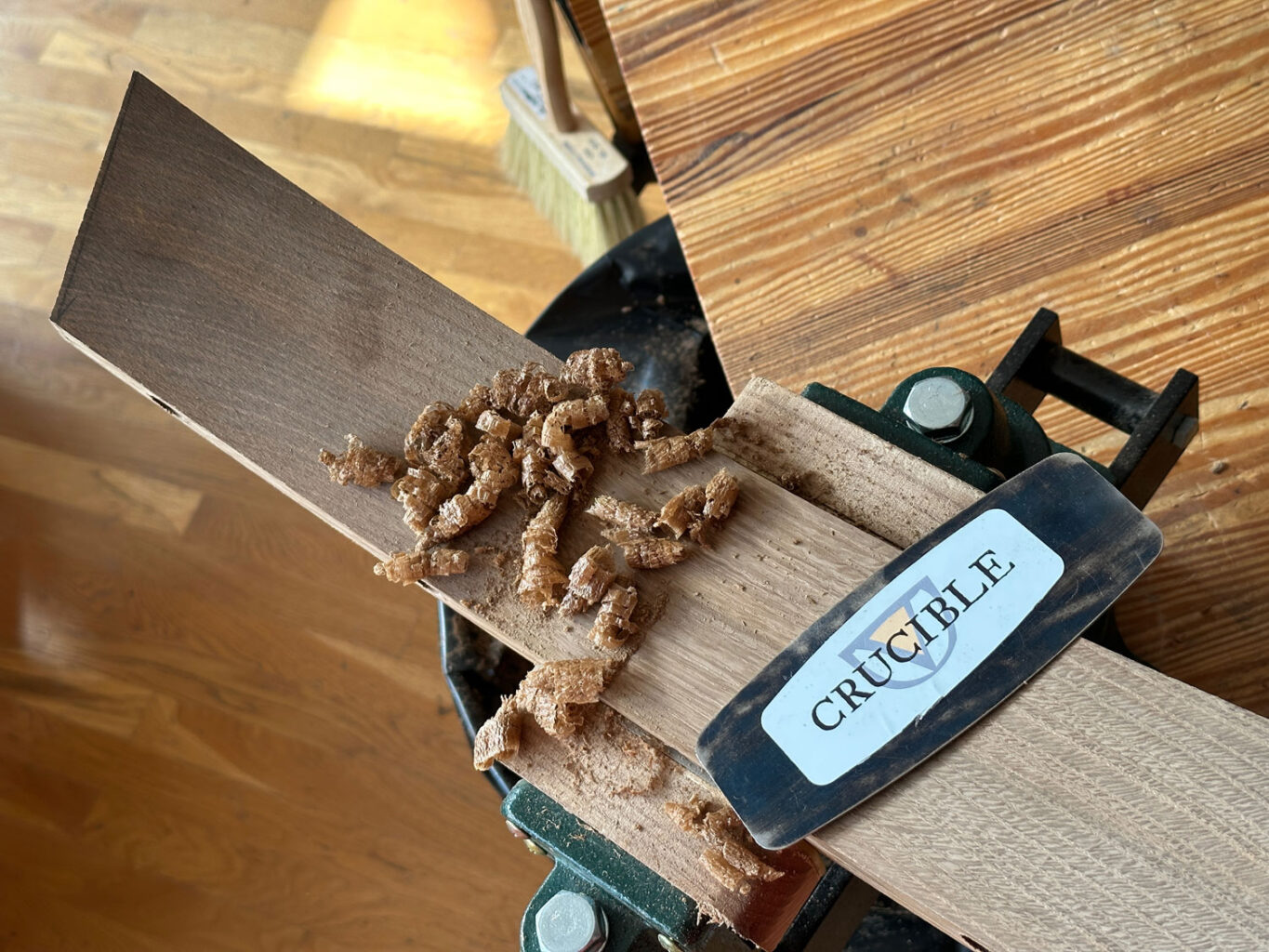
This has been a wild week, and we should be sitting by the pool with some margaritas. But instead, we are here for the Lost Art Press Open Wire.
If you’ve got questions about woodworking, our books, tools or grub ephemera, we are your answer team.
This week’s open wire is hosted by me and Megan. Here’s how it works: Type your question in the comment field. Brevity is appreciated. We will do our best to answer it. It is that simple.
Two notes: 1) Comments for this entry will close about 5 p.m. Eastern. And 2) Next week’s Open Wire will be held in In Person at Handworks in Iowa. So come to the Amana Colonies and meet some of your 5,000 closest friends.
NOTE: Posts are closed for this week’s session. Next week we will be LIVE at Handworks in Iowa answering questions.
— Christopher Schwarz
How did the fund raising go for the fall classes?
I’ve been meaning to write about this…..
It went great. Readers donated $10,163 (after PayPal fees) for the two classes. Most of the money was not designated to either class. So I am splitting it down the middle. Here’s how it will be distributed:
I’m holding onto $2,300 for each class to pay for all the wood and meals during the class. ($4,600 total).
I’ve sent Jerome $2,794, which he plans to use to help pay for students’ travel to his class.
I need to send the same amount to Aspen, but we haven’t connected (will do that today I hope). It will go to fund the Chairmakers Toolbox.
Any money I have left over from purchasing materials and meals is sent to Jerome and Aspen.
Thanks to everyone who donated. Every bit helps.
This makes me happy. Thank you too.
Is it still possible to donate? PayPal wouldn’t take my money the first time I tried and then I forgot.
Absolutely yes:
https://www.paypal.com/donate/?hosted_button_id=QHGYHGZMS5EY6
Thanks and done… PayPal accepted this time. I appreciate the chance to help like this.
good morning to you all. Any idea when lie-Nielsen will resume making there full line of tools again if ever
I haven’t talked to Tom or Deneb lately, so I don’t have any first-hand information.
It seems stuff comes and go. I have found checking the website often helps. Just the other week the brass hammer was in stock along with the tongue groove plane
I was on their waiting list for Lie-Nielsen’s No. 3 smoothing plane for months. When I stopped by LN in Warren, Maine on my way to Acadia this summer it was in stock through their showroom. So was a hotdog for my low angle jack that I thought they had discontinued. Impractical, I know, but Maine is a beautiful place to visit!
I’m enjoying following your linseed oil paint discovery. Have to tried layering like in a black over red milk paint finish? -Tim
We have not tried layering it. I have seen a lot of chairs and benches and houses where that happened naturally over time. So I know what will happen. Linseed oil paint ages beautifully.
I wanted to following up on the linseed oil paint discussion. And I apologize if you have discussed elsewhere. How have you liked working with the linseed oil paint and are there any special considerations. I think I saw a post that you have been diluting it a small amount. Thank you -Morgan
I LOVE it.
We are thinning it 10 percent with low odor mineral spirits. This makes it easier to brush and helps in it flattening out.
There are other methods ahead for us to experiment with. (Such as starting with a radiacally thinned solution as a base coat.)
There’s a good chance I’m going to be doing a wall of built-in bookcases soon but I’m not that familiar with building built-ins. Most of the stuff I see online all talks about using plywood but I don’t really enjoy using sheet goods.
Any suggestions on books specifically geared toward traditional built-in work? Any wisdom gained from multiple building restorations?
Thanks for all you do for the community!
I don’t know of any books aimed at built-ins made from solid wood. Substituting solid wood for plywood is pretty easy – you just have to account for wood movement, mostly.
Jim Tolpin has a good book on built-ins called “Built-In Furniture: A Gallery of Ideas.”
The major differences between free-standing and built-ins are:
Sorry I don’t have a single source to recommend….
I am gluing up large panels with Old Brown Hide glue. Struggle to find good info online…. I have enough clamps for two panels at a time, so do they need to sit clamped for the full 24 hours or can I get a second set of panels glued up the same day, say, after four hours in the clamps? (I know the glue takes 24 hours to cure and won’t work them until then).
As always, it depends. If the joint is excellent, closed easily and is not a spring joint, you can release the clamps after as little as one hour. You can go four hours for safety.
If the joint required some muscle to close, then I let the squeeze-out guide me. When it goes from rubbery to rock hard, take the clamps off.
The information out there is so variable because hide glue is affected by environmental factors, mostly heat and humidity.
I need to square panels for a chest. My largest square is a 12 inch combo square…panels are 20-24 inches wide. Any advice on squaring the end? I am confident to do the actual work with hand planes, but wondering how to mark the knife line and guarantee square so my dovetails work out. Thanks!
Buy an inexpensive framing square at the home center. It is a necessary piece of kit – so necessary that many of us neglect to mention it.
Veritas sells something called the “square fence” you can add to any framing square for just this type of thing. I’m a big fan of mine.
The Stick Chair Book inspired me to finally get around to making some side chairs to go with my dining table. I noticed in The Anarchist Design Book that you only use four sticks for the back with 5/8″ and 1/2″ tenons on opposite ends. This seems puny to my over engineering nature. Have you ever noticed issues with this size, or has time so far proven their strength?
The chairs survive fine. But feel free to jump up to 5/8″ for both. Or go to 3/4″.
I had read through Sharpen This multiple times at this point and I couldn’t find any info on strops. I use DMT diamond stones with a leather strop with green buffing compound. I was taking a class from Peter Galbert and he said my chisels were rounded over from the leather strop so I switched to using MDF. Now I have a piece of MDF that has ridges of rouge on it from use and doesn’t seem quite right. Any advice?
I learned to sharpen using strops. They are the same “grit” as an #8,000 stone.
Strops take some skill to learn to use. If you use too much pressure and lift the tool you get a rounded bevel. That’s not the end of the world (some people like it). But it has to be accounted for in your sharpening regimen (that is, make sure you hone a new edge when you go back to the coarse stone in your sharpening process). You can use honing compound on MDF, as you have tried. You do have to charge the sucker with a good deal of compound. Another option to stops is to use the super fine diamond paper (Lee Valley has it) and stick it to wood. That’s how I touch up all my chairmaking tools.
All this is to say that there are a several mindsets out there when it comes to sharpening. Some (like me) are after a flat bevel. All the time. Others maintain a rounded bevel. All the time. Both approaches work. But mixing the approaches is difficult.
God I hate sharpening.
Taytools.com sells 3m too 3×8
Hi Chris, I’m building the American trestle table and it seems like there might be photos of two different ones you’ve built out there. A painted base one in the popular woodworking article, and then another one in a photo on the Lost art press blog with a through tenon on the stretcher? I’d love to hear about differences in construction and what you like best.
I made two tables. One for the magazine – the painted base. And one for my home. Unpainted.
The only difference on the tables’ bases is the paint. Both are constructed with the same joints.
The tops are slightly different. On the table for my home I used breadboard ends (aka a clamp). The top for the magazine was just a slab. That is purely an aesthetic choice. And I like breadboards as they are a challenge to make and fit.
Oh! This reminds me – I am contemplating a smaller version of this table but wanted to make the base be able to be knocked-down – it’s for a person at the beginning of adulthood who will be moving often. I was thinking to extend the tenon through and use horizontal wedges … Am I nuts? Anything in particular I should watch out for? Any suggestions for a knock-down-friendly top attachment? Thanks for that design, it’s really lovely.
You’re not nuts – extend the tenon and use wedge; my dining room table base, built like that, has been just fine for almost 20 years. And use buttons to attach the top. That makes it all easy to break down for moving.
I built that very table with through tenons and wedges. It works fine. The edges need to be tightened from time to time, but once every few years is nothing.
Thanks so much. That will be a new technique/adventure for me.
Chris, have you made any double stick chairs? What would be the challenges of making one?
I have designed about 20 settees, but I haven’t made one. They all look like double-chairs to me. And that’s not what I’m after.
The construction isn’t the problem – it’s all the same processes. It’s the result. How does it look? John Brown and Chris Williams have made settees that look great. One is shown in Chris’s book.
I’ll get to it soon enough.
Good morning Chris and Megan. Any chair classes coming up that may have an opening.
Megan will announce our January-June 2024 classes shortly. I believe our 2023 classes are full. But being on the waitlist is a very good idea.
I purchased your “Sharpen This” video when it was first released and am wondering if you will be updating it to include and information/recommendations on sharpening hand saws? I am looking forward to seeing/meeting you at Handworks.
We have a separate book on sharpening saws coming from Matt Cianci. It takes more than a chapter or two to explain…..
Hi Chris, Megan,
The woodie planed arrived from HyperKitten (that I had asked about what kind of hammer to use) and is as advertised. A solid user with former owners markings and some wear from use. I’m quite happy to be putting it back to use. The wood needs a cleaning. How do you go about cleaning old wooden tools to remove the grime but keep the patina for what will be a solid working tool? It isn’t a museum piece so I’m not going for restoration if that helps. Many thanks Chris and Megan.
Sincerely,
Joe
I usually use low-odor mineral spirits (low in VOCs). That cuts off the grime. But it won’t change the color of the wood below.
TATHS – the Tools and Trades History Society has a number of suggested revivers in their website. DS
TATHS – the Tools and Trades History Society has a number of reviver formulas listed on their website.
Good morning!,
I was watching an episode of the Woodwrights’ shop from a few years ago where Chris explains how to use the fore plane/jack plane. In the part about sharpening it, it is mentioned that once sharpened, you were good for a few months to a year.
Lazy me likes the concept but Is this still reasonable for a jackplane or more geared towards a plane that is solely used for rough work?
Thanks!
-Sylvain
For a hobbyist, you will be surprised what you can get away with, especially with modern steel.
These days I sharpen my jack once a week. But that’s because chair work demands that I plane miles of wood every week.
Still, it doesn’t have to be crazy sharp like a smoothing plane.
Do you have any thoughts on finding a decent wood threading and tapping tool?
The German ones from Dieter Schmidt.
https://www.fine-tools.com/gewind.html
They are expensive, but worth it. The ones from the Far East are spotty at best….
Tool question, non-crucible division.
Last week I was working on a project that required me to use both my levels. As I progressed, I started noticing weird results, and eventually I put the small level on top of the top level, and realized that they were giving me different readings–if one was level, the other was slightly askew.
Two part question: 1) can I be confident that the laws of space and time still apply? I mean, they’re powered by gravity, right? I guess one of the housings must be twisted, but it doesn’t look like it…but more seriously, 2) how do I know which one to replace? They both agree that the floor itself isn’t level, and most everything else in the house that I’d like to think was a level surface was made level by reference to one of those levels, so…
Calibrating a level is important!
Is there a way to chose a random page from the LAP blog? I sometimes just want a read a random new to me LAP article and a random page/article button akin to the random Wikipedia page would be awesome.
Not that I know of…. but I’ll look and see if WordPress offers a widget.
One option is to start at the beginning and read ‘em all! A lot of good stuff in there!
Subscribe to American Peasant; you get a random one every week, with updated annotations
Have any of you made a baby crib or have any resources for finding plans or ideas for one?
I have not. Too terrified of all the guidelines, which seem to change regularly. Sorry.
I made one which I didn’t know at the time was mission style. Started it for our oldest and finished it two years later for our youngest! Everything was mortise and tenons. I overbuilt it because of my neuroses. Two and a half inch posts . Two by six stretchers. 2×3’s to form the rim. Etc. Though overbuilt I found it to be a great tool for putting the baby to sleep when I rocked her to sleep and put her down. I could lean all my weight on the top rim which might not be the case with some mass produced cribs. let me know if you wanna see pics. I made a mistake in the design and it could have been a lot simpler. acornjointree@gmail.com
How would you go about repairing a broken stick in a chair? I made a chair and decided I didn’t like the angle on the back sticks, so I took it as an opportunity to learn how to reverse hide glue and to plug/redrill the holes with a more comfortable angle. I got the armbow and comb off fine with a steamer, but no amount of steam could get the sticks out of the seat, so I cut them. Curious if you’ve ever successfully removed a stick.
Sure. I use a heat gun and wet rags. A clothes iron only gets you to 212° (100° C). And that can take some time to migrate into the seat. A heat gun speeds things up radically. You just have to avoid scorching the wood.
Thanks. So wet the rag, wrap it around the stick where it meets the seat, and heat it?
Exactly!
I’m trying to figure out what “dead straight grain” means when using Red or White Oak for chair building. The Oaks have the more obvious “larger” grain pattern in the foreground, and then a second, less-obvious “smaller” grain in the background, and they usually are not inline with one another . The “smaller” grain pattern seems best to judge for handplaning direction, and the wood seems to split naturally with the “smaller” grain. But, (I think?) I usually see the “larger” grain running all the way through your chair legs and sticks. Question: When using the Oaks, which grain pattern do you judge when searching for “dead straight grain” in your chairs?
A great question that is difficult to answer in words.
Bottom line, I follow the splits. And I look for boards where the fibers and the rings are both running sympathetically. I need to find a better way to explain this oaky issue.
There is confusion over the meaning of the term ‘grain’. The larger pattern you’re referring to is properly known as figure. Don’t follow the figure, follow the grain.
That’s a good way to put it. The problem in explaining it is that annular rings are also part of the grain structure of the board and can confuse.
Hi Chris and Megan, and as always, thanks for doing this. I am attending the Amama Handworks for the first time this year, and want to be prepared in case I see that must-have tool or whatnot… Is cash mandatory or are debit cards and the like generally accepted?
Most vendors take both. If you are after old tools, cash is ALWAYS better.
As the owner of a small business, I always appreciate cash so that I get to keep all of it (no 3.5 percent to the credit card companies). But people who use plastic are greeted and loved just as warmly.
Good morning! I’m trying to better understand the jack plane. When flattening lumber, does it matter whether I use a no 5 or no 62 jack plane? Are there occasions where one is preferred over the other?
While I am sure someone somewhere will come up with a functional difference, I use the tools interchangeably. We have a No. 62 and a No. 5 Bailey here for students. Both have curved irons. Both work just fine, despite the protestations of the internet.
Good morning! I want to make sure I understand correctly the orientation of the workbench top assembly. Do we stack our boards same grain to same grain or do we alternate the grain as we glue up?
If you can, make the annular rings sympathetic, like a can of Pringles. Sometimes you might get turned around (it’s OK because open glue makes us stupid). And that’s OK. The top will be fine.
How do you all feel about “chasing the burr” after routine sharpening? I often find a burr on my bevels after the final polishing step.
I didn’t find any reference to “chasing” in “Sharpen This” and wondered if you (a) ignore that burr; (b) never get one, somehow; (c) other?
Thanks very much!
I don’t find this to be the case except with some of the gummy steels that have additional alloys (chromium etc.). Or you are making a big-ass honking burr. The burr should be almost non-existent off your final polishing stone and then come off when you dress the flat side.
In some old texts this issue is discussed. They say to rub the tool against your palm to remove the burr. Then go to work.
My father an ex-pattern maker uwho used to slap a chisel too and fro on the palm of his hand to remove burr. I never saw any injury but I expect his palm had toughened up over a life time.
What a timely image for me as I’ve been meaning to ask about the card scraper. I have a crucible and am confused about re turning the edge. I followed your advice when I bought new, but once dull do I need to start over, or can the burr be turned over again with a burnisher?
The world is split on this question.
When the scraper stops cutting, I start over by turning the hook up and hitting the stones as per our instructions. It’s a three-minute process and you end up with a strong and consistent hook.
When I try to turn the hook on a dull scraper the results are inconsistent. And it takes about 3 minutes to do the operation. And the hook is weak and inconsistent.
Your choice.
Thanks again! I really enjoy you sharing your time and knowledge with us.
Hide glue. I live on the Yucatan Peninsula, where it is always hot and humid. Tight Bond seems to take months to fully cure. I have yet to make a batch from granules, for lack of a thermometer. Generally speaking, any thoughts on its use in this type of climate? All of the old furniture we’ve purchased was put together with it.
Thanks for doing this
When the British Empire went colonizing in the tropics, they found that their furniture fell apart due to heat, humidity and insects.
So they invented campaign furniture. Glue is used, but the pieces use A+ joinery and metal hardware to keep things together.
Hide glue is difficult in tropical environments. But it will work (as long as the heat doesn’t reach 60° C (140° F)) and you keep it away from water. It will take time to fully cure (because of the humidity). But it will cure and it will be fine.
Good morning from California! Have either of you worked with eucalyptus before? Besides smelling amazing, I’m curious if it would work for casework or (even better) chairs. Always appreciative of what you do! –Jake
Yes. It has the most interlocked grain I have ever encountered. It’s soft. Tears out every which way. I’m not a fan.
There are lots of different kinds of eucalypts, but every one I’ve encountered does not want to become furniture and will fight you to the death.
Then firewood it is! Thanks so much 🙂
Do you have special techniques or jigs to keep an even grind while using a hand grinder? The one Hayward suggests in his book? I have sometimes slipped and created multiple facets on a blade. Not good. Thanks again for all you do and create!
I do not have any grinding jigs. Never have.
The best investment is a $10 chisel from the home center. Practice with it until you get an even grind. It takes some time on the grinder, but it’s not a hard skill to acquire.
You end up with the skill and a tool that you can use for rougher house-based stuff.
Frank Klauz has a video on hand tools where he uses his finger as a perpendicular guide while grinding a chisel. Might look for that if your needing a visual reference.
Thank you as always for spending your time hosting this. What’s your guys’ preferred size for a smoothing plane? And in what scenarios do you go for a smaller size such as a 3, or go for a wider or longer size like a 4 1/2 through 6. I think I remember someone talking about turning a no 6 into a budget panel smoother, I might be misremembering the name exactly. But essentially a long and wide smoother, not sure what that would be beneficial for though. Thank you and have a nice weekend.
I’m going to drop all pretense here. “Big” smoothers are a dumb idea.
I want the smallest smoother that fits my hands and has a chipbreaker. Small planes do the job faster because they aren’t trying to flatten the panel. The plane that does the above things for me is a No. 3. I wish a No. 2 fit my hands.
Look at old tools that were used for a living. The smoothers are small. This isn’t a new or radical idea.
The 4-1/2 and bigger “smoothers” are simply modern and beautiful ways to part you from your money. Lame-headed ideas cooked up by people at their computers – not the bench.
No fuss, logical, and straight to the point. Thanks you very much!
Or maybe a custom batch of gummie glue. Thoughts?
What’s your favorite pie: Apple, Blueberry, or Pumkin?
Honey vinegar. Hands down.
Hunh?! What in tarnation is that?? (And do you have a recipe?)
Hunh?!?! What in tarnation is that?! (And do you have a recipe? Or is this sarcasm that I’m missing 🤒?)
It is perfection.
https://www.cincinnatimagazine.com/forkopolisblog/vinegar-pie-o-pie-o/
Recipe:
https://www.midwestliving.com/recipe/honey-vinegar-pie/
Good morning. I have two questions:
1.) Do you have any plans to release a crucible compass like something akin to your dividers? I’ve become increasingly frustrated by commercially available ones and I feel like the Starretts are my next option.
2.) Do you think the 18” woodowl auger bits would be beneficial at all for stick chair mortise drilling? I was thinking it might be good for drilling through the arm bow for the mortises for the sticks in the seats and make lining them up a bit easier.
Hi Clinton,
1) Probably not. We can’t do any better than the Starretts. So why bother?
2) I’ve tried them in chairmaking and they make a mess. Their flutes cut to the side and if you move slightly, you destroy the arm….
In a recent substack you mentioned people you referred to as monks, and I’m curious to learn more about their order. Their work resonated deeply with my own aspirations (finding a way to eek out a living woodworking while also researching and exploring). Do you have any names or books you could point to where I could learn more about these folks?
I wish there were a book!
Check out the work and life of Robin Wood in the UK. And his daughter Jojo. https://wood-tools.co.uk/tools/the-robin-wood-axe/
Julia Kalthoff in Sweden: https://www.kalthoffaxes.se/
Their lives are dedicated to research and production. And they stay small. They are a couple of the people I have always looked to for guidance on business….
Thank you so much!
Are there any armless stick chairs out there? Like side chairs for around a table? Do they have a structural issue or is there another reason I’ve never seen them. I plan to replace all the mass market cheap chairs in my life one at a time, but I can’t fit arm chairs everywhere, am I headed in the wrong direction?
I have a couple in “The Anarchist’s Design Book.” They definitely exist in the wild, but are usually called “backstools.”
I think that each time you wrote about wedges, you specified oak. Is there a reason for not using other woods ( e.g., if one wanted walnut wedges to contrast with ash, or vice versa)?
I want stout wedges. Oak and ash are ideal. You can use other species, but they are going to be more fragile.
Good morning! While waiting a good while for a Lucian Avery inshave to become available, I purchased a vintage Marples Coopers’ inshave in excellent condition. Its radius is similar to the Dunbar scorp, but is closer to a C shape than a U shape.
Is this the right tool to saddle a stick chair seat? Understanding that radii vary, are vintage inshaves interchangeable with modern scorps, or did I just purchase a coopers tool that won’t get me very far?
If it’s the tool I think you are referring to, the bevel is on the outside? I have found this tool has the handles at the wrong angle for scooping a seat. My hands keep hitting the seat. But give it a try!
Thanks so much. And if there’s time for further clarification, here’s what it looks like:
https://www.dropbox.com/scl/fi/55xp01f7lho949bugcvjq/Photo-Aug-26-2023-9-55-12-AM.jpg?rlkey=36fiwfarwjw6vkyk6otrbeh1i&dl=0
Chris…thanks for the additional playlist last week, it was great. I really enjoy both of them when working in the shop – shop karma from Covington! Now if we can just work on Megan’s “anti” playlist and maybe even one from the man behind the curtain (John H.)…safe travels to Amana next week.
Good morning Megan & Chris.
Three easy ones for you today . . .
1. For the stick chair what is the correct inside width of the arm bow?
B. When using the Lee Valley dowel maker, how far from the end do you stop feeling the stick?
7. Are updated drawings available? (The ones I have are for a 6-stick back and 3-piece arm bow)
Thanks and have a great day.
Enjoy this question and answer format very much.
Hi Paul!
B. About 8″ from the end.
Is it time to move on from hide glue and stick with (ha!) irreversible glues? Will my hide glued pieces face the same fate as British campaign chests in India as Detroit starts to feel more like Dharmsala?
I have faith that no, that will not happen. If it does get to 140° (F) I probably won’t be worried about the furniture….
Hey there
I’ve got a pile of linden. Is it a good idea to make a Gibson chair out of that wood or would that be too soft?
Thanks a lot and greetings from Switzerland
Linden is strong enough for a chair. I would use it for the seat, arms and backrest. Legs and sticks are best made from oak. And you won’t need much…..
Do you have any plans/musings out there for an Anarchists Adirondack chair?
Haha! No. It has been perfected by so many other people, I couldn’t add anything to it (except a big red A). I like the ones with curved backs.
Hi. Followup on my question on CBN last week. I bought one for my Worksharp 3000. I have the table accessory ( no longer made) and grind using an Eclipse style jig. The CBN really runs cool, no heat, unlike sandpaper. Got the 80/180 wheel. I think the aluminum core acts as a heat sink.
Hi Chris and Megan, I’m interested in understanding how you achieve such a clean straight transition from the flat edges of a chair/stool seat to the saddled ‘interior’. My own beginner efforts on various stools tend to leave an untidy and uneven transition (essentially, a wavy boundary line) between the edge of the seat and the excavated centre.
I have a perfectly adequate set of chairmaker’s tools and the blame clearly lies with me, the workman.
Do you have any advice on techniques or tricks that might help me with this?
It takes time to learn the hand control to cut the transition with a travisher. I nibble as close as I can with a scorp and then swoop along the line with a travisher. I use the curved blade to create a curved track parallel to the line. Then I inch the tool toward the line, following the track I made.
You can also make a template and use a bullnose router bit to cut the transition. That’s what I sometimes do for a real modern look.
Thanks. It seems like there’s no special secret. I just need to become a better woodworker.
Hi Chris & Megan, and thanks for taking this time for our questions. My shop is an outdoors, non-climate controlled shed, and by necessity that’s also where I store my stock. I’ve described my set-up to some folks and they’ve freaked out about my pieces having problems with wood movement when they’re moved indoors. (I live in central Maryland, with moderate to high humidity most of the year.) My take is that people have made furniture for thousands of years before central heating, much less AC, and that as long as I take appropriate measures (right grain direction, figure-8 connectors or buttons for tabletops, etc.) the pieces should outlast most of us if they’re otherwise properly cared for. Am I on the right path? And is there anything in particular I should be doing to account for movement?
(FWIW, my shop 2.0 is going to have a dual split unit because the summer heat is now beyond unhealthy into dangerous. But that’s a year or more out.)
If your stock is kiln-dried, you have eliminated a good deal of the problem. Kiln-dried stock tends to move less compared to air-dried stock.
Otherwise, just be smart about it. If the piece is going into a place with forced heat, prepare to have to adjust the doors and drawers after a season or two. The enemy isn’t the wood or its movement. The enemy is climate control.
You also can use quartersawn lumber to help reduce movement if it goes in a climate-controlled place.
Hope this helps.
Thanks! I do indeed use kiln-dried stock. And thanks for the tip about doors and drawers.
When is your next chair class with an opening
I’m afraid you have to be ready to sign up when they go live; they sell out immediately. But do get on the waitlist; we often have a slot (or two) to fill.
Hey friends! Always appreciate your answers. Quick DTC questions: I am referencing the 2021 Fine Woodworking article and don’t see that there is info on where to put the fixed shelf. Eyeballing it I could see it being around 10″ to 14″. Do you have suggestions on how high (referenced from the bottom of the side) you’d put the shelf? Thanks!
The bottom of the shelf dado is 10″ up from the bottom end. Or 9-1/2″ or 9″ if you want a little more height in the front of the top section. Base it on what tool will be nestled against the front of the top section. I use 10″.
Good morning,
I have 2 unrelated questions:
1: What shoes do you wear in the shop? I dropped a chisel on my sandaled toes once and it’s not an experience I’d like to repeat, but I go in and out of the shop a fair bit and we’re a shoes-free house…
2: If I want a contrasting drawbore/mortise peg in ash are there any good options? I know oak and ash are preferred.
Thank you!
Hi Josh,
The leather uppers stop chisels. I know this.
Hi Chris. Thanks so much for the reply.
I have defaulted to tennis shoes too – glad to know I’m not alone.
I’ll see if I can find some locust but otherwise will try my hand at dyeing some live oak I have.
All the best,
j.
I wear Birkenstock clogs in my shop. They’re easy to take on and off and protect my toes from chisels and are oh so fashionable.
Hi Megan and Chris, I liked the cordless drill we used in class and would like to get a good quality one for myself. I’m finding a lot of options online and not sure what’s best – what would you recommend?
We like the Dewalt XR 20V “Max” – just make sure to get the one with a metal chuck (much better than the plastic chuck) #neversponsored
Can I flatten a benchtop (say, a Nicholson) to be good enough for handtool work with a number 5? Or should I start looking for some overtime to work and save for something a little bigger?
Hell yes you can. It just might take a few extra strokes to get there. Winding sticks and a long straightedge will guide you.
Awesome, thanks…cools are tool but free time is cooler
Hey LAP,
Thanks for doing this. I now have a list on my workshop wall for LAP Open Wire questions.
If a rank novice chairmaker has a Windsor Workshop travisher and was going to get either an adze or a scorp which tool would you recommend?
Thanks
Neither. Use the travisher with the blade set rank and you can do the work of a scorp and adze with ease.
If you have to buy a tool, I get along better with the scorp. I’m not an axe guy.
Hello, and thank you for your time! I have been planning to build the Anarchist workbench. However, I must be able to remove the bench top as it is going in a basement with a narrow stairway. Do you have any new ideas or thoughts on a stable, way to attach the bench top. Any further thoughts would be appreciated.
Easy. Don’t glue the base to the top. And instead of drawbore pegs, use large lag bolts. (If the fit between the base and top is tight, you might not even need bolts…..
For Chris: In a previous blog you showed a book case with bracket feet. Any published dimensions on this? Can you direct to me to the pic you posted? I cannot find it.
thanks and regards,
Les
It’s called the Monticello Bookcase. The plans were in Popular Woodworking.
https://www.popularwoodworking.com/projects/monticello%E2%80%99s-stacking-bookcases/
thanks Chris.
Best.
Les
I was only able to get 6/4 stock for my arms/combs on an upcoming stick chair (finished currently about 1 3/8”) – I have no thickness planer – would it be too off proportionally to have this thick of an armrest compared to what the plans call for? (7/8-1”) ?? Thanks!
By the time you plane it down, you’ll be in good shape. Bevel and shape the arm to hide its chunkiness
Thank you for the response!
You have commented in the past that you use a common angle for sharpening most chisels and planes. In the spirit of your Earlywood post could you share a numerical answer to what that number? Saves me a lot of time searching and doesn’t take much of yours.
Everything is honed and polished at 35°.
Thanks, especially for the extra words. This makes the angle jig simpler.
Hi, Chris! I’m ready to build the staked armchair from ADB but I live in a city so it would be a search to get firewood to steambend the back. Do I have other options? Is it mainly to saw it out of thicker stock? Side note: I live in an apartment which is where I do all my woodworking, and the staked armchair seems very doable for my first foray into stick chairs.
I’ll be at Handworks next week. I am excited to meet you and Megan in person!
Sure. Saw it out of straight, thick stock.
Hello, I have a clarinet that was damaged while playing down in the pitt for a musical.
several nickel silver key posts were torn out of the wood (mpingo or grenadilla). I am going to repair it, what glue or epoxy mix would you recommend to build up the outside of the tube to replace the posts.
I’m thinking it will need to set up hard enough to re-drill the screw holes for the posts.
Hi Jesse, I have zero experience repairing musical instruments. If it were me, I’d call an expert for advice.
When thereaded wood gets torn up, I usually patch it with more wood, drill and then re-thread. But with a clarinet? I’m out of my depth. Sorry.
I’m working on a small Moravian workbench (4’x2’)right now, so that it will fit in the back of my car to take it to job sites. I’m using tamarack 2x4s for most of it, but am wondering if it would be worth using something like oak or ash for the stretchers? Also, do you know of (or sell) any good resources on making a wooden vise?
You’ll probably be fine with all-tamarack. As far as making vises go, just get a threadbox (the good ones are from Germany and sold by Dieter Schmidt. They are expensive, but actually work (as compared to many of the cheap ones).
https://www.fine-tools.com/gewind.html
Once you have the thread and the nut, then it’s just like making any vise. Chop. Parallel guide (if you want one). Garter (if you want one).
Thanks! I’d seen those threadboxes, good to know they work! (Though I probably won’t be getting that 2 threads per inch one anytime soon🤑)
Good Afternoon Chris and Megan,
Thanks for taking time out of your day to answer questions again. I wanted to get your thoughts on re-grinding a primary bevel on A2 steel. I had listened to a woodworking instructor warn against dry grinding A2 on a traditional bench grinder, stating it was more sensitive to heat when compared with carbon steel varieties. I wanted to see if this was your experience or if you had any specific strategies to avoid affecting the temper when grinding A2 chisels and plane irons.
Thanks,
Jacob
I grind A2 all the time on a #80-grit dry grinder. Grind for four seconds, cool in water. Repeat.
I have been told the same thing about A2, but I haven’t found the data that explains it. If A2 had to be water ground only, I would give up like a bad job.
Regular cooling in water is ideal for ALL common the steels I use. Keep it cool and you’ll be OK!
I built a stick chair using the LAR video and templates. The shoe hits me across the back even after I eased the top edge. I used the template to locate the holes, but should I move them forward for the next build?
Haha LAP video and templates – can’t blame that one on fat thumb…
If you can move them forward without drilling through the front edge, yes. And reduce the thickness of the shoe. It can be a thin as 1/2″, which will reduce the instrusiveness of the shoe.
Will do. Thanks!
I know you’ve answered this before and I can’t find it…
Finish for a bar top? I usually use oil, wax, and / or shellac but I think this needs something more water tolerant.
There is “bar top” finish, and it is as ugly as solidified urine.
Conversion varnish is as tough as nails. If you want to go high-tech.
Wiping varnish (lots of thin coats) is a great water-resistant, low-tech and time-consuming finish.
Food for thought: Our oldest bar in Cincinnati (at Arnold’s) was finished with shellac. It has been repaired over the last 175 years, but still look great.