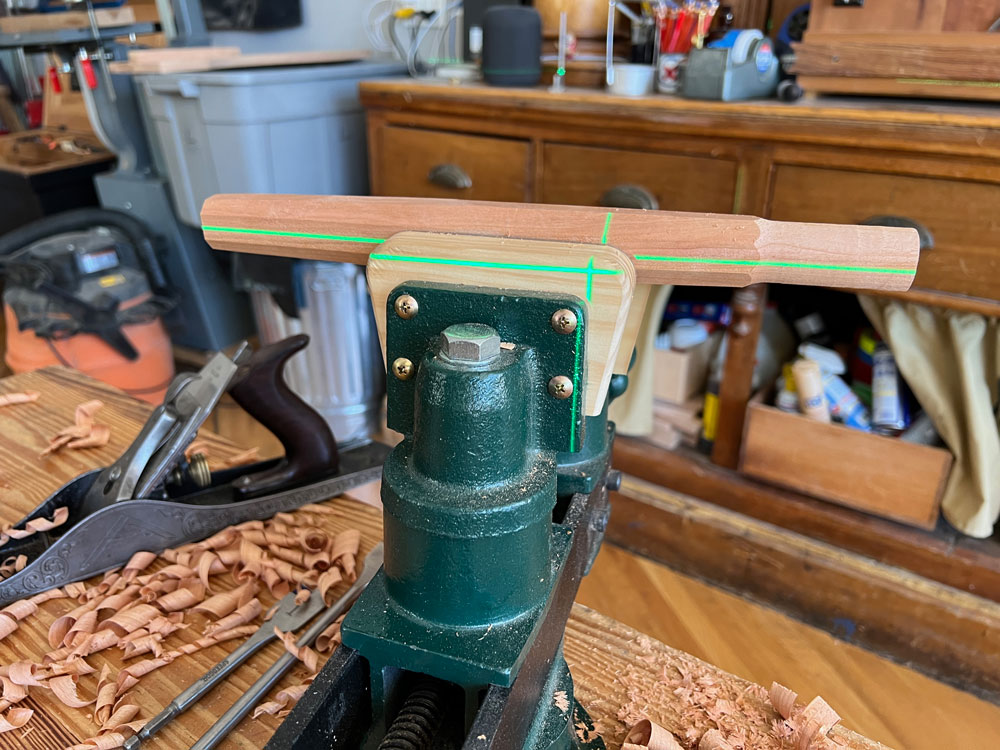
Welcome to the LAP Open Wire, where we endeavor to answer your questions about woodworking – plus our tools, books and apparel.
Here’s how it works: Type your question in the comment field. I will do my best to answer it. It is that easy.
Before you ask a question, please read this.
- If you could limit the number of questions you ask to one or two, my fingers might not catch fire. And remember brevity is appreciated.
- If your question is your first comment here, it will automatically be flagged for moderation. Your question will appear after I approve it.
So here we go…. Note that comments for this entry will close about 5 p.m. Eastern.
— Christopher Schwarz
Hi Chris. You mentioned in a previous open wire that if one had a dovetail saw a suitable second saw would be a tenon saw. Did you mean rip cut or x-cut? Thank you.
Rip. So you can cut tenon cheeks quickly. And, with a V-trench made with a chisel, cut the shoulders.
Sorry for the probably frequently asked question. The type of clamp you advocate for in The Anarchist’s Workbench is a type I’ve never seen on the (pitiful) used market here in Finland, and just once as a new model of dubious quality. I’d be happy to laminate the top in several parts though, so can probably manage with less clamping power. I’ve got a bunch of reasonable-to-good quality parallel clamps and F clamps. Any pitfalls there I should consider?
Also, do you know of a good way to roughly measure the power of a clamp without expensive specialist equipment?
Thanks, and good luck with the new place!
I don’t know an easy way to measure clamp pressure. I just know that parallel-jaw clamps and F-styles are usually not enough for a multi-board lamination of a benchtop.
Suggestions: 1. Can you get pipe clamps there?
https://www.leevalley.com/en-us/shop/tools/hand-tools/clamps/pipe/59405-bessey-h-pipe-clamp?item=17F0615&utm_source=free_google_shopping&utm_medium=organic&utm_campaign=shopping_feed&gclid=Cj0KCQjw9deiBhC1ARIsAHLjR2Dx7MGQgq9X9FvnHXaLDsbvYgYfAK1t8iS1xs3mIWr1uVNi0D9tps0aAgNFEALw_wcB
These will usually do the job without slipping.
Can confirm that pipe clamps work well for a thick benchtop lamination. Get as many as you can.
Hi JK,
You will, I’m sure, get a better answer from Chris on clamps, but I just wanted to say I was in a similar situation, clamp-wise, when I glued up the top of my workbench back in 2021.
I used as many parallel clamps as could lay my hand on (24 in total), and did just one glue joint at a time, but with most of the other laminates in place, primarily to act as a caul but also to make sure that any imperfections in individual joints would be fixed in relation to the (almost) full set, and thus avoid errors gradually accumulating, as they might have done had I done just two laminates at a time.
If you don’t mind it being in Swedish, you can find a detailed description of how I went about it in the build log I wrote at the time, with the glue-up prep starting from this point in the proceedings, and the actual glue-up described as from here.
Cheers,
Mattias
There is a Swedish made clamp called Alex (don’t ask me why). It has a steel bar and a offset handle. I haven’t tried them but they look allt like the old fashioned ones you can find. https://planomaskin.se/sv/tvingar/limknekt-1000mm.html is one of the retailers. There are others as well.
Dictum and Fine tools in germany sells pipe clamps. Shipping to Finland should be reasonable.
Hi Chris, thanks for doing this! I have a big, beautiful 12.5in wide beech slab I’m using for a low bench. The floor in my shop is super uneven and I’m wondering what your thoughts are of going a doing a three legged bench so that it won’t rock. If you don’t think this is a terrible idea, would you put the two legs towards the “front,” like a shave horse? I’ll be moving it around so the other alternative is simply to shim a leg to stabilize it when I move it to a new spot. Thanks again!
Great idea. I don’t know which way would be the ideal “front.” My guess would be toward the single leg. If it were me, I would assemble the bench, then mock up a stop at either end and give it a try before cutting mortises and peg holes.
Are you keeping the line shaft? Plan to use it? Relocate/new motor for the elevator?
The line shaft stays. It has been well cared for, and removing it would be a crime.
Our elevator repair company has done preliminary evaluations of our unit, but we haven’t gotten past that.
Do you have an ETA for Stick Chair Journal No. 2? (Or is it being preempted by Dawn Degreaser Journal No. 1?) Thanks, and congrats on the new space!
I am working on it in my spare time…. I am determined to get it out this year. Several of the stories have been written. I am mostly waffling on which chair to build for it.
I built the Moxon vise I asked about a few weeks ago. (I used SYP). I find that in use, no matter how hard I try to tighten both sides evenly, and no matter how tight I tighten it, whatever I’m holding in it has a tendency to rock or rotate to one side or the other as I work the piece. Would lining one or both of the chop faces with something help hold things more securely? Got any of that leather skirt left that you used on the Moxon you showed Roy?
Leather or Crubber would help. But I would investigate first if the jaws are warped, cupped (across their width), bowed or in wind. We don’t have any Moxon vises that require leather or Crubber. But the jaws are dead flat.
Will check that. Thanks!!
What is the brand/source of the dividers used to scribe the circular patterns that you used with Peter Ross’s inserts?
Starrett. They are widely available on eBay and through Starrett.
Hey Chris – I’ve been having trouble with my 5/8″ wood owl auger bit. It has decided to moonlight as a splitting maul. I’ve lost a couple of stool seats to it, though I admit that the seats were on the thin side. It feels like the lead screw is pulling the auger bit ahead faster than it can properly cut. I’ve switched over to a regular wood-owl bit, but I don’t like that as much because it isn’t a consistent diameter, which makes it harder to eyeball resultant angles. I’m thinking of filing down the threads on the lead screw of the auger bit…is that nuts? Congrats on the new building by the way.
Hi Sam! I have never encountered anything like this. Without seeing the bit, I would guess that the cutting lip was not sharp. So the worm pulls a dull flat into the work….and split.
I would return it and get another. You need the threads on the worm to propel the bit through the work. Otherwise, only your weight/strength has to do it. And with a 1″ bit….. that would be a lot.
I think I’m confused. Wood Owl makes “regular” large diameter bits with a brad point. (I think they call them ‘overdrive’ bits.) And we all use big honking forstner bits that don’t have a worm (though we usually do it in a drill press). So when is a worm critical?
It’s all about the bit’s cutting geometry. Modern CNC mills and the like can make bits (like the Overdrives) that don’t require a worm. But there are downsides to these bits (they cut to the sides of your hole). Spades rely on speed and rapid chip clearance to work. The answer is a book, not a blog comment I’m afraid.
I have been making a pilot hole around ⅛” (or even bigger) for my wood owl bits. It helps me guide the bit and reduce splitting but it doesn’t seem to have any affect on how the lead screw pulls the bit though the wood.
Favorite way to attach a table top or top to a structure, figure 8 fasteners or wooden buttons?
Has sports shaped your live in any way? Fav sports teams?
Buttons. Or nails down through the top if the project calls for it.
On sports: I liked playing as a kid. But I have never understood watching it. The same way I don’t understand gambling. My brain is broken on these topics. I have enough competition and stress in my life from running a business, so watching sports seems like it might give me a panic attack.
I weird.
I have wondered about this question for months – but never looked closely enough to come across buttons as an option. This is perfect – thank you for posing the question I didn’t know to ask!
I’m really fascinated by the symbols in American Peasant. Doing some research has been fun. My question is where did you get your book Acsolt Ladak Titkai? I have ordered Latvju Raksti and some others but cannot find that one. If you don’t already know about it check out symbolikon.com. Thank you
Tamas sent two copies to Peter. Peter sent one of his copies to me. You might reach to Tamas directly (if you haven’t already).
And I have NOT seen symbolikon….. wild.
What other brands of blades or chisels do you use your Lie-Nielsen honing guide on (couple of examples)? Any tools you have that they absolutely won’t work on (an instance or two)? Thanks, Chris!
Almost all bevel edge chisels and plane blades and spokeshave blades work in the Lie-Nielsen, regardless of brand or era they were made. I end up sharpening lots of student chisels and cannot remember any problems. I also manage to get most mortising chisels in there, with a little fiddling.
It doesn’t work with swan-neck chisels and short-bladed Japanese chisels. But those are exotics in my world.
So you’re able to get your Ray Iles mortising chisels in the guide (with the mortise chisel attachment)? Or thinner chisels (like say modern Narex Richter or Ashley Iles)? That’s great. Thanks!
I have been able to fit my 5/16″ Ray Iles mortising chisel in the LN guide with mortise jaws — this was to hone a secondary bevel. If I remember correctly, it was close, and I don’t think it would fit to re-establish the primary bevel.
I have the same chisels. I put them on the bars of the guide and clamp the chisel between the guide’s flat part of the jaws. You need a different angle-setting than using the dovetailed notch, but so what?
What is your experience with Rubio minocoat finish?
I experimented with it a bit. I prefer simpler finishes. But I know lots of people love it.
I am looking at projects in the Stick Chair Book and the Design Book, which use both tapered and non-tapered mortice and tenons. For the tapered mortice and tenons, the tools are the Veritas tapered tenon cutter that comes in five sizes and the Standard tapered reamer, small and large. For round tenons, I am considering the Power tenon cutter, that comes in eight sizes and would be matched to a wood owl bit of the same size.
The question is: What is the most versatile combination of sizes for tapered and non-tapered joints for projects mentioned in the books above? I would prefer to have a smaller took kit that is highly functional, although more than one size of each is easily doable.
BTW, I did recently borrow a 1” power round tenon cutter and bit from a reputable chair maker in the Cincinnati area for a three-legged stool. It worked out fine, but I returned it after I was done.
For vernacular chairs and stools with no tapered joints.
Mortises: 5/8″ spade, 3/4″ spade and 1″ auger
Tenons: 5/8″, 3/4″ and 1″ power tenon cutters.
For chairs with tapered joints
Mortises: 5/8″ auger, 5/8″ spade, 3/4″ spade, tapered reamer
Tenons: 5/8″ and 3/4″ power tenon cutter. 5/8″ tapered tenon cutter
Chris, your energy and capacity for getting things done (one-of-a-kind furniture, videos, books, crucible tools, the blog, classes, the new building, operations) is an inspiration for me. I wonder when you sleep… OK, my last (probably) saw question: what is your opinion on hybrid cut saws (halfway between rip and x-cut)? Money saver or poor compromise? Thank you!
They have their fans. I prefer a rip saw that has been hand-filed. It will have some fleam and will be fine for most crosscuts, especially if you knife in the line and make a little trench with a chisel for joints that will show.
Hey Chris, I want to build a version of the Irish chair from the Stick Chair Book for my four year old niece. Ideally, I’d like to scale the chair down to size for her, and I think about a one half scale would be about right.
My question, for stick chairs, is scaling them down as simple as reducing all of the dimensions by half? Do I need keep anything closer to regular size, like the tensons for example?
Thanks as always for taking the time!
I’ve never built a child’s chair. There are plans out there for child’s Windsors. I’d buy one and study how they scaled the joints and geometry.
Half-scale chairs are fun to make but they not ideal for children over 3 years old. Most historical examples are three-fifths to two-thirds scale. Modern plans are in two-thirds. This scale will serve children to about 9-10 years old.
To scale the stick chair is really is as simple as multiplying by .6 or .66 and then using judgement to adjust. For example: if your calculations give 12-3/4” for length, making them 13” isn’t going to matter. A final seat height of 9-1/2” works well. 1/2” joinery for legs and stretchers. Spindles (back sticks) are usually 3/8” in the seat and 5/16” in the crest. Hope this helps.
Thank you, Travis.
I did exactly this for my nearly 3 yo daughter earlier this year. We built the Irish-y chair at 3/4 scale and it’s a bit big (she’s tall) but the design makes it comfortable and stable, even though her feet don’t reach the floor yet. Great for getting cozy with a book. We scaled all the components and joinery the same, rounding up a little here and there to match the tools on hand. I’ve also built an Anarchist Design book three leg backstool and staked chair at .6 scale. Also a great size for my toddler but it’s really remarkable how much smaller .6 is than 3/4. I LOVE making kids chairs and highly recommend it. It makes for quick and easy experimentation. And the kiddo likes pounding in sticks. Cheers.
Morning, I am away from my bandsaw for the summer. Can you recommend the second best way to cut out a 3 to 6 inch tall curved comb/backrest. I’ve never used a bow saw before. Would that be the ticket?
Thanks a lot!
The originals were cut with a band saw. I have seen the marks. This is just FYI to ward off people who think what I am about to describe is “traditional.”
Shape each lam separately before gluing up. Shape the outside curve with a drawknife. The inside curve: crosscut kerfs near the layout line. Spit off the water with a chisel. Clean up with a half-round rasp.
Glue it up and then clean it up.
I have seen much written about planes including blades, soles, mouth widths and all kinds of geometry about angles, but the only thing I’ve seen written about chip breakers is to make sure it is bedded down on the blade. Nothing about the height of arc or diameter of arc nor width of flat area doing the bedding down.
Comments?
Consider yourself lucky you haven’t encountered the Chipbreaker Rabbit Hole. Because it is a THING.
You can find plenty of it on the forums (Reddit, WoodNet etc.). I refuse to engage in that sort of pseudo-science naval gazing.
Here’s what I do: On all planes except smoothers, I bring the breaker back about 1/16″ from the edge or whatever is required to avoid the curve of the cutting edge. The breaker is just a blade stiffener for these planes and engages the adjustment controls. The edge of the breaker is unmodified. Sharp or flat edge. Whatever. Don’t matter.
On smoothers for difficult woods, I bring it about 5 thou behind the blade. My breaker is curved about the same amount as my iron. You can have a flat or a sharp edge. Both work. I prefer a flat. All this makes the tool much more difficult to push, but the results speak for themselves.
But don’t trust me. Try different settings and see what you like.
Hi Chris,
I’m curious…do you own a big poofy recliner chair like a lazy boy? I have no doubt your chairs are comfortable, but those can be nice after a day of work.
Also, (if I may) any post on the Anthe Building gets lots of comments on the possibility of lead paint or lead dust from the letterpress operation. I’m sure as a staunch supporter of “finishes that won’t kill you” you’ve done your due diligence on this. Could you address that briefly?
Thank you,
Ben
Ben,
No, I don’t own a poofy chair. They are pretty darn ugly to me. We have a leather couch, which is pretty firm. That’s where I read and watch TV in the evenings with Lucy.
On lead: Of course there is lead in this building. Lead paint, for sure. But it is intact and not peeling. So the plan is to leave it for now. The print shop was on the second floor, which we have not investigated for lead. We assume there is. And we will take proper steps to remediate it.
Thank you for the reply! If hobbits can sit in wooden chairs till their old age perhaps so can we. I just don’t have any comfortable ones…yet. Good luck on the building I’m excited to see it.
Chris, I am making African mahogany garden gate doors (30” x 66”) to fit between two stone pillars. What would you finish this set of doors with assuming protection from elements is desired and maintenance recoating is relatively hassle free. Thanks
Geoff
Straight linseed oil is traditional. As is paint. You can also investigate semi-transparent and opaque deck stains.
Avoid film finishes unless you want to spend money on the marine-grade varnishes with UV inhibitors.
What would be your approach to chair making if you didn’t have a good reputable Hardwood dealer local. I’m currently working with wood I can get from the local big box store (menards) finding wood with straight grain sounds nearly impossible right now.
Great question. Sorry I didn’t see it earlier today.
Legs: Firewood from the gas station. Split them out.
Sticks: Straight-grain oak dowels from the home center
Seat: Whatever 2x material you can get from the home center.
Arms: Whatever 1x material you can get from the home center
Comb: Cut from 2x material
For your painted furniture pieces you (and Megan) have such crisp lines between the exterior, painted, surface and the interior, bare, surface. Do you use tape? Or are you coming in with a scraper or abrasive after painting? Is there a timeline to follow for milk paint for this process?
Thanks!
I tape off the edges (Frogtape is the most reliable IMO), and if a little paint does get under the tape, I’ll plane it off if possible, or scrape it if a block plane can’t get to it. I wait until the paint is completely dry before removing any oopsies, however I go about it. (So for milk paint, overnight at least.)
Hi Chris,
I am soon going to visit Ed Lebetkin’s store for the first time. Any recommendations for what I might prioritize while perusing, given I already have most tools from the ATC? I typically build things from the ADB, including stick chairs.
And a quick #2, if possible: I’m currently using a Fray brace with an adapter for hex shanks. It’s not ideal. Do you recommend retiring that when using WoodOwl bits, etc.?
Thanks for all this.
Ed’s place is a wonderland. At my point in life (and yours), I look for upgrading existing tools. Can I find a better awl? Hammer? etc.
If you want to use modern-shanked bits, you should investigate the brace’s with three-jawed chucks. Lee Valley sells a French one that is pretty nice (except for the plastic handles) that I use.
Smearing hide glue all over the clamped dovetail joint? Hi Chris- I’ve noticed in several pictures in IG and possibly here on your site the practice of really covering the clamped joinery in glue. Is this a practice you encourage? I can only assume its to help everything swell and be tight but it seems like something I try to avoid in every single other glue application. Thoughts?
David Savage showed me this technique. It works. The excess is planed off after it dries. Hide glue is transparent to most finishes so it works well. I’ve done it a few times and am impressed.
Any experience or advice on building a stick settee (approx. 48in wide)? Larger tenon/mortise? Six legs instead of four? I have some walnut that could work–hoping that’s strong enough. Thanks for all you do!
I’ve never built one. It’s on my list to do. I have about four or five designs kicking around.
Chris Williams and John Brown built these (there are a couple shown in Chris’s book). Basically, they stretched a chair out.
Chris, thank you for hosting this. I want to build my first stick chair from the stick chair book, but I only have 2x doug fir from the home center on hand. Can this work for a first chair, or should I try to find some 8/4 hardwood from a lumberyard first? Thanks again.
It should be fine as long as the grain is dead straight. You might size up the structural members (legs, stretchers and sticks) up 1/8″ in size.
I’m building a split-top Roubo style workbench incorporating design features from 4 different plans, 3 of which are yours. I want to use a rigid trestle style leg frame with a leg top tenon and blind mortise in the top. What are the best dimensions for the M & T joinery, and how do I account for seasonal wood movement in the top?
The dimensions I used for tenon are in the Anarchist’s Workbench, which is a free download. To account for seasonal movement, I make the front mortises tight. For the mortises at the back, I make them loose to allow the movement. Pegs through the mortise and tenon keep everything firm to the base. I believe all this is in Anarchist Workbench as well.
Caveat: I have never built a split-top bench.
Hi Chris, congratulations on your new building, I hope all progresses as planned. I am currently working on a pulpit for my son who pastors in Michigan.(I live in Alabama). I am using walnut for the build and it will be just a little larger than a music stand. I am relief carving a cross in the front board. My question is this, I am planning to mix up basically a Maloof oil finish without using his second finish which was an oil/wax finish. Planning on 3-4 coats but whatever is needed. Have you ever used that finish on walnut and if so how did it turn out?
I too am weird in that I don’t watch sports of any kind. I like books. You are not alone.
Someone else will have to chime in here I think. I have in my head it is a wiping varnish (oil with a poly). Wiping varnishes look great on walnut in my experience.
His finish was 1/3 tung oil, 1/3 BLO and 1/3 spar varnish, today it would be a spar urathene. So yes it is a wiping varnish.
There was a question I caught after comments had closed about “middles” as women’s clothing that a previous Anthe tenant was hiring seamstresses for last week. I strongly suspect it’s a typo for “middies”, a type of blouse that most folks today would call a sailor shirt, pix at https://genealogylady.net/2015/08/23/fashion-moments-middy-blouse/ I can’t recall them being popular since the ’70’s.
I am curious about the floor cleanup pictures in the May 1 post on the Anthe building. It looks like some kind of black sheeting was scraped up and possibly some 4×8′ underlayment? I am after details because that seems to be what is under the early ’60’s 9″ tile in my 1880 farmhouse.
How did you scrape it? If there was underlayment, how did you pull it up without ruining the floor underneath?
Thank You!
I don’t know how they pulled that up. That was in the storefront and happened while I was off-site. I will ask.
Can the soft wax recipe be used with polymerized linseed oil instead of raw? I accidentally bought way too much.
Probably. But I’d try a test batch.
Hey Chris, Since you put it up there what is your procedure for using the laser level and the Lee Valley tenoned thingies? Asking for a friend
The laser level is set to “self leveling” mode. I level the stick to the laser line in the vise. Then I use the bubble level in the tenon cutter and the laser line to guide me as I cut.
Hi Chris (and Megan, who seems to be lurking too)! Purely aesthetic question here: do either of you have favorite combinations or pairings of woods that you use when making furniture? I’m just starting down the path of mixing woods for contrast and am curious about your experiences with that. FWIW, I aim for just just a bit of mixing to give some “pop” to my otherwise fairly simple pieces.
I am always lurking.
I’m pretty basic…I use secondary woods where they don’t show (drawer sides, e.g.). I mostly just use one species on display, and most often, it’s cherry or walnut. The one time I’ve mixed wood is on a cabinet I built for PWM – walnut with spalted maple panels. It’s still in my living room, and looks nothing like anything else I’ve made.
Thanks! Much appreciated.
Note: Every word below reflects my aesthetics, which are generally historical and vernacular.
Mixed species are very common. But not for visual contrast. Instead, species are mixed for the woods’ other characteristics (strength, price, workability). Or – and this is important – it is what you have on hand. Many times these pieces are unified by paint. Or by age, as many woods end up as a medium brown after decades.
In high-style pieces, mixed species are generally used with restraint, and for punctuation. Example: satinwood gallery drawers in a walnut secretary.
When I design furniture, I am not looking for contrast. I am after harmony, both in form and in color.
I think the way people mix species today (e.g. a walnut racing stripe in a maple tabletop) is unappealing. And when you start mixing species and everything is figured, I cannot see the piece of furniture behind all that visual mess.
Yes, some people do this well (Garrett Hack), but they are the exception.
If I have offended anyone here, I apologize. I generally try to keep this sort of aesthetic judgment out of the blog.
My office is all cherry for horizontal parts and hickory for sticks and legs. Currently making some chairs that are all red oak. I cannot BELIEVE how much easier oak sticks are. I don’t ever want to see hickory again.
Thanks! I appreciate your perspective. I think the notion of “punctuation” is what I aim for. Not to distract from the whole, but to accent. That said, different strokes, etc.
Good Afternoon! Can you suggest a rule of thumb for sizing drawbore pins? I don’t have a ton of access to antique pieces. Is it close to the width of the tenon or something like that to the nearest whatever size hole I have in my dowel plate?
I don’t know of any rule of thumb, but the one you suggest is a pretty good one – as long as the tenon is sufficiently long (typical is 5x the tenon thickness).
I’ve seen Yankee drills and drivers too often to not be curious about them, but I don’t think I’ve seen much about them in LAP or other resources I tend to consult. Do you, Megan, or any other known associates make use of these, and/or have a strong opinion on them?
Also, as a New England transplant from the Ohio River Valley I can’t help wondering about the etymology — of all tools, this is the one Stanley marketers bestowed with a name that does them no favors in a massive chunk of the country?
The inventor of the “Yankee” screwdriver Seems to be a Zachary T. Furbish of Augusta, Maine, who patented the design, which was manufactured by the Forest City Screwdriver Co. or Portland Maine.
North
The North Brothers Manufacturing Company in Philadelphia purchased the Forest City Screwdriver Co., and Furbish went on to work for North Brothers, and his later patents were assigned to them.
North Brothers manufactured all sorts of items, but with the addition of Furbish, tools were a main line of product.
The North Brothers Manufacturing Company used “Yankee” for the various screwdrivers and drills they manufactured, maybe because Furbish was from Maine and hence a “Yankee”.
Stanley Tools purchased North Brothers in 1946, and kept the Yankee name for 50+ years.
I think they may have sold the Yankee trademark during the past decade or do to Schroeder Tools of Germany, who were manufacturing the spiral ratcheting screwdrivers for companies like Sears.
Hi Eli,
I had my grandfather’s Yankee. It works fine. And it is good especially for installing passagway doors. But for woodworking…. I clock my screws so I’m too fussy for the tool.
I live on the gulf coast, between Houston & Galveston, TX. To say that the environment is humid is an understatement. I work in my two car garage – no climate control. I have most of my planes & saws stored inside and smaller things are oiled and stored carefully and kept in the garage. I would like to build something to have everything in one place – ATC or wall cabinet – but I need to countermand swamp I live in. Do you, Ms. Fitz, or anyone else for that matter, have any experience with Golden Rod type heaters that are typically used in a gun safe? I spend a lot of time with rust erasers and oil as it is – trying to find a workable solution…
We don’t need Goldenrods here. But I do know that some people swear by them. As a first step, you might try stringing christmas lights in your chest. They will reduce the humidity. Honestly, the answer for most garage shops is a mini-split. It solves many wood-movement problems, too.
I’ve installed a few Goldenrods in custom tool chests I’ve built. But I don’t want to work in a space that doesn’t also keep me warm/dry and cool/dry …so I have no personal experience with their efficacy in use.
Have you tried putting a VCI capsule (eg Zerust brand) in your toolboxes or wrapping your tools in VCI paper? I don’t have any experience with using VCI products but they seem popular for preventing rust on tools
Hi Chris,
Looking at the sliding dovetails to attach battens to the underside of a tabletop or desktop, it seems like they would need to be cut using a table saw.
I don’t own one. I’m sure I could do a decent job on the battens but the other half of the joint has me puzzled.
Also, what are buttons? The only reference I have found is for upholstery.
Thank you for your time.
Hi Ray,
I cut my sliding dovetail sockets with a handsaw, a chisel and a router plane. Make the battens first and you can use the battens as a sawing guide so you nail the angle of the joint.
On table buttons: https://www.popularwoodworking.com/editors-blog/attaching-a-table-top-with-traditional-wooden-buttons/
Hi Chris,
Thanks for doing this. I found a YouTube channel called Peasant Art Craft. I think you’d like it for all kinds of reasons (simple tools, authentic woodworking, Roman style woodworking, etc). Watched an older gentleman make a pickle barrel. https://youtu.be/jIc6dW-Tbsg
I need to move a 400 lb bandsaw (Powermatic PM1500) off of the shipping pallet and onto it’s moving stand. I don’t want to muscle it. It has an eye hook on top. Do you think using a 1 ton harbor freight chain hoist, suspended above on a metallic tri pod stand with female receptacles for three 3/4″ galvanized 10 foot long pipes (kind you use for pipe clamps) would be a safe way to do it. It only needs to raise a few inches to slide off pallet and then slide under the Rockler all terrain mobile base. At no point would I put body parts directly underneath the suspended bandsaw.
Sincerely,
Joe
Joe – I rented a knock-down engine hoist to lift my jointer and thickness planer on to rollers. I rented from Cresco in Danville; a Cresco location closer to you probably has the same/similar hoist. I believe the hoist has sufficient reach to accommodate your band saw; Cresco could confirm that.
Thanks Joe H. I will call them to find out. I suspect the bandsaw eye hook is too tall for an engine hoist but worth looking into.
Likely Joe you are right. The hook will be too high for an engine hoist. When I get in a weird spot like this, we call riggers or professional movers. It might take them 20 or 30 minutes to do the job, but no one gets hurt. And the bill is less than what I’d pay to the doctor.
Band saws are hard to move off trucks. I have done my share.
Why does the Anarchist’s Workbench have a lower price than the other Anarchist books? Lower production costs, higher sales volume (so you can have more economy of scale), something else?
Because of the nature of this particular book we take very little profit on the book. Basically, we consider the content as free (it is free on the website). So what you are paying for is the cost to produce, store and sell to customers.
I have seen pictures and labels in some of your postings on a small shepherd’s coffer. Any information on why they’re created, why you built one, any general dimensions?
That’s on my Substack, The American Peasant, and will eventually be in the book. You can sign up for a free trial to get the cutlist and other info. https://christopherschwarz.substack.com/p/plans-and-cutting-list-for-the-shepherds
Hi Chris. Long time listener, first time caller.
I’m having spokeshave problems. I pick up the Veritas flat bottom one for the classroom, but I can’t seem to get the results I want. Very VERY rarely, I can get the nice curls like from a plane, but more often it jumps and skitters on the workpiece, leaves a splintery mess, and clogs up almost immediately. I have tried skewing the spokeshave on the workpiece, skewing the blade on the spokeshaves, going with and against the grain, blade settings big and small, changing the amount of pressure I put on the tool…basically the only thing I can think of next is filing the mouth open more, but I don’t want to do something that drastic before seeking professional help. Since I can’t figure it out, the students don’t want to even touch it.
What am I doing wrong and how can I get good? Thanks.
Hi Don,
It’s impossible to diagnose without lots more data. What kind of spokeshave? What kind of wood?
With cheap shaves, there is no good bedding surface, so the cut is inconsistent and there is chattering. Firm bedding is important. Also, the tightness of the blade’s cap. It has to be pretty tight. And light shavings in dried hardwood. Send me a photo of what you got and I’ll see if I can help.
Question about finishing.
Context: I’m building the bookcase from ADB in white oak and want to paint the sides as you’ve done.
Will garnet shellac (tiger flakes) under Tuscan Red milk paint (general finishes) create a deeper, richer finish or should I skip the shellac? Was also thinking of putting black bison wax over the paint as I’ve seen you do on your chairs to great effect. Thanks!
Unless there’s a sap issue (or other smell/exudation) that needs blocking, shellac will have little effect. It might make it slightly easier to apply the first coat of acrylic, but not enough to make it worthwhile.
One more question, do you think had the domino jointer existed during the height of the campaign furniture era it would have been used instead of full blinds for campaign dressers?
I’m saving up for good brasses right now and can’t decide if I should domino the case joinery and only do handcut DTs for the drawers.
I’m not one to guess what dead people would do.
The dovetails and brasses were there to hold the case together if the glue was washed away or eaten by bugs in hot climates. So a mortise-and-tenon joint would not be a good idea for that type of environment (without pegging or other mechanical assistance).
But for a piece that will stay in a home in a temperate environment…. a Domino is a fine choice. I have made a couple campaign chests this way for customers who wanted to save $2,000 or so.
One of the central themes in the Anarchist series seems to be pursuing craft and producing for yourself. A decent section is devoted to self constructing a home. However, tools for general carpentry and the subject at large is quite spare in your writing.
Why is that?
Thanks for your time and your dedication to handcraft.
I’m not a carpenter. I’m a DIYer when it comes to framing and all that stuff. So I’m not in any way qualified to write about how-to with carpentry. But I manage it.
Has the Hi-Vise replaced your Moxon? Does it work well for dovetails or only chair parts? Thanks!
I still use the Moxon for dovetails. Tghe HiVise is ideal for shaping odd stuff, such as chair parts.
I’ve largely adapted your sharpening methodology from the free articles and videos I’ve found, and I plan on getting your book on sharpening soon enough. One question I have in the meantime is about the lack of a strop in your kit. I see a lot of woodworkers often using their strop between sharpenings, and as a means to get rid of the burr. I’m just wondering about your experience and thought process about not using one. (as far as I’ve been able to gather.) Also, a thanks is in order for the immense amount of information you’ve put out over the years. Your writings have been invaluable for troubleshooting and changing the way I work.
In a traditional kit, a strop with rouge is the replacement for an 8,000-grit waterstone. They are the same micron size.
So with bench tools (chisels and plane irons) a strop is just an easy way to round over your bevel and make more work for yourself at the next honing.
I do use a strop to maintain tools with odd edges, such as carving tools and some chairmaking tools. But for chisels and plane irons? The 8,000 grit does the job.
There also is a difference in people’s methods of work. Some people think a strop can lengthen times between honings signficantly. I just haven’t had that experience in my work. Though I consider it entirely valid.
Hi Chris
Do you ever fly with handplanes or saws? If so, any tips or tricks to checking luggage with these items without upsetting TSA? I’m taking a sharpening class this summer that is too far to drive and I’d rather not impose on the school by shipping asking to ship things to them.
Thanks
I do it all the time. I check them in a Pelican case. Tool rolls and plane socks. And I put a label on the outside of the case: Not Firearms (this helps speed things along). I’ve never had any problems.
This is the Pelican I use. The 1510M.
https://www.pelican.com/us/en/product/cases/mobility-case/protector/1510m