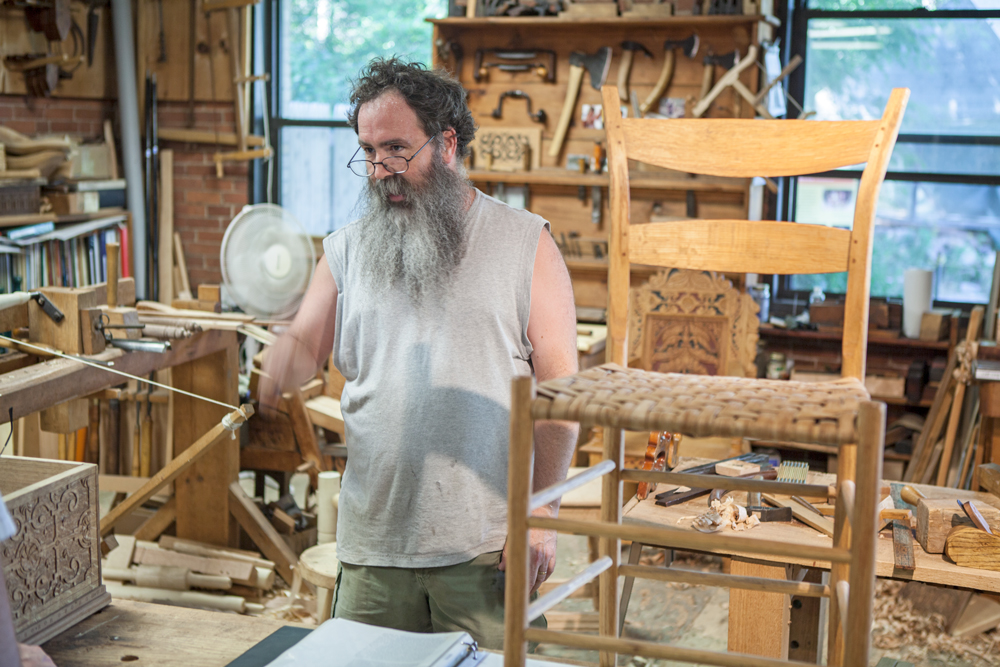
We are quite pleased to have joiner Peter Follansbee as the host of today’s Open Wire.
Peter’s specialty is 17th-century woodworking, though lately he has returned to chairmaking as well. If you love this kind of stuff, I recommend you subscribe to his brand new substack, which is named Follansbee’s Substack.
Today Peter has given up part of his Saturday to answer your woodworking questions (feel free to ask about his bird watching hobby as well).
Here’s how it works: Type your question in the comment field. Peter will answer it. It is that simple.
Comments for this Open Wire are closed.
— Christopher Schwarz
Good morning Peter. Are you working on a new book?
Two – one about a large joined cupboard I’m copying and one about the people who taught me woodworking.
Whoops – I replied from the wrong spot & it fell through. Two books, one on a large, detailed 1680s joined cupboard I’ve been copying and a more involved one about the stories of the people who taught me woodworking.
I would like to make some stick chairs. I have in my possession some very straight oak I can rive. How long do I need to season the wood before I can use it for chairs? Is it critical for the seat and sticks to have similar moisture content?
well, you’d get a different answer depending on who you ask. I only really know ladderback & American-style windsor chairs. for those, I dry the shaved parts in a light-bulb kiln. You can weigh the batch of parts before & during drying. When they stop losing weight, they’re as dry as they can get. But for some, this is over-kill. Chis has a different approach – both work.
Thank you, Mr. Follansbee!
I have incorporated carving into my furniture for many years now. Very simple faceted edges, low relief etc. I do not build reproduction furniture although I try to derive inspiration from those pieces. My father who first taught me the craft past away last November at the age of 84. I want to build a carved box for his Bible and wanted to know if you could direct me to some source material for carving patterns that wouldn’t be out of place on a Bible box?
Jeff – condolences about your father’s passing. The carving patterns I learned by studying furniture in museum & private collections. Books on furniture history often have a chapter or two w illustrations of early stuff – specific books about oak furniture get pricey, usually out of print. My favorite is the new edition of Victor Chinnery’s Oak Furniture: the British Tradition. I have a slew of videos on youtube showing carving and some plans available for purchase on my blog Joiners’ notes. And the Lost Art Press book Joiners’ Work has a chapter or two on carving.
Thank you Peter!!
Jeff – This may be a good starting place to find additional information:
http://www.pageaucarvings.com/index.html
What should I look for in a vintage (or new) draw knife? I’m planning to make a JA chair some time soon and need to buy one, but am unfamiliar with the details. Apart from 7″-9″ inch in size, I have no clue what to look for. Does bevel up/down matter? Curved or straight? Thank you!
Till: it matters to some. Not to others. JA in the last “phase” of her career favored one with a slight curve in two planes. Viewed from above the edge curved toward the user and viewed dead-on at the cutting up it swept up a bit. The Lie-Nielsen knife comes very close to this & I use JA’s version of that tool. But a flat knife works too, we used them for years & years. Sharp is most important, the rest is just details.
Hey Peter, love your work, your focus on historical furniture and methods.
I am looking to get into carving but live in a relatively dry spot in terms of antique tools. I have no v grooves or gouges. What sizes should I start with?
Noah – As for antique tools. If you have a mailbox then you can buy old tools as well as new. There’s several on-line sites Hyperkitten, Patrick Leach and others I can’t keep track of. For gouge sizes, start with just a few if you’re first getting going. Then add more once you find out you’re obsessed. You can download a chart Jeff Lefkowitz did for me about the tools I use –
https://pfollansbee.wordpress.com/carving-gouge-chart/
My V-tool is a semi-modern one, Swiss Made from 35 years ago. About 45° or 50°
FYI, if you go out to Plymouth (sp) and tour the place (where Peter used to work), you will find a lot of Peter’s work in the houses. It’s fairly obvious if you are familiar with his work. What’s really cool is you open the pieces, etc as it’s a living musume. It was a good day spent there.
Hi Peter, many thanks for your work on 17th century joinery – it’s been such an eye opener for me. I have a few queries about joints in a joint stool. First, is it important for drawbore pegs to go into stiles perpendicular to the face or can I use an angle to avoid hitting pegs on the adjacent face; second, should the undercut of a stretcher’s back tenon still be clear of the stile/leg once the pegs are in; third, how green can the seat afford to be when it’s fixed? Sorry, lots there but any thoughts appreciated. Huw
Huw – Re: the pegs on M&T joints in a stool. I stagger the heights to avoid the pegs from around the corner. Generally it’s best to keep them fairly perpendicular to the face of the joint. It just minimizes any weirdness. The rear shoulder’s position shouldn’t change during final assembly. It’s either in contact with the stile or not – usually not. Seat moisture content. There, I like the boards pretty dry. Their shrinkage will be in the thickness so they can get a little rattle-y if too wet at assembly. That being said, it’s pretty hard to go wrong. JA & I did all manner of things when we were sorting this out.
I was fortunate to take your carving class at the North House School years ago and now add decoration to cutting boards and cabinet panels. However, after a weekend of carving my hands are sore. How do you do it?!
John – without seeing what you’re doing, I can only guess. Grip tools with less force, common to use a death grip. Beyond that, sharpening always helps. Once I have gouges the shape I like it’s often just stropping to keep them tuned up. And I always use the best wood I have, straight, clear and radial. All that combines to make it very easy going.
Good morning, Peter. I admire your work highly and have learned much from your book, Joiner’s Work. I also am trying to work green wood with hand tools. Besides splitting wedges (and a sledge hammer, of course), I have a froe, a double-beveled hatchet and a hewing axe. Any other axes you’d recommend and if so, where would you recommend looking for/purchasing them? Thanks!
Garret – sounds like you might be all set. If by “hewing axe” you mean a single-bevel axe that’s the one I use for hewing joinery stock. Mine’s about 3 lbs, maybe a 6″ cutting edge. So larger than a lot of “carving” axes today but smaller than a timber-framers’ axe. One-handed.
Thank you very much, Peter. Yes, by “hewing axe” I meant a single-bevel axe. Mine is a vintage Kent-pattern one with a 6″ straight cutting edge and a 13-14″ straight handle. I keep it razor sharp to dimension and clean up the faces and edges of the wood billets I froe.
Good morning! Thanks for the inspiration and insight you provide in mastering green woodworking.
I watched many times the museum presentation JA and you gave. I loved how it was written so that you were her straight man, the dynamic was very funny. Was it written and rehearsed a bit in advance? Do you have other presentation plans / outlines in the documentation you inherited?
I assume you mean the Colonial Williamsburg demos – the last time JA & I presented together. No, we didn’t rehearse, other than decided what information to cover, i.e joinery, turning, etc. So there was a plan for content, but what came out of our mouths was just what happened. I rarely know what I’m going to say when I step up to a stage. I don’t do much of it these days…but it was always fun. And because we didn’t really have “scripts” or “outlines” there’s nothing like that coming from the JA papers.
Good morning Peter.
What is the typical or average length of a strip of hickory bark used in seat weaving? When harvesting bark, what is the minimum log length you’d want to use?
Joe – I live in a hickory-starved area. There’s some but not great specimens. When I started out, if I got 10′ strips I was happy. Lately, through the help of our friend Brendan Gaffney I got turned on to hickory logs 30′ long & longer. More work harvesting the bark, but less work weaving the seat. Either works, shorter stuff just means more joints under the seat. To some extent it’s just about what length log you can handle.
How do you source green wood? I see you splitting beautiful oak logs, but I wouldn’t know where to begin finding similar logs. Any insight would be greatly appreciated. Thank you!
Stephen – I have used many different sources over the years. Firewood cutters sometimes set good logs aside to sell on to mills. Try them. Small sawmill operations often will sell a single log, I did this for over 30 years. They let me split it there (after I paid for it!) and haul it away in pieces. Recently I got a log from a log merchant who buys them from the wood cutters and sells them to the mills. Tree service people in your area are worth talking to as well, though yard trees rarely yield great wood.
Good morning Pterer. I appreciate your spending time with us today. A question about the 1680s chest shown in the post earlier this week. Are the turnings stained black? And if so how?
Terence = painted black. Lampblack pigment mixed in linseed oil and thinner. Thin coats x 2. Moldings too same setup…
Peter sorry
Hello Peter,
I am working on a joined chest using your plans and am curious about the choice of thickness for the tenons, particularly for the rails entering the stiles. They seem thin to my very inexperienced mind. Is there a reason they were not thicker? Is it a matter of ease of chopping and the shear number makes them strong enough?
Thank you for enabling this great project!
Andrew – I’m reminded of a quote Alexander & I used to drag out now & then. “I don’t care how weak it is, as long as it’s strong enough.” But really 5/16″ is fine, I’ve seen hundreds of joints this size that are over 300 years old. That’s the kicker. it works. So I stop thinking about it.
Peter,
Always great to communicate with you. I have made two oak boxes, one red and the other white and look forward to making a few more pieces. I have a few questions.
What do you think are the best steps to learn Strap Carving (Next Box)
You often work with red oak and not white. why? I want to make a stool in white, does it turn differently than red? I will be using kiln dried wood.
Do you have a preferred film finish (not paint) on your boxes?
Is there any history of handles on the boxes (iron or otherwise)? The boxes can be heavy.
Fred – in no particular order. I use red oak more because it’s more available here and dries more easily than white. White does turn better than red, less chipping. Neither are great turning woods. I use linseed oil with a thinner – there’s sometimes a varnish mixed in on period finishes, but I quit using it. I hate finishing. I’ve not often seen handles on them, but when I have, they’re iron. not sure they’re original though…As for strapwork, now I’ll be like a college professor pimping his own book. Joiners’ Work has a section on strapwork and I did some videos about it too – which I hope to re-do this year. They’re still valid though https://www.youtube.com/@MrFollansbee/videos
Peter: thanks for all you do and have done with research and sharing your knowledge and experience.
Two related questions: if wanting to build a joined stool like from your book, how small of logs can you get away with assuming a centered heart and straight grain?
Second question related to the first: we just had a large red oak taken down and many of the branches and secondary trunks seem to be of decent quality. Any reason they couldn’t be used for the smaller bits and pegs?
choirboy – for the frame of the stool, you don’t need a huge log. 18″ diameter will usually do. but you never can tell til you get inside. You’re tossing the sapwood and the innermost heartwood. If you want a 10″ wide single-board seat – you need a log more than 24″ in diameter. I steer clear of branch wood and anything above the main trunk because that wood is usually (always?) in tension and will dry unpredictably. Or I guess predictably, it will go haywire.
Good Morning, Peter
Do you start the initial split of logs from the crown to root or visa versa? Does the plan change for lesser diameter logs such as ones used to make a split rail fence? Thanks.
Larry – I learned to split from the top down. I just read recently though for subsequent splits to go the other way. No reason given though. I tend to split toward the thicker end.
No question. Just want to comment that you’re an absolute hero of mine and legend of the craft. Thanks for all you do and the content you share!
Cheers,
Dan
Dan – thanks yourself. Glad to do it…and I appreciate the boost.
Hi Peter,
The plans for the chest with a drawer call for fairly thick material in the frame (e.g. 1 5/8″, 1 7/8″, and 2″). Would it be reasonable to use kiln-dried red or white oak in 6/4 and 8/4 without changing the overall dimensions or joinery?
Thank you!
James – make substitutions at will…what Jeff & I worked up in those plans stem from notes I made from about 10 or 12 related chests…those guys consistently worked close to what we drew. but there’s loads of leeway so have at it.
Hi Peter,
I was wondering do you see a common thread running through the carving of eastern areas such as Northern Turkey and the Carpathians (and further east maybe as well) through Germany and to Anglo Saxon land? What are one or two good resources to research this further?
Jeremy
Well, my knowledge of non-British stuff is minimal at best. What I learned all along is the stuff I saw in England (& by extension what I see in New England) descended from the Italian Renaissance, filtered through Northern Europe and mixed with the earlier medieval stuff. Almost everything I know about stuff in the Carpathians stems from a friend I’ve never met – Tamás Gyenes – he & I have parallel woodworking interests – his site is here https://acsoltlada.hu/index_en.html Jögge Sundqvist showed me a lot of stuff about Swedish furniture – and a lot of that was very familiar in construction, form and decoration. There are parallels all over creation just about. I don’t know where to send you for references…sorry.
Thanks Peter. Have a good one!
When I was a kid, we used to love watching the pterodactyls. They were very graceful in the air, but terribly clumsy on the ground. Do you like watching the little birds, or do you favor the larger birds of prey, like hawks, owls, and eagles?
Ralph – I’ll take them all. I spent two weeks in May watching for the spring migrants, little ones all. In the treetops to boot…
Peter thanks for the time you spent on the blog. As always you were entertaining and straightforward in your comments.
Bob
Hi Peter,
Greatly appreciate your writing, drawings and videos. I have read and watched all I could find and it is entertaining and educational. Fantastic stuff and I look forward to both books you are planning.
The decorative carvings you are doing on your spoons these days are similar elements to your 16th century work. I don’t recall you discussing specifics of how you do the decorative carving on your spoons anywhere. Do you use the same kit or smaller version of the same tools? Any different techniques or work holding for the decorative spoon carving?
What is the best bird you have seen this year? (I often show my wife and daughter after you post a good one)
On the carvings on spoon handles – I used to do straight-up chip carving with a small pointed knife. Then I adapted the oak carving designs to the spoons – and I never wrote it up on my blog because it’s so treacherous – a small carving gouge being pushed with my right hand into a spoon handle held in my left hand. Takes great concentration and care to keep the tool out of my flesh. And that’s hard enough without setting up a camera to shoot it. BUT – I haven’t carved many spoons in the last 2 years. Not around a good supply of crooked limbs. Birds – well, some of the small warblers my friend Marie & I chased were great, but fleeting views/no photos. I guess the scarlet tanagers I photo’d this year might be my highlight of the spring.
The main carving gouge I was using to decorate spoons was an antique about 1/4″ wide.
Hey Peter, hope you’re well! I have a question which is more chicken & egg than technical. From what I gather (and forgive my mistakes), your early woodworking experiences led you generally in a green wood direction, with Windsor chairs, and Drew Langsner’s Country Workshop courses, with timber framing, basketry, spoons, etc. At some point you took a class with Jenny Alexander, on how to make her version of a ladderback chair. And later the two of started figuring out how 17th C American pieces were put together, I guess initially with the help of a friend of Jenny’s at Winterthur and some scholars you met subsequently. From theory you dived into doing, it seems. I’m curious, what prompted the dive? Was it a congenial challenge, to make the first 17th C-style piece, to pursue a new vein of the green woodworking you already knew you enjoyed? Or was there a stylistic pieces or pieces you saw, that drove your interest to recreate? Or perhaps it was a back-and-forth between developing new skills, and aesthetics. Just curious. I mean Jenny stuck with making chairs, as much as the theory of the older pieces you two investigated interested her. And you’ve continued to pursue a wider range of styles, with spoons, baskets, Moravian and Democratic chairs. Anyway, best wishes. Thanks for doing this, and thanks too for the classes you teach!
Hi Brian –
You have most of the sequence there, but a little out of order. I met JA & Drew at the same time, 1980 at JA’s second class ever. Mid-80s I was a regular there & re-connected with Alexander then. She loved a captive audience and was showing us a slide lecture about a dis-assembled 17th-century cupboard door she’d photographed at Winterthur w Charles Hummel and Benno Forman. I seemed to be the only one who “took to it.” Looking back now, it’s furniture that was made all around where I grew up & still live – so a connection to local history too. But that came later. It was just an intriguing idea – make a chest from a tree, in addition to a chair. So much easier than making them from boards…
Good afternoon dudes. Mr. PF I find myself attracted to your blog for the birds, equally to the woodworking projects. Would you care to share with a fellow enthusiast some of the techniques and equipment you’re using to get such interesting and sharp images?
Kyle- for bird photos, I’m minor-league. the best shooters have budgets way beyond mine. I use a Nikon D300 w a 300mm zoom lens. And I shoot a lot & delete most photos. My shop has proven a pretty good blind, a little quiet this season so far though.
Thanks for the response? ! I’m much the same way, everything is “worth a shot” only to get home and delete 95% of it. I’m fortunate to have stumbled upon a local population of Prothonotary Warblers that love posing for the camera and make it a little easier.
I’d love to edit out that question mark.
Kyle – there’s a long story about Jennie Alexander and prothonotary warblers. I’ve never seen one, though I look every time I’m south of here.
I used to be a picture-framer part-time to support my meager chairmaking life. JA had me frame a print of John James Audubon’s prothonotary warbler. And she told me about how that bird figured in the Alger Hiss case. At one point it came down to the investigators wanting Whittaker Chambers to prove he knew Hiss well. Chambers said “well, Hiss had seen a prothonotary warbler and was excited about it…” words to that effect. And that proved to be true. Now, where does JA fit in? She was a lawyer and wanted this framed print on her office wall. The morale of the story for her clients: “Be careful what you say, be careful who you say it to.”
https://algerhiss.com/history/the-hiss-case-the-1940s/the-hiss-chambers-relationship/the-prothonotary-warbler/
Mr. Follansbee, thank you so much for showing us some amazing work and technique. Your skill and confidence with the axe are inspiring and nerve-wracking. I’m interested in getting more in to green woodworking and would love to learn more about building furniture/chests and medieval joinery. Can you point me towards any resources that would help?
Alex – I feel like a heel saying so but my books, videos etc show you what I know about making things like chests from logs. Medieval is a bit before my time…but not sure how different it is. Lost Art Press sells two books I’ve done – Lie Nielsen has videos we did – and my wordpress blog has links to my own videos and on & on https://pfollansbee.wordpress.com/
Please don’t feel like a heel. I’ve been slowly availing myself of the wealth of materials you, Lost Art Press, and others have so lovingly prepared. I suppose there is only one thing for it, go forth and try.
In my opinion get Mr Follansbee’s book Joiners Work and his video on making a chest and you will have a great start on green work and joinery apllicable to medieval futnaure and The Anarchist Design Book has staked furniture and boarded furniture including an aubery, medieval style furniture. What you learn from them can keep you busy for years
Two questions on ladderbacks if you will. First, I’ve really struggled to get slats out of green wood. I try to rive them slightly oversized but always end with runout and a useless piece. Don’t have a riving break yet, so that might just be the issue. Otherwise it’s about 1/2″ that I’m trying to drawknife down. The solution has been taking air dried stock and running it through the thickness planer until 1/8″ thick. Got about a dozen chairs out that way but would love any advice you have on drawknife method.
Second, I’ve only ever used shaker tape for the seat. Took the hickory bark harvesting class last summer at Pine Croft in Berea (strongly recommend, one day and lots of fun), so now I have some but I don’t really know how to work with it. Any book or video recommendations (yours or others) for how to splice and weave with bark?
Thanks for all you do and for your time answering this and so many other questions.
Chris – backwards – the bark seat weaving gig. It’s covered in JA’s 3rd edition of Make a Chair from a Tree here at Lost Art press. I think I did a stand-alone youtube video of it too & I know it’s in my vimeo series on making the JA chair – but I plan on re-shooting the seat-weaving chapter. Nothing wrong with the techniques in it, I just wasn’t happy with the video work. https://vimeo.com/ondemand/jachairpf and https://www.youtube.com/watch?v=sob896LHvXg&t=1336s
Now – about slats. Without seeing what’s happening, it’s hard to say. Are you splitting them radially? You can always jam that blank in a strong vise in lieu of a brake. Or the shaving horse jaws sometimes. Mine are thicker than JA’s – I make them 3/16″ thick. I shave them with a slightly upswept drawknife which helps. But a flat knife works too. use the best wood for slats – dead-straight. Skew the knife. Sharpen.
not sure why that says that video doesn’t exist – but search my youtube channel & you’ll find it.
Thanks Peter for your willingness to share so freely over the years. Do you have any experience with using the inner bark of slippery elm (ulmus rubra) for seat weaving in chairs? It is common in my area and I have better access to it than to hickory. I recently cut some lengths out and it worked up nicely. Haven’t tried it in a chair yet. The mucilaginous nature of the inner bark made it separate out easily. Thanks.
Glenn – I bet it’s fine. I’ve never used it. Back in 1978 JA shied away from talking about elm in the book because of Dutch elm disease, though I gather slippery elm is not susceptible. One way to find out, weave it!
Will you be going to HandWorks or GreenWood Fest this September?
Also, any thoughts on the spell carvings Chris S. is doing?
Eric – I’m from New England. Iowa might as well be on the moon it’s so far away. And I almost thought about the North Carolina gig, but the only class I have scheduled for the rest of this year is in Sept and I finally learned to not book too many things back to back. Thoughts on Chris’ carvings – of course I have thoughts about them. It’s about time…all that plain furniture all those years…
Peter —
Thanks for doing this. I enjoyed MACFAT and am looking forward to building my first ladderback chair. (Probably scaled down for the kids.) Do you have any experience using pin oak? It seems to have a bad reputation as lumber but fast growing oak so should be just the thing for a JA chair…
I’ve never used it but seen it growing dead-straight. that counts for something. I think it’s part of a red oak group. I say if you have a straight section, make a chair from it. What’s the worst that can happen?
Hi Peter,
Thank you for doing this AMA. If you had to do some kind of woodworking different that what you currently do (call it a hobby that isn’t bird watching), what would it be and why? For me, I’m leaning towards carving little characters such as Doug Linker does on YouTube. It’s portable so I can easily do it on vacation and it doesn’t require many tools or materials. Looking forward to your thoughts.
Sincerely,
Joe
spoon carving. three tools, axe, sloyd knife & hook knife. perfect.
I made 2 chairs from trees probably 30 years ago. Literal tree saplings harvested in the spring debarked and went to work after drying the rungs out. They are rustic chairs but they will still hold me up 30 years later and have no loose joints. Back then I was reading a lot of foxfire’s books and there was several chairmakers that made chairs this way in the south. Have you ever built any chairs in the rustic sense described?