face frame. How do you get the bead to go to the corners? It didn’t look like a mitered butt joint, but if it is then I’m really impressed at how seamless it is.
The answer is, “write a check to a kitchen cabinet company.” We don’t have the time, space or equipment to build a large run of cabinets. (I’ve done it…and they were built like furniture. Which is stupid.) So I’m afraid I don’t know for sure, but looking at the ones in the kitchen downstairs (same maker), the answer is a mitered joint, sprayed with conversion varnish…which seems to hide seams.
First off, I recently got a job at a small furniture shop, and a version of your staked work table was my audition piece of sorts, so thank you for that!
Second, I recently had a southern red oak fall through my house. I saved some of the wood and I’m going to make some revenge chairs and display them prominently as a warning to any other trees that may wish to cross me. I’ve got some wedges and a froe, but have never done any riving before. For chair parts, would you recommend trying to rive the logs into planks, or wedges, or something else entirely? Perhaps a mix of planks for things like the seat and comb, and wedges for legs and sticks?
First, get a book on green woodwork. Then a chainsaw. (Or hire a miller.) Is the tree dead-straight? Is the pith centered? This might not be a tree destined for stick chairs. That said:
Seats, arms and combs are best sawn out of the log (though you can rive them). Sticks, legs and stretchers are best river (though you can saw them).
If it were me, I’d evaluate the tree closely. If it is a perfect “chair tree” then I would chainsaw a straight part of the trunk and bust out legs, stretchers and sticks with wedges and a froe. Any crooked part of the tree I would have sawn up into 2″ thick planks for seats, arms and combs.
In the stick chair book you suggest pinning the comb to the sticks. Why not also pin the sticks to the seat? Any reason not to do that?
You can pin all the joints if you like. My approach is to only pin the sticks to the comb/backrest. Here’s why: Future repairs.
The pin is the primary thing that holds a comb to the sticks. There is some glue strength, but not a ton. So if something goes wrong up there, drilling out the pins allows for an easier repair.
However, in the seat, the joint is all a close-fit and glue. A pin will inhibit repairs if a stick snaps.
Other chairmakers have different approaches. Mine mimic the old ways so I can try to understand the reasoning.
Thanks!!!
Good morning. I have a workbench question. Any thoughts on HNT Gordon vises. Pros & cons on the tail vise and front vise.
Thanks
Haven’t used them. But they look fantastic. And other knowledgeable people love them. Sorry.
Thanks for your reply on sawbenches–friction fit legs. Im using hickory (top)and white oak (legs). As I have the wood I think I will make two. In case anyone is interested I have a great sawyer nearby: kiln dried and green; almost any native hardwood you can think of, softtwoods too. They cut my orders to rough size and I finish.
King Lumber, just outside Wauseon, Ohio. Owners are great folks to work with. They have supplied all the wood for my benches, chair, work chest, dovetailed boxes, kitchen island.
Brad
I’m wanting to add something to my tool chest for tricky grain. I was planning on getting a 55 degree frog for my smoother. But now I’m leaning towards the Veritas cabinet scraper. Any opinions on the two? Thanks!
It’s all personal opinion. I don’t use either of those approaches (though they work – I have used them). I prefer a smoothing plane with a close-set chipbreaker (there’s nothing more to buy). And a curved card scraper (far less complex than a cabinet scraper).
There are times when a cabinet scraper would be ideal – large tabletops with lots of swirling grain. And when you need a dead-flat surface for a glossy finish, such as French polish.
Bottom line: Your plan will work fine. Mine is different and dumber.
I know you’ve mentioned maple before, but does that include using Big Leaf Maple for stick chairs? That’s what I can get easily here in the PNW. If so would you increase the tenons or anything? I really want to make a chair like the green one you posted which I think is just the most beautiful chair I have ever seen. Really. And thanks very much for making your chair book and video.
How do you know how low or high to put the tenons on the chair legs under your chairs or stools. Love your books and all of your work and posts
Do you mean the stretchers perhaps? If so, it’s an aesthetic thing mostly. Low stretchers are common in old work. High stretchers are modern. There is some minor strength difference between the positions (lower is stronger in my experience). But not enough to be concerned with in my book.
By many measures, big leaf maple is weaker than cherry or walnut. So I would be inclined to bump up your sizes (tenons and piece thicknesses) by 1/8″ all around.
For my first plow plane, do you recommend new or vintage? I’m planning to get a plow plane for a furniture project. I’d like to get something that works pretty well “out of the box” (after I’ve sharpened the blades), so I am interested in getting a new one but they’re pretty pricey. Do you think it’d be relatively easy to get a Stanley No. 45 or 50 that’s in good working order, or should I just go with Veritas?
A Stanley 45 is common and inexpensive. They are easy to set up, sharpen and use. That was my large plow for many years. That would be my No. 1 recommendation.
Thanks!
I’m in the same boat. After a lot of back and forth, I ordered a “lightly used” 45 from Patrick Leach; my thinking is that it will give me more opportunity to find out what I love/hate before branching out into the many varieties of specialty/specialized planes.
Thanks, I’m interested to hear how you like it so far. I took a look at Leach’s website and I’m a little confused about the ordering. His order information included in his emails?
In the kitchen: how’s the French stove? Is that a La Cornue? If so, is the fit and finish as good in person as it looks in the online photo galleries? Curious to get the perspective of someone who is used to handling quality tools.
In the workshop, two questions: (1) for large legs like those on the anarchist work table, how much do you worry about really straight grain? (2) You’ve made a stick chair out of mahogany. Any concerns with using sapele in a similar application?
Thanks a bunch!
I love my La Cornue. It’s overkill. But it is beautiful, inside and out. Once you get a taste for a well-made thing, it’s hard to buy crap.
On the wood questions:
1) Depends on how much downward force the large legs will take. Butcher table? Dead-straight grain. Always. Desk? Kinda straight-ish.
2) No concerns with sapele as long as it’s straight.
A big thank you for doing this. I was trying to use the bandsaw octagon jig from the the Gibson Chair video. Several pieces came out fine but two started by looking like octagons but finished by looking almost rectangular. These were sized and and squared by hand plane and I suspect that I rushed a couple but would like to get better informed input before chasing the squirrel.
Likely one of two problems:
I struggle with design blindness, and my inability to visualize an ash tabletop with some kind of simple but attractive inlaid or laminated walnut strip(s) is paralyzing me into inaction with the whole project.
It’ll be 120 cm by 70 cm, or about 4′ by 2’4″ on a black motorized sitting/standing frame.
Things I’ve tried so far for inspiration: Pinterest, Google Images, cutting boards on Etsy, even Midjourney AI generation. Nothing’s really come up that would set me in the right direction.
One answer might be “just sketch random things, build the one you hate the least and then plan to rebuild it down the line”, but this is not a great option due to the price of lumber, my limited time for woodworking and my perfectionist personality flaw telling me to get it right the first time. I’d like to build something that I could proudly show off to guests without fear of the piece looking outright laughable to anyone who actually does have design sensibilities.
With no knowledge base of design principles to fall back on, I can’t justify any sketch features I make, even if they’re the simplest possible straight lengthwise walnut boards/strips. Why would I have X of them in total? Why would they be these specific thicknesses? Why would they be placed in these spots? And don’t even get me started about shaping the table as anything but a plain rectangle…
Maybe you can’t relate, but in case you can: what kind of a process would you follow in my shoes? Or would you give up and just build a plain ash rectangle and accept your inability to ever build anything attractive if you don’t have someone else design it for you?
It helps to build beautiful pieces to get a feel for them. If you are struggling with design, then don’t. Build something else from a book or museum. Good design is equal parts knowledge and instinct. The instinct comes from building beautiful things.
You don’t have to reinvent the wheel or the Shaker cabinet. But once you get a shed-load of furniture under your belt, you’ll see a path forward with design. Most crappy designers have seen or built enough stuff (in my experience).
I’m not sure if this has been brought up before as this my first open wire, but when it comes to dovetail layout, is there any general ideas you look for in finished or painted work? Is it all personal preference? The Anarchist Tool Chest is silent on this but the illustrations appear to be equal size tails and pins and proportional to the thickness of the panels (at least for this project)
Oops! I was mistaken. The pin are smaller than the tails.
We both lay out using dividers…we just fart around until they look good. Here’s a video on it:
I find myself using my wagon vise more, and less inclined to use (a) holdfast. You have to move the holdfast to different places on the wood because it gets in the way. Am I missing something, I hope this is clear.
If that’s what you like, use it.
Are the rake and splay angles listed for the Welsh Stick Chairs listed anywhere? I’m playing with the chairpanzee and cannot seem to reverse engineer them.
I don’t think I have ever tried to measure them. I design by eye and then use sightline and resultant. If there is a chair in particular you are thinking about, I could try to reverse the process for you.
But if it were me, I’d make a half-scale model using the sightlines and resultants. Then measure rake and splay directly. (Or draw it in CAD).
The new Stick Chair Journal templates with 23 degree resultant and 25 degree back and 21 degree front sightlines would be great. Or maybe a blog about doing the math to reverse engineer it from the Chairpanzee? I have played with the half-scale model I made but it is not really my thing.
Thanks for all your time with these questions. It’s a much valued resource for all of us I think.
So I printed out the drawings on pages 76 and 77 of the Stick Chair Journal and measured the rake and splay with a plastic protractor.
I measured:
Front legs: 19° splay, 14° rake
Rear legs: 10° splay, 20° rake
When I reversed the process through the Chairpanzee it came out close enough for handmade chairs.
Front legs: 23° resultant and 35.9° sightline
Rear Legs: 22° resultant and 64.2° sightline
Fantastic! Many Thanks
Any updates on the claw hammer?
I am the obstacle. Too much to do. The machining processes are done for the metal. I just need to find time to get the handle right and fitting the eye properly. We moved this project to 2024.
Kind folks,
I am about to do a work gig in Cincinnati for 13 weeks. Any recommendations for a travel woodworking kit to make small projects (staying in a small house)? Any recommendations for small projects? Thank you!
Most people use time like that to focus on spoons or small sloyd work, which can be done without a workshop or a lot of tools. Jogge Sunqvist’s two books are excellent for the small kit woodworker.
If it were me, I’d probably take my engraving tools and try to get better at that.
Come visit us at the Cincinnati Woodworking Club as a “Guest”. We meet second Saturday mornings of odd-numbered months at E B Mueller Co. in Reading, OH. CincinnatiWoodworkingClub.org
I am building the staked back stool from The Anarchist’s Design Book with a poplar seat and red oak legs and sticks. The seat is scant at 2 inches thick. Must I add stretchers?
Probably not. The seat is undersized a bit to dissuade very large sitters from popping a squat. 2″ Poplar and oak should be fine for 99 percent of the population.
Hi Chris and Megan,
I used hide glue (OBG) for the first time yesterday. After applying it to the joint it gelled quite quickly but was still soft enough to assemble. Probably because my shop was cold (I heated the glue first to their recommended temp). If hide glue starts to gel before the joint is assembled does it still achieve a good bond?
Thanks for doing this and all you give to the woodworking community!
When it hits the gel point it loses its tackiness. And the bond is not as good. I’d rap the joint with a hammer to see if it pops open. It might be OK. Might not. Depends on how gelled it was.
Along the same line, I just tried a panel glue up with Old Brown Glue and got a consistent 1/64th gap along the entire glue joint that no amount of clamping could remove. I’m thinking it gelled up too much before I clamped it but it’s my first time using it for a panel glue up. Any suggestions?
It might just be that the glue line is visible. I’d try to crack the joint with some pressure to see if it’s sound or not.
To be 100 percent transparent, I like yellow glue for panels. Hide glue for housed joints.
Three questions (feel free to just answer one; I can ask the others in future weeks):
I have a scorp with a larger blade radius, like your Avery. There are obvious differences between the cuts of a smaller radius scrop, like a Barr, and a travisher. However, with some care I can take very similar fine cuts with the larger radius scorp and my travisher. In this case, is the main advantage of the travisher that you can take fine(r) cuts without having to be so careful about it? Do you find more overlap between a scorp and travisher with similar blade radii?
Do you remember a time when you started feeling more competent with hand tools? After several years I now feel fairly confident that I can do most operations and build most things without having to go look up techniques, spend hours thinking things through, making tons of dumb mistakes, etc. Just wondering if you remember a time when you thought “hey, I’m actually ok at this…”, and what sparked that thought.
I live in a big city, and like it. I grew up in a rural area, and I don’t romanticize a home/shop out in the woods a million miles from everything and everyone (but it’s cool if you do!). Did you deliberately choose an urban environment from a business and woodworking standpoint, or would you prefer to be in a smaller or more rural city if you could? Why?
Thanks for taking the time!
Well, I don’t feel competent to answer your scorp question, because I haven’t used them enough…which goes toward your second question. What makes me feel competent is being able to explain and demonstrate a tool/technique. If I can do that effectively, I feel like I’m …if not “actually OK at this,” OK enough! And if it’s a tool/technique I’m not teaching, well, I just have to do it enough to not have to think about it (i.e. if I can listen to a book on tape/sing along with the music, I know it well enough).
And on the urban thing, yes – Chris and Lucy deliberately chose urban (but I’ll let him answer that)
Hi Daniel,
I used a Barr scorp for many years. I can take VERY fine cuts with it and create s nice surface. The Avery makes it easier to get the seat shape I like.
The travisher has a mouth, so you can use it with the grain at times (if it’s a tight mouth). The overlap between travisher and scorp can be considerable, depending on the skill of the user. Some chairmakers can skip the travisher. Some can skip the scorp.
As to skill, I am always trying to learn new things, so I still feel like a beginner (it’s one of the things I love about the craft). But I do see how my new skills come up much faster than they used to. It only took a month before the engraving tools (for example) became fun and easy. Mostly I enjoy know what the next step is in a process without agonizing. That comes after building something a dozen times or so. I don’t know if I answered your question.
Our shop is in the inner city for a lot of reasons. There are lots of people here and allied businesses here. Foundries. Machine shops. Laser shops. CNC. Upholstery. Blacksmiths. On and on. We work with them and they work with us.
We are 10 minutes from an international airport and right near a major interstate. It is easy to get my finished furniture where it needs to go. I can travel. Students and customers can get here easily.
I have more time in the shop because I don’t have to drive much.
It’s easy to be anonymous and a hermit in the city. I am the Poster Child for that.
I grew up with a huge overdose of rural living (compost toilets, solar showers, intense natural beauty). I get it. I love it. But living here is right for us.
I am not sure my question arrived. How much time should I allow between ask and answer before assuming an error on my end?
I answered your question.
https://blog.lostartpress.com/2023/10/21/lap-open-wire-oct-21-2023/
Fitz, what do you use for measurements in the 2 to 3 foot length. Ive been using my tape measure but many say that that”s not the best choice. Thank you, John
Do you mean for inside measurements? I use a pinch rod.
A lot of people say that anything 24″ and shorter should be measured only with a rule – a tape is not accurate enough.
I think it depends on your work (NASA or vernacular). And your tools (precision machines vs. hand tools).
When I am in machine mode, I use a 24″ rule to keep parts bang-on. When I work by hand, I just try to make one part fit another and keep things from looking awkward.
Good morning!
Just assembled my version of the AWB yesterday. Drilling dog holes and holdfast holes today. All of them will be 3/4” holes. My question is on spacing (I’ve already read the Q&A at the back of the book, and your other posts/writings on it). Mt question comes because I haven’t seen you answer it before.
The bench is 8’8” long, but I made this one 37 1/2” wide as I already have a more normal sized one and wanted this to be a bigger surface for assembly as well. Thing is feeling huge. Haha
I’ll figure out the left to right spacing, but it’s the width or depth or however you want to visualize it for the holes. I’m thinking the front row and the back row are both 2 1/2” from their respective edges. Then making 2 more rows evenly spaced between them. So like 13 1/4 for the second row from front and 24” for the third row from front. Leaves about 11 inches in between. Is that the strategy you would recommend, or have something else in mind? Thanks!
Cheers,
Dan
The spacing of the rows is determined by the reach of my holdfast. If my holdfast reaches 7″, the rows are 14″ apart.
I’ve noticed in the book and in other chairs that the combs are pegged from the front. Is there a structural reason it’s from the front and not the back?
I don’t know of a structural reason. But the old ones are done that way, so I do it that way. You can pin from the back. Or pin through.
Hey guys, love your work and your books! Whatever happened to Chair Chat? Am I just out of the loop or is it coming back?
I wish we had the time to do Chair Chat. It was easy during the pandemic. Not so now. We hope to get back to it some day.
You are frequently seen in pictures wearing a carpenter’s apron which Lost Art Press also sells. What tools do you find useful to carry all the time? I use an old carpenter’s leather hip bag to keep my most frequently misplaced tools.
Today I am carrying:
Two 6″ rules
6″ combination square
12′ tape measure
Large-diameter pencil
.9mm mechanical pencil
Sharpie marker
gum eraser
saddle square
hearing protection
When adding through-bolted iron handles to the Dutch Tool Chest, do you have the handles closer to the fixed front or the shiplap back?
Pretty even, possibly cheated 1/2″ toward the back (’cause I pick it up from the front, so that helps to balance it a little with the heavier weight in the back).
Thank you.
Thanks again for being available to answer our woodworking questions. I have a question about scorps. I have an old one that I’ve sharpened as per the approach in The Chair Book. I’ve been practicing on scrap cherry, and while I’m getting shavings, they seem fairly thin. I was expecting that they would be coarser, like when using a Jack plane with a curved blade profile. Am I misunderstanding the function of this tool? I have been working under the assumption that I’d rough out with the scorpion, and use a travisher for more fine finishing. Thanks for any insight you can provide.
The scorp is all in the wrists. Tip the handles down (if you can) to take a more aggressive cut. If you can’t do that because the handles are in the way (i.e. they hit the work), then you either need to adjust bevel of the tool so it is lower. Or bend the handles up.
Hello,
Thanks again for this series. It’s become a fantastic Saturday afternoon ritual.
I’m a 100% hand tool
woodworker for the fun of it. However, after a recent addition to my family I’m left with scant little time in the workshop. Spending weeks of stolen time to process rough stock for a single project has lost its appeal in that light.
What woodworking machine can save the most drudgery while leaving the fun stuff like joinery and shaping for the hand tools?
I was considering a bandsaw but have little experience here. Thanks for your consideration!
The band saw – even a small one – is the machine I could never give up. I have been experimenting with the small 10″ Rikon as a way to help chairmakers without a lot of space. Amazing deal right nor at Highland on these (no affiliation).
https://www.highlandwoodworking.com/rikon10bandsaw.aspx
It is a solid little tool, especially with a better blade.
Second machine would be a thickness planer. Something small like the DeWalt 13″. I used this for many years, even making furniture for a living.
With those two machines (and some dust collection), I’d be fine forever.
For me, it’s the thickness planer first, band saw second, jointer third.
In Welsh Stick Chairs, in many of the photos, John Brown is wearing the most wonderful hat. Is this a traditional part of the profession in Wales? And more importantly, can anyone tell me what the style is called, and/or where I might find one? Many thanks!
Well I should ask David Sears about this to find out the real answer. Pillbox hats like this are worn by chefs. Any restaurant supply store will carry them. With a tassel, some people call it a smoking cap. I’ve seen it called a Darveshi style cap. Some call it a fez…..
Also, a Kufi hat….https://www.amazon.com/Dupsies-Black-Wool-Felt-African/dp/B098Q154DW/ref=asc_df_B098Q154DW
Any changes to the staked stool design from your recent class build vs the one in the design book? Rake changes? Splay? The 3 legged stool didn’t have through mortises for the legs, but this one does.. all because the seat is thinner? (Thanks as always for taking questions from the wild)
The staked stool we build in classes is also from the Anarchist’s Design Book – the chapter on the creepie. It has a 21° resultant. The joints are through because the top is indeed thinner.
The three-legged stool is one that I make from scraps. No undercarriage.
Hi Megan! In the event you have tried out your benchtop bandsaw what do you think if it?
I have made one cut with it. It worked. (We replaced the stock blade with a 1/4″ from Highland Hardware) So far, it look promising.
Hi Chris, I am writing to inquire what happened to the Irish bog oak chair with the little bit of live edge across the bottom front edge of the seat. I’m the guy who posted a comment to Instagram encouraging you to leave it, and then asked you about it at Handworks. I’ve been checking the blog regularly, and haven’t seen it come up for sale. Did I miss it, is it still in process, or did it end up in the firewood pile?
I gave it to my daughter and her husband on their wedding day. I’ll have another bog oak chair for sale soon.
Making stick chairs (I’m on my 4th and 5th chairs so still pretty new to it) yesterday the 1” white oak tenons when wedges were driven in split beneath the 1 3/4″white oak seat on 3 out of 4 legs. The splits are small and run about 3/4 to and inch down the leg. I’m not worried about stability but I am wondering if perhaps I kerfed the tenons too far? Or maybe my wedges (Ash) were cut at too steep of an angle? Have you ever had this happen? Thoughts? And thanks in advance.
It happens. I wouldn’t worry too much about it. You might have had a loose joint fit, which will make a split run like that. Or a too-long kerf.
You’ll find it on old chairs. You are in good company.