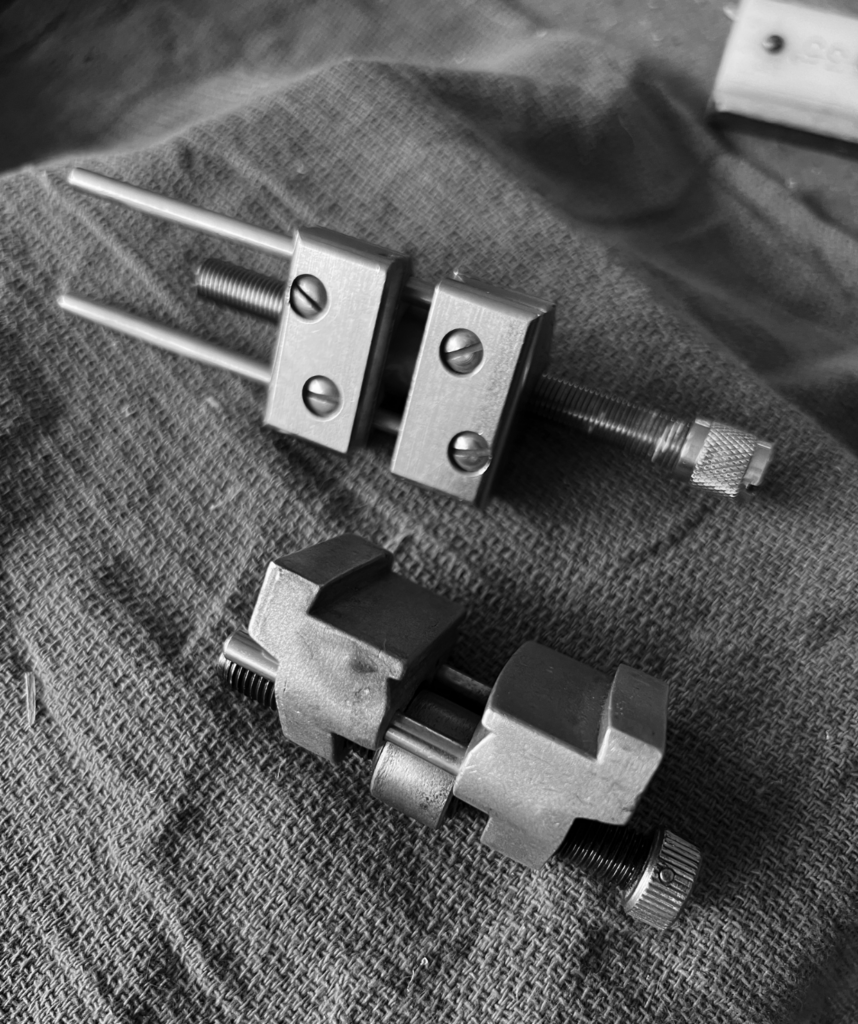
The following short excerpt is from Christopher Schwarz’s “Sharpen This” – a 120-page pocket book on how to get great edges, regardless of the sharpening system you choose. It is about what is important: Creating a sharp edge quickly with a minimum amount of equipment.
Simple side-clamp honing guides are a godsend for quick and repeatable work when it comes to chisels and plane irons. I do sharpen freehand a lot of unusually shaped tools, but when it comes to plane blades and straight chisels, I am happy to let the honing guide do the work.
Side-clamp honing guides can be had for a song – inexpensive ones cost less than $20.2 And I have found no valid downside to using them.
Critics of honing guides deride them as “training wheels” or as a crutch that slows you down. I have regularly challenged these people to sharpening contests for speed and fineness of edge – the winner determined by a judge who doesn’t know whose blade is whose. I have never lost – not because I’m a great sharpener but because the honing guide is an enormous asset.
While I do love my honing guide, my love has limits. I don’t use the endless attachments that allow honing guides to be used for oddball tools or skewed tools or short tools or extra thick tools. For those tools, the honing guide and its accessories slow me down. So I stick with the base model, which works well for chisels and plane blades.
So if you stick with the base-model honing guide, you are five minutes away from being a speedy sharpener. All you need is a simple block of wood that sets the blade at the proper angle in the guide so the steel at the tip of the blade immediately touches the sharpening media perfectly. Which brings us to a discussion of sharpening angles.
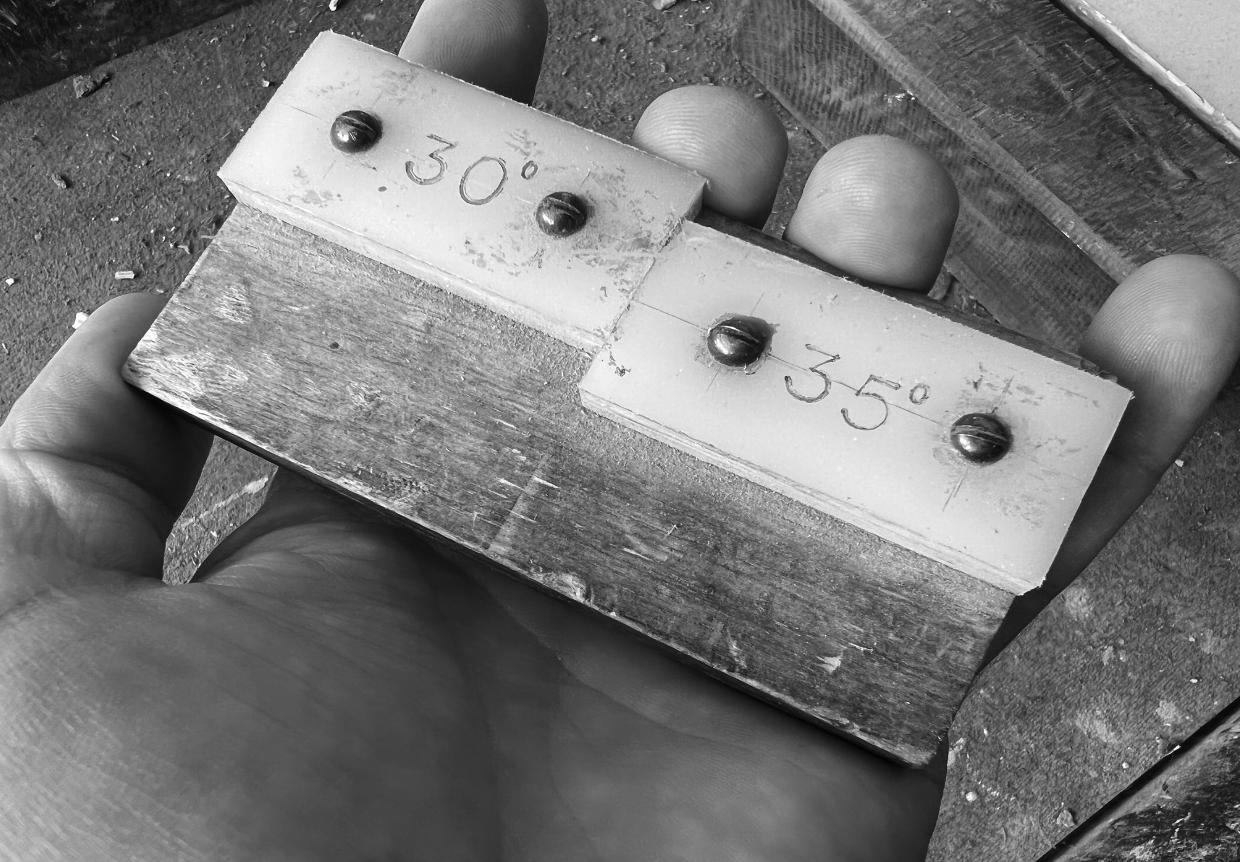
Honing Angles – the Argument for Fewer (or One)
Most sharpening experts steer you toward using a wide variety of angles for different jobs in the workshop. Lower angles for paring tools. Higher angles for chopping tools. And soon you are engraving all the sharpening angles on all your tools and doing more sharpening than woodworking.3
In my experience, the sharpness of the edge is more important than the angle (within reason). A 25° paring chisel and a 35° paring chisel will both do a fine job when really sharp.
When I realized this, I decided to see if I could hone and polish all my tools at 35° and be happy. That was about 10 years ago, and I remain committed to this simple approach. I am sure there are tools out there on the fringes that won’t work with a 35° hone and polish, but I have yet to encounter them.
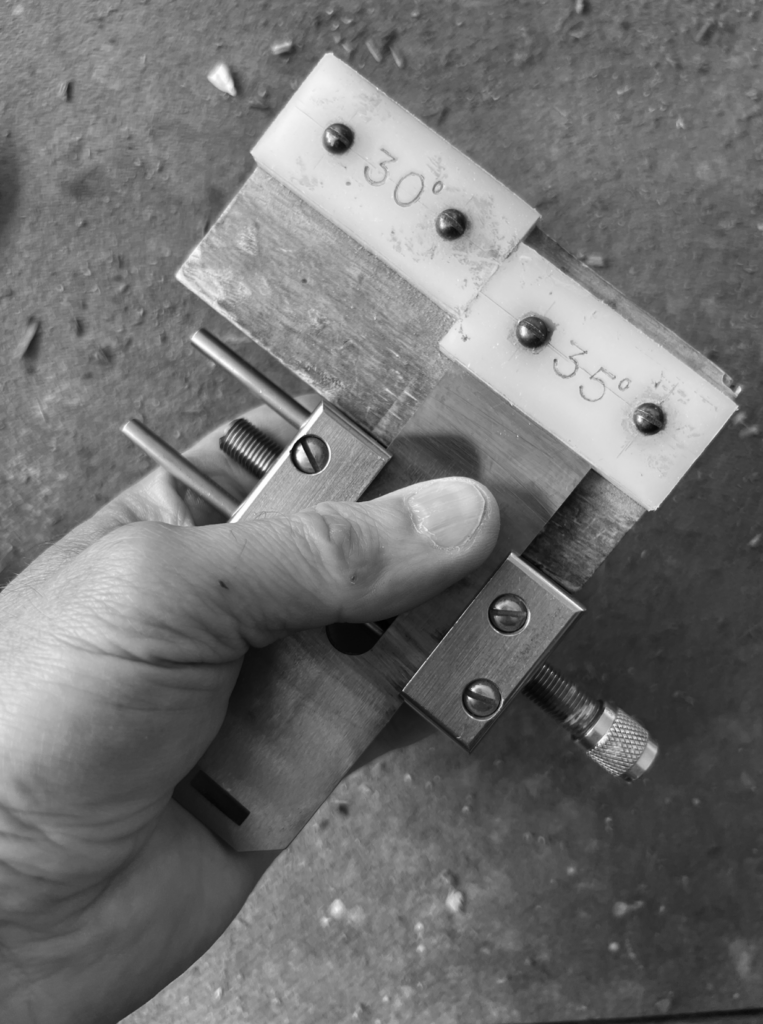
So I have a block of wood with a stop on it. I put the tool in my honing guide, I press the guide and blade against the stop block, then I tighten the guide. I am ready to sharpen. (Making a setting block is simple. Use a school protractor to set the blade to the correct angle in your honing guide. Then screw a stop to a block of wood that matches that projection.)
Hi Chris. Thank you for that post, really helpful. Question. Often you read that a chisel has a “secondary bevel”. Is it the secondary bevel that you are referring to and that you sharpen to 35 degrees?
Yup!
Right on the few bevels. Everything gets a 30mm with a 25mm micro from a LN guide.
Do I sense the Crucible “Wheely Sharp” honing guide coming to market?
Oh, you mean LemurSharp?
My only real complaint about honing guides is that I can never get them to hold the iron or chisel securely. No matter how much I tighten them, they always seem to want to slip. Cheap and fancy ones, only a matter of degrees, it always turns into a faff.
Odd. I’ve never had that problem with side-clamping guides.
I had an expensive top clamp guide that swiveled the blade, especially narrow chisels. But even a cheap side clamp guide holds like iron.
I agree completely. I sharpened freehand for a couple years hoping my skills would someday be perfect. That never happened & I love using the guide. Same for lathe chisels. I still freehand when necessary but it’s not as consistent.
I love your simple approach to sharpening. We can sometimes over-engineer a simple thing to the point that it’s all about the process rather than the goal…a sharp tool. I do notice that you have that lonely 30 degree stop on the same block. I’m guessing it is either older than 10 years or for left-handed screwdrivers. (wink!)
It is for students.
I teach handtool sharpening at the Woodwright’s School. Years ago, I quit using honing guides, but not because I don’t like them or that they are not easy to use. Basically there are just three angles to consider; heavy, thin or in between, covering mortising, paring or general benchwork. What I have my students do is look at the thickness of the tool near the bevel and at the length of the bevel. I ask them to estimate the ratio of the two. This is close enough for any work. If the bevel is 3X the thickness (~20 degrees) this is good for paring. If the bevel is 2.5X the thickness (~25 degrees), this is in the range for generic benchwork. If the bevel is 2X the thickness (~30 degrees), this is good for mortising work. This is just simple geometry. The reality is that it is more important to have a good edge than to have a specific angle. Getting a good edge is all about finding the flat of the bevel on the stone, and this is just a matter of sense of feel and consistency in stroke. I do not measure the thickness of the tool or the length of the bevel precisely, I just eyeball it.
I like Chris’ method a whole lot better.
Crucible needs to make a nice honing guide block for the LN honing guide. One that is water impervious.
Honing guide here: https://www.thingiverse.com/thing:4441255
Service to print it here: https://www.thingiverse.com/apps/3d-print-with-treatstock
Enjoy! 🙂
Any honing guides you like?
I used a vintage Eclipse for years. Now I use the Lie-Nielsen. Both work GREAT. But even the inexpensive Taiwanese side-clamp guide works great.
Over the, admittedly just two or three, years that I have been seriously woodworking, my sharpening has got progressively more slapdash and casual. In the beginning I spent far too much time using a painfully carefully adjusted honing guide and working my way up steadily through the stones. My hands were permanently coated in metallic residue.
Now, if I use a stone at all, it’s usually just the finest that I have and only for a few strokes and I don’t use a honing guide. I feel for the bevel and seem to be able to find it. Mostly I don’t use the stones at all but simply strop, although I do strop quite often.
I am not claiming to be any kind of ‘master of the edge’ but I do seem to get tools reasonably damn sharp … and I don’t spend much time in doing it.
It’s each to their own, I guess. I got into hand sharpening out of laziness to some degree. But it seems to work well for me.
LAP, I believe that once you have achieved the edge you want it keeping it should not be a chore or a science project. Thoughts on the sliding left to right ? Ralph
I’ve tried it. It works. And I get it’s advantages. But I prefer forward and back because that is my muscle memory.
Don you modify the primary bevel for any of tools or do you grind the same primary angle on everything as well?
Everything is grind at 25 and hone at 35.
I have a really old vintage Eclipse 36 side clamp honing guide where the V in the sides for chisels is upside down from the V in the sides of later Eclipse 36s and Taiwanese/Chinese clones. Turns out that it clamps straight sided chisels and plow plane cutters really tightly.
Do you have a primary grind and secondary hone angle?
and secondary
25 and 35.
In most cases, whenever I feel like I disagree with with you it’s because I haven’t invested the time to test your case with hands on proof in the shop. Respectfully, I will always disagree with you on this one. You say that you personally free hand on the more unusual edges, but where would you develop the skill needed to sharpen them? I am a staunch disbeliever in sharpening jigs, but not because I think they are crutches.
Sharpening jigs are fantastic at sharpening simple edges, but if you wanted to really develop your skills to be at your very best when you are faced with an unusual sharpening challenge, where better than practicing your freehand skills on a simple chisel, or plane edge to build your skills and confidence. At my talent level, I need every chance I can get to keep my free hand skills at their very best. A jig robs me of the practice I desperately need when there isn’t a jig option. Because of my practice with simple edges, I can still get the level of sharp I expect with the unusual.
What I’ve found to be true in my shop is that if you can’t free hand sharpen, you can’t saw to a line, you can’t pare to a line, you can’t cut a dovetail, a mortice & tenon, or flatten a board, but many of you can do many of the things I’ve mentioned here, so in my opinion you can free hand sharpen, you just gave up before the rewards came in.
You can do it,
You can do it,
YOU CAN DO IT.
Don’t give up.
Master this little skill and it all gets easier in the end.
And then, with the skills in place, using a jig if you want to, based on the freedom of knowing that you don’t need it, you might find it more effective with out harming the skills you already have.
For the record, it probably took me a more than a couple of years (could have been 3 or 4) to get really good at sharpening freehand, I know that is way, way too long for some people. If you are one of them disregard this whole post.
I can freehand sharpen carving gouges just fine. But it’s a completely different motion from bench chisels and plane blades. And the bevel needs to be flat, with no secondary bevel, as on chisels and planes. And, there is no even halfway decent jig for sharpening carving tools.
I can sharpen plane blades and chisels just fine too. But a jig is faster and easier. It’s just preferable to freehand.
Well, this is just the witch craft of sharp edges… surely sharpening something doesn’t come down to pages and pages of instructions, degree this, degree that… yep, a bevel guide is a useful thing, agreed. Lick a thumb and put it in the air, does it feel right… yep, you got it.
I think wood workers agonise far too much over this rather simple process as if its the pass or failure of working wood, what do you reckon?
Regards, Ed
Hi I saw a neat trick for creating a microbevel using a honing guide. Put
a business card under the wheel to raise the angle. (Wortheffort YouTube)
I think it’s better than the ruler trick.
Hi found it:
https://youtube.com/shorts/qHUTqfJRVIo?feature=share