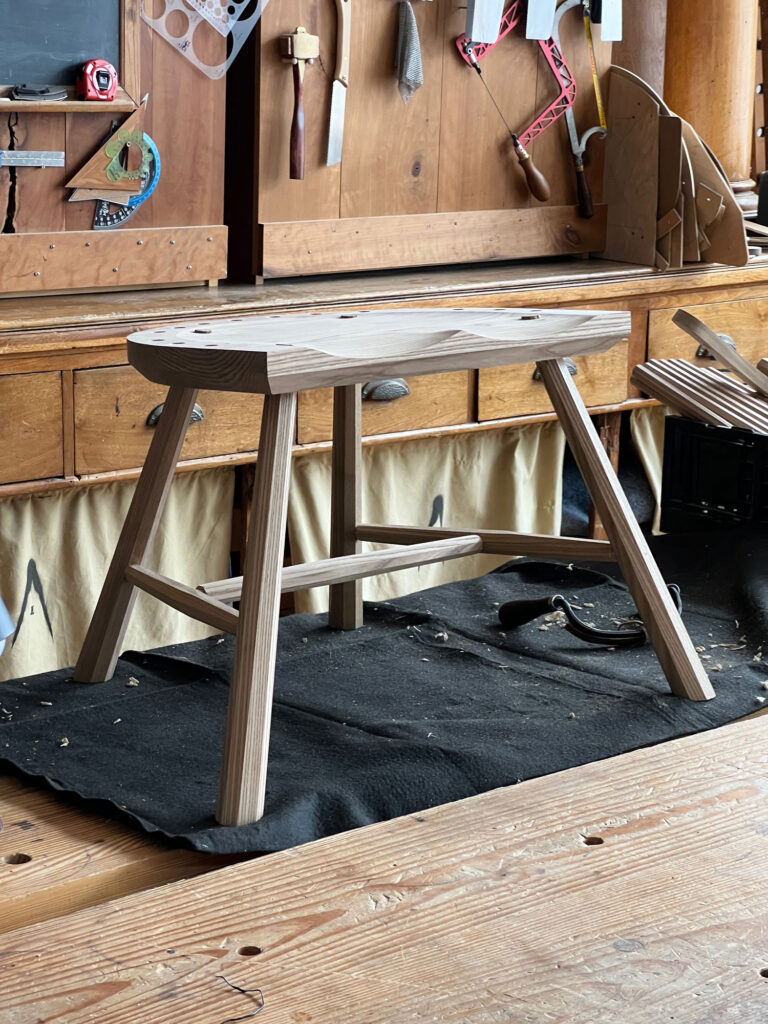
It’s time for our weekly Open Wire. And it’s also our open day here at the storefront in Covington. As a result, our answers might be a little delayed because we are answering other questions from people in the store.
This week’s open wire is hosted by me, Megan and whoever else starts tapping on my keyboard during our open day.
Here’s how it works: Type your question in the comment field. I will attempt to answer it. It is that simple.
So here we go…. Note that comments for this entry will close about 5 p.m. Eastern. But we will answer *all* of the questions.
— Christopher Schwarz
Is there a “rule of thumb” for the size of the hole to drill for a holdfast? I have a couple blacksmith made holdfasts that are slightly different in sizes and wanting to accommodate both. My workbench thickness is 3 1/2″.
The holdfast will work best if it is closely sized to the shaft. The closer you get, the tighter it will hold.
You can grind a spade down if you need a custom bit.
Re power tools, do you ever use a miter/chop saw? Or do you use a table saw + cross cut sled instead? Or handsaw? Thank you Megan.
We use a chop saw to knock down rough stock, but little else. We also have a table saw with a sliding table.
These are necessary for the stock prep we do for classes, mostly. If it were just me, I’d probably knock stock down with a jigsaw.
Converted to your waist apron when it came out and love it as was constantly sweating with my full apron. My question is can it be thrown in the wash?
Our clothing designer is here this weekend (Tom Bonamici). He says:
Why are you washing it?
Wash cold; hang to dry. It might shrink a smidge but it should be fine.
Mr obvious says “no bleach”
Thanks, was milling a bunch of wenge and apron is now a solid grey color
re: Mortise Planes. I mostly use the LeeValley mortise plane. Do you find the depth at max to be direction dependent. I think I have everything taken down to max, then if I reverse cut the plane takes more material. Is that a problem for you (or friends)? Matter of grain direction? Technique? Tool setup?
Thank you for your commitment and engagement to the extended woodworking community. Impressive to have grown while consistently creating a grassroots sensibility.
Are you asking about a plow plane? If so, cutting against the grain can cause the cut to go a little deeper because the cutter levers up wood fibers ahead of the cutting edge. It should be a small difference and shouldn’t be a problem. If it is a problem, let us know some more details about the problem – like how much extra depth you are getting….
Any words of wisdom for folks heading to Handworks for the first time this year? Thanks!
Talk to people. Visit every booth and watch the demos. Don’t be shy – everyone else is an introvert there (except Roy Underhill).
They usually have good sausages and beer for sale in the village.
It will go by in a blur. So take photos.
And some of us will be wearing Depends just incase we get really shy and nervous. No need for a repeat of last time.
This made me laugh. I had just been thinking, maybe I won’t go. Too much of an introvert anyway.
Hello. Do you know of any resources (or have any advice) on repairing a shellac finish? I know you can reconstitute the shellac, but I just seem to get a mess when I try that. Any advice would be great. Thanks!
What do you mean by repair?
Because it’s alcohol soluble, new shellac will dissolve into old shellac, so it’s not like polyurethane, where you need to carefully sand between layers, to get each coat to stick. It’s one of the great things about shellac.
I find that repairing shellac can be difficult, especially if it is crazed or has been exposed to a lot of water.
I am no expert in repairing shellac finishes, I’m afraid. I can fix the problems that I create when I get orange peel or runs or whatever. But older finishes need a more experienced hand.
There are lots of books out there, or you can consult someone who deals with these problems everyday. You might check in with Jeff Stafford, who is an experienced woodworker and finish repair guy. He’s friendly, knowledgeable and happy to share.
https://www.instagram.com/jffs_finishing/
My next project will probably be a stick chair for my desk. I work at home (and play guitar) quite a bit at my desk and was wondering if you have any design suggestions, or resource suggestions for a chair for prolonged desk work
Thanks!!
Usually a back lean of 15° is good for keyboarding. Seat slope of 3/4″. Lumbar support (so use an armbow). As far as guitar-playing, the arms will get in the way. Not sure what to recommend, except maybe cutting the arms short so you have some room at the front of the chair for picking and grinning.
A good smooth plane is next on my tool acquisition list. Both of you (Chris & Megan) use a #3, but recommend trying a plane before buying to ensure the size is comfortable. Do you have a recommendation for getting hands on one? There are no quality hand tool purveyors near me (north Chicago suburbs – reader suggestions?) as far as I can discover. Thank you both for these Saturday live sessions. I find them exceptionally valuable and enjoyable.
You can try out the sizes at any Woodcraft or Rockler. They have knock-of planes that are sized based on the historic Stanleys. The No. 3 fits most people, unless their hands are meaty. My hand (minus thumb) is 3-1/2″ across, which fits well in the No. 3 (but not No. 2).
Thank you
#3 doesn’t get the attention it deserves. It is a great smoother for small projects. Fits so nice in the hand. If I could only have two planes it would be a #5 1/2 and a #3. The 5 1/2 versatility allows for shooting edges and smoothing.
Rockler Woodworking is at 253 W Golf Rd, Schaumburg, IL 60195 (1 847 310 0447) and Woodcraft is at 7440 Woodward Avenue Suite A 107
Woodridge, IL 60517 (630-435-9663) if this helps at all. Hope you find a plane you’re happy with.
Thank you. Much appreciated. Yes, I hope to find one.
Any chance of a few added videos for the Stick Chair and the Gibson? I’d love to see a video on the modified arm jig for the Gibson and making the arm for the Low Back. Thanks for all your work by the way. Making your chairs is the most fun I’ve ever had in the shop.
Perhaps in the future, yes. Right now we are so busy with the new building that there is little time for anything else besides keeping the business moving forward.
I remember y’all posted an article on that modified arm jig but can’t seem to find it. Could you provide a link to it so I can bookmark it this time?
The “Categories” drop-down menu includes “Gibson Chair” so you can easily see a list of posts about same.
https://blog.lostartpress.com/2023/07/06/a-jig-for-drilling-gibson-chairs/
Speaking of that updated arm jig, is it in the revised PDF of the Stick Chair Book, or is that the original? And thanks again for that PDF – your books are so beautiful it’s hard to take them into my messy garage/shop 🙂
Any future plans to do a double stick chair or settee and share the design? I know John Brown did some and have only seen a few pictures of his. I’d love to expunge the tired upholstered love seat from my house.
One thing I’ve been struggling with in my chairmaking is workholding. Specifically cleaning up the surfaces of a glued-together armbow to flatten it for gluing the shoe in. Or in the case of the Gibson (on my workbench right now), the individual arms to clean them up after drilling the holes in them. My workbench is pretty standard new-woodworker: planing stop and moxon vice. I’ve tried nailing some does-feet to my benchtop but nothing I’ve tried has worked well.
Speaking of this, I’m planning an Anarchist Workbench build as I’m frustrated with my bench: thoughts on the smallest electric jointer that would work? Do I even need a jointer?
Hi Jace,
Not Chris, but in reply to your final question, no, you don’t need an electric jointer or planer to build an AWB-type workbench; I know it can be done from rough-sawn lumber with hand tools, because that’s how I built mine (to all intents and purposes an AWB, except for the fancy lad hard maple and tail vise).
What you do need if you do it by hand, though, is I would say (a) rather more time (I’d guesstimate that preparing the 13 laminates for the top took me maybe 200 hours over four months), (b) winding sticks, and not least (c) a reliable straightedge that is longer than your laminates, so that you are not working blind.
For a straightedge, I used an 8’ long bricklayer’s spirit level made from extruded aluminium. To be sure I got one that was true enough over it’s full length along at least one edge, I took along a pencil and a long piece of paper to the big box store where I bought it, and did the draw-a-line-and-flip-and-draw-a-second-line-and-compare test on the spot, before I handed over the €35 or whatever it was it cost.
Then it was just a question of being finicky enough to get a good fit between each laminate. The occasional small hollow is not a problem, but there should be no bumps, no wind, no snipe and basically no concavity in the length. It was a lot of work, and I wouldn’t particularly want to do it again, but it can certainly be done.
I should perhaps say that I have nothing against electric jointers or planers; it is just that I don’t have them, and was not in a position to get either before I built my bench.
Cheers,
Mattias
Mattias,
I always appreciate your perspective here! That’s what I was afraid would be the answer. I was hoping for “skip plane and joint the edges on a tablesaw and you’ll be good to go”. Right now however, the first hurdle is finding appropriate boards. A few home depot trips and I still haven’t found a single suitable board–much less the 12 or so the bench takes!
I have two benches, and imo, having perfectly clear boards is very nice, but looking at historical benches, especially english ones, they used what they had. Don’t be afraid of a few knots, just avoid major twist and the center of the tree.
Thank you, Jace – it’s very kind of you to say so!
Just to be clear, and all that, I have to date built exactly one (1) bench, which makes me not even an Internet expert. In other words, what I say is what I know, based on my rather limited experience, so many things it may well be, but gospel it ain’t. Add salt to taste, is what I’m trying to say here. And also, I’m sure there are people out there who have gone about things differently from me with equally good /or better) results.
However, within said limited experience, I did find that even with 24 parallel clamps involved, there was no way that force alone was going to close a gap caused by even a two-shavings-and-its-gone bump. So while it was a bother and a half, I don’t regret the time I spent just before glue-up of the top, chasing down gaps with my finest feeler gauge (0.05 mm = 0.00197″).
That said, if you can get your hands on skip planed stuff, rather than rough sawn, that ought to save you many a minute (meaning hours) of handplane work!
Another thing, by the way, if you are going the handplane way, don’t bother getting each laminate to the same thickness like Chris does with the AWB. After you have a true face and a true edge, gauge for thickness aiming to take off as little as you can get away with, i.e. fimd the thinnest spot and set your gauge to that. So what if one laminate comes in at 1-7/8″, the next at 1-3/4″ and their respective neighbours at somewhere above, below or in between. Milling to the same thickness makes perfect sense on a planer, but very little sense by hand; all that that does in a hand plane situation is give you less stuff for more work.
And finally, I realised on re-reading that I plum forgot to mention the necessity also of a try square. But then, you knew that.
Cheers,
Mattias
You can joint boards on a plainer using a sled. I hot glue the boards to a piece of mdf. Plainers are cheaper than jointers. Kind of a two for one deal
Would you do Catbus again? Any parts of the experience that lack functionality for hauling wood and finished work? I’m in a region with real winter (similar to North Dakota) and considering kei trucks and vans.
Good morning! Anybody knows what happened to Ray Deftereos of handtoolbookreview ? I was about to re-listen to his reading of the Anarchist’s Workbench, and realized we’ve heard nothing from him for a while!
Have a nice Open Doors day!
Good question about Ray. I’d also love to hear from Richard Maguire again.
Richard Maguire posted a new course a few months ago, so he was still around and kicking recently.
That was over a year ago, I believe, and no blog posts yet this year. He’s been a great resource in the past.
I believe he stopped in order to deal with some family issues. A solid guy.
What are your thoughts on using the 12” or 18” ultra smooth woodowl auger bits for stick chair drilling? Would they work for drilling the stick holes through the arms and seat or would they blow out the arm rest holes?
I have a Knockdown Nicholson bench with a crochet that I’m considering replacing with a leg vise. The crochet works fine for edge planing but it’s a bit of a pain for trying to hold oddly shaped (e.g. chair leg) or really narrow pieces to the side of my workbench. Unfortunately I’ve got a bit of analysis paralysis. Does a crochet have any advantages over a leg vise aside from cost? Additionally, if you were in my situation would you rather replace the crochet with a leg vise or add something like a carvers vise/hi-vise? Assume you can only afford one for now and the other may come later.
I have a Nicholson bench and I replaced the crochet with a leg vise. While I really liked my crochet, I do not miss it. I do like the extra functionality of a leg vise
Chris, You have been so productive over the years, it seems like you are constantly turning out furniture despite everything else you do.
You have written about some of it in the past – use machines for grunt-work (benchtop planer, bandsaw), use the best tool for the job, don’t waste time/energy on furniture components where it doesn’t matter, etc. Any other words of wisdom here? What has been the most critical in being so productive?
As a novice and a hobbyist, I feel like I spend hours in the workshop but don’t really get anything done, but maybe I need to reset expectations…
I’ve got some chair-building on my to-do list. My spouse and I are both large (I’m 350, she’s 300) and I’m seeking advice for how beefy I should make the chairs, and what woods to use. The current plan is for a couple of lounging chairs for the living room (Morris chairs or something similar, function-wise) and a pair of chairs for my office, probably stick chairs. Other things I’m building for the living room are being made from sapele; the office is mostly cherry. Can I stick with those woods and just oversize some of the components?
Good morning Chris,
My question this week is actually in a similar vein as John’s above, though focused on chair comfort rather than strength.
I’m currently working on new dining furniture for our home. I’d like to build stick chairs to accompany the table, but I had some concerns over how well they accommodate larger individuals. We like to host family and friends often, and have several people that need a bit of a wider space to sit, and I worry that the stick chair designs in SCB could end up being very constricting for such people. My options, as far as I see them, are either modify the chairs to be a bit wider, or else omit the arms and make the chairs more backstool-esque (maybe build the staked chair from ADB).
My questions are:
1) Have you ever found a need to modify your stick chair dimensions for this purpose, or seen indications that it may be necessary (visitors to your storefront testing your chairs, feedback from customers, etc.)? If so, is it truly as simple as making the seat wider and modifying the arms to match?
2) What steps would you suggest to mitigate structural concerns for a backstool that would see daily use as a dining chair? In my mind, it would be adding stretchers to the legs and ensuring the back sticks are dead straight grain from a strong species; but I’m not sure if that would be enough.
Thanks for your insight, appreciate you doing this as always.
Hi Julian,
You can make the seat as wide as 24″ and widen the arms a bit and that should accommodate most sitters. Just be vigilant about straight grain and wood that is not brash. I recently had a 340 lb. friend sit in a one of my stick chairs with no problems. It was mostly a matter of getting him in there between the arms.
On the backstool, I’d add stretchers as you suggest and beef up the back sticks to 7/8″ or so.
Hey Chris & Megan! I hope the open day at the storefront is going well and that y’all meet some cool folks.
With the revised version of the ‘The Stick Chair Book’ coming will the original still be available until then?
Yup. We will sell out the first edition and then replace it with the revised one in about four or five weeks. We have about 200 copies left now. If we don’t sell out of those when the new edition arrives, we will likely close them out with a sale.
Curious to know more about your light mention last week of experimenting with hard-wax oils for a more durable tabletop treatment. Can you elaborate about what you’ve been testing and what you’re interested in?
I am just starting to use them and have no wisdom to report I’m afraid. There are lots of people out there who are experts on the hard-wax oils. I’m not there yet.
As a chemist, I suggest being careful with hard wax oils. The hardener is hexamethylene diisocynate. Not something I would want to breath or get on my hands. Once it is done doing it’s hardening, it should be fine.
Good morning, Chris and Megan! Do you use anything else besides (camellia or jojoba) oil to keep your tools free of rust? My shop (like those of many people, I presume) is in an irregularly heated and cooled garage, with dehumidification only provided by the window A/C unit (when it’s on). I’ve thought about moving a dehumidifier in there but I also sometimes want to leave the windows and doors open when it’s cool enough (the open doors allowing more light into the shop). Thanks again for all you do for the community, including this Open Wire. You’re too kind.
Any oil is fine. Mine is soaked with the oils you mentioned plus light machine oil, WD-40 and lord knows what else.
There is some fancy machinist stuff out there for industrial environments as well. But I find that vigilance is more important than the type of oil.
Hi Chris, I was able to grab one of the new hammers yesterday before they were sold out, I know it’s a miracle. All the tools you sell are amazing. What about selling som “scorps” for the chairs. It’s impossible to find them. I was able to get a set of travishers from Allan Williams, after you name them, the wait was like 3 months. Thank you very much for your time. Best luck on the new building.
PD, who can I ask if there is a place to park a big rig (18 wheeler) in Amana for the days of the show, I’m going to try to take my time off there.
Thank
Hi Ricardo,
I think that almost any blacksmith who makes tools (especially drawknives) could make you a scorp. If we did a scorp, we’d have to get them made by blacksmiths – our tooling and machines do do any forging.
The Ray Iles scorp is usually easy to get. And I believe there is a Two Cherries German one out there as well. I have tuned them up when students bring them in, so they are workable.
Sorry I couldn’t be more help.
Jason A Lonon has some in stock I think.
Almost forgot this: an organization you support, A Workshop of Our Own in Baltimore, which provides a safe workspace and training for women, trans, non-binary and other gender non-conforming folks, is holding a fund raiser to support a move to a new location. Would you mind signal boosting? Their GoFundMe is at https://gofund.me/471939f3
I know that this has been addressed in the past but…. I’m now faced with either paying too much for a kiln dried 4” slab bench top or buying green from a rural hobby mill at 1/30 the price. Any suggestions?
Have you got a place to air dry and can you wait a couple years or so for it to dry out? You got another project or 2 to do in the meantime? Best of luck.
I’d prefer option No. 3: Make the top from 2×12 construction lumber. That is both inexpensive and dry.
That suggests another option that I was reluctant to put forward, that of leftover gluelam beams. They seem to be relatively cheap and abundant but I was unsure of their suitability.
I’ve had a bench since 2009 made of glu-lam. Dead flat still. I love it. https://www.popularwoodworking.com/article/lvl-workbench/
I see that Chris has these staked saw benchs in a bunch of photos here and there. However I never hear about them, any tips on building them?
You can find plans for them in the Anarchist’s Design Book. It’s a great way to practice staked joinery since it’s a shop project BUT if you don’t have a drill press be careful about your wood selection. Reaming 3″ of cherry was quite hard.
Howdy! I’m trying to put together a shop space in the garage. The slab has broken into 4 pieces so no level surfaces. I want to build a floor that I can level. Do you have any recommendations for quality levelling feet? I’m thinking about building it from 2x4s and 3/4 ply. I’ll be using my low bench on it. Thank you!
I had the same problem, although maybe not as bad. Make the legs all hit the same plane as well as you can. The bench will then rock on (what it sees as) the two longest legs. Make a long softwood wedge to go under one of the other two (preferably the one away from where you stand), and tap it into place until the bench doesn’t rock anymore. Leave the wedge a little long for a bit, so you can adjust if you move the bench.
This has worked very well for me.
,
That’ll work. When I covered my old shop floor with wood, laid down plastic. Then we used 1x furring strips and shimmed them so they were all in the same plane. Then 3/4″ T&G. Worked great.
I was planning on heading to the open house this morning but I woke to a yard full of chair parts in the rough.
I guess we had some wind last night.
That’s a great “looking on the bright side” for windfall in the yard. 🙂
Enjoy!
Howdy – how do you decide when to use tapered tenons vs cylindrical for stick chair and table legs?
I decide based on the piece. If I am going for an honest vernacular feel, then cylindrical. If the chair is a more modern take on old stick chairs, I’ll use tapered tenons because they are more forgiving to make.
Structurally, it doesn’t really matter.
Hi,
Someday looking forward to be able to visit LAP in person. My wife wants an entertainment center for the family room. Happy wife, happy life so I am in the early design stages and looking for inspiration. I’d like to build it in prairie furniture style. I’ve already been to the local library and combed through their books. I’ve found some info usually contained in books on Frank Lloyd Wright or cottage homes.
1. Do you happen to know of any good books that really delve into prairie style furniture?
2. Do you happen to know of any modern makers of prairie style furniture?
Many thanks for the help.
Sincerely,
Joe
I don’t think of Prairie furniture as a unique furniture style. More like a subset of Arts & Crafts. But not stained dark. And more horizontal. But it’s the same forms, techniques and look as Arts & Crafts. There are lots of makers out there who channel a FLLW vibe, and looking at interiors of his houses will give you a good idea of what fits.
Thanks. Based on what I’ve read so far, it does sound like more of a subset.
Chairmaking Tools question: I recently bought two 24” owl augur bits from Taytools: 1/2” & 5/8”. Would you recommend any other widths?
Those are the last tools I need for chairmaking other than tools for seat saddling. I know people use scorps, adzes, and even saw someone use a travisher aggressively to saddle a seat. Where should I start?
You don’t need another auger unless you plan to use cylindrical tenons on the legs. Then you should get a 1″ auger.
The easy/cheap place to start with shaping a seat is to buy the Windsor Workshops travisher, which can act as a scorp and a travisher. Rarely do tools do double duty well, but this one does.
That’s what I was leaning towards, just didn’t know if it would work. Thanks for the tip!
When saddling a chair seat I like your approach, but after the travister step (mine is a small vintage Stanley) how do you go and remove the scupper marks left by it?
This is Megan, on Chris’s computer… sanding –usually no more than 3 minutes with a random-orbit sander outfitted with a soft pad between the plate and the paper
Thank you Megan! That clears up a lot!
Planning to make a six-board chest based on the PWW article you wrote – my wife and I will be celebrating the first birthday for our twins this September and this will function as a toy chest for at least a few years. The recent blog post regarding scholarship donations had a picture of six-board chest with spear point cranked strap hinges. The cranked strap hinges in the PWW article are beautiful and huge. Do you have this hardware made custom? Buy strap hinges and bend the short leaf in a vise? Buy them already cranky? Any thoughts would be helpful
Any blacksmith can make a good pair. Horton Brasses has some excellent blacksmith-made ones. I think those were from Lee Valley and were discontinued. But I had to bend those.
As usual, had a good time at the open house today. Thank you.
Hi Chris,
Thanks very much for hosting this. Possibly an unfair question for you, but maybe someone has experience with this. I have several dead ash trees that have been killed off recently by the Emerald Ash Borer. Is the wood still usable for woodworking if I try and split boards out of the trunks?
For what it is worth, I had a dead ash tree sawn up into lumber and I haven’t had any problems with live insects in it. I think the bugs impact the sap wood and then depart once the tree is dead.
Ash degenerates quickly, especially the sap wood. After you split it, probe the heartwood and sapwood with a knife. If it’s punky, don’t use that part. Also, compromised wood will feel much lighter than the normal strong stuff.
Thank you both.
After you shape and sand the arms for the Gibson chair, what, if anything, do you use to remove sanding dust?
A brush or compressed air. Or a tack rag.
A question about quick-release vise maintenance. Both my vises have been more difficult than they should be to open and close using the tommy-bar handle. I waxed the half-nut on both, with much improvement on my front vise (Record 53E), but the smaller Jet (JWV-9) end vise still is difficult. What do you recommend for maintaining / lubricating the half-nuts and main screw? Frequency of maintenance?
Can’t speak for Chris, but I use dry-lube spray as needed.
Definitely clean the screw and half-nut of any gunk. They do get crummy (especially with a lot of lube going on down there). I clean mine with Simple Green degreaser and then apply a light coat of machine oil.
However….
Usually the problem is not the screw or the half nut. Or lube. Usually it’s the nuts on the front face of the vise that secure the guide bars. If these are too tight or too loose, the vise will jam. You need to tweak them every year or so to keep the vise moving smoothly (apologies if you have already done this, I don’t mean to treat people like they are stupid).
Hey guys, Hope you’re all having a great day. Two quick questions..
Firstly, do you recommend hide glue for tabletop laminations, or does PVA give better longevity?
And secondly, does liquid hide glue react with pipe clamps the same way as PVA?
No idea of the relative longevity of PVA, but there are things held together with hide glue that have been round for more than a century –so I feel pretty good about it for a tabletop glueup. And yes – I think that’s the iron reacting with the water in the glue; hide glue is also water-based. So same things happens.
Ok, makes sense. Thanks!
Hey team, just wondering about using sticks for stick chairs. Are small tree trunks or branches suitable for chair legs? Would a straight, dry 2″ branch be similar to a riven or sawn piece of the same material? Are there any special considerations to take into account? Are there historical examples of this? Thanks for taking the time to benefit this community; you’re all amazing.
Of course you can! You might get some splitting because the pith is involved, or you might not.
Some people strip off the bark; other leave it on (it can shed the bark depending on the species and when it was harvested).
I used to make lots of chairs and tables with willow sticks. Never had a problem.
Any opinions on tung oil vs linseed oil? I haven’t found anyone compare them in a way that’s not super biased one way or another. I read Steve Voigt’s article in mortice and tenon and enjoyed the defense of linseed oil, but it didn’t really compare the two, and any other article I have found tend to preach the supposed short comings of linseed oil that Voigt refuted. Mainly curious if you have any experience with the claims of superior durability or water repellence of tung oil. Thanks for doing these and offering such a great service here and in so many other places for the woodworking community.
I have used both, both as a stand-alone finish and as a component in a recipe.
I have never pitted one against the other. Nor do I feel the need to. They both work. Neither is defective or seriously lacking. People feel compelled to pick a side with these things, and I just can’t be arsed.
Sorry!
Sam Maloof just mixed them together…
Also fine.
I forgot to ask this at the open house today. Without thinking, I applied wiping varnish (1:1:1 poly, mineral spirits, and BLO) to the inside of a cabinet. If the cabinet interior ends up too smelly, would a coat of shellac likely ameliorate that problem?
Cheers,
Michael
Likely it will smell fine after it has cured after three weeks (the oil is the only problem). Leave the cabinet open for a few weeks. If it still smells strong, then a coat of shellac will help.
The other option is to wipe the inside of the cabinet with mineral spirits, which will thin out and remove the linseed oil.
But my inclination would be to let it cure. There’s not a lot of oil in the mixture.
Hello Megan! Is a 1/2 tapered tenon too small for the comb back stick chair’s legs if using red oak? The Veritas 5/8 tapered tenon cutter is on back order. Thanks 🙂
I’d switch to 1″ cylindrical tenons until the 5/8″ is back in stock. It won’t be long.
I was wondering if you might help me find a name for these chairs. I found them near Yosemite and fell in love, but will need to find plans to be able to build them. https://postimg.cc/gallery/TfMg6nz
Those are Arts & Crafts side chairs. Modern. Very common.