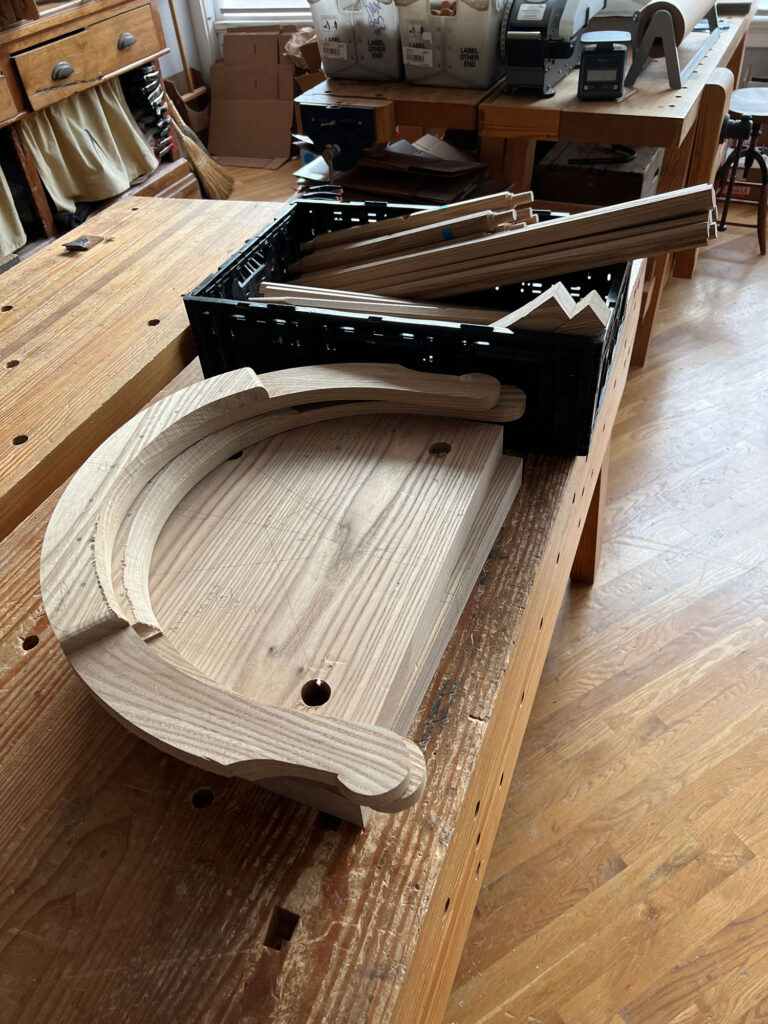
I’m back in Covington after a two-week trip to Scandinavia. So after a couple weeks of guest hosts at the Open Wire (thanks, Monroe and Joel), I’m here today to answer your questions about woodworking or stuff that is going on at Lost Art Press.
Warning: My head is full of cheese. I arrived in America with a bad head cold and an unusual case of Traveling West Jetlag. So I might be a little slow on the uptake
Despite all that, I am happy to be home and back at the LAP HQ.
Here’s how it works: Type your question in the comment field. I will attempt to answer it. It is that simple.
So here we go…. Note that comments for this entry will close about 5 p.m. Eastern.
— Christopher Schwarz
What are the best white markers for dark wood, black walnut?
I have no clue about the “best” marker. For many dark woods, we use a ceramic mechanical pencil (you can find it at many fabric stores) that marks in white or pink or light green. I use it to highlight layout lines. If the wood isn’t too porous, I’ve also used chalk dust or baby powder in a pounce bag, which also works fine.
Search for Faber-Castell Albrecht Dürer Watercolor Pencils, available in a ton of colors, including white. I saw them in use at a green wood spoon carving class, and bought them at my local Blick Art Supply store for about $3 each. I bought 3- white, a darker blue, and a bold red, I use them for layout lines on the wet wood spoon blanks, they work great. I think Blick also sells Chris’ favorite manual pencil sharpener (search his blog), buy a sharpener at the same time. https://www.dickblick.com/products/faber-castell-albrecht-durer-watercolor-pencils/
Bohin chalk pencil might be worth a gander, never used one though.
Have you tried page on stick chairs? Any thoughts versus real no paint or the general finishes substitutes?
I meant “linseed oil paints”, not “page”! No idea how that happened
I haven’t tried it on a chair yet. Been too busy teaching and traveling this month. I do have a chair built for the process and just need to find the time to do it.
My friend Mattias Hallin painted his chair a lovely shade of blue using linseed oil paint. Plus I’ve seen many historical examples. So I am enthused about the prospect.
Thanks! Sounds promising.
Chris, your thoughts on tripod tables? Stable. But tippy in their own way. Thanks.
No more tippy than than a four-legged table at 30″. Both will be pretty tippy. And low tables will be stable.
I find that with tables, it’s more a function of the height than it is of the number of legs. Though I am sure there are some extreme examples out there that would disprove me in part.
Thanks. And for that marvelously cluttered Bergen shop shot…
Welcome back Chris. If one is using only hand tools, what is the best way to make sure a board is square after sawing / hand planing etc?
Again, “best” is not going to happen here.
I use winding sticks for flatness. Try square to check edges to the faces. And a framing square to check the ends to the edges.
As you get experienced, you use winding sticks less and less. Your eye can easily see the problems. Or you can show the board to your workbench top to get a reading on twist. But the framing square and try square are absolutely critical for casework. (Not so much for chairs….)
No questions just wanted to thank you and your friends at LAP for doing what you do. I’ve enjoyed your writings and publications very much over the years.
Thanks John!
I am looking at getting an auxiliary vise to go along with my leg vise in order to try my hand at stick chairs. Is there a reason to go with the Hi Vise over the Pattern makers vise or vice (ha) versa? I noticed you used the pattern makers vise for the Gibson chair video and the Hi Vise in the stick chair video.
Either vise is a big improvement. I’d pick the one that appeals to your aesthetics or your situation. The Hi Vise can clamp anywhere without a hole in the worktop. The carver’s vise needs a hole. Some people hate to put holes in their beautiful benches.
If money is a concern, the carver’s vise is cheaper. But the factory jaws need to be replaced in short order. The Hi Vise can be as robust as you please. But it is more expensive and requires work on your part.
We use both.
Chris, any thoughts on which classes you are thinking of teaching next year?
Probably three or four week-long chair classes. And a few classes on building a peasant coffer and engraving it (two- or three-day classes). I think I’ll return to the Florida School of Woodworker for a charity class (probably a chair class).
Megan and I have to sit down and figure out the calendar for 2024.
I bought the cutters and handle you suggested for making spell panels. The cutter required a tilt of about 45 degrees because of the bevel on the outside. This was fine for handheld but lousy in the dividers. I used a 1/8″ carbide Dremel and sharpened the inside on the opposite side. Works much better now in the dividers with little tilting required. For the hand held I used an old tool handle made by C.E. Jennings. This has a heavy chuck and the weight makes for an easy cut.
The flooring cutters always have to be sharpened to work in wood. I use #200-grit sandpaper stuck to a stick to shape the bevels.
I made a stick chair out of red oak and used the soft wax recipe to finish it. After living with it for a year I’ve decided I want to paint it with either milk paint or linseed oil paint. What kind of surface prep do I need to do to ensure good paint adhesion?
The paint will probably stick to the chair as-is. But I would wipe the chair down with mineral spirits to remove any wax on the surface. That should do it.
If you have adhesion problems (very unlikely) a coat of shellac over the old finish will do the trick.
Big question, I know, but how do you think AI will change woodworking and LAP (if at all) going forward?
AI is a tool, just like social media or the internet in general. It’s already being used to automate repetitive background tasks on our website (such as writing SEO scripts). I look forward to using it for research, looking across cultures and languages for things I struggle with.
I am sure the tool will be used for ill as well (I can think of many ways). But I am optimistic.
Welcome home Chris. I’d like to build a Roman work bench. You have built several styles, which was your favorite and what advice would you give someone about to build one.
The four-legged bench from Saalburg is my favorite. There’s really not much to the benches. If you are apprehensive about them, make them using construction lumber. The one I use now is made from yellow pine 2x12s. The top is laminated from two layers of 2×12. The legs are also yellow pine.
Just make it as stout as you can. Make sure you can straddle it comfortably. And add holes and workholding as you need them.
They are super-basic, unlike a high typical bench. So little can go wrong.
Thanks Chris. I have a huge white oak slab I’ve been saving for the project.
“The top is laminated from two layers of 2×12. ”
When layering two 2 x 12s, Is there a preferred way to orient the grain? For instance, should they both have the “bark side” in the same direction? Or facing opposite directions?
Sorry if this is a really foundational thing to ask about. I was considering something like that for a Nicholson style bench.
“The top is laminated from two layers of 2×12. ”
When layering two 2 x 12s, Is there a preferred way to orient the grain? For instance, should they both have the “bark side” in the same direction? Or facing opposite directions?
Sorry if this is a really foundational thing to ask about. I was considering something like that for a Nicholson style bench.
It’s a very important fundamental. I have done it wrong in the past. Orient the rings in the same orientation. CC or ((.
Not () or )(.
Vimeo question – is there a page on tips for accessing / downloading purchased videos?
I’ve purchased the Gibson and stick chair videos, and find they don’t show up in the mobile app like purchases from other craft people.
Thank you.
Hi Greg,
Are you trying to access them through the Vimeo app? They won’t be visible there. The best way to access them is to:
If I’m not helping here, send an email to help@lostartpress.com and we will give you a hand.
With the video open in vimeo, click on the vimeo icon at the left and you will see a download option.
Congratulations on publishing Sundqvist’s new book, “Karvsnitt.” Just received it. Inspiring and beautiful and poignant. Eager to begin studying and working with this. Jogge says in a podcast I recently listened to that back when he still had a rock band they did some kind of Brian Eno type music while people were working wood and the wood carving was expressing the music. It was never recorded. Maybe someday that Anthe building will have room for a big paying class of carving students and concert goers to fund Jorge’s band to come back together for a recording. It just sounded like such a special blending of these two art forms.
Well we have invited Jogge to teach here in 2024. But I don’t know if a rock opera is in the works for our skill set.
I know that Jogge did record his rock opera somewhere. We have a VHS copy of it here somewhere.
get him to do his Rhythm and Slojd show. It’s mind-bending.
Welcome back! What was the most fun thing you saw in Jogge’s shop?
I wasn’t able to visit Jogge’s shop. He met me in Stockholm on the way home from a show he was working.
Hi Chris – Working my way through The Woodworker Vol. III and there are bookshelves described on page 1093. Any thoughts on how to attach the feet to the case? I’m assuming the cross-grain construction would not allow for glue. Thanks!
I would screw up through the rail to secure the front edge of the case to the base. Then I would use an angled screw (like a pocket screw) through the feet and into the underside of the base – with the hole reamed out a tad to allow for movement of the case.
Thank you.
Hi Chris – Do you experience seasonal cycles in the interest or motivation you have for the different facets of your LAP work? For myself, I noticed a few years ago that winter (I’m in Wisconsin) is shop/woodworking time, but later in the spring as outside activities and gardening chores pick up my interest in woodworking wanes. I’ve learned to enjoy the warm season sabbatical from woodworking, including the anticipation of diving back into the shop once the days get shorter. I’m curious if you or your colleagues have settled into similar season cycles, and what that experience is like for you.
That is historically how the market goes. Our sales reflect that trend as well. People do more woodworking in the cold months in North America.
We are full-bore here 12 months a year because it puts food on the table. But working in the summer is harder, especially trips to the lumberyard and the sweaty work of breaking down stock outside in full sun.
Besides the 60 grit Norton wheel, what do you have or find useful on the other side of your bench grinder?
I use the Razor Sharp wheels for shaping and honing fine cutters (such as the flooring cutters I use for engraving). We also have a ScotchBrite wheel for removing rust from tools.
In your opinion, what is the most comfortable all-wood chair design? For sitting/lounging with a nice beverage. Looking for a “melt into it” design.
I like the Gibson chair, as do most of the visitors to my home. But I also like the Jennie Chair for that purpose.
Hard to say as I haven’t sat on every design out there. Dunbar’s sack back design is pretty damn good, too.
I am making a mitered box with hand tools, going for the grain wrap, and I’m wondering what technique you use to get the nearly perfect mitre. I made myself a mitred shooting board that cradles the shooting plane at a 45 to the work, but the results are less than consistent. Just curious how you would approach this fussy joint (other than just using dovetails). Thanks!
The honest answer is I don’t like mitered-corner casework. I think the joint is weak. I use mitered dovetails when I want the look at the front edge.
Sorry, I’m not a small box guy. Check out Doug Stowe or Matt Kenny for help with these tricky joints. Sorry.
Thank you!
Good morning Chris. We have an abundance of ash trees here in the east that have been killed by the ash borer. Very sad. My question is, have you had any experience using ash that was cut after dying rather than cut down green? I suspect the quality and working properties would be different, but would like to know more before I invest in having a large log sawed into boards.
Not Chris, but episode 103 of the Shannon’s Lumber Industry Update podcast had a long segment on ash and EAB with a scientist guest, including bits about how that affects woodworking.
Yes. We have lots of experience. Ash deteriorates quickly on the ground. It loses strength and weight in the process. Ash should be heavy and dense. This stuff is light and weak.
I won’t use it for structural applications (though I am certain you can pick around the bad stuff and make it work). But for the top of a coffee table or something more decorative, I’d consider it. Take a pocket knife and probe the wood before buying. If you find punky spots, be wary.
So far in my woodworking journey of three years, I’ve found almost no furniture style that I would personally want to replicate. There’s more out there than I’ve seen of course, but after gradual exposure to a wide range from boarded vernacular peasant style to router templated walnut YouTube style to kingly ornate pieces, it’s all just ”meh, I have no interest in building any of that”.
With a lifetime of exposure to clean lines and Ikea style, I guess my only preference is something like ”Nordic minimalism”. What book(s) or other sources would you suggest I look into, if I wanted to use that as a stylistic starting point?
I don’t know what Nordic minimalism is. Danish modern? Bauhaus?
Check out the work of Hans Wegner, Kaare Klint and Borge Mogensen for starters. They were taking the best historical forms, removing ornament, but keeping the joinery as first-class.
The Tage Frid 3-volume set might be a good place to look. The third book, “Furnituremaking,” in particular, which presents something of a hand tool approach to Danish Modern style pieces, may give you some inspiration.
https://www.thriftbooks.com/w/tage-frid-teaches-woodworking_tage-frid/1777668/#edition=3279099&idiq=10420719
https://www.thriftbooks.com/w/tage-frid-teaches-woodworking-book-3-furnituremaking-a-master-craftsman-explains-18-of-his-favorite-designs-with-complete-plan-drawings-and-photographs-tage-frid-teaches-woodworking_tage-frid/277096/#isbn=091880440X&edition=3790125
As someone also conditioned from birth on clean lines and Ikea, I would suggest you might find Chris Beeckvoort’s Shaker Inspiration rather, well, inspiring! I know I very much did; so much so, in fact, that before I croak, I want to have had a go at a 15 drawer chest and a long case clock …
Not sure if quite the style you are after. I really like the work by Christian Becksvoort. His LAP book Shaker Inspiration has the some simple measured drawings for his nicest dozen or so pieces.
I am starting on my 1st Gibson chair this morning.
I realized too late that all the stock for this one is 5/4 or more except the arms.
I have a lot of hickory that is just under an inch.
Can I get away with using it for the long sticks?
If the stuff has dead-straight grain, absolutely. Hickory is tough stuff.
Thanks
I had quite a bit left over from building a 3 legged table for kitchen.
The cabinets are hickory
I love/hate that wood – the love child of concrete and wire rope.
Hi Chris,
It’s been great following you on what has come across as a most enjoyable and successful trip around Scandinavia over the last few weeks! So here’s wishing you a speedy recovery from the jet lag!
I also have a question this week: in The Anarchist’s Tool Chest, pp. 383 f., you say that when using Eastern White Pine for a chest that is going to be painted anyway, there’s no need to discard any sapwood from one’s boards, as it is near enough the same, strengthwise, as the heartwood to make no meaningful difference.
Twelve years on, are you still of the same view?
I’m asking because there’s a certain amount of sapwood in the (quartersawn) boards I plan to use for my chest, and although they were selected to provide more than enough material from heartwood only, it would of course be rather more economical (and might save me a few joints in making up the various panels) if I could plan my final cuts irrespective of the heart/sap divide.
Cheers,
Mattias
Sapwood is as strong as heartwood in pine. The only key difference is its vulnerability to woodworm. Here in the States, it’s not a problem, but in the U.K. (and I suspect Europe) wood-boring insects love sapwood. So you might want to ask around in your area.
Thank you, Chris! I have never, that I’m aware of at least, been the direct victim of woodboring critters, but it is nevertheless a very valid point, and as Erring on the Side of Caution is my middle name (yeah, I know; I blame my parents), and there is more than enough heartwood to make the chest out of anyway, that’s what I will go with, then!
Cheers,
Mattias
For what it’s worth, I built Chris’ mule chest a year ago out of EWP with the intention that it’ll live outside (on a covered patio out of the elements). So far after a summer and a winter on the east coast it’s the same as the day I finished it.
Any tips for drilling straight holes of larger diameters (say 3/4” or 1”) without a drill press? I’ve been using a combination square on end, but it’s kinda hard to visualize the center line of the bit to reference by eye. Also the 6” square is too long to reference against the bit. Just screwed up the holes on my Moxon Vise. Thankfully it was just construction lumber. Thanks!
In those situations I make a drilling guide. Basically a big doweling jig for the larger diameter bits. It can be a piece of 8/4 with one perfect hole drilled through it. Then you place that over your desired location for a new hole.
You can also build up the jig from smaller parts to box in a bit at 90°. I will say that longer bits (augers) are easier to wrangle than short Forstners etc.
I’m not Chris, but if you’re using an electric drill you could stick a cheap bullseye level to the back end and then hold the drill vertically. If you’re using a brace and bit, James Wright (Wood by Wright) recommends using a metal ring to make sure you’re holding it level (hold the bit horizontal, slip the ring over the shank, and watch for the ring to slide forward or back).
Sellers discusses making and using a guide in this video here, if it’s helpful: https://youtu.be/AKVwcdi15Fg?t=435
Any tips on how to sink cut nails so the heads are flush? I’m planning to make a boarded bench with rose-head nails. I’ve used them on one other project and they worked well except that the entire head (sharp edges and all) stood proud of the wood, which wouldn’t work well on the seat of a bench. What should I do differently this time?
Not Chris, but you could try drilling a countersunk hole with a Forstner or brad point bit before putting the nails in.
A countersink or counterbore will work. But roseheads and other headed nails are supposed to be proud when on show surfaces.
The main reason I don’t want the heads to be proud is that their edges can be a bit sharp for something that people will be touching frequently. Do you ever smooth the edges of the nail heads with a file or sandpaper?
Nope. There are roseheads from Acorn/Tremont that are coated with black paint that are quite smooth.
Thanks!
Välkommen hem! Looking forward to hearing more about the Swedish tool chests.
I am getting ready to start a second Gibson chair and want to tweak it a bit from the templates. Specifically, I want to make the seat narrower side-to-side (~23″ instead of 25″). Is the best approach to keep the rear portion as is and only adjust the total length of the seat and angle of the rear clipped corners? So the rear seat arc, arm post, long-stick, and rear leg positions remain unchanged. The short-sticks and front legs move 1″ closer to the mid-line and the angle of the clipped rear seat corners becomes steeper (hence preserving the depth of the right-angle sections connecting to the front)? Or is there a different approach you would recommend? Would you suggest any changes to the arm templates in that case, or only shorten/lengthen the sweep of the arm arcs if one wanted to change the angle of the back?
Your approach sounds fine. I would try to keep the back geometry and dimensions the same. The arms come together close back there.
I can’t say much about changing the angle of the back, however. That would require different arms to do right.
I have really enjoyed your posts while you have been gone especially regarding the Swedish toolboxes. I don’t use toolboxes in my shop, I hang them on the wall next to my bench but ever since Scott Landis wrote “The Toolbox Book”. I have been fascinated with slant lidded boxes such as the Dutch tool chest featured in his book and lots of LAP material as well. I have 2 slant topped boxes that was built by my late father and grandfather who were both carpenters. I think I know the answer to my question but here goes anyway. Were the older boxes that we see here in America built along those lines influenced by the Dutch and Swedish boxes. Both of my boxes just have the slanted Lids but no drawers, tills, racks etc. I am going to build a new lid for my grandfather’s box and keep it in case I ever take a class and need to travel with a tool kit.
Who can say for sure? But slant-lid boxes are everywhere on farms (for tack and feed), in kitchens (tater and onion bins) and anywhere else you need rough-and-ready storage. A lot of campaign images show these chests in use, particularly on pack animals.
They are ubiquitous, that’s the best I can do. Sorry.
Yeah, I’m “that guy” (what can I say; I’m in copy editing mode!). “The Toolbox Book” is by Jim Tolpin.
Have you ever investigated the Kestrel chair from Ireland. Another stick chair variant.
I don’t know the Kestrel chair at all. And a Google search didn’t turn up anything familiar. If you could send a link perhaps?
I’m sorry wrong name. The Leitrim chair.
Well if we are thinking of the same chair, the Leitrim is the inspiration for the staked backstool in “The Anarchist’s Design Book.” A lot of backstools, modern and old, use a similar format to the Leitrim. Very basic, but very useful. Check out the great series “Hands” to watch a guy build one (if you haven’t already).
Where do you store your hammers in the DTC?
In the big lower case.
What sharpening stones do you use for your hand plainers and chisels?
Thanks!
Shapton Pros – 1,000, 5,000 and 8,000.
The shapton pro stones are soooo good.
I am sure this has been addressed by you somewhere in the past, but I can’t find it. What is the thinnest rough stock that you could safely/comfortably use for a chair seat? Is 5/4 pushing the envelope a little too much?
1-5/8″ – without battens below. Once you get thinner than that, you need to consider cross-grain battens that are inserted into the seat with sliding dovetails. It’s a very common Alpine construction. Google brettstchul for photos.
Hi Chris, Thanks again for the opportunity to have questions answered by knowledgeable and experienced woodworkers. (I’m new to the trade and just one day older than you).
I would like to ask you a question regarding the new Veritas Box-Maker’s Plow Plane. Probably you are not familiar with it but it is veritas’ take on the Record 043 plow plane.
I saw your short video on how to make stopped dadoes when working for Popular Woodworking Magazine (sorry about mentioning that name).
My biggest concern with Veritas’ plow plane is that the fence is fixed. I like everything else about it. I’m working 100% with “hand tools” only. So, using holdfasts and other work holding devices for wide and narrow stock is important to me and the Record 043 allows me to move the rods any way I need to.
Some weeks ago I send the same question to LAP but it didn’t make for a response (or I have no clue how to find it). It was key to me to learn from someone with experience making stopped grooves with it , so I could make a smarter purchase. As I couldn’t wait much longer to buy it, I decided to go with the Record 043. I purchased it directly from the UK. Price wise was almost the same as buying the brand new Veritas (actually the Record 043 was a bit more expensive but it is in almost pristine condition, complete in box and with instructions). I received the plow plane Yesterday and I have not unpacked it yet.
Regardless of having made a smart purchase or not, I would still like to learn your opinion about it, if you can.
There are some short and longer videos on YouTube about the new Veritas Box-Maker’s Plow Plane in case you need any of them as reference.
I am aware that you decided to replace your Record 043 for a wooden one (according to one of your blogs when selling it), so that could be an even better option, but for someone just starting I would be more than happy if I can speed up the stooped grooving process with the small metal version.
Sorry for the long story, but I wanted to provide as much relevant information as I could, and it is still just one (1) question.
I tend to buy everything new from Today’s great quality manufacturers when I can (think everyone going to Handworks 2023) because I’m not good at restoring nor have the knowledge to do it, nor have a reference of what is good or not. But in this case I went with what I could “tell” was the best vintage I could find.
Thank you for your time, help, and for doing everything you do for the woodworking community.
All the best,
Edward
Hi Edward,
I thought I answered your earlier question. Forgive me if I missed it.
I still have an 043 (I bought one last year to replace mine) so we have one for student work. It works great as it always has. My only quibble with the old Records is that sometimes the irons are too soft. So look out for premature edge failure.
I’m afraid I don’t have much more to add – you made a great lifetime purchase.
Thank you so much!!! You just made my day! and that’s more than enough for me coming from you! Sorry also if I missed your previous answer. I have a Veritas’ Combination Plane, and I read somewhere (or saw it somewhere) that the narrow blades (1/8”, 3/16” 1/4”) work fine with the Record 043. We’ll see. Have a wonderful rest of your day, and welcome home!
Hi Chris, hope all is good. Sometimes you have to take a vacation to rest up from a vacation. I have made a couple of back stools and making parts for a arm chair. I’m using SYP 2×12. My problem is making the tenons for the stretchers and sticks. I am using plug cutters- tenon cutters. The 1″ and 3/4 cutters work good but 5/8 and 1/2 look like my dog chewed them off. Any suggestions? They work fine on oak. I do not have a lathe.
I’m sure the soft earlywood gets chewed up. I probably would use the tenon cutter to make them over-thick. Then shave them with a block plane to final size.
We all look forward to hearing more about your vacation discoveries!
I’ve made a 6 drawer walnut cabinet carcase dovetailed at all four corners. I will put another top over the structural top, grain running parallel on both boards. Does wood movement need to be considered, or do you think they would shrink/expand in concert with no cracks if they are screwed together tightly from underneath?
Screw it down tight. Its movement is sympathetic to the case sides. That’s the traditional way.
Whoop! Thank you!
Chris – thanks for doing these sessions.
I was wondering if you could comment how the Leaning Shelves Bookcases (Popular Woodworking #149, August 2005) held up over the years?
Thanks.
My youngest had them in her room for 10 years and they got HARD use. Then they went off to a cousin/niece/nephew. So I can’t say anything more I’m afraid.
Did you coin the term “vernacular furniture?” I used it in a conversation with my wife when discussing the staked chopping block I made that lives in our driveway now. (It sees more coffee mug bottoms than keen axe edges, as we coerce our 2 and 4 year old to Get. In. The. Car.) Anyway, she strongly disagreed with my usage of “vernacular” applied to physical objects. Googling it briefly has only returned results of your writing. Happen to have any citations to pass along so I can prove I’m right?
There is a mountain of academic literature devoted to vernacular objects, including furniture and architecture. I sure as heck didn’t coin the term. But I also stay out of domestic disagreements.
Wise. Off to the library catalog it is. Thanks for unwittingly participating anyway.
Hi, is there among the chairs you make and describe in your books/videos one that would make a good dining chair?
The two comb-backs in “The Stick Chair Book” and the the design in my stick chair video are all very good dining chairs (that’s what we use).
I’ve had good luck converting LAP’s Peter Galbert plans into a stick side chair. Cherry seats and comb. Maple sticks and legs. Octagonal undercarriage. The only changes were a D shaped seat and all 5/8 sticks. Kept the resultant angles but moved the legs out a bit on the wider seat. I’ve made 6 so far. Call them North of 60 Windsors.
Welcome back, me! I spose now we’ll have to stop acting like kids, joking about farts and prolapsed ani.
Morning Chris, what is your preferred finish for a dining/kitchen table? I’ve been back and forth on your “shop finish” you posted about, or soft wax. Want something thats natural looking, but still adds some protection. Thanks.
I use soft wax because it is easy to repair. So easy.
I am investigating hard-wax oils now, which are a little more durable.
I avoid film finishes on tabletops now because when they fail, they are very ugly and difficult to repair. So my compromise position is: shellac. Somewhat durable. And easy to repair.
Sorry I don’t have a magic bullet answer here.
All great info and helpful. Thanks!!
Good Morning Chris,
Thanks for taking the time to do this again today. I hope you feel better from your cold. I had a question regarding finishing a workbench top. I flattened my workbench and was planning to apply Minwax Antique Oil (I believe this is similar to your “shop finish” recipe described in the Anarchist Workbench). I wanted to see how long you typically let your finish cure before resuming working on your bench.
Thanks again,
Jacob
That will work fine. I’d use only one coat. You don’t want to build up a slick film on a workbench. Depending on humidity etc., it should be fine to use in a few hours.
During the last couple decades I’ve switched to using linseed oil only (raw or boiled) on benchtops. Thin coat. Wipe on and wipe off. And done. Ready to go in a couple hours.
I really appreciate the guidance. Thank you.
Welcome back Chris. I read your blog a while ago about using recovered sunk mahogany. Could you please provide the contact information again? Is it possible to get this wood in for a quarter thickness? I have some projects I’d like to do using mahogany in much like you, I do not want to buy green washed. Honduran mahogany.
Additionally, do you know of a good organization where I could donate some money so that they would plant some hardwood trees on my behalf? I am starting to think I’d like to have some hardwood trees planted to make up for the wood I am actually using. Many thanks.
That was decades ago and the company is long-gone. If I were buying it today, I’d get it from Hearne Hardwoods or another top-shelf dealer. https://store.hearnehardwoods.com/?filter_species=mahogany-sinker
For Karma, I support the American Chestnut Foundation as my personal wood charity. I’m sure other readers could suggest similar pro-planting organizations.
Thanks Chris. I will reach out to Hearne and others. I’m curious to see what other organizations folks can recommend. My favorite wood is cherry; would love to support that but open to other suggestions as well.
Hi Chris,
Tell me again why I need a lump hammer. Thanks
I find it’s a superior tool for assembly and disassembly of casework and chairs. It has more punch than a wooden mallet in a small format. It is great for setting/unsetting holdfasts. It is great for persuading all manner of things that are stuck. You can get a cheap one at Harbor Freight to try it out. Or on ebay.
Good morning and welcome back. Wanted to get a status on the new warrington hammers. Any updates on when they will be available for sale?
I hope in early August. Our machine shop has been cranking out the heads. The handles are done. But the assembly process hasn’t cranked up yet.
Chris, what are your thoughts on the Mendlesham chair? I discovered the form while watching a British farm show years ago, and I’ve long wanted to make something like this. I did read the excerpt you published back in 2020. Have you ever built one?
I’m afraid that form is way outside my area of expertise. There is a lot written on the form in the literature in the U.K. Not as much here. Sorry.
Welcome home, Chris. A quick one for you: Have you pretty much stopped using tapered tenons in your staked furniture? I have the impression that you use wedged cylindrical tenons now. If yes, any particular reason? More attractive? Just as strong? Easier?
Gosh no. I use both joints and don’t have a preference.
The tapered joint is ideal for a classroom environment because you get four or five chances to dial in the angle with a reamer. The cylindrical joint is fast, uses fewer tools but is unforgiving.
When making a reproduction, I tend to use cylindrical. When making modern-looking chairs, I use tapered.
I’m returning to woodworking after a 5-year hiatus (lived internationally with no shop or tools). Excited but also having a mental block on how / where to start. Would love to tackle a stick chair. Any suggestions on getting going?
A good place to start is with a staked stool, such as this one:
https://blog.lostartpress.com/2023/04/09/3-legged-staked-stools/
It will get you using the joints and the geometry. From there it is a shot hop to chairs – promise!
Welcome back Chris. If you were teaching a “History of Furniture Design” class, what would be on the reading list? I don’t know Chippendale from Gropius.
Hi Chris:
What problem did you have with the Domino XL that you had to
send it back a few times ?
The motor died twice. The rails are sticky, even after three servicings. I have asked for a replacement (I think I got a lemon). But no joy.
The small Domino has been flawless in service.
I have a beautiful traditional windsor chair. It’s a bit tall (17”) for my wife so we’d like to cut it shorter by 1” or 1 1/2”. I’m wondering if it would affect the stability.
Currently, back legs rake so their feet line up with the center of the rearmost spindles (at the seat); their splay puts back feet on the far side of the arm stump. Front legs are 1.5” in front and splay 1” outside the seat.
If i shorten the legs 1.5”, the back legs rake put them just inside of the back spindles (where they exit the seat); their splay would line up just inside of arm stump. Front legs would be 1.25” in front of the seat and splay 1/2” outside the seat.
Would i ruin my chair if i shortened it?
Thanks very much!
On the face of it, it sounds like it would be a bit back-tippy if you shortened the legs. I could be wrong, but there is no “undo” button for this operation.
I have a low footrest for guests who have shorter legs. Which is an option….
Hi Chris, welcome back.
I have been woodworking for about 4 years (“self” taught), and been a non hands on enthusiast for probably 10 more. I took your recommendations to heart and my bench planes are a Stanley type 11 no.5, an LN no.8 and an LN no. 4. I used them to build my workbench and they have served me well. The problem is I am now turning from larger scale work to boxmaking. In boxmaking I find the no.8 to be clumsy, as well as difficult to use on long edges. I’m considering 2 planes, a no. 6 to use as a small parts jointer and a veritas no. 7 custom which has an optional fence for registering against the face of the board. At what point is it reasonable to adjust your tools, or should I just plow on in the name of honing my skills?
Feel better, jetlag is a B
I always try to use the tools I have at hand.
A No. 5 with a straight iron is an excellent jointer for small bits. And you can buy an aftermarket fence. In small work I use a block plane instead of a smoother and camber the iron.
If you want more tools, feel free. But usually you can use existing tools and adapt them slightly instead.
I have the blue spruce mallet in the 13 oz, and it’s great, but it lacks an oomph that I want. (I build household furniture.)
Is there a noticeable difference between the 13 & 16 oz versions?
Or would I be better off going with the rectangular mallet if the 13oz is not meeting the mark for me?
Thanks!
I haven’t found a use for the 13 oz. The 16 oz. is great for dovetails and generalized carving/chopping.
The bigger mallet is better for assembly/disassembly. It’s a bit bulky for chopping.
thanks!
Hi Chris, welcome back.
I have been woodworking for about 4 years (“self” taught), and been a non hands on enthusiast for probably 10 more. I took your recommendations to heart and my bench planes are a Stanley type 11 no.5, an LN no.8 and an LN no. 4. I used them to build my workbench and they have served me well. The problem is I am now turning from larger scale work to boxmaking. In boxmaking I find the no.8 to be clumsy, as well as difficult to use on long edges. I’m considering 2 planes, a no. 6 to use as a small parts jointer and a veritas no. 7 custom which has an optional fence for registering against the face of the board. At what point is it reasonable to adjust your tools, or should I just plow on in the name of honing my skills?
Feel better, jetlag is a B
Camber on on foreplane – I have a scrub plane for more aggressive cuts, the 8 inch camber works great but there is too much tearout – I can’t get the chipbreaker close with all the camber- I was wondering if you have a suggestion for a camber where you can still use the chipbreaker, maybe something correct for a less aggressive cut, like a foreplane?
I don’t care about tear-out with a jack or fore. The other planes remove it. Also, tearing is usually minimized by working across the grain.
A closely-set chipbreaker on a foreplane will make it exceedingly difficult to push.
If the tearing offends you greatly, consider trying a toothing iron for rough work. Leas tering. But slower.
I’m asking because I had tearout that a small family of mice could move into. after the jointer and the smoother I was left with tiny deep pockets.
I just decided that I am going to Handworks in September. What are some of the things you are most excited about at that event? What should be on my must see/must do list?
My favorite parts of the event:
I get to spend a half day visiting every vendor. Watching demonstrations. Keeping an open eye and mind. There is so much knowledge and skill at the event, that I just try to observe, ask and learn.
The people. Make friends there. Get a meal and/or beer together. Don’t say “no” to any invitation.
making sliding dovetails – what angle would you suggest for softwoods and hardwoods?
I usually use 15° or 16°, regardless of the wood. I haven’t found much reason to use a different angle.
I’m building an Anarchists Workbench (just did the first bench top glue-up). For space reasons, it’ll be closer to 6 1/2 feet long rather than 8 feet. Should I just knock off 18 inches from the long stretchers and call it good, or should I make the base a bit longer?
I’d probably reduce the stretchers by 10″ or so to keep a wide footprint for the base.
Hey, just wanted to share some Norwegian/Scandinavian woodworking tradition with you. First of, I saw you mention in a post a danish ‘fugebænk’, it’s called in Norwegian ‘skottebenk’ a ‘fuge’, in Norwegian at least, is what you might call a seam or a notch, and ‘skotte’ is a shooting board in English. this benches where used for both purposes. you can read more about them if you search ‘Norsk Skottbenk Union’ in google. or go to skottbenk.com. Have you seen the box chair from the Oseberg find or the Lund chair from sweden dating back to the viking age? I it has a strangely familiar Scandinavian designs.
Thanks! I have seen both those pieces. Many vernacular pieces would look really modern if stripped of their age and wear….
Hi Chris,
Do you have any updates on the cricket table book?
Not Chris – but I’m editing it, so… Derek turned in the text early this year, and I’ve edited it and done most of the layout. Right now, we’re trying to sort the last of the image challenges. Then it will be back to Derek for review, then a copy edit. So it’s pretty close!
I have some neat old panel saws that I would like to get working again. Some are straight but some have some bend to them, no hard kinks. Is it possible to bend them back to shape? Does it really need to be dead straight?
They don’t need to be dead straight. Many panel saws and handsaws have a shallow bend along their length and cut just fine. I’d sharpen them up and work with them before you try to “fix” them. Bad Axe/Saw Sharp has some great tutorials on fixing up saws.
Here is a very good Youtube tutorial on straightening hand saws.
https://youtu.be/N_KikzIarLg
Chris,
I have enjoyed reading your books and am impressed with the crucible tools. I bought 2 of your holdfasts and a planning stop. Very nice castings. I tried to sharpen the planning stop, and I found it to be very hard. The file was skating across the underside of the teeth and leaving dull tracks across the file. I used a belt sander with an 80 grit belt and cleaned up the top of the stop. The top was quite flat to start with and the belt sander took a lot of sanding to get it mostly cleaned up. I also tried the underside of the teeth with the belt sander and it was having trouble cutting it. As a test I filed a couple of edges on the holdfasts and they filed ok. Any suggestions for what I am doing wrong and how to proceed?
Hi Greg,
I am surprised and bemused. I have sharpened a lot of our planing stop with sandpaper and files with little problem. I’ve also used a wheel grinder and a die grinder. All I can guess is that you got an unusually hard one? Sorry I’m no help here.
I am finally getting around to building the Anarchist tool chest. It has really been a fun project so far–although I am just starting on the lid. So we will see how that goes since I do not have either a mortising machine or a table saw. I plan on putting wheels on it and am wondering what size do you typically use. Thanks.
(I am very envious of your trip to Scandinavia Sounds like it was a good trip.)
Not Chris, but I’ve built more of these lately than has Chris, so… I use 3″ casters (I like these in particular: https://www.amazon.com/gp/product/B07V9Q18V1/ref=ppx_yo_dt_b_search_asin_title?ie=UTF8&psc=1)
You can dowel or domino the lid fyi I doweled mine saves a little time and you will never know cause of the skirt
Good morning, I hope you enjoyed your trip, I certainly enjoyed the pictures on Instagram so thank you for sharing those. As for the questions, I’ve been restoring some old Stanley’s and have found that the irons all taper slightly in width, Which makes checking squareness rather awkward. They’re from different time periods as well as different sellers. Doesn’t really affect anything just curious if you’ve found this in any of the vintage planes you’ve restored. And the second, what’s your preference or thoughts on the means of reducing friction on tools? I believe I read, probably from you, that historically tallow was used on the soles of planes. Does this have any benefit over wax, or was it likely just cheaper than wax way back when. Thanks again.
I’ve noticed that older plane irons can taper in width and thickness. But I haven’t noticed that with more modern stuff. As you said, as long as you know it’s there you can compensate.
On lube, I usually use paraffin (canning wax from the grocery store). I also have an oily rag that helps speed the plow.
Mutton tallow was common as a tool lube back when mutton was common in the kitchen. It’s not so much now. If you feel the need to be traditional, you can try Crisco….
When I drill a? say, 1/2 inch hole in a leg for a stretcher and when I drill out the round tenon on the stretcher with say the Veritas round tenon cutter (or any tenon cutter for that matter as I often use ray iles tenon cutters) the hole is always slightly too big. It’s never tight. Do I need to adjust the tenon cutter or is this just a thing that happens.
You need to adjust the tenon cutter. Or grind the bit a little smaller (if it’s a spade bit). The bit and tenon cutter needs to match so that you produce tight holes.
Thanks for helpingallseekers on the path to woodworking nirvana. I have a question about the suitability of mesquite for the seat of a stick chair. I planks that I milled from a yard mesquite. Here, with regular watering and attention when young the resulting wood can be relatively strtaight for sections 2-4 feet long. Mesquite is quite hard but easy to work in general, but I worry that it may be too prone to split
Mesquite would be great for a stick chair. Go for it.
Welcome back Chris. If you were teaching a “History of Furniture Design” class, what would be on the reading list? I don’t know Chippendale from Gropius.
(I promise never do this from my phone again.)
I get asked this a lot, and I don’t have a good answer. I’ve never found a book that adequately covers things. If it were an academic class, I’d have the series of books “A Cultural History of Furniture.” They are expensive, but give a good overview.
Then I’d probably use other books to fill in the history. Chippendale’s “Director,” William Morris’s writing on furniture. Gustav Stickley’s catalogs and The Craftsman catalogs, Hayward’s books and writing on English furniture design. “The Atlas of Furniture Design” to cover chairs. “Oak Furniture” by Victor Chinnery. “American Antiques” series by Highland House Publishers. “Furniture Treasury” by Wallace Nutting. “One Good Chair” by Hand Wegner.” Gloag’s “A Social History of Furniture.” Kassay’s “Book of Shaker Furniture.”
I could go on and on….
Hi, I have both the Sharpen This book and the videos however I don’t recall you mentioning anything about the generic 3 bladed pocket knife? Just sharpen like any other edge tool and work with the factory bevel (if it still exists)? Any tips and/or tricks? Welcome home – you posted great pics from your trip, thanks. Frank
I use the knife sharpeners for kitchen knives.
The AccuSharp is great. Fast. Cheap.
https://blog.lostartpress.com/2022/11/07/2022-anarchists-gift-guide-day-1/
Hey Chris, hope you feel better soon! On your post “The Anarchist’s Tool Chest at Age 12″ (1/1/2023), there is a small, hinged brass tool laid out on your apron in the fourth pic. I can’t find any mention of what it is… Looks to be about 3.5″x1.25”, has wood inlays similar to the Vesper sliding bevel. Thanks.
It’s a Bridge City saddle square. They made a bunch of them back in the day. They are available on the used market, but are pricey. A hinge works just as well.
Hi Chris,
I have a quick question about Jack plane set up.
Will it be easier to take thicker shavings if the chip breaker is set further back from the edge of the blade?
I keep the blade nice and sharp and wax the sole frequently but still find it can difficult to push.
I also skew the plane as this helps.
Thank you, as always, for your time.
Ray
I have the breaker set well behind the curve of the blade. So maybe 1/8″ back.
The No. 1 way to take thick shavings is to have a curved blade. (8″ to 10″ radius).
No. 2 Wide open mouth. Breaker set way back.
No. 3 Skew.
No. 4 Use your body – not your arms.
Do you have a process for dealing with wheel-wobble in your bench grinder?
It seems lots of wheels come with cheap and sloppy plastic arbor adapter bushings, which leads one to research metal bushings and replacement cup-washers and other possibly-unnecessary fanciness.
Cheers and thanks!
I’ll be honest, I’ve never had a problem with it. Or I’ve never been sensitive enough to it to do something about it.
There are lots of tutorials out there that I’ve seen. But I’ve not experienced the problem. Sorry.
I am wrapping up my first workbench (Moravian, great fun) and looking forward to building a toolchest to protect my tools. While I have a copy of ATC that chest seems a little big to me (my woodworking space is only 9’x6′.) I am currently thinking of making the dutch toolchest. I don’t imagine that the book fitz is working on will be out in the next few months, so my current plan is to get the lie neilsen video schwarz did in 2015. Should I be considering a different toolchest form? Any regrets or considerations you’d suggest up front regarding building a dutch toolchest or a toolchest in general?
The Dutch is ideal for small spaces and for traveling. It’s what I would use in a tight shop space. Other people might have other ideas….
Welcome back! Get lots of sleep and drink lots of water.
Hey Chris, thanks for the pictures of your recent trip. Big fan of the tool chest. This might be the one that finally speaks to me.
Got a wood species question for you. Do you have any experience or insight on Siberian Elm? A friend had one cut and milled recently and supplied me with enough for a pair of lowback stick chairs. I can’t find much info on the species other than it is considered an invasive, and the friend who had it cut down in the first place says it was originally brought here because it grows fast and is (supposedly) great for furniture. Sticks and legs passed the sledgehammer test with flying colors, but the stuff cuts like a dream and is so light that I am suspicious. Thanks for the help.
I don’t have any experience with Siberian elm.
Red elm is fairly light (compared to oak). So that’s not a huge concern. To get a feel for it, I’d try to split some pieces to see if the grain is interlocked, and how much so.
Grey elm is light and cuts easily. But it tends to split. So I avoid it for chair seats, unless it’s all I have.
No matter what, my inclination is to go for it. You will learn some stuff.
What is the best way to attach a heavy stone table top to a wood base (stout legs with M&T rails, etc.). I was thinking maybe wood blocks epoxied to the underside of the stone and then screwed into the rails, with room to account for wood movement. But I worry about something this heavy relying on epoxy. Thanks!
When I deal with stone or concrete, I turn to Tapcons and other fasteners designed for the material. I wouldn’t worry about wood movement in the base. The major concern is wood movement in a tabletop. And you won’t get any with a stone top.
I agree that epoxy is not the best method.