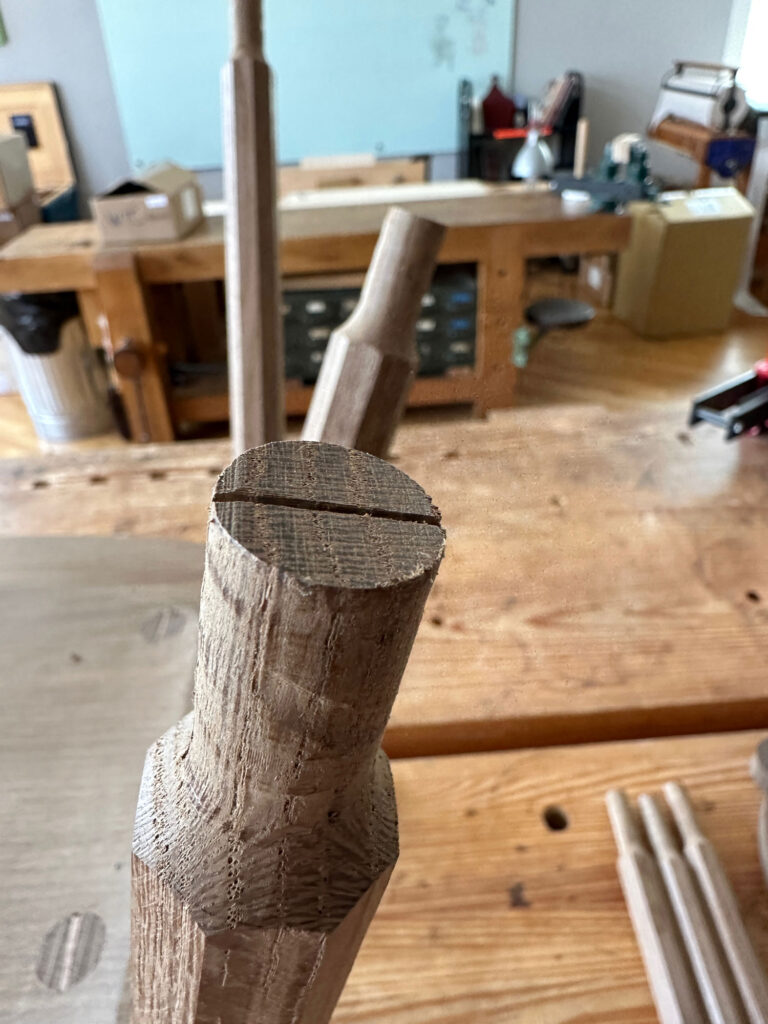
One of the biggest hurdles chairmaking students face when making their stretchers and sticks is drilling the tenon on the end of the stick. I use the Veritas Power Tenon cutters for this. And we do it freehand with the cutter in a drill.
So some skill and practice is required.
(Yes, I know I can mount the tenon cutters in a lathe and build a platform for the stick so the tenon is perfect every time. A lot of students don’t have or want a lathe. And my goal is to teach this craft with as few tools and jigs as possible. Why? It’s just how the Grasshopper God made me.)
Some students get the feel for it after a few sticks. One student burned through – no lie – more than 30 sticks, and he still didn’t get it right.
I’m always asking other chairmakers for tips on how to teach people to use this tool. From my own experience, here are the important steps:
- Level the stick in the vise.
- Level the tenon cutter using its bubble level.
- Press firmly forward.
- Advance steadily, and check to ensure you are still level and the cutter is perpendicular to the stick.
Chairmaker Travis Curtis offered this helpful suggestion: Try to observe the whole operation – don’t narrow your focus to one small area in front of the cutter. This will help you steer straighter.
It’s like driving a car (or cutting with a band saw). If you look right at the pavement in front of the hood, your steering will be erratic and you might squish the Grasshopper God inadvertently, bringing shame and a 20-year curse on your house.
But if you look a mile ahead of your car, your steering will be steady and smooth.
This is a helpful tip. But it didn’t fix everyone’s problems.
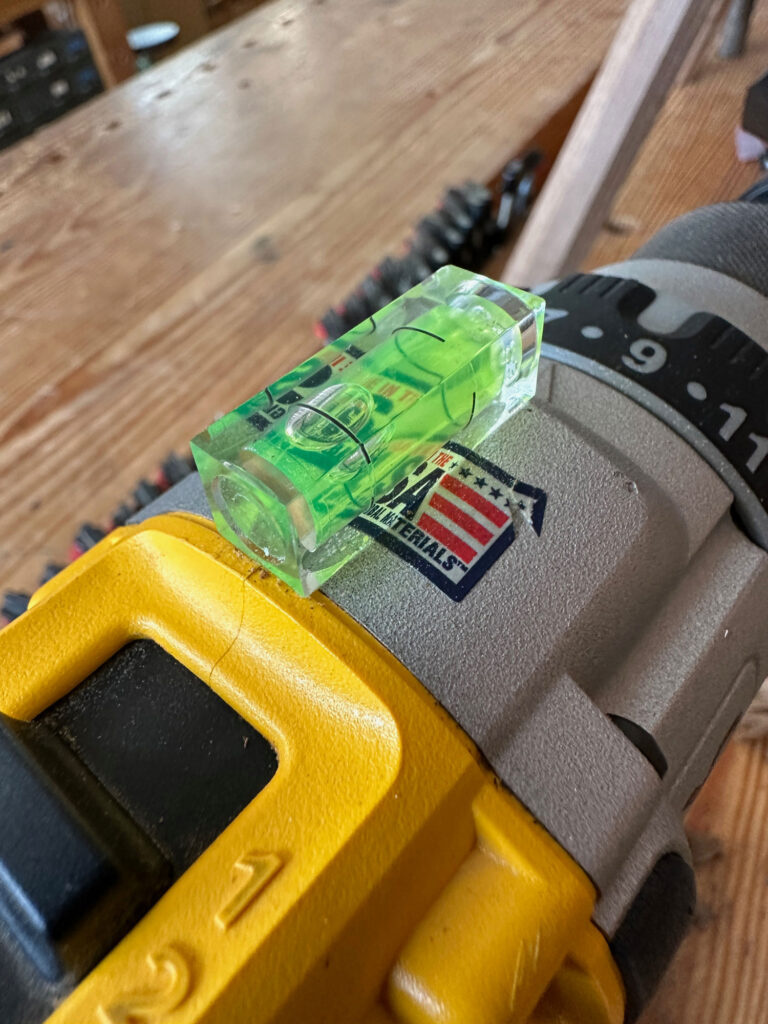
Then Derek Jones taught his Cricket Table class here a couple weeks ago and he modified all my drills by gluing a bubble level on top of each one. (We have an entire drawer of individual bubble levels; you cannot buy just one.)
These bubble levels make the tenon-drilling process even more predictable. You can’t see the bubble level on the tenon cutter when it is spinning. But you can see the one on the drill. So you can make fine adjustments as you drill and observe the entire process in your field of vision.
Like this:
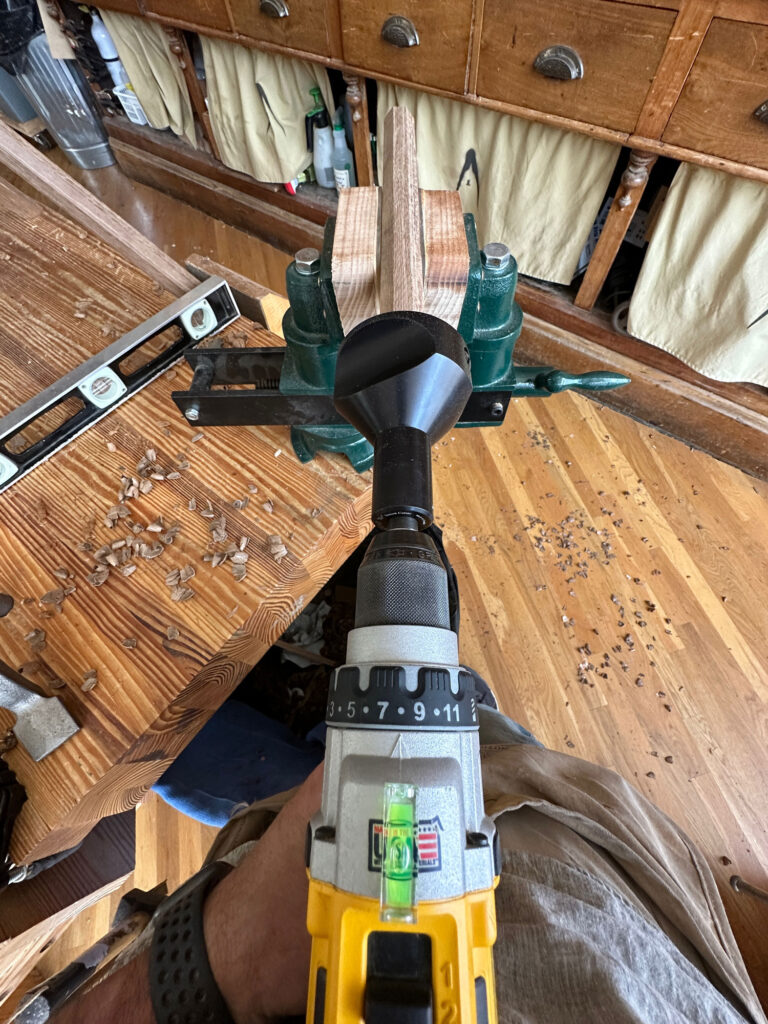
I love solving a problem using the brains of a bunch of people. Give this a try if you haven’t already.
— Christopher Schwarz
Chris, what size cutters do you use in your chair making.
5/8″, 3/4″ and 1″
Thx.
CD
If you are using a lathe, why do you need a platform? Can’t one use centers on the head and tail stock?
The way I read it Chris is talking about using a tenon cutter WITH the lathe. So unless you can feed the stick through the headstock (either small stick or BIG headstock) and hold it with a chuck you’re going to need something to support the far end of the stick while you feed the tenon cutter in via the tailstock advance. If you plan on cutting them free-hand on the lathe (or with a depth guide) then you can do it between centers.
platform is for those of us with access to a lather but whom haven’t mastered the scraper or skew to cut a clean tenon of consistent dimension. the shoulder bit mounts in the headstock and the custom-sized platform/box is bolted to the rails at the correct height so the leg center matches with the lathe centers. there are rails on the box so that the leg stays centered. then you hold the piece down by hand and carefully advance the tail stock crank to cut the tenon. kind of a two-person job, but it’s a low-skill way to to get centered tenons. [so long as your legs are accurately dimensioned]. it can get a little sketchy if you try to pull back during the process — since the bit is in a chuck with a morse taper, it can dislodge if pressure isn’t maintained.
There are some additional tips here: https://edsutton.substack.com/p/better-than-sex. Widening the focus might have much of the same effect as Ed’s pointer rod.
So the grasshopper god is a false god, but the cricket god blessed you?
Discovered this a while back. The hot-melt glue is kind of fragile and needs to be refreshed from time to time.
Use E6000
Finally, a use for all the little bubble levels my junk drawer collected. This has been a pain for me with the tenons, excited to try this out!
I assume you’d need to align the bubble level with the chuck of the drill. None of my drills have a flat spot inline with the chuck, so that could be tricky. Still VERY useful though.
If there isn’t a perfectly level spot on the drill, you can still use the level in the tenon cutter to get the drill to level. Then, as long as the drill’s bubble isn’t pushed all the way against one end, keeping the bubble in the same position will keep the drill level.
A thought I just had. When working with someone who is having trouble with the horizontal alignment of the drill and stick (assuming they have the vertical aligned with the levels), could you use your handy green laser to project a line down the center of the stick and down the top of the drill?
Yup. This is helpful on tapered or shaped work.
The first tip reminds me of Bruce Lee (Enter the Dragon?), “like a finger pointing away to the moon” and when the student looks at his finger, he smacks him on the head “don’t concentrate on finger or you will miss all of that heavenly glory”
Whatcha doing with all them extra bubble levels.
We needed one. You cannot buy just one.
You can buy mason string levels in pairs for $5-ish, though they are long (~2.5″ for the vial without the additional housing).
I admit to being challenged drilling centered tenons . My workaround was to cut a square tenon on the bandsaw about 1 mm oversize and round the corners off with a rasp .Then use the Veritas cutter with a handbrace to create a nice round and centered tenon . Takes a few more steps but helped me over the hurdle of wonky tenons
For some reason this post reminded me of my dad and his many brothers (who were in construction their whole lives) always telling me from eye that something was out of plumb or low in area or something else that my eye just could. not. see. yet they could not un-see. Thankfully, my “eye” has improved (though not precisely calibrated still) but such skills are tough to teach or explain and frustrating to learn until it “clicks”. Thanks for sharing some of the things that help.
Oh the ignominy of the “30 stick” student!
Somewhere along the line I picked up one of those heavy duty Milwaukee drills that plumbers use to rough in houses . Anyways it’s long straight and really slow with lots of torque. Kinda helps cause it’s note odd ball shape like some cordless drills are. Probably can find them pretty cheap cause they are corded and nobody wants that stuff anymore. Take care everyone enjoy your Friday 🙂
I took Derek’s class summer and he had us cut the tenons with a rasp and check them with a test mortise. I am making a Low Back Stick chair today and used the rasp, took about five minutes per end. I am retired and I follow the suggestion from my mom to my dad, “I married you for the rest of my life but not for lunch, get the hell out of the house” I’ll skip buying the tenon cutter and take the extra time in the wood shop.
One thing I observed in your class, Chris, is how you shift the weight forward. It’s something that helped me get more consistency and start to improve the result. This reduced (still working on eliminated) the deviations introduced by arm movement or shifting weight off the axis of travel.
Shifting the weight from the hips while holding the rest of the body “rigid” really made the difference. That meant I had to play with the stance, feet position, etc. It reminded me a bit about learning how to saw a straight line.
From my very limited experience, body mechanics were key to improving the results. As someone who sits for a living, developing hip mobility is not an easy task. Making a conscious effort to pay attention to how my body moves during the operation helped connect the dots.
I use a brace with a hollow auger for 1-11/4 tenon’s and plug cutters for the small ones. I glued a couple magnets to a little level. My brace has a chuck that is straight not like some that look like a bulb. I put the level on this straight chuck. This works good for me. I get to trigger happy with a electric drill.
I’ve considered using a bubble level like this, what I’m not sure about is the placement of the level on the drill. – how do I know if its referencing what I want it to?
Put a bit in the chuck. Put the bubble level on the bit (a spade works great). Level the drill so the bubble reads true. Remove the level from the bit and find a spot on the body where the level also reads true. Connect it there.
I have found that using a 10″ drill bit extension helps students’ better sight along the line left-to-right. We then use the mason line levels mentioned above to rest on the extension while it is spinning to visualize up/down alignment.