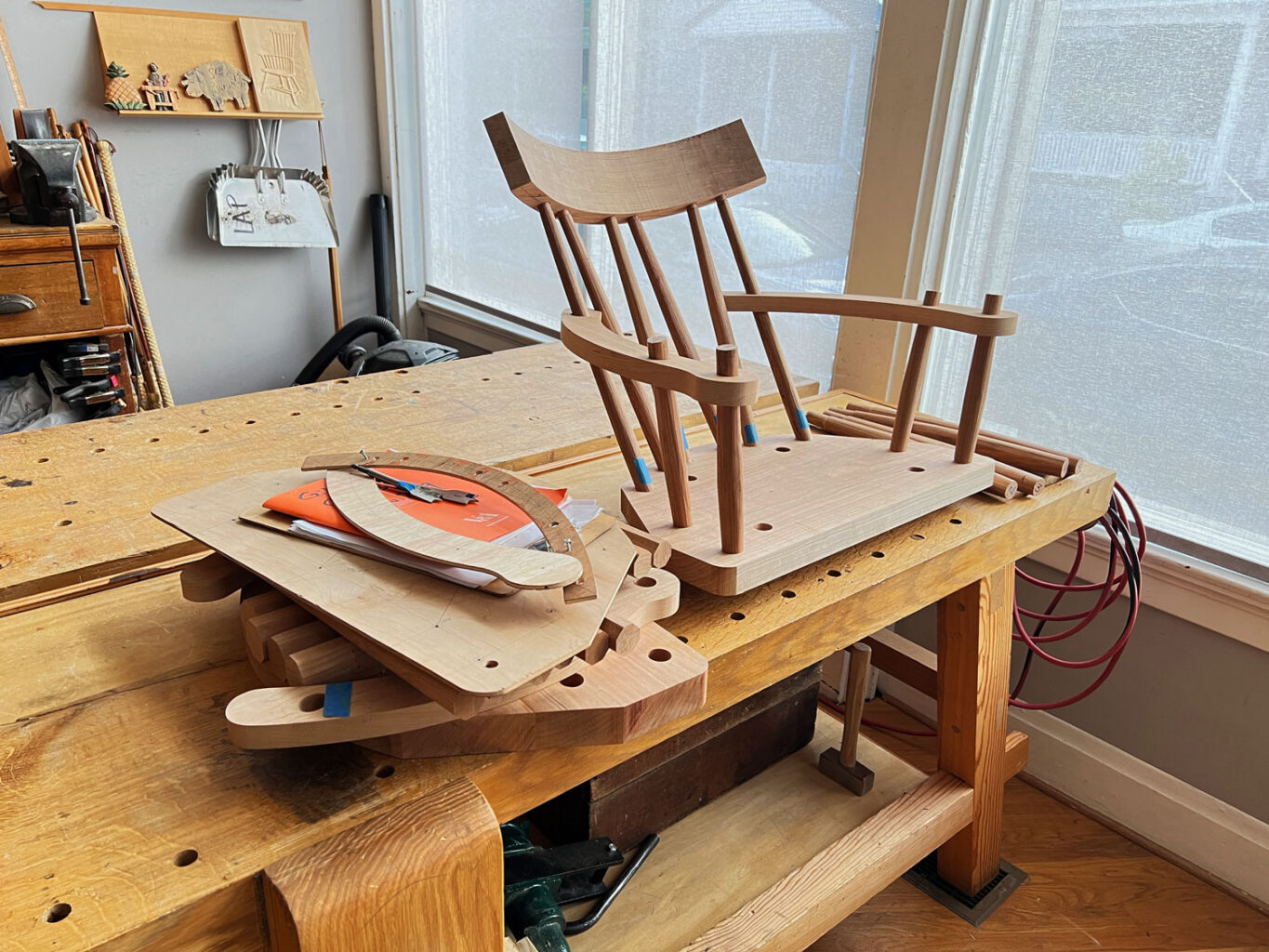
Update: I am sad that no one asked about cat care. So I’ve closed the comments, and am going home to sulk with a cat on my lap. – Fitz
I’m teaching a class this weekend, so Megan has volunteered to staff the LAP Open Wire today. So in addition to woodworking questions, feel free ask about home renovation and cat care.
Here’s how it works: Type your question in the comment field. Megan will do her best to answer.
Before you ask a question, please read this.
- If you could limit the number of questions you ask to one or two, that keeps the load manageable. And remember brevity is appreciated.
- If your question is your first comment here, it will automatically be flagged for moderation. Your question will appear after she approves it.
So here we go…. Note that comments for this entry will close about 5 p.m. Eastern.
I have three questions preceded by some context. Context: I know you have been through the phases of tool acquisition and rationalisation in your journey to-date, especially with hand planes. (1) How did you manage to suppress, or eliminate your tool collection tendencies? (2) Do you miss any tools you’ve dispensed with over the years? (3) Have you ever come across a piece of pine that identified as walnut (Just asking)?
1) Not having a lot of $ helps. That said, I’ve always tried hard to buy the best I can possibly afford, so I don’t have to buy things twice. I do have three smooth planes…but they are all different sizes, so that doesn’t count! Plus I loan them to students, so…that’s my excuse. 2). Veritas left-handed skew rabbet. I never used it – but it would be great to have now for classes. But I greatly regret NOT buying an Eccentric Toolworks dovetail saw. 3). Nope.
Do you have any major projects on the horizon you’d like to share about? Maybe after you guys get the new building all set?
So in 5-10 years? 😉
Later this year, or maybe early next, we’re planning a workbench video, and we have a lot of books under contract that should be coming in soon (including mine).
Hi Megan! What is the most difficult aspect of the woodworking craft that you feel you have now mastered to your satisfaction? Thank you.
Oh – I don’t think I’m ever satisfied; there’s always room for improvement. But I don’t completely hate my dovetails.
How do you store your SYP stash while accumulating enough boards to build a workbench? Some of mine are turning into pretzels 🙁
If you have room, sticker it as you stack it up. And buy the lightest boards you can (the heavy ones are more wet, of course). And maybe try a different supplier. On the already pretzels, hopefully you can salvage enough for shorter parts.
If I can chime in here, I have used southern yellow pine a bunch. It’s one of my favorite woods to use for various things. Definitely sticker it and leave it like Megan said. Make sure there is no pith in the boards you choose at all. Those pithy boards are good for some stuff difficult for furniture other than shelves in closets. Then watch those brown lines going across the board. I feel that a lot of them is better. On the end look for a bunch of growth rings that are tight and go straight up an down. Straighter is better. The fewer the cathedrals the better. Finally I have found that when choosing my SYP if I pick it straight and sticker while keeping in mind the above, then get it after about four to six months it stays straight when I use it even when I am ripping down 2x12s. One of the most beautiful woods imo. Sorry for the long comment.
Good morning Megan,
I have a solid teak cabinet that has face trim coming loose. What glue should I use to secure the trim. I hear teak is oily wood and some glues don’t work real well?
Thanks
Geoff
Are you able to get behind it? If so, wipe the glue surfaces with acetone or lacquer thinner and immediately glue it. Chris used PVA on the teak furniture in “Campaign Furniture,” but some folks swear by poly glue for this (e.g. Gorilla Glue). If you can’t clean the oil off the glue surface, you might need to tack it in place with a headless brad or two.
Thanks for your suggestion. This piece is one a friend owns and as of yet I haven’t seen it up close. I will investigate and follow your suggestions. Perhaps a sharpened putty knife would scrape away old glue/teak oil residual. Getting behind it without cracking the strip my be the challenge.
If there’s glue on it, try to determine if it’s hide glue. If it is, you could just scrape off any loose bits, then use more hide glue (it will re-melt). If it’s not hide glue, or if you use other glue, you’ll need to remove all the old glue, or the new stuff might not stick. Without seeing it, I’m kind leaning toward headless brads!
Is there a woodworking skill you want to learn or develop?
I’d love to get better at trim carpentry. And I will have the opportunity…lots to trim out in the hall, still!
I acquired a couple of smallish, (a little bit bigger than a bowling ball) maple burls yesterday. I planned to seal the end where the chainsaw cut is to slow the drying. Any recommendations on controlled drying or reading material to help find a plan of attack?
Anchor Seal is, I’ve read, the answer. But I’ve known people to use latex paint and melted wax. I don’t know of a book that covers only this, but (and forgive the LAP promo) Richard Jones’ “Cut & Dried” covers that (and just about anything else wood-harvesting related that I can think of)/
I’m looking to get a second sliding bevel. I love the crucible one I have, but would like a longer one. Did I read somewhere in the blog you may be coming out with a longer one?
You did read that, but it has proven to be more of a challenge than we anticipated to hold that longer blade securely in the body. We’d have to do a whole new tool instead of a swapable blade. (It’s still on the back burner though – we haven’t tossed the idea.) I don’t know if you can find one right now…but a Vesper Tools 10″ or 7″ is what I’d look for.
I am considering adding a treadle lathe to my shop. Can you recommend any sources that I should consult? I see very little in the Lost Art Press on this subject. Is this something that you might have in the works?
A commercial one, or are you building a pole lathe? If a pole lathe: https://www.popularwoodworking.com/article/roy-underhills-double-spring-pole-lathe/ or https://www.woodspirithandcraft.com/blog/pole-lathe-plans (and Jarrod is working on a book for LAP, but I don’t know when it will be available). If an old Barnes or similar, though, I don’t know of a source specific to using it (but it’s not that different from an electric lathe…depending on how fast you can treadle!)
Ed Hobbs (https://www.footpoweredmachinery.com/) is a good source for info about old foot powered machines. He’s demonstrated at least one restored lathe at M-WTCA meetings.
What do you do with oil soaked rags when done finishing? I usually take mine and put in a ziploc filled with water, but often wonder if there is a better way (that doesn’t involve burning the shop down). Thanks!
We hang them out to dry for a few days. Once they’re rigid, they are safe to throw away. But another option is a fire-safe canister, such as this one: https://www.webstaurantstore.com/justrite-10-gallon-red-hands-free-oily-waste-can/8449300.html?utm_source=google&utm_medium=cpc&utm_campaign=GoogleShopping&gclid=CjwKCAjw6vyiBhB_EiwAQJRopvyXL2EyhjP2FECAy2aU7epMNxKkOvqzslgpEdzLN8ix_COqKENN9xoC3fgQAvD_BwE
I’m putting together a first aid kit for my workshop based on the LAP first aid book. My shop is in my basement. I would like to avoid duplicating first aid kits. My home first aid kit lives in the bathroom at the top of the basement stairs (very easy to get to from the shop). What components are ESSENTIAL to live in the shop and which ones can live in the main house first aid kit. Bandaids, tweezers, and antibiotic ointment are pretty obvious, but what about all the other stuff?
A tourniquet, I guess? Gauze pads? Anything you might need to keep the blood off the floor as you go up the stairs. Oh – and eye wash – the faster you can get stuff out of your eyes, the better. (I’m sure there are better answers that a doctor or other medical professional could offer.)
In the May 7 blog “Mechanical Library: Work Benches & Tool Chests”, you mentioned some piles of linden awaiting several future projects. Is this just basswood by another name or did you find some European lime / linden? If that is the case, where did you find it?
It is Tilia americana – aka basswood
The best place to order flat head screws that are not brass? Thanks Megan
blacksmithbolt.com
I’ve had good success ordering from fastenal. though you’re likely to get ss or zinc plated. i think they do sell some uncoated steel too.
Hey Megan,
The Anarchists Design Book,Expanded Edition Chapter 12: I am plotting a thin top Mughal trestle table in maple. It will likely be used for many things over the years and will definitely get exposed to moisture. Should the clenched nails be galvanized? I worry that over the years the wood will get stained from the nails.
Thanks.
Galvanized nails will still rust – just takes a bit longer. If it’s going to be exposed to lots of moisture, I’m guessing any rust stains will simply add to other character…which over the years, just about any table will acquire, whether or not it is exposed.
Cut and Dried or With the Grain? For someone who wants a better understanding of reading grain, wood movement, choosing the right boards for certain projects, etc?
WTG is more succinct – if you want just enough info to get back to using the wood, that’s the one. If you want to understand the science, C&D,
How do you pronounce “Anthe”?
an-thee
Good Morning Megan , I am interested in trying to build a guitar . Do you have any recommended books on the subject ? Thanks
I do not – I don’t know enough about lutherie to know what’s good or not. I’d ask Ben Strano on the FWW podcast – he has more experience with making instruments!
I haven’t built a guitar, but for classical and steel string building “Guitarmaking: Tradition and Technology” by Cumpiano and Natelson is often recommended.
You can find the errata here: https://www.cumpiano.com/gtt-updates–commentary
thanks !
Hi Megan,
If I’m remembering correctly, there was going to be a project of some sort involving all the pictures sent in for the Stick Chair merit badges; any updates you’re willing to share on what that might be or when we might see it?
Thanks!
I honestly don’t know! I think the need to find our own warehouse overtook that project in Chris’ mind. Once we have a working bathroom and certificate of occupancy at Anthe, I’m sure he’ll get back to it.
Any recommendations for woodworking schools or people who teach classes? In the US or UK. I’ve woodworked for 2 years as a hobby and hope to turn it into a profession. My first woodwork class will be with LAP in August and I’d like more exposure to in person lessons, whether it’s weekend or month long classes, next year.
Oh gosh – there are lots of good schools. It depends on what you’re wanting to build, I guess, and where you want to travel. Some personal favorites: Port Townsend School of Woodworking (Washington), Woodworking School at Pine Croft (Berea KY) and Florida School of Woodwork (Tampa).
A handful of others: in the Northeast, Connecticut Valley; in the Midwest, Marc Adams (IN); Texas, Austin School of Furniture. Upper Midwest (for green woodworking): North House…and many more that aren’t popping to mind. In England, The Windsor Workshop, The London School of Furniture Making, Rowden Atelier…
I hope others will chime in here, too!
In the San Francisco Bay Area, I attended evening woodworking classes at the Mt. Diablo Adult Education school. They have tons of cool woodworking as well as other classes (painting, jewelry, quilting, ball room dancing, etc). I would guess most major metropolitan centers have similar. Typically, the costs are minimal ($250 per quarter is what I paid) and the teaching is very good.
In the Northeast, add Al Breed, Dan Faia, North Bennet Street. Out west, College of the Redwoods.
You dovetail a lot. How often do you (or should you) have your saw sharpened?
I got down to Colonial Homestead last week, but sadly didn’t have time to see Yoder’s or Keim. I also had lunch at Der Dutchman — excellent boasted chicken. I wouldn’t have known about any of these places if not for you and Chris. Thanks.
Oh, well, I should have it sharpened more. But I have to send it out for that, and I hate to be without my baby. It’s very dull right now…so I got a second one to fit my hand, and will send my old one out. Now that I have two, probably every three years? But I’m mostly cutting softwood and soft hardwood – it doesn’t get much use in, say, oak. If it did, I’d likely have to have it sharpened more.
Colonial Homestead is a treasure.
Hi Megan, I’m a beginner ish hand tool woodworker. What is the best approach to small (1/4”) grooves in a box? I have nice chisels and a small shoulder plane, but curious if I need to invest in a plough plane or combination plane (Veritas)? Thank you!
It’s certainly easiest with a plough. If you’re going to be cutting a lot of grooves, it’s worth getting one (I think). If you’re only doing small work, maybe the Veritas Small Plow?
Thank you! Sounds like a worthwhile investment. (Money is not a driving factor). Quick follow up – for furniture (tables, beds, desks – all inspirational) – would you buy a Veritas combination or dedicated plow? I am right-handed, so I’d assume a righty…. Thank you for your clarity and concise response. The internet is totally confusing me with regards to this decision.
Hey Megan, I just stumbled upon this 3D printed tapered tenon jig. https://youtu.be/Hw-HcpFV6Qc In your opinion do you think these types of tools will get popular considering the low cost and ease on entry, or will the high cost metal versions still prevail?
I’m a terrible prognosticator; no idea really. But cheap always sells. It doesn’t always last.
Any upcoming classes on the art of saw blade painting?
Aren’t you funny.
I always look for them at flea markets and thrift stores. Your kitten/puppy clock on instagram was a good one.
Hi Megan, Happy Saturday! Does kiln dried rough lumber need to be stickered in the workshop? Or can it be stacked on itself assuming the bottom layer of wood is not in contact with the floor? Thanks so much.
With KD, I’ll make sure it’s not on the ground, but I don’t sticker the entire stack (but it doesn’t hurt). Once I surface it, yes – stickers.
What sort of finish did you put on the bathroom vanity you did a while back? Are you satisfied with it?
Three coats of wiping varnish. And so far, it’s holding up.
Hi Megan, I’m just gluing up my first stick chair (like right now! 🤯) and finding that the tapered tenons into the seat keep loosening up as I work my way around tapping (whacking!?) the legs in. When I did a dry fit they drove home and came to a satisfying halt when properly seated. It seems that the darn glue is lubricating the joint any words of wisdom please?
Many thanks, Paul
PS: see how I addressed the question to you this time 🤣
Hi Paul! I wish I had a more informed answer…I don’t build enough chairs to have experienced all the problems. But, I’ve seen that happen to Chris. You pretty much have to just keep hitting them until they seat (and not one hit more).
Perhaps a bigger hammer 😁. Here’s what I have done; I whacked the legs home, turned it over, sat on it, and drove the wedges in. I just need to be careful where it sit now as I have four splodges (word of the day!) of glue on my butt. Thanks Megan
I’ve had the same problem a couple times! I asked about this a few weeks back. Chris recommended to keep pounding until the glue sets up. Sometimes it can take up to 10 minutes he said. It happened to me once more so I just walked away for five minutes had a couple sips of coffee, went back, and pounded them home, and everything worked out great.
Paul, for what it’s worth, the same thing happened to me. This was the chair I made in Chris’ class last September. (Those of us who flew to class shipped our chairs home unassembled.) I just went around and kept tapping legs in until the hide glue set. Then I wedged them. I checked with Chris afterward and he said those joints should outlive us all. Good luck!
Hi Megan. Looking for a two-fer. (1) Does GoDrilla rhyme with the monster or is it pronounced some other way/? (2) Do you thin General Finishes “milk” paint before using it and if so roughly how much? I thinned by about 10% (the maximum, according to the can) but I still feel like I’m obscuring the wood texture too much.
Go – drill – ah (like gorilla or guerilla). I use GF “milk paint” full strength when brushing, thinned about 10 percent when spraying. It does obscure the grain far more than actual milk paint, but not as much as latex. If you want the grain to show, I’d try the real stuff. (Be prepared to be horrified by the first, and possibly second, coat)
The GF stuff sure is easier to deal with. I feel like an alchemist with the real thing; shaking, waiting, stirring, filtering, decanting, etc. all in search of that thin-but-saturated and bubble-free sweetness.
I can vouch for the horrified feeling for the first two coats of real milk paint. It started looking much better with following coats. Still, I questioned my life choices during those first two coats are had to have faith in the process.
Hi Megan, I’m thinking about making and selling some smaller woodworking projects, such as boxes. My reading of my homeowner’s insurance policy is that my workshop would be excluded from coverage if I’m using it for business purposes. The rates for business insurance for a woodworking shop are quite high and some home insurance companies don’t even offer it. Have you delved into that for your personal work? I assume LAP would be on a whole different level, with classes and safety. Thanks in advance.
I’m afraid I have not, really. At home, I’m a hobby woodworker, so my stuff is covered by my homeowner’s insurance. I have a rider on my personal tools that are at the LAP shop.
I had a long conversation with my insurance agent about this within the last 6 months. They will look at things such as tax records, postings on Etsy, Facebook Marketplace, internet, etc if you file a claim as a homeowner but are doing it as a business. If they find that out, then you aren’t covered. She didn’t have an exact cost for me but her thoughts were it wouldn’t be less than $500 or $1,000 per year.
Hi Megan, you mentioned that you would be filming a workbench video. What kind are you thinking of? The full-blown Roubo with mortise and tenon and impossible-looking dovetails at the tail vise, or something more simpler/faster to build with carriage bolts/hex head bolts and shortcuts?
The Anarchist’s Workbench. We already offer a Roubo workbench video!
Hi Megan,
Is the video for the Roubo bench you referenced, the one with Chris and Will Meyers?
Cheers
Yep!
Hi Megan,
A couple of weeks ago, I decided to give linseed oil paint a try. I ordered a couple of cans of Allback and used it to paint a bare concrete wall using brushes and a roller. Worked well.
Cleanup, on the other hand, was a complete mess. I learned quickly that soapy water was not the right solution for cleaning linseed oil paint from brushes.
Can you detail the cleanup process you use when using linseed oil paint? Thanks!
Try the Linseed Oil Soap from Allback. You can also use paint thinner then regular soap, but that kind of defeats the purpose of using a natural product anyway. Also, if you’re not going to use the brushes with other colours or other paints you can just leave them soaking in raw linseed oil.
Linseed oil soap. It’s magic! (But we also use cheap brushes…so we don’t feel bad if they don’t get all the way clean). https://www.leevalley.com/en-us/shop/tools/supplies/finishing/112235-allback-linseed-oil-soap?item=56Z1225&utm_source=free_google_shopping&utm_medium=organic&utm_campaign=shopping_feed&gclid=CjwKCAjw6vyiBhB_EiwAQJRoprFSxB5kcSqqNWzxH84EgbVMzZa0fV4RIuqu-PBgyqZ6QLzK2XBvthoCqIwQAvD_BwE
I’m unhappy with the company’s that have been sharpen my jointer knifes. Have you ever tried sharpening them by hand.
I’m afraid I haven’t. We have a helical head jointer, so we just turn the knives as needed…and put in a new one once each edge is toast. But ask again next week – Chris might have done that in the past.
There are some simple and elegant methods on the interweb. Some pure hand methods with whatever stones you have and a simple jig. And I am lucky enough to have acquired a makita wet sharpener back when the price was right. Made just for this. Though I use it for everything else. Can be messy.
If you do a lot of machine jointing, there are conversion helical drums for many models.
I bought an antique joiner’s tool chest, similar to an ATC. When sliding the tills back and forth, they sometimes wedge and get stuck — really stuck. Have you seen that problem?
My only theory is that the tills are too short, so they can twist out of alignment.
That seems likely – just like old drawers in any case piece. Try adding a strip of veneer where the tills contact the runners if there’s any l-to-r play (or just use uhmw tape – if it doesn’t offend you).
Have you made an anarchists toolchest with a trunk hasp and padlock?
Also, any tricks to reinforce the side handles so they can be used to lift the chest? Or is that impractical. Thanks!
Not an ATC, but I’ve made a lot of Dutch tool chests with a hasp and lock, No reason you couldn’t do that on an ATC.
I guess, If I needed those handles to be functional for lifting, I’d make the runner through which the bolts would poke a little thicker, so that there’s enough meat in them to house nuts for the lift bolts on the inside of the chest.
I have handles to carry my smaller tool chests. My full size ATC has none. It weighs 101 pounds empty. I have no idea what it weighs full. I figure if it can’t be lifted, I might as well not install any lifts.
Megan,
I’m wondering about the dimensions of the sort of stair step block that Chris uses while shaving sticks.
I’m not asking you to measure every little step on it.
I’m just looking for the approximate height at the back, and the depth.at the bottom.
That’s the Hulot block. There’s a measured drawing in “Ingenious Mechanicks” click for an image:
https://blog.lostartpress.com/wp-content/uploads/2023/05/IMG_2268-rotated.jpg
Hi Megan,
Little by little I’m making the furniture I want with classical construction and solid wood. My woodworking spirit animal is a turtle as at best I get two big pieces a year done and the list is long. My wife wants a big entertainment center for the family room. To help get it done in a reasonable time, I’m inclined to use cherry skinned plywood and dominos for the majority of the construction and covering up plywood edges with cherry. Part of me feels like I’m cheating but my wife has given me the ok to do this method of construction. Can you please help me Dear Abby resolve my internal conflict?
Sincerely,
Joe
Dear Joe,
That sounds like a perfect solution…and the same one I used on my vanity. Solid wood for the legs and face frame; cherry ply for the panels. All Dominoed together.
Hi Megan – please forgive my additional follow-up question:
From your earlier response, if a plow plane sounds like a worthwhile investment to cut many grooves and I’d plan to do more than boxes – (Money is not a driving factor) for furniture (tables, beds, desks – all inspirational) – would you buy a Veritas combination or dedicated plow? I am right-handed, so I’d assume a righty…. Thank you for your clarity and concise response. The internet is totally confusing me with regards to this decision.
I gotta tell you…we have the combination plane, and have never used it for anything but cutting grooves. So I’d get a dedicated plow. Less money, less fuss. (And yes – as you’re right-handed, the RH version)
If all you are going to do is small grooves, the new Lee Valley box-makers plow would be perfect. It’s a copy of the old Record 043.
I noticed in pictures of the new building there’s a large A no doubt because it’s the Anthe building. I’m just wondering if there’s any plans to modify that to look more like your divider logo?
Very exciting times ahead for all.
Possibly! But it’s not near the top of the list. (Also, we’re more likely to add an L and a P on either side than to modify the A…I think.)
My attempts at drawboring keep splintering out the backside. Any suggestions? Tom Jones. Santa Fe, New Mexico
Hmm…more of a point on the drawbore pin? Slightly less offset?
Thanks. I’ll try it
I made my first workbench legs with drawbored tenons though SYP. Offset a 3/8 oak peg and ‘reamed’ it with a drift pen. Drove the pegs home. Half went correct, half took the road less traveled and just came out the other side of the leg at an unusual angle.
That was 7 years ago and the bench gets at least weekly abuse. They are all still tight. I say this only to offer that even if they don’t look nice they will probably last many years.
What was the metal part on the pencil marking gauge (from Chris)?
It looks similar to the line splitter shown in MACFAT…..
If I’m understanding the question correctly, that’s simply a pointy pin so you can use the other end for scribing a line rather then penciling it
Sorry for being unclear. There was a post about a pencil gauge, where Chris’s version has two parallel dowels, but this version (gift fro Chris?) had some metal piece instead. What was that metal piece screwed to fence of gauge…
Ah – I think you might be referring to something like a “Double Line Hose Clamp” – screwed to the head, it takes the place of dowels to allow the gauge to work around curves.
Hi Megan! Thanks to you and Chris for answering my question about mixing woods last week. And my apologies to Chris if asking a question about aesthetics like that sparked a nerve.
Actual question: any tips for where to shop for affordable but still decent-looking hardware for the drop-front desk I’m currently building?
The definition of “affordable” can differ enormously, so I’m a bit wary of answering. But my first stop would be Horton Brasses. It’s not inexpensive, but it’s very well made, and not outrageously priced. Salvage is another good option if you have a good architectural salvage place in your neck of the woods.
Firstly…this is an excellent concept.
question: is there an efficient method of making sliding dovetails by hand? Vintage tools include a Stanley 444…but not sure if there’s anything more accessible.
Thanks kindly.
The fastest way I know is to cut the tail, transfer the shape to the batten (or case, or whatever) saw the sides down to the baseline, bash out most of the waste with the widest chisel that will fit, then get to the final depth and into the corners with a router plane.
I’ve never used a DT plane.
Also, check out this article from Frank Strazza (who cuts crazy-tight and perfect joints) https://www.popularwoodworking.com/techniques/tapered-sliding-dovetails-3/
Hi Megan, I carve a little, but definitely not a professional. I just like to carve accents on the furniture that I make. Do you carve?
I’ve done a very little bit of Follansbee-style carving, and that’s about it.
Hi Megan,
If you had to choose between the Dutch Tool Chest or the Anarchist’s Tool Chest to have build and teach for the rest of your time which would it be and why?
Jeremy
Anarchist’s; it pays better (’cause it’s a longer class) and they sell better. Gotta feed the cat! (But students learn more techniques in the DTC class.)