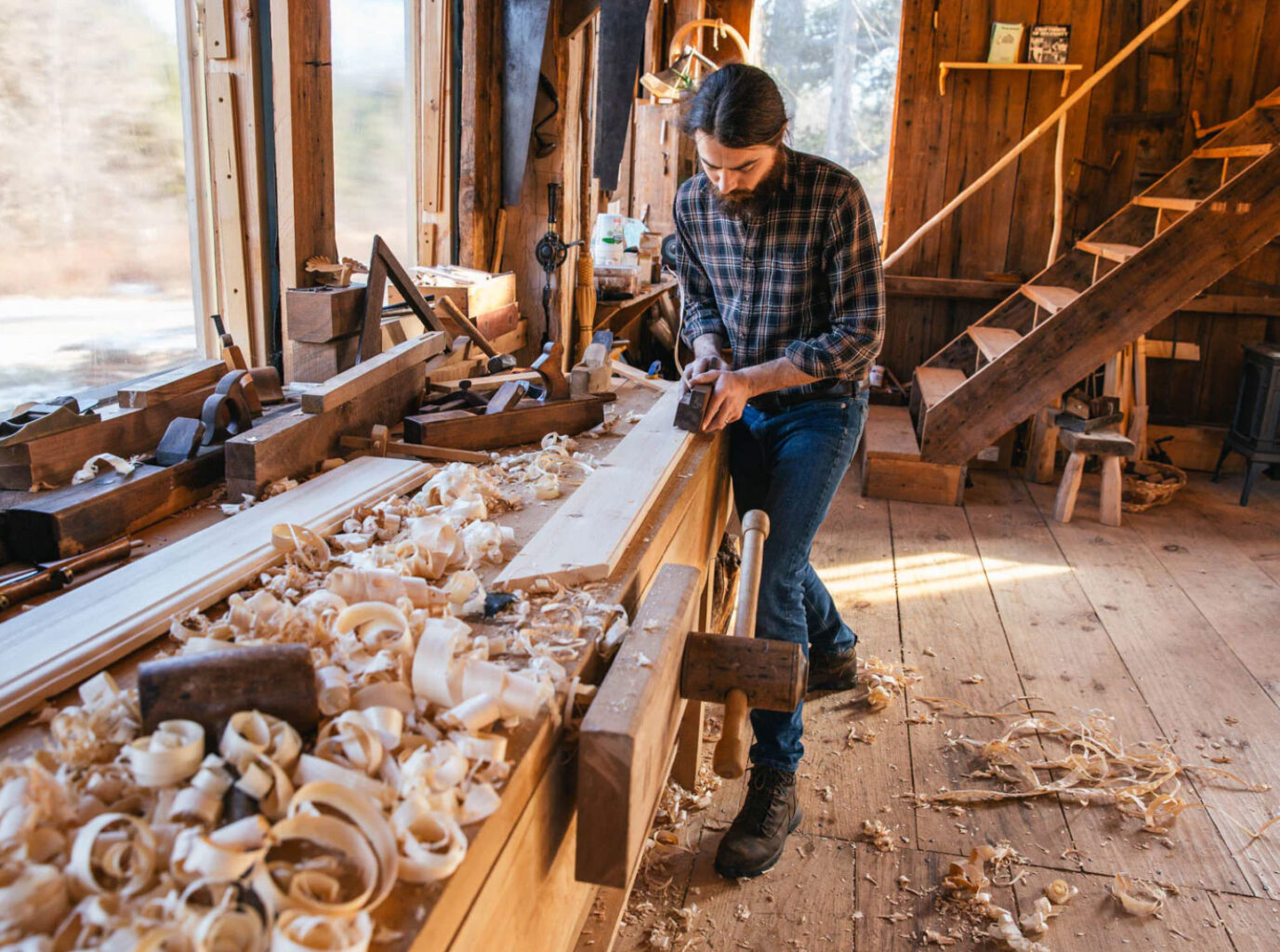
Today for our Open Wire session we have Joshua Klein, the founder of Mortise & Tenon Magazine, as our host. Joshua and his crew are as hardworking as they come. And so we were surprised when he volunteered to spend a Saturday answering reader questions.
Here’s how it works. Ask your question in the comments below. And Josh will post his response.
The comments will close for this post about 5 p.m. Eastern.
— Christopher Schwarz
Hi Joshua. Thank you for doing the open wire today. Question. When making a mortise and tenon joint what are your favorite saws and chisels?
Hey Philippe, My main mortising chisel is a Ray Iles and I love it. I also have various English “pigsticker”-style mortising chisels. They’ve all been faithful and reliable. All my saws are antiques, so I don’t name names to give per se, but I have a reliable crosscut-filed sash saw for shoulders and a nice, big tenon saw for the cheeks. Pretty standard arrangement. I’m not much for novelty…
Hi Joshua! Question, how does one determine if an old wooden hand plane cn be restored and what are the benefits of using a wooden plane over a all metal or transitional plane?
Eric,
There are a handful of factors, but the first considerations are:
1. Does it have all its parts?
2. Are the areas of damage (cracks, splits) easily repairable or is it beyond salvageability? (that’s a rare instance, in my experience)
Beyond that, it’s all about how much time and fussing you’re willing to spend. Most planes are restorable, but some examples would test my patience.
In regard to the benefits of wooden over metal, I’d say:
Lightness (why slug heavy tools around if you’re working by hand?)
Lack of sole friction (I never lube my soles)
Ease of adjustment (tapping is much more intuitive than knobs and doodads)
Comfort in use (Wood is warm and inviting)
Tactile Feedback (I can more easily feel the cutting action through the plane’s body)
Beauty (who doesn’t love the look of wooden planes?)
I’ve written about this here:
https://www.mortiseandtenonmag.com/collections/magazine/products/issue-four
posted a video about this here:
https://www.youtube.com/watch?v=qAHvmMdTqxs&list=PLCW9PYe4R8T1WBnNeoW8ewz3lxJxkPy40
and covered this most extensively in our Back to the Bench tool restoration course:
https://www.mortiseandtenonmag.com/collections/courses/products/back-to-the-bench-restoring-using-heritage-tools
Hey there, I know you guys have a leg vise and a nicholson vise in your shop. Are there pros and cons to either? Does the nicholson vise need pins in the pin board the same way a leg vise does?
Also, having trouble with a wooden jack plane blade coming out/ my wedge loosening very quickly in use. Is this covered in your plane restoration course?
Noah, There are pros and cons with everything, but I find I am happy with either style. The main difference is the horizontal vise has more holding room horizontally. The downside is that the track the guide rides is must be tight to the guide, but never stick. The pin system on the leg vise doesn’t have that complication. I love having both at hand.
That’s a strange issue that I’ve not often encountered (it shouldn’t be self-loosening), but going through the steps in the course should highlight whatever the issue is you’re dealing with.
Thanks!
I think either the wedge or iron are not original to the plane, and don’t fit the ears or abutments carved into the cheeks.The iron + wedge must be a very close fit to them.You may have a way to measure and compare, or use carbon paper to test the fit, which should tighten slightly towards the bottom of the plane, in order to concentrate pressure on the irons near the mouth. You may be able to trim the wedge for a better fit, or it might be best to make a new wedge altogether. Or swap in a tapered iron instead of a parallel one.
As your magazine issues sell out, will you be making more books like you did for the first three issues?
Eric,
Yes, that’s the plan.
In the Meet the Author you say that old time hand tool workers made furniture very quickly. To what extent do you think this was due to division of labour? For example making a Windsor chair in the UK would involve four or more different specialist.trades, whereas today a maker works through every stage. And as a follow-up do you see any difference between division of labour in America an Britain and Europe?
Terence,
Division of labor makes a huge difference in labor time, but I was referring to one-man shops. Those records are surprising. I believe this has more to do with agency in tool use and pre-industrial tolerances.
I don’t follow your second question… difference in what regard? Though America did not have a deeply established guild system of specialists, the nature of collaborative work is ancient and ubiquitous.
I’m planning on/hoping to build a small timber frame shop in my backyard, maybe 16 x20 with a loft. Are there any resources for plans you would recommend? Also, sources for learning timber framing?
Jack Sobon’s books are great. He’s the man.
Tedd Benson also has a good collection of titles.
I’d recommend the Heartwood School (run by the Timber Framer’s Guild – also a good source) for timber framing instruction, but there are so many other good schools out there teaching this. Start by building a chicken shed or doghouse. Do all your mistakes there – animals tend not to care as much about tight joinery as we do.
Joshua, sorry for this, but I have a question about the Moxon vise I saw Fitz use in a video. It’s clampable to work bench with hold fasts. I’m interested learning in the approximate dimensions of the front and rear faces as well as the block for the hold fasts. I want to build one to work on dovetails more efficiently, but I couldn’t find an LAP blog post about it. Any thoughts? Thanks. — Steve
No idea, Steve. I’d have to leave that to Megan.
Steve, Rob Cosman just did a video on Moxon vises about a month ago. He gives dimensions. I built one and it works great. He has a couple cleaver ideas to make it a little more user friendly, bronze bushing and springs. What I found when researching Moxon vises is the width is 20 – 24 inches and height is 4-5 inches. I used Woodcraft hardware and Rob’s spring and bushings. – Andy
https://youtu.be/dz9-Fg6fBLw
I use a Benchrafted twin-screw (usually), and all the dims are in the BC instructions. https://www.benchcrafted.com/download-files/Moxon_Vise_Instructions.pdf
A few years ago my local woodworking club invited a representative of an American manufacturer of PVA and liquid hide glues to give a talk on the characteristics and applications of their adhesives for wood. During the Q&A a member asked a question about the preferred glue for mortise and tenon joints. It surprised us when the rep asserted that the preferred glue is epoxy for that type joint. His reply was based on the fact that epoxy did not swell the joint components and acted as a lubricant for a tight fitting M&T joint, whereas, the water in PVA and liquid hide glue causes the joint components to swell, often inhibiting the ability to fully seat an M&T joint. This effect can happen when there is a number of M&T joints that must be glued simultaneously, providing for more time for the components to absorb water and swell before being joined.
What are your thoughts on the glue selection for M&T joints?
If you care about longevity, hide glue is the only sane choice for furniture joinery. Chris is right about this. If you can’t safely disassemble joints in the future, it is not repairable and will end up in the dumpster before not too long.
For more info about “liquid” hide glue and open time, see this post: https://www.mortiseandtenonmag.com/blogs/blog/how-to-make-your-own-liquid-hide-glue?_pos=1&_sid=8ebd3d679&_ss=r
Most interesting thing you have found while restoring an old piece of furniture?
Favourite furniture book?
Hmmm… there are always sewing pins and buttons. There’s also been some interesting graffiti from little hands. I have an 18th-century table (featured in issue: https://www.mortiseandtenonmag.com/blogs/blog/examination-of-an-18th-century-drop-leaf-table-issue-two-table-of-contents ) that has a shadowy figure underneath. Creepy!
I love Aldren Watson’s “Country Furniture.” And Roy’s Woodwright’s series is still gold. You need to own every single title in that series.
As a hobbyist I have a mostly unplugged handtool shop. I have learned from videos and books (yours, M&T, Paul Sellers, LAP, FWW, etc.) And I feel confident in making whatever I want.
Finish on projects is were I’m not confident. BLO, shellac, and paste wax are my normal for most projects but, that may not be best for the entry way table top I am working on. Can you point me to a good reference for traditional finishes.
Reagan,
Sam Allen’s “Classic Finishing Techniques” is a great starter guide to traditional finishes. And Don Williams (donsbarn.com) is an invaluable resource for this stuff. He did a video on it for PopWood: https://store.popularwoodworking.com/products/digv-furniture-design-dl?_pos=3&_sid=79d69b35f&_ss=r
Hi Josh! If I remember correctly, you said that you trained as a luthier at one time. Have you ever tried to make an acoustic guitar using only hand tools? I know that traditional thickness of of tops and backs was done by hand planes and scrapers, but I think that cutting the binding channel (which is now done with routers) would be very time consuming and difficult to keep consistent all the way around the guitar. What method would you recommend for cutting the binding channel by hand?
Dean, good question, and no I haven’t. I wish I had more instruction in that way of luthiery. I know the violin world works mostly without machinery and that would be the source of instruction I would beginning pursuing.
Hi Josh, I am a new subscriber to M&T! I have a couple of questions if you don’t mind:
if I made an oversized mortise relative to the tennon, what is the best way to tighten up the gap (would blue tape cut it?)?
I am making a workbench I planed on drawboring it with 3/8 dowels – do you think riven walnut is strong enough for that?
Thank you for doing this, Assaf
Assaf,
Thanks for your support! A sloppy tenon could be thickened by gluing wood veneer on one cheek. That’s the simplest way. Tape would not be a good idea because it would prevent glue adhesion.
Yep, riven walnut 3/8″ diameter would be plenty strong.
thanks for the reply, I feel like I need a clarification. I’m building a Roubo workbench. the tenon in question is for the leg to seat in the slab top. it needs to be removable so I am not using any glue. under those circumstances would tape work?
Oh, sure. Tape would be fine. Or don’t sweat it if it doesn’t cause any problems in use.
Thank you Joshua for the answer on the mortise-tenon question. The Ray Isles chisels indeed look great. Could you get away with just one or two and if yes what size? I ask as many sizes are sold out…
Philippe,
One will do most everything you need in furniture making. 3/8″ or 5/16″ are the most common. Try eBay (or eBay UK) for an old one if you can’t track down the Iles.
Last one for me. A silly one… what length and depth is your sash saw? 13ppi?
My go-to crosscut-file backsaw is 14″ long, 2-1/2″ to 2-3/4″ depth to the back, 10 tpi. By the way, I don’t know why I wrote “sash saw” – I meant “carcase saw.” I didn’t realize until read your reply… my woodworking brain must be slow on Saturdays.
Hello Joshua and Mike! Did you make hay rakes? Regarding making the tines, (or any batch of many same-sized pegs), what would be an efficient way to size the pegs/tines to dimension once split from the log? Thanks in advance!
p.s. Is Cameron Turner still writing content for M&T? I feel I have not read articles from him in a while.
No, we haven’t, but tines were shaped with something like a dowel plate. Don Weber shows shaping tines here: https://www.youtube.com/watch?v=DZzW9I9i7cw&t=758s
Cameron’s super busy these days – we miss his posts.
Thanks! I did not find that video before, it will be extremely helpful to show to a blacksmith to get a proper one made. Have a good open wire, I look forward to read everybody else’s answers at the end of the day!
I’ve made several hay rakes – because I’m not in batch production, my method for pegs is to shave down a long piece of round stock to uniform size and cut to length. A doweling jig would be useful for making multiple rakes. Cameron is taking a break from writing to focus on other things at the moment, but we hope to see him again in the not-too-distant future.
Thanks Mike, I will use the shaved and cut method for the first ones. Have a nice weekend!
I’ll jump in and say I’ve seen dowel makers made from a sharpened piece of pipe used for rake tines. It cuts to size faster than a dowel plate but perforce is less flexible, since it can only make one size.
Hey Joshua! In the entire eight weeks of this recent apprenticeship term, I never thought to ask, though I’ve often wondered; what is the origin of the M&T logo (the pyramid with the “S” inside it)?
I have no doubt you’ve talked about it somewhere before, but I’ve definitely missed it if you have. Congratulations with the progress on the house!
Hey Julian!
It’s from the frontispiece of William Hogarth’s “The Analysis of Beauty.” I wrote about it here: https://www.mortiseandtenonmag.com/blogs/blog/the-new-m-t-logo?_pos=1&_sid=4732c4db1&_ss=r
Joshua, Good morning! You and Mike recently put out a new series on restoring old tools. Of all the things you worked on, which tool was the most challenging to restore? Thanks!
Hey Scott,
Well, I gave Mike all the hard ones! In all honesty, saw restoration is something I am less familiar with – planes, tool handles, etc are things I’ve done many times over the years. My saw restoration has been minimal – I’ve always just opted for those that are straight and the teeth are in decent order, only needing an occasional touch up.
Really, none of these tools are that complicated. It just takes a bit of familiarity.
I have used wooden planes for several years and I wouldn’t have anything else. I have restored a jointer and a coffin style smoother that was my grandfather’s. I also have several European horn style planes made by ECE that I really like and use a lot. Have you used the horn type planes and your thoughts on them please?
Jeff,
I have and do not have a strong attraction to them. But neither do I have a problem with them. Not being from that tradition, I’m curious, what do you like about the horn?
I call pull or push the plane and the horn makes it easier to pull. I really have just gotten used to using them and find them easier to use than the coffin smoother and the American style jack planes that I have. The restored jointer plane is another story however. When I bought it years ago it didn’t have a wedge, I made one out of cherry, sharpened the blade and have been using it ever since.
Thanks for following up on this, Jeff! I appreciate hearing your thoughts.
Sorry the question was not well worded. But I think your answer was pretty much what I was asking.. From casual reading I have the impression that one man shops were more the norm in America vs the Old Word
Hi Joshua, I have a question about treenails / trunnels. Are they just different names for wooden dowels and draw bore pins? Or do they refer to actual wooden nails hammered into a piece like we would think of nails today?
Daniel,
It’s my understanding that “tree nails/trunnels” is a term for the wooden pegs used in shipbuilding. I believe this has been mistakenly brought into the modern timber framing world. Moxon, Nicholson, and other period sources call the wooden fasteners that hold mortise-and-tenon joints “pins.”
Here’s an interesting read that touches on historic timber framing pins: https://www.google.com/url?sa=t&rct=j&q=&esrc=s&source=web&cd=&cad=rja&uact=8&ved=2ahUKEwjxjteSnLr6AhUAKlkFHRQ1AJcQFnoECBwQAQ&url=https%3A%2F%2Fwww.tfguild.org%2Ftimber-frame-engineering-council%2Ftechnical-bulletins%2Fview%2F337%2Fdownload&usg=AOvVaw0siB1-LofZH297wb8j3KhC
Daniel,
It’s my understanding that “tree nails/trunnels” is a term for the wooden pegs used in shipbuilding. I believe this has been mistakenly brought into the modern timber framing world. Moxon, Nicholson, and other period sources call the wooden fasteners that hold mortise-and-tenon joints “pins.”
And here’s an interesting read that touches on historic timber framing pins: https://www.google.com/url?sa=t&rct=j&q=&esrc=s&source=web&cd=&cad=rja&uact=8&ved=2ahUKEwjxjteSnLr6AhUAKlkFHRQ1AJcQFnoECBwQAQ&url=https%3A%2F%2Fwww.tfguild.org%2Ftimber-frame-engineering-council%2Ftechnical-bulletins%2Fview%2F337%2Fdownload&usg=AOvVaw0siB1-LofZH297wb8j3KhC
Good morning, Joshua. On the cover of Worked (an excellent book, by the way), your right little finger rides on the side of the plane. I’ve seen a picture of Mike doing the same. Why is this preferable?
Gerry,
Here’s what I wrote about in my planemaking article in Issue Twelve: “Many planes from the 18th century and earlier had totes that were offset to the right (far side for a right-handed user) of the plane body instead of centered as became common in 19th-century planes. The reason for the offset is a debated topic, but I have found that it enables my hand to slip down onto the side of the plane which helps with control. Some theorize that the offset also works to counteract the pressure from the left hand on the toe. Could be. All I know is that I vastly prefer the offset, and I dare you to try it. The tote mortise begins 1-1/2″ from the right side of the plane body and is 1-1/8″ deep.”
You can also refer to my discussion of this in Hands Employed Aright – I first encountered the question in the midst of this research.
I can imagine that an off-center tote would indeed let, perhaps encourage, the little finger to trail along the work. Thank you. If you have time for one more answer, why do you suppose plane makers in the 19th C started to center their totes? Easier to lay out, perhaps?
The best guess I have is interchangeability (right- and left-hand users), but the problem with that theory is (unless I’m mistaken), historically, it seems most left-handed folks adapted their techniques to a right-handed world.
In “Hands employed aright” you discuss the “Mickey Mouse” template and replace a damaged tote on one of your plans with the mouse type. Several years on:
1. do you still like it?
2. if you were to make a toted plane which tote would you use and why?
Thank you!
Esther,
I love the offset position and general shape and am never going back. The “ear” I believe is decorative, however, not functional. In my planemaking article in Issue Twelve, I show the template I made based on other 18th-century totes. Here’s a shot of the tote I’m referring to: https://cdn.shopify.com/s/files/1/1087/8400/files/0131_Klein_Wooden_Plane_Making_Mortise_and_Tenon_Magazine-4.jpg?v=1643910286
Here’s where you could find the article: https://www.mortiseandtenonmag.com/collections/magazine/products/issue-twelve
Hi Josh, Have you decided on the type of roof material for the “Jordan House” yet? Wood shingle, terne coated standing seam, Vermont slate? Do you know what the original roof was and what is your timeframe for starting the roof? (It’s an amazing project to follow.)
David,
Thanks! Wooden shingles. We have a local mill that makes beefy-thick cedar shingles.
Timeframe is uncertain, but everything will be weather tight in the coming weeks. As far as shingles… that may or may not be before winter. I’m guessing it’ll be a spring project.
Thanks!
Hi Joshua, thanks a lot for doing this.
Is there a tool that you use daily but you still consider it a luxury? Examples In my case will be my kerfing plane or my swan neck chisel.
No. I get the most joy out of using the simplest tool for the job. The most “luxury” tool I use is a plow plane. Or maybe an occasional dado plane. But I’m not a fancy lad – I like the basics.
Joshua,
Loved loved Worked. I am building a (Chris Schwarz) bookcase and the lumber I brought home twisted after acclimating to my garage. I was in the verge of using my thickness planer when I read Section I of your book, and I resolved myself to flatten the boards with my jack plane. It’s been a challenge but rewarding, so thank you! Best to you and Mike.
-Chris
A reformed hand tool woodworker always reforming.
Amen, Chris. Thanks for the kind words! Glad to hear you found the inspiration you needed.
Hey Josh, what are your thoughts on manual hand-cranked drill presses for woodworking?
I’m mainly looking for a way to be able to drill very straight & precise holes in wood for furniture scale projects.
They seem to come in two varieties, the larger post/blacksmith version & the smaller workbench/tabletop version (clamped to the workbench). I’ve heard that generally the feed mechanism on them is slow – perfect for drilling metal, but not so great for wood. But, I’ve heard others say that on some, the feed mechanism can be released and if then used with an auger bit with lead-screw, the speed will be fine for drilling wood.
Manual drill-presses don’t seem to be talked about very much in the hand-tool world, so I’m curious to hear your thoughts. Thanks!
I’ve never personally had the need to bore such “very straight and precise holes” that I felt the urge to mechanize boring in my shop. I think they’re not talked about that much because they’re not necessary for furniture making. That said, there are a lot of clever artisans out there who I’m sure have found ways to work post drills into their production. Sorry I don’t have any more I can contribute on this.
Hi Joshua. It’s Saturday afternoon, your family is out somewhere and all the chores are done. What are you popping into the shop to do just for fun? Or are you doing some other hobby?
Chris,
Saturdays are family and homestead catch-up days. I’ve been building a settle table all week, so I’m catching up on other responsibilities today: farm chores, humanure bucket cleaning, writing prayers for leading tomorrow’s worship service, answering questions on this blog, etc. There is only one activity I am more passionate about than woodworking: theological study. I am always reading or meditating on some theological issue or other. Any “free time” I have, my nose is in some book.
Hi Joshua. I often find that researchers continue to find information on their subjects long after publication. And people will just randomly send things or point to something as well. Have you found more on Fisher or his works since your book came out?
John,
I’ve received a good amount of correspondence about the research since the book came out, but to my knowledge, nothing substantively new about Fisher has since been unearthed.
Loved the book would love another one of you playing furniture detective for us. Do you ever think you will release plans for the secretary or the folding card table in the book? Also would love to know how you do the wood grain painting. Thanks Joshua
Thanks, Clay!
I play furniture detective in my course titled, “Makers’ Marks.” You can find that here: https://www.mortiseandtenonmag.com/collections/courses/products/the-makers-marks-an-in-depth-study-of-handmade-furniture
I do not have plans for those plans, but I am interested in teaching grain painting and other decorative painting techniques one day. As soon as I have time!
Hi Josh and Mike. Are hewing axes generally held with the hands in the same position as one would regular axe? (or a hockey stick if that makes sense, given the wider grip). I ask because I’ll be making a curved handle for one but have never actually used one before. Thanks!
Adrian
Thanks also to the LAP crew for all you do.
Adrian,
Basically, yes. Curved handles just get your knuckles out of the way. They’re awkward to get used to… just like anything new, I suppose. Here… I’ve just unlocked this Dispatch post with photos of us hewing a replacement plate for the house project: https://www.patreon.com/posts/81812860
Thanks!
Josh, the Jonathan Fisher desk on the cover of Hands Employed Aright looks like separate top and bottom halves. Is this the case, and how would one attach the shelving/cabinet half to the bottom desk half?
Yes, desk and bookcases were often made into two pieces for practical reasons (moving, etc). The top is held in place by gravity… and by keeping the kids from climbing on it. Sometimes they have cleats for alignment, but these are not earthquake-friendly pieces.
Thanks Josh!
Are you going to write a book or produce a video documenting your house project?
I hope to, but we never know what a day may bring. Whether or not that book comes to fruition one day, I will feel satisfied with our daily documentation of the project on the Dispatch. We’re sharing every aspect of this build over there.
Do you have any tips on getting in to hewing? I have a broad axe head to restore and re-handle and a couple of usable basic axes/wedges.
In lieu of a class, watch some hewing videos and try your hand at it. It’s all about developing feel, and there’s no shortcut around it.
I know you’ve made a video about your leg vise. Is there a video on the Nicholson vise, on the construction and how best to use it? I know that Tom Fidgen has a video of him making one, but there’s little narration. Does it necessitate everything being squared/perpendicular?
No, I don’t have one specifically on that, but yes it does need to be accurately constructed for smooth operation.
I will be making a top for a kitchen island prep table from 5 to 6 boards of hard maple that’s 2in thick and 5in wide. For the joinery, would a simple glue joint be enough? Or would you recommended loose tenons pegged on the underside (or something else?) to join the boards together? Any advise for the construction is appreciated!
A gap-free 2″-thick edge joint is plenty strong! No need for floating tenons or anything. Just make sure you use waterproof adhesive in that application or you might be building yourself a future headache.