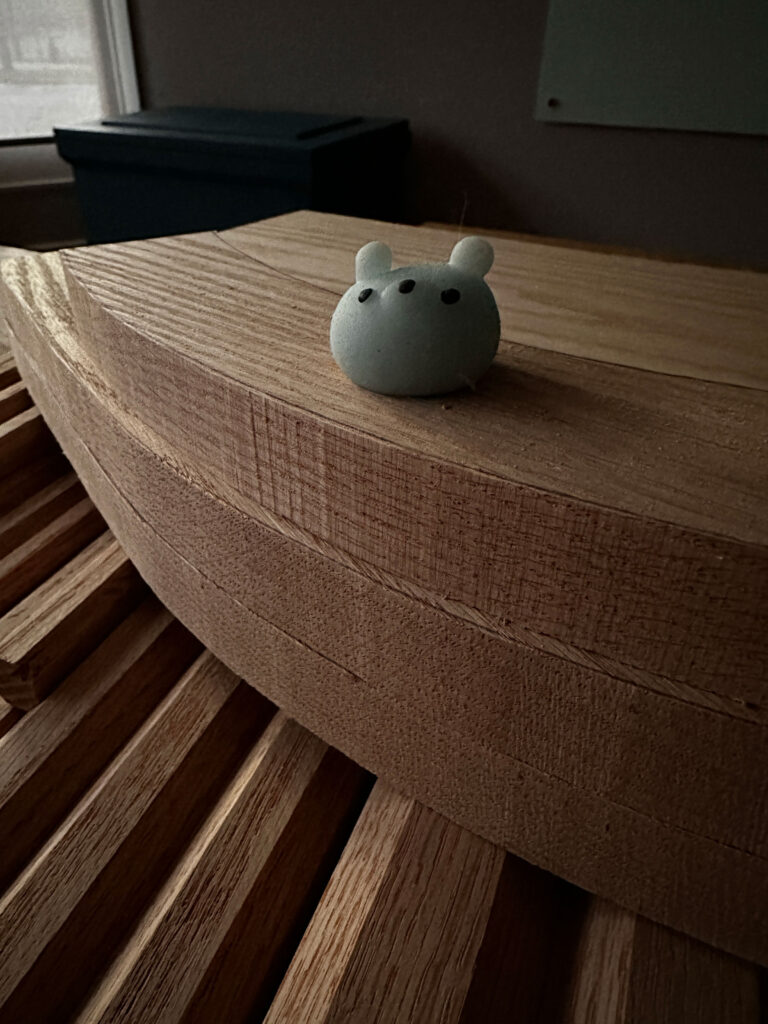
This weekend is the calm period before our class with The Chairmakers Toolbox next week. The wood in the above photo? Y’all paid for that with your contributions. The money you donated will also feed them all week. And there was extra cash ($2,700) left over, which was donated directly to The Chairmakers Toolbox. So thank you.
So onto today’s Open Wire, which we hold almost every Saturday. Type your question about woodworking into the comment field below. Megan and I will try our best to answer it. Apologies if our answers are brief and not surrounded by the usual pleasantries. Saturdays are a lot of typing.
So here we go.
Comments will close about 5 p.m.
— Christopher Schwarz
Thank you for all you do at LAP. The books and blog are some of the best education I’ve had since high school shop class.
My question is about mortise and tenon joinery. When do you use a haunch, and when do you just cut a straight tenon? Most magazines and websites show straight tenons, but Robert Wearing’s book (and I believe Charles Hayward’s) make it sound like haunches are required. I’m planning a coffee table and want to know if I should take the extra time to cut them.
Thanks again.
I use haunched tenons in door construction – when the haunch is needed to fill the groove in the rails and stiles for the panel.
Many workshop writers of the 20th century show a haunch for table aprons as well. The logic is that it will keep the apron from cupping as it dries. I’ll be honest, I haven’t found cupped aprons to be a problem on any table I’ve made. So I omit the haunch.
I might use the haunch in this instance if the aprons were a little wet. But otherwise, no.
Hey Good.morning guys! Did either of you pick up anything fun at handworks?
Besides a nasty case of COVID?
I bought a compass from Patrick Leach. And…. yeah, that’s about it. I only got to leave the LAP booth once, and it was for 45 minutes.
That’s too bad. I attend academic conferences now and then to present in poster sessions. One conference had the nice idea of providing an hour for presenters only, to be able to mingle with other presenters. Hard to do in a setting like Handworks.
Did lost art ever publish that book on Tage Frid from a few years back?
Nope. The author ran into a rough patch with some family health issues. We hope that will be behind him soon and he can continue his work on the book.
I have a nice Hock 2 5/8 blade but no Stanley 8 plane. Are there other planes that use this size blade i could use?
Not that I know of. You might be best off finding a new home for it.
Hey! If you could pick up a Stanley transitional jointer (the metal adjusters on a wooden body) for cheap, that might be the way to go. Numbers 32-34 all take the 2 5/8″ size.
Interested in your thoughts on this: I’ve had both my anarchists toolchest and Dutch toolchest for a few years now and recently have been thinking about which is better for protecting tools. I really love them both and am glad I have them. I wouldn’t give either of them up, but after some investigation I reckon the anarchist toolchest is the clear winner. The dust seal does such an amazing job – you can hear the air gushing out as it shuts tight. When I open it again, sometimes after several months, everything looks the way I left it like it’s been in stasis – no evident oxidation or corrosion. Not so with the Dutch toolchest. I’ve had to cleanup some surface rust a couple of times, but nothing problematic. The slanted top does a good job keeping the visible dust out but the main difference is the absence of the air tight seal. Just wondering what your experience has been like? Have you overcome the seal issue? Notice how I haven’t asked about the status of Megan’s book (I’m sure it’s close)?
I don’t recall any difference in corrosion between the tools in our two chests. But our tools get removed constantly and are wiped down with an oily rag before they are returned to their place in the chest. Wiping down the tools is probably our No. 1 defense against rust.
If I were thinking about long-term storage, a dust seal on any chest is a good idea and could be added to the Dutch chest as well.
As Chris notes, a seal on the DTC would help (and that’s one reason I like a lid with battens, pretty sung to the outside of the top edges. That leave only the back edge and the lower section to address – maybe felt or squishy leather edging would help?
Wood scraps & clamps are over-taking my small shop. Any favorite ways of storing these? Any great hints learned over the years? Do you have a system for organizing wood scraps (similar sizes together)? How do you determine scraps to keep vs. burn (I can’t seem to get rid of hardwood scraps!)?
We are ruthless because we go through so much wood. We have two bins: burn and save. Once the bin of “save” stuff is overflowing, we cull the least-desirable pieces. If it’s a precious scrap (say, bog oak) then it gets stored elsewhere.
We try not to have much wood on hand – there’s simply no space. If we had a barn, we’d have a different philosophy (maybe).
Clamps we hang on simple wall racks.
Magazines such as ShopNotes are FILLED to the BRIM with ideas for clamps and scraps. Sorry we don’t have any real wisdom here.
I’ve jokingly told my dad we are going to give him a proper Viking funeral with all the wood and scraps he has lying around.
As a wood scrap hoarder, I have found some old filing cabinets work well. Different drawers for different species.
Good morning Chris and Megan. Will you be posting you 2024 class schedule anytime soon.
It will be posted on Monday.
I’m going for it this time. I will be there next year.
Good morning Chris and Megan! First, as one of your biggest fans, thank you for developing and maintaining the “Welch Chair Information System”. The effort required to keep this going must be beyond exhausting at times. Second, I am getting ready to glue up two seats and am considering using butterfly joints. I love the look so the extra work would be worth the joint. Aside from the fact that this is not your joint of choice I am really interested in your thoughts.
Hi Rob. Are the butterflies for joinery or for looks or for repair?
Historically, you don’t see many of these joints in stick chairs – though I am sure they are out there. You are far more likely to see the seats joined with loose tenons that are then pegged – sometimes decoratively.
I’ll be a little too honest here: I think butterflies are a current fashion that goes with the live-edge stuff. It looks like 1970s furniture to me (that’s not a bad thing). I try to keep my stuff looking like the old stuff, so I wouldn’t use a butterfly on a stick chair. If I had a split in a seat (a common place for a butterfly), I’d probably use a blacksmith-made mending plate because that’s what I’ve seen on other stick chairs.
As always, make yourself happy and ignore me.
As we all get older, physical issues start impede progress…as nature would have it. If either of you have felt the hand of father or mother time what adjustments have you made to stay in the game? For ex. More machinery, more sitting, lower/higher bench, more libations, etc.
I have handed over more stock prep work to the machines – but that is as much of an economic question and a physical one.
I use the Roman workbench more and sit down. But that’s also a matter of me exploring it and different ways to work.
I now have better shoes. Better light. Better floors. A Moxon vise. All these help my back.
But in the end, I take the “bicycle” approach to the craft. You have to keep pedaling so you don’t fall off. I find the more I work, the better I feel and the fewer aches and pains I suffer.
For those of us who are over 6-feet tall, wouldn’t back trouble be assisted by having a workbench above the average 34-inches in height (say, 35 or 36 inches)? Wouldn’t that encourage less bending over when planing, for instance, keep a straighter back? Or is my thinking bent? 😉
If you can’t in effect “lock” your arms over the plane, it’s a lot more work to plane. I can plane on tall benches (I’m about 5’5″ these days), but it sure does wear me out – and it makes my back hurt!
Workbench height is a third rail in woodworking. It all depends on what you do and your body. There are guidelines out there, but they are only that.
Or you can just set it to 38″ and the magic happens.
Thank you Chris and Megan for doing Open Wire so regularly and taking time out of your weekend. Question. If you were going to build a simple cabinet with drawers to place on the shelf under your workbench, how would you design the drawers? with runners and grooves or metal drawer slides?
Metal drawer slides are too easily broken in a workshop environment (we have some in our machine room and they are a mess).
If I were making it fancy, I’d make traditional dovetailed drawers in a carcase – like a chest of drawers. If I were going for quick-and-dirty-and durable, I’d cut 1/2″-wide grooves/dados in the case sides and make drawers that sat on top of 1/2″ ply bottoms. And the bottoms would be oversized to fit into the grooves/dados.
By traditional dovetail drawers do you mean the “piston fit” drawers? Thank you.
Not piston-fit. Just drawers in holes that slides easily in and out and aren’t jammed by wood expansion/contraction.
Best way to learn sketchup? I’m wanting to create better visual instructions for my students.
I took the SketchUp tutorials when it was first released. That will get you making boxes and basic curved stuff.
There are a couple people who offer books and classes for woodworkers that can take you into the advanced stuff. I’m not a SketchUp whiz, I’m afraid. Perhaps someone here can offer more specific recommendations.
Up here in Minnesota, I found a supplier of #1 SYP at good prices, but the wood is KDAT (Kiln Dried After Treatment) with Micronized Copper Azole (MCA). The usage guidelines allow for indoor use, including furniture, as long as there isn’t food contact. There is no outgassing. Even the California folks allow it. I’ve seen a ton of FUD about using this for a workbench, most of which seems rooted in the old arsenic-based preservative days. Of course, a dust mask and dust hygiene during construction are essential. Do you know of others who have used this for their workbenches and lived to tell about it?
I do not. Sorry, I haven’t read up on the stuff I’m afraid.
Good morning!
Have you heard of sets of “sash planes” which cut complementary, complex mouldings where the sash meets the sill? I was talking to an retired joiner the other day and he mentioned them, but hadn’t seen any since he was young. Do these exist? Is there a different term I should be searching for these with?
Oh sure. But that’s a different trade entirely. I would reach out to Richard Arnold for assistance:
https://www.instagram.com/arnold_richard/
Amazing man with a lifetime of knowledge on the subject.
Thanks! I’ll send him a message!
Love LAP and all that it does, and am slowly collecting most of your books. My question: is there a detailed, handy reference on tenons? Something that provides rules of thumb on thickness vs width, when to start splitting them into two or more, when to have shoulders vs haunches, etc. I have Hayward’s Pocket Book but I’m looking for something more. Thanks!
Our book on joinery by Hayward has everything you need on tenons. There aren’t a lot of hard-and-fast rules except for Moxon’s, which is basically: the strength of both need to be considered and balanced.
Sold! Thank you.
Thanks for these Open Wires!
I made a smaller, lower version of the three legged table from the Anarchist’s Design Book for sitting around with friends and playing music.
I mis-reamed one mortise: realized the angle was too slack and tried to adjust at the last minute, so the tenon was a little bit loose. Tried it anyway, but the leg fell out.
What is the smart way to repair this? I ended up laminating layers of wood shavings into the mortise using the tenon wrapped in wax paper as a mandrel, and then reaming again. It has held up, at least so far.
I’d leave it until it becomes a problem. Some solutions: glue it back in with a lot of epoxy, which is a gap-filling adhesive.
Or plug the hole with solid wood and recut the mortise.
Two woobie question for you. 1) where do you put it while working? hanging on the tool rack? in a small wooden box? 2) do you ever launder them to get the dust/grime off?
I was just thinking about this – I just laundered mine, as per the instructions (just wash and dry – no softener like a normal microfiber? and then added the suggested 4ounces of oil. Even if the rag is completely saturated, it’s WET. like, leave too much oil on the planes wet. I’d probably use like 2-3 ounces next time. Hoping I can wring some out lol.
I hang mine on by bench lamp. You can launder them when they get disgusting and then recharge them with oil. You might launder them alone — or with other shop rags.
As always, thanks for hosting this.
I just finished a Gibson chair (yesterday) and I am thinking about painting it with linseed oil paint. I know you only have done one or two chairs with the linseed oil paint but I would love to hear your process and what you’d do differently if you don’t mind?
I understand you’ve changed a few things from the last time you talked about linseed oil paint and a chair is a little different than a spell blank!
We thin the paint about 10 percent with odorless mineral spirits. This makes it easy to brush and the paint lays out better.
Then we are patient. Wait a week. Then apply a thin coat of oil/wax with a fine abrasive pad. This will smooth out any nibs and give the paint a nice glow.
There are lots of techniques out there yet to explore. So don’t take this as gospel.
Thanks! Hopefully painting today. I learned how important UV is for curing while painting a creepy stool–no natural light in my shop, just UV-free LEDs–so will be converting my living room into a painting booth this time!
What about washing the brush afterwards? Do you use straight Linseed Soap, or do you mix some water with it?
Thanks for the help
Not Chris, but I have had good success with linseed soap and warm water in my sink. Just putting some soap in it, massaging it around, rinsing, and repeating. Even with the soap it is not a quick process by any means, probably ~5 minutes/brush!
Same.
Why not use mineral spirits? With regular paint, I let the solids settle out and reuse the mineral spirits over and over.
Hey Chris, I am moving overseas next year and plan to ship my hand tools in a tool chest with my household goods on the slow boat across the Atlantic. Do you have any recommendations on how best to protect them during the shipment?
I’d wipe them down with an oily rag, then wrap them in articles of clothing and with dessicant pouches. That should be enough (unless you are moving to the equator…. then I don’t have any good advice).
I’ve heard of people using shellac for ferrous components for long term storage. Then it dissolves easily with methylated spirits once you want to put it back in use.
Shellac doesn’t completely block vapor, FYI. But it does help.
I’ve been working on projects and skills in the chair making progression, still kinda intimidated by the ‘butt portrait’ seat carving and have some tools to buy. I like the idea of a flat bottomed inshave but the Lucian Avery is wait listed and pricey for an amateur hack. Do you have a suggestion for an alternative? Or should I just start with a more rounded Scorp? Can the work be done with a decent travisher? Many thanks.
You can do all the seat saddling with the basic travisher from Windsor Workshops. It can be set for a rank or fine cut.
https://thewindsorworkshop.co.uk/product/travisher-wood/
Any thoughts on having Matt Cianci at LAP for a saw sharpening class?
Yes. He is teaching here in 2024. Classes will be announced on Monday.
No questions today, just gratitude for your continued inspiration!
Yes. Thank you LAP for hosting this. I see so many questions I didn’t know I had, and their answers.
Hi good Morning!I recently built a chair based off of your design in the first stick chair journal. All components were made of local kiln dried tan oak except for a beech seat and comb. A few days after completing I noticed a couple hairline cracks here and there in the legs and stretchers. The grain is more or less dead strait. I’m wondering if I could maybe fill in with some glue/epoxy? Would that help at all?
Thanks!
I’d keep an eye on them. They might not be anything more than cosmetic. If they do progress, some thin epoxy might stabilize them (check out West Systems epoxy, which can be adjusted for viscosity).
Stick chairs are known and beloved for their defects. So hairline cracks are like wrinkles on a face to me.
Hi Megan and Chris
I watched Megan’s TWWG Travelling Tool Chest build immediately upon release, and I’m almost finished Chris’s American Welsh Stick Chair build.
Really good production quality and they are the only two TWWG videos I’ve got.
Are either of you planning more videos with TWWG? If so, when do you think these would happen?
Thanks!
Megan has one coming out on building a boarded bookcase. We don’t have any more scheduled with Marc, but would be very open to it.
Ditto what Chris said – we’d be honored to be asked.
Good morning Chris and Megan,
I really like your “garnet shellac followed by Black Bison wax finish.” What are the wood species that work best with this? I’ve seen it on your Campaign Furniture mahogany pieces and think it looks fantastic.
Open-pored woods such as oak and mahogany. Diffuse porous and closed pore woods just look smeary with the wax.
Approx how many board feet is a full sized ATC?
I’d buy 20% more than you need, but it shakes out (exterior only) at about 110 bf
Thank you so much!
I know you wrote somewhere on which cut nails you keep in the shop for work and that you don’t use screws too much. I was wondering if there were any screw sizes that you do keep on hand and use regularly.
We use lots of screws. Mostly slotted steel No. 8s from Blacksmith Bolt. We stock, 1″, 1-1/4″, 1-1/2″, 1-3/4″ and 2″.
We also use a lot of No. 9 1-1/4″ Torx for making crates.
Are you doing a new gift guide this year? Thank you!
Yup. It will go live on the American Peasant first (they are paying me). Then here. It’s a big list I have been working on all year.
I have a question about holdfasts. When working with different thickness stock you set it to different heights, i know its not exact or anythibg but roughly what heights do you set it to? With thin stock, thicker?
Wow. I am not following your question here. Sorry. Could you maybe amplify what you mean about “set it to different heights?”
Facepalm, this is what happens when i dont sleep. Not holdfasts, planing stops. Like the one you sell.
Sorry
I keep it set about 1/4″ to 1/2″ off the benchtop, which handles about 90 percent of my needs. I only raise it when edge-jointing stock on the benchtop. And I lower it when working with thin stock.
You and Aspen Golann working together represents a lot of talent in one teaching team.
I guess I’m just curious if she simply assists, or whether you each have different approaches or preferences that complement one another or benefit the students in some way?
Would love to see any photos from that class on the blog this week.
Thanks for your time today.
Haha. Aspen isn’t my assistant. I teach the chair. She teaches design. And we both teach how to teach.
Hi Chris and Megan, I know you don’t do much green woodworking, but do you have any opinions about froes, such as from Barr, Lie-Nielsen, Ray Iles, or the one in the Chairmaker’s Toolbox? There are differences in how the handle is attached to the blade, blade taper, and steel, but the larger ones are fairly similar in price. I’m keeping an eye out for used tools too, but usually they don’t appear to be in very good shape. Thanks!
Someone else will have to pretend to be an expert here. I have the Lie-Nielsen and have no complaints.
Greetings from the (great white) north!
Many of your products are available to us in Canada (eventually) but not all. Is there an alternative (note: easy + legal) method of purchasing things like T shirts and coffee mugs (and other forms of advertising)? I understand your hesitancy to ship outside of the U.S….
There are lots of companies that will forward things to foreign addresses. Google “package forwarding service” and you’ll see a lot of them. In general, you pay only a little more than you would if you had paid for international shipping.
I thought I read that pocket hole joinery, or at least a pocket hole fixture, is used in the new chair video.
If that’s true, does the design of that chair require it, or can I substitute something more traditional like mortise and tenon joinery is a fairly straightforward manner? I would prefer to use M and T.
I use a pocket hole jig as a clamp to hold the arm pieces together while the glue dries. Then the screws are removed and the hole is covered by the shoe. You can also use a rub joint, a dowel or a loose tenon. Lots of options.
You folks have more cats than I do. How do you keep the cat hair out of the finish!
We are fastidious vacuumers. We also sand between coats, which removes most of the cat hair and other debris. The final coat (wax) doesn’t really trap hair.
Hi Chris/Megan,
I have signed up to take the ATC class at the Port Townsend School of Woodworking Jun 2024. I’m very excited as I had planned to take this class Summer 2020 (stupid Covid).
It is listed as a “traveling version of the Anarchist’s Tool Chest that will fit into the back of a car or truck (14-1/2” high, 19-1/2” front to back, 39-1/2” long.” Sounds perfect for what I will use it for rather than the full sized version. Can you please help translate that into how much it can hold in terms of tools? Is that bigger dimensionally than the Dutch tool chest (as I can find lots of YouTube videos showing what that holds)?
I’m debating to finish it with either milk paint (as I did on a mini-ATC I made a few years ago) or the linseed paint you’ve been talking about recently. Any thoughts on pros and cons of each?
Many thanks.
Sincerely,
Joe
PS Thanks Chris for speaking at the woodworking club (via Zoom) that I belong to this past Wed pm. Appreciate your generosity with your time.
I’m very much looking forward to the class! I can fit maybe 20-percent more tools in the small ATC compared to the DTC – and I can fit longer ones. The DTC is sized for a No. 7 in my case, a No. 8 for some – but it won’t hold a full-size handsaw. The small ATC will. But I can’t store moulding planes in in (at least not on end, as I do in the full size ATC) – and that’s a good use of the bottom portion of the DTC. So…I’d probably bade my choice on the kit of tools you want to keep in it. The tills are both about 2″ deep – do nothing taller will fit in them if that’s a consideration.
The linseed oil paint takes a long time to dry – but it only takes one coat. So it’s a tradeoff. Both are good.
Thanks Megan. 20% more room than a DTC. That really helps. I suspect it will be more than adequate for my traveling needs. If not I can always make a full sized ATC. Time for the paint to cure is a non-issue. I will probably do linseed oil paint just to try it out. Probably two coats with red underneath and black on top. Will be fun. Likely will end up with a full sized ATC out of fancy wood eventually as a blanket chest in the home. All good problems.
I’m really impressed by the recent furniture you’ve shared for the American Peasant project – it looks fantastic. I’m eagerly anticipating the release of your book. I noticed that you used a No. 48 tongue and groove plane for one of the pieces. Will this plane be a frequently used tool for various projects in your upcoming book? I’ve noticed that Lie-Nielsen currently has them available, and I’m considering getting one in advance. Thanks for your insights!
Not Chris…but yes. Either the 48 or 49.
If I had to choose one, get the 48. The 49 is helpful for small coffers. But the 48 can do it all.
My damp, basement shop is a mess and I only occasionally wipe paste wax on the scattered tools. I’ve only once noticed rust, developing on a card scraper: I cleaned it off and haven’t seen it again. Do I have magic tools, a magic basement, or bad eyes? Does it matter?
I got really interested in “grown furniture” a while ago – it’s an ancient practice, especially in the East, where it was used for things like bridges and barricades. In the early 20th century, the West also saw a revival of this technique. Essentially, people shape and grow trees into chairs, tables, and even entire houses.
While books like “Make A Chair from a Tree” and “Make a Joint Stool from a Tree” touch on similar subjects, it’s worth noting that “grown furniture” stands out with its organic forms and nearly waste-free methods. I have an extra copy of Arthur Wiechula’s “Wachsende Häuser aus lebenden Bäumen entstehend” (translated as “Grow a House from a Tree”), which features mind-blowing images showcasing the incredible possibilities of this art form. If you’re interested, I’d be happy to send it to you for the stunning visuals alone.
I’ve seen some of this stuff and it is fantastic.
A possible advantage of the Nicholson workbench is that it appears to be easy to sweep under because it has no low shelf. Do you do anything special to sweep under a heavy bench that has a low shelf?
Not really. I have a high-quality broom and a dustpan. Followed by a floor sweep attachment to the shop vacuum.
Get down on my hands and knees! (And use an extension on the shop vac.)
This is funny because I’m thinking of adding a shelf to my Nicholson style bench.
Ahoy again Chris! I have a few questions:
I read your recent Fine Woodworking article on sharpening – great stuff. I am currently using diamond stones but am on the cusp of needing to replace them and I’m considering waterstones. Which brand of waterstones do you recommend?
I also read your blogpost on pricing work. I think an escrow account is an excellent idea for deposits – but how do you handle material costs? Is that paid for separately from the deposit upfront by the customer and is non-refundable?
Finally: I’ve been lusting over the Crucible Lump Hammer but doesn’t the metal head cause dents? Or should it only be used on striking tools and/or with a striking block during assembly? And I must ask if there are there any plans to make one out of brass?
We both use Shapton Pros (we got a “set” of 1k, 5k, and 8k on – sorry to say it – Amazon. https://www.amazon.com/SHAPTON-Kuromaku-Ceramic-Whetstone-Medium/dp/B01FYEYKEI/ref=sr_1_1?crid=M5V6THTOWC1M&keywords=shapton+pros+set&qid=1694888011&sprefix=shapton+pro+set%2Caps%2C132&sr=8-1&ufe=app_do%3Aamzn1.fos.f5122f16-c3e8-4386-bf32-63e904010ad0)
Materials costs are, for me at least, factored into the quote. And because neither of us make crazy/singular commission pieces – in fact Chris does little commission work at all – we know it will sell to someone else if the first buyer backs out. (e.g. a tool chest for me, a chair for Chris). But if I were building a curious piece/custom design, yes, I’d probably charge a non-refundable stock fee…unless it’s a species I’d use for something else. But to be honest, I probably wouldn’t take a commission in zebra wood or the like in the first place!)
Yes. We always use a “beater block” between the hammer head and the work. And right now, we don’t have a brass one in the works.
Thanks Fitz! I will continue dreaming of an engraved brass lump hammer
Addendum: if you had to buy a new bandsaw (as opposed to fishing for vintage machines on Craigslist), and which one are you getting as a general use saw?
Probably the 14″ JET. I have their new metal/wood cutting band saw. It’s more expensive than their wood cutting saw, but that’s because everything has been upgraded like a vintage band saw.
The wood-cutting JET is good, too.
Thanks Chris! I’ll check it out
Just got the TWW Guild chair videos and the courage to give chair making a try. Is Poplar a terrible choice for a stick chair or is it best to stick to something like Res Oak?
If the poplar is dead straight, you’ll probably be OK. A slightly better suggestion would be to use poplar for the seat, arm and comb. And red oak for the legs and sticks.
I used straight poplar in like 2 chairs it’s worked out fine. They were the chairs with the bigger sticks though no tapered legs. To be honest popular kinda sucks to work with in chairs. Carving the white wood in the seats sucked oak was much easier to work with imho
If you were to make a toolchest for just your chairmaking specific tools, what style would you use?
Probably the Dutch. It’s more compact and easier to travel with. And the tools would fit easily in it with some room to spare.
I thought I had posted but I messed up. Any thoughts on fixing a small (maybe 1/32) gap at unglued
Corner of ATC. I know the molding is good option after glue but any ideas in tweaking joint before glue to eliminate a small corner gap?
A gap in the dovetails? Or between the carcase and the skirt? Both?
We use go-bars (aka goberge) to push the carcase out to close small gaps between the carcase and skirt. This is done while the glue is wet. At the corners, we use small blocks of wood to press the tails into their sockets to pull up gaps. And we paint hot hide glue on the exterior of the components (David Savage’s Juicy Lucky Trick) to swell things up.
The we use Durhams Water putty and paint to finish the job.
Hope this helps.
Sorry meant gap between carcass and skirt. Putty makes sense. I had wild ideas about trying to cut down baseline of top rail to get it to
Seat but that sounds pretty sketchy
Hello friends! Love these Open Wires, I read them like some people read the sunday paper or the sports section.
I plan on making a pair of Gibson chairs (for my kids) in January. Due to lack of space (but also enjoying hands tools as my happy place) I have no power tools. My expectation is that the main thing I’ll need to do on the Gibson different from what y’all do is to use regular rip saws for rough milling, planes for the sticks and legs, and then I guess a frame saw for cutting curves like the seat and arms. Are there any other tips or suggestions for a purely hand tool woodworker? Thanks!
P.S. thanks to fitz for the article on the DTC, I completed mine last weekend: https://files.mastodon.social/media_attachments/files/111/033/504/631/817/248/original/3cf3c044f3140016.jpg
If I were shaping stuff by hand, a small hatchet would speed things up, as would a drawknife.
I were allowed only one hand power tool as a chairmaker, I’d buy an electric jigsaw.
Great. I have a (not yet sharpened) drawknife and will keep my eye out for a small hatchet. Any recommendations (from you or other commenters) on hatchet sizes welcome, but no need to answer, I got in my one question!
The one I use for small work is about 1-1/2 lbs. head. But I am no hatchet/ax expert by any means.
I’ve done extremely little finishing in my life. I just completed some oilstone boxes which I want to protect. I was thinking of using either Allback Boiled Linseed Oil or Raw Linseed Oil then followed by a few coats shellac (made from flakes). Does this seem prudent? Will the shellac coat will over the the linseed oil well? Do you recommend raw or boiled for this application? I’ve heard raw penetrates better. I was going to do the shellac with a wool center wrapped with some linen. Do you have a recommendation for the outer cloth? I’ve heard cotton may leave behind fibers. Thank you!
You can put shellac over oil after it has fully cured (I’d give it about two weeks). Raw or boiled oil is fine for a finish. Just use very very thin coats. Wipe the oil until it is dry.
The boiled sets up faster, but it has metallic driers. So that’s the trade-off. They look the same. And I wouldn’t worry about penetration.
As to shellac, when we pad it on we use old cotton cloths that have been washed so much they don’t deposit lint etc. Old T-shirts work. And we put a drop of mineral oil on the pad to slow down the flashing of the shellac.
Oil is a vary forgiving finish. The first time you use it, you will have success. Shellac is something I would practice first on scraps before applying it to furniture. Yes, shellac is completely reversible (as is oil). But removing it can be labor intensive.
Thank you!
The metallic driers is a concern for me, so thank you for mentioning that. I didn’t realize Allback contained those.
Okay coming back in after my cosmic voyage painting my Gibson chair with Allback Linseed Blue (a great replacement to my beloved General Blue Moon milk paint). Thinned with odorless mineral spirits as suggested.
Overall, more frustrating than I had anticipated. I wasn’t thinking and had burnished the sticks and legs with a handful of shavings during “make pretty” and they were mostly finished from the tools otherwise. The hard maple didn’t want to take the paint. I would lay down a layer and if I came back to tip off the paint I would just expose bare wood. Painting across the grain seemed to help and then a VERY light tip with the grain to get the brush strokes looking better–even this would sometimes expose bare wood, imagine painting on glass or something.
The sanded surfaces took the paint wonderfully but that was basically just the arms. The seat was unsaddled and thus unsanded. It did better than the burnished sticks but I’m thinking if I was going to do this again I might hit every surface with 240 or 320 grit before painting.
Looking forward to hearing other people’s experiences and seeing some more gorgeously painted chairs!
I just receive my first bottle of Piggly No Wiggly glue. I assume that “Death Grip” was already trademarked? Had you ever considered, “Rigor Mortis(e)” ?
We considered about 500 names. Death Grip wasn’t trademarked, but another company uses it. So we did the right thing.
I have a small small mill and I’ll start cutting some white oak and red soon. What dimensions should I cut for stick chair parts
Most of all, make sure your cuts follow the grain. Cut 8/4 for everything but the arms. 5/4 is best for the arms and doesn’t have to be straight. Good luck!
I’ve just completed my third stick chair. All have been made from red oak.
This one is a vast improvement over the first but I’m finding red oak to be a little tricky work with.
I’m going to make one more with this wood and then give cherry a go.
I bought the red oak because it was affordable and I thought it would be good to learn on.
Can I expect cherry or walnut to be a bit more forgiving.
Thank you
Ray
Hi Ray,
I think cherry and walnut are easier to work. They cut like butter. But it pays to master oak because it makes such inexpensive and strong chairs. You also learn the tricks. Make the seat from rift or quartersawn stock so it’s easy to saddle.