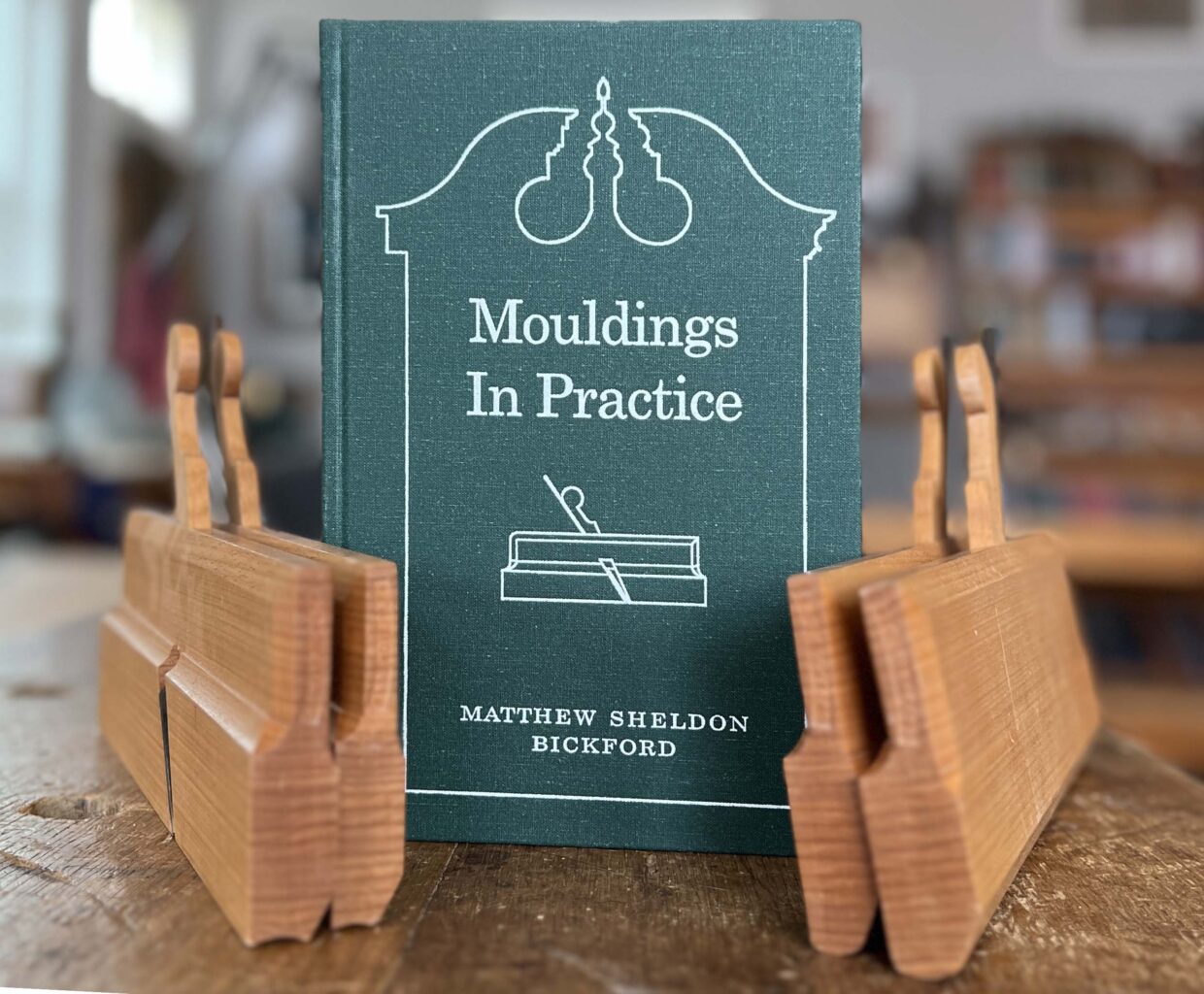
We’re delighted to have Matt Bickford, author of “Mouldings in Practice” (and he’s working on a book on making moulding planes!) on Open Wire today to answer your woodworking questions. (And he knows a lot more about making high-style furniture than do Chris or I – so now’s your chance!)
Here’s how it works: Type your question in the comment field, and Matt will do his best to answer it. And know that concision is much appreciated. Comments will close at around 5 p.m. (Or today, at 9:16 p.m….oops!)
– Fitz
Hi Matt. Thank you for hosting Open Wire. My question is, if you only had one moulding plane in your toolbox which would it be?
Phillippe,
My reply to you appears as a reply in the following comment to Matt.
Sorry,
Matt
I am new to molding planes. If you could only buy a couple sizes of hollows are rounds what sizes would you get? And additionally what would be some good practice moldings to make with those?
Phillippe,
I’d probably choose a 3/16″ side bead.
I don’t recommend this plane to be the first plane moulding plane that somebody acquires, however. 180 degrees of a 3/16″ diameter is not the ideal item on which to learn how to sharpen a profiled cutting edge. Start with something like a 5/16″ Ovolo or a pair of #6s.
Matt
Matt,
You can make dozens of profiles with a single pair of hollows and rounds. Every pair you add will exponentially increase your options. Starting with two pairs will afford you the ability to recognize the versatility that the tools both allow and encourage.
I’ll recommend starting with pairs 6 and 10 if the scale of moulding is for furniture that is chest-height. 4s and 8s are good if you’re looking to adorn furniture that is waist-height. 4s and 6s if you’re making objects that stand upon other objects (e.g. mantel clock, spice box, jewelry box, etc.)
Get hollow/round pairs 4, 6, 8, and 10 and you’ll be able to accomplish 80-90% of most things.
When learning to use the planes, start with single, 60 degree arcs. Then go to 90 degree arcs. Then mix and match the hollow with the round to make a cove and Ovolo. Finally, make an ogee.
Matt
Matt,
You can make dozens of profiles with a single pair of hollows and rounds. Every pair you add will exponentially increase your options. Starting with two pairs is ideal because you’ll then be able to recognize the versatility that the tools both allow and encourage.
Generically speaking, start with pairs 6 and 10 if the scale of furniture you’re making is chest-height. 4s and 8s are a great combination if your scale is waist-height. 4s and 6s compliment each other well if you make objects that stand upon other objects (e.g. mantel clocks, spice boxes, jewelry boxes, etc.)
You will be able to make 80-90% of most profiles with hollow/round pairs 4, 6, 8, and 10.
When learning to use these planes, start with simple, single curves. Make a 60 degree cove or Ovolo. Then make 90 degree arcs. After this, make a cove and Ovolo separated by a fillet. Finally, make an ogee.
Matt
Matt
Thanks for doing this. Haven’t started using molding planes. But my first hurdle is how do you sharpen these ?
Thanks
rcjennings,
Sharpening profiled cutting edges prevents many people from including this type of tool in their work. It is intimidating.
Learn to sharpen a chisel free-hand. If you conclude that you like using a jig, then that’s great. Just start here.
Learn to sharpen a mid-swept, mid-width carving gouge. Learn to rock the a tool across a stone with an edge that doesn’t have to match a pre-determined profile (the plane’s sole). You’ll also use a slip stone here.
If you can sharpen a carving gouge, then you can sharpen moulding plane iron. Start with a simple plane that has a single, shallow curve (e.g. hollow/round, Ovolo)
Once you have sharpened a plane, maintaining that cutting edge is very straight-forward. This is why I send my planes already sharpened.
Matt
I will vouch. The vintage planes I’ve bought to restore are mostly waiting for me to take action. The planes I bought from Matt are (nearly) as sharp as when he sent them. (I.e., maintaining their sharpness isn’t much effort).
How do you feel about using exotic or highly figured woods when making planes? Have you ever used Osage-orange?
Eric B,
I have only made planes out of cherry and beech.
I often get asked about making planes out of harder woods. Why? We have thousands of examples of beech planes that survived multiple working generations. The durability of beech is proven.
Matt
I would save the Osage for boxing. Not quite boxwood, but still a good tough wood, especially if it has some age to it.
Morning
I’m interested in making my own planes and would like to find some quality resources for information and materials.
Specifically
Specs for side rabbet, snipes bill, etc
Iron blanks
Thanks
Ben,
I make iron blanks for myself. They are not an item that I actively try to sell. I don’t enjoy metal work.
Iron blanks are being offered by Red Rose Reproductions along with floats and a couple other things. I have not held or used any of these so I cannot officially recommend them, but I imagine that they’ll be great.
Dimensions for the planes that you referenced will certainly be included in my book. Until then, I have several photos on my instagram feed (@msbickford) of the escapement for the rabbet planes that I make. Get it close with those or change it drastically to please your eyes. There are a lot of viable solutions.
Note: I’m hesitant to offer specific dimensions for wedge width, etc. because they are dependent upon the tang’s width and I don’t know your tang’s width.
Matt
Hi Matt, my question is a general one so feel free to tell me to ask again next week. I’ve gently moved into an apartment in Chicago but would like to make a couple pieces of furniture. Unfortunately, the best place for a workbench is the balcony, which will probably restrict me to warm weather. I’m hoping to keep all of my tools inside, but was wondering whether wood storage and some finishes can stay outdoors under cover. Any other advice for this situation?
Ben Garber,
This is definitely not my area of expertise. I keep wood outside with the ends/sides wrapped in tyvex and covered in a tarp. This wood is not going to be used any time soon, however. It will be acclimating in my shop for a long while first. I can’t imagine that there are many/any finishes that will survive a Chicago winter outside.
My advice will be to not let this deter you. You have an itch to build so intend to scratch it. You’ll figure it out. Incredible things have been made in places deemed unfit.
Matt
Hey Ben,
Some, not-water based, finishes are tolerant of freezing weather BUT remember you still need to be concerned about the cans the finish is stored in (e.g. rust) and expansion/contraction as temperatures change can mess with seals on cans. Personally if I were in your shoes I’d try to keep my selection of finishes minimal so they don’t eat up much space and keep them in a temperature controlled environment. As well I keep mine in a plastic bin/tote to mitigate any accidental spills (last thing you want to deal with in a rental). Wood I would be less concerned about so long as it is covered with a tarp and raised off the balcony surface so it doesn’t have moisture sitting directly on it from above or below, and if you have enough I’d sticker it for air-flow. Just maybe don’t keep your best stock outside.
Matt,
For those attempting to make their first wooden plane and who don’t have a planemaker’s float (or have just a single narrow one), what is the best alternative for cutting the mortise for blade and wedge? Drill, chisel, file – whatever will do the job? More likely than not, I will start with a built-up Krenov-style model but I may get ambitious. Thanks!
Jonathan,
I made 3-500 planes with three floats: push edge float, pull cheek float, push side float. You don’t need dozens (but having a few others will be ideal).
Floats allow you to work both aggressively and ultra-accurately in very confined areas. Using these tools after pre-drilling the holes will set you up for success.
I’m sure that a single plane can be made with the tools you’ve listed, but I don’t think the process will inspire you to make many more because you’ll be fighting your tooling.
Matt
I went with a french style for my first attempts at moulding planes. These use a side cut wedge which is much easier to make. For a basic bench plane, the tools I would consider adding include a blunt chisel (same function as a float but cheaper/eaiser to find), and a hacksaw blade for handling the cheek cuts for teh wedge (not really the right tool, but again cheap and easy to find)
Can you say more about the contents of the book you are working on now? And, thanks for the 5-min tutorial you gave me at Handworks!
I want to expand on Brad’s question. What’s the estimated time of when the book might be released?
Dean,
I am in the early stages of writing the book. Please expect a year, not two.
Matt
Brad,
There are a lot of technicalities in the planes that I make. The planes consist of just two pieces of wood and a piece of steel, but there is a lot that needs to be right for the planes to work correctly. A few seemingly minor things will turn success into a fighting failure.
My new book will walk you through the process of making the planes that I offer by first defining what is correct regarding the most minute details. I will then show you how to replicate these.
While the book will specify the process of making planes, it will necessarily teach you how to tune an antique. The technology, after all, is the same.
Matt
Hi Matt, I’m new to woodworking and have never used moulding planes (yet). Big fan of your work and would like to have all your planes if I could. I have read and heard many times about hollows and rounds as a great idea for a beginner because they are very versatile. Speaking out of ignorance, isn’t more efficient to have a moulding plane with the profile needed?
I’m doing everything with hand tools (so far) and working with only hollows and rounds could make the process even slower wouldn’t it?
To illustrate an example of what I mean, I own a Veritas Combination plane and even though is great (replaces many different planes), Today, I would rather have the Lie-Nielsen tongue & groove planes than changing from the plow to the tongue cutter, to rabbet, to beating and viceversa. I see the value on the grab N’ go idea.
With that said, here are two questions:
1) Are there different sizes of Ogee moulding planes i.e. 1/4”, 1/2”, 3/4” ?
2) What would be the sizes of moulding planes you could recommend to start with? (For small to medium size furniture/boxes)
Your moulding planes are (sincerely) the best and most beautiful ones anyone could own. I am looking forward to your new book!
Thank you, Edward
Edward,
If you have a dedicated plane to make a 3/8″ Ovolo, then it would be faster to use THAT dedicated plane to make THAT profile than it would be to use a rabbet plane and hollow, yes. If, however, you want to change the dimensions of that Ovolo by decreasing the arc or increasing the size of the surrounding fillets, then you’ll need a new plane. You also wouldn’t be able to use that dedicated plane to make its profile in a larger, more complex profile because you’d loose the reference surfaces for the fence and depth stop.
Hollows and rounds afford you, the user, the idea of infinity. Dozens of profiles can be made with a single pair. Every pair you add exponentially increases your options. Hollows and rounds allow you to make what you want, limited much less by what you have.
Onto your questions
1) There are limitless numbers of ogee planes. There are so many different ogees that could be considered a 3/4″ ogee that I do not personally offer a specific line. It’s all custom work. Some people may want two equal 60 degree arcs, or two 90 degree arcs. Some will want the convex arc larger than the concave or vice versa. Hollows and rounds afford me the ability to offer this custom work at a price comparable to my standard offerings because I don’t have to make custom cutters for a one-off. I just use hollows and rounds
2) Generically speaking, 4s and 6s would be a good place to start for adorning boxes
I thank you for the kind compliments,
Matt
I bought an old 1” rabbet plane at a flea market. Strangely enough, it had the iron but no wedge. Not a problem. The sole is 1 1/2 degrees out of square. I was going to take a jointer to it and square it up. Then, I remembered it’s Bickford Saturday and figured I’d run it by you to make sure that I’m not missing some reason for the angle. I assumed it was caused by use and uneven wear. Thoughts?
RonG,
It’s probably out of square due to wear or tuning. I’d spend the few minutes it takes to make it square.
Make the wedge first. You will want to square the bed with iron/wedge set into the plane body and with the iron retracted into the plane’s body. Setting the wedge will slightly distort the plane. You want to flatten the sole with the distortion included.
All of that being said, my rabbet plane on my bench is probably out of square. I don’t often check it after tuning. Slight imperfections like that won’t affect performance.
Matt
Hi Matt,
I just recently found out about your book and planes and I’m thrilled you are doing an Open Wire! I haven’t had a chance to pick up your book yet so please forgive me if this info is already stated in there.
Is it possible to make curved Moulding pieces with hollows and rounds planes? Like the moulding commonly found at the top of a high boy or a curved doorway.
Is there a difference in technique when making curved mouldings?
Thank you,
Madeline
Madeline,
Moulding planes may be used to make straight lengths of moulding. Curved moulding are carved or scraped. When I have made curved moulding, I followed the same process I detail in my book. I just use different tools. I use a v-gouge/router plane instead of a rabbet plane and carving gouges instead of moulding planes.
I have demonstrated this process while making a gooseneck, piecrust tea table, and a few other examples on my instagram feed (@msbickford) or when I was doing my blog.
I probably should have included an appendix addressing this subject. I didn’t feel it was appropriate for me, a hobbyist, to write that. Someday when we make a revised addition…
Matt
i have a 6″ grinder and am planning to grind a set of iron blanks to make a set of 4 & 8 hollows and rounds. What type of grinding wheel do you recommend for roughing out the shape?
Jesse,
I use a 1/8″ grinding wheel. Toolsforworkingwood.com offers this on their website with 1/2″ arbor. The wheel looks like a cut-off wheel, but it is not. It is a 24-grit wheel. It sounds aggressive, but it is right.
Matt
https://toolsforworkingwood.com/store/item/NO-EXTRAG.XX/Norton+Extra-Thin+Grinding+Wheels
Do you make your own irons for your molding planes? If so how do you get the taper from cutting edge to top?
Patrick,
I make the irons that I use from O1 bar stock. I add the taper on a vertical mill.
Matt
I have a project that requires planing tongues and grooves into 2 inch thick boards, which I want to make 5/8 wide. I am thinking of connecting 2 rabbet planes with rods to make a sort of adjustable sash plane thing. Any thoughts?
Jim,
I always disappoint two groups of woodworkers:
1) antique collectors
2) handtool-only woodworkers
I would personally do this on a table saw. (See? You’re disappointed.)
If I had to make the tongue by hand, then I’d make two separate rabbets. You can be as accurate with a rabbet plane as you are with gauge lines.
Matt
Haha you do know your audience! Thank you. Chris said the same thing.
Hope your finding this Open-Wire fun and the questions being asked help with the writing of your book. Do you think you might have another Open-Wire in the future and maybe after the book have some classes?
Eric,
When I was writing my book and Chris was editing it, Chris would usually delete the first 5 paragraphs saying that I’m too long-winded. He correctly pointed out that my 6th paragraph said all of the first five, but succinctly. Please consider skipping ahead a few paragraphs here if you’re looking for your specific answers.
When I started pursuing customers, I had a strategy for using the planes that worked for me. I understood what I was doing and I was able replicate the mouldings that I made accurately and efficiently.
When I stood in front of potential customers for the first time, I realized that I wasn’t able to articulate my process as well as I understood it.
My first book is a product of many people willing to let me fumble over my words and sentences as I described going from A to Z with the tools that I made. These people, you, asked good questions, told me what didn’t make sense, and told me what did.
Mouldings in Practice was the result. It makes sense to most.
Talking to people forces us to be understandable in words and in print. This is necessary for a good book. Lost Art Press books are good books. They’re good books because they’re written by people who genuinely like talking about their subject matter and, as a result, have talked about that subject matter a lot.
I am enjoying this Open-Wire because I like talking about this subject and it lets me know where you are and what questions you have. It’s necessary for me.
Classes are also necessary for me and for my writing. I have a few classes scheduled (CVSW in a couple weeks and Sam Beauford next summer) and will continue to teach. I do intentionally limit my classes because I consider myself a maker vs. a teacher, my back log, the type of school that fits well with my classes, and my desire to stay home and in my shop (I don’t even like crossing the street to get my mail).
I’m always available for questions through emails so long as you’re available for long-winded responses.
Matt
Thank you. Excellent answer. I like long winded.
I’m always wondering how traditional joiners were able to make hundreds of feet of complex moulding for rooms that matched up. Is there some trick for achieving perfect tesselation on profiles over multiple pieces of stock? Thanks. Love your book.
Randall,
Architectural mouldings (i.e. 100s of feet) were likely made with dedicated planes. Uniformity is greatly increased with these planes. Additionally, the idea of perfection 200 years ago was probably not equal to what Williams and Hussey’s idea presently is.
If it looks right, then it’s perfect, right?
When I measured the various pieces for my book, it was necessary for me to take the measurements from a single point along the length. These profiles changed over the course of the seven feet that wrapped around the case. The back-left of the profile along the case was not equal to the back-right. These profiles were likely made with hollows/rounds due to the variation, not imperfection.
The profiles changed, but you’d never notice it unless you were measuring them with calipers. The sellers of the pieces never noticed the changes, nor will the buyers. The changes aren’t imperfections, they just worked to different standards.
Two suggestions for uniformity:
1) keep the fillets/flats uniform. Nobody will notice if an arc increases from 60 degrees to 75 degrees over the course of 7 feet nor will they notice if the profile corkscrews several degrees. A fillet that decreases from 1/4″ to 1/16″ will be visible.
2) The initial rabbets (see my book) largely define the final product. Start with the same rabbets for all of your profiles and you’ll get uniform results that will be considered perfect, so long as you are measuring with calipers.
Matt
My background is more in construction, mostly in building renovation, rather than dedicated woodworking, and I am reminded here of a thing a boss used to say to me and my similar statement to guys who worked for and with me over the years.
When somebody was being too finicky with a detail on a building, maybe piece of trim up on the ceiling or a drywall corner down by the floor that wasn’t super crucial, my boss used to admonish them, “Step away from the piano!” Essentially, your building a house, not a piece of fine furniture.
My less creative (but possibly more understandable) version of this became “If it has to look good from six inches, it has to look good from six inches. If it has to look good from six feet, it only has to look good from six feet.”
Basically, clients (well, MOST clients) don’t want to pay you for the extra time to achieve perfection on something that almost no one will ever notice, but if it’s something they’re gonna see up close (or touch) regularly, you have to make it just right.
Well said, Shane
-Matt
Hi Matt,
So I’m a power tool user who is venturing into hand tools. I love them cause I tend not to have to sand what ive planed; however, due to a spinal injury its hard at times and this is why I lean on the electric gods in the woodshop.
That being said, my 2-part (rule breaker I know and am sorry) question is do you find that the moulding planes give a higher level of finish than a table router and if so, would it be beneficial for someone in my situation to buy/make a moulding plane that matches the profile of router bit being used to run a final pass on whatever piece of wood I’m working on?
I have other questions but I’m probably gonna have to buy the book as I think many would be answered in it.
Thank you from sunny Arizona!
Ryan,
The planes will leave a superior surface that is ready for finish IF the wood is chosen correctly.
When I use a router/sandpaper, I just make sure that I have a piece of wood that is long enough for my need. When I use a hand plane, I pay close attention to the grain direction. Moulding planes do not work well against the grain.
In theory, cleaning up a routed profile with a plane that has the same profile will work great. In practice, the two profiles will never be the same. I imagine that there will always be inconsistencies that prevent the plane from working correctly.
From rainy Connecticut,
Matt
Hi Matt –
So many questions already. That’s great. I’ve tried skimming them hoping not to duplicate questions, but I may have missed them. I have two. Here goes.
I have a 12 inch cherry log (18 inches long) that’s been drying in my garage for two years and it’s time to section it. I don’t have/use power tools, so I’ll be using wedges, a sledge hammer, a froe and a mallet. I plan to rive the log, but I’m uncertain how to get the maximum amount of “rift-sawn” and “quarter-sawn” (though it won’t be sawn) wood out of this log. I do want to try to build some hollows and rounds from this wood….but probably other stuff too. But I want to take advantage of have some free rift-sawn and quarter-sawn cherry. Do you have any advice?
My second question is embarrassingly simple. Are hollows and rounds oriented barkside down or barkside up?
Thanks! I look forward to reading through these questions and your replies more carefully…and appreciate your consideration.
Dear David,
Joshua Farnsworth shares a great video of Elia Bizzari splitting a cherry log for Windsor chair parts. You can watch it here: https://woodandshop.com/how-to-split-a-log-for-amazing-lumber/
David,
1) I am not the best person to answer questions regarding splitting/riving wood, especially if you’re looking to maximize the yield.
2) Barkside down is the correct orientation.
Thanks for reading,
Matt
What was the toughest part of becoming a hand plane maker and how long did it take before you felt “successful” with your business?
Josiah,
First reaction here…
The hardest part of becoming a professional was immediately knowing what mistakes could be fixed, how to fix it, and what needs to be abandoned. There were more errors in the beginning. I spent a lot of time trying to fix many that weren’t worth the effort. It was all just time lost.
Pricing everything in terms of rabbet planes was also a big hurdle to get over: “A new dishwasher isn’t worth 5 rabbet planes.”
Regarding “successful”: I was fortunate to have a backlog since the very beginning. Larry Williams and Don McConnell had created a market that I was able to slide into. That being said, I was shocked when I survived a year. I was again surprised after I survived 2, 5, and 10. It’s been 13.5 years of doing this full-time and supporting my family on this single income. At some point it turned into a success, but I’m still relieved when each new order comes in.
Matt
Hi Matt, looking forward to your book on plane making.
Now that LN is not making plane maker floats , can you recommend a source for these type of files ?
Hi Adrian, I’m new to woodworking, I’ve never made a plane, but I do know that Red Rose Reproductions got the “blessing” from LN to continue manufacturing their floats. This is directly from their website “ Our floats are based on designs that had been made by Lie-Nielsen Toolworks, which were in turn based on floats designed by Old Street Tool. Both have been supportive of our efforts to reintroduce these tools.
Our floats are similar to the no longer made Lie-Nielsen floats with a couple of significant differences. First, we opted to make ours of O-1 tool steel instead of S-7 tool steel. O-1 is easier to sharpen with a file and leaves a cleaner cut. The other difference is that the blade on our floats extends the entire length of the handle. This is a more robust design and gives better balance to the tool. Handles are maple held in place with brass rivets.” hope this helps.
Adrian,
Dan of Red Rose Reproductions is offering floats. I haven’t held or used them, so I can’t officially recommend them. I’d imagine they’re as good as the LN floats.
Matt
Adrian,
I bought two of the Red Rose Reproductions cheek floats from his first production run, and I feel comfortable recommending them.
I also know someone with both RRR & LN floats, and he says that they’re comparable even though he might give a slight edge to the LN
Liogier from france makes them as well. You can buy direct from the manufacturer and pay shipping and no tax/duty so long as its under 800$. Ive used their mortise floats and rasps to produce gun stocks and saw handles, all top notch. As Mr. schwarz has pointed out, use a short haired bristle brush to clean them instead of a metal brush, air compressor helps a lot too.
https://www.liogier-france.fr/
Any thoughts on elegance removing a screw in white oak that broke off 1” beneath the surface?
Jonah,
Unfortunately, I don’t. I have half of screw in my tibia, so my surgeon also won’t be able to help.
If it were me and that screw had to come out with what’s presently in my shop, then I’d likely drill it out with an end mill.
Matt
Get a “screw extractor”-widely available ( google it)
Works great. And could easily make your own once you see what it looks like.
Hi Matt and thank you for offering your time and knowledge, much appreciated. I have a beech billet ready for me to make a traditional jack plane, as well as a Red Rose iron and the wedge stock. Other than standard tools, as far as specialty plane making tools go, I have three floats (Liogier bed and side, and Mazzaglia edge, all push). Is there a good book or video you can recommend that show the process of opening the mortise, shaping the cheeks, the bed, abutment, wear, cheek, etc. in any detail? Any recommendation for how and what on to practice before cutting into the beautiful beech stock? Thanks in advance!
Nick,
I haven’t seen anything out there about making the bed/escapement for a top escapement plane. There is much carry-over between making side escapement planes vs. top, but there’s a lot different, too.
I think that Steve Voigt has put several photos of the process on his page (I think).
My recommendation is to acquire an antique top escapement plane that works and copy it in every detail.
If you’re looking to practice, try cherry.
Matt
Dear Matt,
I am sure you will cover this question in your forthcoming book on planemaking, but perhaps a cursory answer here is possible. I have a few antique wooden rabbet planes and would like to put boxing into one of them; on a beaten up one, I attempted a boxing with the resoling to make a sliding dovetail plane that functions but has a face only a mother could love.
How do you cut the groove for the boxing, and at what angle (if it matters)? I will most likely use persimmon for the boxing as I have ready and easy access to it from farmers.
Many thanks for taking your time and sharing you expertise here on the LAP Open Wire.
Best regards,
Nick
Nick,
I cut the groove for my boxing with two cuts on my table saw at 25 degrees with a standard rip blade (square). I do this immediately after I cut the mouth/escapement.
I also use persimmon.
Matt
Yo Matt! Thanks for inspiring me to start playing with molding planes (I usually run a Delta shaper and Wm. & Hussey molder. I know I know- Boo! Hiss!).
I’ve been getting a smattering of planes thru ebay, sight unseen and not really knowing my stuff yet, and clearly the rabbet is the keystone. You mentioned that skew rabbets are more for cutting across grain than general purpose work, but 2 blurry photos later I have 2 skews and no straight ones. What is the difference?
Cheers and thanks!
Steve
Steve,
There are advantages of the square and advantages of the skew. Any disadvantage that one configuration has will be overcome with 20 minutes of use. The first properly-tuned rabbet plane you use will be the configuration you swear by. As such, I swear by a square, 7/8″ rabbet plane.
Advantages of square:
1) the shaving is ejected onto the bench. This keeps the shaving in your peripheral vision and you can see if you’re out of square because you can see the shaving.
2) the skew does not pull the plane to starboard.
3) easier to make, sharpen, etc.
Advantages of skew:
1) leaves a slightly cleaner horizontal and vertical surface when working across the grain
If you have skewed planes and you’re able to execute with them, then you don’t need the square. One plane does it all (two rabbet planes is a luxury).
Good afternoon Matt
Thoroughly enjoyed your first book and am anxiously awaiting the second. I am working on learning to make my own hollows and rounds. I have some very nice quarter sawn persimmon. Any thoughts or concerns about making planes from it.
Thanks and have an amazing day!
krjones,
I will recommend beech (or cherry). We have thousands of examples of beech being durable enough to survive multiple working generations. None of us will use these planes as much as users of the past did. Using a harder wood will increase the difficulty of the process while not making a better plane.
Save the persimmon for a proper set of woods for your golf bag.
Matt
Good afternoon Matt
Thoroughly enjoyed your first book and am anxiously awaiting the second. I’m lucky that an antique store near me brings in a lot of pieces from Great Britain including a fair amount of molding planes at very reasonable prices. But I am working towards making my own. I have a very nice piece of quarter sawn persimmon. Any thoughts or concerns about making planes from it?
Thanks and have an awesome day!
krjones,
You posted this question twice. I previously double-posted a reply. I replied to your answer above.
Matt
Hi Matt,
No Q here, just want to say thank you very much: I bought your book and a pair of no. 6s and so far have been able to put the 90 degree cavetto from p.29 around a small table top. Amazingly rewarding. Am looking forward to your next book!
Cheers
Adrian
Adrian,
Keep up the good fight!
Thank you,
Matt
Hello Matt, thank you for hosting and your time. I very much enjoyed your book and am eagerly awaiting your next. I already have several billets and tapered blade blanks for a pair of hollows and rounds, and a 7/8” rabbet plane. I followed your advice and got the lie-Nielsen video about making moulding planes, which is a great resource. Thank you for pointing the way. My question has to do with your posts on your website about making picture frames using moulding planes to create the profiles. What a great idea. Why hadn’t I thought of that sooner? The real question is would you recommend smaller sizes of hollows and rounds for that type of work, and would a dedicated plane (like an ogee) get old fast? I love the idea of being able to make each frame unique and not have to acquire many specialty router bits for the profiles. Thanks again!
Craig
Craig,
A picture frame is a great weekend project. They’re quick and easy. Frankly, we should all be giving them as gifts instead of cutting boards.
We make the moulding for frames with a 6/10 combination in the class I teach. Any combination between 4, 6, 8, and 10 will work well. My official recommendation is the 6/10 here.
Regarding the ogee: I prefer hollows/rounds because they offer the idea of infinity. Ogee planes are fun to use. Watching the profile develop is remarkably satisfying. I wouldn’t recommend getting one unless you have a significant amount of the same profile to produce. You’ll be left justifying its use from here to eternity.
Matt
I know it’s late in the day to try for a question, but I have a complex moulding plane that I really like the profile of (kind of an ovolo with a quirk?) but it appears the plane body has shrunk just a bit over the years, offsetting the quirk too much to cut. With a tempered iron, is it generally more appropriate to try to file it to this new shape (lose about 1/8 steel) or file the side of the iron (lose about 1/32 steel) to bring it back in line, or is this just a pleasant decoration at this point? Thanks!
Chris,
I’d start with addressing the iron’s edge vs. removing 1/8″ of steel.
Matt