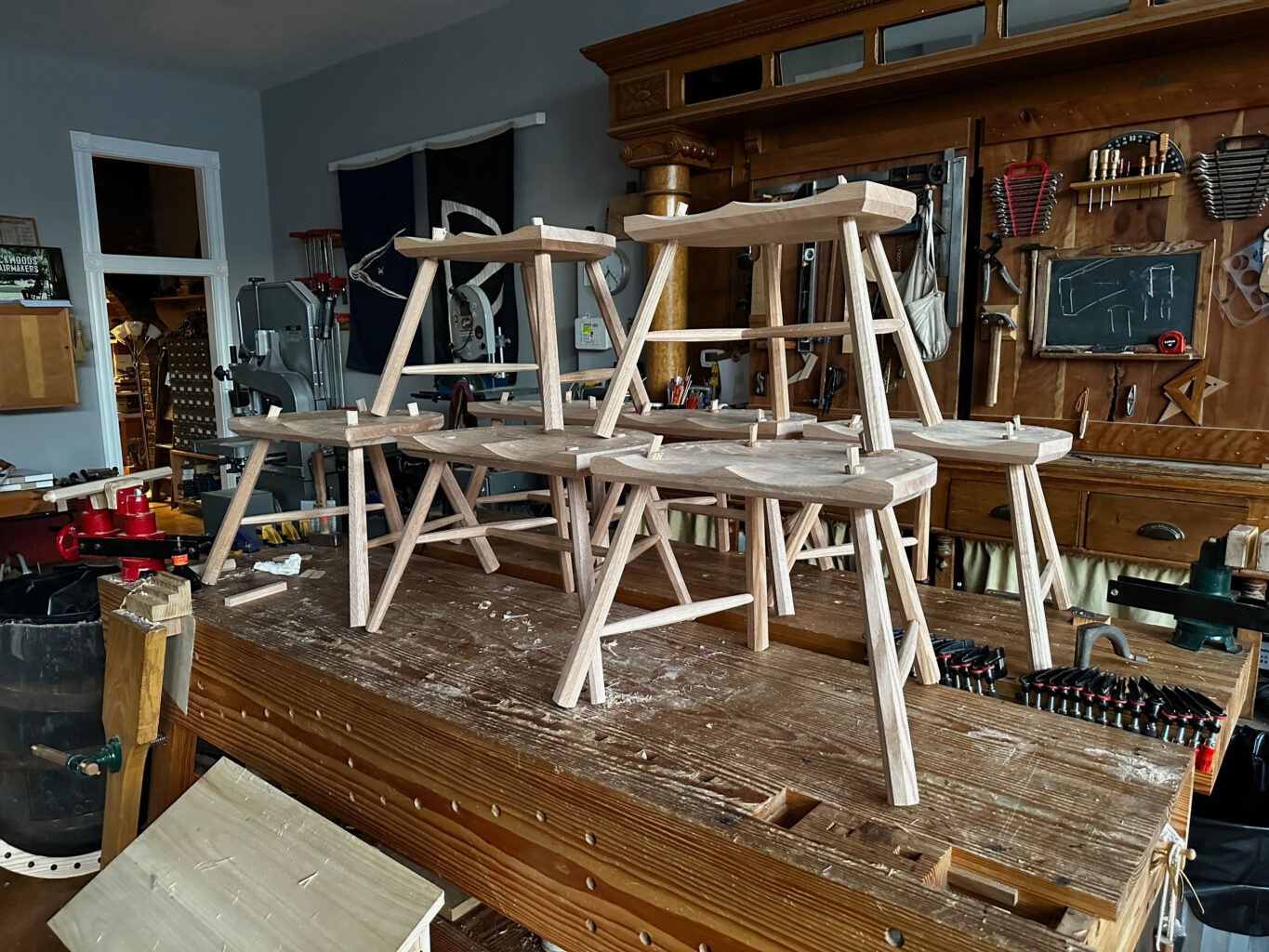
We just finished up the chair class with students selected by Chairmakers Toolbox, and we are both inspired and exhausted. Building eight stick chairs in five days with limited tools is no joke. But working with a group of chair-crazy enthusiastic young woodworkers gives me hope for the future of our craft.
So today I am happy to sit on my tukus and answer Open Wire questions. Type your question about woodworking into the comment field below. Megan and I will try our best to answer it. Apologies if our answers are brief and not surrounded by the usual pleasantries. Saturdays are a lot of typing.
So here we go.
Comments will close about 5 p.m.
— Christopher Schwarz
Hello, I have two questions if that’s ok?
1) I have a memory of you saying you were going to make a stick chair out of plywood – or maybe it was a dream. Did this ever happen and do you have any pictures?
2) Are there any uniquely Scottish chair styles you can point me in the direction of?
And whilst I’m here, thanks so much for all put on this blog. It’s been a constant source of inspiration over the past few years. I have no idea how you find the energy and time to do everything you do!
I haven’t built the plywood chair yet. The idea keeps evolving. These days I’m thinking of laying up my own plywood to make a narrow and curved arm….
There are indeed distinct Scottish chairs. The Darvel and Orkney are two of my favorites. Definitely check out “Scottish Vernacular Furniture” by Bernard Cotton.
Thank you Chris ands Fitz for graciously spending your time answering these questions for everyone. Do you have any reading suggestions or tips on becoming more acquainted with the nuance of identifying the era / style of furniture? I’m always enamored by some professional’s capability to distinguish the era / style of furniture due to a subtle detail on something seemingly insignificant in the grand scheme of things like the foot of the legs. Have a wonderful weekend from Washington state!
There’s a book titled “Field Guide to American Antique Furniture” that is a good place to start. The books that purport to help you identify all styles in the world are bunkum. There is a similar book for English furniture. One for Swedish. Danish. And etc.
And soon you have a wall of furniture books.
What was the winning bid for the Irish Chair?
$2,600
Since we put in a lower bid, I informed my wife of the winning amount. Her comment is, “GOOD! I’m glad he got what he deserved for that chair. It is BEAUTIFUL!”
For peace of mind while laminating the top of the Anarchist’s Workbench, I was thinking of using loose tenons to align the boards and prevent slippage. I don’t have any machinery for this specifically and I just thought about using a router jig for the mortises and making the tenons on the router table. I intend to laminate it about 3-4 boards at a time to be able to use more of my existing clamps. Any pointers or warnings come to mind regarding this process? Thanks!
I plan on doing the same- and I’m thinking I’ll need to be careful not putting any slip tenons near the final locations of the dog holes, but especially not near the final ends of the bench. Would suck to cut the bench top to final length and have a domino/tenon visible!
There are simpler ways to stop slippage. Sprinkle some sand or salt on the glue before you apply the clamps. Or drive some thin nails into one side and snip their heads so 1/8″ is projecting.
A router jig is the last thing I would use.
Oh yeah, the nails in particular would do the trick just fine. Thanks! Saves me a bunch of time.
Hello, Chris and Fitz!
A question about wedged mortise and tenon joint. I know that staked legs need nothing but kerf and wedge. But there’s multiple different guides how to do a wedged through tenon joint. With tapered mortise, relief holes, skewed kerfs and so on.
Are these all equally good and what’s your suggestion to do it? Does tenon size matter?
Going to use the joint in farm style table with relative big tenons (1 1/2″ x 4″)
The answer is more like a chapter of a book I’m afraid.
In square work that needs to take a beating: Yes to a tapered (slightly trumpet-shaped mortise) and relief holes at the bottom of the kerfs. In soft woods, this trumpet shape can be created by the wedging action itself with hard oak wedges (that is, no need to make the mortise trumpet-shaped as the wedges will do the job).
On angled/skewed kerfs, these are best used in wide panels where the risk of splitting the panel is minimal. The angled kerf help fill any gaps around the tenon. But there is a risk of splits.
If I were to be a fancy lad, and try to have some sort of veneered inlay or marquetry panel (or just veneer the entire inside surface) on an ATC lid panel – should I worry about veneering the outside facing face (like you normally would) based on the fact that it’s going to be painted? Would adding a veneer cause any issues with the bevel chipping on the outside?
Looking to avoid creating a pringles chip out of my lid panel but I’d love to have some interior bling as it were. How would you handle this?
The modern approach is to make the lid panel a piece of shop-made plywood and then apply the marquetry to the interior. That’s what Jameel Abraham did when he made the lid panel for the chest be built together for Popular Woodworking years ago.
The traditional approach: Just veneer one side. Use quartersawn white pine as the ground. I have seen tons of veneered tool chests that used this approach and they all survived fine. My first tool chest (a copy of Seaton’s chest) was veneered with walnut on the inside only. No problems.
Thanks Chris!
Your thoughts on beech wood for a chair please.
The European continent has been building chairs from beech for centuries. It’s no fun to rive – so look for dead straight grain. It is plenty strong and can be carved nicely for the seat and hands.
Would it be anti-anarchist (or maybe more anarchist?) to not put casters on a tool chest? I had planned to do so, but now I’m wondering if I should live with it first. I have a small shop, and I don’t really anticipate that it will move around very much. Does this lead to immediate expulsion from the guild?
People used tool chests for hundreds of years without casters. In fact, the size and unwieldy nature of a tool chest was a security feature – you needed an accomplice to steal it.
I like casters for many reasons. Even if I were in a small shop I’d have them so I could easily clean behind it.
Clean behind something in the shop? Ain’t never heard of such a thing! 🙂 🙂 🙂
If you don’t want to commit to casters you can make a little pallet out of offcuts and mount the casters to that. Then just plop the chest on top. If you love it you can mount the casters directly some other time. I did this for my toolchest and actually found it more useful due to the small size (6’x9′) of my shop
I believe in his fine woodworking article, chris’ floor chests have casters.
I built my DTC without casters, but made a little dolly with casters, custom fit for the bottom runners to sit on. Split that baby!
A couple more chest related questions for you this morning. When I made my tool chest I couldn’t decide on a floor chest (i wanted to be able to store all my handtools) and a dutch chest (the slanted lid was attractive for not being able to put stuff there) I ended up doing a dutch chest that was oversized (16x36x36) and have really really liked it so far, the main till is at a really comfortable hight and it’s got lots of room. Have you seen other examples of this?
Also curious about your thoughts on that Swedish chest with the drawers after having some time to stew on it a bit.
I can’t recall seeing any oversized Dutch chests. They were site boxes – so they had to be portable. But anything is possible.
I’ll be building a Swedish tool chest in the coming months. And then I’ll put it to work. Can’t say much more about it than it is a common form and is interesting enough to get me off my butt to make it….
What are your thoughts on Tage Frid and his books?
We love Frid. He was a pioneer of 20th century woodworkers. We have commissioned a book on his life and approach.
I’ll try to breathe while waiting for that one! I know good things take time. Thanks.
I’m wondering about your thoughts on tenon length in a frame and panel construction. The closest I can find is that you use a full length through tenon in your tool chest book. Do you do that for strength. Would a tenon of half length work also? I’m wondering because I don’t know that I can get my router plane to refine a through tenon, but I can probably get to two inches. Thanks
The rule of thumb is the tenon length needs to be 5x its thickness. Through-tenons are used for a variety of reasons – not just strength. Sometimes it is to make the assembly easy to take apart. Sometimes you do it because you are replicating old work (the case in my tool chest).
But, in general:
Tenon thickness = 1/3 of your stock thickness
Tenon length = 5x of tenon thickness
Tenon width = as wide as you can get without risking the mortised component from breaking.
Good morning and thanks for doing this! I’m building the knock-down-friendly Nicholson bench and apparently want to make things difficult on myself – rather than lapping and screwing the lower stretchers, I’d like to use a drawbored tenon. Will a bare-faced through tenon of 3/4×5 be strong enough, or should I double up that stretcher like for the AWB? One 5/8″ pin or two 3/8″? Thanks!
When you say bareface I hope you have one shoulder at least. I think it will work fine. I’d probably peg it with a couple 1/2″ pins. Though 5/8″ would be fine as well.
Ah, I wondered about the importance of shoulders. So maybe 1/2″ shoulders on each side, ~3/4″ thick, for a nominal 2×6 that’s been milled flat and square? Thanks again.
Sure!
What was your favorite thing at Handworks? Any idea if it will be held again next year?
Getting to sit down after two days of standing. (I did see Peter Galbert’s Travisher 2.0, which was cool).
I strongly suspect Benchcrafted will do it again in two years (or longer). It’s a ton of work and they do it for free.
Hi Chris. In the tool list for the staked stool you have a 5/8” spade bit extra-long. How long is extra-long and what is your favorite brand of spade bit? Thank you.
The long spades are 16″ long. The Wood Owl is OK. Irwins from a few years ago are the best.
I would like to tongue and groove some 2×8 boards by hand. However most of tongue and groove planes I have seen produce only a 1/4 inch tongue and I would like a 1/2 inch or 5/8 inch tongue. Any suggestions on how to cut these tongues?
Thanks
I’d use a dedicated plow plane for the groove. And a rabbet plane for each side of the groove. Or groove both sides and put a spline between.
Happy Saturday!
Just wondering if you’ve tested any variation of fish glue?
I have not! We bought some swim bladders to make some isinglass, but then the bladders disappeared…. Wally? Bean?
What are your thoughts on/experience with Ottosson purified boiled linseed oil? Thanks for doing this!
We haven’t had a chance to use it. But we have friends who love it. Sorry.
Any additional tips you can share on applying the linseed oil paint on you most recent Irish Chair? From what I could see in the pics it looked amazing. My experience with using linseed oil paint on chairs has been mixed. The spindles and spaces between the spindles seem to be my biggest challange where the finish tends to come out sandy.
As with all painting, the best success comes from prep. Make sure that spindle deck and sticks are nice and smooth before assembly (if you’re not already). And I guess it wouldn’t hurt to raise the grain before assembly, as it’s hard to get in there with a piece of sandpaper or whatever to knock down nibs (though I haven’t had any issues with the linseed oil paint raising the grain).
I have tiny hands – so maybe I’m able to get in between the sticks more easily to remove dust nibs? I’ve left brush strokes from overworking those small areas, though – is it possible that’s what happening? If so, try moving faster where two parts come together and let it dry. Completely. Then touch up as necessary.
Will “The American Peasant” cover the tips and tricks you guys have collected on using linseed oil paint? I think that so far all the pieces for the book have been painted with it? Looking forward to that book!
There will be a chapter on the paint.
I have a question about the dustpan you made several years ago. Would you use hardboard again? Also, have you had to replace it at all since it was made?
The hardboard has held up nicely, and I would use it again.
Do you have a link / reference for this? I need something better than the beat up metal or flimsy plastic I have in the shop now. Thanks.
https://www.popularwoodworking.com/article/dovetailed-dustpan/
Publishing question: I’ve been reading a copy of “Emma” that uses catchwords. I’d never heard of such a thing before (and probably would’ve knocked it if I had), but now that I’ve tried it I do find it smooths my reading.
Have you ever considered this sort of thing in a Lost Art Press book? I have no idea if it’s even a feature in modern book design software.
https://en.wikipedia.org/wiki/Catchword
I can’t recall seeing catchwords in a modern book, but it would be easy enough to do in In Design using footers. My understanding is that they help for a smooth transition while turning to the next page when reading aloud.
I’m planning on building an ash tabletop on a motorized sitting/standing table frame, and I wanted to inlay it with some walnut strips. What confuses me is that some inlay examples on the interwebs verge on being cross grain, particularly inlaid curves in sections where they’re at their most diagonal in relation to the main grain direction.
Are there some tricks to this, or curve angles to not exceed? I assume truly 90 degree offset inlays are constructed from cuts made perpendicular to the inlaid board for the grain directions of the two woods to match in the final piece. (Photos on Pinterest etc. tend to be too far away to say for sure.)
I am not an inlay guy. Maybe done it twice? Check out the writing of Steve Latta. He is the main guy.
Hey, good morning! I’ve been working on the Irish-y arm chair where the back stick goes through 1 inch holes in the arm. I must’ve missed the mark when drilling the arms – as they are noticeably slanted / not parallel to the seat. I tried to adjust the angle in the arm with a round rasp, but I seem to just be making the hole bigger without solving the problem.
Do you have any tricks/tips for reworking the holes in the arm?
Best,
Kieran
I’d remake the arms. It’s not a lot of wood.
Hey LAP,
Two simple questions. The first came as I opened this page this morning and noticed stretchers on the legs of the chairs being built. How do you decide when to add and how many stretchers to add? The rest of the chair looks quite similar to other chairs without stretchers. Is it principally visual balance or do those chairs differ structurally from other stick chairs in your repertoire? ( maybe not a simple question)
My original inquiry was about the modern built spoon bits. Do they fall in the same category as the older built versions and just don’t work as well as other bits for you building chairs? Did our Welsh and Irish chair building ancestors use those bits?
Thanks.
I’ve written about stretchers when/where/why in “The Stick Chair Book” and in “The Anarchist’s Design Book.” There you can get a complete explanation. The Cliffs Notes version.
Stretchers can be optional when the legs and seat are beefy. Stretchers can be necessary when the legs and seat are thin or weak.
Stretchers can make an undercarriage more durable, but they also make the chair more difficult to repair. Strut legs (no stretchers) are easy to repair. But you might have to reglue them more often.
And many times, stretchers are mostly decorative.
You have mentioned washed linseed oil in a couple of posts. What is it?
It is literally washed – boiled gently to remove protein then siphoned off the water. Purifies it and makes it not mold.
I’m hoping to try linseed paint on a few things. I hadn’t heard of washed linseed oil before either. Is this something you do, or is there a good source you use?
You can’t buy it as far as I know.
Start here: https://blackdogswoodshop.blogspot.com/2022/09/interview-with-joe-robson-part-2.html
It’s a way of distilling linseed oil to make a very nice and light oil for furniture.
That’s a very interesting read. I’ve tried (with middling luck) to find a few good sources on traditional varnish making (a project far down the list once I get enough land to grow some flax). Any chance you (or anyone really) can provide a fresh lead (beyond the text you just linked that is)? Thanks in advance to all.
Good Morning Chris,
Can you please tell us a bit about your business partner with whom you founded LAP. Maybe I’m missing the info and it’s obvious. Thanks,
Joe
John is a private person, so I like to let him speak for himself. We have been friends for about 20 years and took our first chair class together. He runs the fulfillment/accounting side of this business. I run the creative/sales side.
I’m just wondering if any writers in the LAP universe are aware of the work of Dave Engels who builds/rebuilds wagons and wheels out West in Montana? His YouTube channel is a video library of sorts but for preserving worthwhile knowledge, I’m not sure YouTube is a trustworthy repository. I suspect well written, well-made books in the hands of people who care enough to buy them will far outlast video stored in some cloud.
Oh sure. But we are not experts on that craft. We know furniture. And that’s about it. So we don’t have the skills to edit work like that. Or the audience to sell it to.
Great to see Roy Underhill teaching class in Covington this summer!
I’ve always been curious about The Woodwright’s Shop set. I assume what we saw on TV was purely a TV set? Was it a recreation of his workspace? I think we need a Mr. Rogers-esque documentary on Roy an the show…
As I recall, the early episodes were shot in a barn workshop. Then it became a set and was moved a couple times. Roy has all of it at his house now.
I remember seeing a picture of the “set” a long time ago. It sort of “ruined the magic” to see “the shop” Roy walked into at the start of the show tucked into the corner of a sound stage with no front wall and TV lights hanging overhead.
It has long since been scrubbed from the Internet, I’ve looked several times for it.
Charles Hayward once wrote about the joy of using the chairmaker’s scraper spokeshave noting chairmakers usually make their own and could have up to a dozen in various shapes/ sizes. Just wondering if you have given these a go? What chairmaker’s tool gives you joy?
It’s also called a “gunstock scraper” and is a fantastic tool for some operations. Lee Valley makes nice versions. But most of them are user-made.
I have one made by Eleanor Rose that I love. But I don’t need it much if I select my stock with care and shave it with a block plane with a tight mouth.
Not a woodworking question at all but one to satisfy curiosity–favorite fiction book(s)?
All of Kurt Vonnegut’s books and short stories. And Susanna Clarke’s “Jonathan Strange & Mr. Norrell.” And….
How wide is the cut for the wedges in the stick chair legs? Also, I am have trouble consistently cutting for the wedges with a hand saw. The band saw is even worse. Does it make sense to drill a 3/4” hole in a scrap 2/4 and run it through the table saw with the tenon in the 2/4. Help!
Hi Chris, not a question. I am over 1/2 through your new video course for the American Welch Stick Chair from the Wood Whisperer’s. It is the clearest, most educational, and fun video course I have purchased to date. I have built a C-Arm Windsor in a class with Peter Galbert but have not yet ventured into building one on my own. The American Welch is just the ticket. Thank you for this great resource.
I agree. The course is excellent – clear and effective instruction. I look forward to starting the project. Chris, your admonition that this is your way of helping us who fear to tread into the world of chair building get over the hump and DO IT is welcome. Thanks again for carrying the torch.
Thank you! Sincerely.
Good morning. I’ve built two of your Irish arm chair designs and really like them a lot.! I was thinking about building one with skinny sticks. I’m guessing 5/8”-3/4”. probably leave the posts 1”. Have you experimented with that?
I have not. Sorry. I’d dry-fit it with skinny sticks and give it a sit. That should give you your answer.
Good morning,
My question is on shipping. I know it’s not a “wood working” question so skip it if you want. How do you ship your chairs, what company, common carrier, UPS, FedEx? Any help so I don’t have to reinvent the pallet.
Thanks
Malcome
We use UPS for items less than 50 lbs and that are shippable with UPS’s girth rules.
Big stuff goes via Old Dominion, or we drop them off at a professional shipping company that packs and ships them via LTL.
Thanks that is a great help!
Hello! After spending years building things with weird curves and angles, I’m craving some straight lines. After giving a lot of thought about how I work, I’ve decided a chest might be the way to go. I’m thinking that my next project will be an ATC. But with everything I do, I’m overthinking my options. This time for the saw till.
Chris, you use a till at the bottom of your chest. Megan keeps her saws in a rack behind the chisel rack. Could either (or both) of you speak to the pros and cons of each? I know it comes down to personal preference but I’m sure there are advantages or disadvantages either way. If it matters, I don’t see myself needing a moulding plane till, though like everything I’ve ever said “no” to, that may change in the future.
thanks!
My handsaws sit in the rack. The backsaws are placed vertical between the blades of the handsaws. Advanatage: Simplicity. Disadvantage: Sometimes I have to move a backsaw to get a handsaw.
Megan’s sawtill is great. The only disadvantage is it takes 10 more minutes to make than mine.
Good morning, all. Two quick ones:
I have some 1.5” red oak off cuts with straight grain. Could I use those for the ADB staked stool legs (instead of 1 3/4”)?
Any update on how the photos from the stick chair badge submissions will be used?
Thanks as always.
Maybe? Might try them out, sit on it and add stretchers if it flexes too much.
On the merit badge project, the Anthe building has sucked up all my extra time/energy that I would dedicate to silly stuff….. It’ll happen.
The staked low stool legs are supposed to be 1.5”, the 1 3/4” was a typo. I noticed this while im working on mine.
Is that right? I can check the latest PDF from LAP if that’s the case.
Heres a link to the blog post. https://blog.lostartpress.com/2020/01/21/errata-staked-low-stool-in-the-anarchists-design-book/
How did you balance time with young kids, job, health, and still having time/energy for shop time? Curious how you and others do it – b/c I often feel like I’m failing at all of the above when trying to do it all.
Hi Brad,
When I had young kids, it was insanely difficult. Early morning. Late evenings. And I failed – a lot.
Now the kids are older and I get four hours at the bench every day. That’s the goal.
You showed it on the stick chair series and mentioned it on the Gibson chair series. What is that padded thing you use to sand the seats that aren’t flat. That thing looks handy but not sure what you call it. Also where can I find one? Thanks
Do you mean this?
https://www.autopartsandstuff.com/3m-28321-cleansandingsoftinterfacediscpad5inx12in44holes-7100009658.aspx
Or hand sanding? Then it’s a cork sanding block.
Thats the one. Thank You!
Good day Chris and Fitz! Really appreciate your generosity in answering questions. The open wire makes my weekend.
I have found myself in posession of a fair bit of turpentine. I have been experimenting with it as a substitute for mineral spirits when thinning solvent or oil-based finishes, brush cleaning, etc. So far, so good, but can it affect quality of the finish in the long term. Also happen to be addicted to the smell. Any thoughts?
Turpentine is great stuff – as long as you use gloves and appropriate PPE. It’s an irritant.
It was the traditional thinner for paint and other finishes – no long-term issues.
Hi Chris and Megan,
I was reading one of the questions above about tenon sizing.
I’m planning a bed frame and was going to make the rails and legs from 12/4 ash with the legs using draw bored tenons.
If the tenon is 1.5” wide there’s no way to make it 7.5” long
I made a mock up with 8/4 oak and no matter how much I twist on force the joint, it seems solid.
Am I missing something.
I was also planning on using the same 12/4 wood for the cross rails and doing 1/2 lap dovetails in 8:1 ratio to preserve as much meat on the tails as possible.
Is that clear.
Thank you guys so much.
These Saturday Q&A are something I really value.
Using 12/4 is not furniture making – that’s timber framing.
The guidelines I cited are for furniture-scale work. What you are doing isn’t going to apply. If the joint feels solid, you’re in good shape.
Thank you, I wanted to make sure I wasn’t jumping into this with MHUMA
I am working on a stick chair I started 25 + years ago. The seat I glued up back then out of a poplar board that came out of a 1700 era cabin. It is peppered with shallow worm holes and tracks that I think add character to the seat blank. The seat is saddled and out of 2 1/4 inch stock. The legs are out of hard maple. Should I worry about strength give the worm holes and build another blank or not.
If the worm damage is shallow, I’d use the blank. And 2-1/4″ stock is thick. Should be totally fine.
Hi Megan, Chris:
Thanks for hosting this on your Saturday, it’s much appreciated! I’m planning to make a wood tool box, with lid, and am wondering about the design/practicality of having rope handles on the ends, vs. something less obtrusive such as wood hand holds with slight relief on the underside to make it easier to hold on to. The box wouldn’t be nearly as big as the ATC but likely would be picked up/moved fairly regularly. I’m guessing you’ve seen lots of examples so you would have some insights and opinions. Thanks!
Rope handles – called beckets – are common on tool chests. My first chest had them. The lifts at the end aren’t for carrying the chest – just for lifting it so you can get your hands under the corners.
So yes, rope is good.
Comment and question: The green Irish stick chair is beautiful, I was asleep at the wheel during the first bidding. I can’t find the tenon trick where you use the LN tongue and groove plane. Please direct me. Thank you, Bob
It’s on my American Peasant blog.
https://christopherschwarz.substack.com/p/introducing-the-tongue-trick
What’s gives with the new building!? You’ve occupied it but we’ve yet to see any pics of the building’s resident mousers. Ms. Fitz intimated there would be at least two. All joking aside, a couple of cats are the best, and probably cheapest, pest control you can have. Maybe one could be named Fancy Lad…
I’ll have a post up tomorrow with an update on the building!
That was just wishful thinking. For now.
I’m building a child-size version of your staked chair from ADB. The seat height will be about 75% of the original. How would you recommend sizing the rest of the components? Scale everything by .75?, or leave some things, like the leg joinery, full size? Thanks!
I haven’t built a child’s chair. But I would probably scale the joinery as well as the components.
Hi! Thanks for answering my question about building a level floor in my uneven garage. I’ve been traveling and sick since, but I hope to be able to start that soon. On top of that floor, I’ll be using a low bench. I built one a few years ago from 2x4s, but I didn’t do a great job in the glue up. I’ve never fully flattened it, and I cut it down after I snapped a leg so it’s kinda short now. Also, one of the new legs was drilled off angle, so it’s kinda sad right now. I was thinking about building a new one out of 2x12s, and then I saw your comment a few weeks ago about your low bench being built that way. How beefy did you make your legs? I was thinking about gluing up the full 2x12s, and using 5.5 to 6 feet for the top. The rest would be for the legs. Based on measurements, my bench top should be about 18 to 20 inches high. I don’t want to snap another leg, but I’m worried it might be overkill.
Thank you for doing these Q and As!
In general, I use 8/4 straight oak for the legs to my Roman benches. My current one uses 2x material but it is wide.
Thank you!
I used to have some beautiful Vesper tools, but unfortunately they were lost to fire. It looks like he’s not going to be taking any new orders for tools for the foreseeable future. As a fan of his amazing work, have you found any alternative makers that may have similar tools available? Specifically, his double square and try squares have been the hardest to replace. I’m finding most tools available can’t really come close to the beauty and precision of Vesper’s tools. Thanks!
Double square: buy a vintage diemakers square.
Try square: There are lots of vintage ones out there that are beautiful and can be trued up.
Both Vesper and Colen Clenton have stepped back from their toolmaking. My advice for good tools is like when you encounter good wood. Buy it. It doesn’t go bad. And it will disappear so fast it will make your head spin.
Making tools at small scale is a hard life. We couldn’t afford to do it if we didn’t have other aspects of our business to help shoulder the load.
Any plans for journal #2? I know as if you all don’t have enough to do 🙂
Maybe bottle up some of your energy for us mere mortals. Thanks again for being so gracious with your time and thoughts.
Hi Chris, I do have a question today. What brand compass dividers are you using with your American Peasant cutters? I just got mine, they are great. However I tried them in my Lee Valley dividers (that say “France” on them) and I would not be able to use them to carve a tight radius. What do you use?
Thanks, Frank
I use a vintage Starrett. There are lots of vintage compasses that have a removable point, and that’s what allows you to do the tight radii.
I’m going to build an AWB and I had a couple of questions about vice chops and bench dogs. You’ve mentioned you’re own preference for hard maple, and I’ve seen a few others who’ve made similar benches state a preference hard woods, if for no other part than the chop. Are the dimensions for the chop given in AWB designed considering making it from yellow pine, would you consider thinning it down at all if using hardwood? Or am I overthinking it a touch?
On bench dogs, I’ve decided I want a wagon vice, and that I will go with square dogs. I’ve used a Nicholson style bench for a few years now, made from Doug Fir, and have been unhappy with how my holdfasts have wallowed out some of the more commonly used dog holes. Would you recommend making the dogs and dog strip from hardwood, or will the added thickness of the French style bench help resist that better?
On the chop, mine is maple and very thick (as per the dimensions in the book). A 2″-thick chop (in any species) doesn’t really do the trick in my experience. So make it thick. Yellow pine, maple or whatever will be fine.
On the wagon vise question, the dog strip can be Doug fir or yellow pine and be fine. The wear on these is nothing like a holdfast hole, which is abused horribly. But if you have the maple…. I’d use that.
Any familiarity with the long-term dimensional stability of Butternut? Wondering if it would be a suitable wood to make a set of winding sticks & square from. Thanks a bunch!
Quartersawn butternut would be fine. Flat-sawn, not so much.
Long time lurker first time commenter. I have two questions:
1) I recall that Megan was writing a book on Dutch tool chests to be released sometime this year. Is that still on target?
2) Have you ever considered writing a book on vernacular style beds?
Megan is working on it (still). Our new HQ building has sucked up all our time and energy. We are both behind on our writing projects.
I love vernacular beds. But I also know that beds are a hard sell in the woodworking publishing world. Every house can squeeze in a few more chairs or boxes. But beds? One and done.
Any chance there will be another run of brass Warrington hammers?
Not this year. Maybe next year.
I hope you don’t get tired of hearing out thanks. Thanks for doing this.
What is/was the traditional way to flatten a water stone before those fancy diamond plates came along? And before those fancy concrete blocks came along?
Rub the stones against one another. Or a cinderblock.
Hi, will it be possible to buy from you guys a set of wood to make a stick chair, I don’t have a shop, and I live in Miami which is very challenged I wood availability. Like the set you prepare for the classes. I don’t think I’ll be the only one interested. And I’ll promise I’ll will never send it back. (Period)
I wish we had the time to do stuff like this. It takes me five full days of work to purchase and process all the stock for six chairs for a class. In fact, I don’t think I could find enough quality lumber in our area to do this even semi-regularly. I struggle many times to find enough wood for one class and end up visiting two lumberyards – one of which is an hour away.
Perhaps readers here might suggest a woodworker who does stuff like this. I know there are people who supply Windsor kits.
Great seeing you guys at Handworks this year. Just finished Euclid’s door…a great book. The last project in the book is extremely similar to the wooden crucible square / miter you sell on your site. Just curious is there a connection with the book or just councidence?
It’s a common tool, so it’s not surprising that we would both focus on it. Ours is made with lasers. Theirs is made traditionally
Chris, I will be traveling in Ireland next week, mainly in the northern half of the island. Do you have any suggestions for seeing stick chairs or other woodworking craft sites?
Not off the top of my head. A search through Claudia Kinmouth’s book might help.
https://blog.lostartpress.com/2021/03/07/claudia-kinmonth-maverick-furniture-scholar/
Finally have the Veritas tenon cutter working. FYI Veritas sells rare earth magnet. I use the 1/4″ size to place in my plugs for the tenon cutter. I label different sizes with a sharpie. To remove use a long screw or a canted 1/4″ bit to wedge out.
Hi Chris. I read sharpen this, what plane blade bevels do you use (or would you use) for bevel up planes?
I use 35°, just like I do with bevel-down planes. I am simple in the head.