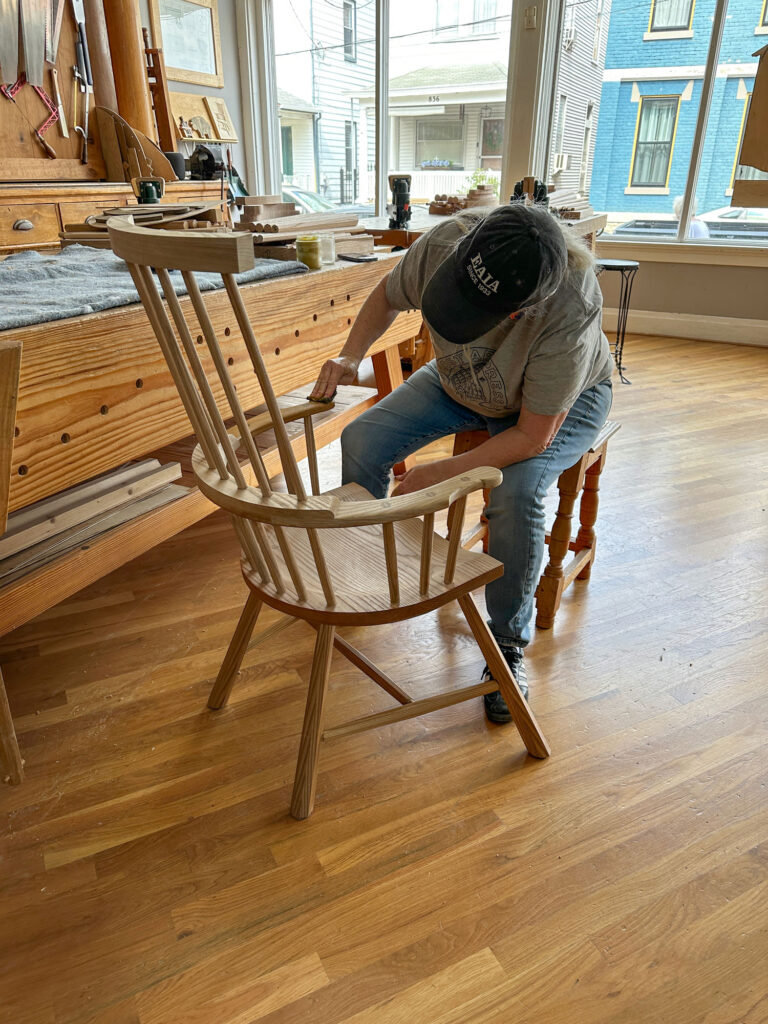
Sorry we took last weekend off. It was unavoidable.
We are here today and happy to answer your questions about woodworking, our books or Wilco songs.
This week’s open wire is hosted by me and Megan. Here’s how it works: Type your question in the comment field. Brevity is appreciated. We will attempt to answer it. It is that simple.
So here we go…. Note that comments for this entry will close about 5 p.m. Eastern.
Comments are closed for this Open Wire. See you next week.
— Christopher Schwarz
Will you be collecting tools for the fall classes? If so, what would you like? What did you think of the Eclipse trammel points?
That’s up to Jerome. I have raised the issue with him, and he is thinking about it.
I haven’t gotten to use the trammels (thank you) but they are in my tool kit to use when I make my next peasant piece.
If you weren’t concerned about drying time, which would you choose between linseed oil paint, faux milk, real milk paint? Thank you.
I like them all, for different reasons. Drying time isn’t the issue with milk paint (well, it is…it has to dry completely between coats, and it take s a lot of coats); I like the dead-flat look of the milk paint. Linseed oil takes a lot of time to dry, but it’s usually just one coat needed. The faux milk paint is a nice matte finish, and dries quickly enough that I don’t worry about cat paw prints and dust.
Depends on the look I am after. How it looks and wears is more important than drying time. And it also depends on what the customer is willing to pay for. (Real milk paint is labor-intensive; the other methods aren’t.)
Right now, I love linseed oil paint. But it’s difficult to put it on chairs because of the drying time. But I will…..
Thank you as always for offering this platform and spending your time answering these questions. Do you have any suggestions or guide lines on gluing up a construction lumber workbench top on the cheap? I’ve read about picking the lumber it self but I was curious about how few clamps I can get away with(and what clamps), and if there’s a tangible difference in performance or longevity on a “name” brand clamp and say the harbor freight version. I saw Rex Krueger using 2 or 3 for a work bench glue up utilizing cauls, but it was a narrow roman bench, do you think something like that would translate well into the larger glue up of a robou style bench? Small side questions, whats your preference for marking pages on a book? Post its, book darts, dog ears? Thanks a lot, and I hope you have a nice weekend.
Hi Kole,
Lots of people will disagree with me. So take this with a grain of salt.
Don’t buy cheap clamps. They don’t last. If you buy clamps with care they will last your entire life. When I started out, I saved my change and bought one clamp at a time, either new (Bessey) or used (Hargrave or similar).
When I had only three or four clamps, I would just work slower. Instead of gluing up four boards, I’d add one board at a time. And I’d fuss over the joints a lot more. Now I have about 100 clamps (it took 25 years) and I can glue up almost anything in one go.
When marking pages in a book, I use little ripped up pieces of paper. I’ve had too many bad experiences with anything with an adhesive. I have dog-eared books (I’m not precious) in a pinch.
I built a roubo-style bench by stacking the dimensional lumber on its face to make a thick benchtop. Since I only had a few clamps, I used 3 1/2 decking screws with fender washers under the heads. I placed them every 8 inches or so in two rows along the length. The only downside is you have to go one layer at a time. I could only grab a half-hour of shop time here and there anyway, so it was perfect. Pre-start the screws into the board before the glue, and you can bang them in very quickly.
I am wondering if Megan uses Soft Wax on the inside of tool chests she builds.
I’m sure Megan will be around here shortly….
I don’t like to have any finish on the interior. If I did, I would use a high-solvent wax (soft wax 1.0), which does not contain linseed oil. Or shellac.
It depends. If I’ve used a “showy” hardwood for the tills, yes – but only on the tills and other tool-storage bits. I don’t use it on the case; no need. No need for it on the storage bits either, but it brings out the color and grain nicely.
I completed the gibson chair and the angle of the back sticks is 30 degrees which tends to make the sitter feel like he is sliding out of the chair. In the video you state the angle is 25 degrees. would that angle make the chair more sitable. Thanks.
I misspoke. It is 30°. You can try 25° if you don’t like the 30°. I love the 30°. But everybody’s a different shape….
Do you have any recommendations for reading on hide glue and its behaviors or general practices for its use? I read The Glue Book on Project Gutenberg. I found somewhat helpful. I am curious about things such as clamping time (various internet sources say 4 – 24 hours, but you can do a rub joint for a 3ft panel in seconds…), how important is cleaning the pot out at the end of the day to keep glue strong ( I know it denatures above a certain temp, but what if you keep it at a safe temp for a very long time.), other things too. Thanks!
Hide glue information is like sharpening information. There is a lot of it out there. And it is confusing. The good news is that the glue is resilient and not terribly fussy.
On your specific questions. Clamp time. In a complex glue-up, I remove the clamps after an hour. Don’t stress the thing for a day. Simple rub joints need almost no clamping. Drawbored joints need no clamping. Hide glue gets its initial tack by it cooling and reaching its gel point. The rest of the bond is completed through evaporation. Hence the conflicting advice.
On heating and cleaning. My advice is treat it like food. You wouldn’t heat up a piece of pizza 20 times and then eat it. You wouldn’t want to eat something from a filthy pot. You MIGHT not get sick. But there’s a greater chance of bacteria getting in there. Or you cook the stuff until it is gross and unusable. I use my glue pot like a double boiler. Make the glue in small batches in glass jars. Refridgerate them. Heat them up in a water bath. We use so much glue that I never throw it away. But I would when it begins to smell. Wash the glass jars in a dishwasher.
You can make your glue last longer by adding salt or urea (a salt). And this is just like food. You are making liquid bacon or hardtack.
I would love for someone to write a no-BS book on the stuff. And no, Steven Shepherd’s book (which is valuable) is not that book.
Awesome. Thank you so much for the information! That would be great if there was a book on it…
When can we expect the next issue of The Stick Chair Journal?
It’s about half done. I keep getting overwhelmed with current projects. I need a couple weeks of peace and quiet to finish it.
You are usually so good about defining terms when you use new ones. What is “peace and quiet?”
Not what we are dealing with now with the new building. Every day about three hours of my day is dealing with that project and new employees and new workflow.
Do you ever use your shop Finish recipe for furniture? How many coats?
Additionally, any news on books in the pipeline?
Sure. Lots of pieces in my house use that finish. Usually two thin coats. And I sand lightly between them. You can add up about six coats of you want more shine and protection.
On books: We are about to send Derek Jones’ book on cricket tables to the printer. And I am working on Matt Cianci’s book on saw sharpening and Andy Glenn’s book on ladderback chairmaking in Appalachia.
Thanks!
Any thoughts on using hemlock for stick chairs and benches? It is the cheapest wood around here.
Sure. Just use pieces with dead-straight grain, make sure they are completely dry. And beef up the pieces a little more than you would with oak.
Thank you! I hadn’t seen anything on hemlock on the blog here so thought I should ask. Thank you for doing this q&a.
What do you do with all the thickness planer shavings? I prep wood for one tool chest, and I have bags on bags. I give some to friends for chicken coops, sew some into my compost pile and I still have bags left over. Surely there’s a better use than just chucking plastic bags full into the city trash.
It’s a never-ending battle to find someone who will take our shavings. We have given them to farmers and community gardens. Right now we don’t have someone who can take it. I want to take them to the woods behind the cemetery and spread them out for the bugs.
We do sometimes throw a bag or two away. If anyone out there wants to take our shavings, let us know.
It is good tinder. Try Boy Scout troops
Not sure where you are, but around here they pick up our lawn clippings and leaves and such every two weeks. All of it goes in paper bags from Home Depot. I’ve put my shavings in those and they go with the rest. It all goes to the town compost yard.
Ditto for me.
I have access to some local red elm. What is its workability like with hand tools only, compared to ash? For chairmaking, that is. I can get it rough dimensioned. But I have no access to machinery. Thanks.
It is very similar to ash. Except you cannot split it because the grain is interlocked. So it would be difficult to saw out the sticks, legs and stretchers. Most chairmakers would use ash for those parts. And elm for the seat, arms and comb, where its intlocked grain is a big plus.
Wasn’t elm the wood of choice for wagon wheel hubs because of its interlocking grain? Seems Roy Underhill mentioned this once (though I have no idea why I remember this)
It would be great for a hub.
How do you prevent a finished piece from warping from humidity during shipping or transport to a customer?
Zack,
I don’t. And that’s because I sell chairs made from kiln-dried wood. There isn’t much wood there to warp. And if it does, it won’t warp as much because it has been kilned.
When I used to make casework for clients all over the country, I would only ship to places with a similar climate. Not a desert. Not a rainforest. And climate control. And you have to pick wood very carefully. Quartersawn wood for drawers. Rift for doors. Avoiding really flatsawn surfaces. And you can’t have insanely tight fits of your doors and drawers.
I am making a six stick come back chair, my first one. The arms are a bit thin and I oriented the grain wrong and both arm pieces have broken and I have re-glued them. What are your thoughts on adding a layer underneath that maybe tapers off towards the back, and then I sort of round over the front “hand” part? Or would it be better to find more maple (I am out of the maple I had) or redo them all together ?
You can laminate some wood on the bottom if you want to try to rescue the arm. But honestly, if I’ve had a couple breaks, it’s easier to start fresh with a new arm. If you clamp it in the same place over the seat while drilling you can use the same seat/undercarriage.
Many times repairs are MUCH more time-consuming and complex than just making a new part.
Hey guys! So now with the addition of the warrington hammer and a claw in the works is there any chance of something in the 8 to 10 oz range so all my hammers can be crucible?
Yes.
Hi Chris,
Imagine a frame-and-panel back, total size around 45” x 34”. Three stiles, eight rails.
The two outer stiles are 1-1/2” wide, and will be through-mortised for the rails.
The middle stile is 1-7/8” wide, and has rails tenoned in from both sides, meaning the max length of the rail tenons either side is a full 7/8” (to leave a little room in between for excess glue). All 32 joints are drawbored.
Based on your experience of casework, would you deem those 7/8” middle tenons long enough?
Or would you either (a) let them overlap in some way or other, or (b) say “sod matching the grain and colour on the stiles and rails” and make a wider middle stile from a rather different-looking board, or (c) something else again?
(Not in any way asking for a friend.)
Cheers,
Mattias
Hi Mattias,
The tenons are plenty long for a frame-and-panel back. You are deep into “overkill” territory already because of the number of joints and the fact that this will be attached to a carcase.
Thank you, Chris! I kinda though as much, but, ( guess because the width was limited by the available matching stock) this turned into one of those just-before-I-fall-asleep niggles that wouldn’t quite go away, no matter the amount of shooing. So thanks again, for as it were softening my pillow for me.
How’s the Anthe building coming along?
I’m going to do an update on Monday. Yesterday the first layer of drywall went in (this is all for fireproofing). Monday that gets inspected. Then the second layer and tape. Then an inspection. Then beadbaord. And an inspection. Then final electrical. And an inspection. Then a final inspection for our certificate of occupancy.
If the calendar of inspections holds we will be in by the end of August.
Correcting warped boards for a tabletop: I’m building a large tabletop from 10′ 8/4 cherry boards sawn from one tree. Half are somewhat warped, to the point that flattening would remove half an inch in thickness. Given that the ultimate owner wishes to preserve the thickness of these boards, are there any novel techniques to correct the bowing? One thought was kerfing, bending, and wedging. Foresee any big drawbacks? The bottom side needs to be reasonable flat to receive batons.
If you are willing to triple or quadruple the amount of time on the table, there are options. Me, I would adjust the design to use thinner boards that were flat.
If I had to do it, I would flatten the exterior faces and true the edges. Glue up the top with a wonky underside. Then I would dress the visible edge so it didn’t look wonky. Then I would build a base and shim between the base and wonky underside to deal with the gaps. And selective plane out sections to deal with high spots on the underside so there is complete contact.
Most methods of pulling a wonky board to flat are in vain. Wood always wins.
A couple years ago I bought about half a ton+ of mahogany from an estate sale. I got it unexpectedly cheap. Most of it dates from the late ‘50s and early ‘60s. Most of it is five and six feet long. It ranges from 5/4-8/4. Some 4/4.
I am a pretty raw beginner. I am very interested in chairs. I have been buying your chair books… the original as PDF, and I will buy the new edition as hard-cover. I am wondering if the mahogany is good in any part of the chairs.
Frankly, I don’t really know what to do with so much mahogany. I have been skill-building with shop fixtures on lesser wood. But one day I will have skills enough to touch the mahogany.
Also… I have been wanting to share this for a while… I love that goofy blue cap with the floppy bill! 💕
Also again… I just recently bought the divider. I am unexpectedly amazed at its hand feel. That is a work of functional art. As is the Warrington hammer. These tools feel so awesome to use.
Thank you for all you do. All of you.
Mahogany is fantastic wood. Old mahogany even better.
I have used it in many chairs, tables, casework. It was overused to the point where it is endangered. So pick good projects and use it wisely! It is strong enough for any stick chair design. Works beautifully. Finishes like a dream.
So you are quite lucky.
Hello again,
I recently realized that my attraction to woodworking is, in part, an attraction to design. I’d like to begin designing my own pieces, and while I intend to learn CAD, I know from other areas of my working life that working on paper is often good for my creativity. Do you have any suggestions for setting up a drafting workstation? Supplies, table, anything you might be able to suggest would be helpful. I took many years of drafting in high school, but that was a long time ago, and almost everything was provided.
Thank you!
Matt
You need a vintage pre-CAD book.
Try “Basic Technical Drawing” (MacMillan) by Henry Cecil Spencer. It is the classic, foundational text.
Who’s your favorite Blues artist; Eric Clapton, BB King, or Stevie Ray Vaughan?
Howlin’ Wolf.
300 pounds of heavenly joy
Yes!
Do you have good book(s) to recommend on framed chair? By that I mean not-stick chairs, with mortises and tenons as the main type joinery. I’m interested in dining chairs in particular.
All I can find are random projects, with no context whatsoever.
“Chairmaking & Design” by Jeff Miller. It’s the best book on framed chairs out here.
Is there a structural reason to only pinning the outside long sticks on a chair with the bamboo skewers or is this simply a design choice? (I would imagine pinning all of them is just unneccessary…?)
I’ve asked the same thing! Pinning the outside ones keeps the comb attached and in place if the glue fails. Pinning the rest is 5 (or 3, or…) opportunities to screw up. But you can pin the rest if you like the way that looks.
Design choice. Some makers pinned only the outside. Some did all of them. Some did three…..
Question about the Cornett chairs at Kentucky folk center. Comment first: Loved the center and what they are promoting there. Also freaked out my wife, I walked around the wall, saw the chairs, and said “those are Cornett’s!” She about fell over because I knew something about culture. Question: where the chairs back slats go into the frame. From the front of the chair, I noticed that the peg holding the slats tight seemed so low as if they were not going through the back slat tenon completely, it looked like he just caught the edge of the tenon. I don’t remember if that was on the other chairs too. Was that typical for him? Or was there some sort of element I missed (like the peg at an angle) As for holding the slat in place, it works obviously. Not sure how I exactly feel about the glancing blow of the peg as a design element (if that was it). Or if it was an order of operations for him, or if it was how he measured off the back splats. It was just interesting to see.
Thanks for the blog about Cornett and the Center
I’m afraid I don’t know the answer. I’d have to inspect the chairs again (it’s been about five years). Sorry.
Hi Chris & Megan,
My question is about drilling holes for staked tables. Without a drill press, what’s the most effective way to drill a 1.5″ hole at a resultant angle of 15 degrees? Last night I did 2 such holes in 2″ ash using a hand brace and WoodOwl auger bit. My left elbow is crying. What’s a better way? I realize there are T-augers but I seem to have trouble finding those. If there’s a electric specific drill / bit setup, I am all ears.
Thanks,
Louis
Chris typically uses a powered drill; 18 (I think…could be 20) volt DeWalt. But we have a plug-in electric drill, too, when needed.
You could break up the wood with a bunch of smaller holes and finish with the bit. Or switch to a square mortise and chop it out. Big holes were handled with T-augers. And muscle.
I clamped a drill guide when building a stick chair and it worked well
This question is for both Chris and Megan… In your time at LAP, what are you most proud of and what is your biggest regret?
I’m most proud of featuring more underrepresented woodworkers; I regret I wasn’t able to do more on that front
Ever tried Tru oil?
Not looking for advice — I’ve used it for decades — just don’t remember it being mentioned in finish discussions. Whenever someone says something about oil drying (curing) time, I always wonder, “why not tru oil?” Looks expensive on the face of it, but very high solids and saves a lot of time. (No affiliation. Just like the stuff. Tried all sorts of finishes, including tried & true. Mostly woodturning. Some cabinetry.)
Yes. It’s great. Gunstock makers love it. Jameel Abraham turned me onto it. I like to be able to make my own finishes from scratch, but it is one of the best out there.
Hi Chris, Megan,
I love my 12″ square but hate, detest the 32nd and 64th inch marks on it. I would love to buy a blade that has only 16th and 8th inch marks on it. Does anyone make one? If not, has Crucible tools considered making one or working with a vendor to do a limited run based on pre-orders? I would buy a few and pay much more than I should just so I wouldn’t feel annoyed every time I use the square. Thanks.
Sincerely,
Joe
We were working on one until these guys beat us to it.
https://taytools.com/products/benchmark-tools%E2%84%A2-rigid-woodworking-rulers?variant=39754819502167
Available in 6″ and 12″ lengths. Very inexpensive. Made in India, I believe. But good for the price.
Thanks Chris. Do you have a feel for how “square” it is.
Square?
Hi Chris,
I was referring to the beam for a square rather than rulers. I have those rulers from Tay Tools. I saw your blog on those a while ago and bought them. They are fantastic rulers and I use them all the time.
Sincerely,
Joe
If you’re looking specifically for a combination square without the 32nd and 64ths, they used to make them up until about the 1950s. Most major brands had some in 6″, 9″, and 12″. I think Starrett called theirs the “92 Carpenter’s Square? 8ths and 16ths on both sides. Millers Falls and Lufkin had 8ths and 16th on one side, and 16ths and 32nds on the other. Some lesser makers such as Bates had a version without the teeny markings as well. As did Craftsman, but I think those might have been Starrett made.
I’m a big fan of the 9” models myself.
I am working on finishing the insides of my first dutch tool chest. I am trying to figure out a good way of attaching the saw till to the bottom and/or back of the chest. I don’t really want to put screw holes in the back or bottom since it seems a little too drastic.
The saw till is two vertical ¾x5x5″ boards with 3 saw kerfs cut out. It is sandwiched between the plane dividers and the back wall. It stays put pretty well without anything; but I know I need to anchor the plane dividers and saw till somehow.
How do you attach your saw till and plane dividers to the walls and back/bottom?
If I had a book on Dutch tool chests I bet that would be under the chapter on bits and parts…
Thanks for your time… and being good sports with friendly ribbing.
Aren’t you funny. (That is indeed in the chapter on interiors.) I sometimes screw through the back, but I’ve also been known to pin it in place with a nail gun both through the back, and toenailed into the top of the shelf (bottom of the cubby) and through the plane till/dividers in front of the saw till, to catch it on the front edge.
Thanks for the tip on the older ones. I will have to go looking for them.
Thanks for the help. Found a vintage Lufkin that had 8ths and 16ths only on both sides on eBay. Delivered for $40.
Guitar builder here just looking for ideas other woodworkers might have. Specifically on how to easily hold the plates for guitars in order to thin them with hand planes: tops, backs and sides (typically spruce for tops and mahogany-like or rosewood-like woods for the backs and sides). These plates usually come from the tonewood dealers bookmatched, quarter sawn and about 4-6 mm thick, straight off the band saw. They are usually then jointed and glued (for tops and backs) and then need to be very carefully and precisely brought down to around 2.5mm, very flat, no tearout. Very few builders do this with hand planes. Most resort to a thickness sander.
My question: how could you imagine holding the plates for planing? The traditional way is to clamp each plate at two corners, plane across the grain or diagonal to it, and then move the clamps. Repeat until done. But this is a lot of clamping and unclamping. Any ideas for how to do it more easily and efficiently?
I have affixed thin pieces to the bench with hot-melt glue. Worked them. Then popped them off when done.
The issue here is that one needs to pick the piece up quite often to test its deflection or measure it or feel how much it’s bending. Gluing or taping it down makes that impractical.
When I have needed multiple pieces of something thin, I used a technique I saw from Paul Sellers in which I created a housing dado of the desired thickness using a router handplane. Then, glued some cyanoacrylate glue slightly wider than the hand plane. Took me all of literally 10 or 15 min to make the jig. Once the place stopped removing material from the over thick pieces, I was down to thickness. Would be a bit tricky but you might be able to do something like this and the pieces can be easily taken out of the housing dado. Would need some modification to the concept to make it work for you. Here is a link to my blog post that has a photo of it (4th photo down).
https://joeswoodworkingjourney.blogspot.com/2021/07/making-square-bench-dogs.html
Turners tape
I’m thinking of making a pair of Roorkhee chairs as outdoor furniture. With the realization that all outdoor woodwork eventually fails from sun and water I’m taking the approach of cheap(er) materials. I also plan on finishing with faux cedar paint for fences.
Since cedar 2x4s are really 1.75 thick I’ll probably laminate the legs with epoxy or titebond3 so they’re fully 2″ to handle my American body.
Finally I’m planning on using a canvas meant for outdoor furniture instead of leather.
Anything you’d do differently?
I’ve never used cedar in a chair or a Roorkhee. I’m sure it could be done, but I would probably use white oak with straight grain for the rungs.
Hi Chris, thanks for doing these open wires.
A question that came to mind recently, just from curiosity:
Are there stick chair rockers? Windsor rockers are plenty, but as far as I remember, I have never seen a picture or read about them.
Regards from Germany!
Leo
I have seen only one stick chair rocker, and it looked like the rockers were added later.
Rocking chairs are a pretty American thing. You’ll find them in other cultures, but not like here. So European vernacular cultures (Scandinavian, Welsh, Irish, Scottish etc.) are unlikely to have rocking forms.
So feel free to Americanize them…..
Have you ever stained a chair? What colors?What did you use for a top coat? Was worried about wearing through not that I really care per say was just thinking it might look like crap. Was gonna do green than a walnut with black wax. Oil stain. Oh put like 20 grams of vinegar in the glue seemed to help couldn’t smell the vinegar when applied.
I’ve been thinking about building an ATC for a while now and I might be ready to take the plunge. I’m in the Northeast and cannot get Southern Yellow Pine here. I also only have a six inch jointer so I’d want to use surfaced lumber. Is there any reason I can’t build it with whatever 3/4″ pine boards I can get at the local Home Depot? Obviously I’d still use oak or something tougher for the skirts and tills. I don’t need it to last for centuries, just the rest of my life.
White pine will work great — and I would not want to use SYP anyway! Far too heavy.
I have the same limitations so I used 6″ popular boards and laminated them together to make the panels.
I think Chris used white pine for his.
You mentioned keeping a screwdriver out while using the lie neilsen #48, for making sure the fence stsys jiggle free. Whar size screwdriver are you using?
I use a No. 10 Grace USA driver, which fits the slot snugly.
While making the Folding Bookstand from Chris’s article in the June 2018 issue of Popular Woodworking it mentions “You can buy a rivet-setting tool, or you can make one from a 1/4”-diameter dowel.”. I would like to consider purchasing one but am unable to locate what I picture as a one-hand tool to press from both ends, like scissors or more like a one-hole paper hand punch. Can you please suggest a make / model / vendor? Am using the #12 Hanson rivets mentioned in the article.
A rivet/burr setter looks more like a nail punch (but with a hole in one end). You set the burr on the rivet with the side that has the hole. Snip. Then peen.
https://www.weaverleathersupply.com/products/heritage-rivet-burr-setters?_pos=5&_sid=b6f544f65&_ss=r
Thank you, I see. But that particular tool seems to only push from the burr and not the rivet head. What about if the rivet head is recessed in a hole deeper than the head? That’s why I’m looking for a tool to squeeze from both ends. I reckon I’ll have to build a jig with a short post to rest the rivet head on while pressing only on the burr.
For a Schoolbox-sized box (10-11”x13-16” lid), I usually glue up 2-piece quartersawn for the lid and bottom. I have no QS left; rare where I am. In commercial kiln-dried Eastern White Pine (4/4 rough) am I in for long-term wood movement grief using flatsawn for tops? Will be stickered 9 weeks. (Thanks for the Open Wire!)
You’ll almost certainly be fine. White pine doesn’t move much in service. You could add some battens to the undersides of these panels for added insurance. But it’s unlikely to be needed.
Thanks : – ) And thanks for TJACM with Joel M. It spurred me to think about a progression of practical projects that build skills.
Can you recommended a simple set of quality wrenches, for use around the shop (thinking GoDrilla, router, etc.)? I think you’ve used Tekton, but I’d welcome any suggestions. Thanks to you both.
I love my Tekton. But I’m not a wrench snob. Maybe there are some out there….
Stahlwille
Good morning, afternoon all. Hope that everyone is doing well. Just a few errant questions. I’ve noticed many of the photos in your posts are exceptional (the balcony/roof tops photo during your recent trip to Europe was gorgeous). Aside from KSA (knowledge, skill and abilities), are these typically taken with you cell phone?
Was the hide glue naming contest ever resolved? I’ve only seen “Death Grip Glue” mentioned since.
Finally, received the Warrington hammer early this week. Oh, it is so, so nice…….
Thanks and have a great rest of the weekend
Hi Matt,
I use my iPhone for all photos. No filters or processing. For working in the shop (not in the field), I have a tripod that holds the phone. Modern “phones” are actually awesome cameras with one stupid accessory (the phone).
On the glue, we loved many of the names. But I think we are going to stick with Death Grip. We’ll still name a winner and send them some.
Glad you like the Warrington!
Hi folks – I’m finally embarking on the project of building a knockdown Nicholson bench per the PW plans. But somewhere (maybe in AWB?) I remember Chris saying that workbenches shouldn’t have lapped/screwed stretchers, and to use a tenon joint instead – in particular, a half-width (rather than centered 1/3l. Did I make that up? It sounds like a nice addition, including a drawbore, to try to learn to make work. My only concern is the order or operations to make that side assembly square… Fit the top plate but don’t glue, then measure for the stretcher, disassemble, mortise, assemble? Something else?
Thanks! I’m excited to finally be on the path for my own bench. I’ve tracked down some reclaimed Doug fir that should be lovely.
That project is designed to be used with knockdown fasteners and has compromises for its ability to knock down and be simple to build.
If I were building it to be bomb-proof, I would tenon the stretcher etc. in to the legs and wedge or drawbore them. The top plate would have twin tenons on each end. The stretcher a single tenon on each end. Then it’s just a straightforward mortise-and-tenon frame.
Hope this makes sense.
Thanks, yes, it makes sense; I’ve never built this kind of thing before so I’m trying to figure out the order of operations to achieve “can’t miss” squareness… I’ll still use the knockdown fasteners, but my intent was to have the “show stretchers” be tenoned and drawbore, just because!
Hello! Long time reader first time poster here. Love all the content.
Just as a suggestion. For the Gibson Chair video, it seems to me that the pattern maker’s vise and tenon/plug cutter are essential equipment.
These, in my uneducated opinion, are outside normal casework tools. I really wish the video description had elaborated that. It should have been obvious from your books and the trailer but for some reason I just did not think about it or really dig into it.
I’ll probably pick up the Veritas Tenon Cutter and Grizzly Pattern Vise over the next few months when my budget allows. Or make do with what I got.
I do have a tapered tenon cutter that I 3d printed and a reamer that I’ve used on some primitive staked furniture. I’m sure that would work okay for the legs. What would you suggest for doing the sticks efficiently? Maybe a smaller diameter for them so they would be easy to shape with a spokeshave and bench vise?
Sorry I’m not following the question. Shaping the tenons on the sticks? Or the sticks themselves?
The tenons need a 3/4″ or 1″ tenon. Shaping the sticks is all done with a plane. I knock off the corners with a band saw, but I don’t run them through any shaping tool.
Sorry if I’m following the question.
I was thinking about no taper on both ends of the long and short sticks. Just straight sticks for the short with the body of the stick being 1″ in diameter. Then I’d knock of the corners with a spokeshave to shape the tenon. The long sticks tapering to 3/4 but having a straight 1 section at the end.
Regardless of reply, I think this is what I will do. After all the origin of furniture styles can sometimes be attributed to the tools on hand.
Hi! One more brief question. Are there publishers or texts similar to your work, but for blacksmithing? My teenaged son is interested, and I’m wondering if there are any great places for him to start.
No clue. Sorry.
Thank you anyway!
Try “the skills of a blacksmith” by Mark Aspery. Volume one is fundamentals. No affiliation other than having bought and used it.
Thank you!
I am going to make the Curved-Back Armchair from The Stick Chair Book. I want to try making the leg tenons with the Veritas tapered tenon cutter, but have overthought the sizing to the point of confusion. Is the size they sell based on the cylindrical part of the tenon or some part of the conical section? Can you describe the sizing guideline for these cutters and or post a chart for which cutter goes to which tenon. Thanks for your patience.
The size refers to the smallest diameter at the end of the cutter. For chairmaking, the 5/8″ is best. It makes a robust tenon. I haven’t found much use for the other sizes in my work.
Hi. Stumbled on a tool to clean up grinder swarf, etc. Bessey Magwand MW-1. Do CBN wheels keep the iron cooler than traditional wheels?
No clue. I’ve used one and it was great. I don’t know if they keep the temperature down, however.
If you only had one vise for your bench, what would choose. Face, tail, leg, etc?
Leg, no question. In fact, a leg vise is the only vise on Chris’s AWB, Roubo and my Benchcrafted benches.
Chris,
Regarding the Comb-back with an improved arm.
How far does the top 1/8×1/8 champer come around on the interior of the arm bow hand?
It can recede into the shoe, which I do sometimes. Or you can end it 1″ or so from the shoe, which I do sometimes.
Thanks for your time last week. Visiting your shop was a highlight of the trip. I hope I wasn’t too disruptive. And the cricket table class looked fun!
Hi Chris,
I will soon start making the anarchist’s workbench from your book. I recently bought an 8″ bench top jointer to help the process. I’ve never owned or used a jointer before. Are there any tips, tricks or advice you would be willing to share on how to face joint an 8′ 2×6? It seems daunting to me and I’m slightly nervous about screwing this up. Thanks!
Get some things that help you with infeed and outfeed so you can focus on keeping the piece moving smoothly across the cutterhead. The stands should be coplanar to the tables or very close.
The tendency is to use way too much downward pressure, which can out out a bow or curve. Resist. The right approach is to use just enough downward pressure to keep the piece stable and moving.
Buy some every crappier 2x6x8s to practice on. They are cheap.
When I finish a furniture project I almost never feel like I made it. I remember making each piece and assembling them and then finishing all of the pieces. The gestalt seems to appear out of thin air regardless of my effort. “I didn’t make the thing, I made its parts.” It isn’t a negative feeling, just strange, like I’m looking at the letters instead of a word.
Do y’all ever have this experience?
I remember making the mistakes. Then hiding them. (Not joking!)
Have you given any thought to teaching woodworking to the young? With manual training all but gone in public schools kids are losing out, IMO, on vital life skills. You have reached out to the under represented already – I’m wondering if there’s not some opportunity to teach the craft to some adolescents that need a hand up in life. If someone were to start a scholarship to send a kid(s) in need to a good wood working school I would be happy to pitch in as I’m sure many others would.
We think about a lot of these things, and we are TINY almost insignificant company. We have to pick out battles.
Tiny perhaps, but definitely significant.
Look up Sloyd Experience….this is precisely what they do.
Does anyone know what happened to Chris Vesper? He seems to have dropped off the (bottom?) of the earth! I was lucky to purchase one of his bevel gauges, but would really like a smaller one!
He is currently spending his time in the world of upgrading band saws and other personal projects.
We all hope he comes back to toolmaking at some point.
See the post in his website from February of this year: https://vespertools.com.au/ordering-info/
If ya’ll have ever worked with old reclaimed lumber that was just rough sawn and that might have dirt in its crevices, what process do you use to get the dirt out? I don’t want to use a wire brush (for fear of embedding wire particles) but the dirt scratches my tools, of course, so I need to get it out. (It’s not stone grit, just dirt.) Do you just wash and then dry the lumber off? Thanks again for all of your kindnesses. I don’t know how to thank you enough.
A lot of people use a power washer to dislodge the dirt. I’m afraid I’ve never used reclaimed lumber that need that much help, I’m afraid.
Thank you!
Megan I thought about you and your house projects this morning when my wife and I started running T&G pine square joint boards on the ceiling of our future dining room.
We need to do that in the machine room, to cover up the new insulation
Chairs. For some reason, I fell into the realm of wanting to make chairs. Stick chairs in particular and the Gibson chair first.
Question is the importance of a band saw. How steep is the chair building process without the shop assistant band saw? And how big or small would it need to be?
Thanks for all you do. It’s appreciated by the rookies.
You can certainly do without a band saw. People did just fine for hundreds of years and did a fine job.
Chairmaking doesn’t need a big band saw. Even a little tabletop one like the Grizzly 9″ would be an enormous help in cutting parts to rough size.
https://www.grizzly.com/products/grizzly-9-benchtop-bandsaw-with-laser-guide-and-quick-release/g0803z
Hey Chris and Megan! Hope you guys are well! I have some street tree logs (23″ dia. ~9’ and ~10’ long elm) that I plan to mill up soon on my friend’s mill into some material for a bench build. I was thinking of a 2-3 piece benchtop and solid stock components for the undercarriage. I am just wondering if you have any recommendations on how to divide out the cants. Straight 5” thick slabs or more dimensioned pieces? Thanks for keeping the Q&A going, spinning out webs of deductions and melodies, on a private beach in Michigan. -Matt B.
Someone needs to strong arm Dave Fisher into letting someone publish his blog entries as a book. I don’t think I’ll ever carve a bowl from a log but I would buy a book on it if he ever wrote one just as a payment for the blog.