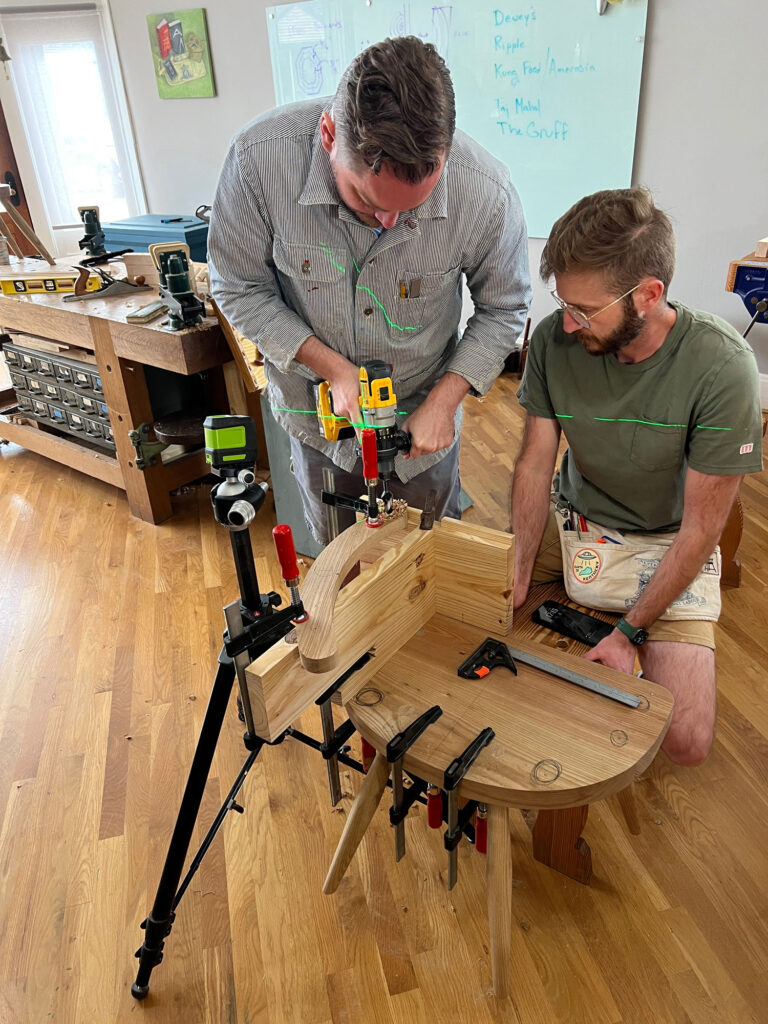
I am fairly jig-averse. Not because of some philosophical reason – it’s just not the way my head works. When I look for solutions to problems, “making a jig” is way down on the list.
But sometimes, jigs are the only way forward. Last week I taught my first-ever class in making Gibson chairs. I was an emotional wreck the whole time, trying to keep seven students on track while I revised my lesson plan. But everyone ended up with a nice elm Gibson chair.
In my recent video on making the Gibson chair, I use the same drilling jigs for the Gibson that I use for all my chairs. But when thrown into a classroom environment, the old jigs were too finicky and required too much setup in order to get the arm positioned in the correct place over the seat.
So I went into our machine room for 20 minutes and devised the jig shown here. I’m sure it can be improved, but for now I’m thrilled with how simple and repeatable it makes the process.
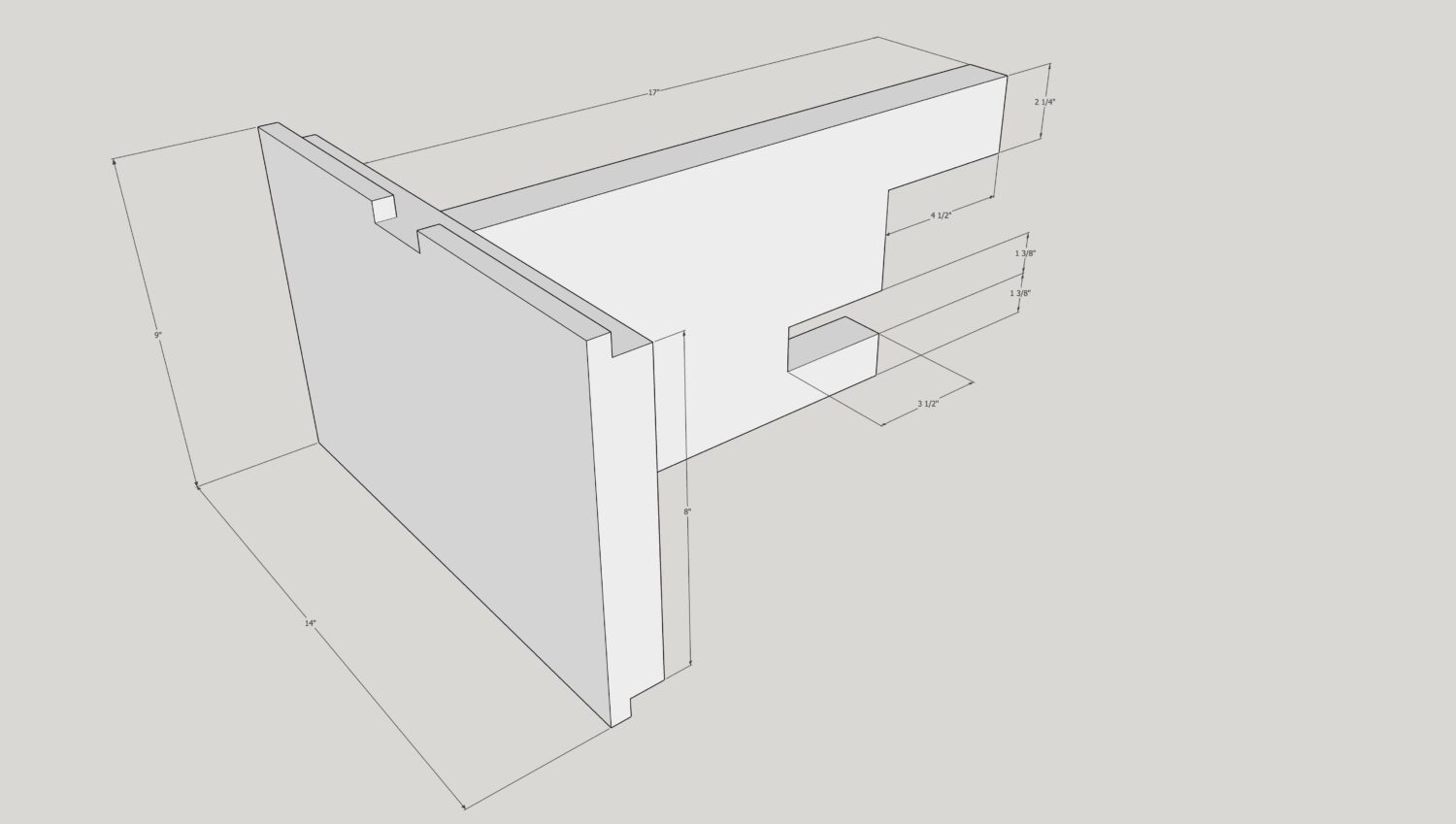
It is made from 2x10s from the home center. Here’s a cutting list:
1 Front piece 1-3/8” x 8” x 14”
1 Back piece 1-3/8” x 8” x 17”
2 Top stops 1/2” x 1/2” x 6”
1 Bottom stop 1/2” x 1/2” x14”
Screw the front piece to the back piece in the T shape shown above. Glue and nail the top stops to the top edge of the front piece. Glue and nail the bottom stop to the underside of the front piece. Done.
Now you need to set up the jig so it can be used over and over. Place the jig so it is centered between the mortises for the short sticks and long sticks. Mark on the jig the location of where the seat meets the jig. This allows you to put the jig in the right place every time.
Place the arm on the jig and position it for drilling (as shown in the video). The top stops put the front of the arm in the same plane as the front of the seat. Shift the arm so it is in the correct position over the front mortise (the inside edge of the arm should be tangent to the center point of the mortise on the seat – also shown in the video). Then rotate the arm so its rear mortise is directly in line – a 0° sightline) with its mortise in the seat. I do this with a laser in the video.
Now trace the shape of the arm on the jig. You just made the process repeatable. Shift the jig to the other side of the seat and repeat the whole process for the chair’s other arm.
View the model here.
https://app.sketchup.com/app?3dwid=3b50693c-69e2-4bba-aeb9-75c3166b38b9
You can download a SketchUp drawing of the jig at the 3D Warehouse for free.
— Christopher Schwarz
I don’t use jigs much either, how hard is it to eyeball it? I am currently working on a Gibsonish type chair. I hope you have a safe and productive trip.
Eyeballing the rear post is tricky.
I smell a crucible jig coming soon with some witty version of “Gibbon” in the name to tie into “Gibson”
16 years ago this week, I was in a class with Brian Boggs. Pretty sure it was right before meeting you at Lie-Nielsen, when you were on the “Holy Holtzappfel!” world tour.
He was very clear about his use of jigs in a classroom environment: “Jigs save time in the absence of skill.” As the class unfolded, he explained that he was such a minimalist starting out, when it came to tools, etc. Building skill was more affordable than buying tools, and so he refined his ladderback process to the point where he could build one almost completely with little more than a hatchet.
BUT, for the classroom, removing the skill aspect from the equation helped keep him on track and on schedule, because he could guarantee that a given operation would be done within a certain time frame. It also meant that, once a few students had performed a given operation, they could then help other students who were waiting.
And while it de-emphasized skill, it provided windows of time in between tasks for him to lecture. Lectures covered everything from how to break down a log, which boards from the log to use in what way, edge geometry and tool usage, layout of angles with a framing square, how the story stick was set up to lay out holes and mortises, what geometry makes for a comfortable chair, how that geometry affects the curves in the bending form, how to lay out and make the bending forms, good finishing practices, workarounds for various operations, etc. Tools and materials list for the class included a notebook and writing implement, because he was insistent that we took comprehensive notes. And he looked them over at the end of every day, in case we missed something, or had questions. As far as he was concerned, the understanding of why we were doing what we were doing, would help guide us in building skills at home, if we wanted to keep building more chairs. But because there’s always a spectrum of skill in any given class, the jig approach helped him keep everyone on track, and kept anyone from struggling too much, or getting demoralized by that struggle. (Dovetail-heavy classes are notorious for this, as I’m sure you’ve seen.)
And in 10 days, every student had an assembled ladderback chair, with a woven seat, a pair of bending forms, (for posts, not for back slats) and a story stick for layout.
One caveat: everyone had to build the exact same design. BUT, we all left with enough material and understanding to keep going at home if we wanted to build more, or design and build others.
In the context of your recent posts re: the stress of teaching classes… If you think there’s a way I could be useful, helping you adopt some of this approach, please feel free to reach out directly. (I promise to follow applicable HIPAA rules re: your contact info.)
Hi James. I’d be stressed no matter the topic. Or the prep. It’s just the teaching.
I like the low-jig, low-tool approach because I find it liberating.
Should the dimensions of the uncut back piece be 17 x 9, rather than 17 x8?
Nope. Arm is parallel to the seat. And rests inside the rabbet
Can you post a pdf of the sketchup drawing?
Chris, thank you so much for expediting these jig plans! Your timing is perfect for my mortising the arms of my Gibson chair. I had wondered, from the photo, whether those were rabbets, or separate rails, for the top and bottom stops. I was anticipating drilling the arm mortises with some trepidation, and this will help.
Keep us up-to-date on that Polish enema.
Any chance you will or could make a brief video using this jig? My mind is still pretty bad at understanding 3d renders
Chris- you made a few posts lately about how gut wrenching teaching can be. But also how important it is. My reaction is to cut yourself some slack. I taught 13 yr old kids for 40 years. That’s 40 x 190 school days -5 classes per day. My point is two fold. It takes a teacher years to become comfortable and “at ease” is elusive even nearing 40 years. When you care about something – furniture, science, writing etc. with all of your being it will always be exciting and never be a cakewalk. Embrace the taste of bile before each class- it’s the taste of passion.
Yo Chris what d said . tai chi breaths
Need some help with this new jig. I understand the function of the top stops but what is the function of the bottom stop? And where does the 17 inch piece attach to the 14″ piece? Does it align with the bottom stop or with the bottom of the 8-inch height? If it aligns with the 8-inch height, then the entire jig tilts at a downward angel. Is that correct?
Also, the paragraph that starts “Place the arm on the jig . . . ” What does this sentence mean: “inside edge of the arm should be tangent to the center point of the mortise on the seat.”
Also, if you trace the position of the left arm on the jig, how can that work to position the right arm? Seems like you would have to flip the jig.
Another question about the chair back. What is the measurement from the top of the seat to the bottom of the back?
The inside edge of the top and bottom stops are co-planar. The bottom stop hangs over the front of the seat and its inside edge rests against the front of the seat. The front of the arm rests against the top stop. This makes the front of the arm co-planar with the front of the seat.
I attached the 17″ piece to the center of the 14″ piece. The 17″ piece is 8″ tall so it aligns with the 8″ dimension of the 14″ piece. This makes it parallel to the top of the seat. (Sorry if this complicates things, but I made the 17″ piece 7-3/4″ tall because I attached a 1/4″ piece to the bottom of the rear of the arm like Chris shows in the addendum video. The bottom of the 17″ piece is aligned to the bottom of the 8″ dimension of the 14″ piece. That way the arm stays parallel to the seat.)
That is the same as shown in Gibson Chair video #5.
I haven’t done this part yet (hopefully tomorrow!), but I imagine there will be two sets of marks: one for each arm.
Thank you Steve. Your comments helped understand how the jig works.
Have you used the jig? It seems that the location of the first short stick is right next to the edge of the jig. It looks like it is going to be hard to drill without hitting the jig.
The picture of the two guys using the jig does not have the same cutouts on the end of the long board as the sketchup drawing. Wonder why?
Thanks again.
Hi Joe,
I’ve used the jig. It wasn’t too close to the mortise location for the front short stick. Did you mean the front edge of the jig (with the “rabbet”) looks too close? It wasn’t, in my hands. The whole arm setup worked very well, I thought, though the back post passing through the mortise in the rear of the arm was a source of anxiety. I didn’t break the arm, yet. I still need to disassemble the upper carriage to glue it, so of course I could still break the arm. I made the arms 1/4-inch thicker, to prevent breakage. It’s red oak.
I noticed that the jig in the photo isn’t identical. I surmise that the photo depicted an earlier, or modified, version of the jig. Mine was modified, also. I used the large crosspiece from Chris’ original jig plans (I’d constructed that, already), put some rails on it to make the “rabbets,” and attached the newer, shorter jig section perpendicular to the center of the front crosspiece. I didn’t want to remake the front crosspiece. Lazy.
I started to try it yesterday but my boards are too thick. When I centered it between the holes for the short sticks and the long stick, it was less than 1/2” from the holes in the seat so there wan’t enough space to drill. Same with the hole for the first short stick in the arm as you noted. This afternoon I’m going to reduce the thickness of the boards and try again.
In the photo caption Chris says, “I cut some more notches in it after this photo was taken, which are shown in the drawing.” I believe that’s so you can use a smaller clamp when clamping the back of the arm to the long board.
Joe, Steve,
I used nominal 2 X 10 lumber for the jig. That made the actual thickness 1-1/2 inch. With the 1/2-inch rail in place, there’s an inch left on the jig. The front mortises were, indeed, close, but I didn’t hit the jig. Not much room for variance, on the mortise position. Inserting the sticks pushes the jig aside (I just tried it), so it’s close. I can see how the jig could be too close to drill the mortise. My inclination would be to tell the jig to get out of the way (grind it, a bit), if it’s too close. May the farce be with you!
Thanks to Bob and Steve. We’ll eventually get this figured out. It would be nice if Chris could make another video using this new jig . . .
Well, in his defense, he has been traveling in Scandinavia since the day after the post about the jig.
Thanks for jumping in to help, guys
Joe, I just measured my printed out plans for the seat. The measurement I get from the front edge of the seat to the center of the front short stick mortise on the printout is 1-1/2 inches. If your jig has a one inch or less recess from the front edge of the seat, then a 1-inch diameter bit should drill a mortise (1/2-inch radius) that is just adjacent to, but not overlapping, the edge of the jig. My seat width (of the chair) is about 15-1/16-inch width, so I had a little room, when marking centers, for planing/sanding the edge. How do your measurements agree? Looks like the slightest variation in these distances would cause a collision with the jig. Just trying to over-think this.
Bob
I trimmed 3/4 inch off the thickness of the 2×8 on one side of the jig leaving just enough under the stop to support the arm. It looks like I can now drill the hole without hitting the jig. If that works I’ll trim the same amount off the other side. I’ll check the measurements of the seat to see how they compare to yours.
I planed the long piece down to about 1-1/4” and there was plenty of clearance for drilling. It was pretty nerve-wracking hoping I wasn’t in the process of ruining everything. Now I understand why Chris in the video said he had to change his underwear afterward. But I successfully dry-fit the arms so I guess I haven’t ruined everything yet!
Steve
I was finally able to make the jig work with lots of clamps. My problem now, which I can solve with time, is I drilled the holes in the arms with a woodowl bit and the holes in the seat with a spade bit. The short sticks fit in the spade bit holes but not in the woodowl holes.
I also had trouble following the tenon instructions for the backrest.
I had a similar experience with the back sticks. I started the seat mortises with the spade bit, and finished them with the wood owl auger. The 1-inch tenons fit really well, but they were so tight that the joints prevented assembly. Needed to do some reaming and paring, to get the sticks loose enough to assemble to the back rest. But I do have a rough chair that I can sit in, and type this reply. Live and don’t learn, I always say.
I’m so happy to hear you’re sitting in your chair. How exciting! I think I’m pretty close. I’ve got the first two holes in the back rest. Hopefully I’ll have time after work today to get the rest of them done. Cutting the laminated back pieces to final size on the bandsaw was something I was dreading. But I did it yesterday and it came out well, much to my surprise.
Congratulations.
Thanks, Joe and Steve!
It was quick and dirty, much like me. I’ve actually been working on this chair for quite a while. I stopped at each step, delaying it until I thought I knew exactly what I was doing. Made lots of errors. All the parts were finally done, and it was, “Why don’t I try to put it together?” As Chris alludes to in The Stick Chair, the force needed was significant. I don’t make straight, or reproducible, tenons. Lots of opposing forces, but once it’s together, it’s like a rock. Thanks to Chris for the great videos. I needed them for inspiration.
Chris, this doesn’t have anything to do with the jig, but I have a question about the backrest. In video 6 you cut 2-1/4” tenons at the top of the long sticks. In video 8 you drill 1-1/2” mortises in the back rest. When you fit the backrest onto the sticks it went all the way down to the shoulder. Did you cut the stick tenons down to 1-1/2” long?
I cut them down to whatever filled the mortises and looked good
It seems obvious, but I don’t trust myself when something I do doesn’t match the video. Thanks!
Chris,
Sorry for commenting on an old post but I’m in a little bit of a pickle. Using your templates and this new jig (which is SWEET by the way), the angle of the post seems to be 35-degrees. Is this right? I confirmed my templates were printed 100% scale and even setup the templates on the jig to make sure that it wasn’t a problem with my parts. It seems that the arm would have to be a little under 2-inches shorter with the mortises moved the same to get the 25-degree angle you call out in the video.
I figured I’d check with you before I commit an atrocity on my poor chair–its suffered enough indignities by my hand. I’ve double checked everything and can’t figure out how I’ve screwed it up!
I’m anxious to read Chris’ reply.
I’ll check but I thought it was 30.
Sounds like I’m on the right track. I’ll send it and hope for the best. Thanks as always for making this stuff possible for us!
The arm posts are not at the same angle as the long sticks that make up the back of the chair. But you know that. My arm posts are at about 28 and 29 degrees, so 30 degrees is probably about right. Not that my chair attempt is a model for emulation.
Hi, Jace. I finished my Gibson chair today. (I’m still a little in shock about that.) FWIW, my post through the rear of the arm is about 32°.
Congratulations, Steve! Mine needs a lot of prettifying. No hurry, I like sitting in it. I’ve glued only the legs. It’s as solid as oak, strangely enough. Enjoy your chair!