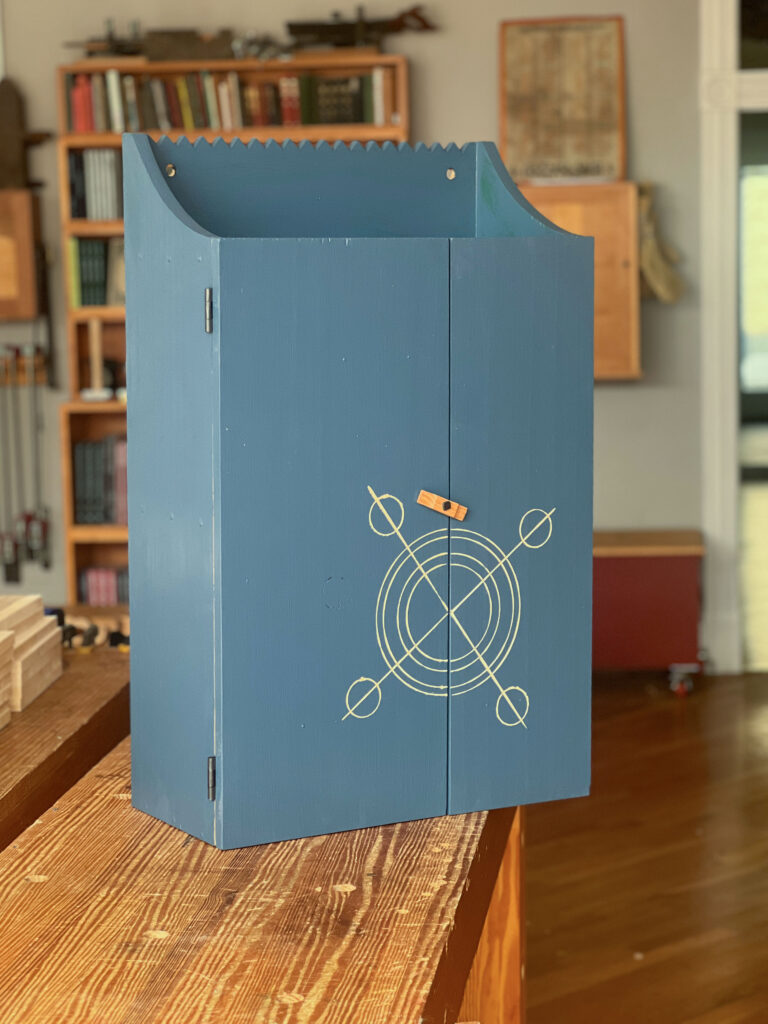
It’s time for the LAP Open Wire, where we endeavor to answer your questions about woodworking – plus our tools, books and apparel.
Here’s how it works: Type your question in the comment field. I will do my best to answer it. It is that easy.
Before you ask a question, please read this.
- If you could limit the number of questions you ask to one or two, that would be great. And remember brevity is appreciated.
- If your question is your first comment here, it will automatically be flagged for moderation. Your question will appear after I approve it.
So here we go…. Note that comments for this entry will close about 5 p.m. Eastern.
Note: Comments are closed. See you next week!
— Christopher Schwarz
As you have honed your skills in carving spells with the various tools you’ve shown, have you gone back and tried again with pine. In the early going, you said you couldn’t avoid the tearout with pine and switched to poplar, but maybe you’ve developed methods for pine?
Yup. As always, I was the problem. Not the wood. This cabinet is pine.
I am at the point in my woodworking journey that having a tool chest to store hand tools would be nice. I am also at the point in my life journey where one toddler (and soon to be an additional new born) make my shop time fairly limited to nights and nap times on the weekend.
I am thinking either the plywood ATC or Dutch Tool Chest would be my best bet for having a chest together in a semi-timely fashion (I also have access to a jointer, planer, and tablesaw for expediting some of the work).
Would you recommend one over the other (or something else entirely) for someone with limited time looking to get their tools stored sometime this year? If the answer is a plywood ATC, is there a particular grade or type of plywood I should look for?
Thanks for offering your time for this open wire, I enjoy reading it every week!
If space is an issue or you plan to take classes in the future, the Dutch is ideal.
If you aren’t going to travel, have the space and like the look of the big chest, then the plywood ATC is ideal. Good plywood is hard to find. Baltic Birch is usually a reliable purchase. Our lumberyard has decent ply with a poplar core.
Like with lumber, I want to pick my plywood myself to make sure it is flat and dry. So grades aren’t as important to me.
I’ve got a tiny (7’x10′) shop and a Dutch tool chest with some strategic wall and rafter hanging works great. I built the smaller model and later built a rolling stand, which I don’t currently use for reasons. Building it from pine went pretty quickly, even with the less-than-adequate set up I had a the time. If I had to use plywood, I’d probably go for cabinet-grade stuff, as construction-grade material these days is utter crap. But given the tools you’ve got access to, you ought to be able to put one together with pine boards in a weekend.
Is the wall cabinet in the photo finished with linseed oil paint?
Yes. Allback.
Breadboard ends for tabletops – Yea or Nay ?
If the wood is fully acclimated, they are not mechanically necessary. They are just for show and look nice.
If the wood is still a little wet the breadboard/clamp will reduce cupping (within reason).
Shipwrecked at sea, you wake up on an island and come across a fully furnished hand tool workshop and a warehouse of dimensioned lumber. No hope of rescue, building furniture is the only way to pass the time as you see out your days on the island. You don’t have your years of woodworking skills due to amnesia by falling coconut. What single book on joinery/furniture building do you hope is in the workshop? (You are in the Bermuda Triangle and burning the warehouse of lumber will not get you seen by any passing planes/ships)
Wallace Nuttings Encyclopedia of Furniture Vols 1&2
I would rivet all five volumes of The Woodworker books together and bind them in duct tape. I have no idea why those books haven’t sold better. They are better than I can personally do.
I have the first four. Fantastic books.
I agree Chris. Articles written by working folks in an easy to digest article length.
Build a boat
Bermuda Triangle. You will disappear at sea without a trace.
My holdfasts…don’t.
On the rare occasion they do, they are delightful.
But mostly, the holdfasts fail to cinch down.
I made a thick (3-5/8″), laminated southern yellow pine benchtop, just like you told me.
I made a boring jig out of three pieces of scrap plywood, just like you told me.
I used a WoodOwl UltraSmooth auger in 3/4″ (“19 mm”), just like you told me.
I used a corded electric drill at half speed, just like you told me.
I drilled a sparse, staggered pattern of holdfast holes, just like you told me. (But they were 3/4″, just like you told me not to; I had already bought two Gramercy holdfasts before you published your book and I already had that size auger bit.)
I de-greased the holdfast shaft with mineral spirits.
I circumferentially scuffed up the holdfast shaft with 60-grit paper, just like you told me.
I then tried scratching the holdfast shaft with a coarse file, just like you told me.
I then tried adding a series of pings with a center punch.
After all that, neither of my two holdfasts grab consistently in any orientation, over any thickness, in any of the ten holes, even when I bash on it with heavy metal hammer.
I think my holes are bored pretty darn vertical. Or, at least, some of the holes ought to be good enough to cinch down more than a quarter of the time. I was observing some splintering/mushrooming along the bore rim on the bench top surface and underside. Given all those previous steps, I wondered if that fragile corner of the bore cylinder was failing, so I added a light <1/16″ chamfer.*** That didn’t improve the holdfast grabbing in an observable manner.
So, I think I’m pretty good at following your instructions, and I’m willing to keep trying.
What should I try next?
***[Please calm my fear: I am concerned that the chamfering may have “ruined” the possibility of getting the holdfasts working. Chris heavily chamfered the holes in the $175 workbench (https://blog.lostartpress.com/2020/04/06/workbench-tour-no-1-the-175-workbench/#comments) and I don’t recall him mentioning that the heavy chamfering affecting the holdfasts’ action.]
All those instructions are to assist holdfasts that are temperamental. The root cause is that the shaft of the holdfast is not a close fit with the recommended hole size. That’s why we make our holdfasts a few thousandths of an inch smaller than 1″.
If it were me, I’d ask a blacksmith to make a holdfast with the shaft just under 3/4″. Or make it a true 3/4″ and then open up the holes slightly. Sorry you are having trouble.
Before I started, I did make sure that the WoodOwl bit bored close to 3/4″ before I started (0.742″-0.750″ subject to vagaries of measuring inner diameters in pine). What I neglected to do was measure the holdfasts themselves. I just made some quick measurements of my two Gramercy holdfasts, and they come in at 0.716″-0.720″. That surprises me. I would not think I could upset the steel enough (or rough up the surface) to jump that chasm. I’ll talk to Joel and also start a search for some blacksmith-made ones that have a better fit.
Thanks for the input.
I had a similar problem with holdfasts and found one of the problems was my technique. They seem to cinch much better when struck right over the leg than if they are struck in the arm part that extends parallel to the bench. I would recommend getting a few scraps of varying thicknesses and trying some tests.
Good suggestion, but I already tried that. I smacked them all along the bar as far as I dared. These holdfasts are formed or drawn and therefore don’t have a sharp corner, so there’s a limit to how far someone can strike it before it starts going sideways.
I also tried varying thicknesses from 1/4″ up to >4″.
My Gramercy holdfasts worked well on my Nicholson bench in 1 1/2 inch boards. I built a Roubo with a 3 1/2” top and using the same Woodowl 3/4” bit and the holdfasts wouldn’t hold. I ended up drilling a 1” counterbore about 1” up from the bench bottom and the holdfasts now work very well.
I’m sure Chris is right about the too-large bore, but I might experiment with this in some offcuts. Problem is, I have never been able to counter-bore very well after the primary hole is bored. Any suggestions?
I had the same problems, bench too thick, difficulty counter boring. I think I found I could just use the Veritas tapered reamer from the bottom of the bench. It was pretty easy. gramercy holdfasts work great every time.
Plug the hole and re-drill. There are 3/4” dowels out there, as well as 3/4” plug cutters. It seems silly, but it works.
Alternately, you could try buying some metal shim stock, and use it (with epoxy) to line the inside of the hole.
I second the “maybe too thick” observation. My bench and sawbench tops are 2.5 and 2 inches thick. My dog/holdfast holes aren’t a particularly tight fit. Gramercy holdfasts grab great for me. I occasionally have a hard time getting them to release.
Couple thoughts from my own experience.
Is your bench flat? If your piece is not resting securely on the bench it may introduce vibration that could work the HF loose.
Does your bench wrack? A tiny bit of wracking “could” twist a bench top just enough to loose grip.
Does your bench rock? Same result as above, just get some shims under the offending legs.
But really, every Gramercy HF should be sold with a piece of rosin. If you don’t have any stop by your local violin/music store and get some. Rub on the front and back of the rod, and re apply as necessary. (couple times a year?)
Yes, I just recently flattened it to the best of my abilities. Checked with winding sticks. I don’t detect and wobbling, wracking, or rocking. I’ll have to verify that, though.
Rosin is an interesting suggestion. I’ll have to consider that.
I’m looking into getting a replacement iron for a handplane and have heard a lot of conflicting information about the various steels. I’ve gone down the rabbit hole of blade steel metallurgy and am unsurprisingly left with even more questions and not a lot of answers. I thought I had it narrowed down to pm-v11 if I were to replace a blade, but recently in an Instagram post, some very respected plane makers put pm-v11 in a rather negative light, saying they’re more work and less forgiving than o1, mainly in regards to sharpenability and chipping, so my question is, what’s your current opinion on replacing vintage irons with pm-v11? Do you find that it chips and leaves tracks? Is it difficult or fussy to get it sharp with your setup? And how does it perform in hard woods like rosewood, ironwood, etc. compared to o1 or vintage irons? Thanks as always for doing this and for the immense amount of information you’ve put out over the last few decades.
I have not had any problems with PMV-11. I have it in my smoothing plane. It doesn’t chip or leave tracks (like A2). It is easy to sharpen – just as easy as my O1 blades. I have been using the steel since it came out.
Because of its expense, I wouldn’t buy it for all my planes. I was a bit bewildered by Dan’s post. I wonder if he got a bad batch? It doesn’t match my experience at all.
I suggested the same in a comment on that Red Rose post. I haven’t had any of those issues with PMV-11. Dan suggested that endgrain planing is tough on the metal and maybe that’s it? I don’t know, before I got my Ray Iles pig stickers, I used my PMV-11 bench planes for all manner of mortice chopping and endgrain slicing – never had issues similar to those described by Dan. So a bad batch does seem the most likely? Weird how experiences with the same steel could vary so widely otherwise.
I suspect I could have a bad iron after hearing about the good experiences with others who use the same PM-V11 irons. If the steel is too hard in my particular iron, that could explain the chipping of the cutting edge and also the harder time I have sharpening it.
You might send it to Veritas for testing. I am not a steel snob. I just want the stuff to work and be easy to sharpen. And since day one, it has done that. Thanks for your honesty, Dan!
I like the way boiled linseed oil looks as a finish but I’d like to apply a French polish over it on a ukulele project. Is 24 hours enough time to wait between the oil & shellac mixture?
I do not think I have ever applied shellac over oil. Oil takes a couple weeks to fully cure, but I don’t know at what point it is OK to coat over it. When I have applied paint over oil, I wait couple weeks.
I would try a test board first.
Hey Brad.
Try boring up your dog holes from the bottom of your bench with a 7/8 bit to reduce the length of your 3/4 holes. Try drilling up about an inch. This should allow the holdfast to wedge in the hole better.
Nope. Making the fit of the shaft to the hole looser is not going to help. The shaft is already too loose. The hole needs to be tighter, or the shaft bigger.
His recommendation is to decrease the depth of the hole not increase the radius, so this will not make the hole any looser. I agree that this is the proper solution if he wants to use these particular holdfasts which I also own.
Good morning! It is very generous (and completely crazy) of you and Megan to do this so frequently.
When planing protruding dovetails, especially in very soft wood (balsam fir), I find it hard to avoid breakout that tears at the unsupported corners of each ot the tails and pins. What should I try?
How much are they protruding? It must be quite a bit if they are breaking off.
When we teach dovetails, we set the baseline to the exact thickness of the wood. If there is any protrusion, it is very minimal. We do this in very soft woods such as white pine and basswood. (As well as hard woods.)
If I had big protrusions, I would use a flush-cut saw first to get them close.
What does the spell on the front of the cabinet mean
It is a general, all-purpose protection glyph for the owner (represented by the center circle) and the contents of the cupboard.
In general, when you see a circle with an X through it, that represents a person.
It kind of reminds me of a crop circle. I like it.
Lovely post – the wooden cabinet featured in the image is so precisely detailed!
Thank you!
Noticed on your “Family Tree of Chairs” poster that you omitted an interesting one called a “Birthing Chair”. Saw one that was three legged with hand holds on each side. Saw a few other designs too. Is this one chair you will probably never build?
I classify that as a backstool. I’ve seen several, but I’ve never felt the urge to make one.
Chris: two crucible questions. First, any eta on planing stops coming back in stock? Second, what’s next on the Crucible tool roadmap after the cross-peen hammer?
They are pouring the planing stops in June. Then they have to be ground. So probably July.
I am working on two Crucible tools at the moment. A 16 ounce nail hammer. And a grooving cutter for a compass a la “The American Peasant.” Everything else is Top Secret (just kidding, we’re making it up as we go).
Can sweat stain wood??? I work in a 2 car garage in South louisiana, today is 92 with 80% humidity and it’s 8 am lol. It’s awful I sweat all over my tools and projects!
That’s a great question. I’ve never seen my sweat cause a problem. Our skin produces an oil that is similar to jojoba, and that is what helps color and oil old pieces (especially chairs). But most of the color is dirt.
So, bottom line: No clue!
If you sweat on part of the piece, you might have to apply an even coat of sweat to the rest.
A spit coat of sweat
Does the spit also have the jojoba oil like the sweat? I like the idea of spreading my bodily fluids evenly on the wood. Written from Southwest Florida where it is 90+ degrees, the Gulf of Mexico exudes salt into the high humidity, and I have to flap-sand rust off some of my tools.
I haven’t seen a problem with it myself and I have dropped a lot of sweat on my work, but if you want to minimize it wear a sweat band around your forehead. ( I roll up a bandana and tie it around my forehead). It also helps with sweat dropping on the inside of my eyeglasses.
Brown paper carpenter’s hats work well
It’s interesting to observe the differences in methodology between John Brown (as in his book), Chris Williams (as in his book), and you (as in your books). Is the best way to understand these differences to say that they reflect an evolution in efficiency of work and availability of certain tools? Or do these differences reflect an intended stylistic difference in the resulting chair? Thanks!
A lot of JB’s techniques were from tradition, or boat building or made up by him. Chris Williams comes from that same tradition as he worked with JB for years.
I didn’t have that (for better or worse). I learned chairmaking from David Fleming, Don Weber and Mike Dunbar. I read every single book I could find on the topic. And during the last 20 years have settled into the methods and tools I prefer. I eschew most jigs, but I am happy to have some specialty tools.
I do not think the approaches change the chair much in appearance. That comes from the maker.
Hi Chris. After a long wait, I now have an Allan Williams travisher and a Barr Scorp/inshave. I am sure, somewhere, you have written about sharpening these types of cutters, but I couldn’t find it. Could you point me to any blog entry, article, or book that you may have written about this? Thanks!
I cover it in my sharpening videos. Basically I use diamond paper (from Lee Valley) wrapped around a thick dowel to dress the bevel and the flat face. You also should check out how James Mursell at Windsor Workshop does his. He has a free video on his site.
I looked, but cannot find diamond paper on the Lee Valley website. Any hints?
They call it Diamond Lapping Film:
https://www.leevalley.com/en-us/shop/tools/sharpening/sheets-and-belts/68943-diamond-lapping-film
https://www.leevalley.com/en-us/shop/tools/sharpening/sheets-and-belts/33004-3m-micro-abrasives-for-sharpening
The second design in the Stick Chair Book is the strikingly modern Curved-Back Armchair, which you mentioned draws inspiration from the Gibson and other Irish designs. Given you just released a video on the making of a Gibson Chair, I’m curious about the comparison of the two designs strictly from a comfort perspective? The Gibson seems like it lay back so much more than your Curved Back Armchair, is that just an optical illusion? Lastly, are the added tips and tricks from the Gibson Chair video relevant to your Curved-Back Armchair, or is the instruction from the “Build a Stick Chair” video more applicable?
The reality is, eventually I will purchasing both videos, because every bit of your instruction is worth the price of admission multiple times over, so I should one day be able to answer these questions myself. But you do seem to have such an affinity for the Gibson, despite those rounded outside curves on the Backrest… Have you ever tried a more angular Backrest like the Curved-Back Armchair, and it just took too much away from the Gibson’s charm? Those curves there, just, bother me…
They are similar. The Gibson is trickier to build because of the intersection of the arms and the angled back sticks. Comfort-wise, they are very similar. The Gibson is wider. And the angles for the legs are different. But I would say that you could use The Stick Chair book to figure out a Gibson and the video to make the curved-back armchair.
Part of the Gibson’s charm is the crazy backrest. The chair in The Stick Chair Book is my design, which reflects my approach to stick chairs, which is more toned-down.
We have homeschooled all of our children and Joshua is our youngest, he is 15. I started him last year in shop or handtool woodworking. We built a Nicholson style workbench and a pair of end tables using Cedar rounds with staked joinery. This year I want to go more in depth with him using a textbook. I have recently acquired a copy of Aldren Watson’s book, Furniture Making Plain & Simple. So far I am really impressed with th book and his instructions and illustrations. (I also have a copy of his book Country Furniture). Are you familiar with this book and if so your thoughts on using it for a textbook? I am also open to other suggestions you may have.
He really likes working with hand tools and is getting really good at it for his age
The Hayward books are excellent, both the old ones and the ones we publish. Those provide the foundation for exploring all the styles.
i love my lil accuburr! Do you find utility in the different sized grooves for certain situations? Or are you mostly using just one? I played with it and couldn’t tell much of a difference…
Thanks!
I’m glad the Accuburr exists and has helped so many people master their scrapers. I still sharpen mine the same way I was taught in 1996 with a burnisher and sharpening stones.
In my experience, most hook angles work about the same. The angles at the extremes (0° and 25°) are different.
Chris, I’ve seen a number of boutique publishers pop up recently who specialize in ultra premium editions of popular books (Lyra’s, Thornwillow, Arion, etc). You have had some success with fancy editions yourself in the past. Do you have any plans to make “lettered” or “numbered” premium print runs in the future? Why or why not?
As a publisher, I don’t want to cross over into the collector community. Why? I don’t understand collectors. When we have dome some special editions (leatherbound, letterpress, the deluxe Roubos), the customer complaints from the collector set were Criminally Insane. For example: They complained about the exterior mailing box (not deluxe enough). And their special requests drove me to drink.
I fully support these presses and their work. I am not complaining about them. I simply am not wired to serve that community.
We are shooting for the quality of printing and binding from the early and mid 20th century. Books that are taken to the shop. At a price that normal people can afford. And content that will be read and used.
Hi Chris – There is a bit of beautiful joinery called a false miter that is used to connect the crest rail and arm posts in a certain style of chair. Have you ever seen an article/video illustrating how to perform this joint? I’m happy to pay for the information if you can point me in the right direction.
Maybe someday I can take a chair class that uses this joint but until then I’d love to see a tutorial.
I’ve never made that joint. I know that Curtis Buchanan and Peter Galbert use that joint. You might check out their websites. It’s a pretty common joint. Perhaps other readers know of good resources.
http://chairnotes.blogspot.com/2007/04/false-miter.html?m=1
Hey Chris when you make the arm bow from two separate pieces what’s your method of making sure they join squarely, and do you join with dowels or just use the shoe for strength? Thanks Stu
I use pocket screws. John Brown and Chris Williams use dowels. I have also used a Domino….
And if you use pocket screws, consider removing them after the joint sets up. Or you can do what I did and hit one while you are drilling for your sticks.
I’m gathering all these great lessons learned the hard way😂😂
Have you discovered any further finishing refinements for Allback linseed oil paint?
Do you plan on painting a chair with it?
Thanks
Here’s how we do it now:
We have not had any of the problems other people are reporting (adhereance etc.)
And yes, my next painted chair will be with Allback.
Thanks!
Intro: i really, truly appreciate the work you all do. It may sound corny, but the quality and integrity of everything LAP puts out has had a positive impact on my life in general. Luckily, there seems to be no risk of LAP going under anytime soon, and I’d kike to keep it that way.
Question: How do I put as much money in your pocket as possible? Of modest means, I still want to make sure that my money spent maximizes your earnings. Living in Europe, I buy books as PDFs, but I feel almost guilty since they’re only half the price. Are you still making enough on your digital content?
Thanks! Just keep buying the books that suit your work and in the format you prefer. We make plenty of money on our pdf books. And we are not greedy, like some other publishers.
Dear LAP, I enjoy your blog and books, which I own several. My question is about wood specie selection for stick chairs. I have made a stick chair proto type which was a great learning experience. I would like to pursue more chairs for use in my house. Question: I like walnut but notice you don’t construct chairs in walnut. Is walnut not straight grained enough? Too brittle or??? Your guidance most appreciated.
I have made many stick chairs in walnut. You need to beef up the size of the components by about 1/8″ for best results. Don’t use a lot of taper on the legs. Use 3/4″ sticks instead of 5/8″. Beef up the stretchers by 1/8″.
Morning
A few months back, I was pretty stoked on your spells and picked up an otter timber scribe and a grooving compass. I have zero problems with the grooving compass but creating straight lines with the timber scribe is super hard for me (especially when intersecting another line). I am left-handed, so it is definitely a challenge to hold the flat side of the tool along a straight edge with my right hand, but I can make it work. My line still wanders though. I also feel that my angle of attack is super high (I have to hold the cutter handle super high without digging into the wood too deep). Any suggestions would be appreciated. thanks! Also, I have been practicing with many different species of softwoods and lately I’ve had a surplus of scrap beech that I have been practicing with.
Try putting a 5° bevel on the outside of the tool’s edge. That seemed to help mine. Is yours an Otto scribe? Recently a student came in with one that was a knock-off of the Otto and we couldn’t get it working.
Great, thanks I’ll give that a shot! Yes, it’s an otter scribe
I have a low staked bench that resonates quite loudly like the world’s worst cello when I use it for sawing. It does this no matter what saw I use, how the board is held in place (clamped, sat on, held lightly by hand), or thickness/species of the board being cut. The bench is otherwise stable, not budging an inch when using it for chiseling, planing, driving nails, etc, whether I am seated on top or not. Any idea what may be causing this, and how to make sure it doesn’t happen when building the next one? Thanks!
Wow. I have never encountered this problem. I am clueless here. Any one else have any ideas? (Sorry!)
The resonant frequency of upright basses sometimes causes problems (“wolf notes”) so people use “wolf eliminators” (https://www.stringemporium.com/upright-bass-wolf-eliminator.htm). Maybe try to disrupt the resonant frequency of your bench? Attach some kind of weights to the underside? May be a long shot.
I ended up adding bolting a 90×90 piece of larch to the underside of my low bench to as part of a second phase of stiffening it up, slightly OTT but I had it lying around and my bench as original built was far from stiff enough, being made of two separate 3cm thick slabs that were only screwed together, not glued (will not repeat that mistake a second time). What also helped was to isolate the bench from the floor with some rubber or felt pads. I have a wooden floor, and the wood on wood was very loud when sawing. I used some rubber pads I got at a local hardware store, they are meant for outdoor wooden decking, and as a bonus also help with stopping the bench creeping around the floor when using the bench while seated on a stool alongside the bench…
Thanks a lot for doing this!
Is there any wood species that, despite not having straight grain, can be sawn (not riven) and safely be used in shaved legs for a stick chair? If so, is there any consideration to improve the mechanical disadvantage in relation to straight grain species?
There might be some exotics such as purpleheart that could be used with grain run-out. But why risk it? I can go to any lumberyard and find hundreds of boards that have straight grain I can use for stick chairs.
Hey Hi Hello! I’ve never tussled with hide glue before, but I am attempting to repair some failed mortise and tenon joints in some old Stickley chairs. I just bought my first bottle of Old Brown.
Megan mentioned last week that hide glue will remelt (what a relief!) and stick to itself. Does it need to be reheated/disassembled to do this? Or can I just try to syringe in some fresh goo?
Thanks so much for your time XOXO
You might get away with injecting some. You might not. It’s always best to disassemble the joint, make sure everything is intact and fits. Then apply a fresh coat of liquid hide that has been warmed.
I’m sorry if this has been answered before, I did a quick search of your blog and couldn’t find what I was curious about.
What advice can you give a small business owner, working in the trade, on when to spend the Lie Nielson money and when to spend the craftsman money? I took over a dying business that is now doing much better than it has in years. However, I am unsure if I’m being responsible with my businesses funds 100% of the time. I also feel that I have wasted too much time fixing bad tools or replacing parts.
p.s. If you ever have questions about gilding or historic picture framing, I have a decent library on those subjects.
Good tools are never a bad investment. Usually the bigger problem is buying tools you don’t need or use. Once I decide a tool is core to my work, I’ll buy the best one available. But that’s not always the most expensive one….
For example, modern jack planes are too heavy. So I bought an old Type 11 Stanley No. 5. Modern nail hammers suck. So I bought a Plumb octagonal-handled 16 ounce hammer. The Lie-Nielsen smoothing planes and the 60-1/2 block plane are the best ever made and fit my hands. Good chisels are more about weight, balance and feel in your hand than edge-retention.
Figure out the core set. Then spend time researching and trying out the options for that tool.
I am teaching my 7 year old grandson wood working . He has some tools (small hammer, block plane,screwdriver). Any other suggestions? Do you sell a child size shop apron?
You can get a nail apron at the home center for $5. Other tools kids like to use: coping saw, spokeshave, brace/eggbeater drill. I’m sure readers here could chime in with other suggestions.
I teach elementary and middle school hand tool woodworking. The kids love spokeshaves once they get the hang of it. Block plane is great, but by 7 they can handle a no. 3 or no. 4. I find kids have better luck using a Japanese pull cut saw (and the ryoba saw has both rip and crosscuts). 12oz hammer is better than those stubby ones, as they get more leverage. If you have him using a coping saw make sure to stock up on extra blades! Knot free wood is important. Texas Heritage sells a really nice youth apron (I have their adult one and it is wonderful). When you’re teaching him let him make mistakes and experiment and make sure shop time is fun! Good luck!
Chris, can you share any books on East European peasant styles/furniture/spells that you have found to be particularly helpful or intriquing as you researched your upcoming book?
The book by Gyenes Tamás is excellent. Check out his links page: https://acsoltlada.hu/kapcsolat_en.html
“Latvian Design” by Aleksandrea Dzervitis
Most of my research has been in bits and pieces. Academic papers here. Bits of books there. There will be a bibliography with the book. But I haven’t assembled it yet. Sorry.
I’m building a Roubo basically based off the anarchist workbench but using 8/4 stock for the stretchers. When I went to alter the tenon that interferes with the crisscross, instead of notching it, like a dumb, I just cut it all short. I’m using 5/8” drawbores with the 1” offset on center. There’s prob around 9/16” of tenon left after the hole in the tenon. Am I asking for trouble ? If so, do you have any recommendations?
Best!
You’ll likely be fine. The joints between the legs and the top carry most of the burden. You can bolt some metal L-brackets to the stretcher and leg to reinforce things.
I have become increasingly unhappy with the commercial sharpening company’s I have used to sharpen my jointer knifes. I am experienced at sharpening my hand tools. Do you have any advice or opinions on hand sharpening jointer knifes?
Thanks Ray
I have never sharpened jointer knives by hand. And now I have a helical cutterhead. I know you can do them by hand, but I don’t have any resources to recommend. Perhaps other readers here can chime in? Sorry!
Tangential to you question: Anyone’s thoughts on converting to helical? Shellix, etc.?
We have Sheelix heads on our jointer and planer and LOVE them.
I’m currently building a roman workbench. My bench is made of red oak and about 2-3/4” thick. The tenons have a 1-3/4” diameter (as described in your book) but I’m having difficulty finding such a bit. Or I’m looking for the wrong thing. Recommendations?
If I remember right, I used a Mikwaukee bit to make the mortise (from the home center). And I turned the tenons. If you drop down to 1-1/2″ you’ll be fine.
I’m wondering how much general finishes milk paint you use, when you spray a chair.
I realize each HVLP sprayer is different, and you pick up some volume when you thin the paint.
I’m just looking for an approximate amount of paint to purchase,
so I don’t run out half way thru a coat.
Also, I see you have applied Sinopia milk paint with a brush.
Have you tried spraying it?
Thanks,
Mark
I usually buy a quart for a chair. But we don’t use the entire thing. It depends on how many coats you need. Which depends on the paint and your skill in spraying it.
On the Sinopia, you cannot spray it in my opinion. When I thinned it down enough to spray the binder did not bind.
I am going to have some time over the summer. Would physical assistance with the Anthe Building restoration be helpful?
Hi Michael,
Thanks for the offer of help! Right now the first floor work is all plotted and bid out. We are just waiting on a permit to begin the construction phase.
I might organize a demolition and cleaning “party” for the second floor this summer. Send Megan a note.
Hey Chris,
While waiting for the ‘spring pole lathe’ book to be published by LAP I came across a blog post by Jarrod Dahl where he elaborates on his development/design of a lathe that is primarily designed for bowl and plate turning. He implied that you build a spring pole lathe that is designed either for bowls or one that is primarily designed for spindles. Unlike motorized lathes they don’t do both well. I’m looking for spindle work primarily. Do you know if his book has designs for both or am I to be disappointed when it comes out and are better off looking at the Mortise and Tenon design or a Roy Underhill design for a spring pole lathe.
Thanks.
I do not know the answer as I haven’t seen the manuscript. You should send a message to Jarrod.
I am going to download the Gibson video today, but wondering how you would go about cutting the backrest without a bandsaw? Would this be job for a large frame saw?
I would shape the three laminations separately with a frame saw. Get them really close to final shape with rasps. Then glue them together and finish the shaping afterward. FYI, the original Gibsons were cut with a band saw (I’ve seen the tool marks). So don’t do it by hand if it’s some sort of machine-shame you are experiencing.
Thanks! Would happily use one if I had one! Only shame is that I didn’t buy bandsaw first (before cabinet saw) when I started down this path.
Hi Chris! Thanks again for answering my aesthetic question about using different kinds of wood a couple weeks ago. And thank you also for Sharpen This! It’s immediately improved my work. And it contains the clearest, most intelligible explanation for using a secondary bevel that I’ve come across.
Good afternoon, Chris!
I’ve got a challenge with soft wax.: I just finished a shelf for my record player and amp. I let the shelf cure for a month before I set up the stereo, however, the feet on the amp and the record player seem to have acted like a sponge and sucked up the finish.
My question:
Did I use the wrong finish? Should I have used a shellac or lacquer instead?
If so how should I strip the soft wax off and reapply a different finish?
Thanks,
Gary
Weird. I wonder what the feet are made of. I have never seen this.
If you want to use something else, simply wipe the cabinet with mineral spirits. Shellac, lacquer or a wiping varnish will provide a film finish.
I’ll give it a rub down and try a wiping varnish.
The feet have a felt layer (on the record player) or a foamy layer on the amp. I feel like the weight of the amp plus the foam makes it like a sponge.
I bought the soft wax a year and a half ago – it doesn’t “go bad”, does it?
No, it doesn’t go bad.
Good afternoon from Atlanta!
I work in a countertop shop, and I’m always curious about the historicity of end grain in its use as a countertop surface. I’ve seen dedicated butcher blocks, but they seem more akin to hewing stumps than what we think of as modern countertops – that is, it’s more about the size of the block than the grain orientation. Is there any record of using end grain outside of that pretty specialized field? Is there any truth to the supposed self-healing properties of end grain in its resistance to knife cuts? Or is this all just faux history used as marketing?
Thank you and the LAP crew for all you do.
I am not a fan of end grain cutting boards or countertops. Wood movement is real. I prefer face grain. It lasts a long time and is easy to keep clean and doesn’t delaminate. I think of cutting boards and countertops as workbenches for food prep. And I wouldn’t want an end-grain workbench.
Just my 2 cents.
hey chris! awhile back i made a couple of spinning stools for some neighbors who do period spinning wheel demonstrations. i made them 3 legged because they are often in parks with uneven ground. they asked me if there is a way to stabilize them because they have proven to be a bit tippy. the back leg passes through the seat and helps support the removable back. i thought about cutting the back leg short, adding a cross piece with two stubby legs (could look real cool or real crappy), or cutting off the back leg flush and adding two back legs like a regular 4 legged stool. any other ideas i should consider?
The traditional way is to use more splay. Look at some old milking stools for inspiration. If you have a back on the stool, the leg under the back needs to rake back to the point where it is below the sitter’s head.
Hope this helps.
Hi Chris. Just wondering why you put on shellac first, and then add black bison wax. It seems to me that the shellac would fill the open grain and not allow the wax to do its proper job. Can you shed some light on this? Thanks for this forum, much appreciated!
It takes a LOT of shellac to fill the grain. I’ve never encountered the problem you describe.
Also, applying shellac over oil/wax/solvent can be dicey and is not something I would do without a test board. The traditional arrangement is dye, then shellac, then wax.
Hi Chris. This is likely more of a Megan question. Like Megan, I love a No 3 hand plane as my final smoothing plane. I’ve wondered what would a No 2 smoothing plane be like. Any thoughts? Could be too small could be just right. Thanks.
I use a No. 3. Always have. I tried a No. 2, but my hand is too big. Definitely try one before you buy one.
Thanks. Will try one at the next local collector tool show I attend.
Are there a lot of fakes in the primitive antique market some them look to perfectly old?
Yes. Tons of them. Some are old pieces with doctored finishes. Others are built new and finished to look that way. I wouldn’t buy one over the internet unless I trusted the dealer.
I’ve used both 12 degree and 6 degree reamers and I use a drawknife and spokeshave to cut the tenon. Is there any mechanical difference in strength between the two?
If there are differences, they are not significant enough to mention. I have used both with great success.
Good morning Chris, thanks as always for doing this.
In “Roman Workbenches”, you seem to indicate that you’re not a fan of red oak, saying “The fact that red oak dries without massive distortions or checks is the nicest thing I can say about it.”
I noticed that a lot of your chairs are made in red oak. Is that simply due to price/availability at the yard? Or has your opinion on the wood changed? Do its mechanical properties make it preferable for chairs over other similar woods?
I built my first stick chair with red oak, entirely because it was the most affordable choice at the lumber yard. But I found it exceptionally challenging to work, scooping the seat out was probably the most exhausting and frustrating moment in my woodworking “career”. It might be quite a while before I try to use it again.
Red oak is the punching bag of the furniture world. Everyone who has to work with it has their ups and downs with it. Some people don’t like the smell. Some people don’t like its pink cast. Some people don’t like that it’s not as strong as other oaks.
I’m sure I wrote that after having to build a lot of stuff with it. And when it was plainsawn (which is when oaks are at their ugliest).
In truth: It is in expensive, strong enough and can be cut (quartersawn or rift) to look nice.
And if you make your next seat quartersawn (instead of flat sawn), saddling it is a joy.
Good Afternoon, Chris.
Thank you for doing this again today. I purchased the vintage Ulmia workbench from your workshop last year, and I was thinking about adding the Benchcrafted Swing-Away Seat to the front right leg. I typically see these installed on French Roubo style benches, but I wanted to see if you would have any concerns attaching it to the sled-style leg. Thank you again for the opportunity to purchase the bench. I have really enjoyed using it!
No concerns that I can think of!
I appreciate it, thank you!
what the heck has happened to all the Star-M F-Type drills in the world. Mines gone dull and I can’t find one in stock anywhere?
Good question.
Same question re Green Chartreuse.
I got two of the 16 mm from Workshop Heaven just 2 or 3 weeks ago. I didn’t buy more, because I didn’t want to be greedy. But my guess is it’s like toilet paper in March 2020. When they appear, people hoard, and they’re gone quickly.
Hey Chris,
I’m going to be doing my first tapered tenon, but Lee valley seems to always be sold out of their 5/8 cutter. I figure a 9/16 would work just as well—I would just have to leave my legs slightly longer? Or should I wait out for the size you usually recommend?
-James
Try 9/16″ … should be fine.
On a similar note, for those who can’t ever find the 16mm Star M type F bits, would a 15mm or 18mm work?
Yup
Hi, thank you for this Q&A. It’s very generous, and very helpful.
I am turning some chessmen using walnut and maple. I would like to use natural finishes, and ideally I would like them to have at least a little shine. My experience with these kinds of finishes is limited to the soft wax your daughter sells. Do you have any recommendations?
Shellac and wax is a traditional and natural choice.
Hi Chris,
Not a question, just came up with a pretty good idea you might enjoy.
I received my reamer and my tennon cutter and was anxious to give them a try in preparation for my first staked project, the lowly sawhorse. I started reaming and realized I didn’t have a tenoned stake to measure my progress. I pulled out the tennon cutter and tried to use it. No go. I couldn’t get it to cut.
I thought maybe the blade wasn’t adjusted properly but was afraid to move it. I remembered your admonition to cut a master tennon when you first got the tool, but I felt like I was stuck between a rock and a hard place. I wasn’t sure what to do.
I then had an epiphany! I do have a master tennon, I have a perfectly matched reamer. I carefully inserted the reamer into the tennon cutter and found that the blade was almost 1/8” off. I loosened the set screws and lowered the blade to the reamer’s body. Voila, I was able to quickly cut my first tapered tennon. I hope this helps.
George.
Hey guys,
Any tips on how to cut an angled tenon for a joined chair rail? Other than careful layout and some undercutting? Thx!
Jeff Miller in Chicago has developed a system to do this with a flat frame that surrounds the rail and clamps it. Then a flush cut saw is used against the frame to cut the shoulder. It’s based on an old jig. French perhaps? Try some googling, reach out to jeff or maybe someone here can remember where it was published.
Hi Chris (and Megan), thanks for doing these. Are you planning on printing any more stickers? I unfortunately missed out on the bandit t-shirt, will you reprint those?
Right now we are too damn busy to work on fun things like that.
You can download our artwork of the Bandito shirt free with this link:
https://www.dropbox.com/s/yu84ru4ebcdbhll/newbandito6nobackground.pdf?dl=0
And make your own shirt!
wow, thanks so much 🙂
In The Anarchist’s Workbench, should the boards for the bench top also be mated “sympathetically”? In the photo, they are not. In the section on the legs, it says that’s important. What gives?
Ideally, yes. But I screwed up with the top.
Must have been the glue. Thanks!
There was a LOT of glue. It’s a small miracle I can still spell my name.
My best learning style is to start simple and work up, and collect a lot of mistakes on the way. Could you suggest a “progression” for learning to make chairs? I.E. simple projects that would yield a finished item and give some hands on experience on the various skills and then steps to lead to more complex results. And please not only completed chairs but also progressively more difficult components. Thank you
And thanks for giving us your Saturday.
Half of “The Anarchist’s Design Book” is this lesson. It starts with a lesson on the geometry. Then a staked saw bench. Gradually leading up to the four-stick Welsh chair with a little saddling. From there, “The Stick Chair Book” takes over. Same progression. Up to the chair on the cover.
Sorry that the answer is “buy my books,” but that progression was my plan all along (to make all woodworkers into chairmakers without them noticing).
Sorry Chris for question 2 but it fits here. Is full blow carving like what Mary May does the evolution after chairs? If not, what is? I’m still oogling over building rectilinear furniture.
It can be veneering, carving, painting, turning, marquetry, parquetry, bedazzling.
There is no order in the next steps. It’s just what you desire to do.
Claus,
I found a good starting project to be the tall stool, from “The Anarchist’s Design Book”.
You will learn about sight lines and resultant angels for the legs, tapered tenons, and how to make octagons. The project has some very simple stretchers between the legs.
Best of all, it is intended to be built with 2 x 12 construction lumber, as opposed to hardwood.
Now mistakes are inexpensive, and nothing to freak out about.
Just grab another hunk of 2X and get back to the project.
Good luck,
Mark
Hi Chris. I’ve had a lot of success sharpening with Shapton stones (1000/3000/8000 grit) and both Lie-Nielsen and Veritas honing guides. If I want to touch up an edge, I need to set up the guide and go back to the 8000 stone. This works, but is fiddly and time consuming, so often I just wear the edge down until I have to go back to the 1000 grit stone.
As an alternative, I’ve experimented with freehand stropping since it would be a lot quicker, but it’s given me nothing but grief. I’ve got some soft shop leather spray glued to 3/4” birch plywood, treated with green compound. Whenever I try stropping, I just seem to lose the cutting edge to (presumably) roundover since I can’t find the secondary bevel angle I’ve produced on the honing guide. None of the YouTube tutorials have cleared this up. Can you help?
That is the problem with freehand sharpening – beginners tend to dub the edge. Or they keep raising it until the tool needs a lot of work.
For bench tools (plane irons and chisels), I don’t strop. I just hone and polish. It saves time in the long run.
You can learn to strop freehand. It takes some time. But you have to practice to get a feel for it.
Hello Chris,
I am planning a an outdoor garden project using African Mohogany and have a question regarding the moisture level desired when cutting, making joints and glue up indoors in the shop. When one acclimates wood to the the shop environment prior to planing/machining, should there be any adjustment to target moisture level knowing that the finished price will live outdoors year round?
Geoff
Usually, no. But if there are doors, drawers or frame-and-panel constructions, I would probably built the piece, let it swell outside, then adjust the doors and drawers to fit. Most outdoor projects are simpler constructions that don’t have the same considerations as indoor furniture.
Finished piece
Hi Chris. My next workshop project will be a new Anarchist-style workbench with a nice leg vice. Because of space constraints, I will be asking it to be a bench, and also an out feed table. It will have to be shorter than yours, and likely wider. At what point beyond your recommended 22” width does wood movement become an issue? I’m afraid the movement differential between the stretcher and the top might start to impact the vice… Is say, 32-36” asking for trouble? Thanks!
Wood movement won’t be a trouble if you push it toward the rear of the bench. You do this by opening up the mortises in the top for the rear legs. I thought I covered this in the book.
I’m cutting up some logs for firewood and am noting that some of them are nice and straight and a good diameter – I’m thinking I’ll give my froe a go, yo, and make some sticks for chair parts.
If you were going to cut up some logs to split out for chair sticks in general – a mix of legs and spindles – how long would you leave the logs?
Most stick chair parts can come from a log that is 24″ long.
Have you tried the Woodriver metal bodied spokeshave that is made like an old wooden bodied shave? I gave my Stanley to my middle son and replaced it with the Woodriver shave.
I have not. Sorry.
For someone with pretty good WW skills, especially with hand tools, what is the first stick chair to start with?
I have built several sculptural chairs, similar to Maloof types, but wish to start on stick chairs……
Thank you
Any of them! Sounds like you are past ready to build one.