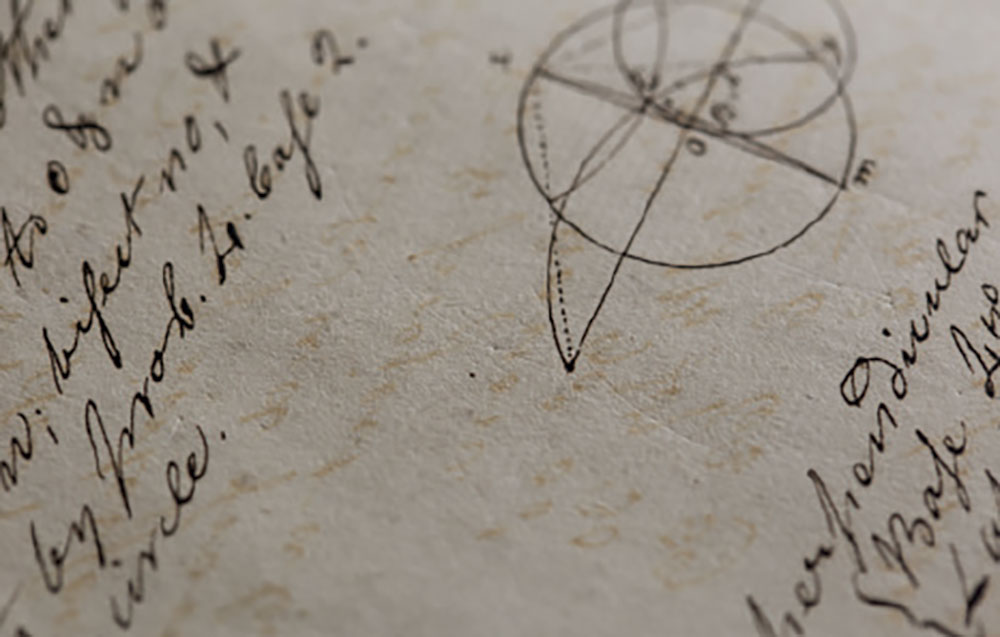
I am so pleased to have George Walker as our first guest host of the Lost Art Press Open Wire. George is a traditional woodworker who (with his friend Jim Tolpin) has spent nearly 20 years exploring and explaining “artisan geometry.”
Artisan geometry is the clever and simple system behind all the good designs and simple layout methods that flow from the bench. It is the footers and foundations of our craft – and that of architecture. And once learned, it will open your mind (and hands) to a simpler and more direct way to design and work.
George and Jim have already written four books about it for us, and they are working on a fifth.
If you have questions about this unseen world, George is here to help answer them today.
Here’s how it works: Type your question in the comment field. George will post his answer. It is that easy.
Before you ask a question, please read this.
- If you could limit the number of questions you ask to one or two, that would be appreciated.
- If your question is your first comment here, it will automatically be flagged for moderation. Your question will appear after I approve it.
So here we go…. Note that comments for this entry will close about 5 p.m. Eastern.
— Christopher Schwarz
Do you utilize the golden ratio in designing your furniture projects or are there other principles which are more important?
I do not use the golden ratio. Historically, artisans used simple whole number ratios. They’ve become second nature to me.
Really glad that you are participating in the LAP Open Wire. I own all four of your books and they have been so helpful in changing the way I see the world. Thanks. Please tell us more about the new book.
Mike,
Jim and I are deconstructing historic furniture examples to uncover design lessons hidden within. Many of these lessons are “rules of thumb” that makers used to tackle design problems. We’re learning alot in the process so we’re pretty excited about it.
Are your and Jim’s Lost Art Press books meant to be consumed in a particular order ?
The are all meant to stand alone. If I was just getting started, begin with “By Hand & Eye”. If you tend to learn more through your hands, “Truth To Tools”.
Anonymous was me George. Guess I have to enter me name on these replies.
I just sent an invite to your email – I think, if you accept, you’re added as an author here and that should solve having to enter your name each time. I think.
Awesome to have George here, I have really enjoyed By Hound and Eye!
My question is on stick chairs though, any thoughts on finish, design details or wood selection for a stick chair that will live outside on a deck (no cover).
Stick chairs are a bit out of my wheelhouse. I’ve always had a soft spot for rustic weather beaten pieces in an outdoor setting.
I am not an experienced stick chair maker but if you can get hold of and use locust (even though it is very dense it is workable with hand tools), mulberry or white oak (large growth rings), you could proceed without worrying about finish I think. I may be wrong but I understand these types of wood among others to be rot and weather resistant. Also those three species are very strong.
If you can get hold of some locust, mulberry, or white oak (large growth rings, that is one I learned the hard way) you could proceed without worrying about finish I think. Those species among others are very strong and also weather resistant. Locust and mulberry would be my first choices for outdoor furniture partly just because I can get it quite easily. Cypress would be cool too.
George,
I saw a recent post by Jim about the proportions of a six-panel door. If I’m trying to fit a given door opening, what is the order of steps to get the dimensions of the components I need to build?
Will there be more layout tool videos? I only see the first from 2018.
Do you//Jim have any in-person/virtual classes coming up somewhere?
Thanks, Steve
We are unpacking some historic doors as part of the next book. If you can’t wait for the book to come out, look at some examples you like. Explore with dividers the proportions. Rails will relate to the height and stiles will relate to the overall width.
We pulled together the layout tools video and midway it deserved to be a book. “Euclid’s Door”.
We have no classes scheduled right now.
Also explore the design by drawing diagonal lines from various primary points such as outside and inside corners of the framework…you’ll likely discovery intersections that locate other elements and also reveal symmetry.
Shout out to George Walker regarding your book. Thanks so much for writing “Euclid’s Door” I have read it twice and so far have built the three straight edges, 18″ & 12″ Squares and the 5″ wide Layout Marking Square. I learned a whole bunch about making precision instruments. Patience whilst planing, rinse and repeat. Please keep writing these fine books.
Anyone new to hand tool woodworking should buy this book and build these tools
Hi George! Thoroughly enjoyed the books and I’m thrilled you and Jim are working on another.
Is there any idea or concept that you’d hoped would resonate with readers more than others? Any thing that you’ve learned or that surprised you from the response to your books?
Would like woodworkers to understand that design principles from the past are timeless. They can be used to create fresh exciting work in a contemporary setting.
One surprise response has been the breadth of different crafts that have responded to our books. We’ve heard from blacksmiths, knife makers, folks in the building trades, as well as a few architects. Oh, and more than a few geometry teachers.
“Oh, and more than a few geometry teachers.”
I’m really glad to hear this. I have to admit that when I finished By Hand & Eye followed up with By Hound & Eye that my first reaction was that I had been cheated by my high school geometry teacher. 🙂
I wish geometry was taught as a discovery process, not a memorize-formulas process. Teach to the child, not to the test is not just a platitude to me.
There are programs like that. I taught a combination geometry with construction course. The downside is these programs are expensive to start and operate.
What level of accuracy do you aim for when 1) making measuring tools 2) making joinery?
Using just hand tools and geometry, you can make a square or straightedge to machinist level accuracy. Not really necessary but I had to satisfy my curiosity. Concerning joinery, I don’t really think of accuracy as much as fit. If a joint is supposed to be invisible, I don’t want to see it. If a tight joint is called for, I shoot for as tight as I can without damaging the wood.
When making layout tools, you can achieve machinist level accuracy just using hand tools and geometry. Though that’s beyond what’s needed for most woodworking it is possible. For my own curiosity I measured tools I made using micrometers and could get tools within a half thousands of an inch to dead parallel or square. This is not necessary but it is possible.
When fitting joinery, I go by feel more than any measured tolerances.
Just wanted to say Thanks your books changed the way I design. Can’t wait for the next one m.
Thanks Chris. Each book for us has been fun exploration. This next one is already opening up discoveries for us.
Hi George,
I’m really glad you’re doing this. Thank you for taking the time.
I made a dresser from plans a few years ago. We really like it except the size of the drawers. How would I go about “sizing up” the rest of the piece to accommodate larger drawers without ruining the beautiful proportions? The overall depth and width would not have to be limited, but I would think the height would have to remain an “normal” dresser height and that’s where I’m really stumped.
Thanks again!
Am assuming you want to reconfigure the drawers in an existing case? If it has five drawers, you could reconfigure it to a four or three drawer arrangement.
Hi George! I’ve read By Hand and Eye and Euclid’s Door, but I’m not able to really apply the principles in my work. I have trouble visualizing designs in general, so this may be a part of that. Do you have any advice about how to actually learn to pick pleasing whole numbers ratios in projects where the design is not significantly derived from any existing pieces? Or in other words, how to make the leap from consuming to producing, preferably without a string of abject failures on the way?
It helps to look closer at work that you admire. Step back and try to visualize those pieces as just simple shapes. Then go a step deeper and look at how parts (shapes) within a design relate to each other. That relating or connection is what we call proportions. Some you can unpack with dividers. Over time you can gain a feel for when the parts are all playing nice together.
I start by sketching numerous concepts, just eyeballing proportions…then refine to simple whole number (ie. steps) relationships.
Good morning George (and Jim)! When I read the explained examples from Hound and Eye, the proportion rules make sense. However, when left to my own device, I find it hard to decide which elements to include in the global proportions, vs which are part of the ‘punctuation’ or otherwise; as in if you include the foundation of a building the ratio could be 4:5 but if you exclude it it will be 3:5, if you include the chimneys it becomes 3.5:5, on and on…
Apart from deep historical knowledge (furniture / architecture from this or that period and place would almost never use “that” ratio, so it must be “this” ratio), do you have a quick advice to figure out the right ratios? Thanks in advance!
Think of proportions like salt and pepper or spices. There are no right or preferred proportions. In our books we spell out some general rules of thumb. Ultimately, your eye will tell you if it needs a bit more salt.
Dido to brousseaucharles post. How does one discover sub-dividing the field. When I look at some of the drawings that include the “proportion ruler” in them; they confuse me, take for example drawing 2.4.5-D. This drawing is downloaded from the https://www.byhandandeye.com/; store. Any one “ruler” makes sense; but soon I get lost in relating one “ruler” to another. In other words I get the whole picture and the pieces of the puzzle soon get me lost. I picked that one drawing as an example because you would be familiar with it. But looking at examples from the historic sources is what I am referencing to. I hope you can see the details from the drawing that is being referenced by my comment.
P.S. I have hung the quote of Gustav Mahler in my office as sign to others. 🙂
These proportional rulers you reference help to see how the parts relate to each other. They are typically arranged to show the big overall proportions and then smaller rulers cascade down to unveil the details. Try drawing the example you cited, starting with drawing from the big proportions on down to the smaller. Drawing always helps me unscramble my thoughts.
Good morning George. I am a retired grandfather of three grandchildren (16, 14, 12). They no longer have “shop” class in school. They have each made a bird house, tool box (which I have filled with hand tools), the stool from “Good Clean Fun,” and now we are working on a simple automaton (for this project, they each drew their own simple blue print). I will have them one day a week this summer for “shop class,” These are kids… how would you balance “class time” with “shop time.” I have all of your books, and love them. Is there any additional curriculum you would recommend for this situation. Thank you!
You could take some of the lessons from artisan geometry to lay out the boundary lines for a basketball court (or half court). Anything fun they like to do outside, there is a geometry connection. Also, pick up an old Boy Scout Handbook from the 1950’s. Lot’s of info about building rope bridges etc.
We homeschooled our boys and I taught each of them a shop class. Try the woodworking books of Aldren A. Watson.
The books by Eric Sloane were highly inspirational to me as s young craftsman
Any recommendations for books about the proportions/design of medieval architecture? I feel like arched tracery windows have a lot of stuff to them that you guys talk about in your books.
Here’s a resource on Jim and I have been digging into recently. https://historicbuildinggeometry.uk/shelter/
Following the recommendation of a previous post, this was discovered. I hope it helps.
https://historicbuildinggeometry.uk/downloads/
https://historicbuildinggeometry.uk/article/winchester-palace-rose-window-geometry/
I would recommend this site.
I use a spar gauge for making …spars. It seems that a spar gauge would be excellent for any round or 8 sided length of wood. It needs no ruler and follows any sort of taper. Do you know of any one who uses it for furniture?
I have not used a spar gauge. Perhaps Jim can chime in on this later today?
I believe the spar gauge is seen in the Woodwright’s Shop: Roy called it his “octagonater”. Chris was on that show…
I’ve used my spar gauge to lay out chamfers on tapered table legs. The gauge itself is a great learning tool for understanding the geometry of how similar triangles maintain proportional relationships.
Any advice on how to balance tradeoffs between sticking to whole number ratios versus needing drawers or cupboards to be a certain size ?
I use whole number ratios to rough in a design. Often it’s dead on perfect. But I’m not married to them. If you need to bump them to please your eye or function, feel free. Your in good company with some of the great historical builders.
thanks
George!
Thanks for doing this! You’re books have really been a frame-shift for me in terms of my thinking on furniture design and woodworking writ large.
I have tried to find online any information on how to layout the “other lines” on a sector (such as line of tangents), have you written something that I’ve missed or know of any resources if I want to take a deep dive into the dark arts of sector layout and use?
Thanks!
A treatise of Mathematical Instruments by John Robertson
https://www.amazon.com/Treatise-Mathematical-Instruments-John-Robertson/dp/1931468117
This 18th century book explains all the lines on a sector as well as filled with examples of common problems it could help solve. i.e. What is the weight of a 13 inch iron bomb shell, the metal being two inches thick on mean?
making 3 legged chair – the scoop is shown front to back but not side to side. Is what is shown the same left to right (one big valley) or is the scoop ala windsor (kind of a dip in the center only)? thanks!
Given that your drawing isn’t clear, I’d start with a limited scoop in the center and see how it sits. You can always expand it but you can’t put it back.
As a musician I am intrigued by the shape of the G clef, C clef and F clefs. Do they have any basis in your whole number ratios?
Great question. I’ve wondered the same thing but haven’t dove into it to find out. If you decide to decipher it let Jim and I know what you find.
Google how the draw a g clef, the parts are based on certain things are on certain lines which are equal distances apart. Sorry on the phone with comments closing soon I can’t gi a url.
Hi George, this is a bit mundane given I’m building a deck foundation on a 20% slope. It’s been great fun using some of the oldest artisan tools for the layout: plumb-bob & level. I calculated the slope by dividing the run/rise (20%). My question is – do you know of a formula to determine how much deeper than normal (below frost line) i need to place my piers (sonotubes), given this slope?
You got me on this one. Think I’d reach out to a local builder who could advise you on this.
Take a look at this link – https://www.decks.com/how-to/articles/deck-footing-frost-depth-map. Helped with several decks in northern Illinois, mostly south suburbs of Chicago and we usually had footings 4 feet deep. In one where the soil was sandier than usual we went another foot deep and that deck is now 35 years old and solid as when first built. There’s this one too – https://www.familyhandyman.com/project/how-to-build-a-solid-frostproof-deck-footing/ Hope this helps. All the best.
Many thanks – those links were very helpful!
Recently had a screen room built in northern Chicago suburbs – very sandy soil, but flat, not sloped. “Code” (for what that’s worth) is 4 FT. deep for sonotube footings. See what your municipality uses as a building code reference and start there. They are pretty conservative so you should be safe following that guideline.
I’ll cast my deep appreciation and gratitude onto the pile too (thank you)! BHBE has been paradigm shifting in the best way.
You write about the classical orders as foundational training for generations of past artisans. Do you have recommended resources for how to learn/practice this skill today?
Drawing the classic orders is a time honored approach to help you gain a feel for proportions. Most of the 18th century books on building and furniture have plates dedicated to that end. Here’s an online resource that was a pocket guide for artisans.
https://archive.org/details/buildersdirector00lang/page/20/mode/thumb
It contains images of the orders as well as examples about how they were incorporated into fireplace surrounds, doorways, etc.
Pick out an order and draw it with just a straightedge and compass.
I show students how to sketch proportions of their project (i.e. dovetailed box) using isometric view. Some take to it more quickly. Do you have a recommendation for a progression through elevations (primary views) or visualization examples to help those who struggle? Drawing is not an advertised goal of these adult classes at a city arts centre, but rough sketching ability is valuable IMHO. (Joel M./Tools for Working Wood generously provides graph paper PDFs but have not yet given that to students. Thoughts?)
Love From Truths to Tools and have given it to my favourite high school math teacher : – )
One strategy I’ve used for struggling students is to have them draw the elevations on card stock (or 100 lb. paper), then cut them out, tape corners together and observe how they fit together to create a 3D object. In truth, that describes my own approach for any form beyond a simple cuboid!
In addition to Jim’s suggestion, I’ve helped students with drawing by teaching them to use a pencil held at arms length, using their thumb to pick off measurements from an object and transfer them to a drawing. Get them familiar with it by drawing a front elevation of a chair or house or whatever. Then have them make another drawing, but move them to a spot where they are looking at the object with some perspective. Same drawing method, but grabbing the object from an angle. Usually gets some light bulbs to flash.
Hi George, thanks for doing this! I have “Euclid’s Door” and “By Hound and Eye”, and those are all about building the skills for designing pieces based on your taste and needs. Do you ever build projects to a detailed plan? If so, what pushes you one way or the other?
I’ve made a progression over time. I used to rely on plans, but as my design skills improved I found I could visualize better so drawings took a back seat. Now I may make up a drawing to help sell an idea to my wife Barb, but I can and do work without plans. That being said, if I wanted to tackle something with new technical challenges (stick chairs for example), I’d definitely use plans to walk through it.