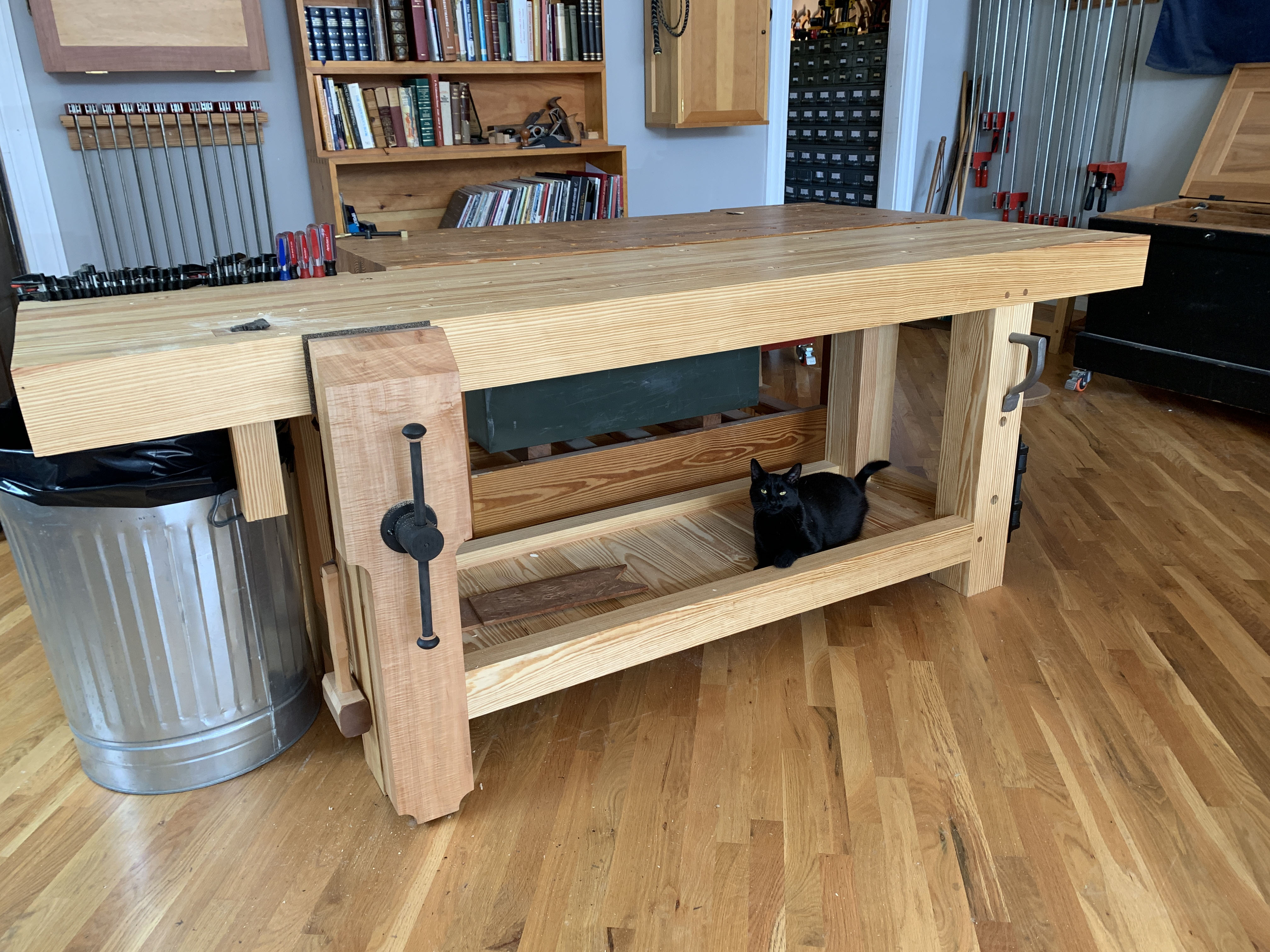
The following is excerpted from “The Anarchist’s Workbench,” by Christopher Schwarz.
“The Anarchist’s Workbench” is – on the one hand – a detailed plan for a simple workbench that can be built using construction lumber and basic woodworking tools. But it’s also the story of Christopher Schwarz’s 20-year journey researching, building and refining historical workbenches until there was nothing left to improve.
Along the way, Schwarz quits his corporate job, builds a publishing company founded on the principles of mutualism and moves into an 1896 German barroom in a red-light district, where he now builds furniture, publishes books and tries to live as an aesthetic anarchist.
“The Anarchist’s Workbench” is the third and final book in the “anarchist” series, and it attempts to cut through the immense amount of misinformation about building a proper bench. It helps answer the questions that dog every woodworker: What sort of bench should I build? What wood should I use? What dimensions should it be? And what vises should I attach to it?
Building a timber-frame workbench isn’t like building a birdhouse. I have found there are a few tools outside of the furniture-makers’ kit that will help the process. Consider calling this appendix “The Anarchist’s Bench-building Addendum to ‘The Anarchist’s Tool Chest.’”
Snappy title, that.
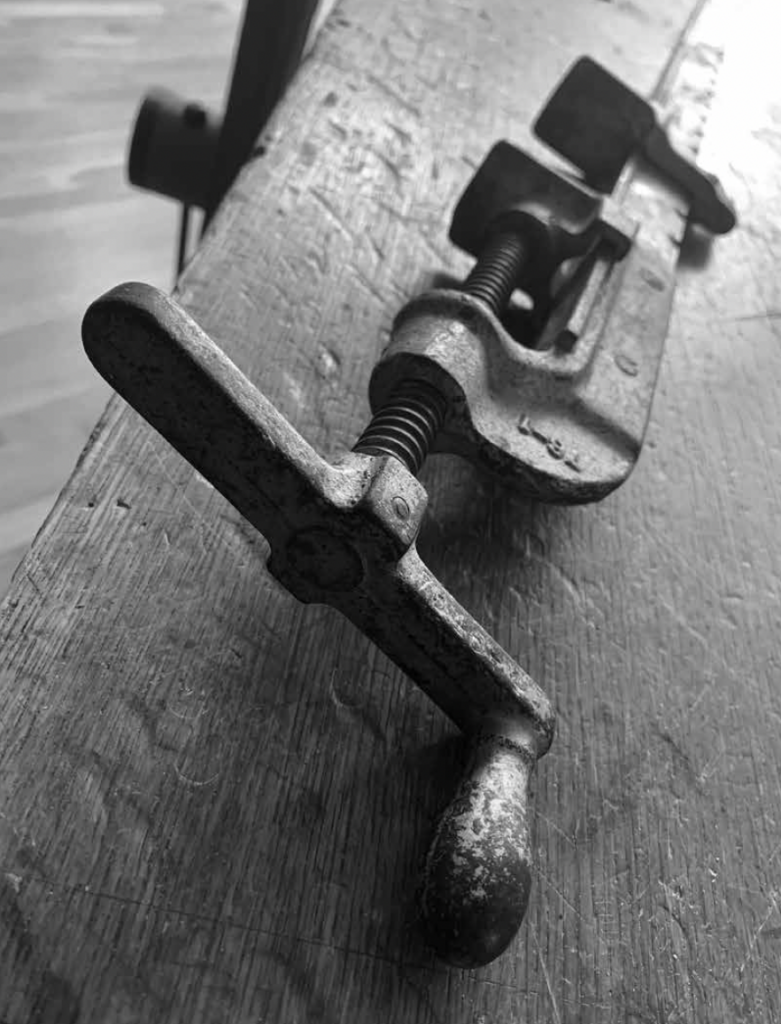
Heavy Metal Clamps
I mentioned this in the chapter on building the benchtop, but it bears repeating. A laminated benchtop will laugh at your lightweight aluminum and nylon clamps. If you want tight joints and you don’t want to glue up your benchtop one board at time, you need heavy iron or steel clamps.
As far as I know, these aren’t available new. So you need to buy vintage. The good news is they are readily available and are usually pretty inexpensive when you buy them in person (shipping online can be a killer).
The best clamps have these features:
- A movable pad with a spring-loaded tooth that bites into notches in the clamp’s bar. The clamp head will not slip under pressure, unlike clamps that use a friction clutch.
- A heavy Acme-thread screw. My clamps have a 5/8″-diameter screw with square threads. The clamps with the little triangle-shaped teeth are puny and worthless.
- A handle that is an offset crank. A straight handle will not let you unlock the full force of the clamp. A cranked handle will.
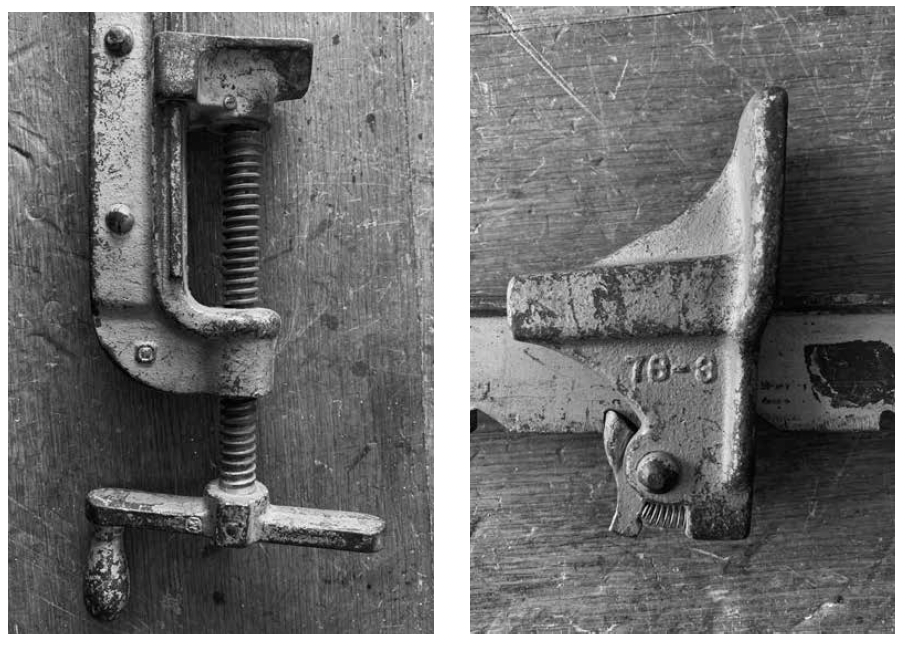
punishing pressure. The notched bar ensures the sliding head won’t move under that pressure.
There are many brands of vintage clamps that have these same features in a slightly different configuration. Instead of a spring-loaded tooth, the clamp might have a removable pin. Instead of an L-shaped cranked handle, it might have a handle that is hinged so you can rotate it 90°. The screw might be 1/2″ or 3/4″ in diameter. Or metric.
Bottom line: If the clamp won’t allow the pad to ever slip, if the thread is Acme and robust, and if the handle allows you to add force at 90° to the screw, buy the clamp. We have a dozen of them in the shop, and I wish we had a dozen more.
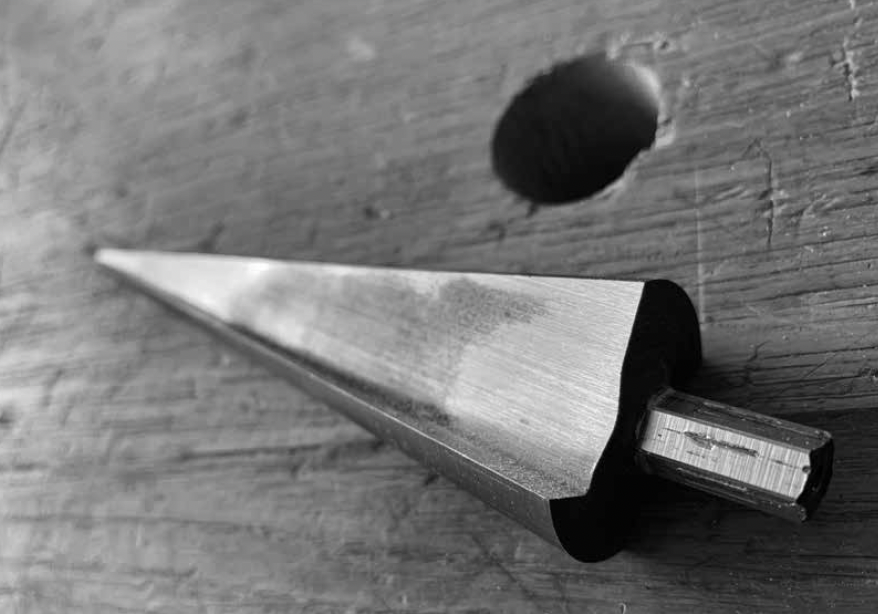
Tapered Reamer
For years I used drawbore pins to deform the hole through the tenon. The deformation allows the oak peg to bend (instead of explode) when it hits the tenon. Another option is to use a tapered reamer on the hole to create the same effect. You just ream the hole that passes through the tenon a little. Too much reaming, however, will weaken the tenon.
There are lots of vintage reamers out there, especially in the plumbing trade. Or you can buy one made for chairmaking.
Here’s how I use it. First I trace the shape of the hole through the leg (or benchtop) onto the tenon. Mark the offset and drill the hole through the tenon. Then ream the hole. There is no need to ream beyond the boundary you traced on the tenon. Ream the exit hole on the tenon a little, too. This method, I have found, lets me use a strong offset (1/8″ or 3/16″) with no failures.
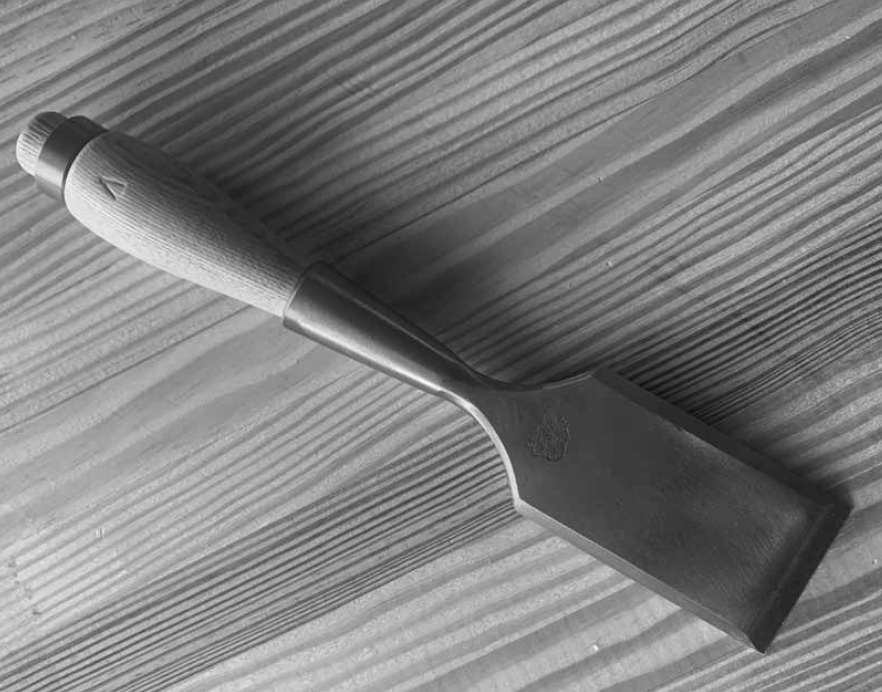
is helpful. If you want the best, buy a Barr.
2″ Heavy Chisel
Your 3/4″ bevel-edge chisel is not going to like bashing out the mortises in the benchtop and the legs. A heavy 2″ chisel will make the job a joy. And you will love having that wide chisel for furniture work – especially defining tenon shoulders and removing waste material for bevels.
I rarely recommend brands, especially in a book. But the bench chisels from Barr Specialty Tools in McCall, Idaho, are the best I have found. Barr Quarton hand-forges each one. The 2″ bench chisel shown above takes and holds an incredible edge.
For years I have used vintage wide chisels because new ones weren’t available from good manufacturers (such as Lie-Nielsen Toolworks) or they just plain sucked. But even the vintage ones were of spotty quality and didn’t hold an edge as well as I wanted.
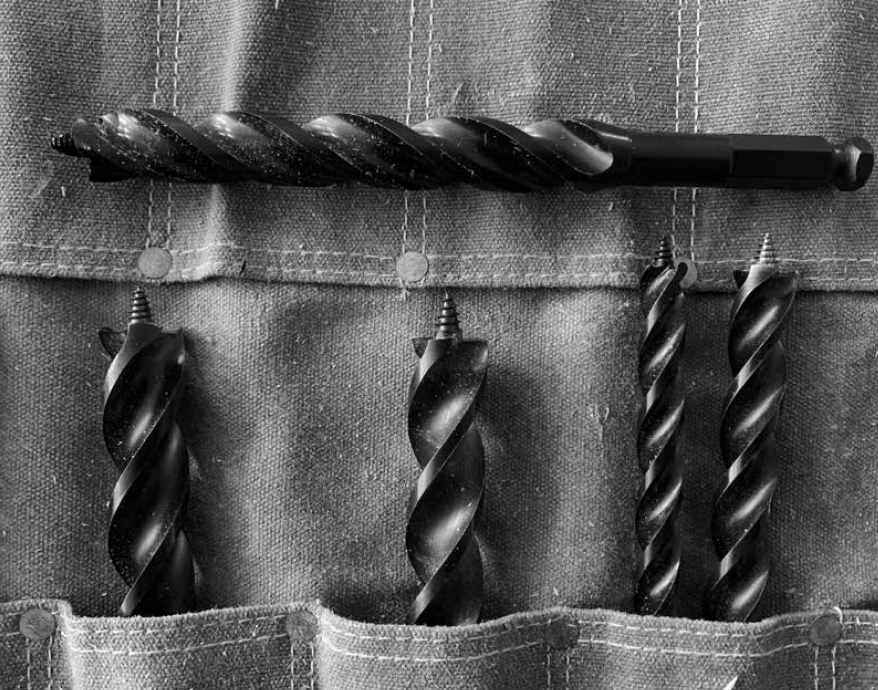
WoodOwl Auger Bits
Again, I dislike recommending brands. But again, here is an exception. WoodOwl auger bits are the best for bench building. They plow through thick and heavy stock without complaint. So they are ideal for boring holes for mortises freehand (don’t use them in a drill press) and drilling holdfast holes. The only downside is they are metric, so the U.S. Customary Units marked on the package are an approximation.
Look for the WoodOwls labeled “tri cut” or “ultra smooth.” Those are the ones that work best for bench building.
Did Barr or you change the handle shape of the chisel pictured or is it actually the (discontinued) cabinet maker chisel as opposed to the “bench” chisel the text mentions?
https://barrtools.com/product/cabinet-maker-2-filler-chisel/ (4″ blade / 10.5″ overall length)
I see they currently offer:
“bench” – 3.5″ blade / 13.5″ overall length
https://barrtools.com/product/bench-chisel-2/
vs
“framing” – 7″ blade / 18″ overall length
https://barrtools.com/product/framing-chisel-2/
Is any of that relevant or does the recommendation stand regardless?
I’m again listening to the audio recording of the book (podcast “Handtool Book Review”).
I deeply respect Chris and his whole attitude, and admire everybody working for / at / with LAP.
This section caused me endless anxiety in the months before I built my bench. Try as I might, I simply couldn’t find a single one of those clamps locally and I wasn’t willing to pay exorbitant prices for the ones online. Finally I decided that an imperfect, gappy bench of this design would be far superior to the “Apocalypse Bench” I had been using; I simply borrowed every set of clamps I could get and went to town. While the top is not perfect, about 7’9″ of the 8′ top is gap free… and it turns out that this bench is indeed better than what I’d been using. Far, far better.
The lesson: don’t let perfect be the enemy of good, and everything I do doesn’t have to be exactly like someone else. Make do and get making.
Same here. The clamps that Chris recommends are like hen’s teeth where I live (eastern Ontario). I definitely let perfect be the enemy of good and brought my two slabs of ash to a local cabinetmaker/carpenter/craftsman/machinist (Jack Forsberg – https://www.instagram.com/jackenglishmachines/ ) and had him join and joint my bench top. It is, indeed, “perfect”. But I still need to build the rest of the bench myself – so I’m going to have to accept “good” (or even not-so-good) eventually.
Adding to the clamp discussion, I also couldn’t find the antique clamps mentioned. I ended up using 8 1” pipe clamps, 4 k-body clamps, and 8 heavy duty 3.5” deep f-clamps, all Bessey, that I was able to collect in various sales while I waited 6 months for my wood to dry. Properly jointing and planing everything and promptly assembling lead to a very tight, gap free bench top and legs.