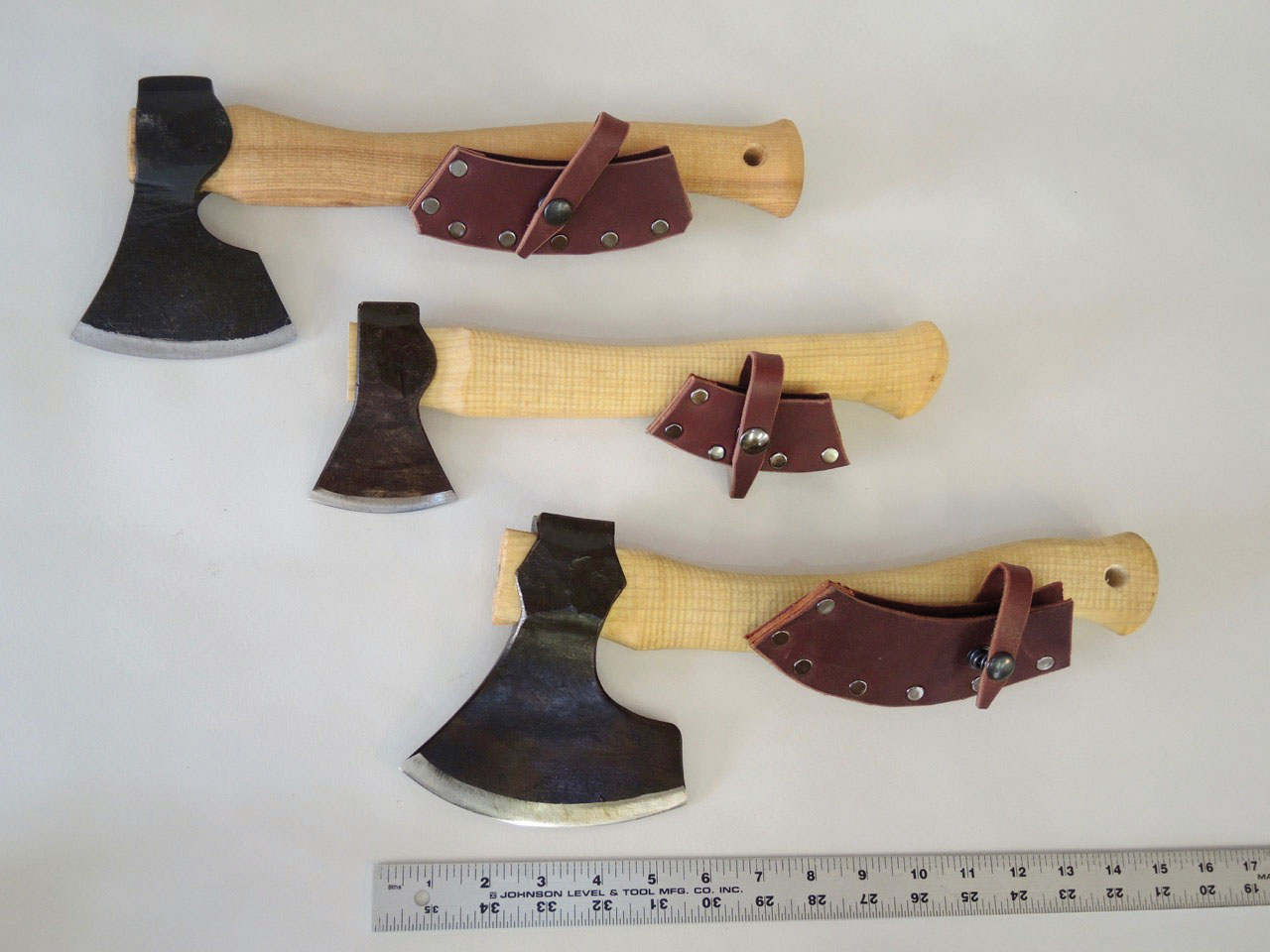
The following is excerpted from Drew Langsner’s “Country Woodcraft: Then & Now.” In 1978, Drew Langsner first released this book to the world, and it sparked a movement – still expanding today – of hand-tool woodworkers who make things with mostly green wood.
“Country Woodcraft” showed you how to split wood from the forest and shape into anything you might need, from a spoon to a bowl, from a hay rake fork to a milking stool, a pine whisk to a dining table.
After more than 40 years, Drew revisited his long-out-of-print and important book to revise and expand it to encompass what he learned since “Country Woodcraft” was first released.
The result is “Country Woodcraft: Then & Now,” which was expanded by nearly 100 pages and updated throughout to reflect what Drew has learned since 1978. Among many other additions, it includes greatly expanded sections on building shavehorses, carving spoons and making green-wood bowls.
Axes are honorary members of the primitive tools family. Axes are simple tools, but the good ones are also refined, the result of countless generations of use and thinking about specific requirements.Simple means that you need to do most of the work. There’s a definite learning curve, and practice is necessary to develop and maintain technique. As an example of this, you can watch Wille Sundqvist hewing a spoon in 1982 in a video posted to the Country Workshops YouTube channel. The video records Wille at his prime…a world-class axe master who grew up in rural Sweden when men used axes every day.
Safety First! Axes are easily the most dangerous hand tools. This is because they work with a throwing action. There’s accelerated force that doesn’t let off until overcome by friction. When using an axe, you must always be extremely careful – on your best woodworking behavior. During spoon carving, you’re holding the workpiece with your free hand, so you must be extra careful.
The first rule is that your holding fingers must always be on the backside of the workpiece, never gripping around or over the top. This rule always applies.
A few terms. These aren’t official, but offered here so that we understand one another. Axes are one or two handed. Single-handed axes are also called hatchets. Carving axes are single-handed hatchets designed for wood carving. In contrast to a camping hatchet, carving axes are a refined and tuned instrument. “Hewing axe” refers to double-handed axes that can also be a broad axe – heavy, with a massive blade, and a single bevel on the outer side of the cutting edge.
Carving axes are what we’re concerned with here – for working on spoons, ladles, bowls and maybe sculptural work. Broad axes are usually used for architectural work – timber framing and working on log structures. Much was learned about carving axes in the years after the historic Spoon Carving – Then photos of Wille Sundqvist hewing a spoon with my Kent hatchet were taken (in Chapter 26).
This appendix is an introductory guide to selecting a carving axe. Makers and models are provided, but these aren’t exclusive picks. Everyone has their own requirements, and different makers and models are available at different times.
Weight isn’t a major factor with double-handed axes, but it’s an important consideration with carving hatchets. Because they are single-handed tools, all of the grip and heft – power – are concentrated in one hand and arm. This statement seems overly basic. But consider trying to fasten something with one connector compared to using two connectors that are spread apart. The single fastener requires enormous connectivity when stability is a consideration. With a double connection the stress per connector is much less than half.
With a carving axe comfort is exhausted quickly as axe weight increases. This is felt in your hand, wrist and forearm. This is not only tiring, but can lead to a loss of control – even releasing the axe unintentionally. Older users – like me – should be particularly concerned with axe weight.
A carving hatchet should be light enough that you won’t become tired using it. Svante Djarv’s Baby Axe weighs less than 1 pound, with the handle. Spoons are small things that don’t ask for a big axe.
The cross section of a carving axe handle is critical to the user’s comfort, especially after the first minute or so of use. I’ve been trying to understand what makes the perfect feeling/gripping handle cross section going back to before Country Woodcraft was originally written. I still haven’t figured this out. I have favorite carving axes with handles that contradict one another.
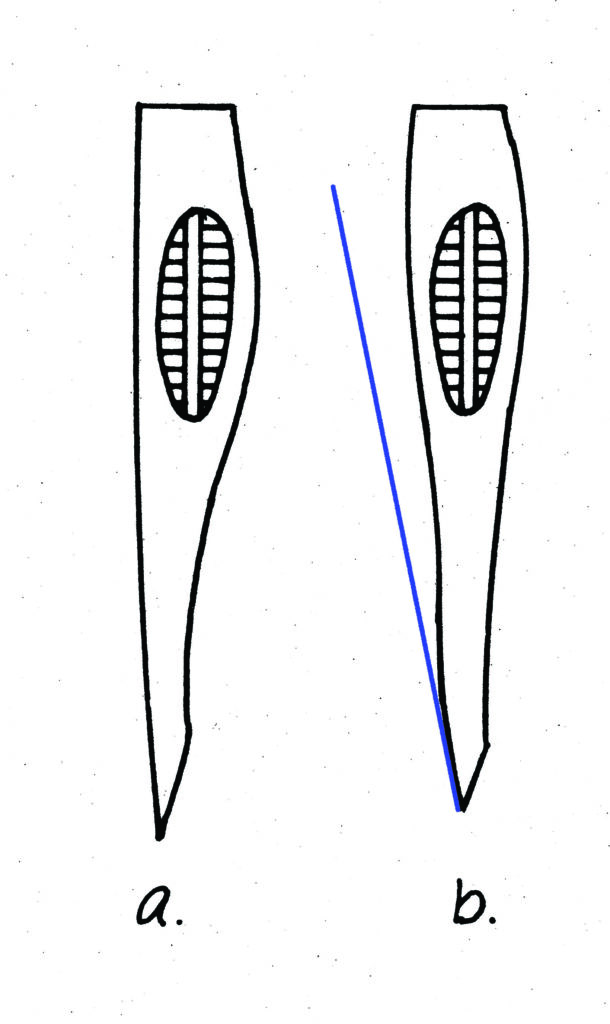
Balance. One of the problems with the Kent axe is that the head hangs below the axis of the handle. It always wants to flop downward. It also has double bevels, so you need to hold it at a rotational angle for the edge to slice wood. This means that you’re always expending energy to correct the hanging angle. The problem is – sort-of – remedied by increasing the size of the poll, the hammer-like protrusion at the top of the axe head. But this increases the weight – probably not a significant problem in the past when axe users were tough and strong.
Angling the piece being axed partially solves the problem. Then the axe swing is closer to plumb.
Balance comes about with good design. The axe head shape, and the angle of the eye relative to the handle, can be made so that the handle axis is in line with the center of gravity of the head. The objective is that the axe can be deployed at a rotational angle without needing to physically pull it into the desired plane. This can take various forms, all with pros and cons, of course. The carving axes in the photos all have good balance.
The reproduction 10th-century Viking axe (shown on page 99) has exceptionally good balance. The original was probably an all-purpose tool, used for butchering, fighting and even woodworking. The axis of the handle is in line with the center of balance of the head. This means that it can be swung in any direction, without the distraction of the head wanting to angle downward.
Bevels. There are three possibilities – symmetrical double bevels, single bevel and hybrid double bevels. A symmetrical bevel is the most versatile configuration, even allowing a moderate scooping action. But it requires angling the axe to get a controlled, supported cut. This is where axe balance is consequential.
The single-bevel version is known as a broad axe or broad hatchet. It’s like a chisel used with the flat side inward. There’s minimal angling needed for getting a controlled cut. This makes single-bevel axes easy to control. Gravity does much of the work. It’s possible to hew a convex shape, but concavities are out of the question.
The hybrid version is sometimes called long and short bevels, or asymmetric bevels. The inner bevel is longer and at a lower angle than the outer bevel. These often come about as a user-made modification of a symmetrical-bevel axe. With this configuration you get some of the advantages of the double-bevel and single-bevel variations.
With any of these three configurations it’s important that the inner bevel is flat. If the inner bevel is convex – slightly curved from cutting edge toward the head – you would need to tip the axe outward to get it to cut. Then you lose support of the bevel during the cut. The axe will tend to bounce away from the work.
There’s some confusion in the broad axe realm as to what version is right- or left-handed. Right-handed means that the left side is the flat side of the head when the axe is held in your right hand. The bevel is now on the right.
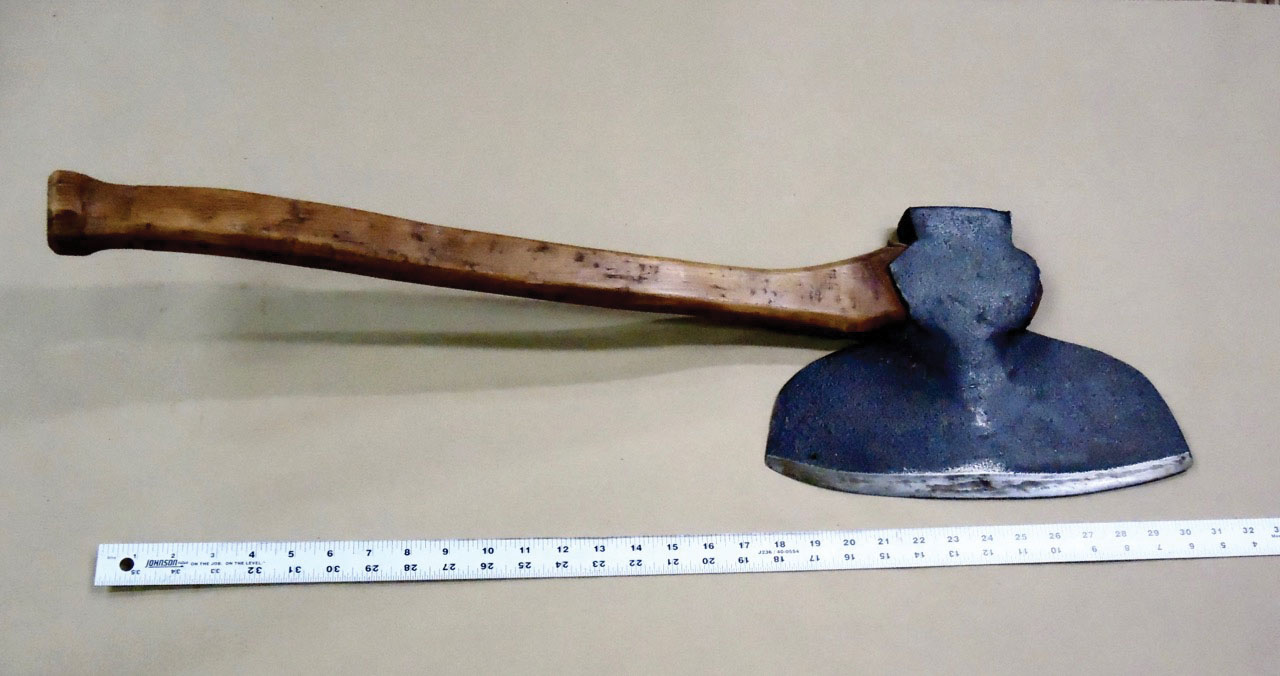
Clearance. There should be some clearance when you hold a straightedge on the inner bevel – or the flat side – laying the ruler from the cutting edge toward the eye of the head. The straightedge shouldn’t bump into a bulge at the eye for the handle. This doesn’t matter with very light axe cuts, but it’s a disqualifying factor if you’re using the axe with enough force that the eye of the axe head passes the work during each swing.
Clearance is a design problem, not impossible to solve, but annoying to get right for some toolmakers. Clearance can sometimes be jimmy-fixed by regrinding the angle of the inner bevel on an existing axe head.
Cutting edge curvature. Axes are most efficient when used with a slicing action – the wood fibers are cut in succession and at an angle. That’s the reason for the curved cutting edge. The cutting angle is also regulated by the angle of the edge relative to the handle axis. And to how the user swings the tool – a matter of skill and preference.
Can confirm that axes can be dangerous. I won’t get gory, but I nearly lopped off three of my fingers a few months ago. Thankfully, everything turned out fine and I now have regained full sensation and function. Just be careful and don’t rush! They’re still fun to use!
In case you hadn’t seen it, NPR has a wonderful article about using medieval tools and techniques being used in rebuilding the cathedral. This includes axes fabricated specifically to the standards of the original construction. The pictures are beautiful and informative.
https://www.npr.org/2023/06/11/1179648233/notre-dame-paris-fire-rebuild-roof
Can I get a clarification?
Years ago, I was playing with my newly-made, four-pound, short-handled broadaxe, and lost control of it. It hit the floor equidistant between my bare feet. I thought, “Jeez, I’m clumsy.”
Are you telling me now, that my actions were imprudent?
Couldn’t you have mentioned that a few years ago? I might have dulled the blade!
Sorry to go long… Concerning the article section on weight, consider this information as gold. I have three carving axes (aka hatchets). My first purchase was the Swedish Gransfors Bruk Large Carving Axe, which on my home postal scale weighs 2lb 2oz. Being my first, I had no reference to compare. It eats wood with authority, but it will wear me out soon enough (and I’m not a petite woodworker).
So I kept buying, and next came the Gransfors Bruk Hand Hatchet (model 413). Wow, at 1lb 3oz it makes a world of difference. It, too, eats wood, but with smaller bites, and a whole lot less stress on your arm and upper body. It has a very short handle (like a small adze) but it has the advantage for packing on your body into the wild, and excellent control at the chopping block. I’ve reshaped the cutting side inner bevel of each GB axe similar to Drew’s article, drawing B, a great change to each tool.
(The GB Small Hatchet model 410, which I don’t own, is their smallest and lightest at .7lb. Think tack/trim hammer weight. A viable option if every ounce matters to your body.)
Buy GB axes only through authorized dealers, shown at their site. Amazon is not an authorized dealer, no warranty.
Last, my Swedish forged Julia Kalthoff Small Carver axe, the only axe she makes, designed specifically for carving work. This axe comes in at 1lb 6oz, and performs beautifully just as the smaller GB axe, and it’s easy on the arm. The 3 extra ounces over my small GB is found in its traditional length handle. Julia makes her axes to order so there is a bit of lead time, but well worth it, such a great tool.
Try before you buy is great in theory, but if you can’t, start with lighter axes (hatchets) before going heavy. And don’t be afraid to modify the bevels and handle to suit your body and your work, it’s only steel and wood. And here in the USA, I’ve since learned of domestic smith’s making similar great axes, but at three I already have enough.
I once met the grandson of Dr. Charles Mayo, one of the founders of the Mayo Clinic, who is also a medical doctor, and an avid crafter. I noticed that he and I have identical scars across the 2nd knuckle of the thumbs on our left hands. I asked him how he got his. He replied instantly that it was with a hatchet. Bingo! We’re blood brothers.