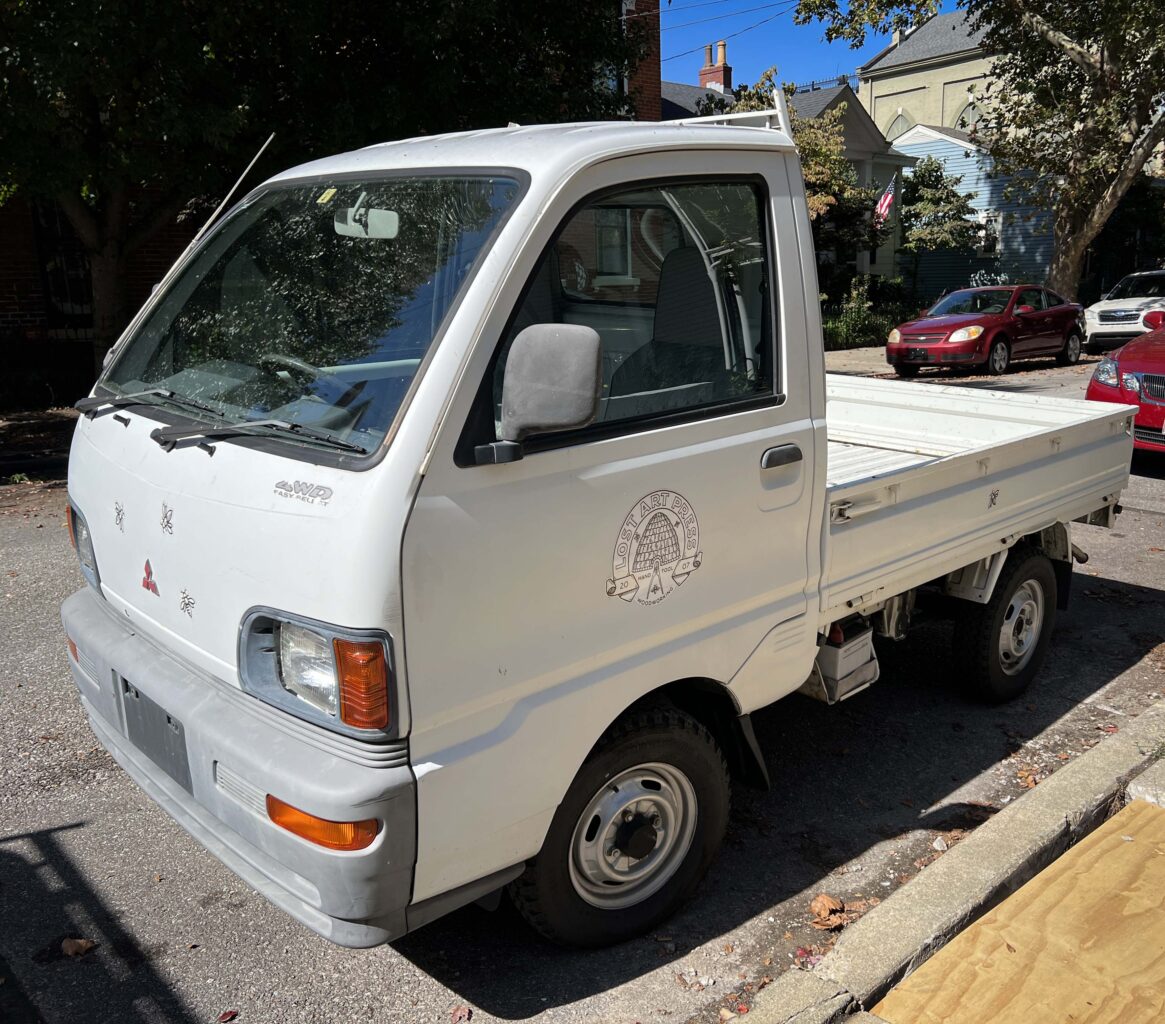
Today, Chris and I are taking turns behind the wheel and at the keyboard (one person per job at a time, of course); we’re headed to Wisconsin to celebrate a dear friend’s birthday. You can help us while away the travel hours with your Open Wire questions.
As always, simply post your woodworking questions in the comments below (brevity is appreciated), and we’ll do our best to answer them. Comments will close at around 5 p.m. Eastern, or when we run out of internet, or when we reach our destination – whichever comes first. So if you have a question, I’d recommend not waiting until the last hour today – there are swathes of our journey that might be out of cell service.
– Fitz
p.s. No, we are not really driving CATBUS; we need to get there in one day.
My question is can you construct your gibson chair without the use of a template? Set up the locations for the legs, sticks, posts, then use your sliding bevels to approximate angles, fore/aft, rt/left. Once the sticks/posts are properly seated then place the arms/back rest over to est location for mortises.
Thank you.
Brad
It’s likely that the original ‘vernacular’ chairs in Ireland (and the Welsh Chairs too, for that matter) were made by eye, using what scantlings were left over from other, bigger things. The size and shape most likely determined by what was available. Wood in forests in bygone days belonged to the landowner and was definitely not free to take.
For example, Elm for seats in Britain (and probably Ireland), were plentiful at one time – no longer so, due to Dutch Elm Disease – as a by product of coffin-makers.
On this subject, try to search out a poem by Thomas Hardy, written in 1916, entitled, appropriately, ‘The Work Box’.
Good luck.
That’s basically how I did it when I made a “Gibson-like” chair. Mine was a little wonky but not bad for a first chair.
Sure. These chairs were made in a production shop, so I suspect they used templates and jigging for some operations. But there is no reason you can’t go Full Vernacular with these forms.
Any suggestions for a toy box for a soon-to-be 4 year old? I’m thinking of basically scaling down the ATC but perhaps there’s a better idea.
That’s a lot of work for a toy box. I’d probably just make a six-board chest and use the special no-slam hinges.
May I suggest a stool height 6 board chest? https://aethelmearcgazette.com/2017/10/24/lets-build-a-mary-rose-chest/ written by a friend of mind will get you started and doesn’t require a ton of tools. It has unfortunately been experimentally discovered that the commercially glued up boards don’t have waterproof glue, but if you glue up the front and back panels and lid you can make the whole thing from 2 1x12x8′ planks. The author and I walked a friend through making one at a 2 week camping event, took a week doing one thing a day, was her first attempt at woodworking, and came out very well.
Rope in bracket or other handles optional if it won’t be moved much and you may want to investigate soft close hinges.
Thanks for the link! I can’t seem to find 1×12 where I am but have had good luck in the past gluing up 1x6s.
Thoughts on using QS white oak for the seat of a staked stool?
Absolutely yes.
I’m building the ATC. Yesterday, I assembled shell with hide glue without clamps because I didn’t have any large enough. It’s out of square. Diagonal measures are about 1/8 different. I made a parallelogram… ( Two diagonals obtuse, two opposite acute). The joints I beat into place and I’m afraid of taking it apart. Can you recommend a method of fixing it? Also, how did people do large casework without metal clamps in the past? Thanks!
Clamp across the long diagonal. While in the clamps, nail or screw the bottom in place, making sure the ends of your bottom boards are shot square.
Clamps have been around a long time, whether they were iron or wood. But you don’t need them as much if you are clever. Mortise-and-tenon joints can be assembled via drawboring without clamps. Dovetails, when tight enough, are a self-clamping joint.
Thank you so much, the nailing the bottom while clamped is awesome.
I’m curious why you mainly (exclusively?) suggest using powered tenon cutters and reamers, rather than the hand versions, for chairs. Ease of use? Cost and availability? Is there a practical reason to stay away from the hand cutters and reamers?
I have a cordless drill and I build a LOT of chairs. So the power tenon cutters are the way to go. (Plus, less tendonitis.) I used hand cutters/reamers for years. They work great. Choose your own poison.
Hi – Very new to chair building, in the process of gathering necessary tools and info (greatly appreciate all of the latter you share); taggin onto the question re tapered tenon cutters & reamers: If ordering Veritas from Lee Valley, I believe you have suggested the 5/8″ tapered tenon cutter, correct? And do you go with the large, or small tapered reamer? I will build VERY few chairs (if I someday complete just one that I’m not completely embarrassed of I will be happy); would like to do so on a tight budget as well – if there is something less expensive than the Veritas that will get the job done that is even better – Thanks!
Use the large tapered reamer for 5/8” tapered tenons.
I want your truck.
Now that I’ve got that out of the way, what do you use the truck for? And is it public-road legal? Any other fun facts or trivia about life with it?
I’m interested too!
It’s legal in Kentucky and many states. Just keep it off the interstate. I love the thing and wish I had bought it earlier. It moves everything and anything. Its bed is winder and longer than the bed on my Tacoma. And it low (easy to load). And all three sides fold down to create a flatbed. 52 miles to the gallon. Parks anywhere. Brings a smile to my face every time I drive it.
Cool! Thanks.
I love the truck, too. Unfortunately, in any of the 50 states, though I can maneuver around in all manners of vehicles (was a county park ranger so many summers ago and drove a flatbed truck within the park), I cannot get a driver’s license on account of sub-par vision. Anyway, for some reference, do you know if there is an EV version of your truck?
Dunno. Check out Duncan Imports in TN for mini truck info
Favorite easily available paint brush for linseed oil paint? And for milk paint (Old Fashioned and Real, not the acrylic “milk” paint)? Thanks!
Have a nice drive and stop at Kopp’s in Milwaukee if you need a burger or to taste the flavor of the day.
Megan, the Brush Princess, will have to answer this one.
My favorite for linseed oil (so far) is the Wooster Yachtsman angled white china bristle. For actual milk paint, I like a cheap chip brush (pull all loose bristles first)
Thanks Megan!
Aside from the cost of the wood, is walnut strong enough to be used for a stick chair? Assuming grain is straight.
Thanks
Absolutely yes. I have made about 10 stick chairs from walnut in my time.
Thank you.
Do you play the ABC game while you travel?
I don’t. Mostly listen to music (or catch up on podcasts). And enjoy the scenery.
Got a lay list to share & what pods do you listen to?
Morning Chris and Fitz,
I have a rod back chair with a broken rod (the back post) I used hide glue but it I also has a tapered tenon and is wedged.
The break is through and through and very low to the seat.
I’ve turned a new post and
My plan was to saw off the post at the break and then heat the joint.
Two questions. Do I use a heat gun and douse it with warm water ?
What about that wedge -do i drill the tenon and wedge and re ream it.
Any tips welcome appreciated .
Dave
Can you get at the broken stump with a drill?
If so, try drilling out as much of the centre of the rod-stump as you can with a sharp twist-drill, leaving a thin piece of the original rod around the hole, but not touching the wood of the original seat.
One trick that I picked up from an old restorer, was to select an old drill bit of the same diameter, then holding it with pliers, heat it and slip it into the hole. This transfers heat to the original glue very quickly which allows you to pare the old remnants out. You may need to repeat it a few times to break the original glue-bond.
It demands some accuracy and care with a sharp drill, but this will allow heat to penetrate directly to the original glue without affecting the area or the finish of the original seat which may happen with indiscriminate hot air from a heat-gun or the like……
Personally, I’d avoid water……. it has a nasty habit of getting things wet and leaving stains behind – solve one problem and substitute another!
Good luck with the fix
We approve of this answer
Great advice- much appreciated- I’ll give it a go
If you are going through Milwaukee don’t forget to stop at Kopps. They got some good flavors today.
Welcome to Wisconsin! (If you are coming thur Madison avoid campus, it’s Homecoming!
A big thank you to both of you for sharing your time and expertise.
I am enjoying making a DTC from Megan’s FWW article. First time for me to make dovetails, use square nails and linseed oil paint. The dovetails came out ugly, but I learned a lot.
I love the Ingenious Mechanics book and experimenting with work holding on low benches.
Please keep doing what you do!
Thanks Evan! Welcome to the craft!
On that last chair you posted, what finish did you use? I really liked that.
The red one? Two coats of General Finishes Tuscan Red milk paint, with a coat of Black Bison wax in Dark Oak.
Will there be a PDF version of the Cricket Table Book?
Thanks
That’s up to the author, and I haven’t yet discussed it with Derek.
If you had to re-handle a ‘pig sticker’ style mortice chisel and didn’t have some beech handy, what wood would you use?
Chris says probably maple — or something else not easily split or rived (ironwood/hornbeam, e.g.)
Not sure of this, but I think a lot of the old British pig-stickers were handled with elm.
I’m in Florida. Will SYP do?
If it’s dense slow growth, probably
I’ve rehandled a few, probably about a dozen now. That bit about not easily split is exactly what to look for. I live in the Midwest, got some large pieces of honey locust that has been very difficult to split. Perfect for these handles and it’s a really fun project besides. Worst case scenario, the handle breaks and you make another one with what you learn from the first. If you’re passing through Indianapolis, send me an email and I’ll give you some of the locust:
cwclark1@gmail.com
I’ve been tooling up over the last couple years to build a chair (limited funds). What would make a better first chair to build a roarkie or a Gibson?
Gibson can be made with minimal tools and there’s no saddling (unless you want to); Roorkhee takes a lathe and leather working tools. So the Gibson will cost you less, I think.
Hi Matt, my first stick chair is going to be (hopefully starting next week) the American Welch Chair from Chris’s new video on the Wood Wisper’s Guild which I highly recommend. It is designed to be built with regular tools (band saw nice but not required) and only a couple of “chair” tools.
Good morning,
If you were to make your chair from the Stick Chair Journal for a larger individual, what would you adjust? The seat width? If so, do you keep the same number of sticks for the back?
Thanks in advance. Safe travels.
Make everything wider, up to 24”, make sure there’s an undercarriage, 3/4 sticks instead of 5/8. Add a stick or two if it looks better, says Chris.
Thank you for your input
In the ADB (expanded edition) chapter 17 on the Staked Chair, I cannot find any reference to the radius of the curve on the back edge of the seat. I also searched chapter 16 on the Staked Backstool as it uses essentially the same seat shape. Am I being obtuse or are you intentionally leaving this up to the reader’s discretion?
The radius, which results in a curved row of back sticks, and in conjunction with the crest forms a truss effect on the back structure. Is this important to the strength of this chair as it has no arms to brace the back?
Thanks!
I asked the same question in an earlier Open Wire. Chris replied 13” I think I changed it to 15ish though.
Good luck
We’ll have to look at the book for that one; Chris will reply tonight or tomorrow (even if comments are closed).
If you were asked to provide three pieces of advice – advice that would have helped you with every project you’ve ever made – and that advice had to come in the form of a single Haiku, what would that Haiku be?
“Oh Brother Squirrel
We are one — your tail, my hair
Now I must eat you”
A bit of bloodthirsty Zen?
For an ADB low staked stool, what is the narrowest leg (in straight grained, riven ash) that you would feel safe with?
Sizing parts by hand from the wood pile is yielding legs closer to 1 5/8 than the 1 3/4 in the design. Should I put in the work to make new larger legs, or am I safe to keep building?
Wishing you both all the best on the road trip- thanks for still opening the wire!
Its supposed to be 1 1/2”. There was a correction https://blog.lostartpress.com/2020/01/21/errata-staked-low-stool-in-the-anarchists-design-book/
Hi how would you make the curved element of a tapered table leg that the bottom 6” is curved outwards. I have a picture but not sure I can attach it here
Steam bend that section, or find the butt end of a log that has curved grain in the direction you need (says Chris)
Megan & Chris,
Thanks for doing this again; here’s my query. I’ve had a large ash tree milled in the garden and the boards are big enough that (once they’re seasoned) I could make a desk or table top with just one or maybe two of them. I seldom see this done though, I assume because of the risk of wood movement. Is that likely to be a problem and how should I best mitigate it: choose a board from near the centre of the log, rip them to narrower lengths and edge join them, go for a bread-board design? Grateful for your thoughts.
Thanks, Huw
Lots of old furniture has single-board tops; you don’t see it now ‘cause not as many appropriate boards. Use quartersawn and that will reduce the risk of cupping.
I am starting the AWB and have a question I am somewhat embarrassed to ask… but cannot find an answer in the book or the blog posts.
I have ripped all the bench top boards from the 2 x 12″ SYP and started the wood prep to square and size it to the 1¼” x 5″ x 7′. Only 7′ long to fix in my shop. I prepped the boards to 1¼ width and squared it up for 1 edge and 2 sides, but have not decided how tall to make the prepared boards for the 5″ target height of the finished top.
As part of the bench top glue up & cleanup I assume I will lose some height to get it all square and level.
Should I be 4 squaring the boards to the finished dimensions of 1¼ x 5″ or just leave one edge rough/extra wide? Or pick a size like 5½ for planned cleanup?
Looking for some general advice on the prep for something this bulky. Pretty sure I will need some extra height to make sure I do not go under the planned 5″ heigh.
And because I am a gluten for punishment, am doing everything by hand with hand tool kit I moved into my DTC I just finished. I.e. Panel saws to rip and size and #5, #7, #40 ½ planes to prep.
Pick a slightly oversized size if you like, and clean up to it. But know that 5” isn’t a critical dimension; anywhere near 5” is fine.
Maybe I’m answering by writing, but I’m fitting the interior of an ATC. I know Chris writes (and Fitz says in video) that the sliding tills should be tight fit to sides to prevent racking. It appears that my carcass is very slightly out of square. So, it means to fit slides “tight” at the front creates a very slight play at the back…..not much, but enough so that it’s not “tight.” Is this normal? Should I do something crazy like try to reinstall the slides on side to compensate for this, or just live with it. When I try to slide trays now they are okay but can rack. However, I haven’t yet installed the tills on them, which I assume will help hold them in place. Hope that makes sense.
Safe travels.
What I do in a case like this (not that it’s ever happened to me…haha) is to fit only one of the bottom boards on each till as tight as possible to the narrowest dimension, and use that bottom board on the side of the till that’s tight (eg, if the back is tighter, use it in the back of the till). Then use a lot of wax on the edges, and pull from the middle. If it’s still racking a little and getting stuck after the till sides are attached, a strip of UHMW plastic tape can be magical.
This raging controversy is probably what brought down the Roman Empire. What’s your take on the easiest way to hand-cut dovetails, pins first or tails first? Or does it mostly come down to what a person gets comfortable doing? I know Frank Klausz does pins first,; others do tails first. Thanks!
I cut tails first (usually), as does Chris. A) you can gang-cut. B) holding the saw at the angle for the tails is the more difficult cut than the straight up and down of the pin cut. So I teach people to cut the “difficult” one first, then the pin only has to match it. (The saw spine helps keep the pin cut at 90 …as long as you don’t get in the way of the saw)
When finishing with linseed oil paint, is there a specific brush that you prefer? Thanks!
I see that my question was answered above.
I found a guy with a chainsaw mill who has a lot of 8/4 white pine that was cut down about a month ago. There’s an 18″ wide and 21″ wide board. Between these I could get seats for about 5 chairs, and stock for a simple roman workbench.
BUT… should I have any concerns with using wood this green for the seats / workbench “top,” with kiln dried red oak legs? Do I have to wait for it to dry a bit to avoid excessive cupping, splitting, etc?
For the bench: The moisture content should be at equilibrium to its home if you don’t want it to cup (and most movement is as it loses the last few percentage points of moisture).
For the chairs, it can be a little wet, but not by much. (Per Chris…I dunno…I build casework)
Hello to the pilot and co-pilot!
Is there any extra tip/caution/consideration for building the Low Back Chair entirely in pine? Fell free to tell if this is just a dum idea.
May you have a smooth drive
If it’s white pine, the components need to be significantly thicker (2” if you can manage it, 3/4” sticks). If yellow pine, slightly thicker. Download the free book for the chapter on this. https://lostartpress.com/collections/all-books-1/products/the-stick-chair-book
If I was going to be driving through Covington later today, would anyone be at the storefront to sell me books and or tools?
Sorry I’ll miss you!
Sorry, no.
Good morning kind travelers! My question is regarding your Conover lathe. Does the headstock bearings run hot on your machine? I’ve had my lathe for several years now and I replaced the bearings and seals after the first year. Before and since that it always runs fairly hot after just a few minutes of running. I’ve played with the bearing pre-load nut experimenting with numerous amounts of preload but nothing seems to make a difference. I’ve followed (to the letter) the instructions in Conover’s owner’s manual.
I typically turn at the 1700 rpm belt setting.
I’m a pretty good mechanic and have done many machine rebuilds over the years so working on this lathe seems a pretty minor project. But, that said, I’m feeling pretty stumped with this persistent hot running problem. I’m wondering if this is typical for that type of lathe (running open tapered bearings).
Thanks!
All we know is that yes, it runs hot. And you’re certainly a better and more experienced mechanic than Chris…so we should be asking you!
I’m wanting to make a chair for someone 6’5″. Does the entire chair need to be upscaled – leg length, seat depth, arm, height, back height? Or am I over-thinking it?
You’re overthinking it; 6’5” is in the range of normal. Unless they are 300 pounds, no need to upsize..
If you could only work with one species of wood, what would it be?
Fitz: Air-dried walnut
Schwarz: White oak
Do you have a go-to bandsaw blade that you use for most/all of your wood processing? Brand, tpi, etc?
1/2” Woodslicer
https://www.highlandwoodworking.com/woodslicer-resaw-bandsaw-blades.aspx
Perfect! Thanks so much.
I’m building the AWB. Almost done! This one will be in the middle of the shop (not near walls), and I’m about to chop the mortise for the planing stop. Why is your recommendation on location so close to the leg vice? Obviously, I’m gonna put it close to the front face, but can’t I just push it further towards the end? I really like having more unobstructed work area around the leg vice, so I am wanting to push it closer to the end of the bench (perhaps 2” in from the front face and 4 or 4 inches in from the end). Am I missing some crucial aspect of its placement being closer to the vice? Thanks!
Safe travels.
It’s so your body doesn’t run into the leg vice chop/screw while planing. Running into vises hurts.
I’ve started falling down the rabbit hole of washed linseed oil. I’ve already got a bit of Tried and True Danish oil, which is I believe has been already heated and polymerized (I could be mistaken). Is there any benefit to washing this type of oil? I’ve read guidance to not try and oils that have been heated like “Boiled Linseed Oil”, but haven’t found out why. Just typing this out feels like more of an organic chemistry question than woodworking, with lots of black magic that I don’t yet understand.
I’m afraid we don’t know enough about tried-and-true to answer the question
Have you found Steve Voigt’s blog posts on this? He has good information and is hosting Tad Spurgeon’s work, which goes deeper. It certainly is a rabbit hole, potentially a rewarding one though.
I don’t yet own any kind of a grooving plane. Can you recommend a place to start? I’m thinking of something to create grooves for door panels, bottoms or backs. Thanks!
A Stanley 45 is a great plow plane. Lee Valley makes a fine new combination plane as well. Or you can buy an old wooden plow. Lots of ways to go no matter what your budget or taste.
Hello good traveling folks.
I only yesterday finished my first stick chair. For the last week I’ve been eating, sleeping, working and thinking about this chair and the next steps. Now I’m already starting to design and build a second one. Is there a cure?
Fair winds!
The only cure is to build more chairs until you get them out of your system.
A laziness and frustration question. I need to reglue the kitchen chairs for the eleventi-eighth time. Giving up on hide glue finally, here in the Yucatan. Gluing the seat to the back sticks. Two mortise/tenon joints.Can I simply draw bore them with no new glue? Or do I have to clean off the hide glue and use PVA.
Thanks
Sure, you can drawbore them – if you have enough material in the tenon to do it without weakening the tenon.If they are inexpensive chairs, epoxy might hold better.
Good morning! Thanks for doing these, I look forward to them every Saturday.
Not sure how clear of an answer I can get but I might as well try: I only have one spokeshave, and it’s a roundbottomed metal shave, I think Kunz (one of the green ones.) It does not take clean, tidy shavings like I get out of my planes, and instead makes a mess of anything I touch. I have sharpened the iron (though I will try again, maybe I did a bad job?) but do you have any suggestions on what I should try? Is a round bottomed spokeshave something I should only ever use on interior curves so maybe it’s too aggressive for random other tasks (like chamfering?)
It could be a lot of things:
My recommendation would be to find a vintage Stanley 151. They are plentiful, inexpensive and damn nice.
When you get a chance, could you please post the dimensions for your recent green Irish chair? Thanks
It is the Irish-y armchair from “The Stick Chair Book.” It’s a free download here:
https://lostartpress.com/collections/all-books-1/products/the-stick-chair-book
I used a slightly different shape on the backrest. And the sticks are faceted instead of rounded.
So I have converted to using bees wax and linseed oil finish almost exclusively. Haven’t begun to make it myself yet – so I’ve used what I have bought from The Anarchist Daughter. My latest project involved a drawer of oak plywood. I used the finish as I normally do, but after a few days it began to smell rather foul (hard to describe the scent; almost rotten). Normally it smells so good. I have had to keep the drawer open to keep the smell down, and it doesn’t seem to go away. I’m not sure if it is the original or 2.0 – I had some of both and now I’ve only got half a bottle left. I used it on a table and I don’t have the smell problem – perhaps because it isn’t an enclosed space? Has this been a problem you have had trouble with, or heard about? Any suggestions on a cure? Before I noticed the smell the drawer just had stationery in it, so I think it has to be the finish.
Thank you! Drive safe.
Usually oil finishes aren’t recommended for the interiors of case pieces. The oil can take forever to cure and can be attacked by bacteria and get a foul smell. I’d remove the oil/wax by wiping it with mineral spirits. I leave the interiors of my drawers bare. Or, if you really want a finish on the interiors, use shellac or lacquer or a film finish.
I made a batch of Soft Wax 2.0 and kept it in a tuperware container. I used about half of it. Over time, the remainder has polymerized into a rubbery glob. Is this normal or should I be using a different container? What is the shelf life of the wax once made?
Thanks for taking the time to do this.
If kept sealed, it should last indefinitely. Perhaps the plastic container leaked air? We’ve kept large tubs of the stuff for a couple years with no problems – as long as the seal was good.
Once you cross the border into Wisconsin, it’s illegal not to present a cheesehead hat. Will you immediately put yours on or just at the birthday party?
My cheese hat is on the inside of my skull.
We stopped for curds at the first conveniently located cheese curd provisioner
I just finished the version of the 3 legged stool from the blog. It turned out fantastic and I love it!
I have a question about the tennon depth. I apologize if I missed this from your design book, but what’s the rule of thumb for the tennon depth in a seat? Mine ended up being 1 3/4” deep.
Lastly, funny incident with the mortise. A 1” wood owl bit is actually 25mm. I didn’t realize and ended up “shoe shining” the tennon with sandpaper.
Thanks to you guys for your help and time!
1-3/4″ is deep enough for almost all staked pieces, including the stool.
And the metric/U.S. Customary Units discrepancy is real and can bit you in the butt on occasion.
I admire how clean and neat the Lost Art Press always is. A companion volume, Clean Up That, to accompany Sharpen This seems an easy one. Until then some short answer questions:
Broom, vacuum, or compressed air?
Clean up every morning, evening, after each task, or when your messiness threshold is reached.
Best argument for a clean, neat shop.
I don’t advocate cleanliness for others. It’s not a choice with me. It’s the only way I know how to work without losing my mind.
We use quality brooms and dustpans to get the big chips and shavings. Shop vacuums to get the final debris.
In general, I tidy up after every operation – just quick sweep to keep the mess down. At the end of the day, I put the tools away and vacuum up around the workspace. Every week we do a “bigger tidy up” on garbage day.
I know lots of people who work just fine in a messier shop. But my personality won’t allow it. Never has.
Don’t let Toonces drive the CATBUS. He’s used up several lives already, and you don’t want to accompany him on his adventures. WI curds are great. Just don’t let ’em get warm. They don’t smell so good.
Do you have any tips for fitting threaded dowels and tapped holes? I have cut some in attempt to make a vise but they squeal horribly when put together. I did oil them and am wondering if sanding the threads would help any.
I should clarify, the dowel is oak and the receiving threaded hole is Pine, 1 inch
Sounds like your threadbox needs adjusting. Just a little deeper cut.
Sanding the threads will help. But I’d try making new threads.
Hi All, what a gift you all provide with your time and knowledge. Thank you. My question is guidance on stick chair back angle. I see Chris’s personal chairs offered for sale vary on their back angle. What is your design guidance for a comfortable reading 7 back stick chair vs a dining chair. I think I have seen 12, 15, and 17 degrees with a 1” drop in the seat front to back. Are there construction issues I should be aware of?
That is covered quite well in the Stick Chair book, in the Chapter “Chair Comfort & Design”. Much better to know the “why’s” rather than just following plans. You might measure some chairs you or some friends already have to get a feel for the angles, etc. Have fun!
I use 11-12 degrees for keyboarding and dining. The other angles approach lounging angles. They can still be used for dining (esp 15).
There are other factors that come into play, such as the height of the comb/backrest. But first decide on a back angle. Then fool with the comb’s position after assembly of the rest of the chair.
Chris, I was inspired by your post on building the beautiful green Irish armchair which was some version of work with what wood you have on hand. I left the lumberyard with more cherry for the top and subtop of my second drinking table from The Anarchist’s Design Book but with my leg stock being 1 7/8″. Is that doable for the design and strength of the joint? Is laminating the cherry to get the proper dimensions not a good idea for legs that are under significant stress in that design?
Thanks.
Oh sure. As long as you don’t dance on the table I think you’ll be fine.