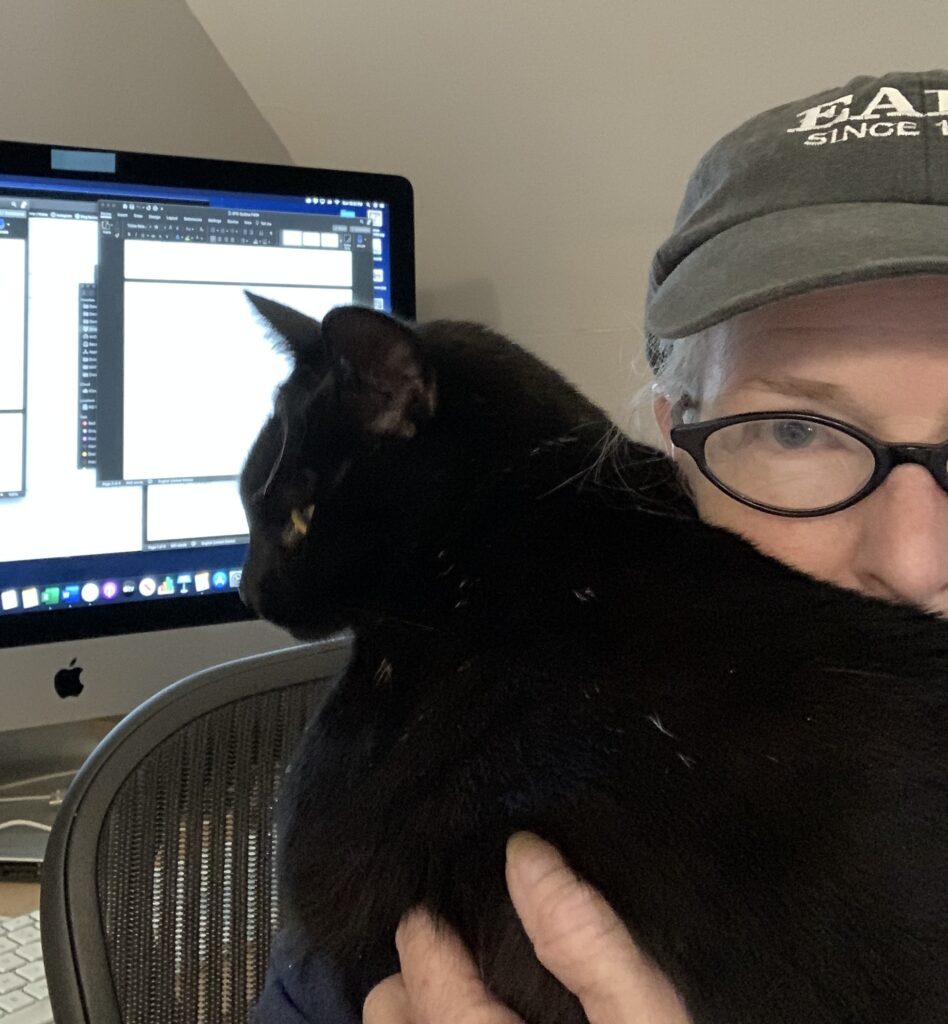
I’m afraid you’re stuck with me again for the LAP Open Wire this week (though Chris might pop in from time to time to make sure I’m not telling tall tales).
So let’s hear your woodworking, old house renovation and cat-related questions.
Here’s how it works: Type your question in the comment field. I will post my answer. It is that simple.
Before you ask a question, please read this.
- If you could limit the number of questions you ask to one or two, that would be appreciated.
- If your question is your first comment here, it will automatically be flagged for moderation. Your question will appear after I approve it.
It’s been a busy week – so I might sleep in and therefore not get to the first questions (or approve new commenters) until a bit closer to 9 a.m. Or possibly 10 a.m.Darn it. I woke up at 7 (which actually counts as “sleeping in” these days).
Comments are now closed. Thank for all the questions!
– Fitz
p.s. For the following two weeks, we have special Open Wire guests!
Good morning! As always, thanks for giving your time a expertise to us!
After reading about milk paint in ADB, I decided to give it a try. I got some real milk paint and mixed it up as Chris recommends, 2 parts water to 1 part powder. I put them in a glass jar, put on the lid, and shook it vigorously for about 5 minutes, then let it stand. When I opened it to pour it through cheesecloth, I discovered I had a jar full of barn red meringue. There was very little liquid I could pour out, and the foam never settled. What should I have done differently? Stirred, not shaken? Anything else? Thanks!
Well, if you want advice from an actual milk paint expert, get Peter Galbert’s video series: https://www.petergalbert.com/blog/2020/4/9/new-milk-paint-video
I have tried stirring and shaking, and stirring does result in less foam, but there’s still some. Regardless of how you incorporate the water into the powder, Pete says to let it sit a 1/2 hour after, then mix it again, then wait an hour. Then strain it with a cone-shaped filter. He writes: “Yes, you are going to throw out a lot of paint, believe me, you don’t want it.” His way results in a nice, smooth finish. (He also uses a little more water.)
But I kinda like a streaky look on some things – and when I’m going for that, I’ll dip my brush in the foam, drop foam onto my surface, then draw it out with the brush. But it does create color striations, which are likely less appealing for many. (I like them…but would never do that on a piece I’m selling.)
Milk paint feels so personal; everyone does it a little differently!
I can vouch for the approach Galbert uses in his video – gently pouring out the smooth liquid milk paint from underneath the head of foam. That smooth paint creates (for me at least) a very even finish. But like Megan says, it’s not better. Just different.
i’d highly recommend contacting the company because different products can behave wildly different. i recently used Real Milk Paint and Old Fashion Milk Paint. Real Milk Paint worked best after settling for at least an hour or even a day and then the Old Fashioned congealed after 30 minutes. I tried shaking, stirring, adding more water, it kept congealing. I called them and got one of the owners. She told me that for their milk paint you don’t let it sit, you mix it then use it within 15 minutes. I did that and it worked great, and since i was using it and consistently stirring it it didn’t congeal as i was going.
I’ve noticed that you saw, chisel and router plane your dados. I’m curious if you’ve experimented with other methods and tools, and what you liked or disliked about them.
I’ve used a saw and chisel only – a bit slower for me to get a smooth/flat bottom that way, though a smooth bottom doesn’t matter much except at the dado ends. I’ve used only a knife and chisel (knife to score the walls then a chisel to remove all the waste – takes too long. I’ve also used a dado stack; too much dust! I confess to never even having held a dado plane.
Minutes 29 or so to minute 32 or so of Richard Maguire’s video (https://www.theenglishwoodworker.com/how-to-make-a-shooting-board-video/) shows him cutting a precise and clean dado with saw, chisel and router plane. He shows a nice method of chopping out the waste. What is really nice is that he saws inside the knife lines and chisels the remaining waste cleanly and precisely by starting the chisel in the knife line.
I have really been struggling with edge planing. Sometimes I can get square to the face but when I start trying to take full width passes I end up with a bevel again. Are you aware of any common beginner mistakes that I could be making and how to resolve this? Thanks for your time.
Hard to say without watching, but in general, the longer the board, the harder it is (because your body shifts and that shifts the plane and…).
I use my fingers as a fence, pushing down on the plane (in my case, a No 7) in the front next to or in front of the knob with my left thumb on top, and my fingers fenced at 90° underneath.
If you’re consistently out of square at the same angle, concentrate on tipping the plane slightly in the opposite direction (really, shifting your body so the plane is square).
You could try adding a fence to help keep you square, something like: https://www.leevalley.com/en-us/shop/tools/hand-tools/planes/maintenance-and-accessories/41716-veritas-jointer-fence?item=05P3001 or, if you can find one, a vintage Stanley No. 386
Or get a No. 95 edge plane if you continue to struggle.
I struggled for a very long time as well before I found this suggestion from Chris back in the PW days:
https://www.popularwoodworking.com/article/an-awesome-edge-jointing-jig/
It’s been years and I still use that thing. Hope it helps you too. Haven’t used the one posted by Megan but I like the narrow profile which makes it easier to skew my jointer.
I think everyone has had trouble with this. I certainly have. One problem I had for a long time was not getting the blade perfectly (I hate even saying perfectly) even with the plane sole. Even if the blade is initially set perfectly, it is possible a slight touch with your hand or a bump will change the setting. If it is off just a slight amount, repeated full length passes will produce an increasingly out of square result. This problem is also exacerbated by taking thicker shavings. And, some planes are more susceptible to being knocked out of alignment than others. I have taken to keeping little bits of wood–a bit of a pop sickle stick–to quickly run across the blade to verify that it is protruding as evenly as possible. It’s a trick I’ve seen others use and I find it worthwhile.
Also, you could build a long shooting board–but that has some of its own quirks.
Hi Megan!! How long is the comb on a Gibson chair in relation to the width of the seat? The 25 year old seat blank has come back out and I am in the process of building a Gibsonish side chair.
The seat is 24″-25″ long. The backrest is 23″ long.
Thank you!! I thought it looked a little shorter than the seat!
So with a 20 3/4 long seat use maybe a 19-20 inch comb?
I do mock-ups in cheap softwood before I commit with the good stuff.
Hi Megan! Thanks for doing this. How did you learn to do house renovations? Any first projects you’d recommend?
Honestly, just by doing…and being too poor/too cheap to pay someone if I could do it myself (or thought I could!). So, I’ll do the “easy,” stuff (e.g. tear-out, underlayment, most things wood-related), but won’t do plumbing, electric, or other tasks that could flood/burn down the house or otherwise hurt someone if it goes wrong. And I do a lot of reading first on and around a given project before starting (which helps to teach me if it would be better to pay an expert).
But I used to do a lot more – I had more energy and slightly better knees 15-20 years ago!
Thanks so much! I’m amazed by all that you do!
Looking at Tools For Working Wood website I see they supply an ant-foaming agent for Real Milk Paint
Yep – Real Milk Paint sells it on their site too (of course). I’ve never used it, so I can’t speak to its efficacy.
I have used the anti-foaming agent several times now. It does indeed work to knock back the foam after mixing.
Hello and thank you Megan, Chris, and all the guests for spending their time answering questions! Do you have any experience or opinions on having a leg vice skewed/slanted? Rex Kreuger used it in one of his bench designs and it seems alluring. Additionally what is your preferred medium for reducing friction on tools? (Wax, oil, tallow, ect) I’ve been using Don Williams “blend 31” and it works great, but I have no experience to compare it to. Thanks again.
The leg vise is angled on the Nicholson Chris built in 2006. It has a deeper capacity…but I’ve rarely needed that. It works fine; so do the straight ones. You can see it here in this bench tour:
For tool wiping, I usually just grab my woobie. It’s impregnated with oil(s) – mostly jojoba. If the wax is closer, I might grab that. Both work.
OK now I have a question. Around the 3 minute mark on that video Chris is demonstrating an adjustable from below the bench planing stop, looks something like a rectangular floor flange screwed to the bottom of the top with a slot so that you loosen a wingnut to adjust the height. I can probably install something like that easier than making a mortice tight enough to hold but not too tight to bind the block the stop sits on.. and you could do something like put the cage on the home bench and the occasionally portable one and just grab the stop (2 week every year excursion coming up).
Thank You!
Record No. 169 Bench Stop
Is there a chance the new employees will be at the open house this month?
Probably not. They don’t work on the weekends.
What would you say are your 5 most important router bits? Probably based on use.
Ha ha – that is a joke, right? (That said…I do on rare occasion use a flush trim bit.) Chris has more router experience – a necessity at PopWood at one time. Perhaps he’ll chime in.
Hi Chris and Megan. A comment, a contribution, and a question, all about your Death Grip glue (or as I am calling it: “Clearbond”). The comment: talk about sticking it to the man, even if the man is you! Making your recipe open source when you plan to sell it is walking the walk, not just talking the talk. You continue to inspire and humble, big “A” for “Anarchist”. There is freedom in knowing I will never have to buy wood glue again. The contribution: you gave several suggestions on how to cook and prep the glue at 140F. Here’s another one: use a sous vide stick if you happen to already own one for cooking. Stick the squeeze bottle in a bath of hot water in a pot with the sous vide, and it’s fool-proof and ready in minutes. Finally, the question: cleaning up squeeze out as you clamp the joint is easy with a wet rag. But what about hardened squeeze out that you may not be able to get to immediately, like when the clamps are in the way. How do you clean that if the glue has hardened overnight?
If it’s just a little glue, I’ll use a chisel (yeah, yeah…cue the horror). But if it’s a lot, I reach for my Benchcrafted Skraper (I love that thing every bit as much as I hate how it’s spelled).
Also, hot water and a toothbrush… to get into corners.
A heat gun and water will do wonders at softening hide glue squeeze-out that’s fully cured. Mind you don’t scorch the wood.
I believe that Phil Lowe gets credit for imparting that but of wisdom to me.
In “Door making and Window-making” our author first describes the production of the casement window. They describe an open mortise in the sill into which the tenon of the jamb is drawn in by the drawbore peg. The author does not give any detail beyond the instruction that “frames such as these should be fixed together by draw-boring.” The sketch shows the pegs clearly from the interior elevation. But what happens on the exterior side of the sill? I’m playing around with this and trying to decide whether a through bore (such that the bore pin exits the sloped face of the exterior sill) will invite water trouble. One thought would be to use a “stopped bore joint” (if that’s even a real joint). At any rate, it’s good puzzling trying to tease out the secrets of the joiner. (I might add that in the present trial there is no sash, it’s only a picture window) — thanks for your thoughts on this!
I suppose water more easily gets into the pin if the finish fails, but I do think through is traditional (at least going by old windows and doors that I’ve seen).
I have semi-taken in a feral cat. I say “semi” because it hangs around for the food but then disappears after it eats. I would like to be more friendly with “Clipper” (it has a clipped ear). Maybe pet the him/her/it, or introduce it to a ball of yarn? Seems like every time I get within 8 ft he scatters away. Can I persuade a feral cat to be more people friendly? Thanks!
I’ve been feeding one of my ferals wet food daily for seven years now. The only time she lets me near her is when I’m holding an open Churu tube. She will lap up Churu from the tube in my hand – but if I move to pet her, well, she runs. So I’ll keep trying. Good luck!
Ok, I’ll just learn to live with a long distance relationship (sigh!)
Hi is there one nonessential hand tool that you do not have but have always wanted because it would be so cool to have?
Well, given an earlier answer, maybe a dado plane? But I don’t really want one…I’d just like to try one out because I never have. I doubt I’d switch to that method of work, because I’m most often cutting dados in a class, and I prefer to work with tools that are more easily obtainable/easier to set up and use. But I guess the “luxury” tool that I love to use is a shooting plane (I just borrow Chris’s!).
Hi Fitz! Have you ever made your iwn handsaw?
I have not. I don’t particularly like tool making – I have enough other work already!
How did/do you decide on the next project to build if it’s not for personal use but for selling to earn a crust? I remember Chris saying he stopped commission work and now just builds what he wants to to sell but I wonder, do you just make what you like and hope someone buys it?
I don’t build what one might call “spec” work. If I’m making something these days, it’s for my house, for a book, during a class, or a commission – which I do still take. (And I also sell projects I build for a book and during classes…but those aren’t really spec pieces.)
When I was at PW, many of the things I made were because I needed/wanted that piece of furniture, or wanted to learn a new tool/technique/try a new style. Or, worst case, we needed that kind of build (e.g. a contemporary, live-edge, mixed-wood wall cabinet … that looks not at all like my style) and I couldn’t find anyone else to do it quickly enough!
Thanks Megan. Almost everything I’ve built has been for my house or as a gift, although a lot of it is very superfluous; I’m not sure my house can cope with any more stools (bathroom excepted)!
Does Roy Underhill have another woodworking book in him?
You’d have to ask him. (Hope he does!)
Hello,
I’m in West Virginia, near Canaan Valley and the Dolly Sods Wilderness.
First, I adore your cat! and please let me say that I love Chris’ book about Campaign Furniture. I will most likely spend the remainder of my life working through projects for it.
For this autumn and winter, I will be culling trees on our land for several projects. The first is for an old skool pedal lathe using a bungee cord rather than a sapling to drive it. I have maple, shagbark hickory, cherry, ash, a few elm, sycamore, apple and many other species of trees on this land. I can’t be more specific because I’m just learning how to identify them.
Out of the small group that I’ve mentioned, which would you recommend for the uprights, ways and poppets of this lathe? It will spend its life outdoors, under cover when not in use. I intend to use it to turn stuff like tool handles and legs for benches, chairs and tables – the diameter won’t likely exceed three inches.
Thanks in advance!
Opey
If it were me, I’d pick a wood that likes the outdoors, such as white oak or black locust. (Oak is easier to work with.)
On behalf of Olivia, thank you! (And see Chris’ answer)
How’s your home renovation project? I haven’t seen any updates in a long time.
Slowly! But I’ve actually completed some things about which I’ve not written – the first-floor powder room, for example, and HVAC on the third floor. And, as of three days ago, a newly pointed foundation (I personally did only one of those three).
Hey Fitz,
I purchased my first bandsaw and went with the LAP rec and got the 14″ Jet metal/wood saw. I need a good reference for bandsaw set up, use, and maintenance. Do you have a favorite? Chris?
Thanks.
There are lots of good video tutorials out there by Michael Fortune and others that are easy to find. I learned to do it from Mark Duginske’s books. Pick one and you’ll be fine.
These two Michael Fortune videos are great.
Setup:
https://www.finewoodworking.com/project-guides/shop-machines/how-to-set-up-a-bandsaw
Eliminating drift;
https://m.youtube.com/watch?v=vNdrkmx6ehI
In the Anarchist’s Tool Chest in the section about painting the tool chest, Chris describes applying the milk paint, then applying a topcoat or oil, varnish, or wax before applying late. paint on top. I was curious why you need or want the topcoat over the milk paint before applying the final coat of latex paint. I recently did this but with two colors of milk paint rather than a final layer of latex paint. Just wondering if it was something I needed to do or if it has something to do with the latex paint. thanks!
It’s simply what he had to hand. Two colors of milk paint are just fine.
Sorry, I was more trying to understand why you need a finishing coat in between paint colors. Just wanting to learn
Ah. You don’t. Just need it to completely dry.
Hi Megan,
As I heard recently on the Internet that you are “The Style” (I believe that was the expression used), I have a (probably) stupid, but genuine (inquiring mind wants to expand its vocabulary!) terminology question for you.
Dovetails consist of tails, and pins. So far, so simple.
When, however, there is but a single tail, what would be the correct term in English for the space that said single tail goes into when the joint comes together? “Pins” seems kinda wrong, as there really are none, just an empty space surrounded by otherwise unbroken, very “un-pinny” wood.
(At least I hope I haven’t misunderstood the word “pins”, when I think it means the sticky-out bits of wood at the end of a pin board that go into the empty spaces between the tails?!)
This is not a question that has kept me awake at night, but it does bother me that I don’t know what it is called in English, so when I saw that it is you (The Style! Who also knows dovetails like the back of her hand!) who have the watch at the Open Wire today, well … see above!
Cheers and all best,
Mattias
I don’t know what “the style” means…which means I can’t be that 🙂
I would say “dovetail socket.”
And hi!
Thank you Megan! “Dovetail socket” makes perfect sense.
Also, I double checked, and my memory did me a disservice; what I’d heard on the Internet was that you are The Stylebook. Qoud erat demonstrandum!
Cheers,
Mattias
Oh. Well, I don’t know about that – but I consult ours a lot!
“I am The Stylebook” (at around 11.58) is what I was referring to … 😇
I was drinking 😉
Two questions about the ATC. First, are you able to share the nail sizes and styles you use for the exterior and interior? I’m new to cut nails so I don’t want to buy the wrong ones. Also for the whitechappel crab lock, is there a good escutcheon that matches the forged hardware? Thanks so much!
I use 50mm Rivierre nails (if I can get them) to nail on the chest bottoms; if I can’t get those, Tremont 6d clout nails work just fine. Sometimes I’ll use 6d rosehead nails around the dust seal on the lid…but most often, I just grab the nail gun and pin it place (along with glue).
On the Whitechapel lock: I have yet to find a commercially available escutcheon that is both large enough to fit the keyhole and shaped so as to fit under the top skirt. So I either don’t use an escutcheon or I make one out of wood.
Thanks! Any nails you prefer for the interior like nailing the drawer bottoms and tacking things to the side. Fine finish nails, or something with a bigger head?
Ah – for the till bottoms, I use 4d clouts, and first drill a countersink for the heads on the ends of the bottoms, where the nail heads would hit the runners.
If you want to read more about nails in general: https://www.finewoodworking.com/2020/09/30/on-nails
What is your preferred method for making octagonal pieces for chair legs? For example, plane them, saw and then plane to finish?
I’ve seen Chris do both – it depends on how many he has to make, I think. Most often, they get octagonalized at the band saw, then tapered by hand.
I have MANY through mortises to chop. they are all 1/4″ x 1″ and will go through 1 1/2″ thick material. it would be even better if i could cut the mortises through a 3″ thick board and then rip the board in half (this would cut the number of mortises i need to chop in half). thus far, I’ve been using a drill press to clear most of the waste and cleaning up with a chisel. what machine would you recommend to speed up this operation? i have a small shop, so a bench top or smaller tool i can put away when not in use would be ideal.
Mortising machine. It’s one of my favorite machines (though we don’t have one any more, as we don’t cut enough mortises to justify to space it requires). But you can also cut mortises with a router – So I’ve heard 😉 (and square the ends if need be). And I’m sure there are other powered ways.
How much wood would a woodchuck chuck if a woodchuck could chuck wood?
^silly nonsensical question to levitate the levity on this Saturday morn.
https://gf.nd.gov/wildlife-notes/how-much-wood-can-woodchuck-chuck
well that explains why attempts to discourage them from from the garden by filling the holes with things like chickenwire with stones on top doesn’t seem to work well…
I’ve dove into ornithology, with the musical question, “How much chucked wood would a wood duck duck, if a wood duck would duck chucked wood?
Hi LAP and thank you! I’m new to woodworking and have been focusing on hand tools only box making. I saw an old Popular Woodworking Magazine YouTube video with Chris using a Record #043 Plough Plane for speeding up stopped grooves/dados for box bottoms. Veritas recently launched their modern version under Veritas Box-Maker’s Plow Plane. I would like to know if he/you can recommend one over the other. I would like to buy one, but before I do your input is highly appreciated. (My biggest concern on the Veritas is that the rods are fixed, and for a hand tool only woodworker it may get in the way of holdfasts). P.S. most like you don’t have the new version, so I want to let you know that there is a YouTube review on it that you could refer to, in case you want additional information on the plane. link to follow: https://youtu.be/23Dl636—4 Thank you again!
Hi Edward,
I wouldn’t worry about the fixed rods much. The rods aren’t long, and there are a million ways to hold a workpiece down. I haven’t used the Veritas, so I don’t have an valid opinion about this particular tool, but we are fans of their planes in general.
That was a really thorough review video, thanks. What isn’t clear to me (newbie!) is how to use it to make stopped grooves… One end is obvious, the other isn’t, unless the workpiece is narrow enough? Or does one chisel the back end to clean it up?
Hi Olivia!
Are you gonna host one of these LAP Open Wire sessions?
Thought I’d ask, cuz your mom gets oh so cross, if we don’t ask about you.
You’re gorgeous, Olivia!
Is there a minimum number of dovetails you recommend for attaching the bottom to the sides on a dutch tool chest for holding integrity? Thank you for doing this open wire every saturday!
Three or four is plenty. Actually, one is plenty, though it might look odd. The nailed-on (or screwed-on) back, front and bottom lip, and nails into the sides of the shelf – will hold it together.
I have a layout/order of operations question for the DTC. I’m planning on a shelf in the lower section and the shelf that makes the floor of the upper section. My aim is to have as little fussing as possible after the dados and shelves are cut to square up the case. My plan (in order) is to lay out and cut the dovetails on the case sides, measure up from the the baseline on one side and mark the top of the lower shelf and then measure down from the front edge of the case side to the top of the upper shelf. Then transfer those marks to the other side of the case using the baseline of the dovetails to align the sides. Once all the shelves are marked and dados cut to each shelf I plan on knocking together the dovetailed bottom first. If I cut my shelves just over-long and use a luxurious shooting plane to trim them to make the case square will I be in good shape? Or is there an easier order of operations?
And if I can ask a second question, Blue Spruce round mallet: 13oz or 16oz? I made a copy of the son of Roy Underhill’s mallet, but I really want to try a round one.
And thanks for being awesome! I learn much from the questions and replies from others.
Your order of operations almost follows mine…but I recommend marking/cutting the dados on one side, then marking the second side off the cut dados on the first. That way, if you’re off a little on the first ones, the mating ones will match. (Also, I prefer marking one wall, cutting it, then using the shelf itself to mark the second). If only there were a book that showed, this… Soon!
I was just ablut to comment “If only there was a book.”
But then remembered only you can mention it.
Hi Megan and Chris,
Two questions regarding Crucible Tools… Do you expect to have the Warrington pattern hammers available soon? And are there any plans to bring back the Crucible Design Curves?
Thanks so much for all you do!
The Warrington hammers are in production now. So we hope to have them available later this month. I don’t know about the curves.
Hi LAP and thanks for doing this! I’m new to the woodworking world and am thinking about my first workbench. I have a small space and think I can manage to build a Nocholson – I was going to build the “Minimalist” version but then found Chris’ knockdown design. I won’t ask about what wood to use because I can’t find SYP in California… But instead about the prospect of eventually adding a Crisscross. It seems like the required mortise might be deeper than desirable in the ~3″ thick legs (not to mention interfering with the stretcher). Am I thinking about this right?
chris
The thinnest leg in which we’ve a Crisscross installed is 3-1/2″. But the BC directions read: “You should not mount the Crisscross Solo in a bench leg that’s narrower than 3″, or the Retro in a leg narrower than 4″. Bench leg and chop each need to be at least 2-1/2″ thick. You don’t need thick stock, you can laminate 8/4 stock onto 4/4 stock to achieve that thickness.”
Aha. It was right there, if I’d read all the fine print. Thanks (and for confirming that I’m thinking about it right). I was planning to live with a crochet for a while, anyway…
Now that you have employees and they are helping with production, will you be concentrating on the DTC book? Perhaps at the new buildings “Grand Opening” in January you could have a book signing?
(If it’s done and printed by then).
I’m working on it. We shall see.
Have y’all ever looked into Acadian or Creole furniture of Louisiana? At one time there was a maker of this style named Greg Arceneaux. I really liked the lines of his furniture without all the ornamentation of the French Provincial style.
Chris built a creole table for PW some years back, but I know the style isn’t foremost in his mind right now. I admire the style, but am more drawn to plainer furniture.
Last week I asked Peter about moisture content in wood used for chairs. He mentioned he uses a “light bulb kiln.” Do you know of any plans for an effective light bulb kiln or are there any plans in any of the books LAP sells? I am interested in making one. I’m sure there are plenty if plans online but wanted to check with you before I launch into that other world.
Thanks!
Peter’s kiln is shown in the LAP edition of “Make a Chair from a Tree” – and he writes that it’s based on the one JA showed in the 1994 edition.
Mark Hicks has free plans for i.a. A lightbulb kiln over at his Joint Effort site.
Hi Meghan, eventual tools that I would like to own for woodworking are a drill press and lathe. Also, at some point, I want to take some basic machining classes at our local city college to expand what I can do for woodworking. I’ve seen some mill and lathe combo machines for metal working that may also provide both lathe and drill press use for woodworking. Below is link to one such Grizzly machine (there are others). Do you know anything about them in terms of quality and suitability for both woodworking and metal work? Thanks.
https://www.grizzly.com/products/grizzly-31-3-4-hp-combo-lathe-mill/g9729
I’m afraid I don’t — perhaps someone else can chime in?
I’m fairly new to milk paint & have struggled through a few projects before watching Curtis Buchanan’s You Tube video of how he mixes & applies milk paint – an installment in his Windsor Chair series. For me his process was spot on and while I lose some paint due to skimming some of the foam the results were worth the waste. Curtis uses a manual kitchen hand mixer – I use a wire wisk ( have to let my inner Julia Child out sometime ) Not sure if this qualifies as stirred and not shaken.
I could not find a Record 43 anywhere stateside and the overseas options were pricey. I ordered and just received the Veritas Box Makers plane and, like all of their tools, is a superbly engineered piece – heading out to play with it now…
C, love of my life: is there a special guest today(on Open Wire)? Me: no; Megan. C: she’s special! And, she likes West Wing : – ) [No question — just thanks for hosting the discussion on milk paint. I have some suggestions to test now for my foaming issues.]
Hi, Megan! Long time reader, first time commenter. Love the Lost Art Press blog and books, and I’m slowly making my way through the Stick Chair and Gibson Chair videos. (Thanks for doing the camera work!)
I’m thinking of making the boarded bookshelf from ADB but I want to put a board on top so that the carcase is closed. Should the top board sit on top of the sides and be nailed down through the top, or should it fit between the sides (maybe sitting on a dado) and be nailed through the sides? Thanks!
Hmmm… I’d probably rabbet the top edges of the sides to house that top shelf, then nail it (so that it matches the construction of the rest of the unit). Or make the top slightly larger to hang over the front and sides, and nail through it into the sides.
Hi Megan, thanks for this! In designing a basic staked stool or sitting bench, how much should the feet of the legs go outside of the shadow of the seat? Looking for stability without being a tripping hazard for those walking past.
I’m afraid I’m not the right person to ask. But I’m looking at one of Chris’s chairs right now and the rake and splay put the back legs about 2” behind the seat, and the front legs about the same to the side of it.
Favourite saw set? (Notwithstanding Chris’ recent spot-on post that one is a “real” woodworker even without sharpening saws — my paraphrase from memory). A student brought an Amazon Eclipse/Somax knockoff that was OK after grinding the hammer thinner. (I make no comment on quality, longevity or knockoffs usurping legitimate toolmakers). I loan out Somax and Taintor Positive No.7 but students wish to buy.
No clue; I prefer dulling saws to sharpening them. But Matt Cianci (@thesawwright on IG) recently posted that he likes the Stanley 42 now, along with the 42X.
Megan, I live in an area with very low humidity which affects glue open time. In order to improve my chances of accurate glue-ups, I have searched for glues with longer open times and hit on liquid hide glue as possibly the best option. So, I purchased some Old Brown Glue which seemed to work fine until I needed to edge join three 75 inch long boards. After covering all of the edges thoroughly with glue, I clamped them up. I did all of this as quickly as I could. But, the glue had gelled enough that the clamps didn’t squeeze out the glue on the first joint I coated. So, while it dried okay, and created a seemingly strong joint, it left an unacceptable glue line where the glue didn’t get thoroughly squeezed out. I don’t think I can work any faster. Any suggestions from anybody would be much appreciated.
And, thank you to you and Chris for doing this. I look forward to Saturday mornings!
This is going to sound sarcastic…but isn’t! Maybe run a humidifier in the shop when need be? You might also try making and using gelatin glue from the instructions Chris has posted – the stuff is pretty much clear, and won’t leave a dark glue line.
Low-humidity here also. I give students OBG thinned slightly, in chocolate warmers that hold 60C, glass jars, trimmed acid brushes. Students pair to help each other apply glue (project owner is the pilot). YMMV; make test joints to determine acceptable % of water. Don’t forget — you will get faster each time : – )
Thinning glue (PVA or protein glue) with a little water will extend the open time. There are extended-open time PVA glues that are worth trying.
I’m addition to heating and thinning the hide glue, working under a heat lamp can help!
Hi Megan,
Are you aware of any resources to using and troubleshooting spokeshaves?
After watching a brief video of Chris Williams using one with one hand, I’m certain I’m doing something (many things) wrong.
Mine skip and chatter but don’t shave.
Thank you for your time and continued guidance.
Ray
Need screaming sharp blade, thinner cut, and go with the grain.
Pete Galbert has a good FWW article on using one: https://www.finewoodworking.com/project-guides/handplanes/spokeshave-tips-to-get-started
Hi Megan , In the June 12 LAP blog on the stunning Welsh Chair that Chris Williams built there was a comment:
” The chair is stained with a black dye and topcoated with a linseed oil finish. The open grain of the timbers is clearly visible through the matte/satin finish.”
I have been building my stools/ stick chairs with poplar seats and Red Oak sticks . The above finish sounded like an interesting and simple alternative to my usual method of painting .
Since reading the blog I have tried several different combinations of black dye / black stain , topped with oil then wax . My results have been pretty average , Is there any way of getting more information on Chris Williams method and what products he used ?
Thanks for any suggestions !
What he was using isn’t yet commercially available, is what I recall him saying. You could try asking through his website contact form. https://www.welshstickchairs.com/contact
What is a great zero VOC finish to use on a dining table top? Do you think Tried & True Danish oil and/or Soft wax 2.0 is durable enough?
Chris and I just put a soft wax finish on his old table top, after stripping the failing lacquer. I expect it will need refresher coats at least yearly, but it looks and feels nice. I’d rather do that than spray a high VOC finish that will likely fail…eventually if not immediately. If you want more protection, perhaps use a wiping varnish (make your own with low VOC mineral spirits).
I asked a similar question a few weeks ago. Chris suggested a harder version of the “soft” wax that included Carnuba as well as beeswax, along with the linseed oil and a bit of citrus solvent. I mixed up a batch following the LAP blog instructions and used it on my cherry dining table. So far only one coat, but it looks FANTASTIC and survived one big party well. Note, Chris points out this is not a tough finish that will survive anything, but he says multiple coats allowed to cure well between applications will create a good surface that still has a feel of the wood. As I recall, I used 60% beeswax and 40% Carnuba. The Carnuba requires heating to +180º. I used a sous vide heater and it worked great.
Thank you
Megan, you might be the perfect person to ask this question to… We have fairly beautiful views from the front and back windows of our house into our native plant beds, and my wife loves birdwatching through these. She has mentioned wanting something more comfortable to sit in for said viewing, and just today brought up the terrible idea of getting a chaise lounge… Mind you, our front windows are in the dining room. Adding a chaise lounge?? No. So my question, of all the different stick chair designs LAP have bestowed on us, which do you think is best suited for this bird-watching/lounging combination? I’m leaning towards the Gibson chair… Thanks so much for your consideration 😀
Uh…I have a chaise! But if I had to choose a stick chair, it would be the Gibson. But what about a Rhoorkee? It’s comfy for long periods. And I’ve always wanted to try making a Campeche chair, which looks cool and comfortable (to me).
I am lucky enough to have just gotten a Stanley 65 chamfer spokeshave. It occurs to me that when building Stick chairs, if properly sharpened and set this spokeshave would work wonders when cutting octagons from my square sticks. I would appreciate your thoughts, advice and warnings.
Thanks,
Rob
I hope Chris weighs in on this one. But: I think that would take a long time. I’d rather use a jack plane.
Hi Rob,
I have one here but don’t use it much. It’s too lightweight to handle wide chamfers on legs unless you take a thin shaving, which is slow. Maybe it would be OK for sticks.
When making legs and stretchers and sticks by hand, I use a jack plane to octagonalize them and taper them.
But please give it a go. I had to kiss a LOT of toads to get to the kit I use today.
I want to dabble my toes in stick chairs since buying the Stick Chair book/video and purchased a 1” Veritas power tenon cutter as well as a tapered reamer and 5/8” tapered tenon cutter. Are there any other sized tenon cutters that would be useful? I’m a bit turned around on which sizes are best.
Hi Clinton,
For making comb-backs and lowbacks, I use:
5/8″ power tenon cutter
5/8″ tapered tenon cutter
Standard reamer
For making Gibsons and other Irish-y chairs, I use:
1″ power tenon cutter
3/4″ tenon cutter