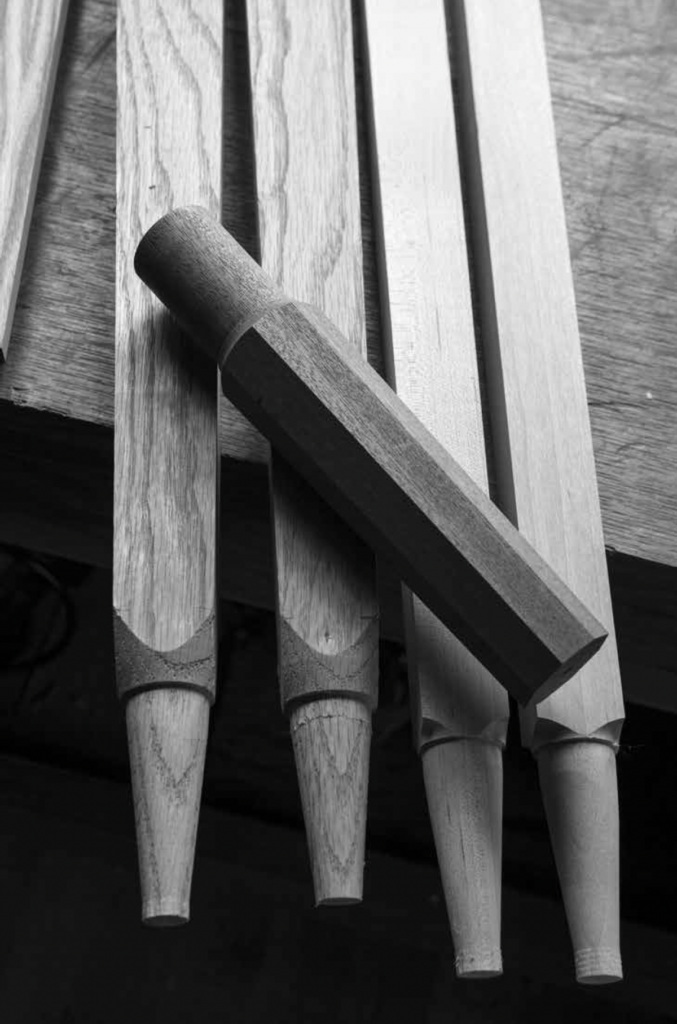
The following is excerpted from “The Anarchist’s Design Book” – an exploration by Christopher Schwarz of furniture forms that have persisted outside of the high styles that dominate every museum exhibit, scholarly text and woodworking magazine of the last 200 years.
There are historic furniture forms out there that have been around for almost 1,000 years that don’t get written about much. They are simple to make. They have clean lines. And they can be shockingly modern.
This book explores 18 of these forms – a bed, dining tables, chairs, chests, desks, shelving, stools – and offers a deep exploration into the two construction techniques (“staked” and ”boarded”) used to make these pieces that have been forgotten, neglected or rejected.
But this isn’t really a book of plans. “The Anarchist’s Design Book” shows you the overarching patterns behind these 18 pieces. It gives you the road map for designing your own pieces.
Cutting tapers on legs with a jack plane and a smoothing plane is simple work if you have only a handful of legs to do. But if you need to do a production run of legs – 10 or more – you might want to switch gears.
One way to speed the plow is with a band saw. Saw the leg square and tapered on the band saw. Then finish the job with a jack plane.
But the easiest way to do it is with an electric jointer.
The first time I learned this process from woodworker Troy Sexton in the 1990s, I thought it looked dangerous. It’s not. I’ve used this procedure for more than 16 years in production work without a single incident. But if you are skittish, skip it.
Troy told me that this operation came to him in a dream. He’s one of the smartest woodworkers I know, and after you try it, I think you’ll agree with me that it is brilliant.
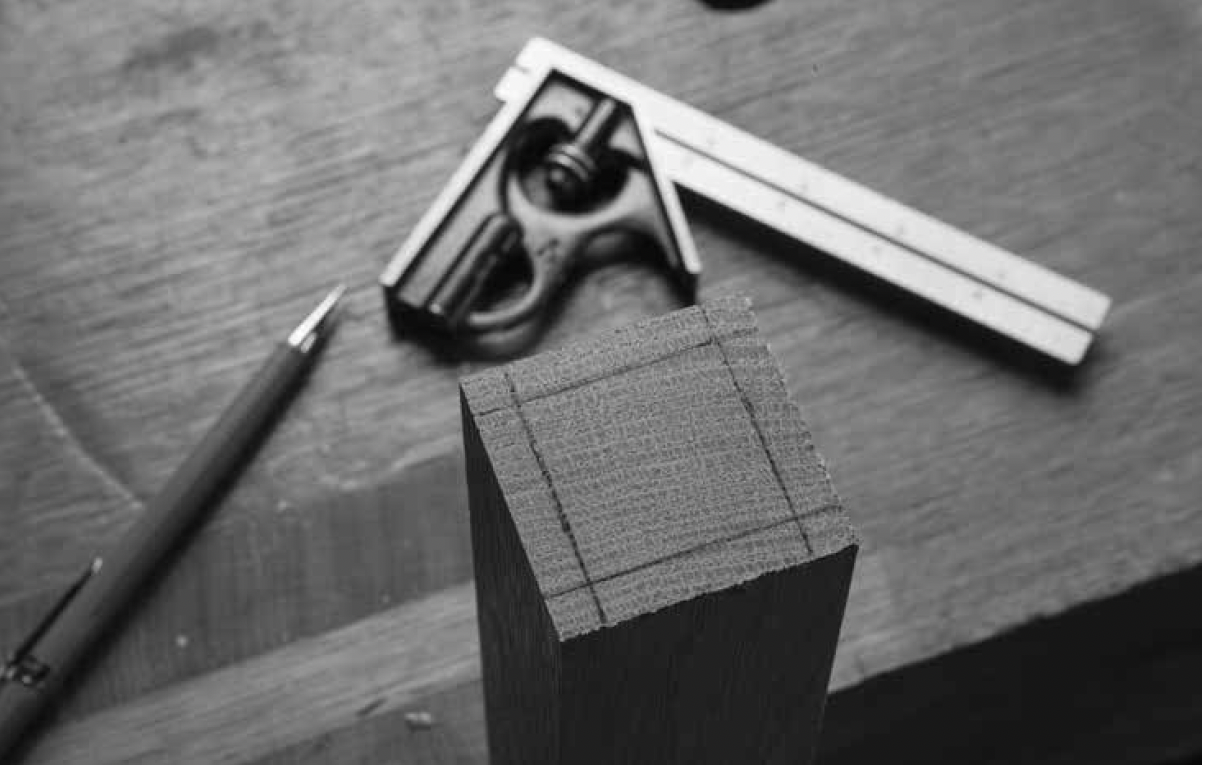
Here’s an overview of the process.
- Decide how much material you want to remove from each face of the leg at the foot. Let’s say it’s 1/4″. So you need to set your jointer to take half that amount (an 1/8″-deep cut). Lock it. You are done setting the jointer.
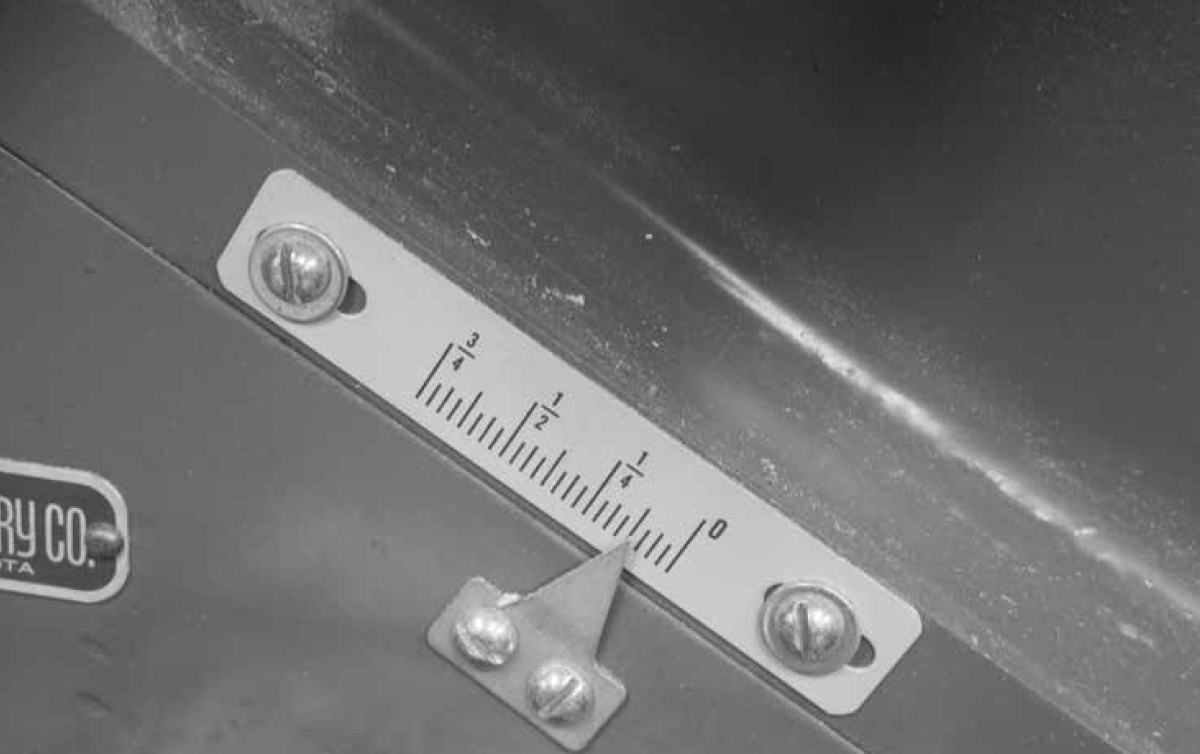
- Decide how long the taper needs to be. Let’s say you have a 30″ leg and you want the taper to be 26″ long. Divide that in half (13″). Clamp a stop-block to your jointer fence so it is 13″ away from the top dead center (TDC) of your jointer’s cutterhead. You are done setting stops.
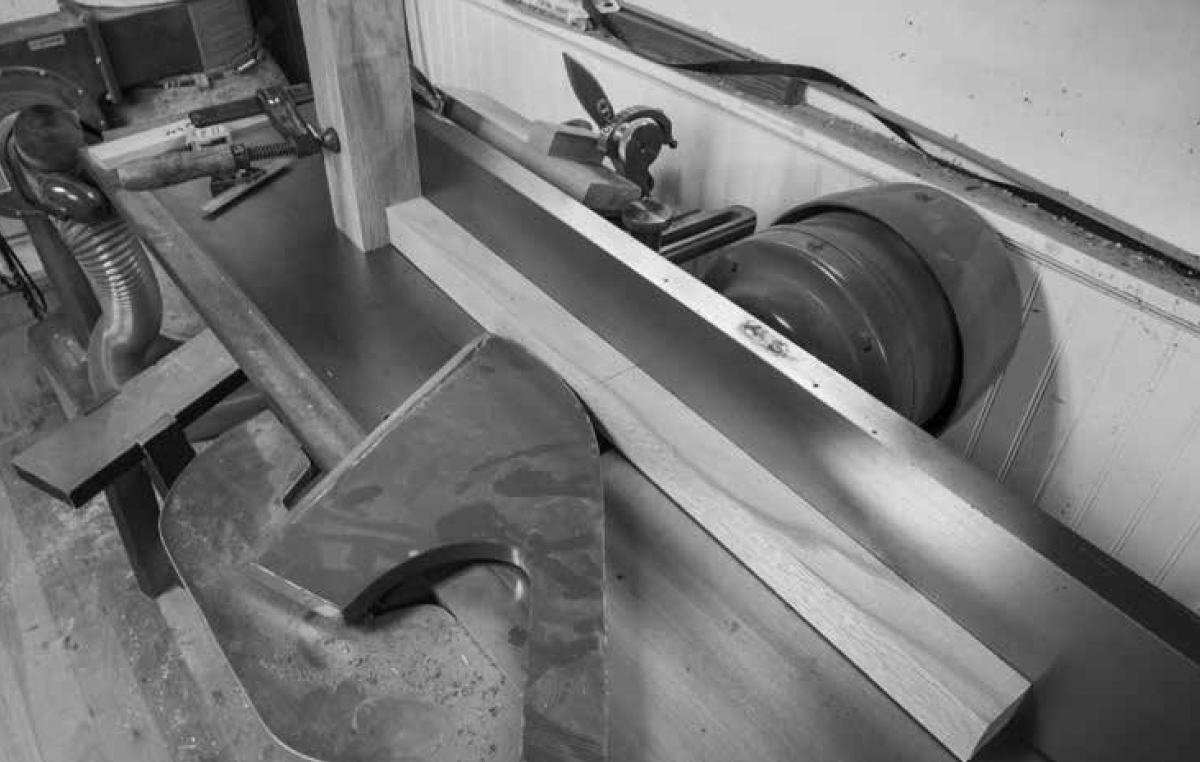
- Take your leg and push it into the cutterhead foot first until it touches the stop-block. Lift the leg off the jointer’s table. Repeat this process for all the leg faces that you want to taper.
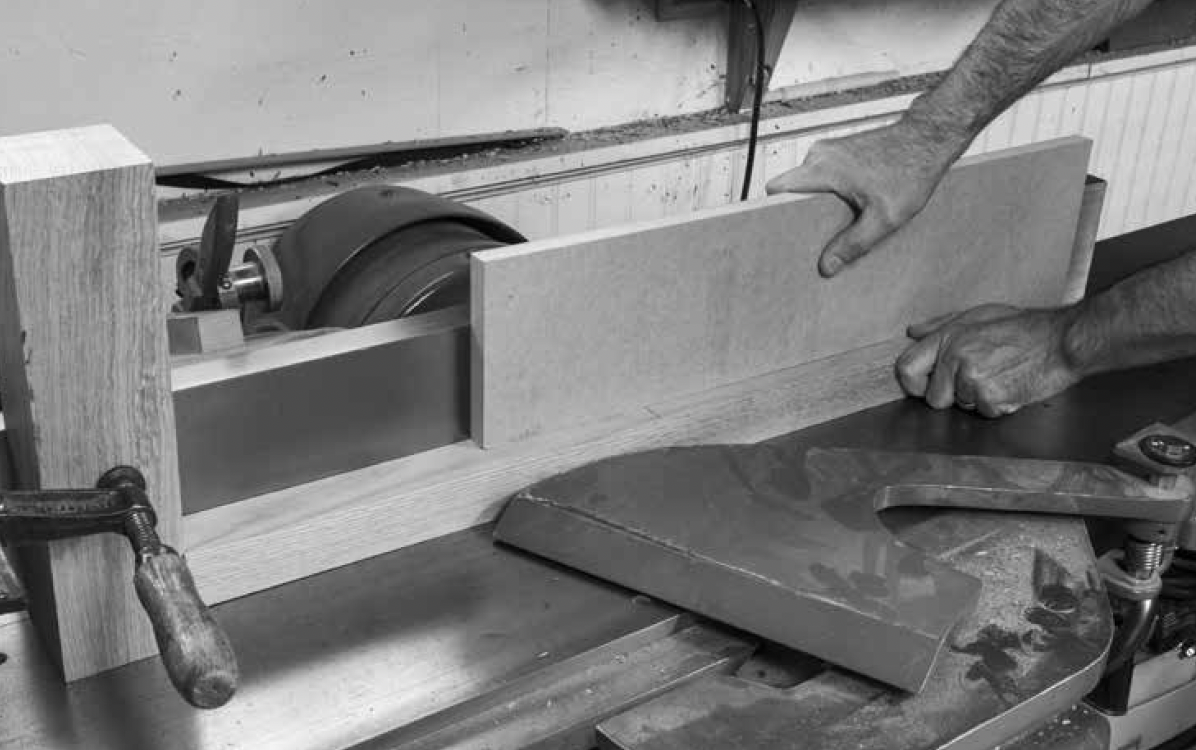
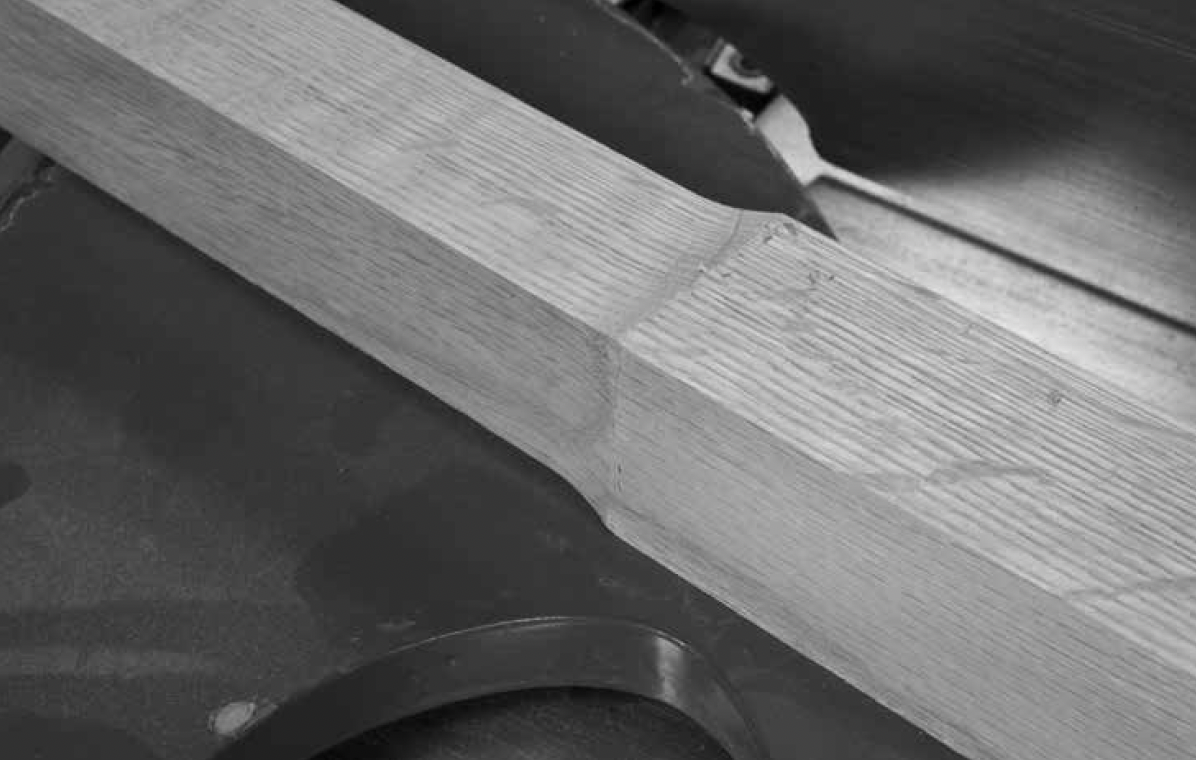
- Remove the stop-block.
- Now push the leg through the jointer a second time. This time the top of the leg goes in first. And you need to press the leg down against the table so the top of the leg “pops a wheelie” (for lack of a better expression) as you push it across the cutterhead. Cut all the faces this way and you will have a perfectly tapered leg in just a few minutes.
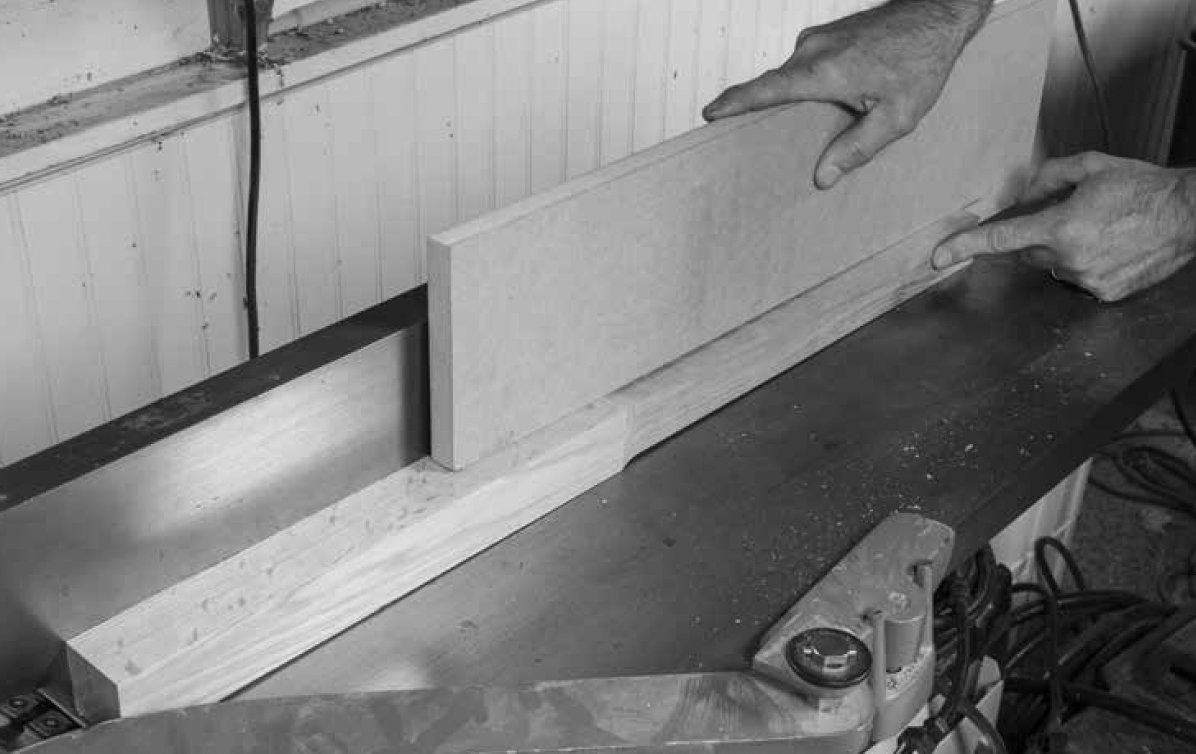
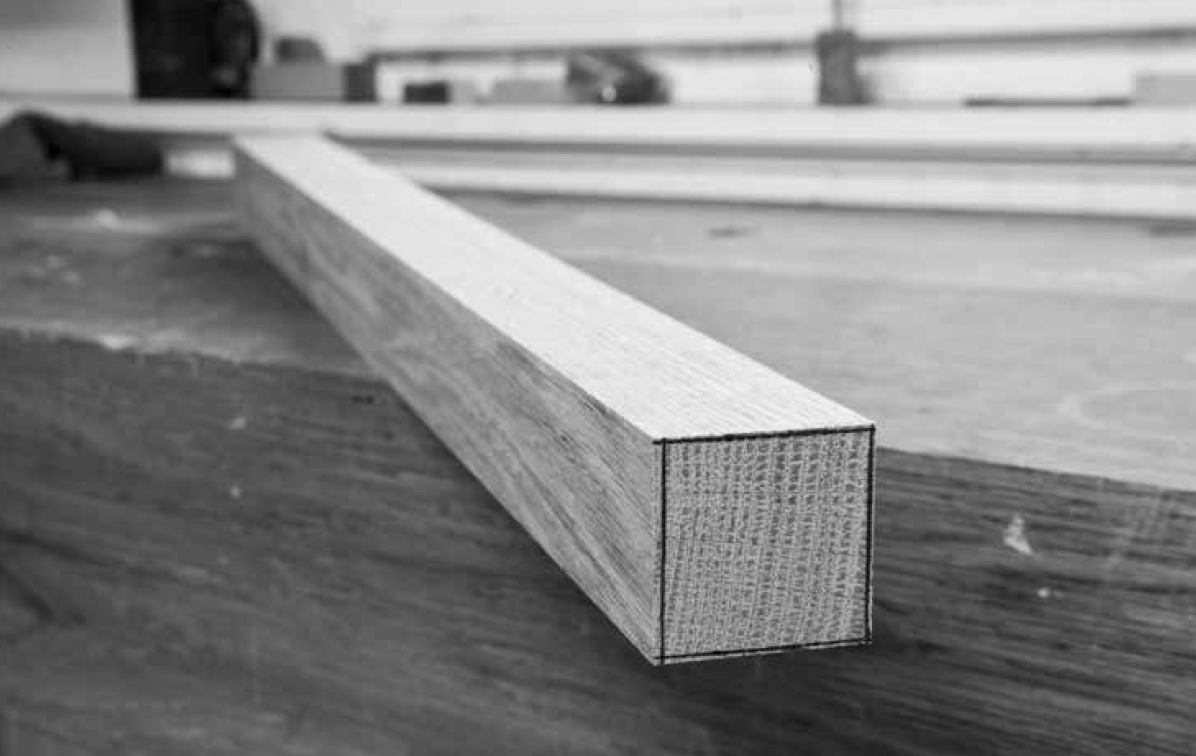
Note that this process is far safer than using most commercial tapering jigs for a table saw. Those jigs are designed to remove fingers as much as create tapers.
Editor’s note: These days, we skip the stop block and simply mark a line in Sharpie on the fence.
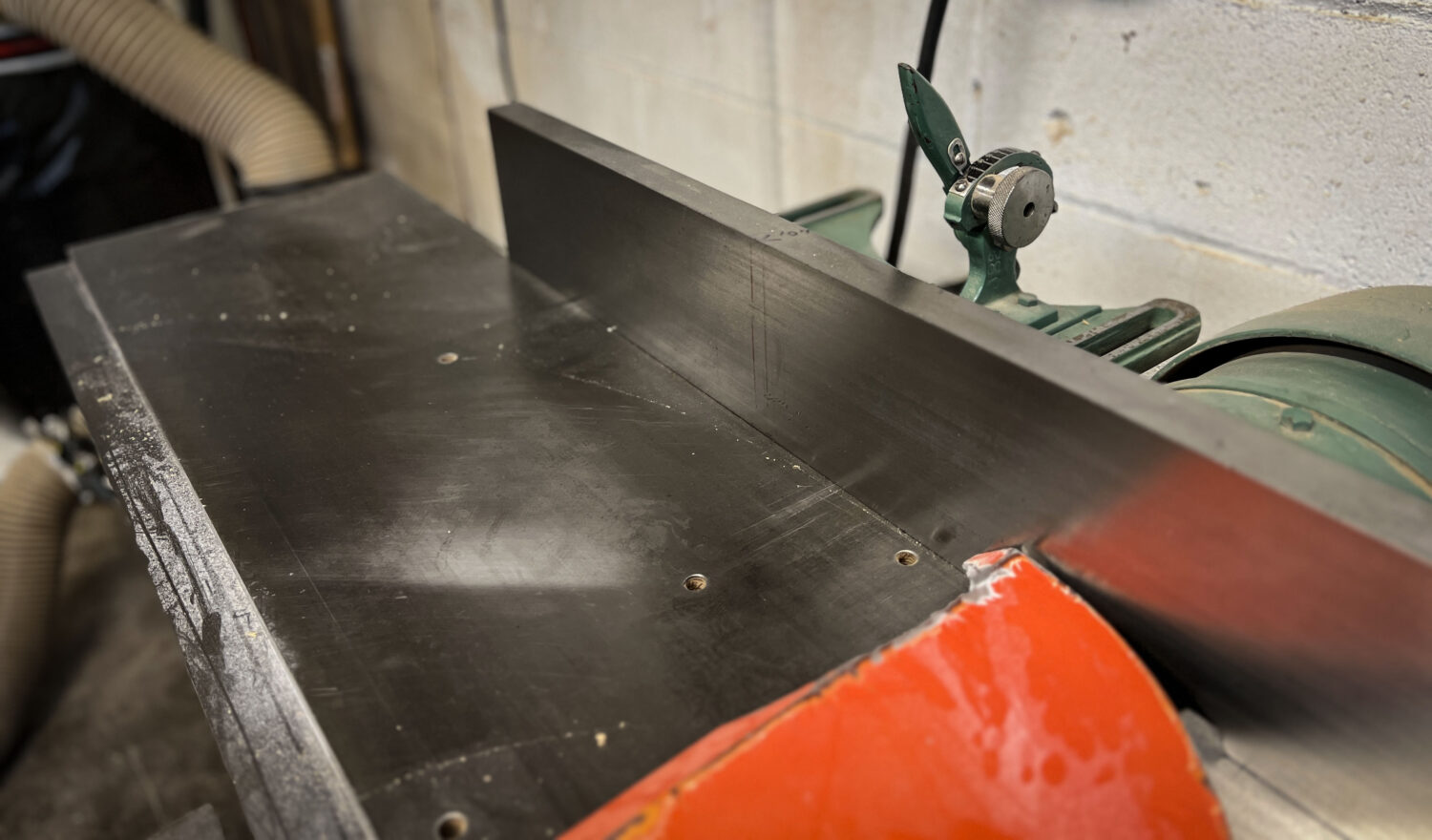
Created many card table legs using this machined method.
I have used this method to taper legs. It works just like Chris said.
Interesting. I will be making a hot tub surround for a round hot tub, so will need a bunch of tapered planks. May try this method out to see if this is faster/safer than the table saw.
Yeppers – “Cabinetmaking and Millwork” – John Freirer, 1967; pg. 379. Vocational education is a wonderful thing, even if it was 50 years ago!!!
Very cool. Can’t wait to try this and kicking myself for not reading that part of Cabinetmaking and Millwork!
Hot darn. That Flippin genius
I have used this method and I agree it’s super-fast and precise. The moment that gives me the willies is when I lift the bottom of the leg off the jointer at the end of the first cut. Would you mind explaining precisely how you do that, and/or telling me I’m overestimating the risk of that step?
I press the stock forward until it contacts the stop. Then I lift just the back end straight up, which causes the guard to close asap over the cutterhead. Then I lift the whole stick off the bed.
I’m in the firmly agree camp. I learned this from Glen Huey. Setting the stop is the difference between a full, or partial taper. I have no idea what Glen is up to these days, but I’m happy to have had the brief opportunities to learn from him.
Glen runs this shop: https://the-donutdude.com/
While the construction isn’t as permanent, we hear it’s tasty.
While geometrically this should work, I’m curious if you have used this technique on octagons or even more particularly, to create octagons directly via an angled fence
It works both in theory and in use (I have done at least 500 legs this way). Yes, it works on octagons and hexagons easily. Plus double-tapers.
I wouldn’t make an octagon on a jointer, however. Too slow or too unpredictable. It’s much faster on a table saw or band saw.
I am new and just starting out with planes, what type of finishes can be used? They all seem to have a preferred surface roughness, IE 150, 180, or 220 grit. Thanks for all your info.
Kind of impolite to slam an off topic question into the post (trying to educate, not dissuade).
This is coming from an internet rando with no affiliation to Chris and crew. Unfortunately, finishing is a whole other can of worms on top of a superfund site–way too much material to go over in a brief blog post. However, I can send you in the right direction with regard to your question. The higher grit, the more smooth and impermeable the surface. Eventually you get to a point where the surface is burnished and won’t accept any penetrating finish like dye or stain with any consistency.
Most sources agree that the 180-220 grit surface is smooth enough for appearance, and still ‘rough’ enough to accept a penetrating product. Also, do not worry at all about the difference between a 180 grit surface and a 220 grit surface. If you are happy with either, they will work fine.
Look for books and articles by Bob Flexner if you really want to dive into finishing.
You can also search the blog (top right of screen) for finishing content that will entertain you during many a bathroom commode communion.
I tried the whole search thing, got nothing. My question has to do with using a clear finish on a planed surface, being glass smooth an all. Is there a place where you can just post questions generally?
Not here. LAP used to run a forum, but it was shut down some years ago. BUT, they have recently started a Saturday morning virtual coffee clutch called ‘open wire’. You ask a question on Saturday morning by way of a comment on the blog post and LAP staff, or guest authors, will try to answer in a reply like this one. See here for this Saturday: https://blog.lostartpress.com/2023/07/12/this-saturdays-open-wire-is-with-joel-moskowitz/
Let Joel take a stab at your question. 🙂
This technique might have come to Troy Sexton in a dream in 1990, but I learned about it from my 1951 Altas Jointer instruction manual (see page 7 here: http://vintagemachinery.org/pubs/51/728.pdf )
Nice. Thanks for the reference.