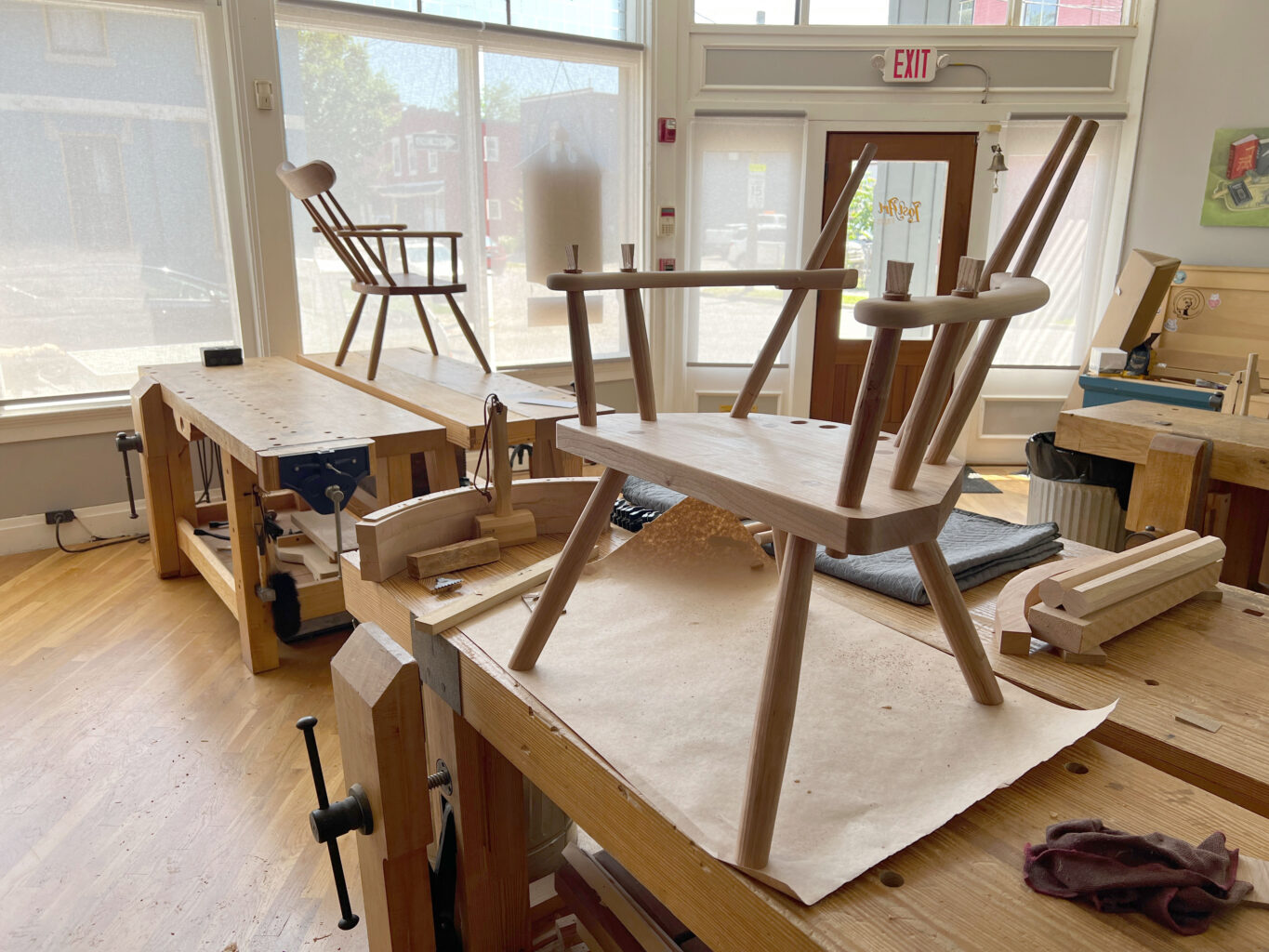
Hey wood nerds, it’s time for the LAP Open Wire, where we attempt to answer your questions about woodworking – plus our tools, books, apparel and Napoleonics.
Here’s how it works: Type your question in the comment field. I will do my best to answer it. It is that easy.
Before you ask a question, please read this.
- If you could limit the number of questions you ask to one or two, my fingers might not cramp up. And remember brevity is appreciated.
- If your question is your first comment here, it will automatically be flagged for moderation. Your question will appear after I approve it.
So here we go…. Note that comments for this entry will close about 5 p.m. Eastern.
Comments are closed. See you next week!
— Christopher Schwarz
Is lightness always a design virtue? For instance a stick chair is light, it looks light and it feels light. The design intention is to be light. Similarly campaign furniture is light for obvious reasons. However in the UK there are heavy furniture traditions that are heavy, look heavy and feel heavy. But they look great. Can heavy be a design virtue if it looks great? This is by way of asking if a dining table for 8, 40″ by 80″ and 3″ thick, with turned tapered legs (maybe from 3″ down to 2″) with 1 1/2″ tenons wedged directly into the top with no other supporting structure a) would work as a structure b) would fit into any historical precedent c) would look, in your opinion, inappropriately heavy? (Incidentally the dining context would be a largish dining room in an old house with a tall ceiling)
Lightness is not always a virtue. I love a chunky timber frame. And I love some chunky chairs.
(Warning, opinion ahead) Instead, lightness is something that furnituremakers embrace when they have run into a dead end on a design. They lighten all the components to push the idea forward. This works, to a point. But you eventually encounter the structural limits of the material. And then what?
I love brutalism and Prairie and Arts & Crafts – three styles that embrace the chonk (though they have their light moments).
Hello, My question is regarding your smoothing plane set up. I read a LAP article a while ago in which Chris made a comment on how highly tuned his Bronze No.3 smoothing plane is, so much so you no longer look at any others. My question is regarding that set up of and bevel angle on the Chipbreaker in particular – has this changed since the article in PW “Reconsidering Chipbreakers as Not Totally Evil” in 2012. Thank you.
My chipbreaker is ground at 25° and I have honed a slight curve on its edge. It sits about .005″ from the cutting edge when I am in some tricky wood. Open mouth. 45° frog.
Thank you. So you no longer hone a higher angle secondary bevel on the Chipbreaker?
No. I experimented with it. And it does increase performance, but at a cost – the tool is harder to push.
I work in domestic woods, so that sort of performance isn’t required. But if it ever is, I know how to get there.
If I might chime in, Kees van der Heiden and I wrote an article on chipbreakers for Pop Wood a while back. In my experience and messing around with chipbreakers, the secondary bevel helps with performance, but the angle of the secondary bevel is the least critical aspect of making the chipbreaker work well. The most important factors are making sure the chipbreaker mates well with the plane blade, and that it’s close enough to do its thing.
The secondary bevel also doesn’t have to be huge. 2-3 swipes of the edge of the chipbreaker on my highest grit waterstone is all I need to set that part up. I hold the chipbreaker at an angle such that the secondary bevel will be close to vertical once it’s on the blade and in the plane.
Last point — although a chipbreaker does work, it is my least favorite way of dealing with tearout. Resharpening the blade and taking a thinner shaving are easier things to do.
Thank you. So you no longer hone a higher angle secondary bevel on the Chipbreaker?
Which are the main types of rasps a woodworker should own, the ones that will get used the most? And who would you give the nod to, Liogier or Auriou?
Thank you again for contributing you Saturdays to Open Wire!
I use a half-round cabinet rasp (9 grain), a modeller’s rasp (13-15 grain) and a rattail rasp (coarse – I forget the grain). That is it.
I have Aurious and have never used the Liogiers. I’ve never done any comparisons of hand-cut rasps. I can say that hand-cut is the only way to go. The machine-cut rasps are only sad facsimilies.
For the new building you have mentioned the future plans for the first two floors. What about the third floor? Maybe a tool store like above Roy Underhills school?
Probably not a tool store. I have ideas for the third floor that I am sill developing. If I say what they are now, then I will have to answer 1,000 questions about something that is really still a shadowy notion. When the plans coalesce, we definitely will discuss them.
I take that to mean Megan will be opening a Cat Cafe on the 3rd floor!
Nope. Olivia plus my foster is quite enough at home, and Bean et al keep me happy at the shop 🙂
I am allergic to cats. So I am looking forward to having one place in my life where I can breathe somewhat regularly.
Cat allergists unite!
I am guessing that the planned activity for the 3rd floor will require you to learn to make oak barrels.
We’ll have a brewery/distillery across the street from the Anthe building soon, so we’ll leave that to the experts. It will be woodworking in the whole building. No AirBnB, speakeasy, cafe, abattoir, haberdashery or boulangerie.
Many readers expected us to open a brewery here when we bought the bar on Willard Street. Truth is, I stick to what I know: writing, design, woodworking, research, teaching. So whatever will be on the third floor will mix those things in some novel way. I am terrible (honestly terrible) at many other things. So I’ll stick to that.
The drinking table in the The Anarchist’s Design Book, Expanded Edition was my first attempt at staked furniture. It was great for a number of reasons not the least of which was the almost foolproof ‘banjo drill press jig’ that I credit with making the mortise drilling easy. Why don’t you use that for chair mortises? I see mirrors and lasers and Megan spotting when I think the jig would work wonderfully. What am I missing?
We use lasers (not mirrors) as a training tool for students and when writing for people who are beginning in chairmaking. When I work flat out, I do it without a spotter or sighting aids. And most vernacular chairmakers I know do as well.
The Banjo Jig is another training tool. It’s great for shallow resultants (such as the table). And for large-scale mortises.
It’s not so great much for the extreme resultants I use in some of my chairs.
Hi. In your Stick Chair book you say that you make octagonal legs that are 1 3/4″ in diameter. Is that 1 3/4″ point-to-point? Or is it from facet face-to-facet face?
Flat to flat.
Chris, why don’t you like hanging tool cabinets as much as tool chests? Because of their lack of mobility/portability? Thanks again for everything you do. Lost Art Press changes lives!
Isn’t there a historical precedent for hanging tools on the wall as well as any type of cabinet? To me it is handy to my bench and everything is in sight and easier to find. But I don’t travel to woodwork, everything I do is in my shop.
A cabinet (as with a chest or any other type of box) keeps dust, dirt, and moisture off of one’s things, and gives one the ability to lock them up. That’s why I prefer cabinets to open hanging (at least with some of my tools).
But in modern shops that are well insulated dirt and moisture shouldn’t be an issue. With dust 2 or 3 shots of compressed air blows it right off.
Yes, but I work in a cord-free shop, so brooms and brushes are the way I clean!
It can be a cultural thing. Woodworkers in some countries in the EU have a tradition of hanging tools on the walls. Other countries preferred chests.
For me, I like that a lot of the till space is undefined. So the chest changes easily with my needs. With a cabinet, the tools have defined places/spaces/hooks. My chest is constantly changing based on what I am working on that week.
Out of curiosity, then where do you put the tools specialized for, say, flat work, when you’re in chair making mode when you cycle the tills out? Hope that makes sense?
Layout tools and tools I need ASAP are in the top till. Chairmaking and nailing tools are in the second till. Larger hand tools in the third. Saws in the sawtill. Planes in the center well. Moulders at the back wall.
The Gibson Chair video is wonderful. I have started my chair. The video will not let me open the tool list or patterns anymore, because I have opened them 7 times. Is there a way for me to fix that? Thank you.
Done. You should be able to open them again…seven more times. Then let me know if you need it reset again (fitz@lostartpress.com)
Thanks! You are the best. I planned to work on my chair this weekend.
LAP if I download the video to a external storage will it still be limited to 7 times?
Nope; it’s yours for eternity.
LAmy LAP, if I download my LAP video to a external storage can I then open them more than 7 times?
Yes. There is no DRM that prohibits opening the files. Only downloading them from our servers (this is a theft-prevention measure).
Greg, the next time you open one of the files, save a copy to your computer (assuming you’re using a computer, not a phone). That way you don’t have to be online to view the files again later and won’t run into the download limit. Likewise, you can save the videos to your computer. If you click “vimeo” in the lower-right corner of the video, it will open on the Vimeo website. Below the video on the right, you’ll see a downward-pointing arrow. Click this and you’ll get a menu where you can select the video size to download. (Where I live, I have to download the video because my internet isn’t fast enough to stream it.) If you need help, click my name on this comment and it’ll bring you to a webpage with an email address at the bottom where you can reach me.
Thank you, Steve. You are a good guy.
You can also save it to an external cloud platform ( I use Dropbox) from your phone/tablet/computer then access it from anywhere. On an iPhone, i use the share button and send it to my Dropbox account that way.
I’ve been watching your Gibson chair videos and am wondering why you use a Veritas tenon cutter for the 1″ tenons, but a plug cutter for the 3/4″ tenons.
Those are the tools that I own (I don’t own a 3/4″ Veritas power tenon cutter – wish that I did). And it allows me to show two approaches.
Quick question on the sawbench project. The legs are glued to the the top base, then nailed. Isn’t this a cross-grain joint, so I’m wondering if glue is appropriate in this situation? (I bet the sawbench has been fine over time)
Love everything that you do – thanks so much!
Nails allow wood to move, in general. With small components such as this wood movement isn’t an issue. Strength is. So glue, nail, screw, peg or whatever to make sure the legs stay in place.
Is there a Caleb James book in the offering anytime soon?
Caleb is working on a book for us on Danish Modern. Don’t hold your breath. It is years out, but it will be worth it.
Chris and Megan, Not really a question, I just want to say thanks and encourage you both to keep up the great work.
Thanks for all you do! As a mostly self taught hand tool woodworker, the team making up LAP have been the closest thing I’ve had to teachers on the subject.
Your books, YouTube videos, and Blog have become an invaluable resource for learning from a far.
I grew up watching the Woodwright’s Shop Sunday mornings on PBS. LAP is doing a great job carrying on the tradition of keeping hand tool wood working knowledge relevant in a modern world.
I stopped by the LAP shop this week while driving through. I appreciate your hospitality and letting me poke around the shop and tool chests.
Keep up the great work!
Thanks Colin!
Aw – thanks!
How to sharpen a spokeshave?
Bevel down: Most blades fit into my honing guide. For those that don’t I have a couple little gizmos that help.
Bevel up: I clamp the blade/tangs in a handscrew to hold it still while I sharpen the bevel.
I have a large Red Oak that needs to be removed and I’m considering having it milled onsite. In the past few years, I have had a Pignut Hickory and a Black Walnut milled. (Many regrets about the Hickory) For a newish handtool woodworker, should I just consider the Red Oak firewood? (“large = 40” diameter at 5′ off of the ground)
Impossible to say without seeing the tree. It could be rotted inside. Twisted grain inside. Bugs. Metal. Knots from branches. Or (maybe, just perhaps) perfect for milling.
Peter Galbert’s book has a good section on choosing trees and transporting them to be milled. It’s definitely an adventure worth trying. But you have to be prepared for unbridled success or utter failure. Like anything in woodworking, it takes time to learn to read a tree’s exterior. And even when you are good at it, the trees are tricky.
If it looks like you’ll get straight grain when milled, go for it. It’s not as desirable as white oak, but a great wood to work with, and strong enough to make cabinetry and chairs.
I’ve been loving your American Peasant sub stack and thought I’d try carving spells. I’ve made a grooving knife and a grooving blade for a standard compass out of some scraps of O1 and I’m slowly working my way through some spell panels. It’s all going really well apart from I’m finding that the compass point digs in deeper with every concentric circle I carve and I’m left with a nice deep hole in the middle of the carving. Have you got any tips for grooving with a pari of compasses without making a big hole in the middle?
That’s awesome, thank you very much!
One one of your workbenches, I seem to remember you making a saw/chisel rack on the back of it to have a place to put those tools you are currently using. How did you make the rack and did you like it? I am considering one for the Nicholson bench my son and I built last year.
I have the rack on the back of my personal bench. It’s just little squares of 1/2″ thick wood plus a long strip of wood. Glued together to make the spaces. Then nailed to the bench. I use it hold my small clamps. Love it.
The 1/2 inch slot should hold back saws, chisels and most carving tools shouldn’t it?
Yup. That’s a good all-around opening for bench tools.
iirc Chris’ article (and this is what i did on my bench–works great) use a single long board at least 1″ wide thickness doesn’t matter. then make small spacers 1/2″ thick (you want only 1/2″ space between the board and bench). at least 2 spacers, 1 on each end between the long board and the bench. might want another spacer or 3 in the middle depending on how long your rack is to add support and create dividers. i glued the spacers in place then drove enough screws (or you can nail it) to hold it to the bench.
The Anthe Building is separated from the law firm building at the top. Can you elaborate?
Early on in the building’s history it pulled away from the adjacent building. Many buildings in this area have listed, and I am told it happened because of the change to the city’s water table when they built the levee.
In any case, we had a structural engineer look at it last week and he said it’s nothing to worry about.
Photoshop that gap. You’re going to get this question a billion times.
We’re at a million already, I think.
Morning! I know your suggested setup for bench tools is a 6” grinder and water stones. Do you have a suggested setup for sharpening and maintaining lathe tools?
I am not a professional turner. I grind my lathe tools freehand on the same grinder I use for my bench tools. And I hone them on my waterstones.
If you are going to get deep into turning, then there are lots of different options to consider for grinding and honing. And jigs for holding the tools. So yo better ask a real turner. Sorry.
Thank you!
Are the shapton stones able to sharpen HSS?
Sure. It just feels a little gummy on the stones. But I’ve sharpened HSS chisels on the Shaptons with no complaints.
180 grit cbn wheel.
Check out @richard_findley.
Has a very clear series on lathe tool sharpening
Found him. Think this is it? Very helpful. https://www.instagram.com/richard_findley/reels/
Thanks for the response above re the rasps. Quick follow up. Are the ones you use 9”? Thank you,
No clue. 9″ or 10″ is fine.
Chris,
I’ve got the Stick Chair book and read many blog entries on chairs. So, please point me somewhere else if you’ve written about this. I’ve tried to find it.
I have an inahave, German made, I think by Hirsch Werk….? That doesn’t matter. It’s good steel, but I bought the tool on ebay and it has never been sharpened. I can’t figure out how steep a bevel angle to put on it, because no matter how I hold it, it won’t scoop wood from a board flat on a bench. It’s sharp enough to cut from a piece held in a vise, but the geometry of something is off to make it work correctly. Maybe it’s the handle angle to the blade?
Is there a reference that might help me sort through this? I probably should have bought a nicer tool that came sharpened, but at the time that wasn’t feasible. This was $25 a few years ago and it’s in unused condition.
Before I give up, where should I read about something I could try?
Many thanks.
I have had a couple students bring these to classes. I believe the solution was to grind a much lower bevel on the outside (17° to 20°). That allowed the blade to access the wood.
If you have blacksmith tendencies, you could bend the handles upward with a the help of a torch. That also works.
I’ve read Sharpen This. Something I’m still struggling with is grinding a new edge that’s 90 degrees to a side. I’ve seen you mark the new edge with a sharpie and grinding down to it, but my edge still ends up rough and wonky. Is this something that just takes practice? Or should I forget about making it perfect and just adjust it flat once it’s in my hand plane?
Mine aren’t ground perfect, but they are close. That’s practice. What makes them perfect is the honing in side-clamping honing guide. That overrides the out-of-square grinding. It can look wonky, but who cares?
Good morning Chris. Greetings from the other side of the globe. A few moths ago I built a French style workbench from reclaimed timbers left over from other projects on our house.I call it my “ten quid bench” because the only timber I purchased specifically for this project was a 4 inch thick slab roughly 15 inches wide by just over five feet long. Th cost in local currency was the equivalent of ten pounds sterling or twelve US dollars. So far I have used it without a vice and am planning to fit a leg vice using a steel screw and a parallel guide. As the simplest and quic way. I am thinking of fitting the parallel guide above the rails rather than just above the floor as seems to be the norm on Rubuo style benches. I notice that on th Moravian workbench and some English style benches the vide chop comes to just above the rail. Do you see any disadvantage with this arrangement? On the plus side there is less far to bend and a lighter chop.As a final thought I wonder if the long chop is a hangover from early benches where the vice was kept parallel by wedging to the floor. I apologise if I have rambled on too long and really appreciate the time you spend on these questions.
I haven’t noticed and advantage or disadvantage to putting the guide at a high position or a low position. Having a long and heavy chop isn’t a big deal, and there are times I have furniture legs in it that reach almost down to the floor and are clamped there.
It comes down to what stock you have on hand and what you want the chop to look like. The only real variable is the chop’s thickness. A thick chop is better than a thin one, which bends and is weak as a result.
Still flabbergasted and delighted that you’re doing this publicly and regularly – it makes for great weekly reading.
A question about PPE and hand tools: which operations really require protective equipment (steady, now)? I have no power tool background, but assume gloves for finishing (brushing and wiping on fairly benign finishes), ear plugs for driving big nails in my metal-doored garage… Currently that’s it. Hand sawing and sanding with the door open seem ok. Are there times you reach for any other PPE when using hand tools?
I am a practical person. Most of my effort goes into avoiding the exposure. So when sanding I use the best dust extraction possible. When hand sanding I do a little work and then clean up with a vacuum.
Finishing: I avoid VOCs. When I do have to use them, I use a respirator and try to work outside.
Ear protection: I have earplugs in my apron. Every machine has good earmuffs by its switch. Hand tool work is not quiet. Chopping mortises will deafen you in short order.
Being a scientist by day, I like to measure things. Early on I bought one of those Dylos machines and measured several times various hand tool woodworking operations with the garage doors closed. For hand planeing, spoke shave, and chisel work, the air quality really didn’t degrate. For handsaw work with long rip cuts, there was some increase in the particulates but like from excellent to good air quality. For hand sanding, that is where the air quality plummeted (don’t recall the specific numbers). As such, I wear proper dust PPE when hand sanding and keep the garage and side doors open to get a cross breaze. Also, using a DeWalt 735 (straight knives) with a shop vac had air quality drop so used dust PPE. In the process of installing my bandsaw and proper dust collection system from Oneida; still plan to wear dust PPE when using either the bandsaw, planer, or even the table top mortiser (though I didn’t measure it). Hope this helps.
For people making stick chair parts from green wood, how dry would the parts have been before assembly? For example, the chair maker, Gareth Irwin, from the article on hexagonal legs… Would he air dry / kiln dry the legs before use?
Thank you
The legs have to be dry. The seat can be a little moist. Both “Chairmaker’s Notebook” and “Make a Chair From a Tree” detail the process of drying. It’s too much for a blog comment. Basically split them when wet. Keep them in a moist environment so they dry slowly (an occasionally opened garbage bag is a good choice). As they get near equilibrium MC, air dry them in the shop or in a homemade kiln (which can be a box with a lightbulb inside).
Thank you.
If you have measurements for a chair, how do you scale them down to work for a kid?
This comes up every week on the open wire.
I haven’t done it. But those who have recommend scaling all the parts to 2/3s of the original.
First off, thanks for everything LAP does. You all are such a huge inspiration.
I need an entry door for my house. Looking at new doors I can buy is like looking for tools at a dollar store. The stuff that’s out there is garbage. I’ve decided I need to build by own. I live in Tucson, AZ and live in an Adobe mid century modern ranch home. I’d like to make a door that looks right with the architecture and has some glass (either a single lite or multi-lite door).
Do you have any recommendations for resources on how best to build something like this in a home shop. I have a decent setup of hand tools plus a jointer and planer. No table or band saw unfortunately. I don’t necessarily need a step-by-step but something that gives me the basics of construction/ joinery methods, wood selection, etc. Will the LAP book Doormaking and Window-making be a good place to start?
Thanks!
Erik Curtis recently built a cool door for his new workshop. Might find some ideas here. https://www.instagram.com/encurtis/
Thanks, Jason. Sadly I’m not on Instagram so I can’t look at it.
I have a question that is only slightly off topic. I noticed in a video or photo somewhere that you had an arm strap below your right elbow; was this because of tennis elbow? If so, how did all of that work out for you? What worked and what didn’t? And was it from any particular woodworking procedure?
I’ve been dealing with tennis elbow (from fly fishing no less!) since a Thanksgiving trip to visit family in Florida. I’ve had a couple of visits with a physical therapist and basically was told to do a lot of stretching and strength exercises, which I’ve been okay about, but not great. Also, I started off with a fairly stretchy armband but moved on to a more rigid one, which I’ve found to be a lot better. That being said, I’m at the bench or on a construction site pretty much every day, so my arm gets a lot of work, but I don’t overdo it. And I’ve only messed around with my fly rod once in the last six months.
(The moral of the story: be a little more careful when you’re muscling a saltwater fly into the wind with an 8-weight rod four or five hours a day for a week. Listen to your damned body when it tells you to go a little easier!)
The soft strap and exercises helped only mildly. What helped more: Using my left hand for typical right-hand operations until the elbow had time to heal. For the last decade or more I’ve been training my left hand to do stuff so I can hammer and saw in awkward situations.
It has paid off in that I can also transfer wear and tear to BOTH joints. Anyway. Sorry about your injury and good luck.
Doormaking and Window-making is a good place to start. It’s about layout, design and proper joiner for entryway and passageway doors. There are lots of other resources out there, but they are out of our furniture-based myopia. Sorry. I’ve only made a half dozen in my life. So I am no expert.
Excellent. Thanks!
I don’t remember anything about wood selection in it, but otherwise I think it would suit your needs! I think Brent Hull on YouTube had some good info on wood selection for doors in hot/dry environments, might be worth checking out!
If you are looking for diagrams with typical dimensions on doors, the best book I have found so far (that doesn’t go into the how to specifics) is Robert Lan’s Shop Drawings for Craftsman Interiors. There is whole chapter on doors and windows (mid 60s page numbers). It is a bit light on the how to part but has lots of images. This is the book I will be using when I make my front door.
These are all great resources. Thanks everyone!
My question is in regards to gluing and “clamping” the arms to the middle arm for your stick chairs. In the past, I saw that you used pinch dogs to draw and hold the two arm-pieces together after gluing. In the Stick Chair Book and video you advocate using pocket holes and screws for this purpose. I have noticed you prefer the “simple” over the “more complex” in your woodworking and also avoid jigs whenever possible, unless there is good reason to do otherwise. The pocket hole jig seems to be the more complex method and requires a jig. The pinch dogs are simple and take up no space. I am wondering if you found that there is a distinct advantage to using the pocket hole jig over the pinch dogs for this purpose and what that advantage is?
We have a pocket hole jig, which was a free cast-off from someone else’s shop. It’s more reliable than the pinch dogs, which can slip. But if I didn’t have the pocket hole jig, I’d use pinch dogs or a dowel or whatever. Hell, I’ve used a domino. I’ve used a loose tongue-in groove. There are 100 good ways to do it.
Hello there! I’m working on an Workbench currently and just done with cutting the mortises for the legs and did a testfit. Now the legs are 2mm too wide and stick out from the benchtop. What you recommend to do? Plane the entire legs and stretchers down to get them flush?
Greetings from Switzerland
Michael
I would plane them down – 2mm is just a few minutes of work. Will it improve the function of the bench? Not really. Will it look intentional and orderly? Yes.
Thanks a lot!
Many thanks for your extraordinary generosity running Open Wire. This is a (re)finishing question. One end of a cherry dining table exposed to sun has lightened considerably over the years. I want to apply a non-film finish before turning end for end to hopefully even out the color. We took it unfinished, so it also has food oil and liquids spots in places that could use moderating if possible. Thoughts/recommendations on prepping the surface and suitable finish? I used Soft Wax 2.0 on a project recently and was mighty impressed, but I think this could use a bit more heft, accepting that any non-film isn’t impervious. LAP has transformed my thoughts on woodworking!
I would clean the table with odorless mineral spirits to remove any oil/grease from food and to clean up the surface in general.
For a tabletop, you can use something similar to soft wax but instead of using 100 percent beeswax substitute something like 60/40 beeswax and carnauba wax. That will add protection (it also will make the wax more difficult to buff).
The best solution is patience and persistence. As you reapply the oil, coat after coat, it will eventually polymerize into a finish that is durable and beautiful – this is how gunstocks are finished.
Thank you so much for taking the time to do this, Chris–it’s quite comforting reading the various questions and affirmations that come up in this venue!
Your Stick Chair book has inspired me to make five chairs in the past four months, and I can’t seem to stop myself (so..thanks?) 🙂
In all your years of making chairs, what’s one of the greatest “successes” you can remember within the process? And, conversely, do you remember a great “failure” as well (a la Mel Gibson in The Patriot, perhaps)?
The success part is that I still have hundreds of chairs in my head that I want to build. Running out of ideas or inspiration is my greatest fear.
The fail was a three-legged backstool. The glue failed for the back leg, tumbling the sitter to the floor. He was unhurt, but it made me re-evaluate my glue choices and made me as paranoid as ever about the structure of my chairs.
I am always impressed at your productivity. In the middle of a project I sometimes experience the equivalent of writers block and get stuck and sometimes for a protracted period. Unsureness, fear of screwing up and wasting materials and time or whatever. I am sure everyone experiences this at one time or another. How do you approach getting unstuck and back to work?
It happens. I usually have two projects going at once. When I get stuck, I move to the other and let my brain sort through the problem on the other one. This almost always works. Getting some distance from your work brings perspective.
Restoring some old antique boxwood rules here. Best solvent to remove black india ink stains — and what should be my expectation? Can I totally get the black out without ruining the rule?
I don’t know. I use oxalic acid (wood bleach) to restore rules. But I have no idea what that would do to india ink. Sorry.
India ink is the black stains on old rules. I think you’ve done this in the past — did the black spots go away?
Hi Chris,
I’m 54 and planning to “retire” in 5 to 10 years. I’ve been woodworking for 7 years. When I retire, I want to go to a 1 to 2 year woodworking school. I’ve been considering North Bennett, Krenov School, and Center for Furniture Craftmanship in Main. Are there other schools I should put on the short list? Where would you go? The cost and moving temporarily to any area isn’t an issue and would be fun. Plan to visit and take a class at all those on the short list before deciding. Thanks Chris.
Sincerely,
Joe
PS Retirement will consist of volunteer work where I live (and currently volunteer), teaching college chemistry (which I already do), and woodworking.
Congrats. Sounds like a great plan. My 2 cents on schools: NBSS offers a traditional education. If you want to make traditional pieces, you cannot find a better school. The Krenov School and CFC emphasize personal/design exploration outside of the tradition. There are traditional roots in their work, but they aren’t as deep or strong as at NBSS. All three offer an incredible high-level of education. I’d start by looking at the work produced by the students and instructors and ask: Is this what I want to make?
On the personal side, none of these schools offer what I was after when I was 30. I wanted a chairmaking apprenticeship. And so I had to piece that together with week-long classes, endless reading, endless failure and (eventually) mild success. What I really wanted to do was what Chris Williams did. He wormed his way into John Brown’s life and became his student and grasshopper.
Thanks Chris. Helpful. I do like traditional pieces. It is a good problem to have.
Hoping also to eventually teach a woodworking class at school I teach college chem. They have “physical ed” classes such as tai kwon do, ball room dancing, rock climbing. They fill up those classes. I don’t think it would be a hard stretch for them to offer a woodworking class if I were to teach it as long as students enroll. Would be interesting what items the bookstore would sell for that class compared to the others.
Thank you all for being consistently delightful.
I’m looking for a band saw but don’t have one (or access to one) yet. I’m considering attempting the oven steam bend. But assuming I want to cut one, do you have suggestions for cutting backrests or crests without one? I’ve thought of using a jigsaw or coping saw with relief cuts. Thanks!
I’d use a hatchet and drawknife.
Jennie’s Hacking Knife – could you please let me knof the primary angle of the blade? also, if you don’t mind could you update the page with that information? Thank you!
I don’t know the included angle, but you can calculate it. The cross-section of the blade is 3/8″ wide at the base. And the height is 2-3/8″.
The blade is 4-3/8″ long.
Reload here — did the oxalic acid remove the black stains on the boxwood? Or not?
That was 14 years ago, so I don’t know. Here is the link to the post. You’ll have to register with PW.
https://www.popularwoodworking.com/techniques/restore-a-folding-rule/
Or visit the Wayback machine at archive.org to view it.
Thanks, Chris. You’re demonstrating you’ve forgotten more about woodworking and old tools than I know! 😉
Will your Sharpening Book additions also include sharpening turning tools; and how do you sharpen your Bedan that I saw you use on your chair legs in a recent video?
There won’t be any additions to the book, only the videos.
I am not a professional turner, so my sharpening is quick and dirty for lathe tools. Earlier in today’s Open Wire there is reference to a skilled turner who has good info on sharpening turning tools. I’m not your guy. I sharpen the parting tool on the grinder and then finish with my waterstones – 1,000 and 4,000 grit. Like a chisel.
Hello,
I am just starting to build the Anarchist Workbench. My question is about the orientation of the wood for the bench top as far as the end grain. You covered this for the legs, should I do the same for the top or does the end grain need to oppose each other. Sorry for the terminology I am a Newb.
Thanks, Josh
Hi Josh,
I meant to orient the boards in the top the same way I did the legs. But I got turned around at one point and mucked it all up. So if you can orient them sympathetically, it’s best.
Hi. I am going to Denmark for two weeks with a short side trip to Oslo. Can you recommend any shops to visit/tour, museums that you have found interesting that may be off the beaten path, tool or tool makers (carving/axe/knives) that you would buy if you were in the area? Thanks,
Steve
I’ve never been to either place I’m afraid. So I’m clueless. Perhaps a reader here has some recommendations. Or you might reach out to our dealer in sweden for some thoughts. Sorry!
Not specifically woodworking (I’m a ship and boat nut), but when I had a half-day layover in Oslo I made a pilgrimage to the Viking Ship Museum. And a short walk away were the Fram and Kon-Tiki museums. I did not have time to visit the Norwegian Maritime Museum which is in the same complex, but those three museums made for a wonderful visit.
Designmuseum Danmark might be of interest. A whole museum dedicated to Danish design with a focus on furniture.
Not a question, but a followup from last week. I was having trouble with my 3/4″ Gramercy Tools holdfasts in my 3-5/8″ thick laminated pine workbench top. Myron, Dawson Moore, and Anonymous suggested that that was too thick for the Gramercy holdfasts. Later, Joel Moskowitz quickly and kindly replied to my email and also suggested counterboring from the underside to reduce the effective benchtop thickness. Instead of trying to jig up a way to bore without a center, I tested my 12-deg taper reamer in some scrap. I reamed a depth of about 1″, which increased the diameter on the under surface to about 15/16″. After I demonstrated to myself enough times that it worked in scrap, I held my breath and reamed the holes in the underside of my benchtop. Now, every single hole, in every orientation, from thick to thin, grips the holdfasts tenaciously with a mere tap, including the ones in the vertical legs. Thanks, LAP, for hosting this discussion that helped solve my issue.
Have you ever worked with Kentucky Coffee bean wood?
Do you have any opinions or advice on working with it ?
I have not, I’m afraid. We have several of the trees here in Covington. But I’ve not encountered the wood on the bench.
Question on grain orientation for wedges. I’ve started making mine the way Rudy showed in the July 2021 post. I’ve found that if the grain is oriented quartersawn if such a term can apply to something as small as a wedge, the chisel is easier to push. Any loss of strength in the wedge or do you have any preference regarding aesthetics or otherwise?
Thanks as always!
I cannot fathom why the wedge would be any weaker. Radial grain is easier to work than tangential grain. So you are merely exploiting the wood’s structural characteristics….
I’m working on a set of Staked Chairs a la Chapter 7 of The Anarchist’s Design Book (Shouldn’t it be Anarchists’ since it is for all anarchists? Or does collectivism in any form rub the anarchist the wrong way?) If I wanted to make a couple chairs with arms to round out the set, is there one of your published designs that would go with it well?
You’ll need to widen the seat to add arms. Look to Irish chairs for how to add the arms to the back sticks and a couple front sticks. But definitely widen the seat to at least 18″, otherwise sitters will get stuck (I made this mistake).
I should be able to figure this out on my own, but I don’t trust my reasoning. In the video and plans you said the angle of the seat back of the Gibson Chair is 25º. Is that from the seat or from the floor? I suppose really I mean it is off from the normal to the seat or the floor?
Off the seat.
Removing a soap finish? I made a welsh chair 5 years ago and used a soap finish (your recipe). After a few refreshes I’m of the mind that I’d be happier if it stripped it off completely and went a different route. It has looked nice in the past but now it’s just seven different kinds of dull/bland.
Warm water rinse and repeat? Something else? Most importantly knowing that I got it all will be tough… I think. I want to go with a 1:1:1 wiping varnish. Is this a fools errand?
Try vinegar and baking soda. That will do an effective job of removing multiple coats. Look for recipes on removing soap scum on the internet. That will give you the ratios.
I bought some new production cut 4d box nails. The whole box appears to be slightly “corkscrewed” down the length of the nail, so the in order toget the heads parallel to the grain I have to start them about 20-30 degrees counterclockwise, and they twist themselves parallel as I drive them.
Y’all have used a lot of cut nails; is this normal, or did I get a bad batch?
I’ve never seen that. Might want to send a note to the manufacturer.
How strange that you mention this. I have the same problem with a batch of 4d “fine finish” nails. But it’s only some of the nails from the batch, not consistently all of them. Mine aren’t twisting out past maybe 20 degrees or so, and my solution has just been to ignore it. I’m only using them on the back of pieces or on painted stuff.
I’m making the first cabinet from the American Peasant blog (with the sawtooth top) and am about to hang the doors. I made it to about 3/4 scale because I have a specific place for it that will not support the full size cabinet per your drawings. The problem I’m running into is installing hinges. I’m using what I have, which are reclaimed brass butt hinges that are 2″ tall. The dimensions are spot on for the Horton Brass PB-407 but the leaves on my reclaimed hinges look a little thicker than the image on Horton’s website. My conundrum is that the hinges are chunky compared to the dimensions of the cabinet and I’m looking for the best way to install them to hide the chonk. I.e. I need spanx for hinges. Should I let them into the cabinet only and mount them onto to the doors? Let them into the doors only and mount them onto the case? Or split the difference and let them into both the case and the door evenly leaving the barrel to interrupt the seam? Or am I being completely obtuse in trying to save a buck and I should just buy the correct hinges? It’s unfortunate that hardware is so cost prohibitive these days. I bought these hinges for $3.50 a piece from a junk store and the equivalent quality hinge newly manufactured (in the more appropriate size) is nearly five times that price. Since I made the entire cabinet from scraps and leftover hardware from other projects it seems to go against the peasant ethos to veer off course now.
(this is no means a rant against Horton Brass’s pricing. I know their quality is top notch and the cost of production is higher than ever before. It just makes it tough for the peasants these days.)
Two things:
Those are the competing choices. While I am interested in No. 1, I never forget No. 2. Hardware doesn’t go bad or expire like meat. So it’s not like you are throwing away money if you switch gears.
That doesn’t mean you have to spend a lot of money. I buy a lot of used hardware off eBay. It can be very reasonably priced. Sometime New Old Stock.
Sorry- One more part to the question. Internet says equal parts vinegar and baking soda to remove soap scum (never really thought of my soap finish as soap scum -ouch). Then flood with water. The chair is 5 years old. Hide glue on all joints. All joints solid and tight. Am I worried about the final water rinse effecting the joinery? or just proceed with abandon. BTW- everything I know about chair making I learned from you so thank you.
I wouldn’t worry about the joinery as long as you didn’t inject the solution into the joints. But if they come apart, they are easily repaired with more hide glue.
You can’t lose.
Hey, Chris. I’ve tried to sift thru the blog posts since you first started posting your spell patterns, so if I missed an obvious answer, I apologize (I did try), but my question is, other than a fascinating use of fun tools, what is their point? Making works more decorative? It definitely does that very nicely. But you don’t seem the “needlessly foofoo” sort, so is this something you’d have found on the furniture of the working class sorts, back before mass produced stuff and the general conformity that comes with factory work, so this is another way to make your works more (I kinda hate the pretentiousness of this word) “Authentic”? Thanks, and I hope you and yours have a great weekend!
Screw the word “authentic.” Always and forever.
The apotropaic marks (spells) are integral to the purpose of the piece. They offer protection and good fortune to the owner. While you might not believe in their power, the communication from the woodworker to the user is undeniable and as important as the piece’s form and surface finish.
Most surface decoration in furniture was used to exhibit wealth. (Oh look at all the endangered animals I paid to have killed and have their little bits arranged in a marquetry portrait of a banana!) This is different. These symbols are used by people who didn’t have time or money to f-around with self-indulgent gestures. These symbols worked for a living.
And yes, they look nice, too.
Hi Chris, many moons ago during your PW times you did a review on an Earle sprayer, do you still use it, I remember your review was quite good.
I had an Earlex for many years and I still recommend it. The perfect setup for the home woodworker or small pro shop. And well made. Mine finally started to show its age and I upgraded to another HVLP system. It’s better, but not worlds better.
Hello!
I’m building a rectangular stool with four legs as a first staked-furniture project. Do you have advice for how far back to set the leg mortises back from the corners? I’m not following a plan, but I have looked at some and it seems they tend to be 2-3″ from the edge. In general, is this something you’d decide by building a model?
I feel very lucky to be able to ask you random questions like this. Thanks for your time!
(If it matters, the stool top is ~23″x19″ and 1.25″ thick. That’s large, but I want to be able to sit cross-legged on it in my lawn. The legs are octagons 1.25″ wide, and I’m thinking a resultant angle of 12-14 deg. It’s made out of some straight-grained Douglas fir I got from a friend.)
About 2″ to 3″ in from the edge is great. When I make little stools, I use a resultant that’s about 20°. But that’s personal taste…. Good luck!
Got it, thanks!
Have you read either of Peter Korn’s books, “Why We Make Things and Why It Matters” or his book on woodworking?
I read “the Woodworker’s Guide to Hand Tools” a million years ago and liked it. Peter is a talented woodworker, writer and thinker.
After reading about five of the “why we make books,” I developed an allergy to them. So I haven’t read it. Perhaps it is genius, but I would rather bang out some dovetails than ponder why. Apologies. Many people love this sub-genre.
Hi, I recently read Jim Toplin’s Measure Twice, Cut Once and found the various methods of measuring and marking very helpful. It looks like Euclids Door is very similar in content. Do I have that right? Thanks.
Euclid’s Door is an introduction to artisan geometry through the building of some very useful and important workshop toosl and appliances. I suspect you will enjoy it. I sure did.
Are you at all familiar with a tool supplier or maker H.A. Langhorst of Cincinnati Ohio?
Sorry.
I tried to copy a photo of a pair of tongue in groove planes, but it wouldn’t take.
I’ve heard of them, but I don’t think I’ve ever seen any of their tools. In the early 19th century, the city was awash in edge tool makers.
I read Sharpen This. Hayward recommends a primary bevel at 25 degrees, then establishing a secondary ” [by] lifting the hands a trifle” (think I got the quote…). Why do you recommend grinding a hollow primary bevel if you’re using a honing guide? It seems to me Hayward’s reasons would be 1. it makes it easier to feel for the angle when free hand sharpening 2. conserves wear on the stone as less steel is coming into contact due to the hollow. You say ” The most common operation on a grinder is to grind the primary bevel to reduce the size of a secondary bevel that has grown so large that honing and polishing have become a time-consuming chore.” This doesn’t make sense to me. With a honing guide, you’re keeping the blade at a consistent angle, therefore the amount of time on the stone will not change at all. The amount of strokes is exactly the same because even though the secondary bevel has increased in side, its all mating on the stone simultaneously and your only concern removing the front edge.
Hollow grinding is the cheapest and easy way to grind any blade. All the flat-grinding machines are expensive. So that’s why I recommend hollow grinding.
A hollow grind can guide you with freehand sharpening, but you don’t lift the handle. You keep the bevel flat on the stone. Downside: you are sharpening steel that doesn’t cut wood at the back of the bevel.
On your statement: “With a honing guide, you’re keeping the blade at a consistent angle, therefore the amount of time on the stone will not change at all. The amount of strokes is exactly the same because even though the secondary bevel has increased in side, its all mating on the stone simultaneously and your only concern removing the front edge.”
Nope. Proper abrasion takes longer when you increase the surface area that you need to abrade/polish. Once the bevel becomes wider than 1/4″, the polishing especially takes several minutes. Whereas with a tiny secondary bevel, polishing can take only four or five strokes.
Hi Chris , For the Worktable from the Anarchists Design Book two questions
1 ) Is there any practical way to make the 2 inch diameter mortice with hand tools or is it just time to buy a drill press ?
2 ) Is there any value in adding side and back stretchers ? Or is this just overkill ?
thx
You don’t need stretchers unless you plan to do a table dance on it.
You can indeed make the mortise with hand tools. You’ll need to find an old T-auger. Or a T-auger handle with a 2″ auger bit. They are not terribly expensive. And then sharpen it (usually not difficult). It is work….
Other option: chop out a square mortise. No reason it has to be round.