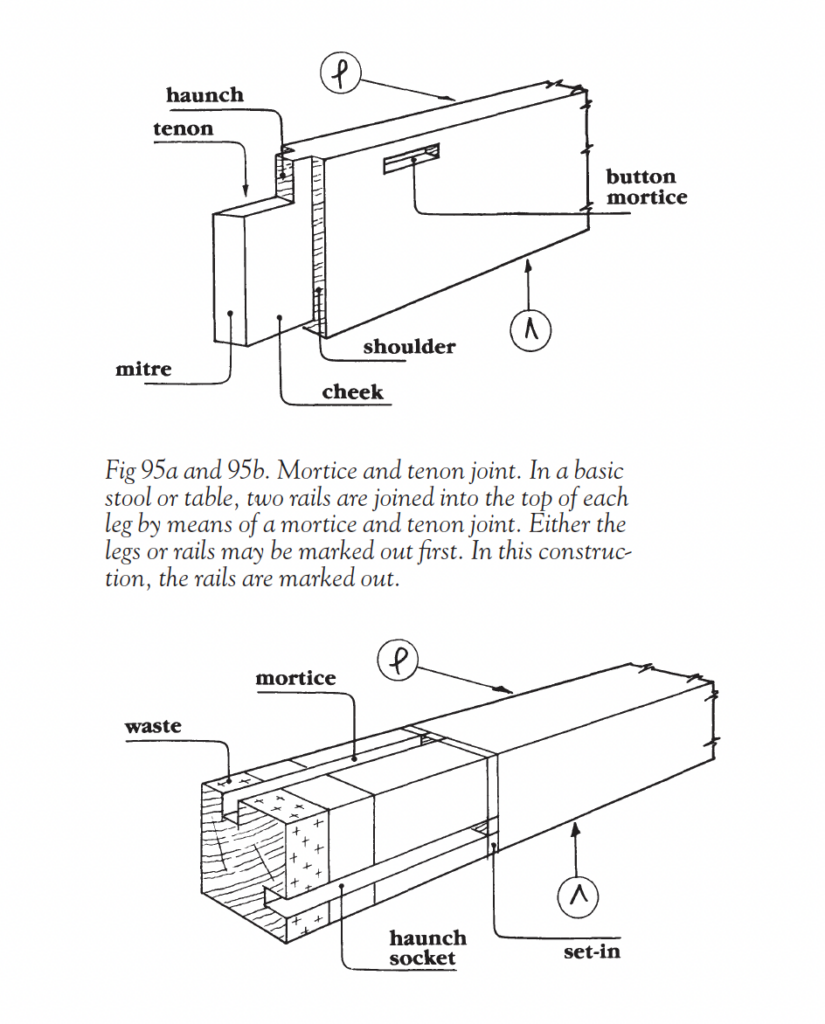
The following is excerpted from “The Essential Woodworker,” by Robert Wearing. In our opinion, “The Essential Woodworker” is one of the best books on hand-tool usage written in the post-Charles Hayward era. Wearing was classically trained in England as a woodworker and embraced both power and hand tools in his shop and in his teaching.
He begins with a table. As you read the chapter on building a table, Wearing connects the dots for the hand-tool user by showing how all the tools are used in concert to produce accurate work. It’s not just about sawing a tenon or planing an edge. Instead, it is about how to gather these skills and apply them to building furniture – tables, doors, carcases, dovetailed drawers, plinths, etc.
The book is filled with more than 500 hand-drawn illustrations by Wearing that explain every operation in a hand-tool shop. His illustrations are properly drafted, drawn in perspective and masterfully clear.
The accurate sawing of tenons (Fig 119) is a vital skill. They should be sawn with confidence and should fit from the saw. To saw clear of the lines, for safety, is not recommended since whittling an overthick tenon to size is both more difficult and less accurate than sawing correctly in the first place. A 250mm (10in.) tenon or backsaw is the most commonly used for this purpose. Frame saws are used in Europe and by some workers in the USA, but they have never been popular in Britain since the manufacture of good-quality backsaws, and beginners usually find them rather clumsy.
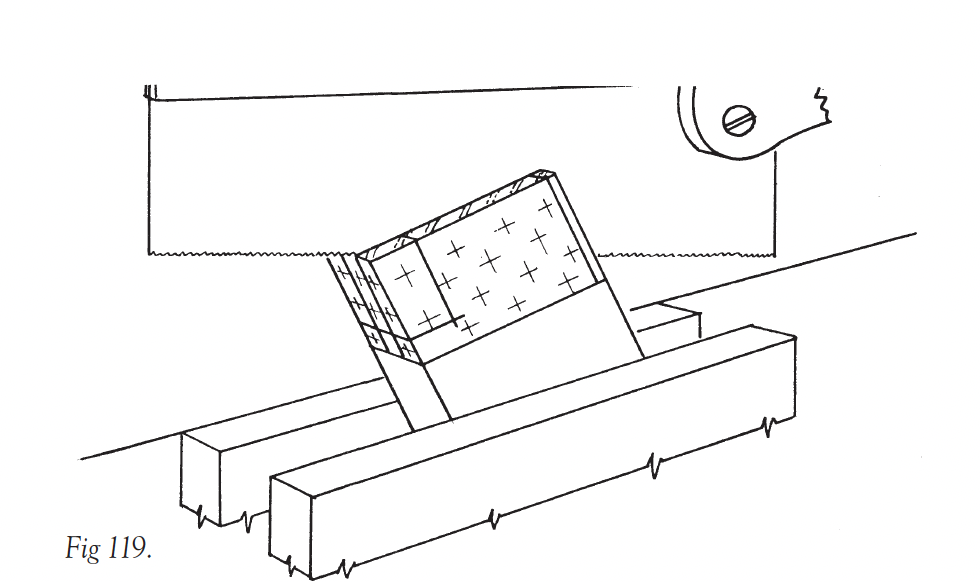
Before starting, check over the names of the parts on Fig 95 [top] and shade in the waste. While there is little chance of throwing away the wrong piece, it is essential that the sawdust should be removed from the waste and not from the tenon. That is, the ‘kerf’ (the sawcut) should be in the waste and just up to the line. Beginners using the thick pencil aid in Fig 105 [see bottom of post] should saw away one pencil line and leave the other intact. The technique is not difficult if the following guidelines are followed: do not saw down two gauge lines at a time; do not saw to a line which is out of sight. (A modification to the saw is described in Appendix B.)
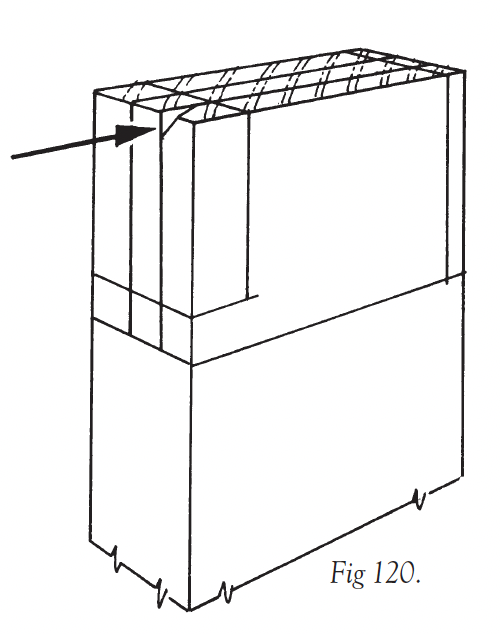
Start sawing always at the farther corner not the nearer one. Beginners may find it useful to chisel a triangular nick there to start the saw accurately (Fig 120). With the rail held vertically in the vice, start to saw at that far corner, slowly lowering the handle until a slot is cut about 3mm (1/8in.) deep (Fig 121). Now tilt the workpiece (Fig 122) and, keeping the saw in the slot, saw from corner to corner. Then turn the work round, or stand on the other side, and saw again from corner to corner, leaving an uncut triangle in the centre (Fig 123). Now grip the work vertically and, running down the two existing sawcuts, remove this last triangle, sawing down to the knife line, but no farther. Keep the saw horizontal (Fig 124).
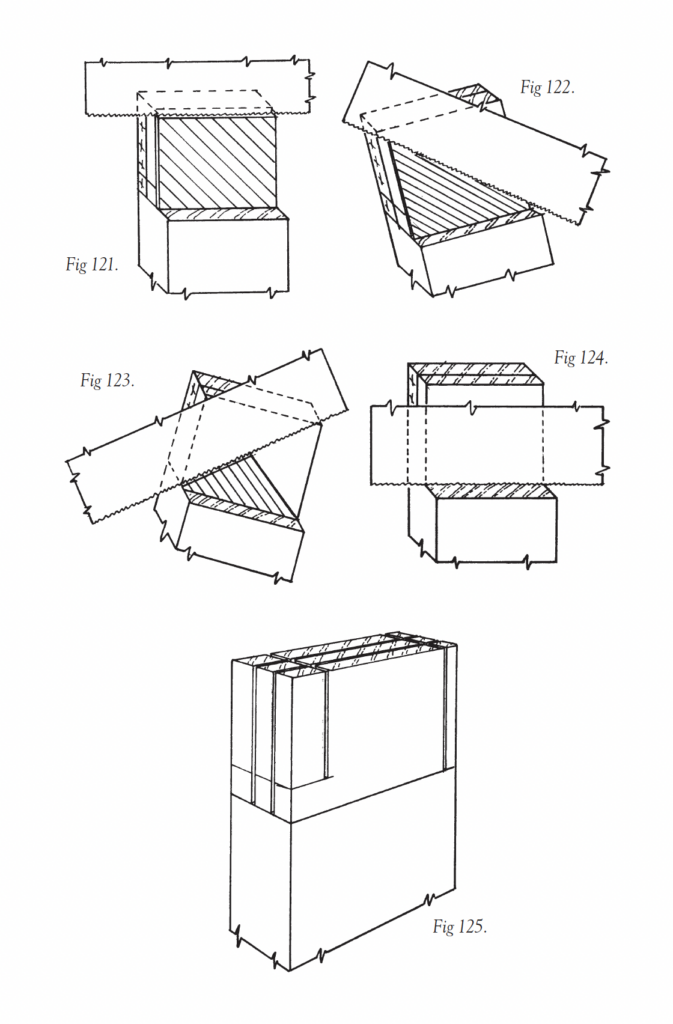
If there is a set-in or haunch, saw this next. Repeat these stages on all the other tenons (Fig 125). The haunch may be sawn right off now or later.
Sawing the shoulder is most important as this is the piece left exposed. Except on wide rails, which may be planed, the shoulder should go up from the saw.
Cramp to the bench, deepen the knife cut and chisel a shallow groove (Fig 126). Lay a very sharp saw in the groove and draw it back a few times to make a kerf, then saw off the cheek. Take the greatest care not to saw into the tenon (Fig 127), which would then be severely weakened. Should the waste not fall off, the cheek has probably been sawn with an arc-like motion, leaving some waste in the centre (Fig 128). Do not saw the shoulder deeper. Prise off the waste with a chisel, then gently and carefully pare away the obstruction. Saw off the haunch if not sawn previously.

Saw off the set-in with a little to spare, and trim this back to the knife line with a chisel only just wider than the tenon size. This avoids damage to the corner of the shoulder. Finally saw the mitre (Fig 129). The tenons should be lettered or numbered to identify them with their mortices.
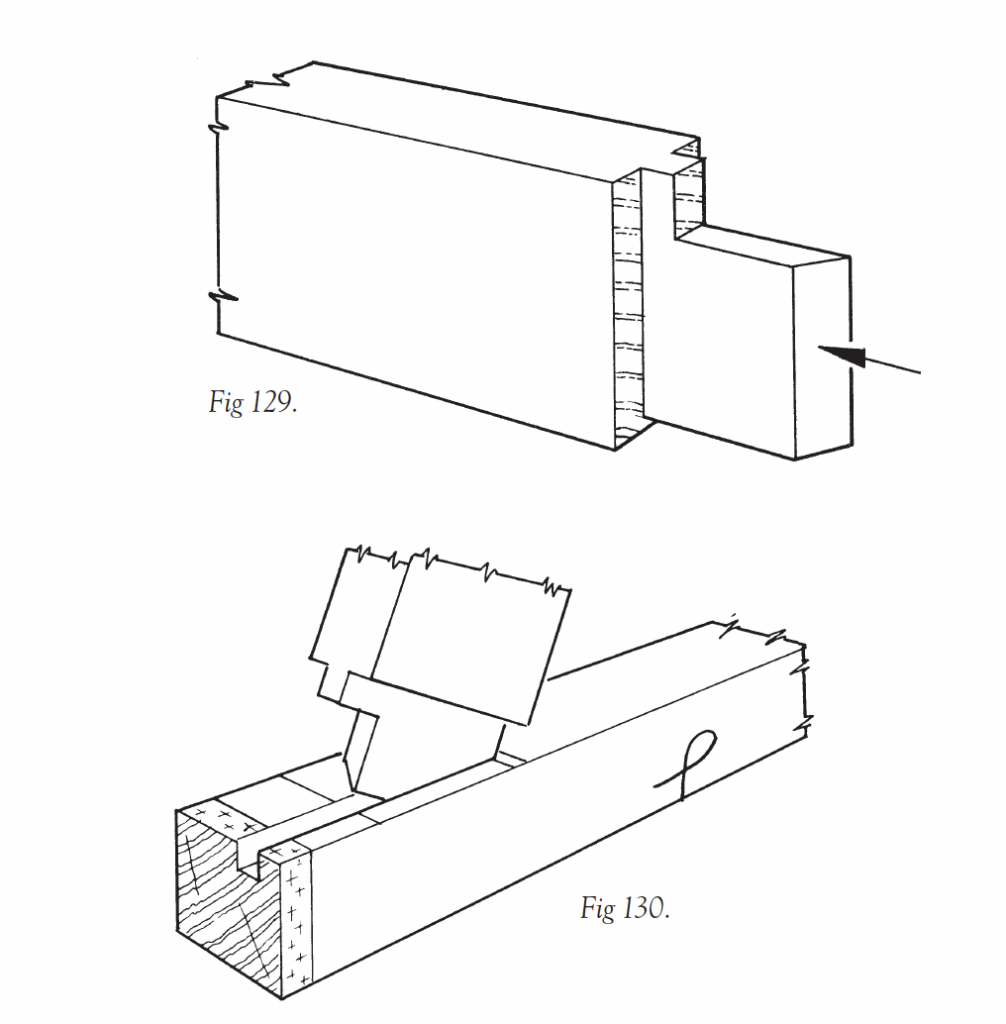
Make a preliminary fitting of the joints. The tenon may be too wide or too thick. Check for the latter by inserting it diagonally into the mortice (Fig 130). A tenon may be wrongly thought to be too thick when in fact it is too wide. It may have been sawn too wide or the mortice may have been chopped tapered (Fig 131), in which case trim it square. The most accurate way to correct an overthick tenon is to use a router plane, to the sole of which has been screwed an offcut of rail material (Fig 132).
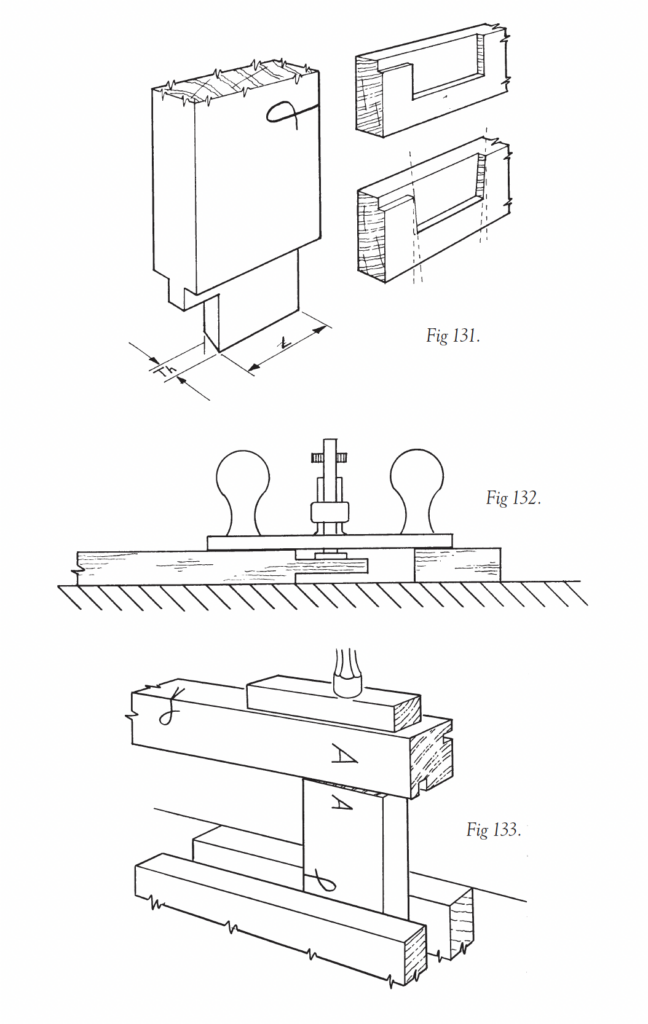
Having checked that the tenon will enter the mortice, grip the rail in the vice and tap on the mortised member using a woodblock and hammer (Fig 133). The hammer face is small and makes it a more precise tool than the mallet. Check every joint in this way. If the shoulder does not close, either the tenon is too long or the haunch is too long, and either of these problems can easily be corrected. But a badly sawn shoulder can only be corrected by re-squaring and taking back with a shoulder plane.
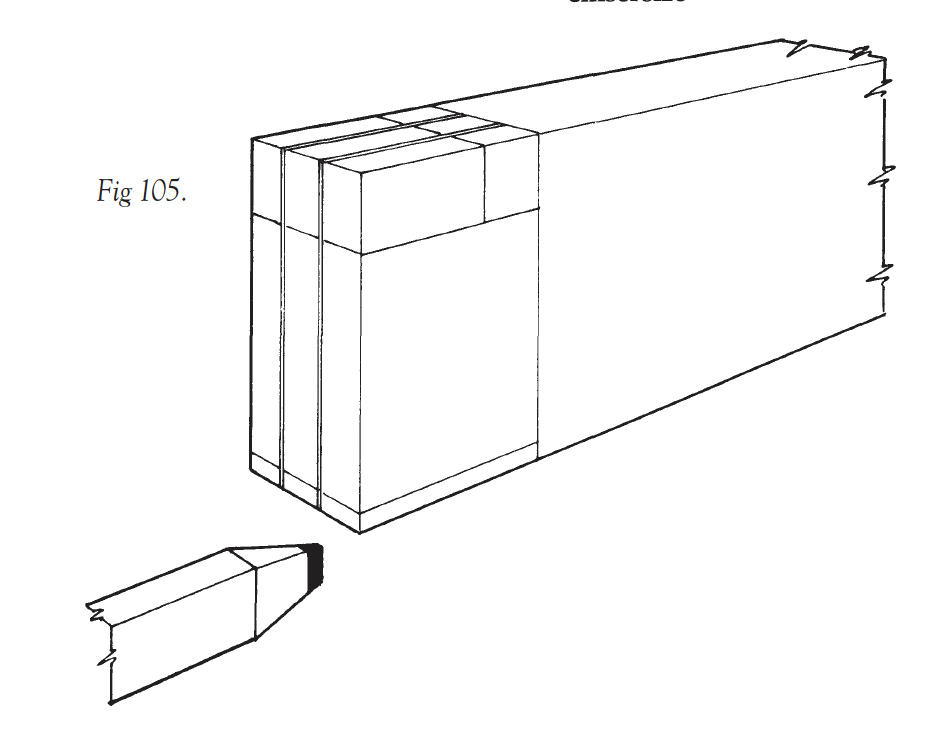
a thick, soft pencil is run in the gauge marks. This produces a double
pencil mark (Fig 105).
Hello Megan
Thanks for this. The first drawing has a “button mortice” shown. I wonder if you would explain this please.
Not Megan, but a “button mortice” is a mortice to receive one end of a shrinkage button, which is used to secure for example a table top. This further brief extract from Robert Wearing’s book should hopefully make it clear:
“Wood is porous and, depending on the atmosphere, will absorb or give out moisture causing it to expand and contract […]. This cannot be prevented, and allowance must be made for this movement in the construction of the table top.
If the top is screwed directly to the frame it will either split due to contraction or bow due to expansion. […] The problem is overcome using shrinkage buttons to secure the top. […] Buttons on the long sides must have room to move in and out so their mortices need to be only slightly longer than the buttons. Buttons on the short ends need room to move sideways in the mortices which must therefore be longer” (Wearing, The Essential Woodworker, pp 113 ff.)
The buttons themselves are small blocks of wood with a rabbet on one end; that rabbet fits into the button mortice, while the block itself is screwed to the underside of the top. There will of course be rather more than just one button used.
I should perhaps have said towards the end of my previous post that the buttons are small blocks of wood with a tongue at one end (that may have been created by rabbeting; hence my confusion of terms), and that it is this tongue that fits into the button mortice.
What Mattias said! Here’s a link to an example image: https://www.instagram.com/p/CxYZiPpOV1e/
I recommend this book all the time. I think I got the pdf from you 12 years ago? It teaches the way learn best and is full of little experiential details, like that little hump of remaining wood at the bottom of the kerf.
I have an old library hardback copy that went through a house fire in 2007. It’s charred and well read. I’m really glad LAP reprinted the book. It’s a keeper.
I have a question regarding the first illustration. The illustrator is showing the working edge (the edge with the “V” mark) downward on this rail. My instinct tells me that the working edge should be upwards. Does Wearing’s book offer an explanation for why he chose to do it this way?
In the laying-out process described and illustrated on pp. 59 ff., the relevant layout information is transferred from a rail/tenon (the rails and their tenons are laid out first) to the legs/mortises, with the true edge of the rail as the reference point, at what will become the underside of the rail.
Wearing does not say why in so many words, but apart from the obvious point (i.e. any reference should always be from a true edge or face), the inference I make, in particular from the illustrations, is that this will ensure that all four rails will end up with their lower edge/underside in the same plane, which is something that will be visible enough that it matters.
The true edges should not have been touched again by a tool after they were trued in the first place (except for minimal clean-up just before assembly), so will fit this purpose so much the better, while the top side, that will go against the underside of the top, can still be worked after assembly to get everything flat and co-planar there to receive the top without it affecting the final appearance of the piece.
Good answer. Thank you for replying.