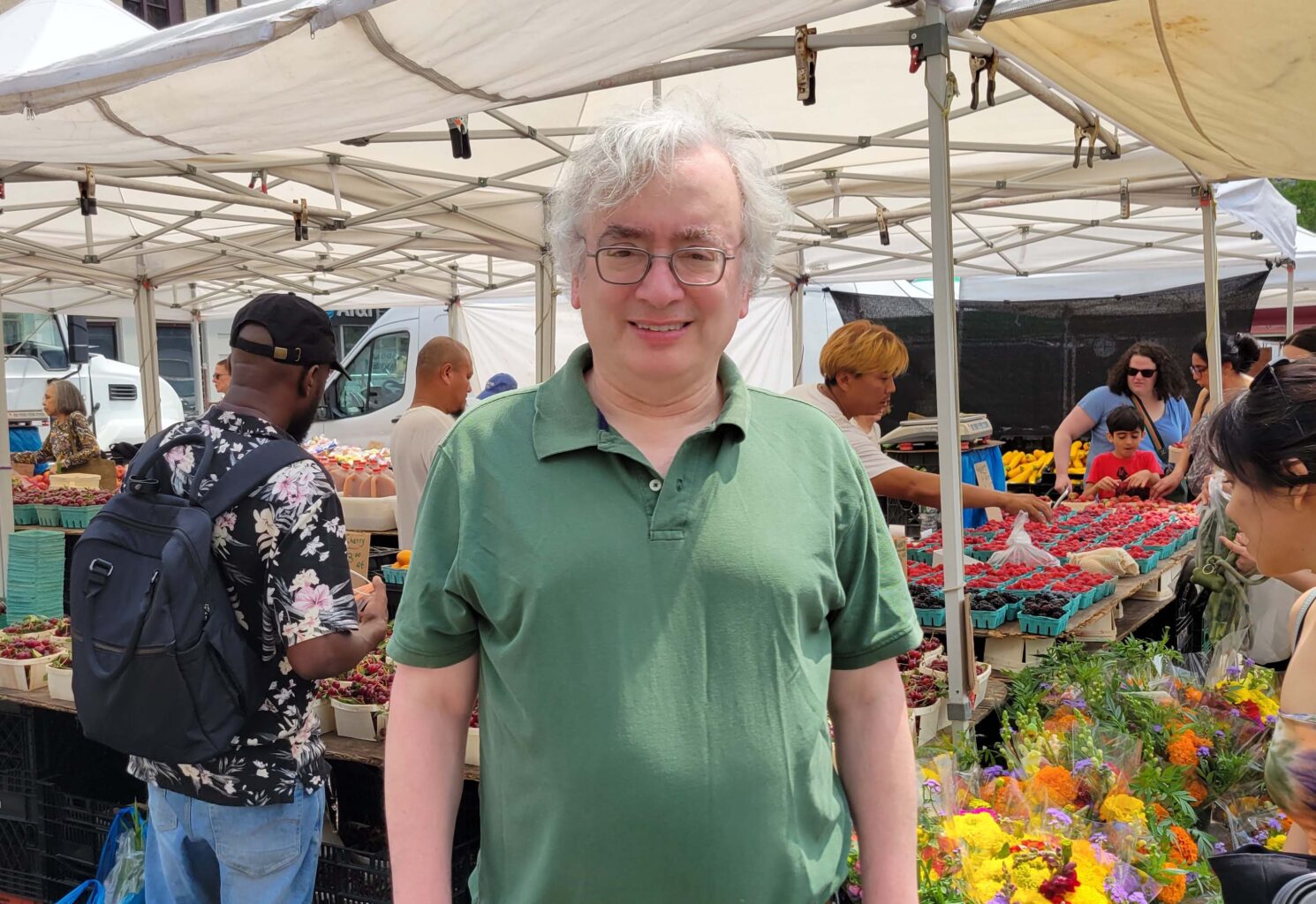
We are delighted to have Joel Moskowitz, co-author of “The Joiner and Cabinet Maker,” and owner of Tools for Working Wood in Brooklyn, N.Y., as the host of today’s Open Wire.
Here’s how it works: Type your woodworking question in the comment field. Joel will answer it. It is that simple. (Note that he will likely not be sitting at the computer all day, but will drop by as his schedule allows to post answers.)
Update: Thanks for all the great questions today, and thank you to Joel for spending part of his Saturday with LAP. Comments are now closed.
Morning gents… Joel, you are a purveyor of very fine woodworking tools. The US used to be a leader in fine hand tool manufacturing. With very few exceptions, it’s all overseas now. Power tools became popular, demand for woodworking hand tools fell, but the demand for mechanics tools was always there. Do you see tool production ever coming back to the states? Is it very high labor cost making it prohibitive? Or is it a lost art and skill gone forever? (On a side note… thanks for folks like Lost Art Press, Lie Nielsen, Veritas, and Tools for Working Wood for rejuvenating the craft…)
Hi Joel. Any input as to why there are always shortages from some of your suppliers? I would think they would hire more people to satisfy demand. Also, do you see demand for some tools going up, indicating a shift towards a new focus of attention? Thanks.
Most of the suppliers we deal with are small companies that have a limited capacity. And demand ebbs and flows. In the case of traditional companies hiring skilled people is hard. Expanding machinery is expensive. And the goal of most makers isn’t satisfying demand, but producing enough to have a sustainable income.
We have a job opening currently for two part-time sales people. We hired one excellent candidate, but there just aren’t enough skilled people sitting around to easily fill the second spot. We will do it, but the lack of skilled labor is a problem. This is what happens when national policy dictates schools would rather churn out lots and lots of unfulfilled business graduates than a few more welders, cabinetmakers, and plumbers. (they don’t even churn out business graduates who took shop in high school anymore)
Joel did you happen catch PBS news last night about Mark Ellison? He made a point that construction is not for everyone, but if you have a desire it is quite rewarding. In the discussion he pointed out that it is possible earn more than many degrees careers. His work and approach to details was stellar.
Brian, This is a very interesting and important question. Certainly in the US lost of skill and know how has disappeared. but technology changes have made a 40 year factory and it’s practices obsolete worldwide. The best power tools currently made in the world are from Germany and Europe; Festool a giant company, and Mafell. Both high cost tools from a high cost country. But none of these places and North America either can compete with low cost labor and a lack of regulation. But why would we want to? The US is caught between two models – the low cost labor low regulation of places like China, and high cost, high regulation of places like Europe, Japan, and Germany where universal health care, far better practical education, and high taxes make it possible and desirable for young people to take a risk and start a company. Unfortunately VC in the US looks for massive returns only and in the case of woodworking national policy in education treats wanting to do things with your hands as something weird. So people like myself are trying to manufacture but it’s hard.
Hahaha… don’t get me (us) started about the demise of Shop Classes my friend! I’m a retired engineer who was blessed with 3 years of shop classes (2 mandatory and one optional) and a dad and neighbors who did everything themselves. It’s astounding to me how many of my younger friends and neighbors are “tool challenged, and have never had the exposure. They borrow you and your tools… you show them how to do something “complicated” like cleaning a lawn mower spark plug, or you give them a cutting board you made and they are amazed. They never had the introduction to working with your hands and the thought of “getting dirty or dusty” hasn’t occurred to them. (But they are incredible at fixing things with a keyboard!) We need more national voices like you guys and Mike Rowe. Sorry for the rant… I’ll go have another cup of coffee now, and then on to my shop for some therapy! Stay safe out there.
Hi Joel, Nice to see you hosting today. Keep up the good work!
Ken C.
Hi Joel. I’ve always been impressed that you’ve kept your operation in NYC. I know it’s expensive to operate there. What do you see are the built-in advantages to trading in NYC. Here, for example, we have incredibly inexpensive real estate.
Thanks for hosting this week while I’m
In Norway….
C
Chris,
Thanks to you and Lost Art Press for giving me the opportunity to host and for all your support over the years. We are in NYC because we love living here. It is one of the safest cities in the US, very low transportation costs, lots of cultural amenities, and a highly skilled customer base doing amazing work for well heeled end users. Real estate is ridiculously expensive because people want to live here. What makes it work is that we have a huge number of walk in professional customers who need high end tools. I just wish I was able to buy a building.
PS. I do however wish I had a job that allowed me to bicycle around Norway and do other fun things.
Joel I have thoroughly enjoyed your blog over the years. Thankyou for sharing your knowledge. I was curious about the details of an edge and stropping. Have you used a jewelers loop or other magnifier to see these details? Thanks
Morgan, Occasionally I have looked at an edge with a microscope but the real checking I do is with my fingers and seeing how well the edge performs. After stropping with a plain untreated strop you can materially feel a change in the edge and see how it performs differently.
The lack of US manufacturing and skilled trades is a huge problem that few politicians seem to want to address. It will eventually bite us. But that is not why I write. I want to express my appreciation for you. As a long-time customer and reader of your articles, I often think how instrumental you have been in my love for carving and woodworking. My question is this: do you have another book in you? I assume life is busy for you, as it is for most of us, but I have always been surprised that you do not publish more. You are insightful and a good writer. Thanks.
Mike, Thank you. I think I have a least one more book in me. My goal is to eventually retire and then walk every day to the main reading room of the public library and work on a book. Fiction probably.
Hi Joel, Another thank you for TFW and your Knowledge and Explainer sections. The internet is filled with “Experts” but very few true teachers and knowledgeable practitioners such as you and LAP folks whose willingness to share is much appreciated. Ron K
Joel,
Question from this 72 year old carpenter turned builder and a so- so woodworker:
Tools for Working Wood? I’ve been through a number of ups, downs and turn a rounds in this profession for 50+ years, plus my having thoroughly enjoyed the tools, the stories and the teachings of two excellent grandfathers (both born in the 1890’s) and also my having been reared, educated and apprenticed in the glorious northeastern US…
How and why did you sense a need (hope- filled I’m sure!) for the creation of such a cool company, A) a company that understood woodworking, woodworkers, B) and in addition to finding and working with great tool makers from all over creation…your wee company to begin making tools!?!? I’m gobsmacked by who and what you all are at TWT- thank you!
Ed Latson
When I was in my 40’s and working as a programmer I realized that I would be unemployable in my 50’s – so I needed to start my own company. The only subject I know anything about except for programming is woodworking tools. So it seemed like a good idea at the time. It’s tons of work but really interesting work. And challenging. We just announced the newest and most complicated project we have ever done. A folding treadle lathe for people who want an intensely satisfying maker experience, but also don’t have a large space.
(see my web site for details)
Similar to Chris’s question above, what are the challenges of being a woodworker in NYC? I’m thinking the space limitations could be tricky for a lot of folks. Are there any hardwood lumber yards nearby? Perhaps there are shared spaces in old warehouses that one could rent out for shop space?
We have several giant lumber yards that deliver. You don’t go to a lumber yard except in desperation. Time is money. Shop space is the big challenge. There are coop shops but more likely if you come here you will find a good of like minded people who share space, or a large shop that rents bench space. The good news is that just about everyone I speak to is socked up with work and looking for people. Skilled people. Here’s the key – if you just spent millions on an apartment spending a million getting to look the way you want isn’t a big deal. The wealth here amongst end users is crazy, and they hire the rest of us.
I’m curious about the average shop size in NYC (not dedicated rented spaces or co-ops but the guy taking up wood working as a hobby) and what kind of tool kit decisions people make and use. for simplicity, let’s say their end goal is to make furniture for their apartment. i have a dedicated 10′ x 16′ room for my shop and live without a table saw. but i suppose that would be huge for the average apartment dweller who might also need to use that shop space as a living space. I’m hoping to find some nuggets that might help me part with some unnecessary stuff (i do use ATC as a culling guide).
IT’s not just the size of the shop. It’s noise. Most New Yorkers don’t have shops – space is a problem. I used to use the spare bedroom and I built a lot of nice stuff in it. My entire shop was: 1 – 7′ workbench. 1 – toolbox. extra tools I didn’t use much were tucked away in another room. 1 – saw bench.
That was pretty much it. Some people use a track saw for sheet goods. It takes planning and patience. Or pick something smaller – carving, lathe work, modelmaking.
Hello Joel,
First I want to tell you how much I appreciate the booklet “Modern Edge Tools”. The section on Plane Spotting always brings a smile to my face because my late father was a B-25 pilot in WW2 and had to know airplanes by their silhouette. As a kid, I was amazed how he could immediately identify a spec on the horizon as a certain vintage fighter (it was practicing for an air show on the shore of Lake Erie). He would have gotten a kick out of spotting hand planes.
Second, you have occasionally covered museum exhibits in your blog. In museums, I have noticed the wide variety of frames around the artworks. Since I carve, I sometimes focus more on the frame than on the artwork. In major museums, like MoMA, do you know if they are generally chosen following any particular methodology? Are they made in-house? It doesn’t seem like that would be just left to chance, whim or to use up whatever stock they have laying around.
“Modern Edge Tools” was a lot of fun to make.
Every museum has a framing department. Depending on the frame – which might be historic they will either leave it along. or some museums like a consistent look and they put everything in the same frame. From a conservation point of view framing is a big deal. It’s not done willy nilly. The Metroplitan has a display of frames.
Check out the frame blog, run by frame historian Lynn Roberts. You will find a ton of painstakingly-researched information on the history of picture frames and framing as well as images of the best of the best frames. They have done several articles on the selection of frames in the National Gallery London that you might be especially interested in.
Hello Joel, two questions. if I worked at TFWW, i would probably eat ice cream at the Brooklyn Ice Cream factory all the time, anybody else there like that ice cream? 2nd question, i love the Gramercy bow saw kits, any plans to make a Roubo frame saw kit?
TFWW is a long way away from Brooklyn Ice Cream. We are in Sunset Park – they are in Dumbo.
Personally I prefer Panna Cafe – near my house but they keep bankers hours and always have a huge line.
Fortunately there are other easier to indulge treats nearby too.
For a Roubo frame saw try Blackburn Tools: https://www.blackburntools.com/new-tools/new-saws-and-related/roubo-frame-saw-kit/index.html
We don’t have plans to make a Roubo saw – all our energy is going into the new lathe (even today that’s what I am doing)
JOEL! What is your favorite block plane?! Thanks for everything!
I don’t use Block planes – My go to plane for just about everything is a Stanley Bedrock 604C which I have had since 1986 (or 7) for tricky wood or just more fun planing I use a Norris 5A (which I have had since about 1987 or 8.
I find block planes too small for my tastes. (I know I am in the minority)
How many people do you manage? What is one or some of your hardest learned management lessons?
It’s a small company about 10 people. The hardest lesson is learning to trust and delegate (something I am still not very good at). Also nobody cares about your business the way you do.
Joel,
A treadle lathe or a spring pole lathe?
Bill
Full sized treadle lathe – folds up for storage. as we can release details we are. Take a look at the website.
Hello Joel,
Recently you mentioned your Stanley 444 plane on your blog, and I had mentioned to you that you should make a video showing its use. Have you ever considered that? As you know there are very few videos on YouTube showing the Stanley 444 plane. That plane could be presented in a series of videos, and the owners would probably not get bored!
Lewis,
It’s a great idea but I just don’t have the time or really the skill for video. Good video is really hard.
A while back I read the series of posts you had on designing the bow saw. I enjoy reading of that process so much that I bought the bow saw to reward the details and insights. That saw always makes me smile when I take it off the rack. Thanks so much for your writing and products you carry and share information on.
I just noticed that the tiny Tom Buhl icon by comment is of me using that very bow saw. Sweet coincidence.
Glad you like it. With the lathe coming out I hope to start talking about that design process in my blog. Right this second I am knee deep in Fusion 360 designing parts. but as a start I hope to have a few hours to organize material on historic treadle lathes, especially ones used by hobbyists.
Signed up for lathe really interested. Especially if it folds. I really don’t want to get an electric one.
Since I was a kid I have always been a lathe guy. (metal though) and I have wanted to make a production treadle lathe for years. And I love the health aspects of it all. But in an apartment it HAS TO FOLD. and that was a challenge. What was really cool is that Kris, the main engineer on this project, had never used a treadle lathe before but when he started using the first prototype he discovered Zen and the art of turning – with a satisfaction you get because you are powering the machine yourself like a hand tool, not just operating a lathe tool. So I am guardedly optimistic this might be a popular tool.
Having a tool that offers a workout sounds exactly what I like. Can I switch legs when one gets tired or will my right leg become twice the size of my left? I am very excited to see more about this lathe.
Joel,
Your Moxon kit is awesome. Made me realize the screws didn’t have to be massive to work really well. I am excited to learn more about this folding lathe! After the lathe are their any tools out there on your radar you’d like to carry? What is your favorite tool you have put out into the woodworking community?
Jeremy, We already stock Ashley Iles turning tools which are excellent. We might also add something very inexpensive just as an add on so someone can get started. Favorite tool? Maybe the Holdfasts – when we first started nobody thought they would be successful – now they are ubiquitous. But I really love everything we put out. Otherwise we wouldn’t put it out.
Hi Joel:
Are you going to have a good mix of your tools at Handworks for demonstration and/or purchase?
Assuming all goes well (and unfortunately we are behind) we will have all the Gramercy Tools and BT&C and a folding treadle lathe. It’s just going to be two people and there is a limit to what we can handle. (my son starts college that weekend so we have a lot going on). IT’s going to be a great show!
Joel, I want to thank you for not only your time today but also for making the pair of holdfast that I use almost daily in my shop.(I don’t go to the shop on Sunday’s). They have never failed to hold whatever I have asked them to hold. Great product!!
Hi Joel
Have you used the Norton ceramic stone? How would you rank it as a polishing stone? What is the best way to clean it?
Have you tried the business card trick to put on a micro bevel, (raising the sharpening jig up by putting a business card under the roller).
What Norton polishing stone? Do you mean they’re 8000 grit waterstone? Or is there something not aware of?
I’ve never thought much of the ruler trick. I’ve never had a real issue turning a burr, unless the edge is in terrible shape. If it is I grind back. And there is no excuse for any modern blade maker to give you a wonky blade. Blades should be either dead flat, or slightly better by being slightly hollow.
Hi
The official name of the stone is “Norton Ascent Ceramic”.
The business card trick is not the ruler trick. You put the roller on top of the card thus increasing the angle from for example 35 to 36 degrees..
I am not aware of the norton ascent. I will call them and get a sample. The only experience I have with ceramic stones like these were a bunch of years ago. They were OK but they clogged. No opinion on these yet.
Since I freehand sharpen I don’t have anything to put a card on. That being said I can trivially add a tiny consistent microbevel freehand. (learned in first day in woodworking school back in 1985
Thanks for doing this! Any plans to sell your 4/4 glue in the 16oz bottle again? Why is it “four four” and not “four quarter”? Also, a selfish question: have you thought about staying open later one weeknight per week, or some Saturdays? I’m in Brooklyn but work a 9-5 job, and wish I could by more often 🙂
We are having supply problems with the glue. Hopefully it will return. Possibly only in gallons. THe problem with more hours is we are working long hours as it is. We did do a Festool Fest and sratch and dent sale a few weeks ago on Friday and SATURDAY. so all is not lost.
Dear Joel,
As all have said already, I want to extend my thanks for making and stocking quality tools here in the US.
As a small business, I assume that the supply chain issues during the pandemic made problems for you and your employees. Have you noticed changes in your supply chains so that they are not as fragile, or have you cultivated alternate sources? My father is a manager for an agricultural pest, soil, and crop production firm. They have had to make orders a year in advance. However, most of their raw materials come from China.
At the risk of being too winded, I wanted to add a few comments to the issue of skilled labor and manual training education. I was told to do well in school, go to college, and get a good, well-paying job. Despite graduate school education, that all crapped out. America is stubbornly fixated on book educated as the height of intelligence and accomplishment. We need to learn that there are many types of intelligences, and that all are valuable.
Most of our supply chain issues have minimized but out costs has skyrocketed.
Just a “Thank You!” I always had trouble getting coping saws to do what I wanted. Not so with your (my) bow saw. It moves like a part of me. (Love the holdfasts, too.)
Aside: If you offered a taller blade for the bow saw for small ripping / resawing tasks, I’d line up to buy it.
Joel, Ditto all those who appreciate all you’re doing for woodworkers. A question about handsaws: I’ve been happily using a couple of refurbished older 26″ saws (an Atkins to rip and an unknown to crosscut). What are the advantages to your BT&C hardware saw? Would I be even happier using one? I do mostly handtool work starting with rough sawn lumber. Mainly common USA hardwoods.
Atkins made fine saws. The BT&C hardware store is shorter, so easier to take to the lumberyard. and it also contains a square. You only need one saw as it xcuts and rips like a demon. Would you be even happier with one. I don’t know. But I certainly would be.
Joel, what wood working tool do you think is underappreciated and no longer made? Would you sell it if someone made it?
Eric,
I couldn’t have asked for a better chance to plug our new tools. “underappreciated and no longer made” – A treadle lathe. And we are planning to sell it as soon as we finish making them. It is the biggest and most complicated project we have ever done!
Good Afternoon Joel,
Thanks for taking the time to do this today. I know that you have written extensively about Norris planes, and I was curious if you thought that the post-war Norris A5s are worth the time to tune up, or if modern options (Lie-Nielsen, Veritas, or Clifton) offer better performance.
Thanks,
Jacob
Post war Norris’ aren’t as perfect as pre-wars but they can be wonderful – (as my 17 1/2″ post war is). I would be really wary of tuning up, as except for a careful flattening if needed it probably won’t need it. I can’t tell you about better performance, norris’s are certainly finickyer than Stanley clones. But they are intensely satisfying to use. when the blades are sharp all work well. When the blades dull Norris doesn’t chatter, it just takes more effort to push.
Thank you!
Hi Joel,
Have you heard anything from Colon Clenton recently? I’ve kept an eye on his squares for a long time, and even asked family in Australia if they’ve come across anything, but now I’m wondering if he’s still in business.
Side note, I own several Gramercy saws, and love them. Thanks for all that you and your team are doing.
Best,
Andy